Align Manufacturing, we specialize in manufacturing silicone components outside of China, leveraging our trusted network of factories across Southeast Asia, including Vietnam, India, and Thailand.
Our deep expertise in managing the entire production process ensures high-quality products delivered on time and within budget.
Brief Overview
To produce high-quality silicone, the process begins with the careful selection of raw materials. The primary raw material is metallurgical-grade quartz or gravel, which consists of about 99.5% silica. This material is blended with a carbon source and heated in an electric furnace at around 1800°C. This high-temperature process, known as a reduction process, removes oxygen from the silicon dioxide, resulting in silicon and carbon monoxide. The silicon obtained can be in powder or liquid form and serves as the foundational element for all silicone products. This step is crucial for ensuring the purity and performance of the final silicone material.
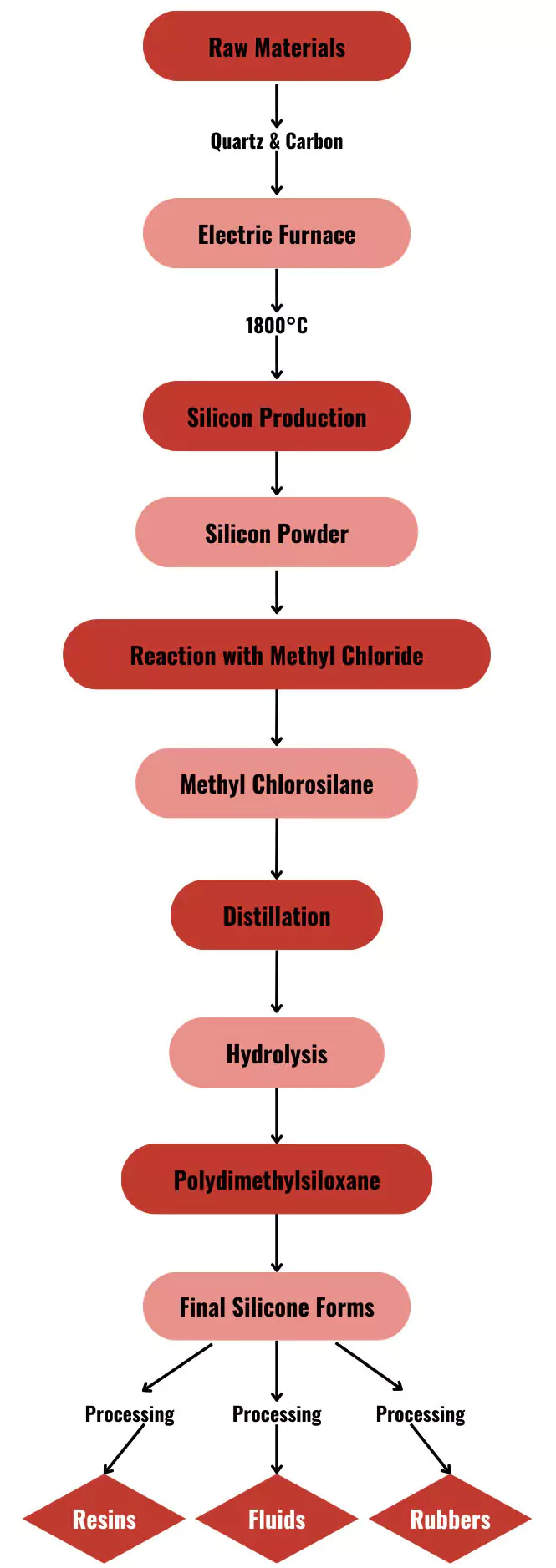
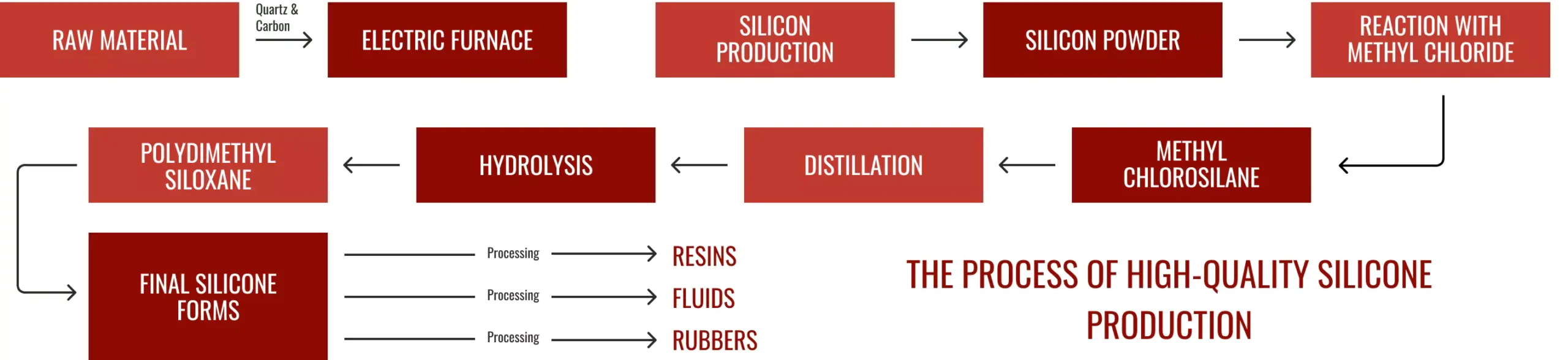
Once silicon is produced, it undergoes further chemical processes to create silicone. This involves reacting silicon powder with methyl chloride to produce methyl chlorosilane, a critical compound in silicone production.
Through a distillation process, the mixture is separated into various chlorosilanes, and then hydrolyzed to produce polydimethylsiloxane. This compound forms the backbone of silicone, with the siloxane bonds giving silicone its unique properties. Depending on the required grade and application, this polymer can be processed into different forms, such as resins, fluids, or rubbers, each with specific characteristics tailored for various industrial applications.
Silicone Manufacturing Processes

Compression Molding
Compression molding is a time-tested process used to produce high-volume silicone parts. In this method, pre-measured amounts of silicone are placed into a heated mold cavity. The mold is then closed, and pressure is applied to shape the silicone into the desired form. This process is particularly effective for producing robust and durable components like gaskets and seals, which require precise dimensional stability and excellent mechanical properties.
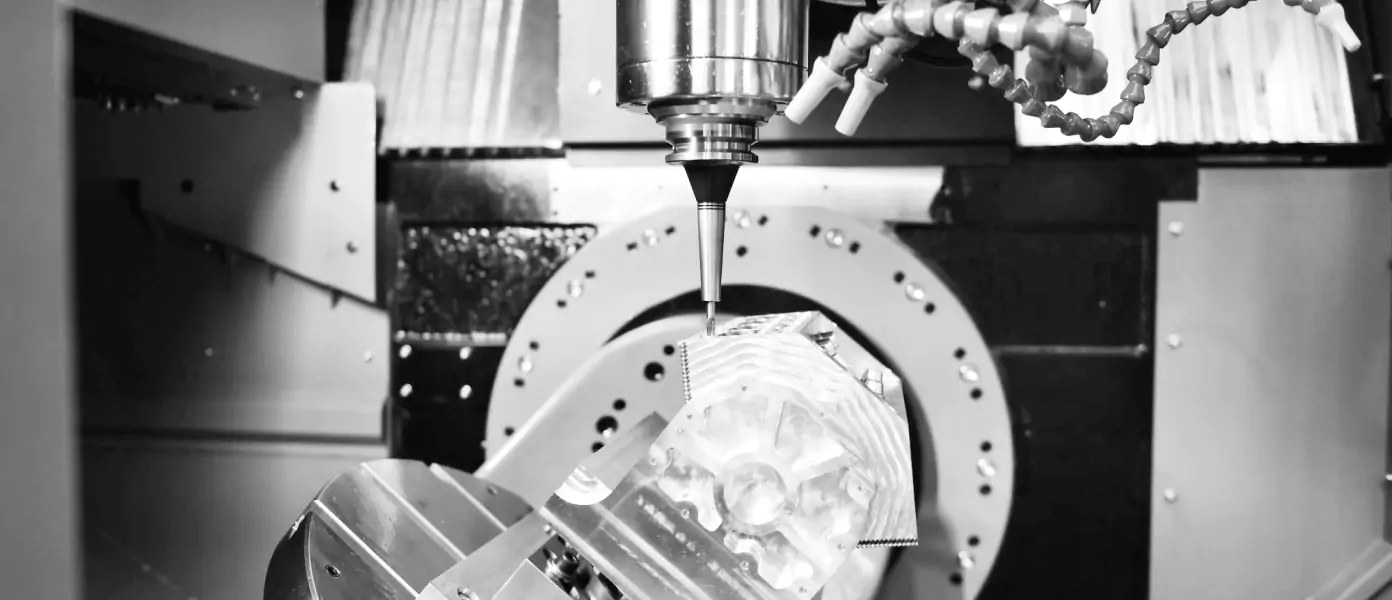
Liquid Injection Molding (LIM)
Liquid Injection Molding (LIM) is a cutting-edge process ideal for high-precision silicone parts. In LIM, liquid silicone rubber (LSR) is injected into a mold under high pressure. The process is highly automated, making it suitable for producing complex and intricate parts with tight tolerances. LIM is especially advantageous for manufacturing medical-grade components due to its ability to produce clean, consistent, and high-quality parts in a controlled environment.
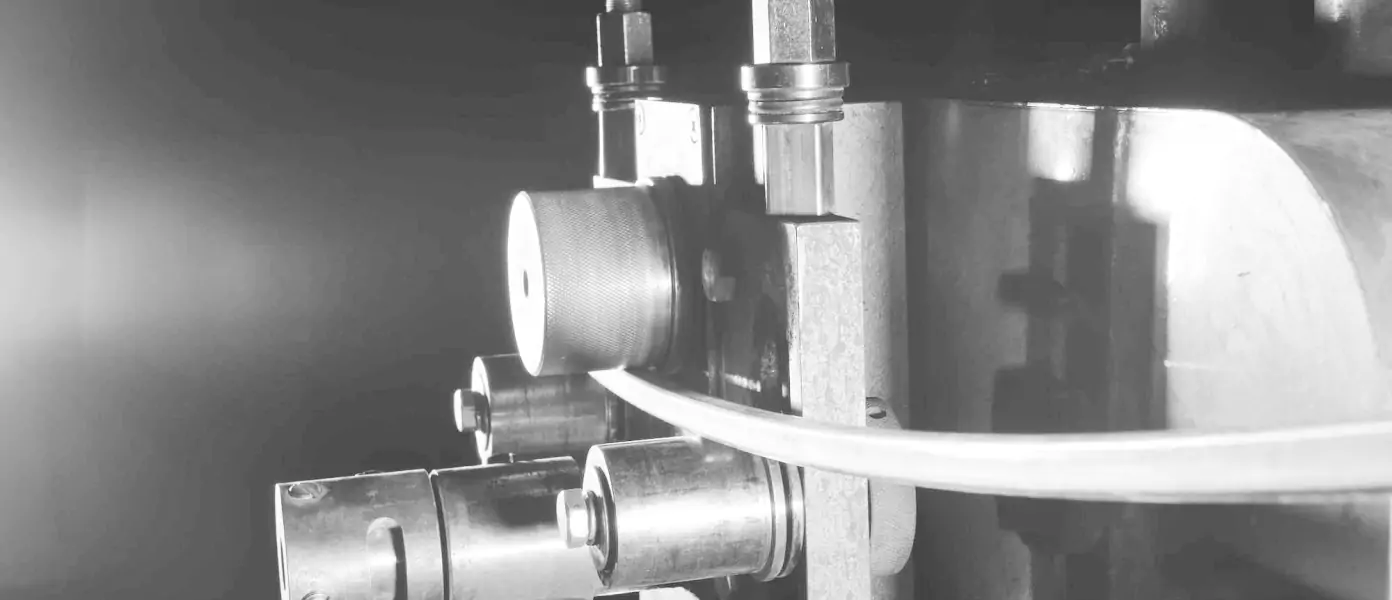
Extrusion Molding
Extrusion molding is used to create continuous lengths of silicone products, such as tubes, cords, and profiles. In this process, silicone is forced through a die of the desired cross-sectional shape and then cured. Extrusion molding is highly efficient for producing parts that need to be cut to length, offering excellent material consistency and uniformity.
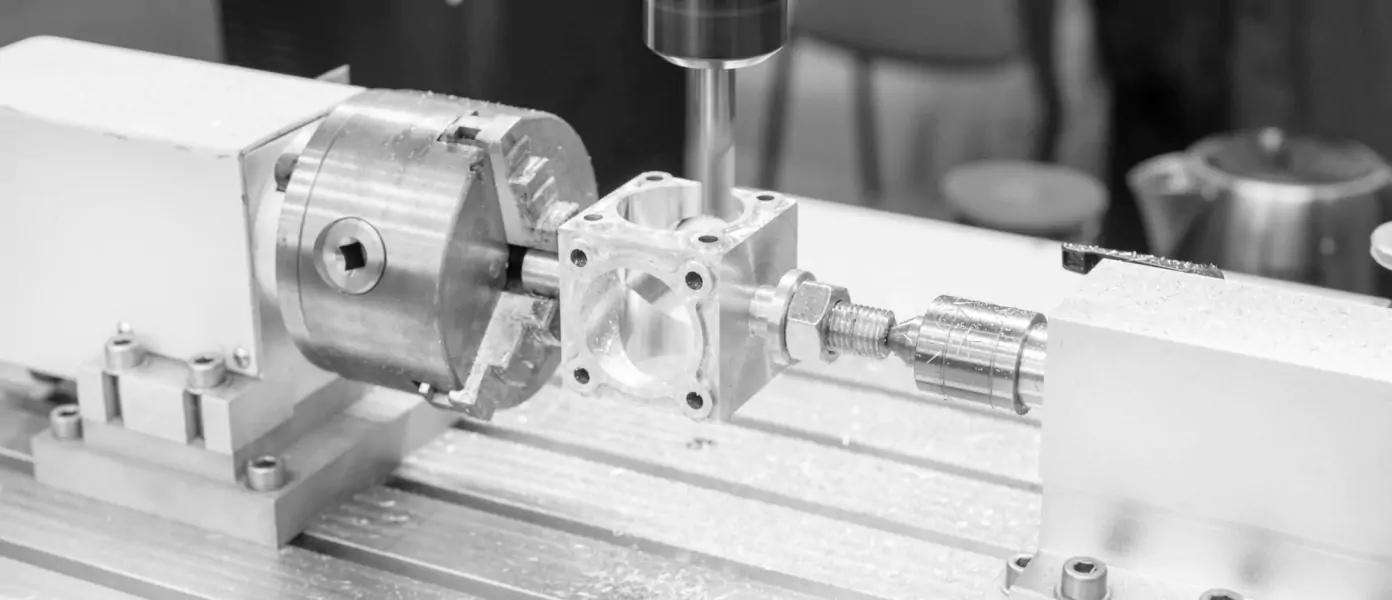
Overmolding
Overmolding involves bonding silicone to another material, such as metal or plastic, to create a composite part. This process is critical in applications where different materials need to work together seamlessly, such as in medical devices or automotive components. Overmolding enhances the functionality of the final product by combining the unique properties of silicone with those of other materials.
Popular Silicone Parts
Seals
Silicone seals are essential components in various industries, including automotive, aerospace, and electronics, where they provide reliable sealing against environmental factors like moisture, dust, and extreme temperatures. Align MFG specializes in producing silicone seals that meet stringent industry standards, ensuring long-lasting performance and durability.
Gaskets
Silicone gaskets are widely used for their flexibility, resilience, and ability to maintain a seal under high-pressure conditions. These gaskets are ideal for applications in harsh environments, such as engines, machinery, and electronic enclosures. Our expertise in silicone gasket manufacturing ensures products that deliver superior sealing capabilities and withstand prolonged exposure to chemicals, heat, and UV radiation.
Bushings
Silicone bushings are used to reduce vibration, noise, and wear in machinery and automotive applications. The material’s elasticity and resistance to environmental factors make silicone bushings a preferred choice for applications requiring reliable performance under dynamic conditions. We produce high-quality silicone bushings tailored to the specific requirements of each application, ensuring optimal functionality and longevity.
Bellows
Silicone bellows are flexible connectors that protect mechanical systems from contaminants and compensate for misalignment or movement between parts. These components are essential in applications where flexibility, durability, and environmental resistance are critical, such as in the medical, industrial, and automotive sectors. Our silicone bellows are designed to provide exceptional performance and durability, even in the most demanding conditions.
Plugs
Silicone plugs are used in a wide range of applications, from medical devices to industrial equipment, where they provide reliable sealing and protection. The material’s non-reactive nature and ability to withstand sterilization processes make silicone plugs ideal for medical and laboratory environments. Align MFG manufactures silicone plugs that meet stringent quality standards, ensuring safe and effective use in critical applications.
Silicone Materials
Why Choose Align Manufacturing?
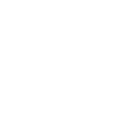
Cost-Effective and Reliable
By sourcing outside of China and leveraging our network of factories in Vietnam, India, and Thailand, we offer cost-effective manufacturing solutions without compromising on quality. Our reliable supply chain and efficient project management processes ensure that your products are delivered on time and within budget.
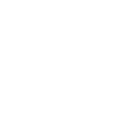
Proven Track Record
Align MFG has a proven track record of delivering high-quality silicone components for a wide range of industries, including oil and gas, railway, construction and more. Our ability to meet tight tolerances, handle complex projects, and deliver consistent quality has earned us the trust of clients worldwide.
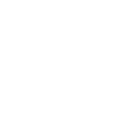
Expertise and Experience
With over 10 years of experience in managing silicone, plastic and metal manufacturing projects across Southeast Asia, Align MFG is a trusted partner for companies seeking high-quality industrial components. We have a deep understanding of the manufacturing processes and the specific requirements of different industries, allowing us to deliver customized solutions that meet your exact needs.
Ready to start your next silicone manufacturing project? Contact Align MFG today to discuss your requirements and discover how we can provide the reliable products you need. Fill out the contact form below, and our team will get back to you promptly to discuss your project in detail.