Gray and Ductile Iron
Gray Iron and Ductile Iron are both popular types of cast iron, known for their durability and mechanical properties. Gray iron is characterized by its graphite flakes, giving it excellent compressive strength and vibration-damping qualities, though it is brittle. Ductile iron, on the other hand, has graphite in spherical nodules, offering superior ductility, toughness, and impact resistance. Both materials are used across various industries, with gray iron often found in machinery bases and engine blocks, while ductile iron is favored in automotive components and pipelines for its strength and resilience.
Gray Iron
Gray Iron gets its name from the gray fracture it leaves due to the presence of graphite flakes. These flakes cause the iron to be brittle but provide excellent compressive strength and machinability. It is commonly used in applications that require good vibration damping and wear resistance, such as engine blocks, machinery bases, and pipes.
Key Properties:
- Brittle: Can fracture under tensile stress, but provides excellent compressive strength.
- Good machinability: Easy to machine, ideal for complex shapes.
- Heat resistance: Performs well under high temperatures
Gray Iron Grades
ASTM A48 Class 20
- Tensile strength: 20,000 psi
- Properties: Lower strength but excellent machinability.
- Uses: Pump housings, low-stress machinery components, and small parts that require intricate shapes.
ASTM A48 Class 25
- Tensile strength: 25,000 psi
- Properties: Slightly higher strength with good machinability and damping capabilities.
- Uses: Applications requiring vibration damping, such as small engine components, covers, and light-duty parts.
ASTM A48 Class 30
- Tensile strength: 30,000 psi
- Properties: Good combination of strength and machinability with moderate vibration damping.
- Uses: Engine blocks, transmission housings, and medium-stress machine components.
ASTM A48 Class 35
- Tensile strength: 35,000 psi
- Properties: Better wear resistance and moderate strength, suitable for components under heavier loads.
- Uses: Cylinder heads, brake drums, and flywheels in automotive applications.
ASTM A48 Class 40
- Tensile strength: 40,000 psi
- Properties: High strength with good wear resistance, but slightly less machinable than lower grades.
- Uses: Machinery bases, brake rotors, and engine components requiring higher tensile strength.
ASTM A48 Class 50
- Tensile strength: 50,000 psi
- Properties: Highest strength in gray iron grades, offers enhanced wear resistance and durability.
- Uses: Heavy-duty applications like large machinery bases, high-pressure pipes, and heavy industrial equipment.
ASTM A126 Class A
- Tensile strength: 21,000 psi
- Properties: Lower strength, designed for non-pressurized applications with good machinability.
- Uses: Valve bodies, pipe fittings, and components in low-stress applications.
ASTM A126 Class B
- Tensile strength: 31,000 psi
- Properties: Improved strength and wear resistance compared to Class A.
- Uses: Pressure-rated applications like pump casings, valve bodies, and industrial castings.
ASTM A126 Class C
- Tensile strength: 40,000 psi
- Properties: High strength and excellent wear resistance, ideal for more demanding applications.
- Uses: Steam valves, large industrial castings, and high-pressure components.
These grades of gray iron are selected based on the requirements of specific applications, considering factors such as strength, machinability, wear resistance, and cost.
Ductile Iron
Ductile Iron, also known as nodular or spheroidal graphite iron, contains spherical graphite nodules, which give it superior ductility, toughness, and impact resistance compared to gray iron. Ductile iron is commonly used in automotive components, pipelines, and heavy-duty gears.
Key Properties:
- Brittle: Can deform without breaking, allowing for better impact resistance.
- Good machinability: Stronger than gray iron, with better wear and fatigue resistance.
- Heat resistance: Performs better in harsh environments.
Ductile Iron Grades
ASTM A536 Grade 60-40-18
- Tensile strength: 60,000 psi
- Yield strength: 40,000 psi
- Elongation: 18%
- Uses: Pipe fittings, valves, machinery components.
ASTM A536 Grade 65-45-12
- Tensile strength: 65,000 psi
- Yield strength: 45,000 psi
- Elongation: 12%
- Uses: Automotive components, housings, pump bodies.
ASTM A536 Grade 80-55-06
- Tensile strength: 80,000 psi
- Yield strength: 55,000 psi
- Elongation: 6%
- Uses: Gears, axles, crankshafts, heavy-duty components.
ASTM A536 Grade 100-70-03
- Tensile strength: 100,000 psi
- Yield strength: 70,000 psi
- Elongation: 3%
- Uses: Heavy machinery, structural parts, high-stress gears.
ASTM A536 Grade 120-90-02
- Tensile strength: 120,000 psi
- Yield strength: 90,000 psi
- Elongation: 2%
- Uses: Military equipment, high-pressure pipelines, industrial machinery.
Solid Solution Ductile Iron
- Properties: Enhanced heat and wear resistance due to solid solution strengthening.
- Uses: Exhaust manifolds, turbocharger housings, high-temperature components.
Low Temperature Impact Resistant ASTM A536
- Properties: Retains toughness and impact resistance at low temperatures.
- Uses: Cold-weather pipelines, transportation systems, pressure vessels.
Manufacturing Processes for Gray and Ductile Iron
The selection between gray and ductile iron depends on the specific mechanical requirements, such as compressive strength, ductility, or wear resistance. Each grade and manufacturing process is designed to meet the needs of applications ranging from heavy machinery to automotive parts.
For more information on selecting the best material and manufacturing process for your project, contact Align Manufacturing and connect with their expert team today.
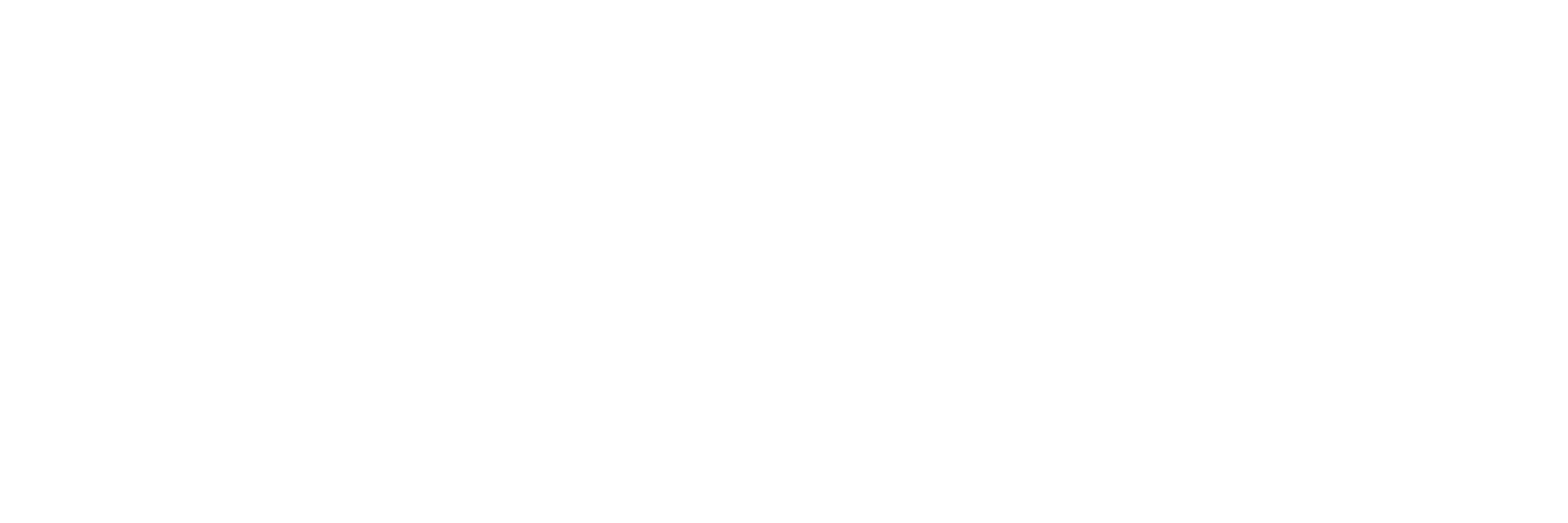
At Align Manufacturing, we pride ourselves on our commitment to producing quality metal parts. Our experienced team utilizes equipment and processes to ensure each component meets the highest standards of precision and reliability.
We continuously strive to innovate and improve our methods, ensuring that our clients receive parts that not only meet but exceed their expectations in performance and durability. With a focus on excellence and customer satisfaction, Align MFG remains a trusted partner for all your metal needs.
We're dedicated team of local professionals passionately committed to fueling your project's success. Our team is dedicated to maintaining a keen eye for detail in every aspect of the process, from design to delivery. Simultaneously, we prioritize clear, consistent communication with you to ensure that your vision a and requirements are fully understood and met.