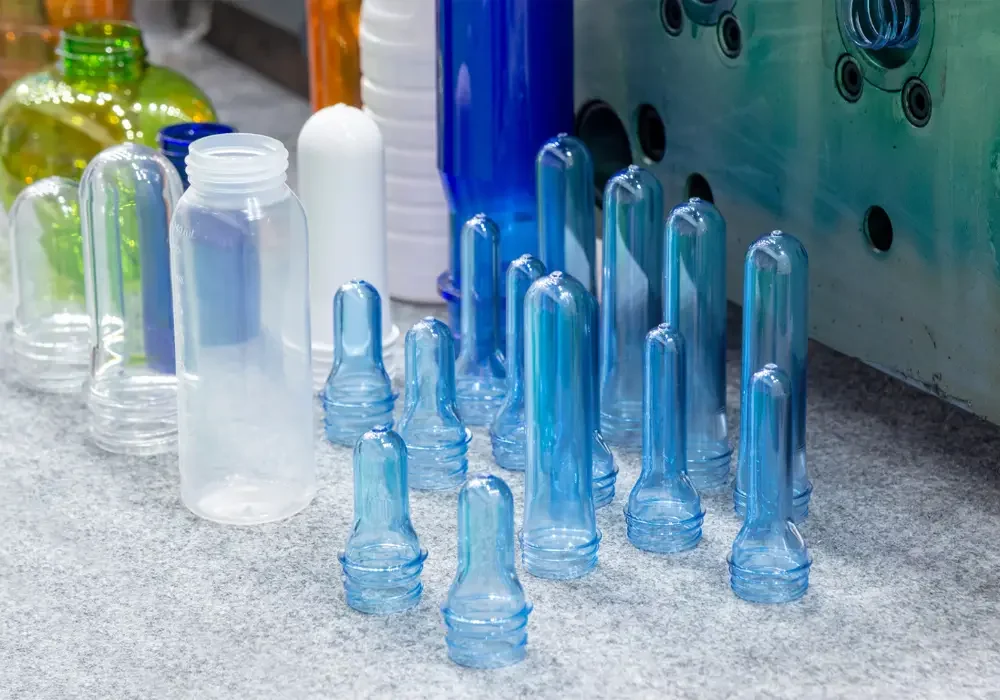
What sets us apart? Our ability to work with advanced materials, our integration of complex assemblies, and our deep understanding of overmolding and insert molding. With our cutting-edge technology, a vast range of materials, and a commitment to quality, we stand out as the go-to partner for all your injection molding needs.
The Plastic Injection Molding Process
At AlignMFG, we harness the power of injection molding to create durable, high-precision parts. Here’s how we do it:
- Design Collaboration: Our engineers work closely with you to design the perfect mold for your part, ensuring that every detail meets your specifications.
- Material Selection: We guide you in choosing the best materials based on your product’s requirements, balancing performance, durability, and cost.
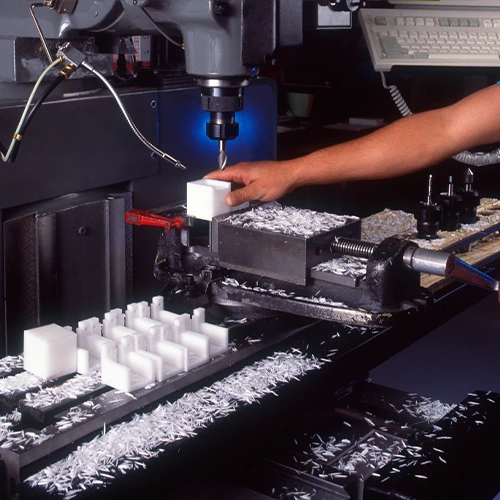
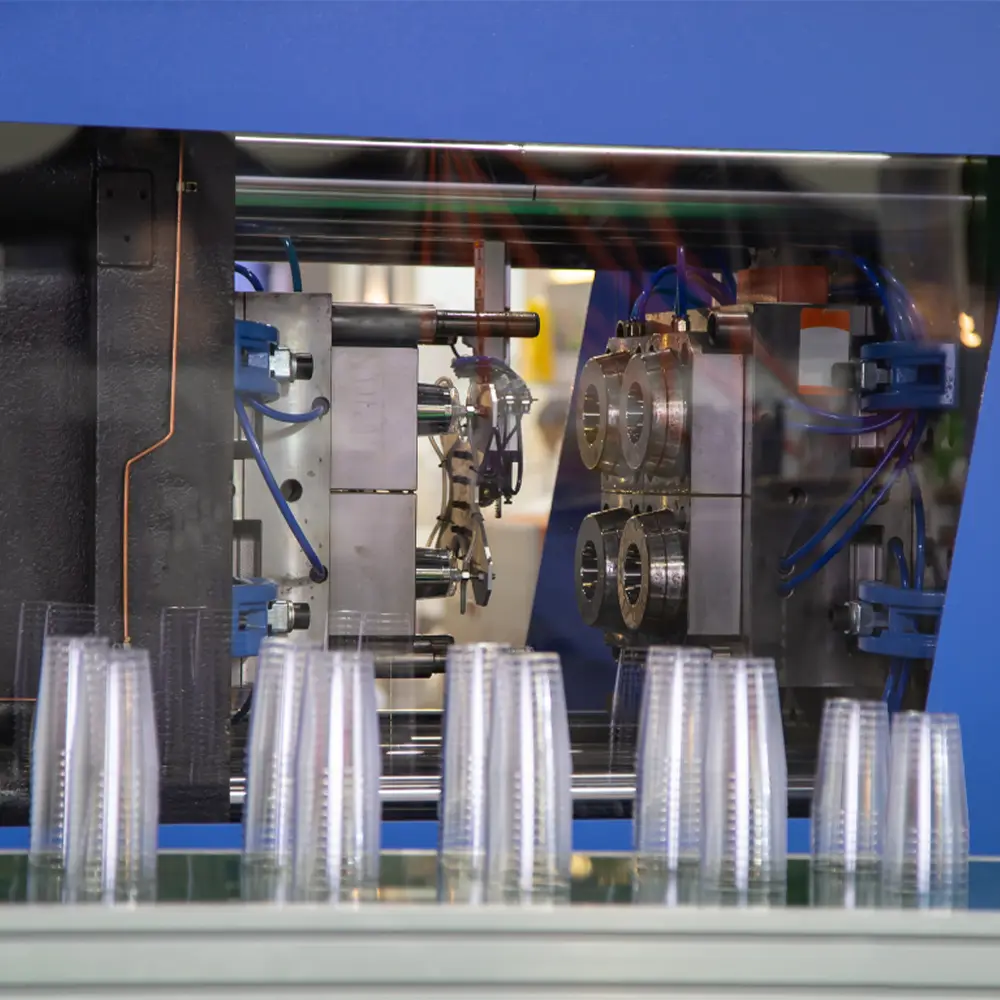
- Mold Fabrication: Using state-of-the-art machinery, we fabricate high-precision molds that guarantee consistent quality with every production run.
- Injection Molding: With our advanced injection molding machines, we inject molten material into the molds, rapidly cooling and solidifying them into the desired shape.
- Quality Assurance: Every part undergoes rigorous testing to ensure it meets our strict quality standards before it reaches your hands.
Materials We Work With
We specialize in a broad spectrum of plastics, each selected for its unique properties:
- PP (Polypropylene)
- PS (Polystyrene)
- PPS (Polyphenylene Sulfide)
- PC (Polycarbonate)
- PC-ABS (Polycarbonate-Acrylonitrile Butadiene Styrene)
- ABS (Acrylonitrile Butadiene Styrene)
- PA66 (Nylon 66)
- POM (Polyoxymethylene)
- SAN (Styrene Acrylonitrile)
- PET (Polyethylene Terephthalate)
- PBT (Polybutylene Terephthalate)
- PEI (Polyetherimide)
- PVC (Polyvinyl Chloride)
- PA (Nylon)
- HDPE (High-Density Polyethylene)
Specialty Materials:
We take pride in our ability to work with advanced materials like UHMW (Ultra-High-Molecular-Weight Polyethylene) and glass-filled nylon. These materials offer superior strength, wear resistance, and durability, making them ideal for demanding applications.
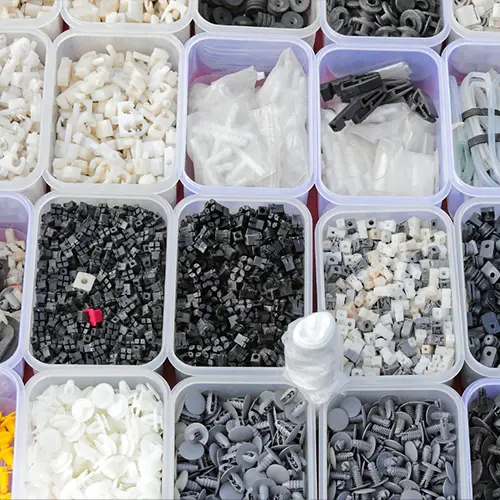
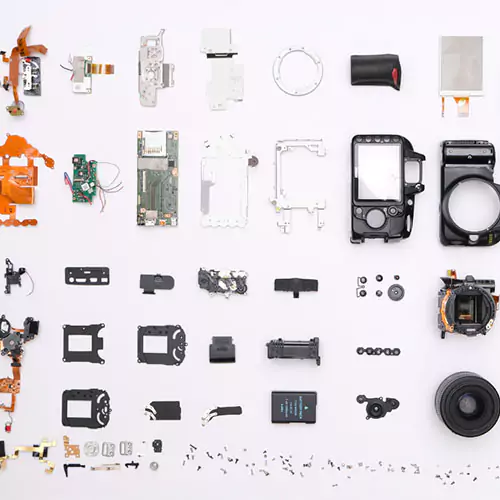
Assembly Capabilities
Our expertise extends beyond molding parts; we excel in integrating these components into larger assemblies. Whether it’s a complex multi-part product or a simple two-piece assembly, our injection molding process is designed to seamlessly fit into your overall production strategy.
We ensure that each part is precisely engineered to integrate smoothly, reducing the time and cost associated with post-molding assembly.
The Benefits of Choosing AlignMFG
Choosing AlignMFG for your injection molding needs comes with a host of benefits:
- Quality & Precision: Our advanced machinery and rigorous quality controls ensure every part meets the highest standards.
- Cost-Effectiveness: Our process is designed to minimize waste and reduce costs, offering you the best value for your investment.
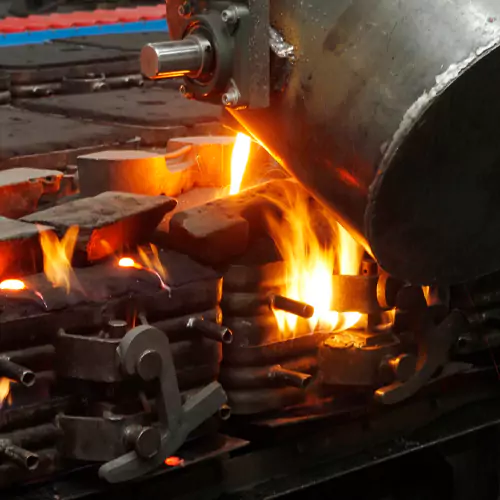
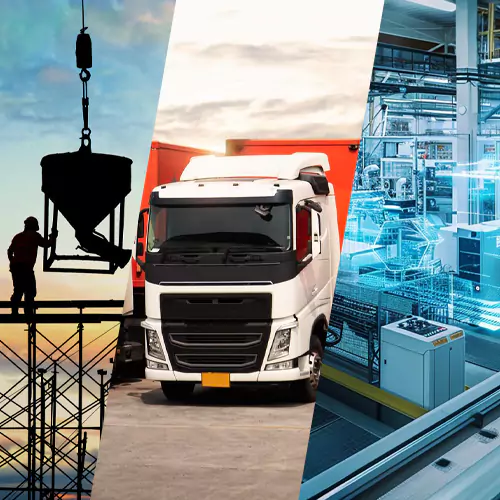
- Construction: Robust, high-performance components built to endure the tough demands of construction projects.
- Truck & Trailer: Reliable parts that deliver long-lasting performance in heavy-duty applications.
- Industrial: Versatile, high-strength components tailored for a wide range of industrial applications.
FAQ
Plastic injection molding is ideal for mass production due to its ability to quickly produce consistent, high-quality parts with minimal waste. Once molds are created, the process has a rapid cycle time, allowing for thousands or even millions of identical parts to be produced efficiently, making it highly cost-effective for large volumes.
Common materials include polypropylene (PP), polyethylene (PE), polycarbonate (PC), ABS, and nylon. Each material offers unique properties: polypropylene is flexible and durable, polycarbonate is impact-resistant, ABS provides good rigidity and toughness, and nylon offers high wear resistance. The choice of material affects durability, with some options providing better resistance to heat, chemicals, and physical stress.
Injection molding uses high-pressure injection to push molten plastic into molds that capture intricate designs and fine details. Advanced mold-making techniques and multi-part molds allow for complex shapes with precise tolerances, producing detailed features and accurate dimensions, even in highly complex components.
The initial cost of mold creation is offset by the low per-part production cost in large-scale projects. Once molds are made, production is fast and requires minimal labor, making it extremely economical for high-volume production. Additionally, minimal material waste and consistent quality reduce costs further over large runs.
Plastic injection molding can be sustainable, especially with options to use recycled plastics in production. Additionally, the process generates minimal waste, as excess material from each mold can often be re-ground and reused. Advances in biodegradable and bio-based plastics are also improving the environmental footprint of injection molding.
Choose Align MFG for Shell Molding
At AlignMFG, we are dedicated to providing injection molding solutions that enhance the performance and reliability of products across these key industries.