Powder Metallurgy (PM)
Cost-Effective, High-Performance Metal Components
Struggling with High Material Waste and Costly Machining?

Need complex, precision metal parts without the high costs of traditional machining?

Looking for a cost-effective, high-volume production method?

Want to avoid China tariffs while ensuring a stable and reliable supply chain?
At Align Manufacturing, we specialize in high-precision powder metallurgy (PM) manufacturing from our Vietnam, India, and Thailand facilities—helping U.S. companies reduce costs while ensuring consistent quality and supply chain stability.
Why Choose Powder Metallurgy?

Material Efficiency
Utilizes 97%+ of raw material, reducing waste and lowering costs.

Near-Net Shape Production
Reduces or eliminates secondary machining, saving time and production cost.

Custom Mechanical Properties
Utilizes 97%+ of raw material, reducing waste and lowering costs.

Design Flexibility
Produces intricate geometries that traditional manufacturing methods can't achieve.

Eliminates Excess Machining
Components are produced close to final shape.

Fine Features & Tight Tolerances
Internal channels, undercuts, and complex geometries.

Consistent High-Volume Production
Reliable repeatability for mass production.
Material Selection for Performance & Durability
Powder metallurgy supports a wide range of ferrous and non-ferrous materials, allowing for customized properties such as corrosion resistance, strength, and self-lubrication.
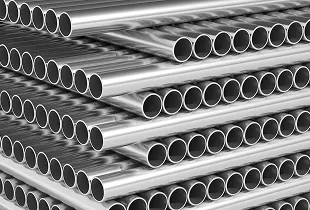
Ferrous Metals
Stainless steel, low-alloy steel, and iron-based materials for automotive and industrial applications.
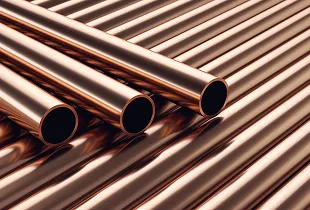
Non-Ferrous Metals
Copper, bronze, and aluminum alloys for conductivity and lightweight applications.
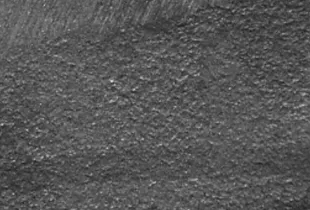
Controlled Porosity
Ideal for self-lubricating bearings, filtration components, and fuel system parts.
Not sure which material fits your project? Request a quote with Align Manufacturing today.
High-Strength, Durable Components for Demanding Applications
Powder metallurgy parts can be heat-treated and density-controlled to meet specific strength, wear resistance, and performance requirements.
Industry Applications – Proven Performance in Multiple Sectors
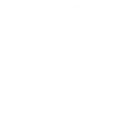
Industrial & Electronics
Heat-resistant and magnetic components.
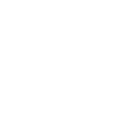
Automotive
Gears, brackets, and structural components.
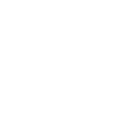
Medical & Healthcare
Biocompatible materials for surgical and orthopedic applications.
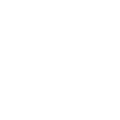
Aerospace & Defense
High-strength, lightweight parts for extreme conditions.
Key Advantages of Powder Metallurgy
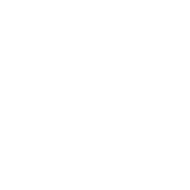
Eco-Friendly Process
97% material utilization, minimal waste.
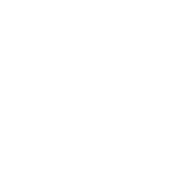
Versatile Material Blending
Combine multiple metals into a single part.
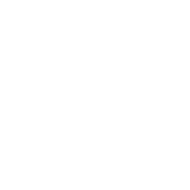
Mass Production Ready
Cost-effective for high-volume production.
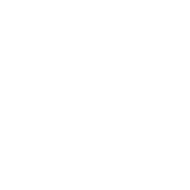
Repeatability & Precision
Every part is manufactured to exact tolerances.
Align Manufacturing: US Manufacturing Expertise You Can Trust
At Align Manufacturing, we utilize cutting-edge powder metallurgy (PM) and metal injection molding (MIM) technologies to ensure precision, cost-effectiveness, and high-performance OEM metal components. With over a decade of experience in metal powder production and shaping, we provide high-quality, customizable metal powders.
Comprehensive Services: Wide range of services and processes to meet diverse needs such as MIM(Metal injection Molding).
Tailored Solutions: Customized approaches designed to address specific requirements.
Efficient Turnaround: Streamlined processes for fast and efficient production.
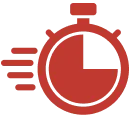
Faster Lead Times
Optimized supply chain for quick turnaround.
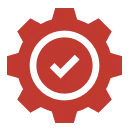
Strict Quality Control
Validated by AQL standards,Metallurgical testing, NDE, and destructive testing ensure compliance.
FAQ
We offer a comprehensive selection of metal powders, encompassing ferrous, non-ferrous, superalloy, soft and hard magnetic, coating, and additive manufacturing powders, catering to a wide range of applications and industries.
Advanced Powder Production: We use gas, water, and plasma atomization, plus PREP technology, to create high-quality metal powders. This yields spherical particles for excellent flowability (MIM, PM, additive manufacturing), custom particle size for strong sintering, and consistent purity for superior mechanical properties. Our PREP process delivers ultra-fine, high-purity, uniform particle size powders for demanding applications (aerospace, medical) cost-effectively.
Powder Purification: Our tri-mode system (vacuum degassing, electromagnetic refining, ultra-fine sieving) ensures top quality by removing impurities, enhancing microstructure, and guaranteeing consistent particle size.
Precision Manufacturing: MIM and Press-Sinter technology produce high-density components (96-99% wrought strength) with near-net shape precision, minimizing machining. We work with various materials, including stainless steel, titanium, copper, and superalloys.
You can request a quote with us through our website or give us a direct call.
Lead times for custom orders vary depending on the specific powder, quantity, and complexity of the order. We will provide you with an estimated lead time upon request.
We maintain stringent quality control measures throughout our production process to ensure the quality of our metal powders. This may include testing for chemical composition, particle size distribution, flowability, and other relevant properties. Specific quality certifications or documentation can be discussed as needed.
We're dedicated team of local professionals passionately committed to fueling your project's success. Our team is dedicated to maintaining a keen eye for detail in every aspect of the process, from design to delivery. Simultaneously, we prioritize clear, consistent communication with you to ensure that your vision a and requirements are fully understood and met.