Carbon Steel
Carbon steel is an iron-carbon alloy known for its strength and versatility, with carbon being the primary alloying element. It is classified based on its carbon content into three categories: low, medium, and high carbon steel. Each category offers distinct properties such as ductility, weldability, and hardness, making carbon steel suitable for a wide range of applications. From construction materials to cutting tools, carbon steel is a popular choice in industries like automotive, manufacturing, and infrastructure due to its cost-effectiveness and durability.
Carbon Steel Grades
Carbon steel consists mainly of iron and carbon, with low alloy content. The carbon content determines its classification:
Low Carbon Steel (Mild Steel)
Carbon content: Less than 0.25%
Properties: Good ductility, weldability, and formability. It is easy to machine and offers moderate strength, but low wear resistance.
Uses: Structural beams, sheets, pipes, automotive body panels, and other construction materials.
ASTM A36
Tensile strength: 58,000–80,000 psi
Properties: Standard low-carbon steel with excellent weldability and machinability.
Uses: Bridges, buildings, and general structural purposes.
ASTM A283 Grade C
Tensile strength: 55,000 psi
Properties: Lower strength with good formability and weldability.
Uses: General-purpose structural steel, such as tanks and light structures.
Medium Carbon Steel
Carbon content: 0.25–0.60%
Properties: Higher strength and hardness compared to low carbon steel but lower ductility. It can be heat-treated to improve toughness and wear resistance.
Uses: Machinery parts, automotive components (e.g., axles, gears), and railway tracks.
ASTM A572 Grade 50
Tensile strength: 65,000 psi
Properties: High strength, good toughness, and weldability. It offers better yield strength than A36 steel.
Uses: Bridges, construction equipment, and heavy-load structural applications.
ASTM AISI 1045
Tensile strength: 77,000 psi
Properties: Medium carbon steel with higher strength and hardness, suitable for components that require durability.
Uses: Shafts, gears, bolts, and machinery parts.
High Carbon Steel
Carbon content: Above 0.60%
Properties: Extremely strong and hard, with reduced ductility. It can be heat-treated for higher hardness, but it becomes brittle in the process.
Uses: Cutting tools, blades, high-strength wires, springs, and wear-resistant parts.
ASTM AISI 1095
Tensile strength: 85,000 psi
Properties: High carbon steel with excellent wear resistance and strength, but low toughness.
Uses: Cutting tools, springs, and industrial knives.
ASTM AISI 1080
Tensile strength: 80,000 psi
Properties: High carbon steel with good wear resistance, used in applications that require high strength.
Uses: Saws, wires, and wear-resistant industrial components.
Manufacturing Processes for Carbon Steel
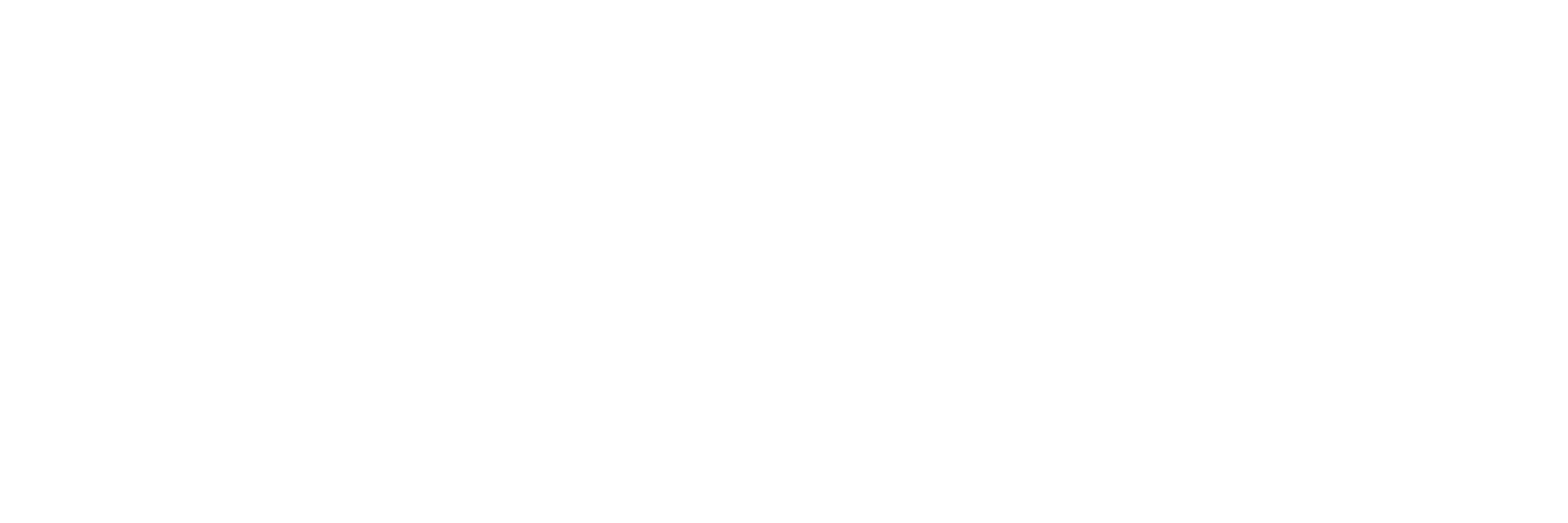
The selection of the appropriate grade ensures the best performance for each application. To explore custom manufacturing solutions for carbon steel components, contact Align Manufacturing.
We're dedicated team of local professionals passionately committed to fueling your project's success. Our team is dedicated to maintaining a keen eye for detail in every aspect of the process, from design to delivery. Simultaneously, we prioritize clear, consistent communication with you to ensure that your vision a and requirements are fully understood and met.