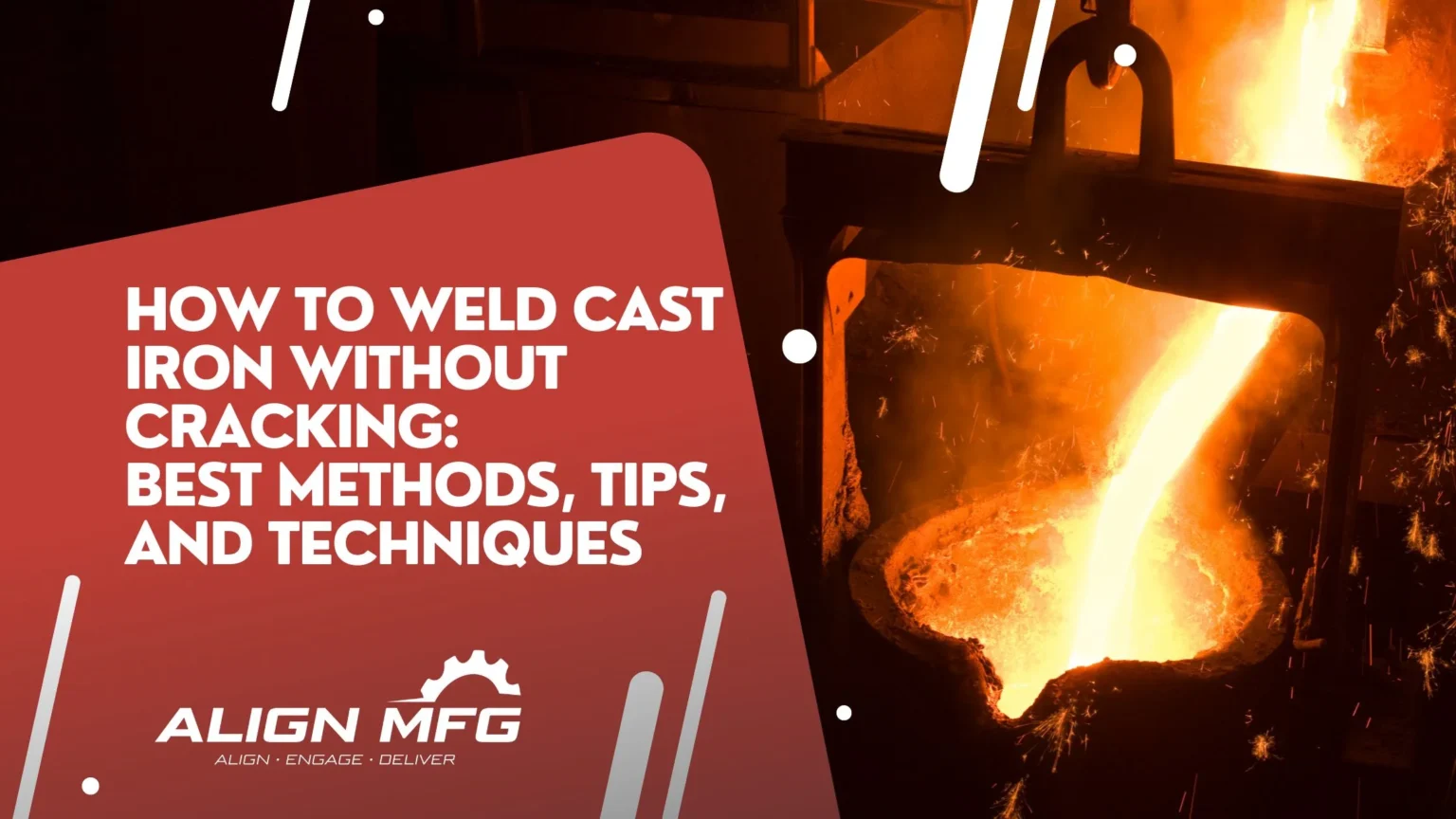
How to Weld Cast Iron Without Cracking: Best Methods, Tips, and Techniques
Welding cast iron is a specialized process that requires careful attention due to its unique properties. This elevated carbon level makes cast iron prone to cracking and other challenges during welding. In this article, we will explore the definition of cast iron, the challenges associated with welding it, effective techniques, and best practices to ensure successful outcomes.
What Is Cast Iron?
Cast iron is an iron-carbon alloy characterized by its high carbon content, typically between 2% and 4%. This composition gives cast iron its distinctive hardness and brittleness. Common types of cast iron include gray cast iron, white cast iron, ductile (nodular) cast iron, and malleable cast iron, each with varying properties and applications.
- Gray Cast Iron: Gray cast iron is the most common type of cast iron, characterized by graphite flakes that form within a pearlite or ferrite microstructure. While it is more ductile and weldable than white cast iron, these graphite flakes can enter the weld pool, leading to embrittlement and weakened welds. To achieve a successful weld, preheating and careful filler metal selection are crucial to minimizing cracking and maintaining structural integrity. Due to these challenges, welding gray cast iron requires expertise and a controlled approach to ensure durable and machinable results.
- White Cast Iron: White cast iron is known for its extreme hardness and brittleness, as it retains carbon in the form of iron carbide (cementite) rather than graphite. This cementite microstructure makes the material highly wear-resistant but also incredibly difficult to machine or weld. Unlike gray cast iron, which allows some degree of weldability, white cast iron is unweldable due to its tendency to crack under thermal stress.
- Attempts to weld white cast iron often result in rapid cooling and the formation of even harder, brittle microstructures, making post-weld machining nearly impossible. In cases where repair is necessary, alternatives such as brazing or buttering with a machinable weld overlay are sometimes used. Another approach is to anneal white cast iron before welding, converting some of the iron carbide into graphite to improve ductility—though this is rarely practical in most industrial applications. Given these challenges, white cast iron is typically repaired using mechanical fastening methods or part replacement rather than welding.
- Ductile (Nodular) Cast Iron: More flexible and weldable than gray cast iron, but still requires special techniques.
- Malleable Cast Iron: Similar to ductile cast iron, it has some flexibility but is more challenging to weld without preheating.
Identifying the cast iron type helps determine the right welding approach and filler material.
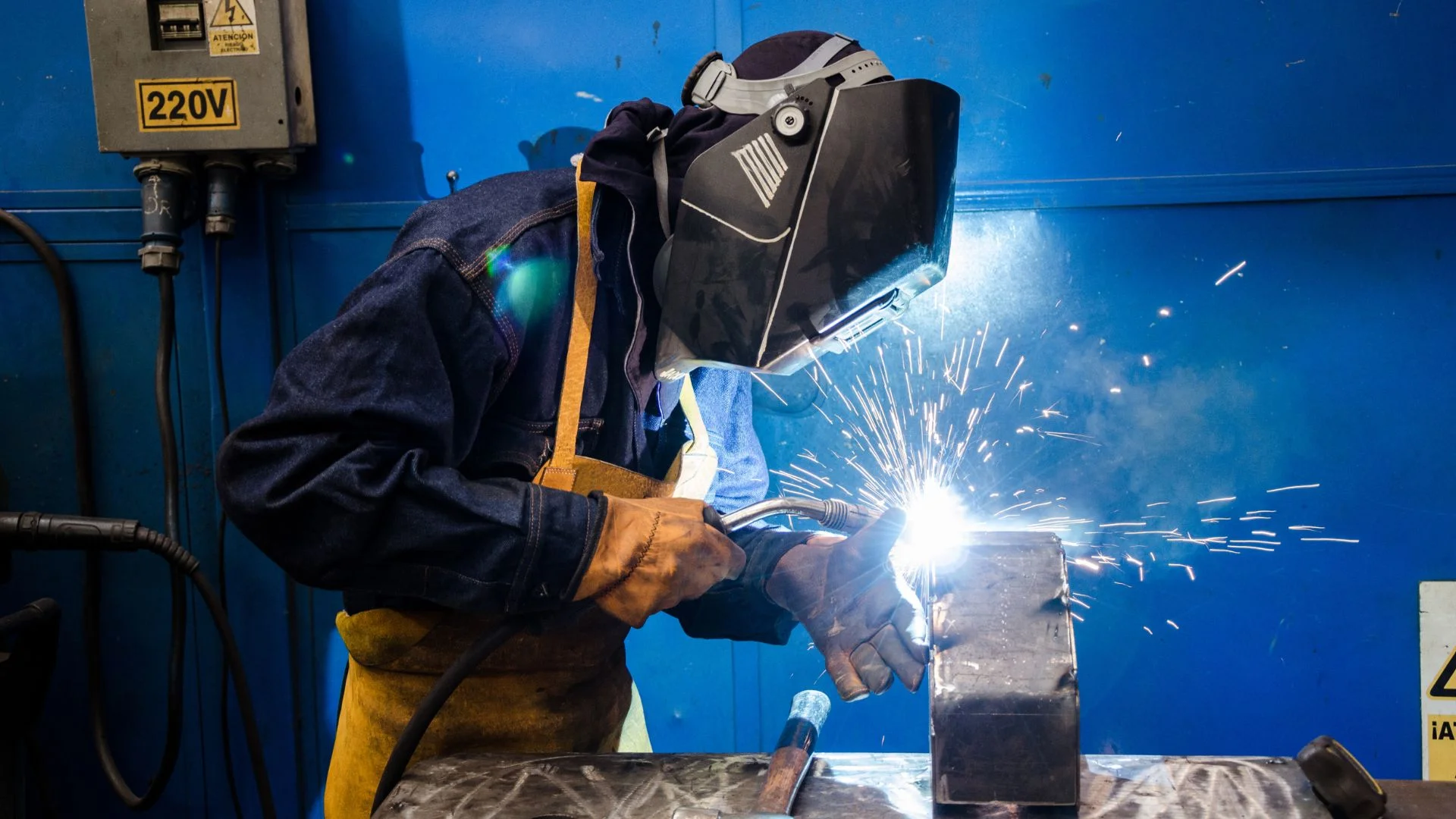
Challenges in Welding Cast Iron
Welding cast iron presents several challenges, primarily due to its high carbon content and brittle nature. Key issues include:
- Cracking: Rapid cooling can lead to the formation of hard, brittle microstructures, increasing the risk of cracks.
- Porosity: Entrapped gases during welding can cause porosity, weakening the weld.
- Contamination: Surface impurities like oil, grease, and rust can lead to defects in the weld.
- Hardening: The heat-affected zone (HAZ) can become excessively hard, making machining difficult.
Techniques for Welding Cast Iron
Several welding methods are suitable for cast iron, each with its advantages and considerations:
1. Shielded Metal Arc Welding (SMAW)
Also known as stick welding, Shielded Metal Arc Welding (SMAW) is one of the most commonly used techniques for welding cast iron. The process utilizes a consumable electrode coated with flux, which creates a protective gas shield when burned, preventing contamination and ensuring a clean weld.
Different types of electrodes can be used depending on the application, required color match, and post-weld machinability. The three primary filler materials for cast iron stick welding include:
- Cast iron covered electrodes – Designed for cast iron applications, though they may be brittle.
- Copper alloy electrodes – Provide a strong bond but are less common for structural welding.
- Nickel alloy electrodes – The most popular choice due to their compatibility with cast iron’s properties.
Nickel-based electrodes are especially preferred because they create a softer, more ductile weld that is less prone to cracking. According to New Hampshire Materials Laboratory Inc., nickel-iron welds are stronger and have a lower coefficient of thermal expansion, reducing welding stresses and improving crack resistance.
Key Considerations for SMAW on Cast Iron:
- Electrode Handling: An electric arc between the electrode and the welding area melts the metals and enables fusion. The arc should be directed at the weld pool, not the base metal, to minimize dilution and reduce hardening.
- Current Setting: It is recommended to use the lowest current setting approved by the manufacturer to avoid excessive heat input, which can increase the likelihood of cracking.
- Preheating: Heating the workpiece to a moderate temperature (typically between 500°F and 1200°F) helps to reduce thermal stress and minimize the formation of brittle zones.
- Post-Weld Cooling: Gradual cooling is essential to prevent cracking. Wrapping the part in an insulating blanket or burying it in dry sand helps slow the cooling rate and prevents the formation of hard, brittle microstructures.
2. Oxy-Acetylene Welding
This method uses a flame produced by burning acetylene with oxygen to weld cast iron. It allows for slow heating and cooling, which can reduce the risk of cracking. A cast iron filler rod is typically used, and the process is suitable for repairing thin sections or intricate parts. However, it requires skilled handling to avoid overheating and potential distortion.
3. Braze Welding
Braze welding involves using a filler metal with a lower melting point than the base metal, such as a bronze or brass alloy. This filler metal melts and flows into the joint through capillary action.This technique is beneficial for joining dissimilar metals and minimizing heat-induced stresses, as it does not melt the base cast iron. Proper surface preparation and flux application are essential to ensure a strong, defect-free joint.
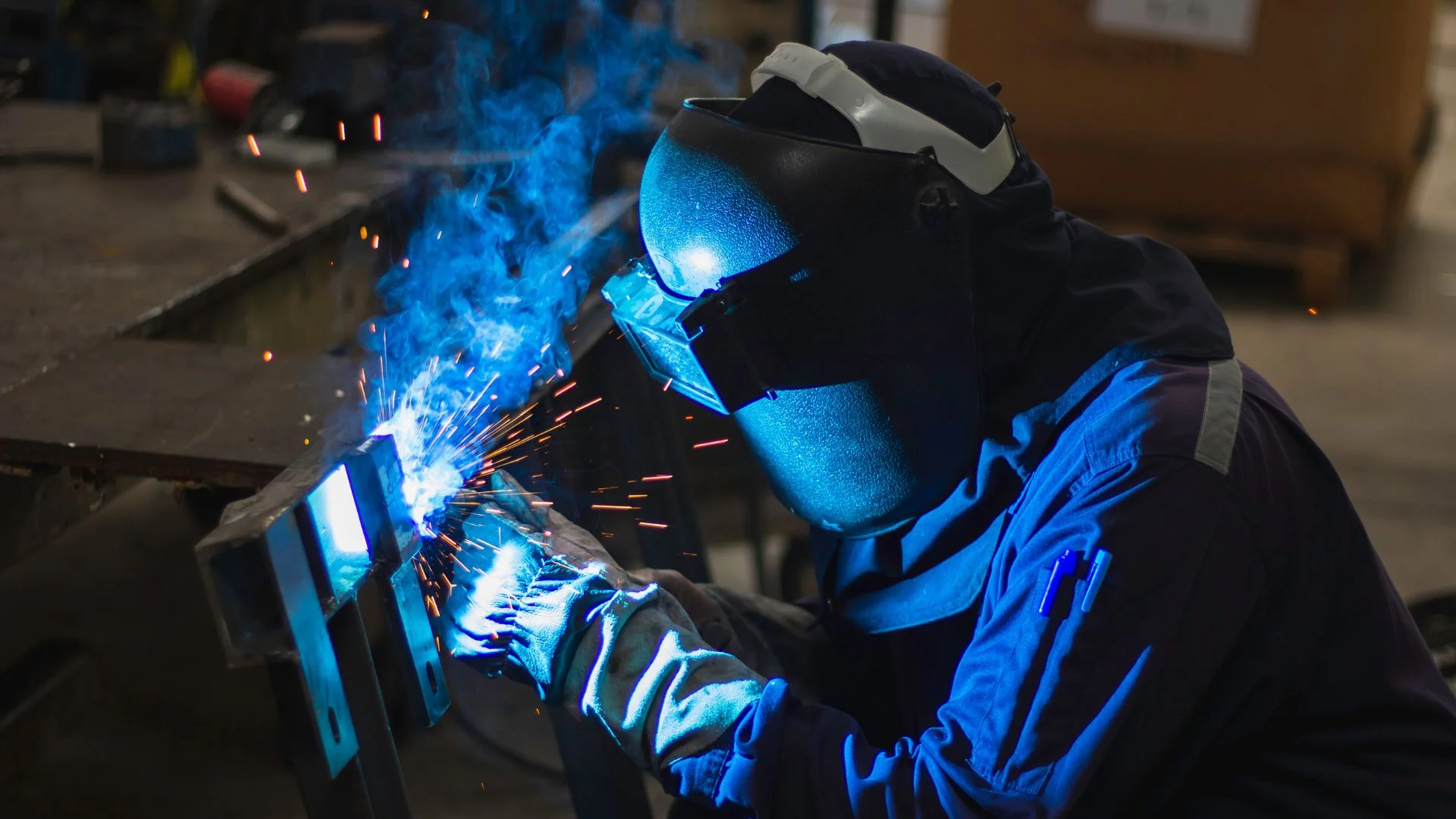
Best Practices for Welding Cast Iron
To achieve optimal results when welding cast iron, consider the following best practices:
Best Practices for Welding Cast Iron
1. Surface Preparation
Proper surface preparation ensures a clean and strong weld.
- Thorough Cleaning: Remove paint, rust, oil, and grease before welding to prevent impurities in the weld pool.
- Avoid Abrasive Grinding: Using abrasive tools can smear graphite over the surface, leading to porosity. Instead, use a carbide burr or gouging electrode for preparation.
2. Preheating the Cast Iron
Preheating Cast Iron: Why It Matters and How to Do It Right
Preheating cast iron is a critical step in preventing thermal stress, cracking, and weld failure. Since cast iron is brittle and has poor ductility, it does not stretch to relieve stress like steel or other ductile metals. Instead, any localized heating can result in restricted expansion, leading to stress buildup and ultimately cracking during the cooling phase.
Why Preheating is Important
The primary reason for preheating is to control thermal expansion and contraction during welding. If only the weld zone heats up, while the surrounding metal remains cool, the heat-affected zone (HAZ) expands unevenly, creating internal tensile stresses that can cause cracks—either immediately or after cooling.
Preheating reduces the thermal gradient between the weld area and the rest of the casting, allowing for a more uniform expansion and contraction. This minimizes stress buildup and lowers the risk of cracking both during and after welding.
How to Properly Preheat Cast Iron
1. Determining the Right Preheat Temperature
The required preheat temperature depends on:
- Type of Cast Iron:
- Gray cast iron: 500°F - 1200°F (260°C - 650°C)
- Ductile cast iron: 500°F - 900°F (260°C - 480°C)
- White cast iron: Typically unweldable; extreme caution required
- Size and Thickness of the Casting:
- Thicker and larger castings require higher preheating temperatures to ensure even heat distribution.
- Welding Method Used:
- Higher-temperature welding methods (e.g., stick welding) require higher preheating temperatures.
- Lower-temperature methods (e.g., brazing) may require little or no preheating.
2. Even Heating: Preventing Uneven Expansion
- Heat the entire casting evenly to avoid creating temperature differentials that can induce stress.
- Use large ovens, torches, or induction heating to distribute heat uniformly.
- Avoid spot heating, as this can cause localized expansion, leading to cracks.
- Slow heating is crucial—do not rush the preheating process.
3. Maintaining a Consistent Temperature
- Once the desired temperature is reached, maintain it throughout the welding process.
- If the workpiece cools below the necessary preheat temperature during welding, reheat it before proceeding.
- Use temperature indicating sticks, thermocouples, or infrared thermometers to monitor temperature.
What to Do When Preheating Isn’t Possible
In some cases, preheating may not be practical due to part size, accessibility, or equipment limitations.
Use a low-heat welding process (such as TIG or brazing).
- Select low-melting-point welding rods or wires to reduce heat input.
- Increase interpass cooling time—welding in small passes with extended cooling time between them.
- Apply peening between weld passes to relieve stress.
3. Welding Techniques
Different welding techniques can be used for cast iron, each with advantages and considerations.
Shielded Metal Arc Welding (SMAW) - Stick Welding
- Uses nickel-based or cast iron-specific electrodes.
- Requires preheating for best results.
- Produces a strong, machinable weld.
Oxy-Acetylene Welding
- Allows for slow heating and cooling.
- Suitable for thin sections and small repairs.
- Requires a cast iron filler rod.
Braze Welding
- Uses a filler metal with a lower melting point.
- Ideal for joining dissimilar metals.
- Reduces heat-induced stress.
In-House Welding Feasibility
While welding cast iron in-house is possible, for critical repairs or structural components, professional expertise is recommended to ensure weld integrity.
4. Welding Execution Techniques
Certain techniques can improve the chances of a successful weld.
- Short Weld Passes: Limit weld beads to 1 inch (25 mm) or less to control heat input and minimize cracking (WeldingHandbook.com).
- Peening: Gently hammering the weld bead while still hot relieves internal stress and prevents cracking (WeldingHandbook.com).
5. Filler Material Selection
Choosing the right filler material is crucial to a strong and durable weld.
- Nickel-Based Electrodes:
- 99% Nickel rods are preferred for their machinability and compatibility with cast iron.
- Ferro-nickel rods (47% nickel, 53% steel) are more affordable and suitable for welding cast iron to steel.
6. Cooling Methods
Controlled cooling is essential to avoid cracks and maintain weld integrity.
- Slow Cooling: Rapid cooling can lead to hardening and cracking. Wrap the welded part in an insulating blanket or bury it in dry sand to cool gradually (MakeItFromMetal.com).
- Slow cooling methods include:
- Wrapping the welded part in heat-resistant blankets
- Burying the casting in dry sand, ashes, or lime
- Placing it in an insulated oven for controlled cooling
- Never quench or expose the welded part to sudden temperature drops, as this will create excessive stress and lead to cracking.
By understanding the inherent challenges of welding cast iron and implementing these techniques and best practices, welders can achieve strong, durable repairs and fabrications.
7. Alternative Methods for Repairing Cast Iron
In some cases, welding may not be the best option. Alternative techniques include:
- Brazing: Uses a filler metal that melts at a lower temperature than the base metal, reducing thermal stress.
- Suitable for non-structural repairs or when welding risks damaging the part.
(Eng-Tips.com).
- Suitable for non-structural repairs or when welding risks damaging the part.
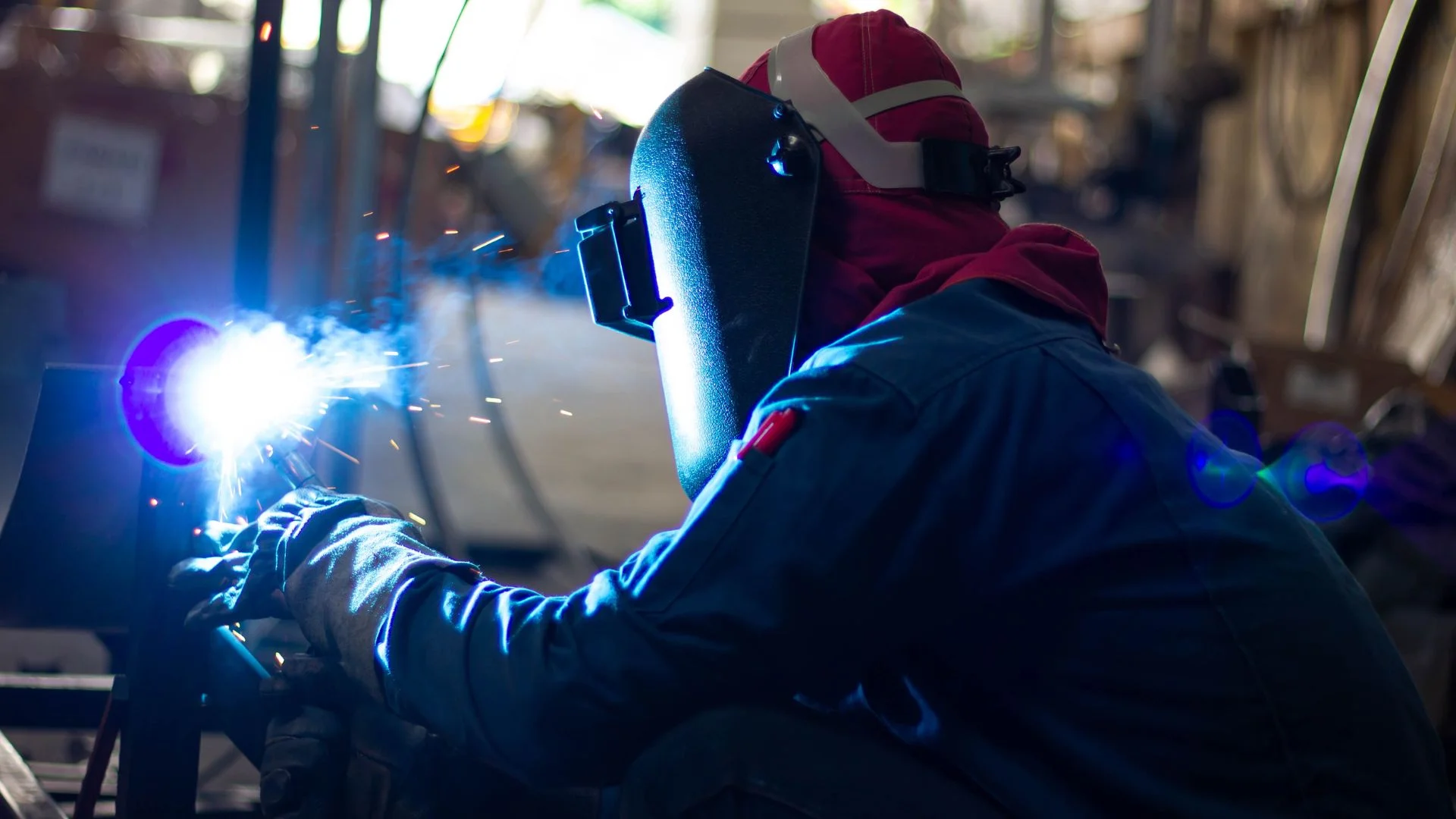
Welding plays a crucial role in the broader manufacturing ecosystem, often complementing our key processes such as casting, forging, and machining. By understanding how welding fits into fabrication and assembly workflows, manufacturers can make more informed decisions about when to incorporate welding into their production strategies.
Whether you need high-strength cast components, machined parts with tight tolerances, or fabricated assemblies, Align helps you achieve cost-effective and durable manufacturing solutions tailored to your industry needs.
Frequently Asked Questions (FAQs)
While it is possible using cold welding techniques, preheating significantly reduces the risk of cracking and improves weld quality.
99% Nickel electrodes offer the best machinability, while ferro-nickel electrodes are more cost-effective for structural applications.
MIG welding is generally not recommended due to its high heat input, which can increase cracking risks.
For high-strength repairs, stick welding with nickel electrodes is best. However, brazing can be an effective alternative for non-structural repairs.’
- Preheat the workpiece properly.
- Use short weld passes.
- Peen the weld bead to relieve stress.
- Cool the part slowly using insulating materials.