Stainless Steel
Stainless steel is a highly versatile, iron-based alloy known for its exceptional resistance to corrosion and staining. This property is primarily due to the presence of chromium (at least 10.5%), which forms a passive protective layer on the surface, preventing rust. Stainless steel also offers excellent strength, durability, and aesthetic appeal, making it an essential material across numerous industries. Its ability to maintain structural integrity in harsh environments, combined with resistance to heat and chemical corrosion, makes stainless steel indispensable in applications ranging from kitchen utensils and medical instruments to aerospace components and industrial machinery.
Zinc Grades
Zinc is widely used in industries for its excellent corrosion resistance and low melting point. It is commonly alloyed with other metals to enhance performance, as seen in materials like brass (zinc + copper) or zamak (zinc + aluminum, magnesium, and copper).
Stainless Steel Families and Grades
Stainless steel is categorized into various families and grades, each with unique properties suited for specific applications. The four primary families of stainless steel are austenitic, ferritic, martensitic, and duplex. Each family is differentiated by its microstructure and chemical composition, which influence its mechanical properties and corrosion resistance. Here’s an overview of these families and some common grades within them:
Austenitic Stainless Steel
Austenitic stainless steel has a face-centered cubic (FCC) crystal structure, making it non-magnetic and very ductile.
Key Properties:
- Excellent corrosion resistance due to the high chromium (16-25%) and nickel content.
- Non-magnetic in its annealed state, though some grades may become slightly magnetic when cold worked.
- Good formability and weldability, making it widely used in construction, kitchen equipment, and medical devices.
Common Grades:
- 304: Known as the most common stainless steel, it offers excellent corrosion resistance and is used in food processing, chemical containers, and sinks.
- 316: Contains molybdenum, enhancing its corrosion resistance, particularly against chlorides and acidic environments. It’s commonly used in marine applications, pharmaceuticals, and chemical plants.
Ferritic Stainless Steel
Ferritic stainless steels have a body-centered cubic (BCC) crystal structure, making them magnetic and less ductile than austenitic stainless steels.
Key Properties:
- Moderate corrosion resistance, typically lower than austenitic grades but better suited for specific environments like automotive exhausts and architectural applications.
- Magnetic, unlike austenitic grades.
- Good resistance to stress corrosion cracking.
Common Grades:
- 430: One of the most widely used ferritic grades, it has good resistance to corrosion and oxidation and is used in automotive trims, kitchen appliances, and architectural decoration.
- 409: Primarily used in automotive exhaust systems, offering good resistance to heat and corrosion.
Martensitic Stainless Steel
Martensitic stainless steels have a body-centered tetragonal (BCT) crystal structure, making them hard and strong, but less corrosion-resistant compared to other families.
Key Properties:
- High hardness and strength due to heat treatment (they are the only stainless steels that can be hardened by quenching and tempering).
- Lower corrosion resistance compared to austenitic and ferritic steels.
- Magnetic and used in applications requiring high wear resistance.
Common Grades:
- 410: Offers good wear resistance and moderate corrosion resistance, commonly used in cutlery, turbine blades, and surgical instruments.
- 420: Known for its higher hardness, it’s often used in knife blades, surgical instruments, and hand tools.
Duplex Stainless Steel
Duplex stainless steels have a mixed microstructure of approximately 50% austenite and 50% ferrite, combining the best properties of both.
Key Properties:
- Superior strength compared to austenitic and ferritic steels.
- Excellent resistance to stress corrosion cracking and pitting, making it suitable for harsh environments like offshore and marine applications.
- Better corrosion resistance than ferritic steels and higher strength than austenitic steels.
Common Grades:
- 2205: The most widely used duplex grade, offering excellent corrosion resistance and strength, typically found in oil and gas applications, chemical processing, and heat exchangers.
- 2507: A super duplex stainless steel with even higher strength and resistance to corrosion, used in demanding environments like desalination plants and marine engineering.
Stainless Steel Grades Designation
Each stainless steel grade is designated by numbers based on its composition and properties. The most common systems used to identify stainless steel grades are:
- AISI (American Iron and Steel Institute) numbering system (e.g., 304, 316).
- EN (European Standard) system (e.g., 1.4301, 1.4404).
- UNS (Unified Numbering System), which combines several identification systems into one (e.g., S30400 for 304 stainless steel).
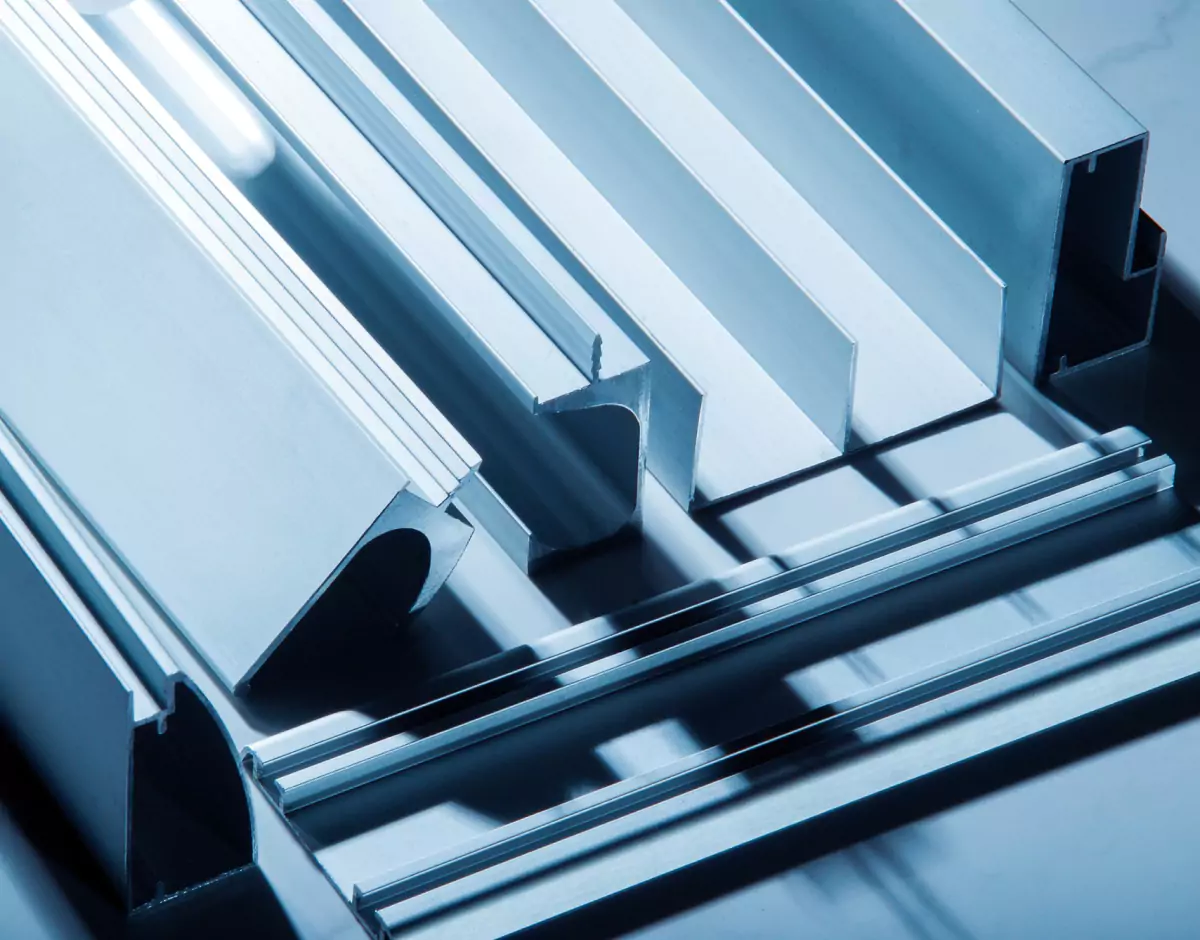
Manufacturing Processes for Stainless Steel
To find the ideal stainless steel components for your project, contact Align Manufacturing for expert guidance and solutions tailored to your requirements.
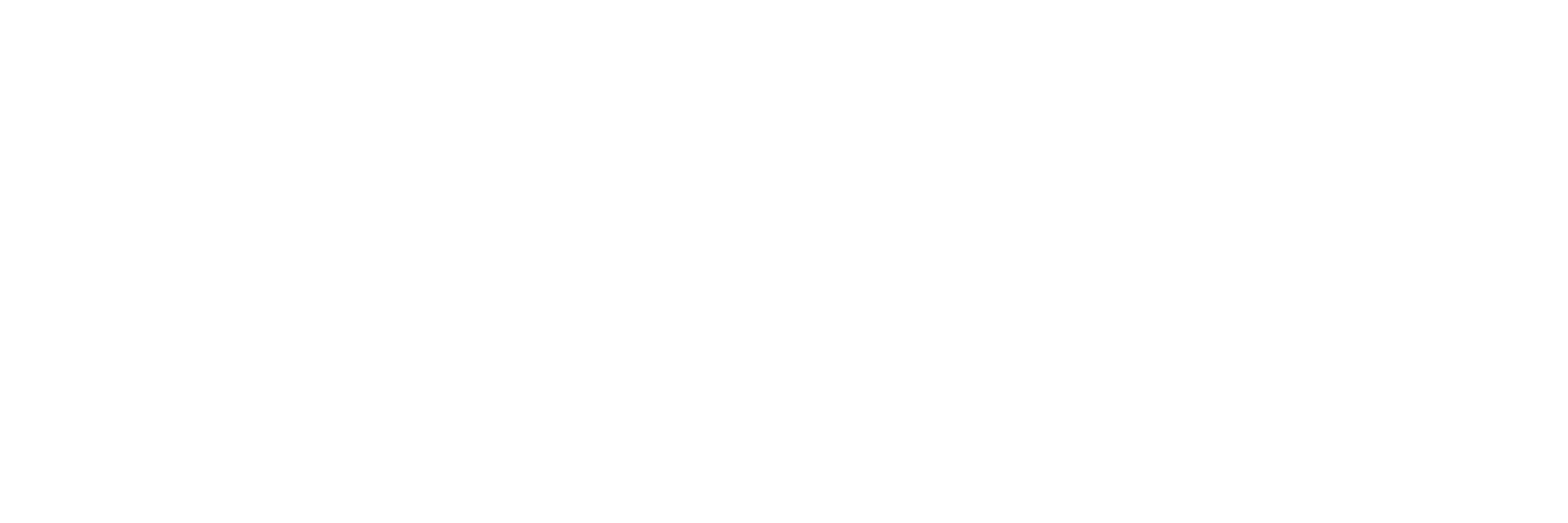
At Align Manufacturing, we pride ourselves on our commitment to producing quality metal parts. Our experienced team utilizes equipment and processes to ensure each component meets the highest standards of precision and reliability.
We continuously strive to innovate and improve our methods, ensuring that our clients receive parts that not only meet but exceed their expectations in performance and durability. With a focus on excellence and customer satisfaction, Align MFG remains a trusted partner for all your metal needs.
We're dedicated team of local professionals passionately committed to fueling your project's success. Our team is dedicated to maintaining a keen eye for detail in every aspect of the process, from design to delivery. Simultaneously, we prioritize clear, consistent communication with you to ensure that your vision a and requirements are fully understood and met.