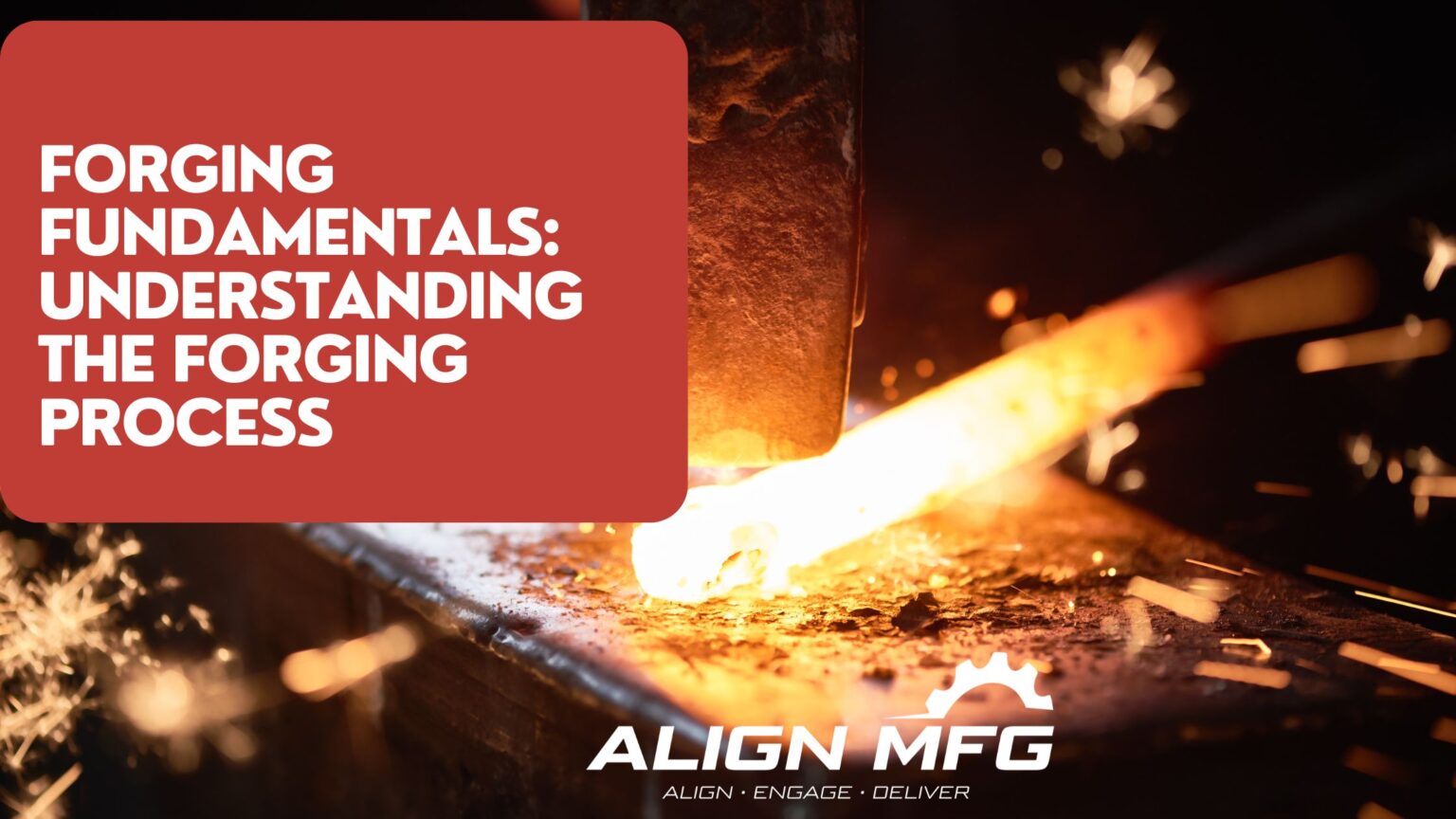
Forging Fundamentals: Understanding the Process
What is Forging?
Forging is a process that involves shaping or forming materials, usually metal, through the application of heat and pressure. This process alters the material’s shape and structure, making it stronger and more durable. Forging is commonly used in manufacturing industries to create tools, machine parts, and various metal products.
How does the forging process enhance the mechanical properties of metal?
Forging strengthens metal by refining its internal grain structure and eliminating defects. During the forging process, the grains within the metal are deformed and realigned in the direction of the applied force, which helps improve its strength and toughness as the grain structure conforms to the new shape. The compression involved in forging also densifies the material, reducing voids and air pockets that can weaken the metal. Additionally, the repeated hammering or pressing causes work hardening, where the internal structure becomes more compact and resistant to deformation. This process also helps remove impurities or defects within the metal, creating a more uniform and robust material, ideal for demanding applications like automotive and aerospace industries.
Metals suitable for forging
The best metal for forging depends on the specific application and desired properties, but some of the most commonly used metals for forging include:
1. Steel: Steel is the most popular metal for forging because it’s strong, easy to work with, and widely available. Different types of steel, like carbon steel and stainless steel, are used based on whether strength or rust resistance is more important.
2.Aluminum: Aluminum is lightweight and easy to forge, making it a good choice for industries like aerospace and car manufacturing. It’s also resistant to rust and corrosion.
3. Titanium: Titanium is very strong and lightweight, making it great for high-performance applications like aircraft and medical tools. However, it’s more expensive and harder to work with than steel.
4. Copper and its alloys (like bronze and brass): Copper and its alloys are softer and easy to shape. They are often used in electrical parts, plumbing, and decorative items because of their good conductivity and resistance to rust.
5. Nickel-based alloys: These metals are used in extreme environments, like jet engines or chemical plants, because they stay strong at high temperatures and resist corrosion.
Forging Equipment
Forge or furnace: This is used to heat the metal to the appropriate temperature for forging, making it soft enough to shape. Traditional forges burn coal, gas, or oil, while modern furnaces may use electric induction for precise temperature control.
Anvil: The anvil provides a hard surface on which the metal is placed while it is being hammered or shaped. It has a flat top and various edges and horns to help form different shapes.
Hammer: Hammers are used to strike the metal and shape it. These can be hand hammers for small-scale work, or power hammers for larger, more industrial processes. Power hammers deliver repeated heavy blows quickly, saving time and effort.
Tongs: Tongs are essential for holding and manipulating the hot metal while it’s being worked on. They come in various sizes and shapes to grip different types of material securely.
Die: Dies are molds used in closed-die forging. The heated metal is placed between two dies, which are then pressed together to form the metal into a specific shape. They are often used for producing consistent parts like gears or tools.
Quenching tank: After forging, the metal is often cooled quickly in a quenching tank filled with water, oil, or another cooling medium. This helps harden the metal and set its final shape.
Protective gear: Since forging involves high heat and heavy tools, safety equipment like heat-resistant gloves, aprons, face shields, and ear protection are necessary to protect the smith from burns, sparks, and loud noise.
Different types of forging
Open-Die Forging
Open-die forging is like traditional blacksmithing. A large piece of heated metal is placed on an anvil or between two flat dies, and it is hammered or pressed into shape. The dies don’t completely enclose the metal, so it can spread out freely, making this process flexible for creating large or irregularly shaped parts. The metal is hammered multiple times to gradually form the desired shape. Open-die forging is often used for big parts like shafts, rollers, and rings that need to be very strong.
Closed-Die Forging (Impression-Die Forging)
Closed-die forging, also known as impression-die forging, involves pressing heated metal between two molds (dies) shaped like the final product. The metal is forced to fill the die cavities, taking on the exact shape of the mold. This method is highly precise and can produce parts with detailed, intricate designs. It’s ideal for making smaller, high-volume parts like automotive gears, bolts, or connecting rods.
Roll Forging
Roll forging is a process where a heated metal bar or rod is passed through two rotating rolls. These rolls have grooved shapes that gradually reduce the thickness of the metal and lengthen it. Roll forging is used to create long, uniform parts like axles, tapered shafts, and leaf springs. This process is very fast and efficient for mass production.
Cold Forging
Cold forging takes place at or near room temperature. The metal is placed into a die and shaped using high pressure. Cold forging doesn’t require heating, which means it uses less energy and produces parts with a very smooth surface and high dimensional accuracy. Since the metal is not heated, it hardens during the forging process, increasing its strength. Cold forging is mainly used for small parts like screws, bolts, rivets, and other fasteners, often made from softer metals like aluminum or copper.
Hot Forging
Hot forging involves heating metal to a very high temperature (above its recrystallization point) before shaping it. When metal is heated, it becomes softer and more malleable, making it easier to form into complex shapes. This process is used to create both small and large parts, including bolts, engine components, and structural parts in the construction industry. Hot forging also helps improve the metal’s internal structure by refining the grain size, making the final product stronger and more durable.
Align MFG offers a range of forging services designed to meet diverse industry needs, ensuring high-quality components that prioritize strength and durability. Their expertise in forging is complemented by metallurgical services available outside of China, providing valuable insights and support to clients globally. This combination allows customers to benefit from not only precision manufacturing but also tailored metallurgical analysis, enhancing the overall quality and performance of their products. Contact us to learn more about how our forging and metallurgical services can support your specific needs.
FAQ
What is forging?
Forging is the process of shaping hot metal by hitting or pressing it. It’s similar to molding clay but with metal. This makes the metal stronger and gives it the desired shape for tools or machine parts.First, we heat the metal until it’s very hot. Then we hit or press the hot metal to change its shape. We use special tools or big machines to do this. This makes the metal very strong. People use forged metal to make things like car parts and construction gear.
What are the three types of forging?
The three main types of forging are
- Open-die forging: The metal is placed between two flat or simply shaped dies. It’s then hammered or pressed, allowing the metal to flow freely except where it contacts the dies.
- Closed-die forging: The metal is placed in a die resembling a mold of the desired final shape. It’s then compressed between two dies that contain the metal, forcing it to take the shape of the cavity.
- Roll forging: The heated metal is passed between two rotating rolls with semi-circular grooves. As the metal passes through, it’s shaped into a round or cylindrical form.
Why is forging used?
Forging is used because it strengthens metal by aligning its grain structure, making it more durable and resistant to wear. It also allows for precise shaping, which is essential for creating tools, machine parts, and other components that need to withstand heavy use.