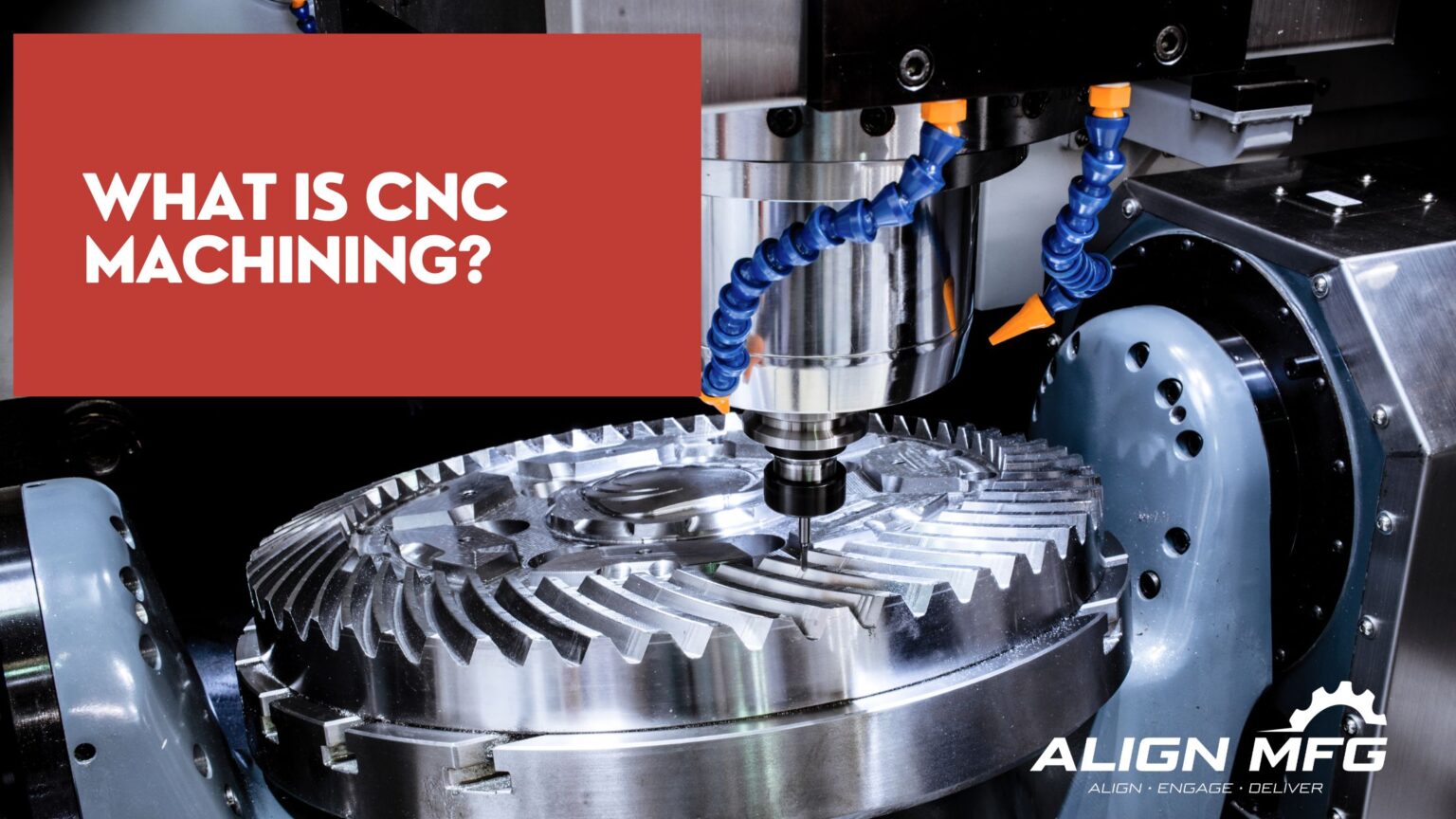
What is CNC Machining?
CNC (Computer Numerical Control) machines use command codes to control the movement of tools and machinery, enabling precise and automated operations. This process begins by creating a digital design using CAD software, which is then converted into a set of instructions that control the operation of the CNC machine. As a US-based manufacturing firm sourcing outside China, CNC machining is essential for ensuring high-quality, consistent parts. Whether through CNC milling in China, or China CNC machining parts, the global availability of CNC services ensures efficient manufacturing.
The key benefits of CNC machines include automation, which allows them to operate without manual intervention; precision, ensuring they can create complex parts with tight tolerances; and consistency, guaranteeing each part is identical, crucial for mass production. Whether producing components for cars, airplanes, or intricate molds, CNC machines form the backbone of modern American manufacturing by delivering reliable and repeatable results that improve both efficiency and quality.
How Do CNC Machines Work?
CNC machines operate by following coded instructions, known as G-code, that tell the machine how to move its tools to perform specific tasks like cutting, drilling, or shaping materials. The process typically unfolds in five phases:
- Design Phase: A part is designed using CAD (Computer-Aided Design) software, creating a digital blueprint.
- Programming Phase: The design is converted into G-code using CAM (Computer-Aided Manufacturing) software, which provides the machine with instructions.
- Setup Phase: An operator secures the material (workpiece) and installs the necessary cutting tools.
- Machining Phase: The CNC machine automatically shapes the material as per the programmed instructions, performing tasks like cutting or drilling.
- Finishing Phase: After machining, additional processes like polishing or heat treatment are applied to meet the final specifications.
This process eliminates the need for manual operation, ensuring consistent, high-quality results with minimal human error, making CNC machining ideal for manufacturers in the U.S. who aim to compete globally, including sourcing CNC milling service China for specific projects.
The Versatility of CNC Machining
CNC machining offers unparalleled precision, versatility, and efficiency, making it ideal for a broad range of industries across the U.S. and worldwide. Here’s why CNC machining, including China CNC milling service, excels:
- Precision Manufacturing: CNC machining ensures tight tolerances and high accuracy, crucial for industries like aerospace, automotive, and medical devices where precise measurements are vital.
- Complex Part Production: CNC machines can easily handle intricate designs and complex geometries that would be difficult or impossible to achieve manually, ideal for CNC machining milling operations.
- High-Volume Production: Perfect for mass production, CNC machining ensures identical parts with minimal variation, essential for maintaining quality.
- Prototyping: CNC machining is widely used for rapid prototyping, allowing engineers and designers to quickly create and test physical models.
- Material Versatility: CNC machines can work with a wide range of materials like metals, plastics, wood, and composites, making them adaptable to multiple industries, including China CNC machining parts.
- Reduced Human Error: Automation in CNC reduces the likelihood of errors, ensuring higher quality and consistency across production.
- Time and Cost Efficiency: CNC machining accelerates production processes and reduces labor costs, essential for keeping manufacturing competitive in the U.S., where companies might also consider outsourcing CNC milling service China for cost-effective solutions.
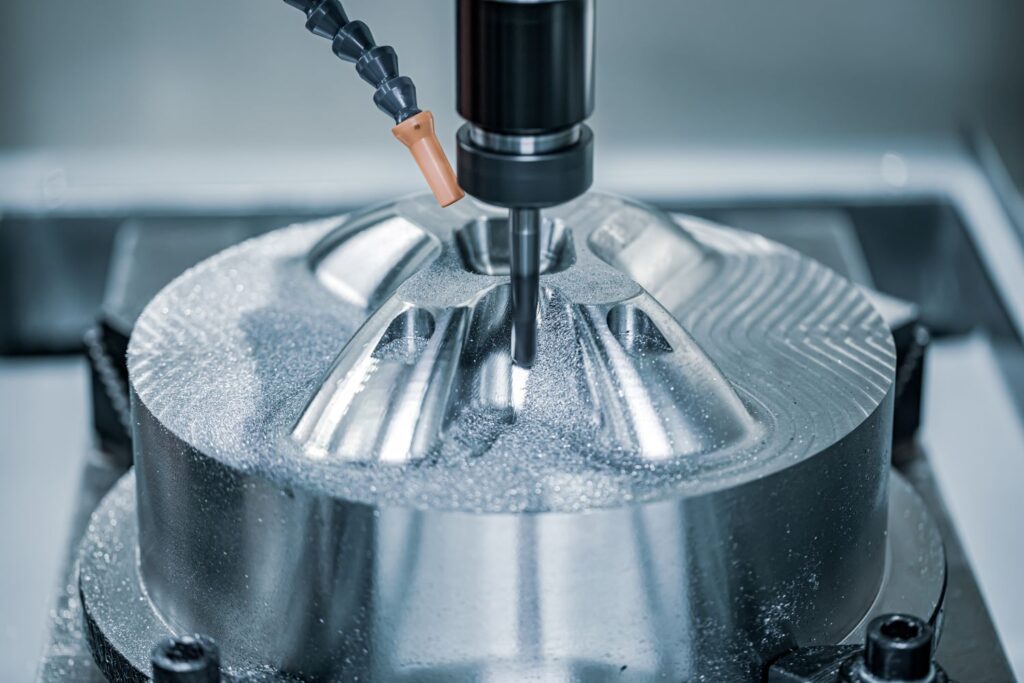
What are the 5 common types of CNC machines?
CNC machines come in various types, each tailored for specific tasks, making them versatile tools in both U.S. and global manufacturing. The most common types include:
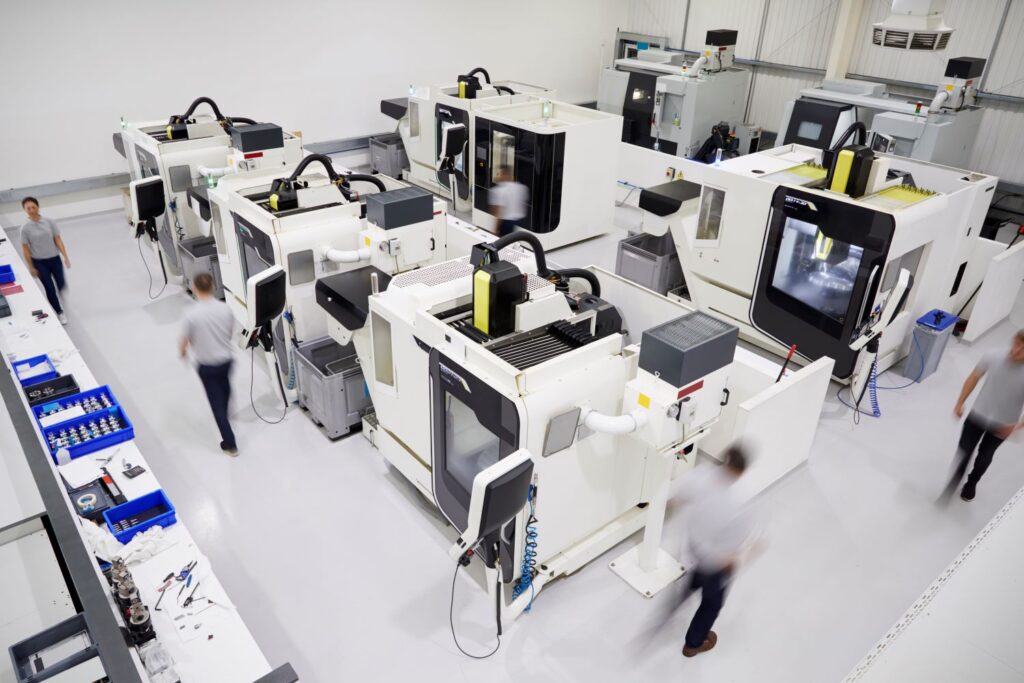
CNC milling machines use rotating tools to cut and shape materials, ideal for creating complex parts with features like holes, slots, and pockets.
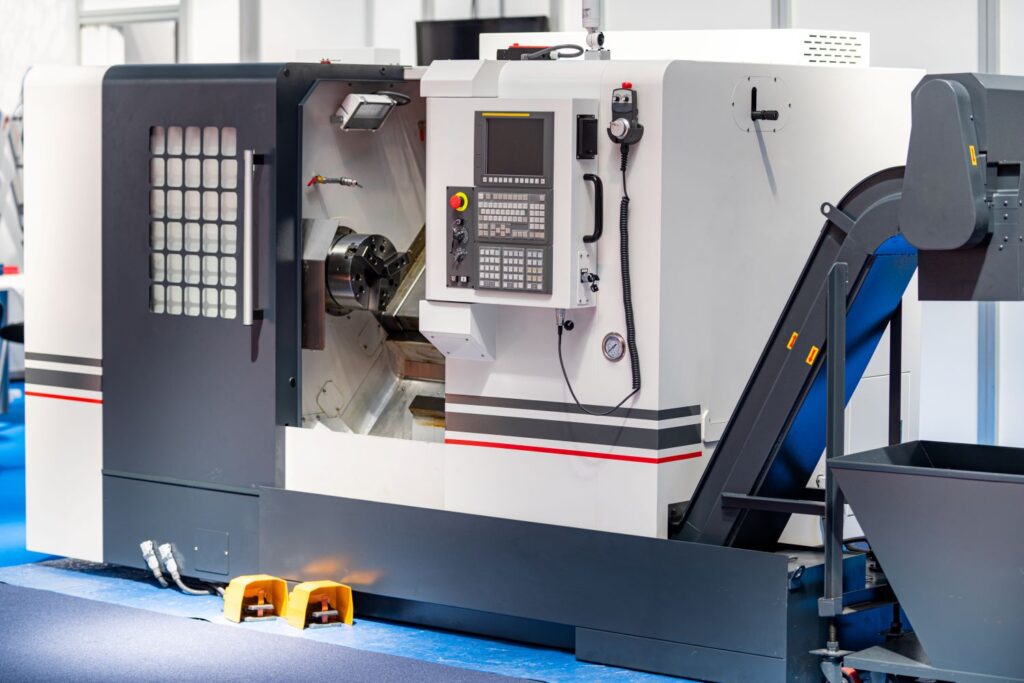
CNC lathes spin the workpiece while a stationary cutting tool shapes it, making them perfect for producing cylindrical parts such as shafts, rings, and threaded components.
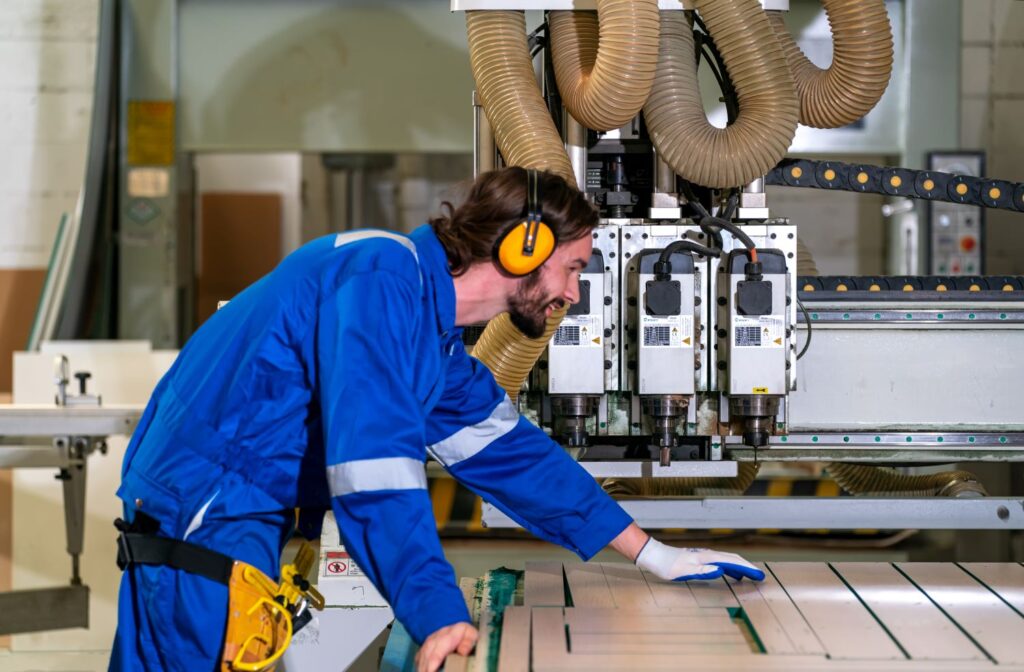
CNC routers function similarly to milling machines but are designed for softer materials like wood and plastic, widely used in woodworking, sign-making, and foam modelling.
CNC plasma cutters use a high-powered plasma torch to cut through conductive metals, commonly used in metal fabrication shops for steel, aluminium, and other metals.
CNC laser cutters employ a focused laser beam to cut or engrave with high precision, suitable for detailed work on metals, plastics, wood, and glass.
The growth of CNC machine usage in the industry over the past five years has been significant, driven by advancements in technology, increased automation, and the demand for precision in manufacturing. Here’s an overview of the trends that contributed to this growth:
- 2019: CNC machine usage started gaining momentum with an approximate growth of 8%, as industries began adopting more automated solutions for efficiency and precision.
- 2020: The demand for CNC machines increased, partly fueled by the pandemic’s impact on labor shortages and the need for automation, resulting in 10% growth. CNC technology became more relevant as manufacturers looked for ways to maintain production while reducing human intervention.
- 2021: As supply chains adapted to the post-pandemic world, CNC machine usage saw further adoption across industries such as automotive, aerospace, and medical devices. The growth rate hit 12%, with companies investing more in digital transformation and advanced manufacturing capabilities.
- 2022: The trend continued as industries embraced CNC machines for their ability to produce complex parts with precision. The growth accelerated to 15%, reflecting increased reliance on CNC technology for both mass production and custom parts.
- 2023: CNC machine usage reached its highest growth at 18%, thanks to innovations like multi-axis machining, AI integration, and smart manufacturing solutions. The expansion of CNC applications in new sectors such as renewable energy and electric vehicles also contributed to the increased demand.
Overall, the last five years have seen CNC machines becoming a critical component of modern manufacturing, with their usage growing steadily due to the need for automation, precision, and cost-efficiency in industries worldwide.
Conclusion
Align Manufacturing, headquartered in Singapore with offices in Bangkok, is dedicated to providing high-quality industrial production solutions on a global scale. Our expertise extends beyond China, offering intricate sand casting, robust forging, efficacious stamping, and state-of-the-art precision machining. This diverse range of metallurgical services ensures we meet the complex needs of our clients worldwide with meticulous attention to detail and seamless communication. Partner with Align Manufacturing for efficient and precise manufacturing outcomes tailored to your project’s success, wherever you may be located
FAQs
Which components move during CNC Machining?
In CNC milling machines, components move along the X, Y, and Z axes. Each axis is divided into two directions: the positive (+) and negative (-) directions. CNC machining involves precise movements of key components, such as the cutting tool, workpiece, and machine table, all controlled by the CNC system. The cutting tool moves along multiple axes to shape or cut the material, while multi-axis machines add rotary movements for complex angles. In some machines, the workpiece rotates, and gantry-style machines move the entire tool-holding gantry, ensuring efficient and accurate production of detailed parts.
What are the basics of CNC?
Automated machinery that operates with a computer system to produce material parts to the desired size and shape through turning. It is suitable for turning work that requires precision or has a high level of complexity.
CAD/CAM Software
- CAD (Computer-Aided Design) software is used to design parts and components in a digital format, creating a 2D or 3D model.
- CAM (Computer-Aided Manufacturing) software converts the CAD design into G-code, which CNC machines can understand. G-code contains instructions for the machine on how to move and manipulate the cutting tools.
G-Code
- G-code is the programming language that tells the CNC machine how to move. It includes commands that dictate the direction, speed, depth of cut, and the specific movements required to shape the material.
CNC Machine Components
CNC machines consist of key components that work together to achieve precision manufacturing:
- Controller: The “brain” of the machine, the controller interprets the G-code and sends the commands to the machine’s moving parts.
- Spindle: Holds and rotates the cutting tool or workpiece, playing a crucial role in the cutting, drilling, or milling processes.
- Axes: CNC machines typically move along the X, Y, and Z axes, while more advanced machines may include rotary axes (A, B, C) for more complex movements.
- Tool Changer: Automatically switches between different cutting tools for various machining tasks.
Automated Movements
- CNC machines are capable of highly precise and repeatable movements. Based on the programmed G-code, CNC machines perform tasks such as cutting, drilling, and milling without human input.
- Machines can move along multiple axes simultaneously, allowing for the creation of intricate and complex parts.
Material Versatility
- CNC machines can work with a wide range of materials, including metals, plastics, wood, and composites. The choice of material depends on the specific industry and application.
Consistency and Precision
- CNC technology ensures that every part produced is identical to the original design, maintaining tight tolerances and high levels of precision. This is critical for industries such as aerospace, automotive, and medical devices.
Applications of CNC
CNC is widely used in industries such as automotive, aerospace, electronics, medical devices, and consumer goods manufacturing. The versatility of CNC technology allows it to produce complex components in large quantities while maintaining quality and precision.
What are the 7 basic types of machine tools?
The seven basic types of machine tools are essential in shaping and forming materials in manufacturing processes. These tools provide precision, efficiency, and consistency in creating parts and components across various industries. Here are the seven basic types of machine tools:
Lathe
A lathe rotates the workpiece while a stationary cutting tool shapes it. It’s ideal for creating cylindrical parts such as shafts, bolts, and rings.
Milling Machine
This machine uses rotating cutting tools to remove material from a stationary workpiece. It is commonly used to create complex shapes with slots, holes, and pockets.
Drill Press
A drill press uses a rotating drill bit to create precise holes in a workpiece. It is often used for boring holes in metals, wood, and other materials.
Grinder
Grinders use abrasive wheels to remove material from the surface of a workpiece, usually for finishing or shaping. They are used for smoothing surfaces or precision finishing.
Shaper
A shaper moves a single-point cutting tool back and forth across a stationary workpiece, removing material in a linear motion. It is typically used for creating flat surfaces, grooves, and keyways.
Planer
Similar to a shaper but larger, a planer moves the workpiece back and forth while the cutting tool remains stationary. It is used for shaping large, flat surfaces.
Broaching Machine
Broaching machines use a toothed tool (broach) to remove material in a single pass, typically creating precision holes, slots, or keyways with specific shapes.
Future Trends of CNC Technology
CNC technology continues to evolve, pushing the boundaries of global manufacturing, including in the U.S. and China CNC milling service. As demand for precision, speed, and customization grows, CNC technology is adapting to meet new challenges. Key trends include:
- Increased Automation and Smart Manufacturing: The integration of Industry 4.0 is set to make CNC machines more interconnected, leveraging data analytics, cloud computing, and the Internet of Things (IoT) to improve production efficiency.
- Additive Manufacturing Integration: Hybrid CNC machines that combine subtractive and additive manufacturing (3D printing) will allow manufacturers to build complex parts layer by layer and then refine them using traditional CNC methods, minimizing waste and enhancing customization.
- Multi-Axis and Multi-Tasking Machines: As industries demand more complex parts, multi-axis CNC machines will allow manufacturers to perform multiple operations in one setup, increasing efficiency.
- Artificial Intelligence (AI) and Machine Learning: AI-driven CNC systems will optimize tool paths, predict tool wear, and automate quality control, leading to enhanced productivity.
- Advanced CNC Materials: CNC machining will increasingly focus on advanced materials like composites, high-strength alloys, and carbon fiber, particularly for industries like aerospace and medical devices.
- Green and Sustainable Manufacturing: CNC machines will play a critical role in green manufacturing, focusing on reducing waste, optimizing energy use, and supporting sustainable practices.
- Customization and Personalization: As consumer demand shifts toward customized products, CNC technology will enable manufacturers to efficiently produce small, personalized batches without compromising quality.
- Cloud-Based CNC and Remote Operation: Cloud-based CNC systems will allow operators to monitor and control machines remotely, increasing flexibility and efficiency across multiple locations.