Duplex Steel
Duplex steel is a type of stainless steel known for its two-phase microstructure, consisting of both austenitic and ferritic phases. This unique structure gives duplex steel a combination of high strength, excellent corrosion resistance, and superior toughness. Duplex steels are used in industries like chemical processing, oil and gas, marine applications, and construction where resistance to stress corrosion cracking and pitting is crucial. Its ability to withstand extreme environments, coupled with good weldability, makes it a preferred choice for high-performance applications.
Duplex Steel Grades
Ductile iron, also known as spheroidal graphite iron, has several grades, each with distinct properties.
Duplex 2205 (UNS S31803/S32205)
- Composition: 22% chromium, 5-6% nickel, 3% molybdenum
- Properties: This is the most commonly used duplex grade, known for excellent resistance to pitting, crevice corrosion, and stress corrosion cracking. It offers high strength, good weldability, and exceptional toughness.
- Yield Strength: 65,000 psi (450 MPa)
- Tensile Strength: 90,000 psi (620 MPa)
- Elongation: 25%
- Hardness: 293 HB (Brinell Hardness)
- Uses: Ideal for pressure vessels, storage tanks, heat exchangers, and pipelines in the chemical, petrochemical, and oil industries.
Super Duplex 2507 (UNS S32750/S32760)
- Composition: 25% chromium, 7% nickel, 4% molybdenum
- Properties: Offers superior resistance to chloride stress corrosion cracking, pitting, and crevice corrosion. It also has higher strength and toughness compared to standard duplex grades, making it suitable for extremely harsh environments.
- Yield Strength: 80,000 psi (550 MPa)
- Tensile Strength: 116,000 psi (800 MPa)
- Elongation: 15%
- Hardness: 310 HB
- Uses: Offshore oil rigs, subsea equipment, desalination plants, and high-pressure chemical processing.
Lean Duplex 2101 (UNS S32101)
- Composition: 21% chromium, 1.5% nickel, 0.3% molybdenum
- Properties: A cost-effective duplex steel with lower nickel content while maintaining good corrosion resistance, fatigue resistance, and strength. This grade offers a good balance between performance and price.
- Yield Strength: 65,000 psi (450 MPa)
- Tensile Strength: 94,000 psi (650 MPa)
- Elongation: 30%
- Hardness: 260 HB
- Uses: Ideal for structural components, storage tanks, and bridges.
Duplex 2304 (UNS S32304)
- Composition: 23% chromium, 4% nickel, 0.1% molybdenum
- Properties: Offers similar corrosion resistance and strength to 316 stainless steel but with lower nickel content, making it more economical. It is also known for good stress corrosion cracking resistance.
- Yield Strength: 65,000 psi (450 MPa)
- Tensile Strength: 87,000 psi (600 MPa)
- Elongation: 25%
- Hardness: 270 HB
- Uses: Suitable for water treatment systems, food processing equipment, and heat exchangers.
Manufacturing Processes for Duplex Steel
If you're seeking high-performance duplex steel solutions customized to your manufacturing needs, contact Align Manufacturing for expert support.
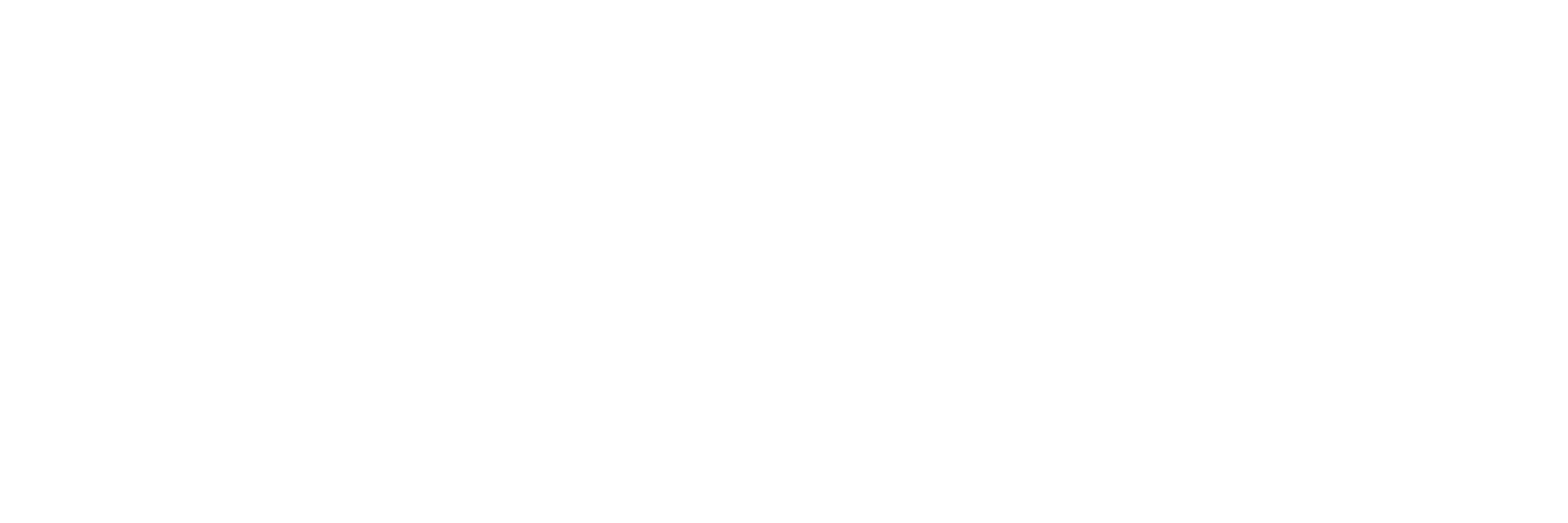
At Align Manufacturing, we pride ourselves on our commitment to producing quality metal parts. Our experienced team utilizes equipment and processes to ensure each component meets the highest standards of precision and reliability.
We continuously strive to innovate and improve our methods, ensuring that our clients receive parts that not only meet but exceed their expectations in performance and durability. With a focus on excellence and customer satisfaction, Align MFG remains a trusted partner for all your metal needs.
We're dedicated team of local professionals passionately committed to fueling your project's success. Our team is dedicated to maintaining a keen eye for detail in every aspect of the process, from design to delivery. Simultaneously, we prioritize clear, consistent communication with you to ensure that your vision a and requirements are fully understood and met.