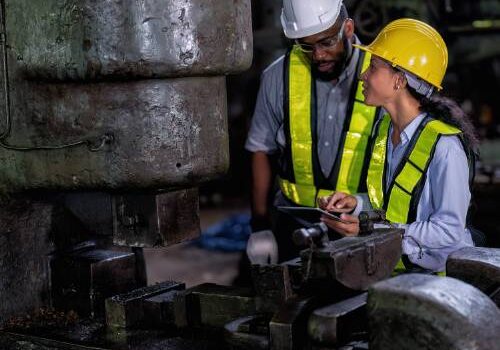
Our shell molding process stands out for its precision, efficiency, and ability to handle intricate designs and complex molds. This casting technique is especially beneficial in the production of critical components like cylinder heads for the truck and trailer industry, where precision and reliability are paramount in the United States and beyond.
Why Shell Molding?
Shell molding is renowned for its high dimensional accuracy and excellent surface finish, making it ideal for complex geometries that are challenging to achieve with traditional casting methods. This process is particularly effective for manufacturing components that must withstand high temperatures and pressures, such as cylinder heads in heavy-duty vehicles.

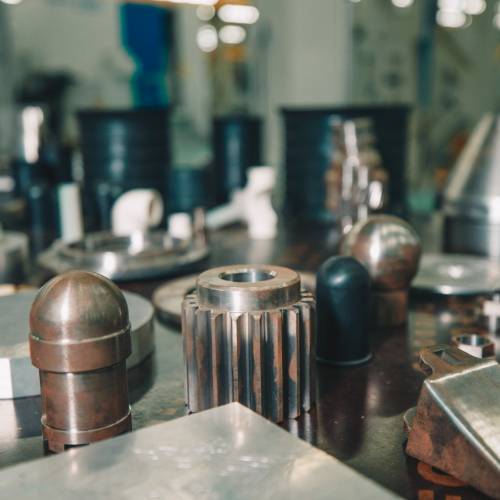
Our Shell Molding Capabilities
- Complex Design Handling: Our technology allows for the manufacture of detailed, intricate designs and complex molds that are not only robust but also consistent in quality.
- Material Versatility: We utilize a variety of metals in our shell mold casting process, including carbon steel, iron, and stainless steel, ensuring that we can meet diverse industry needs and material specifications.
- Precision and Quality: Each shell molded part undergoes rigorous quality control, ensuring that every component meets our high standards and your exact requirements.
Benefits of Shell Molding with Align MFG
- Superior Surface Quality: Achieves smooth surfaces that often require no further finishing, reducing overall production time and cost.
- Enhanced Dimensional Accuracy: Provides tight tolerances that are crucial for complex components like cylinder heads.
- Increased Durability: Produces parts that are robust and durable, ideal for the demanding environments of truck and trailer applications.
Application in Truck and Trailer Manufacturing
Our shell molding process is particularly valuable in producing cylinder heads that are critical for the performance and longevity of truck and trailer engines. By leveraging shell molding, we can handle the demanding specifications required for these components, ensuring optimal engine performance and reliability.
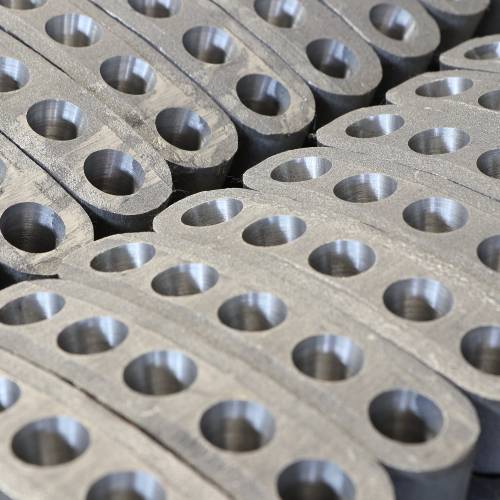
FAQ
Shell molding is a casting process that uses a thin, hardened shell mold made from a mixture of sand and resin. It’s chosen for precision casting because it produces high accuracy and smooth surface finishes, making it ideal for parts requiring fine detail and tight tolerances.
Metals like steel, cast iron, aluminum, and copper alloys are commonly used in shell molding. Steel and cast iron provide excellent strength and durability, making them suitable for high-stress applications, while aluminum offers a lightweight option. These metals work well with the shell molding process, resulting in high-quality parts with smooth finishes and strong mechanical properties.
Shell molding uses a hardened resin-sand mixture to form precise, thin molds that capture intricate details and complex shapes. The molds are rigid and hold their form well, allowing molten metal to fill small cavities accurately, producing parts with complex geometries and fine details.
Shell molding offers better dimensional accuracy, smoother surface finishes, and the ability to capture fine details compared to traditional sand casting. It also has a faster production cycle and requires less post-casting machining, making it more efficient and suitable for higher-quality, precision components.
Industries such as automotive, aerospace, and industrial machinery commonly use shell molding. It’s ideal for applications that require precision components like gear housings, engine parts, and brackets, where strength, durability, and intricate designs are critical for performance and reliability.
Choose Align MFG for Shell Molding
Opt for Align MFG’s shell molding services to benefit from our capabilities in handling complex designs and producing high-quality, durable components. Whether you are in the automotive sector needing cylinder heads or another industry requiring precision cast metal parts, we are equipped to meet your needs efficiently and effectively.
Contact Align MFG today to discuss your project, or request a quote directly through our form.