Metal Injection Molding (MIM)
Precision, Cost-Effective, and Scalable Manufacturing
Struggling with Costly Machining for Small, Complex Metal Parts?
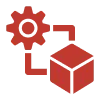
Need high-precision components that traditional machining can't achieve?
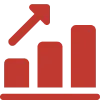
Looking for a cost-effective, high-volume manufacturing solution?
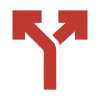
Want to avoid China tariffs while maintaining quality and supply chain stability?
At Align Manufacturing, we provide high-precision metal injection molding (MIM) solutions from our Vietnam, India, and Thailand facilities, helping U.S. companies reduce costs while ensuring reliable production.
How Metal Injection Molding (MIM) Works
MIM combines metal powder metallurgy with plastic injection molding to create high-strength, precision metal parts with complex geometries.
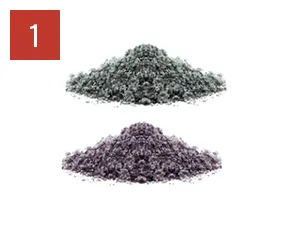
Feedstock Preparation
Metal powder is mixed with a binder (lubricants, polymers, waxes, surfactants) and ground into granules.
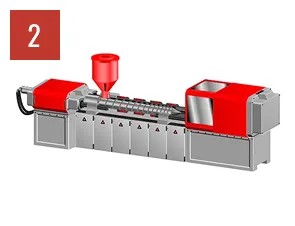
Injection Molding
Heated and injected into a custom mold cavity under pressure.
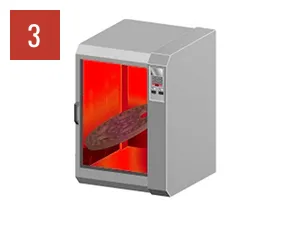
Debinding Process
The binder is partially removed, leaving a porous "brown part."
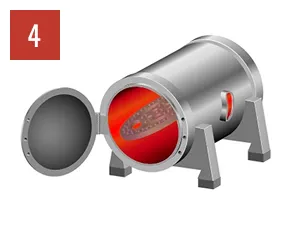
Sintering
The brown part is heated at high temperatures (up to 95%+ density), removing pores and achieving final strength.
Why Choose Metal Injection Molding?
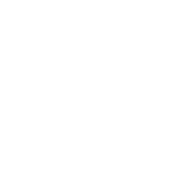
Intricate Geometries
Produces fine details, internal threads, and undercuts with ease.
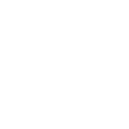
Cost-Effective for Mass Production
Achieves up to 50% lower costs than 5-axis CNC machining.
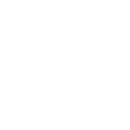
Material Efficiency
Up to 98% utilization, reducing waste, allowing for customized properties such as corrosion resistance, strength, and magnetic performance.
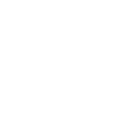
Less Secondary Processing
Eliminates the need for extensive machining.
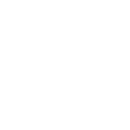
High Strength & Density
Achieves 95%+ of the material’s full density for durability.
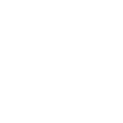
Ideal for High-Volume Production
Best for industries requiring consistent, repeatable parts at scale.
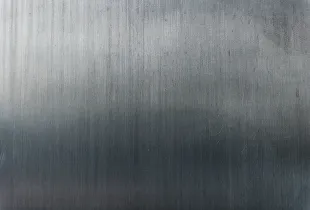
Stainless Steel
Corrosion-resistant for medical, aerospace, and industrial applications.
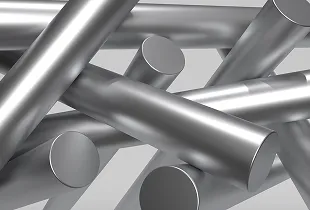
Low Alloy Steel
High strength for automotive, defense, and heavy equipment parts.
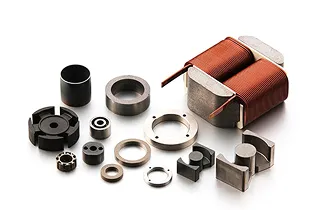
Soft Magnetic Materials
Essential for electronics, energy, and sensor applications.
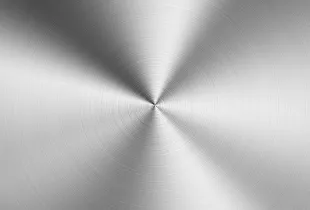
Titanium & Specialty Alloys
Lightweight and biocompatible for medical implants and aerospace.
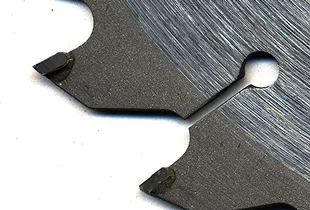
Superalloys & Cemented Carbides
High-performance materials for extreme environments.
Diverse Industry Applications
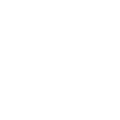
Electronics
Soft magnetic components and precision connectors.
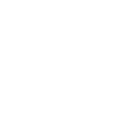
Automotive
Gears, brackets, and structural components.
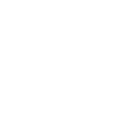
Medical & Healthcare
Surgical instruments and implantable devices.
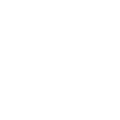
Aerospace & Defense
Lightweight, high-strength parts for critical applications.
Align Manufacturing: Your Partner for Precision MIM Solutions.
- Tariff-Free Production – Manufacturing in Vietnam, India, and Thailand avoids China tariffs.
- Reliable Quality & Testing – Metallurgical review, NDE, and destructive testing for compliance.
- Flexible Production – From prototyping to high-volume runs.
- Consistent On-Time Delivery – Optimized supply chain for fast, reliable shipping.
FAQ
MIM is a high-precision metal forming process that combines the flexibility of plastic injection molding with the strength of powdered metal sintering. It is ideal for producing small, intricate metal parts with tight tolerances and near-net shape, reducing the need for machining. Compared to CNC machining or casting,
Stainless steel (316L, 17-4PH), low alloy steels, titanium, copper, and even some magnetic alloys are widely used. Material selection depends on strength, corrosion resistance, and finish requirements.
MIM generally supports a wide range of metal powders, including:
✔ Stainless Steels – 17-4PH, 316L, 420
✔ Low Alloy Steels – FN02, 4140, 8620
✔ Soft Magnetic Alloys – FeSi3, FN50
✔ Titanium & Superalloys – Ti6Al4V, Inconel 718
✔ Copper & Bronze Alloys – CuSn10, CuNiSiCr
MIM is most effective for small components under 100 grams, especially those with intricate features. Larger parts may require hybrid approaches or alternative processes.
MIM is most cost-effective for mid-to-high volume production (typically 10,000+ parts per year). Lead times depend on part complexity but generally range from 6 to 12 weeks, including tooling, prototyping, and mass production.
MIM is up to 50% more cost-effective than CNC machining for complex, small parts, especially in high volumes. It also produces stronger, more precise parts than casting, with better material utilization and less secondary machining required.
MIM eliminates much of the time and waste associated with CNC, particularly for complex geometries. It’s common to see 30–50% savings in part cost at scale.
We're dedicated team of local professionals passionately committed to fueling your project's success. Our team is dedicated to maintaining a keen eye for detail in every aspect of the process, from design to delivery. Simultaneously, we prioritize clear, consistent communication with you to ensure that your vision a and requirements are fully understood and met.