Aluminum
Aluminum is a versatile material widely used across industries due to its inherent characteristics, such as low density, high strength-to-weight ratio, excellent corrosion resistance, and superior thermal and electrical conductivity, making it an ideal choice for a wide range of applications, from transportation and construction to electronics and packaging. Additionally, several manufacturing processes like sand casting, precision machining, high-pressure die casting, and gravity casting are employed to shape aluminum components based on specific design and performance requirements.
Aluminum Grades
Aluminum is classified into different grades based on its alloy composition and mechanical properties.
1000 Series (Pure Aluminum)
The 1000 series includes aluminum with a purity of 99% or higher, known for its excellent corrosion resistance and high thermal and electrical conductivity. The primary alloying element in this series is aluminum itself, with no significant additions.
Properties:
- Outstanding corrosion resistance, particularly against atmospheric and chemical environments.
- High thermal and electrical conductivity, making it suitable for electrical applications.
- Soft and ductile, with low tensile strength.
Common Applications: Used in electrical wiring, chemical and food processing equipment, heat exchangers, and reflective materials due to its reflective properties.
2000 Series (Copper Alloys)
Primarily alloyed with copper, the 2000 series offers high strength but has lower corrosion resistance than other aluminum grades. This series is often heat-treatable, allowing it to achieve enhanced mechanical properties.
Properties:
- High strength-to-weight ratio.
- Lower corrosion resistance, requiring protective coatings or treatments in many applications.
- Good machinability and weldability (with certain precautions).
Common Applications: Widely used in aerospace components, military applications, and high-stress structural applications like aircraft frames, wings, and fuselage.
3000 Series (Manganese Alloys)
The 3000 series aluminum is primarily alloyed with manganese, providing better strength than pure aluminum while maintaining good corrosion resistance and formability.
Properties:
- Excellent corrosion resistance and workability.
- Moderate strength, allowing for easy forming and shaping.
- Good weldability, though it is not as strong as some other series.
Common Applications: Commonly used in beverage cans, roofing sheets, heat exchangers, and other applications requiring good corrosion resistance and formability. Notable grades include 3003 for its excellent workability and 3105 for residential siding.
4000 Series (Silicon Alloys)
Alloys in the 4000 series are primarily alloyed with silicon, which lowers the melting point and improves fluidity when molten. This makes them well-suited for welding and casting applications.
Properties:
- Lower melting point than other aluminum grades, enhancing casting and welding processes.
- Good wear resistance and reduced expansion.
- Lower strength compared to other series, but with good machinability.
Common Applications: Often used in welding wire, automotive components, and brazing applications. Specific grades like 4045 are used in brazing and cladding, while 4032 is ideal for high-stress applications like automotive pistons.
5000 Series (Magnesium Alloys)
The 5000 series contains magnesium as the primary alloying element, which provides excellent corrosion resistance and good weldability. These alloys are non-heat-treatable.
Properties:
- High strength and excellent resistance to corrosion, especially in marine environments.
- Good workability and weldability, allowing for various forming techniques.
- Moderate to high strength.
Common Applications: Ideal for marine applications, pressure vessels, automotive parts, and architectural applications due to their corrosion resistance. Common grades include 5052, used in fuel tanks and marine structures.
6000 Series (Magnesium and Silicon Alloys)
The 6000 series combines magnesium and silicon as its primary alloying elements, resulting in a versatile aluminum grade with good mechanical properties and corrosion resistance.
Properties:
- Good corrosion resistance, weldability, and extrudability.
- Moderate to high strength and good workability.
- Can be heat-treated to enhance strength.
Common Applications: Widely used in structural applications such as frames, bridges, and buildings, as well as in the manufacturing of extruded products like tubes, bars, and angles. Notable grades include 6061 and 6063.
7000 Series (Zinc Alloys)
The 7000 series is primarily alloyed with zinc, which provides the highest strength of all aluminum grades. It is often used in applications where weight savings and high strength are critical.
Properties:
- Exceptional strength, often comparable to steel.
- Lower corrosion resistance than other series; protective coatings may be required.
- Good machinability but limited weldability.
Common Applications: Frequently used in aerospace and military applications, including aircraft structures, bicycle frames, and sporting equipment. Notable grades include 7075, known for its high strength and durability.
Each grade is selected based on the requirements of the end product, such as strength, weight, or corrosion resistance.
Manufacturing Processes for Aluminum
To transform aluminum into specific components, various casting and machining methods are employed, depending on the desired accuracy, complexity, and production volume.
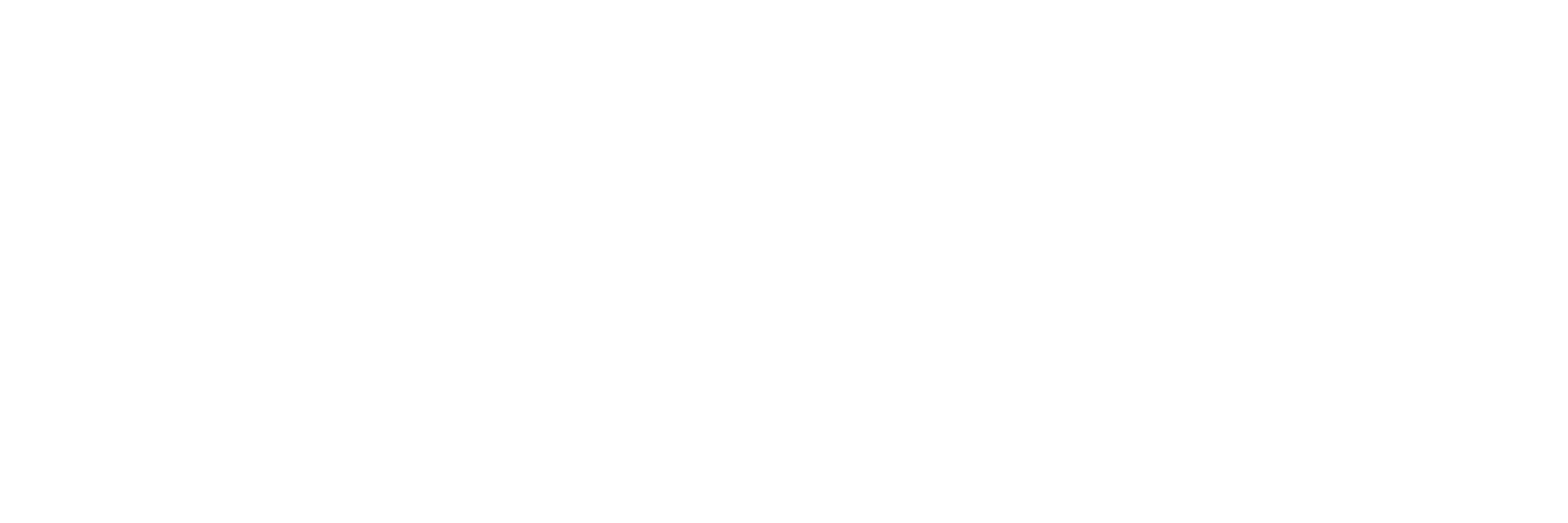
The choice of aluminum grade and casting or machining process depends on the specific needs of the project, balancing factors like strength, corrosion resistance, weight, and cost. By selecting the appropriate method, manufacturers can optimize both the performance and efficiency of aluminum components.
Align Manufacturing specializes in manufacturing aluminum parts, ensuring that your specific project requirements are met with precision and quality. To explore how Align Manufacturing can support your next project, request a quote or contact us.
We're dedicated team of local professionals passionately committed to fueling your project's success. Our team is dedicated to maintaining a keen eye for detail in every aspect of the process, from design to delivery. Simultaneously, we prioritize clear, consistent communication with you to ensure that your vision a and requirements are fully understood and met.