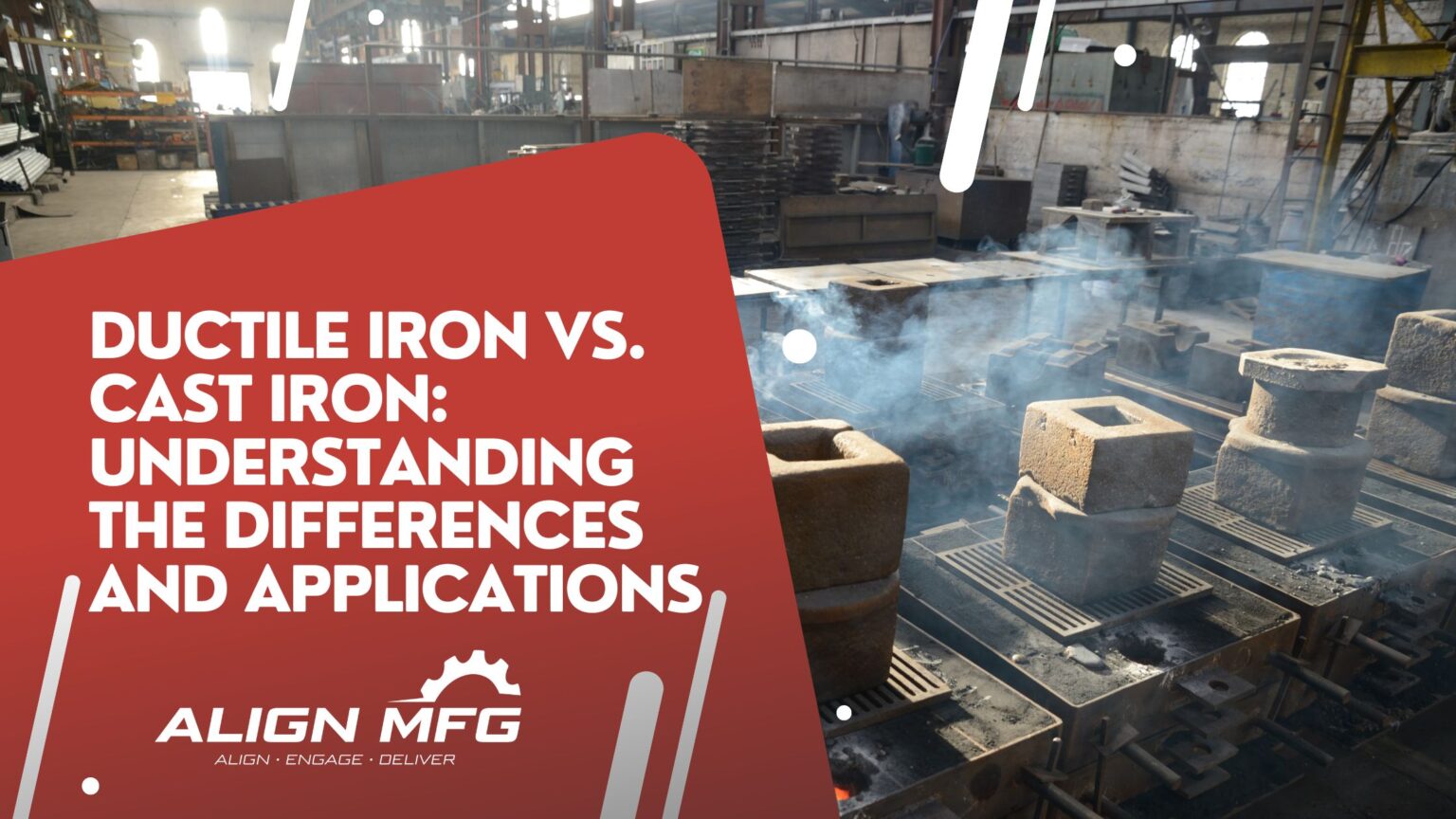
Ductile Iron vs. Cast Iron: Understanding the Differences and Applications
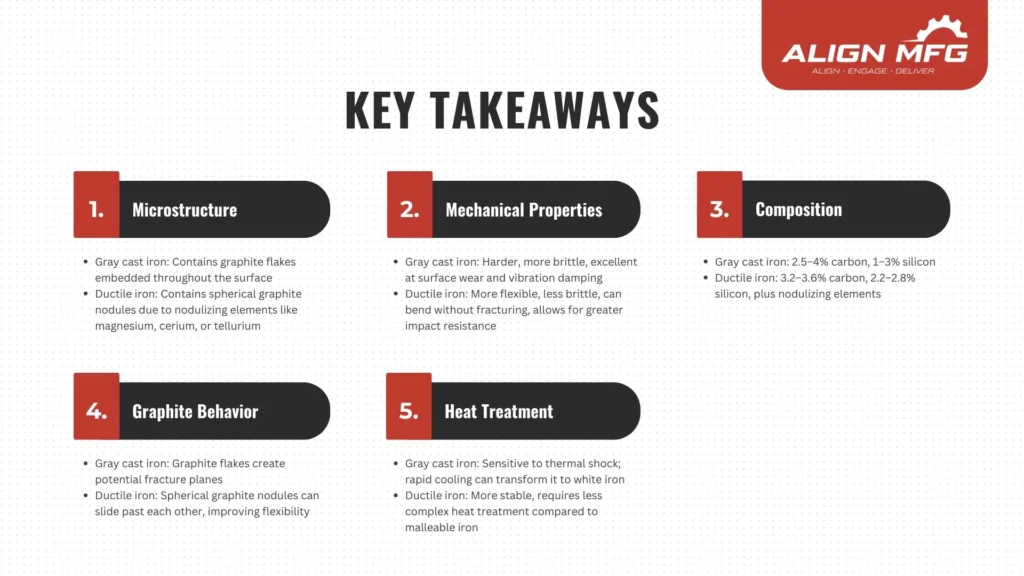
Iron has long been a cornerstone of industrial manufacturing and construction, with various forms serving distinct purposes. Among these, ductile iron and cast iron are two of the most widely utilized materials. While both originate from iron, they exhibit unique properties that make them suitable for different applications. In this comprehensive blog post, we will explore the characteristics, advantages, and disadvantages of ductile iron and cast iron, as well as their respective applications and welding capabilities.
Historical Context
Cast iron has a rich history, dating back to ancient China in the 5th century BC, where it was first used for making tools and weapons. Its use spread to Europe in the 14th century, where it became a popular material for cookware, pipes, and construction due to its durability and ease of casting.
Ductile iron, also known as spheroidal graphite iron, was developed much later, in the 1940s. The invention is attributed to the work of American metallurgist Keith Millis, who discovered that adding small amounts of magnesium to molten iron could change the graphite structure from flakes to nodules. This transformation significantly improved the material's strength and ductility, addressing the brittleness associated with traditional cast iron. Since its introduction, ductile iron has become increasingly popular in various applications, particularly in the automotive and construction industries.
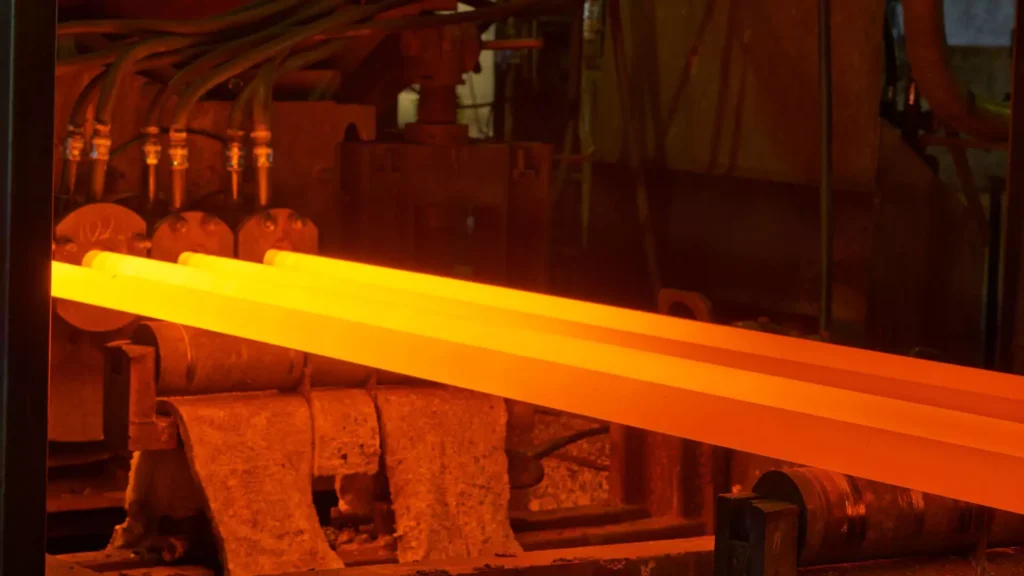
What is Cast Iron?
Cast iron is an alloy primarily composed of iron, carbon (typically 2-4%), and silicon (1-3%). It is produced by melting iron and pouring it into molds to create various shapes. The distinctive microstructure of cast iron, characterized by the presence of graphite flakes, gives it a grey color and contributes to its mechanical properties.
The term "gray cast iron" refers to a specific type of cast iron characterized by its distinctive microstructure and appearance. Here's some context:
When molten iron cools and solidifies, its carbon content determines its microstructure. In gray cast iron, the carbon precipitates out as graphite flakes during cooling. These flakes give the metal a characteristic gray color when fractured or polished, hence the name "gray" cast iron.
The gray color comes from the graphite flakes distributed throughout the iron matrix. These flakes create a distinctive metallic appearance and contribute to the material's unique mechanical properties. Under a microscope, the graphite appears as flat, interconnected structures embedded in the iron.
The formation of these graphite flakes depends on specific cooling conditions and chemical composition, particularly the silicon content. The silicon helps stabilize the graphite formation, preventing the carbon from forming harder, more brittle structures like cementite.
This microstructure gives gray cast iron its notable characteristics:
- Good vibration damping
- High wear resistance
- Low ductility
- Excellent machinability
One of the notable features of cast iron is its remarkable hardness, which makes it resistant to wear and abrasion. However, this hardness comes at a cost; cast iron is also brittle, meaning it can fracture easily under stress. Despite this brittleness, cast iron offers excellent machinability and vibration damping properties, making it a popular choice for applications such as cookware, engine blocks, pipes, and architectural elements.
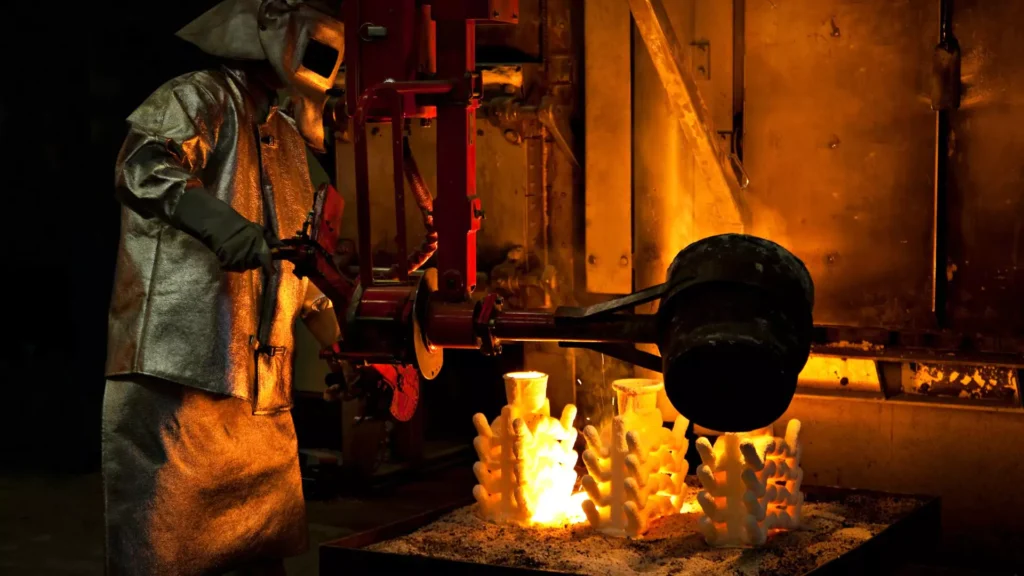
Advantages and Disadvantages of Cast Iron
Advantages:
- Cost-Effective: Generally less expensive to produce than ductile iron, making it a budget-friendly option.
- Wear Resistance: Its hardness provides excellent resistance to wear, suitable for various applications.
- Good Vibration Damping: Ideal for machinery and equipment that require stability and noise reduction.
Disadvantages:
- Brittleness: Prone to cracking and breaking under high stress, limiting its use in certain applications.
- Corrosion: Over time, cast iron can rust and degrade if not properly maintained.
Applications of Cast Iron
Due to its durability and affordability, cast iron is widely used in various industries. Common applications include:
- Cookware: Frying pans, Dutch ovens, and griddles are often made from cast iron for its excellent heat retention.
- Engine Blocks: Cast iron is commonly used in automotive manufacturing for engine components due to its strength.
- Pipes: It is a popular choice for water and sewage pipes due to its corrosion resistance.
- Architectural Elements: Decorative features like railings, columns, and manhole covers often utilize cast iron for its aesthetic appeal and durability.
Exploring Ductile Iron
Ductile iron, also known as nodular cast iron or spheroidal graphite iron, is a more modern alloy developed in the mid-20th century. It is produced by adding small amounts of magnesium to molten iron, which transforms the graphite structure into nodules rather than flakes. This unique microstructure imparts significant toughness and ductility to the material.
Ductile iron is characterized by its ability to bend and deform without breaking, making it far less brittle than cast iron. It exhibits excellent tensile and yield strength, making it suitable for demanding applications. This material also offers good machinability, allowing for precision engineering and manufacturing.

Advantages and Disadvantages of Ductile Iron
Advantages:
- Strength and Toughness: Ductile iron is superior to cast iron, making it ideal for high-stress applications.
- Flexibility: Its ability to bend without breaking allows for better performance under stress.
- Corrosion Resistance: More suitable for outdoor and moist environments, reducing the risk of degradation.
Disadvantages:
- Cost: Generally more expensive to produce due to its complex manufacturing process.
- Weight: Heavier than some alternative materials, which may be a consideration in weight-sensitive applications.
Comparing Properties of Ductile Iron and Cast Iron
To better understand the differences between ductile iron and cast iron, the following table outlines their key properties:
Property | Cast Iron | Ductile Iron |
Composition | Iron, 2-4% Carbon, 1-3% Silicon | Iron, 3-4% Carbon, 0.1-0.5% Magnesium |
Microstructure | Flake Graphite | Nodular Graphite |
Ductility | Low | High |
Strength | Moderate | High |
Corrosion Resistance | Moderate | High |
Machinability | Good | Good |
Cost | Lower | Higher |
Welding Capability | Difficult | Good, with appropriate techniques |
Welding Capabilities
When it comes to welding, ductile iron is generally more favorable than cast iron. The brittleness of cast iron makes it challenging to weld, as it can crack or warp during the welding process. However, if welding cast iron is necessary, techniques such as pre-heating and using nickel-based electrodes can help mitigate some of the issues.
In contrast, ductile iron can be welded using traditional welding methods, including MIG (Metal Inert Gas) and TIG (Tungsten Inert Gas) welding. The presence of nodular graphite allows ductile iron to absorb the stresses associated with welding, making it a more versatile choice for applications that require welding.
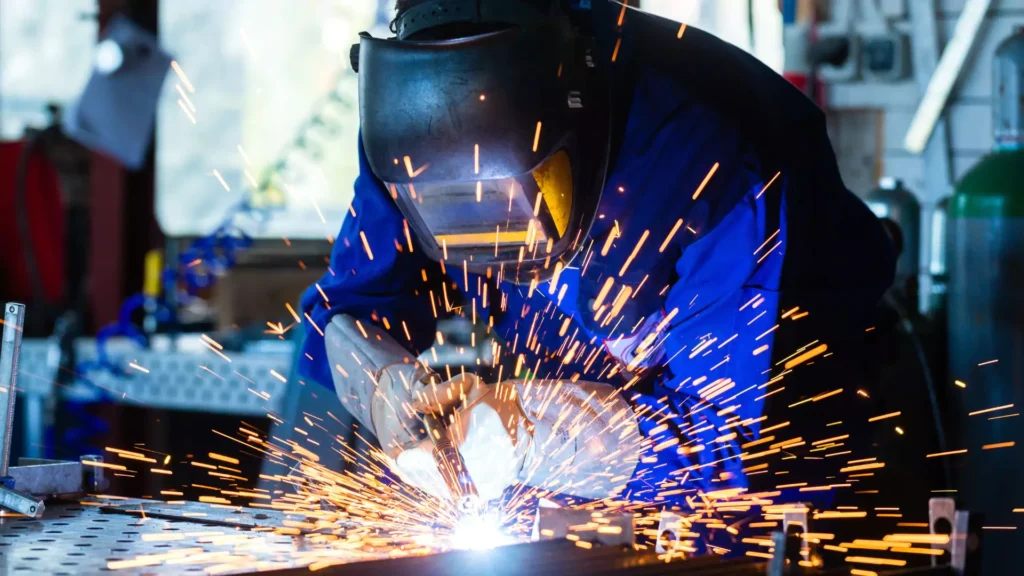
Which Should You Choose?
Both ductile iron and cast iron play vital roles in the industrial sector, and recognizing their differences will enable you to make well-informed decisions for your upcoming projects. With continuous technological advancements, both materials are evolving to meet the demands of modern industry. For further inquiries and assistance, you can contact Align Manufacturing, where our experts are ready to help you choose the right material for your project needs.
Material Selection Criteria for Iron Alloys:
Key Considerations:
- Analyze working stress and component requirements
- Evaluate specific mechanical properties
- Compare cost-effectiveness
Selection Factors:
- Load-bearing capacity
- Stress tolerance
- Dimensional stability
- Environment of use
- Manufacturing constraints
- Budget limitations
Decision Process:
- Ductile iron: More flexible, better impact resistance
- Cast iron: Higher hardness, better vibration damping
Final Choice: Balances technical performance with economic feasibility. Not just about material properties, but matching precise application needs.
FAQS
The primary differences between ductile iron and cast iron lie in their microstructure and mechanical properties. Ductile iron contains nodular graphite, which provides it with greater ductility and toughness, making it less brittle than cast iron, which has flake graphite. As a result, ductile iron can withstand higher stress and is more resistant to cracking.
Yes, ductile iron can be welded using traditional welding methods such as MIG (Metal Inert Gas) and TIG (Tungsten Inert Gas) welding. Its unique microstructure allows it to absorb welding stresses effectively. In contrast, welding cast iron is more challenging due to its brittleness, but it can be done using pre-heating techniques and nickel-based electrodes.
While cast iron can be used outdoors, it is prone to corrosion if not properly coated or maintained. Over time, exposure to moisture can lead to rust and degradation. Ductile iron, however, is generally more resistant to corrosion, making it a better choice for outdoor applications.
Cast iron is typically more cost-effective to produce than ductile iron, making it a budget-friendly option for many applications. However, ductile iron's superior mechanical properties often justify its higher cost in high-stress applications where durability and flexibility are essential. The choice ultimately depends on the specific requirements and constraints of the project.
Ductile Iron Applications:
- Pump casings
- Valve bodies
- Large gas and oil pipes
- Major water and sewage lines
- Bollards designed for impact resistance
- Automotive components
- Cable casings
- Pipes under pressure
Cast Iron Applications:
- Manhole covers
- Tree grating
- Trench grating
- Cookware (like cast iron skillets)
- Engine blocks
- Machine bases
- Brake components
- Smaller pipes
- Guttering pipes
- Stove and grill plates