Zinc
Zinc is a versatile metal known for its excellent corrosion resistance, low melting point, and ease of alloying with other metals. Commonly used in industries ranging from automotive to construction, zinc is often alloyed with aluminum, magnesium, and copper to enhance its mechanical properties, forming materials like zamak. Zinc’s applications span die casting, galvanization, and manufacturing, making it a crucial component in producing durable and corrosion-resistant parts. Its high strength-to-weight ratio and protective qualities have made zinc indispensable in areas requiring longevity and reliability.
Zinc Grades
Zinc is widely used in industries for its excellent corrosion resistance and low melting point. It is commonly alloyed with other metals to enhance performance, as seen in materials like brass (zinc + copper) or zamak (zinc + aluminum, magnesium, and copper).
Zinc Alloy 3 (Zamak 3)
- Composition: 96% Zinc, 4% Aluminum
- Properties: Good balance of strength, ductility, and corrosion resistance. It is easy to cast and has excellent dimensional stability and surface finish.
- Uses: Widely used in die casting for parts such as automotive components, hardware, and appliances.
- Strength: Tensile strength of 41,000 psi, making it suitable for medium-strength applications.
Zinc Alloy 5 (Zamak 5)
- Composition: Similar to Alloy 3 but contains 1% copper for added strength.
- Properties: Higher strength and hardness compared to Zamak 3, with slightly reduced ductility.
- Uses: Ideal for components requiring higher mechanical performance like gears, housings, and mechanical fittings.
- Strength: Tensile strength of 48,000 psi, offering improved durability over Alloy 3.
Zinc Alloy 7 (Zamak 7)
- Composition: Like Zamak 3 but with lower magnesium content, offering better ductility.
- Properties: Has enhanced impact resistance and excellent casting characteristics for thin-walled parts.
- Uses: Used in precision components where improved ductility is needed, such as electronic housings and small mechanical parts.
- Strength: Tensile strength of 41,000 psi, with increased flexibility for detailed designs.
Zinc Alloy 12
- Composition: 88.9% Zinc, 10% Aluminum, 0.2% Copper
- Properties: Higher aluminum content provides increased strength and hardness but reduces elongation. It has good thermal conductivity and excellent wear resistance.
- Uses: Typically used for applications requiring higher strength, such as bearings, bushings, and large structural components.
- Strength: Tensile strength of 50,000 psi, suited for heavy-duty uses.
Zinc 99.9% Pure
- Composition: Pure Zinc with minimal alloying elements.
- Properties: Excellent corrosion resistance, especially in harsh environments. It is often used as a coating to prevent rust.
- Uses: Widely used in galvanization (coating steel and iron), battery casings, and chemical applications.
- Strength: Lower tensile strength compared to alloys, at around 19,000 psi, but excellent for coating and chemical resistance.
These zinc grades are selected based on their mechanical properties and suitability for various casting, manufacturing, and galvanizing applications.
Manufacturing Processes for Zinc
If you’re looking to explore how zinc alloys can benefit your project needs, contact Align Manufacturing today.
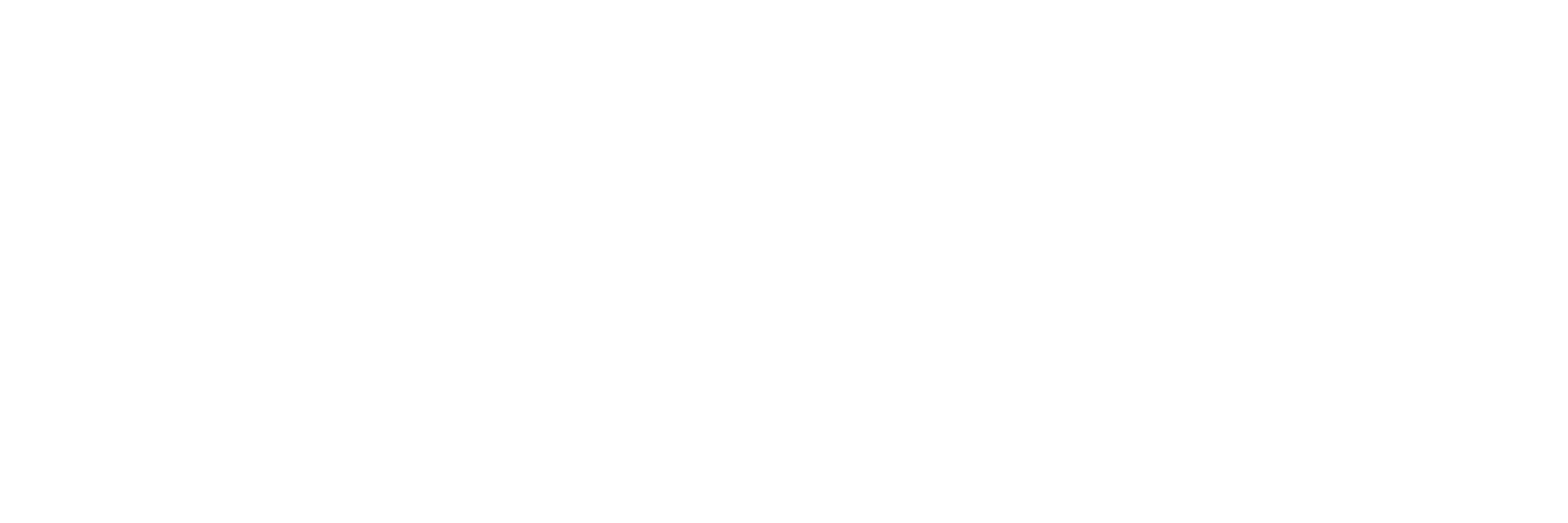
At Align Manufacturing, we pride ourselves on our commitment to producing quality metal parts. Our experienced team utilizes equipment and processes to ensure each component meets the highest standards of precision and reliability.
We continuously strive to innovate and improve our methods, ensuring that our clients receive parts that not only meet but exceed their expectations in performance and durability. With a focus on excellence and customer satisfaction, Align MFG remains a trusted partner for all your metal needs.
We're dedicated team of local professionals passionately committed to fueling your project's success. Our team is dedicated to maintaining a keen eye for detail in every aspect of the process, from design to delivery. Simultaneously, we prioritize clear, consistent communication with you to ensure that your vision a and requirements are fully understood and met.