Copper
Copper is a highly conductive metal renowned for its excellent electrical and thermal conductivity, malleability, and resistance to corrosion. As one of the oldest known metals, copper has been used for thousands of years in various applications, from electrical wiring to plumbing. Its unique properties make it an ideal choice in industries such as electrical, construction, and electronics. Copper is often alloyed with other metals like zinc (to form brass) and tin (to form bronze) to enhance its mechanical properties. Its ability to resist biofouling and its antimicrobial properties also contribute to its importance in plumbing and architectural applications.
Copper Grades
Copper grades are classified based on their purity and alloying elements, impacting their electrical, thermal, and mechanical properties. The choice of copper grade depends on the specific requirements of the application, including conductivity, strength, and corrosion resistance.
C10100 - Oxygen-Free Electronic (OFE) Copper
Highly pure copper with minimal impurities, ensuring excellent electrical performance.
Composition: 99.99% copper, minimal impurities (oxygen content ≤ 0.001%).
Properties: Excellent electrical conductivity; high purity.
Uses: Ideal for critical electrical applications like electronic components and high-performance wiring.
C10200 - Oxygen-Free (OF) Copper
Similar to OFE copper but allows for slightly higher impurity levels.
Composition: 99.95% copper, slightly higher impurities than C10100 (oxygen content ≤ 0.003%).
Properties: High conductivity; slightly higher impurity content than OFE.
Uses: Suitable for various electrical applications, including connectors and terminals.
C11000 - Electrolytic Tough-Pitch (ETP) Copper
A high-quality copper grade known for its excellent electrical conductivity and toughness.
Composition: 99.90% copper, with oxygen content of approximately 0.02%.
Properties: Excellent electrical conductivity; good formability.
Uses: Commonly used in electrical wiring, transformers, and motors.
C12000 - DHP (Deoxidized High Phosphorus) Copper
A copper alloy with phosphorus added as a deoxidizer, enhancing its performance.
Composition: 99.90% copper, 0.02-0.15% phosphorus, with minimal impurities.
Properties: Good conductivity; resistance to oxidation.
Uses: Often used in electrical applications requiring good conductivity and durability, such as bus bars.
C12200 - DHP (Deoxidized High Phosphorus) Copper
Similar to C12000, this grade also features phosphorus for improved characteristics.
Composition: 99.90% copper, 0.02-0.15% phosphorus, low levels of impurities.
Properties: Enhanced conductivity; oxidation resistance.
Uses: Utilized in various electrical applications, including conductors and connectors.
C12500 - Fire Refining, Tough-Pitch Copper
A tough-pitch copper grade produced through fire refining, enhancing its electrical properties.
Composition: 99.95% copper, minimal impurities.
Properties: Toughness; good conductivity.
Uses: Suitable for applications needing robust electrical performance.
C14500 - Tellurium-Copper
Copper alloyed with tellurium to improve machinability, making it ideal for precision parts.
Composition: 99.90% copper, 0.4% tellurium, with low levels of other impurities.
Properties: Enhanced machinability; good conductivity.
Uses: Ideal for precision machining applications like switches and contacts.
C14700 - Sulfur-Copper
This copper grade features sulfur for improved machinability, suitable for electrical applications.
Composition: 99.90% copper, 0.1% sulfur, minimal impurities.
Properties: Good machinability; solid conductivity.
Uses: Used in electrical applications, such as connectors and terminals.
C18200 - Chromium-Copper, Unwrought
An alloy of copper and chromium, offering high strength and temperature resistance.
Composition: 95.0% copper, 0.5-1.0% chromium, with low levels of impurities.
Properties: High strength; resistance to softening at high temperatures.
Uses: Suitable for aerospace and defense applications.
C19200 - Copper-Zirconium
A copper alloy that incorporates zirconium, providing enhanced strength at elevated temperatures.
Composition: 98.5% copper, 0.15-0.25% zirconium, with minimal impurities.
Properties: Enhanced strength at high temperatures; good conductivity.
Uses: Ideal for high-temperature applications, including aerospace components and welding electrodes.
Manufacturing Processes for Carbon Steel
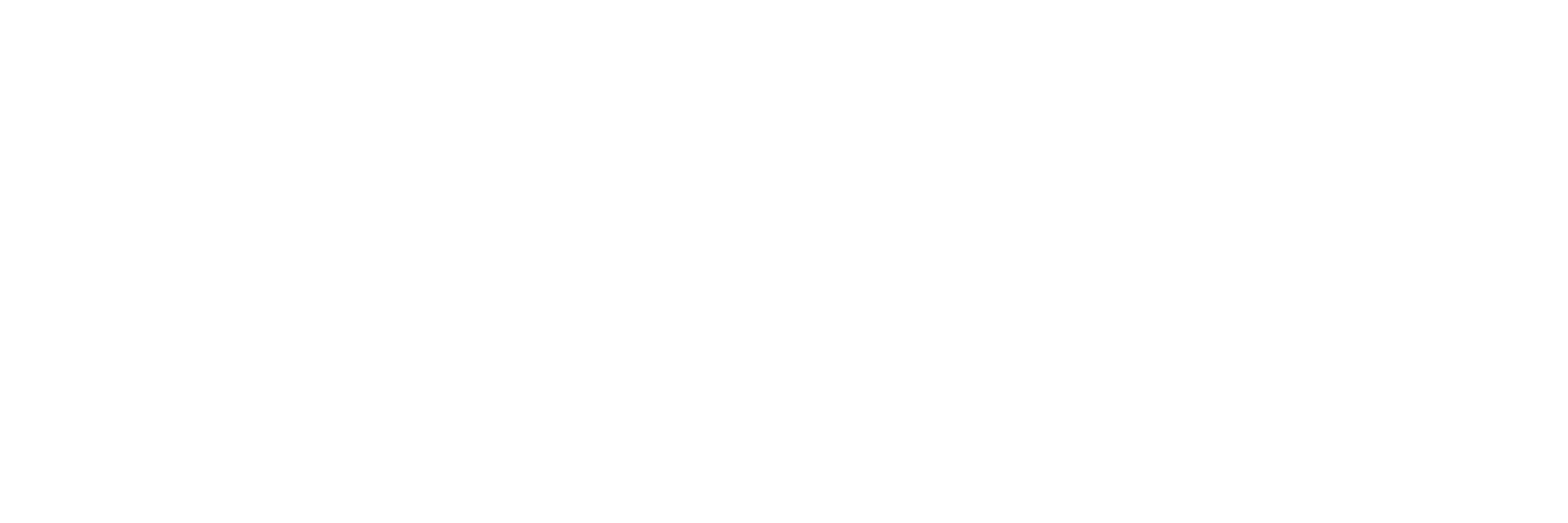
If you require copper manufacturing solutions for your projects, Align Manufacturing is here to help with expert guidance and support.
We're dedicated team of local professionals passionately committed to fueling your project's success. Our team is dedicated to maintaining a keen eye for detail in every aspect of the process, from design to delivery. Simultaneously, we prioritize clear, consistent communication with you to ensure that your vision a and requirements are fully understood and met.