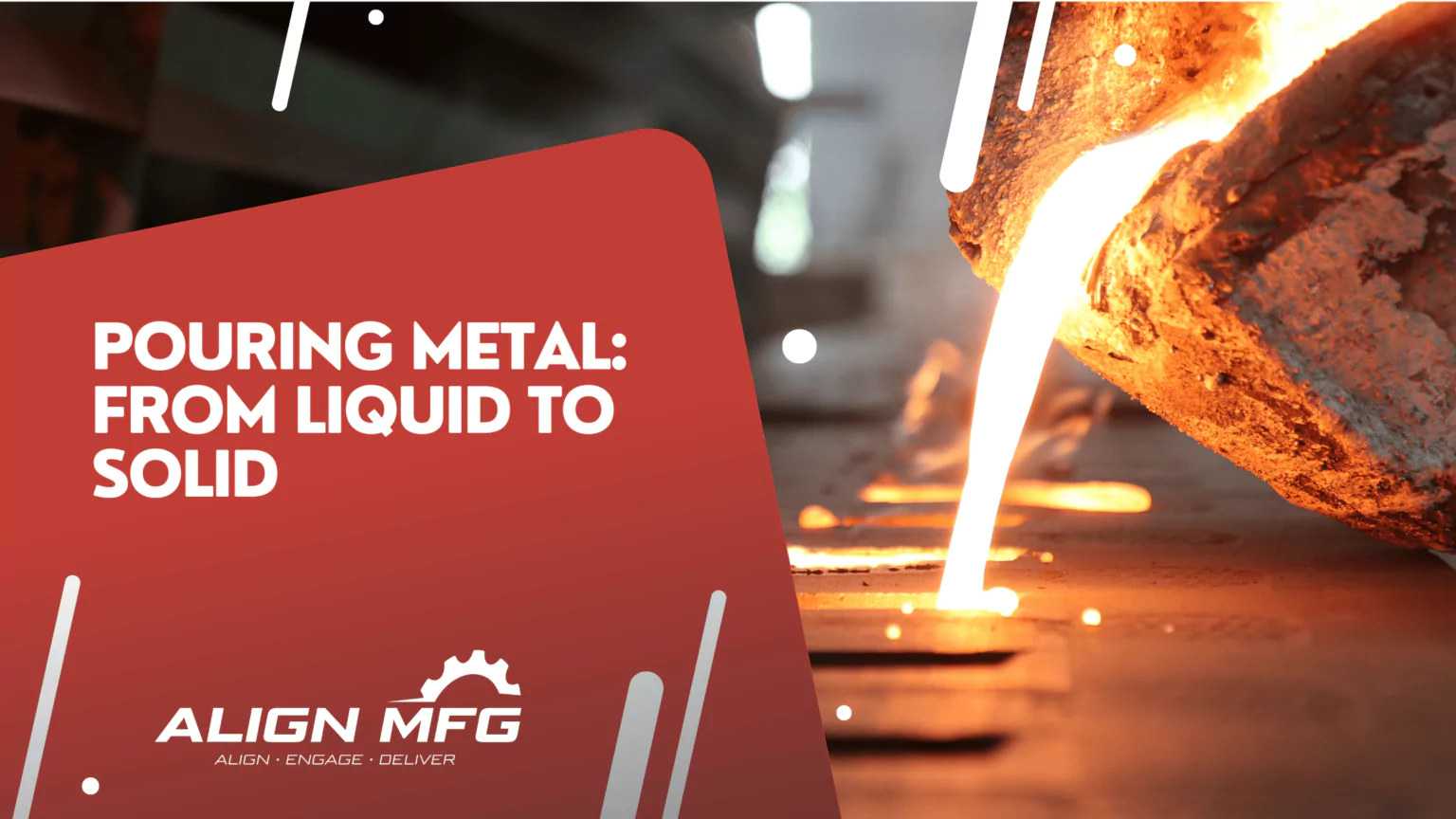
Pouring Metal: From Liquid to Solid
The transformation of molten metal into a solid form is both a critical and captivating phase in the sand casting process. This stage is where the preparatory work of pattern making and mold preparation converges with the alchemy of metalwork. Let’s explore the intricacies of pouring metal, focusing on preparation, techniques, and considerations crucial to achieving a defect-free casting.
Preparing for Pouring: Checking Metal Temperature and Mold Readiness
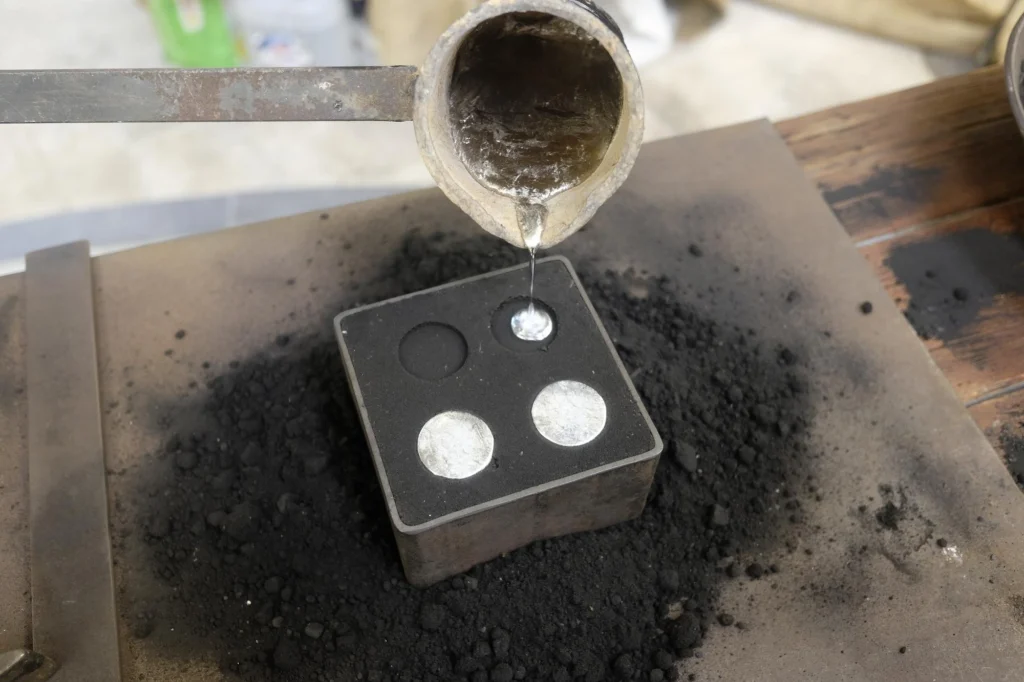
Before the molten metal is introduced into the mold, two pivotal checks must be performed: ensuring the metal is at the correct temperature and confirming the mold’s readiness.
- Metal Temperature: The temperature of the molten metal is crucial for a successful pour. If the metal is too hot, it may cause unwanted reactions with the mold material or result in defects like gas porosity. If too cold, the metal might solidify before filling the entire mold cavity. Using a pyrometer, the temperature is precisely measured to align with the specific metal’s ideal pouring range.Use pyrometers to ensure optimal pouring temperature (700-750°C for aluminum, 1,200-1,400°C for iron)
- Mold Inspection: Check for moisture, contaminants, and structural integrity
- Mold Readiness: The mold must be dry and free of contaminants. Moisture can cause steam explosions, while dirt or debris can lead to surface defects in the final casting. The mold’s integrity is inspected to ensure it can withstand the thermal shock of the molten metal without collapsing or cracking.
Techniques and Tools for Pouring: Ladles, Pouring Basins, Gates, and Runners
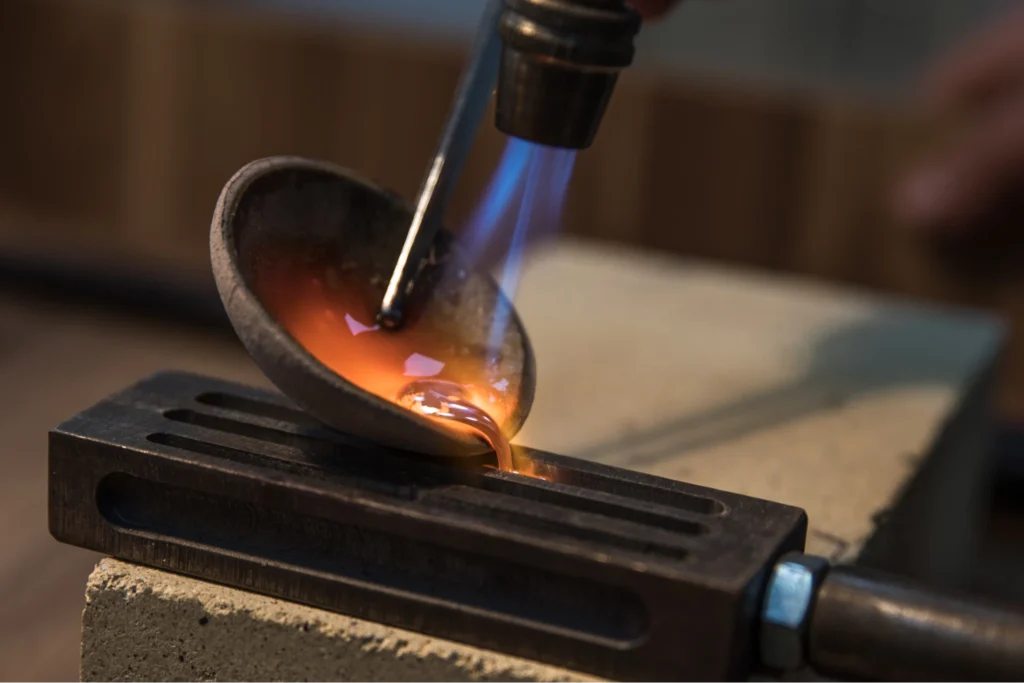
The actual pouring of the metal requires skill and the right tools to direct the molten metal from the furnace to the mold cavity efficiently.
- Ladles: These are the primary tools for transporting and pouring molten metal. They range from simple hand-held devices for small quantities to mechanically operated ladles for large volumes, ensuring precise control over the pour.
- Pouring Basins: A funnel-shaped reservoir at the top of the mold that receives the molten metal from the ladle. It helps in minimizing splashing and directs the flow into the mold’s gating system.
- Gates and Runners: These are channels carved into the sand mold that guide the molten metal from the pouring basin to the mold cavity. Proper design of gates and runners is vital to control the flow speed and reduce turbulence.
Considerations to Avoid Defects: Turbulence, Air Entrapment, and Temperature Control
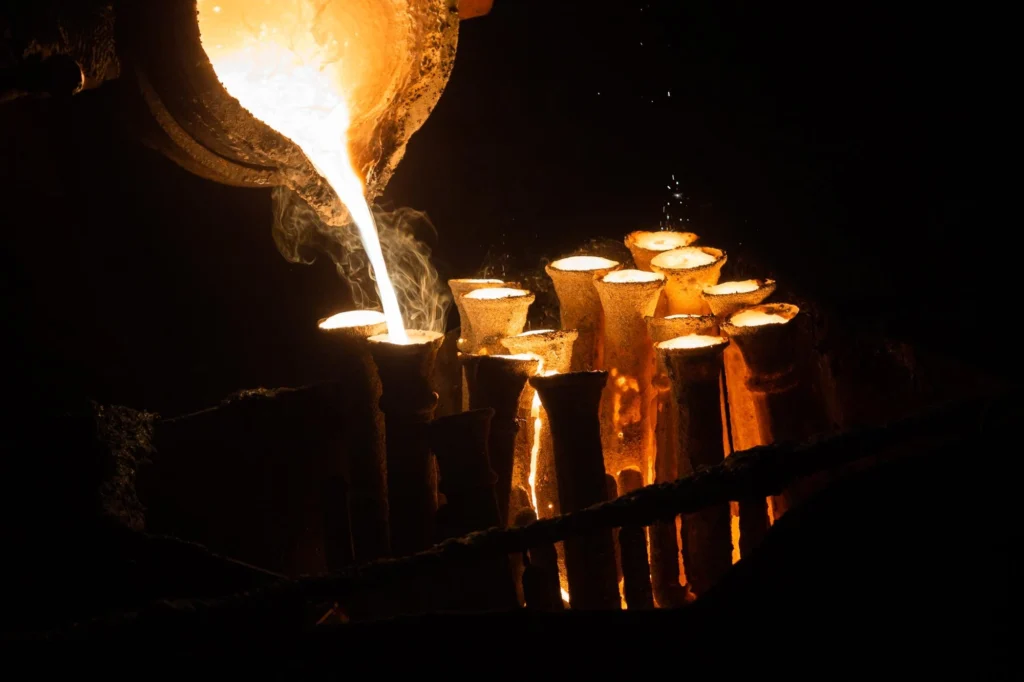
The way metal is poured can significantly impact the quality of the casting. Here are key considerations to mitigate common defects:
- Turbulence: A gentle and controlled pour is essential to prevent the molten metal from splashing and creating turbulence as it enters the mold. Turbulence can lead to air entrapment and oxide formation, compromising the casting’s integrity.
- Air Entrapment: Strategic placement of vents in the mold allows gases to escape as the molten metal fills the cavity. Ensuring an uninterrupted flow of metal helps in minimizing air pockets or voids in the final casting.
- Temperature Control: Besides the initial temperature check, maintaining an optimal temperature gradient during the pour is crucial. Too rapid cooling can lead to cold shuts (where liquid metal streams don’t fuse properly), while too slow can cause shrinkage cavities as the metal solidifies.
Mold Coatings for Improved Casting Quality
Mold coatings enhance surface finish and reduce casting defects:
- Types of Coatings:
- Graphite-based coatings: For smoother surfaces.
- Zircon-based coatings: High thermal resistance for larger or complex molds.
- Applications: Applied as a wash or spray before pouring to create a non-reactive layer between molten metal and sand.
This reduces surface roughness and minimizes metal-sand reactions.
Metal Fluidity and Flow Analysis
The fluidity of molten metal determines how well it fills the mold cavity without defects.
- Factors Affecting Fluidity:
- Pouring temperature (higher improves flow but risks oxidation).
- Mold material and surface smoothness.
- Metal composition: Alloys behave differently in terms of viscosity.
- Flow Simulation Software: Modern software tools predict how molten metal will flow, ensuring optimal gating and riser design.
Automation and Technology in Melting and Pouring
Advancements in foundry technology have streamlined the melting and pouring stages, improving safety, precision, and efficiency.
Technologies Enhancing Melting and Pouring:
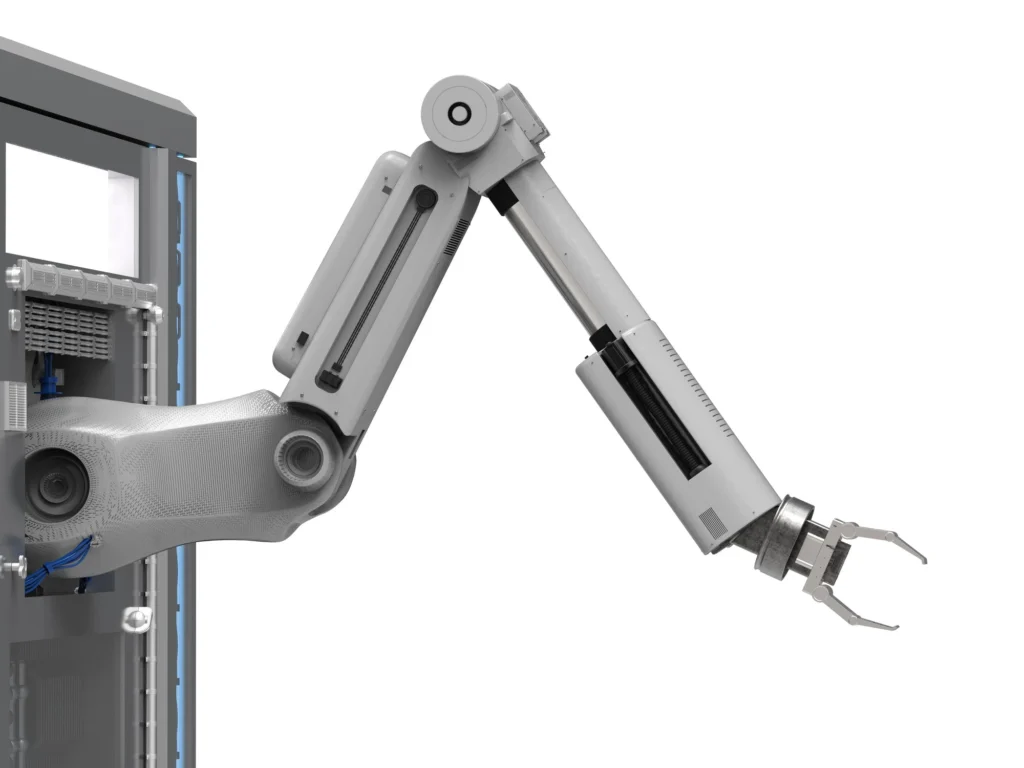
- Robotic Ladle Pouring: Ensures consistent and controlled pouring while reducing human error.
- IoT Sensors: Real-time temperature and quality monitoring optimize performance.
- Automated Furnace Controls: Maintain precise melting temperatures with minimal energy loss.
- Simulation Software: Predict and resolve defects before the casting process begins.
Automation reduces waste, enhances repeatability, and boosts productivity for modern foundries.
Mastering the pour is a delicate balance between art and science, requiring attention to detail, precision, and timing. When executed correctly, it culminates in the magical moment where molten metal begins its transformation into a solid, embodying the desired shape and properties embedded in the sand mold. This phase is not just about transferring metal from one container to another; it’s about ensuring the integrity, quality, and success of the casting through meticulous preparation and execution.