Choose the Perfect Manufacturing
Process for Your Plastic Components
At Align MFG, we understand that plastics are the backbone of modern industry, offering unparalleled versatility, durability, and cost-effectiveness.
As a leading manufacturer, we work with a wide range of plastic materials and processes, providing our clients with customized solutions that meet their exacting standards. Whether you're in automotive, aerospace, consumer goods, or medical devices, our expertise in plastic manufacturing ensures that your components are produced with precision and reliability.
Types of Plastics
We offer an extensive selection of high-performance plastics, each tailored to specific applications and industries. Here's a look at some of the key thermoplastics we work with:
Polycarbonate-ABS
(PC-ABS)
Combining the strength of PC with the flexibility of ABS, this material is ideal for applications requiring toughness and heat resistance, such as in automotive interiors and electronics housings.
Acrylonitrile Butadiene
Styrene (ABS)
ABS is known for its toughness and impact resistance, making it perfect for automotive trim, consumer electronics, and toys.
Nylon
(Polyamide 66 - PA66)
With excellent mechanical properties and resistance to wear, PA66 is a go-to material for gears, bearings, and other high-performance components.
Polyoxymethylene
(POM)
Also known as acetal, POM offers low friction and high stiffness, ideal for precision parts like gears and bearings.
Polypropylene
(PP)
Known for its excellent chemical resistance, low density, and fatigue resistance, PP is ideal for automotive parts, containers, and consumer products.
Polystyrene
(PS)
A versatile plastic with good clarity and rigidity, PS is commonly used in packaging, disposable cutlery, and laboratory ware.
Polyphenylene
Sulfide (PPS)
High temperature resistance and mechanical strength make PPS suitable for demanding applications in the automotive and electronics sectors.
Polycarbonate
(PC)
This strong and impact-resistant material is widely used in automotive components, electronics, and safety equipment.
Styrene Acrylonitrile
(SAN)
SAN combines clarity with rigidity, commonly used in food containers, cosmetic packaging, and medical devices.
Polyethylene
Terephthalate (PET)
PET is widely recognized for its use in beverage bottles and food packaging, thanks to its strength and barrier properties.
Polybutylene
Terephthalate (PBT)
PBT offers excellent dimensional stability and electrical resistance, making it suitable for connectors, switches, and automotive components.
Polyetherimide
(PEI)
Known for its high strength and flame resistance, PEI is used in aerospace, medical devices, and electrical components.
Polyvinyl Chloride
(PVC)
PVC is valued for its chemical resistance and flexibility, used in piping, medical tubing, and construction materials.
High-Density
Polyethylene (HDPE)
HDPE offers excellent toughness and chemical resistance, commonly used in containers, piping, and geomembranes.
Ultra-High-Molecular-Weight
Polyethylene (UHMW)
With outstanding impact resistance and low friction, UHMW is ideal for wear strips, guides, and high-wear components.
Choosing the right plastic material:
Choosing the right material for your plastic components is a critical decision that impacts the performance, durability, and cost of your final product. At Align MFG, we take a holistic approach to material selection, considering not only the mechanical properties of materials like Polypropylene (PP), Polycarbonate (PC), or Nylon (PA66), but also how these materials will perform in the specific conditions your product will face.
For instance, if your application involves high temperatures and chemical exposure, materials like Polyphenylene Sulfide (PPS) may be ideal due to their excellent thermal stability and resistance to harsh chemicals.
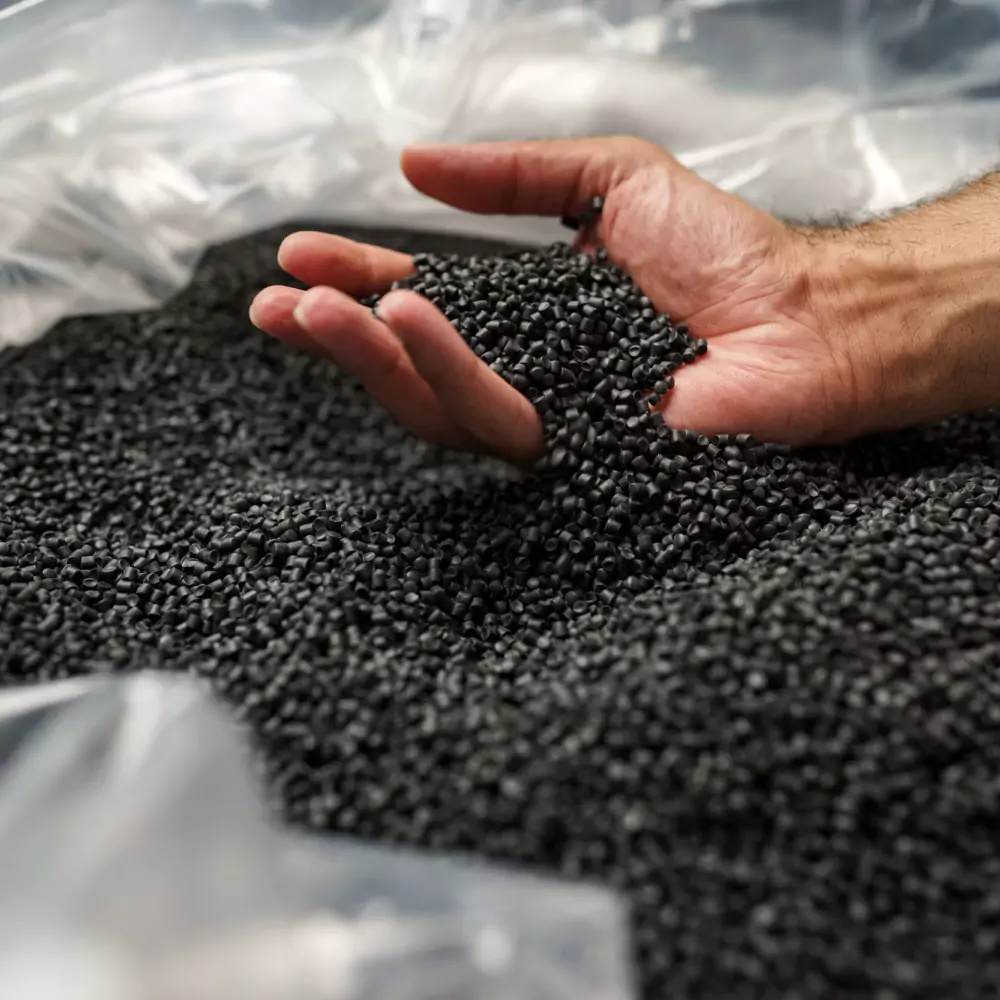
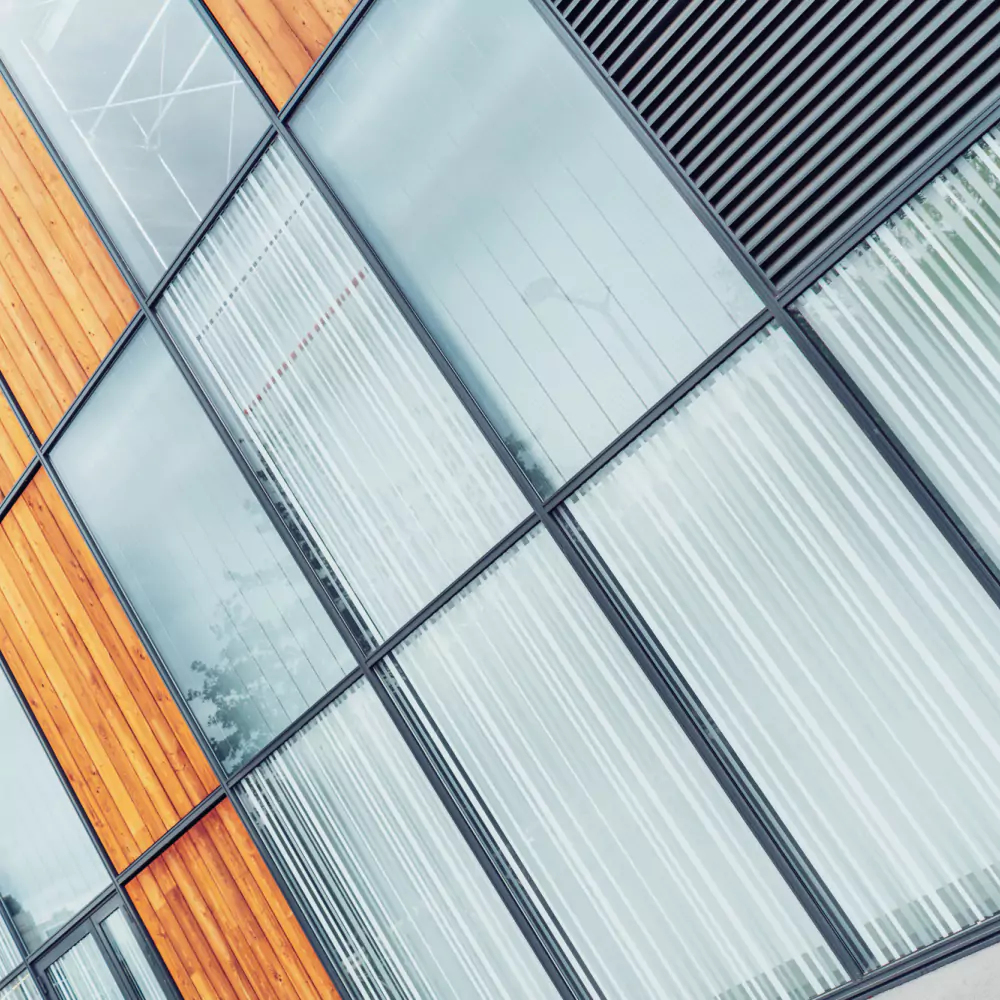
Alternatively, if your product requires transparency and impact resistance, Polycarbonate (PC) might be the best choice. We also consider factors such as weight, flexibility, and cost-effectiveness, ensuring that the material you choose will meet all functional requirements while remaining within budget.
Our team is dedicated to helping you navigate the complexities of material selection. We provide expert guidance to ensure that the materials used in your project not only meet but exceed industry standards, delivering high-quality, durable, and reliable components tailored to your specific needs.
Plastic Manufacturing Processes
For plastic manufacturing, a variety of processes are included, ensuring that we can meet the diverse needs of our clients.
Rotomolding, Blow Molding, Extruding, and Machining: Each of these processes is tailored to specific applications, with detailed control over dimensions and material properties. While injection molding is predominant, these processes offer alternative solutions for specific product requirements.
Choosing the Right Manufacturing Process for Your Plastic Components
We recognize that selecting the right manufacturing process is crucial to achieving optimal results for your plastic components. Each process—whether it's injection molding, rotomolding, blow molding, extruding, or machining—has its own set of strengths, limitations, and ideal applications. For example, injection molding is unparalleled in its ability to produce high-volume, precise components with complex geometries, making it ideal for industries like automotive and consumer electronics. On the other hand, rotomolding excels in creating large, hollow parts such as tanks and containers, offering seamless construction with excellent durability.
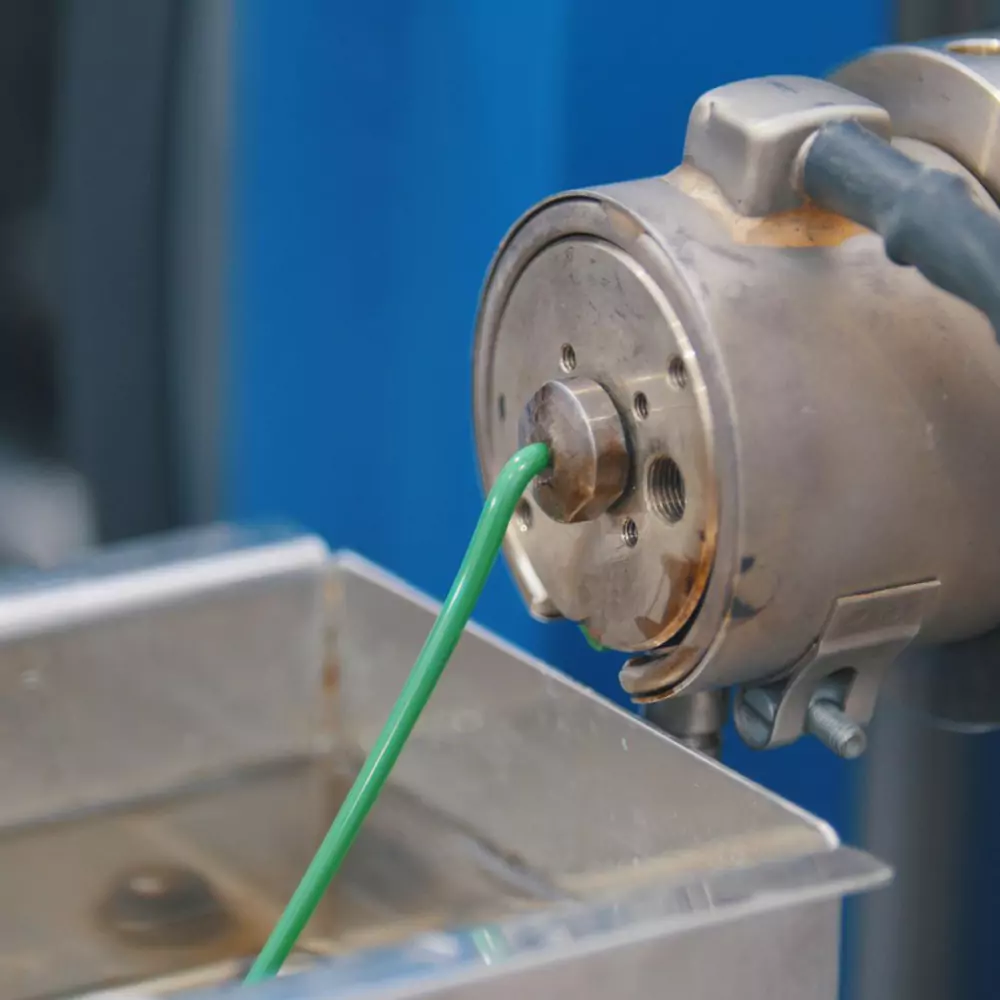
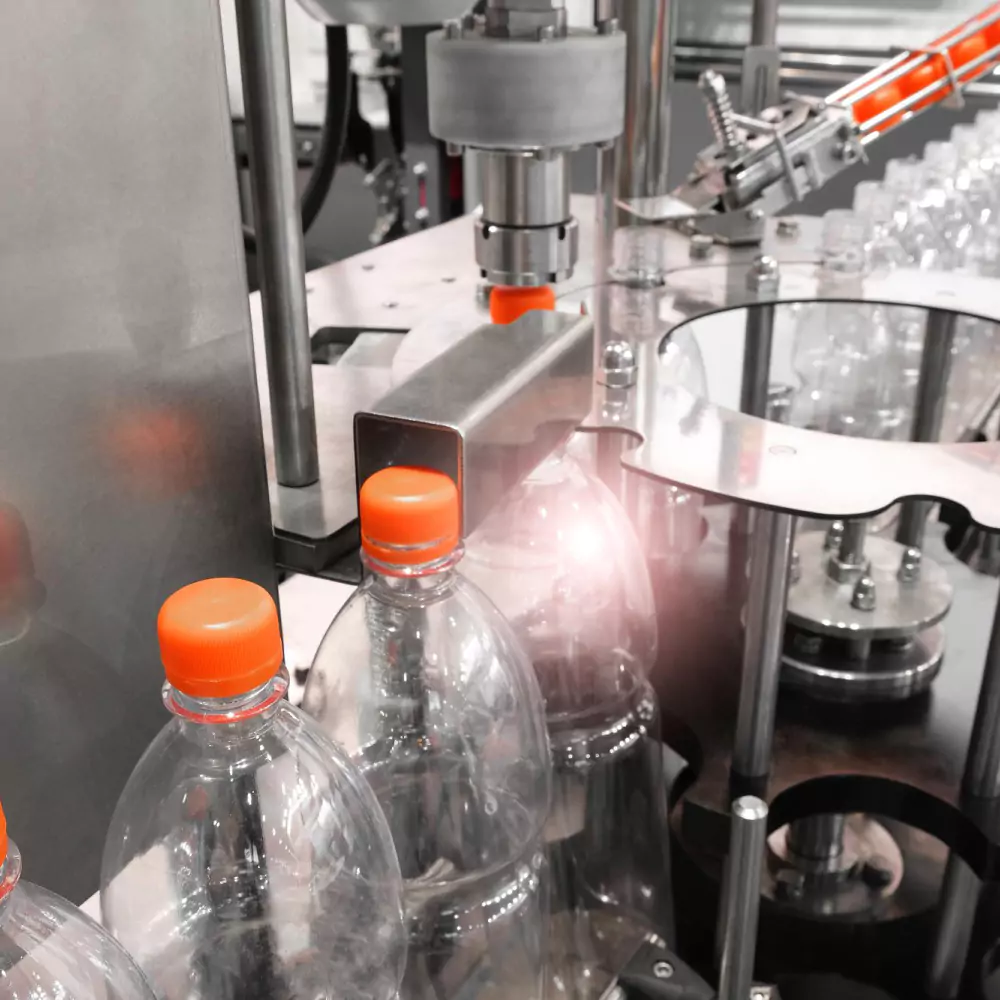
However, the choice of process is not just about the product's shape or size; it also involves considerations like material properties, production volume, and cost-efficiency. For instance, blow molding is perfect for producing high-volume hollow objects like bottles, but if your product requires high tensile strength or impact resistance, materials like Polycarbonate (PC) used in injection molding might be more appropriate.
By understanding the specific requirements of your project, we at Align MFG guide you through selecting the most suitable manufacturing process. Our expertise ensures that whether you need mass production or a custom, one-off piece, the chosen process will deliver the best possible results in terms of quality, cost, and time-to-market.
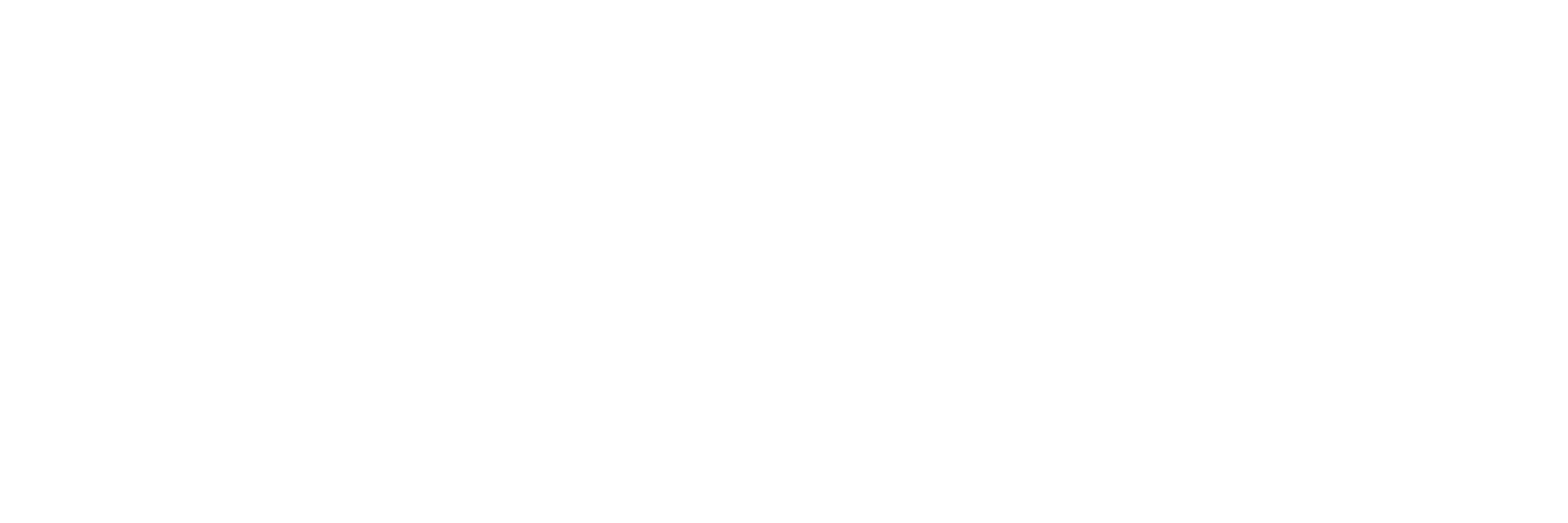
Why Choose Align MFG?
Our commitment to quality and cost efficiency sets us apart. We work closely with our clients through each project stage, providing expert guidance throughout the manufacturing processes. Our facilities across Southeast Asia and our experienced team ensure that your plastic components are produced to the highest standards, meeting the demands of your industry.
At Align MFG , we are dedicated to delivering top-tier plastic components that drive your business forward. Our comprehensive range of materials and processes ensures that we can meet any challenge, no matter how complex.
Contact us today to discuss your plastic manufacturing needs and discover how we can help you achieve your goals.