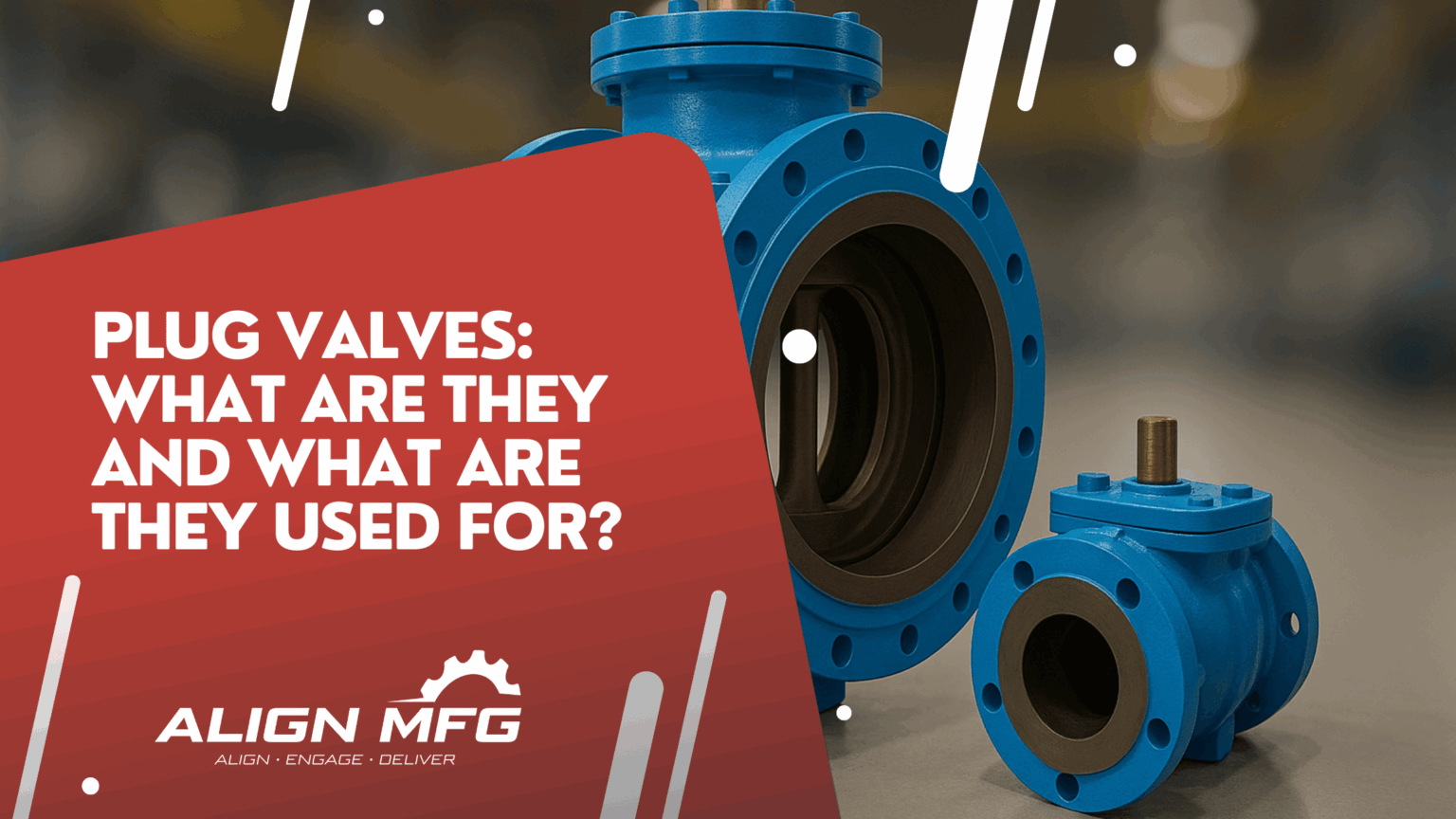
Plug Valves: What are they and What are they Used for?
In the world of fluid control, plug valves stand out for their simplicity and reliability. Known for their straightforward design and effectiveness, they play a crucial role in numerous industrial applications where tight shut-off is essential. A deeper understanding of their functionality and versatile usage can demystify these pivotal components of fluid dynamics.
The hallmark of plug valves is their conically tapered plug, which aligns ports to regulate flow efficiently. From lubricated to non-lubricated, multi-port to eccentric, and jacketed types, the varied designs offer an array of solutions tailored to specific needs, from quick shut-off requirements to specialized use cases in diverse industries.
Definition of a Plug Valve
A plug valve is a type of quarter-turn valve used for controlling the flow of fluids through a pipe system. Its primary feature is a cylindrical or conical plug that can be rotated inside the valve body to open or close the passageway, allowing or stopping the flow of fluids. The design ensures a tight shut-off, making them suitable for a wide range of applications, including those requiring minimal leakage.
Basic Design and Operation
Plug valves are integral components in managing the flow of fluids in pipelines. Their simple yet robust design offers a reliable, efficient solution for fluid control, suitable for numerous applications from chemical processing to oil and gas distribution. The valve’s body, crafted from durable materials like stainless steel or carbon steel, supports longevity and performance under diverse operating conditions. Operators favor plug valves for their minimal leakage potential and overall resilience, making them a top choice for ensuring tight shut-offs and consistent system operation.
Conically Tapered Plug
Its conically tapered plug, plays a crucial role in controlling the flow of fluids. This taper is designed to fit snugly within the valve body, ensuring minimal leakage and a reliable seal when closed. The conical shape not only aids in achieving a tight shut-off but also facilitates easy rotation, allowing for swift actuation and precise fluid control. Its design provides low resistance to flow, minimizing energy consumption and pressure drop, which are critical considerations in maintaining an efficient network. The conical plug design is versatile, allowing it to adapt to various fluid types and flow rates, further solidifying its status as an essential component in numerous industrial applications.
Ports Alignment for Flow Control
Ports alignment in plug valves is vital for accurate and efficient fluid flow management. The alignment involves positioning the plug’s openings to match the valve’s ports, ensuring optimal fluid passage. Proper alignment allows for precise control over the flow of fluids between connected pathways, a feature crucial in systems where fluid direction must be regularly adjusted. The ability to direct flow efficiently helps in maintaining desired flow rates and preventing potential bottlenecks in the system. This control mechanism optimizes the operational efficiency by reducing issues such as pressure loss and product contamination, making plug valves an indispensable asset in processes that demand high accuracy and dependability in fluid handling.
Types of Plug Valves
The main valve types include lubricated, non-lubricated, multi-port, eccentric, and jacketed plug valves. Each type is designed with specific features tailored to enhance performance and efficiency, thereby reducing energy consumption and ensuring optimal fluid flow.
Lubricated Plug Valves
Lubricated plug valves incorporate a lubricant film between the plug and valve body, facilitating smoother operation and minimizing friction. This type of plug valve is favorable in handling gases and fluids at varying flow rates, due to its capacity to withstand higher pressure drops with less wear and tear. Lubricated plug valves are commonly used in industries that require durable and reliable sealing for high-temperature applications, making them a popular choice across a wide range of sectors.
Non-Lubricated Plug Valves
Non-lubricated plug valves utilize a different mechanism where the smooth surfaces of the plug and body are polished to achieve a tight seal without the need for lubrication. This type is generally more compact and requires less maintenance, as there is no need to replace or monitor lubricants. The absence of lubrication reduces the risk of contamination, making them ideal in industries like food and pharmaceuticals. Their design, commonly utilizing materials like stainless steel, helps in efficiently managing fluid flow where product purity is critical. Additionally, non-lubricated plug valves are known for their low friction operation and long service life.
Multi-Port Plug Valves
Multiport valves are designed to handle the flow of fluids through multiple pathways with a single valve body. These valves can streamline piping systems by allowing for flow direction changes without the need for multiple valves, effectively reducing energy consumption and pressure drop. They are particularly beneficial in chemical and processing industries, where altering fluid paths quickly and efficiently is crucial. This type of plug valve promotes operational flexibility and minimizes downtime during maintenance.
Eccentric Plug Valves
Eccentric plug valves, such as the DeZURIK Eccentric Plug Valves, are distinct due to their unique plug design that moves off-center, allowing for an unobstructed flow path and reduced resistance. These valves provide excellent tight shut-off capabilities and are known for handling solid or fibrous materials without clogging. Suitable for applications involving abrasive slurries, sewage, and wastewater, these valves are vital in industries where robust performance is required under challenging conditions.
Jacketed Plug Valves
Jacketed plug valves are designed to maintain process fluid temperatures by providing additional insulation around the valve body. This design is crucial for applications dealing with viscous or temperature-sensitive fluids that need consistent thermal control to prevent solidification or degradation. By circulating a heating medium through the jacket, these valves ensure the fluid flow remains unobstructed and efficient. Their construction, often in stainless or carbon steel, supports durability and effective thermal management.
Plug Valve Application
Plug valves are versatile components used widely to control the flow of fluids in various systems. These valves provide excellent performance in a wide range of applications and are available in materials such as carbon steel and stainless steel, enabling them to cater to diverse operational needs. Their ability to offer tight shut-off and control flow between ports makes them suitable for numerous industrial settings.
Quick Shut-Off Requirements
In settings where quick shut-off is critical, plug valves are the valves of choice. They are designed to provide an almost instantaneous stop to fluid flow, minimizing any potential loss or contamination. This feature is vital in preventing pressure drop and reducing energy consumption. This capability makes them an excellent choice for applications requiring frequent and rapid operation settings, ensuring operational efficiency and safety.
Industrial Use Cases
Plug valves are integral to industrial operations, offering robust performance in a range of applications. With sizes varying from 3 – 24 inches, they are adaptable to different systems and specifications. In industries where tight shut-off and precise flow rates are necessary, such as chemical processing, plug valves maintain the integrity of fluid flow while reducing the risk of product contamination. Their durability is enhanced by using materials like carbon steel and stainless steel, ensuring longevity in aggressive environments. Industrial applications also benefit from non-lubricated plug valves, which reduce maintenance requirements and offer enhanced reliability.
Factors to Consider When Choosing a Plug Valve
Plug valves are essential components in various industries, providing reliable flow control for numerous applications. When selecting a plug valve, understanding the specific needs and operational context is vital. Several factors, including the type of plug valve, construction materials, and desired flow rates, play a crucial role in determining the most suitable choice. Considering these aspects ensures optimal performance, minimizes pressure drop, and decreases energy consumption. By evaluating these critical factors, you can secure the right plug valve for your requirements and enhance system efficiency and longevity.
Specific Application Needs
Identifying the specific needs of your application is the first step in choosing the right plug valve. Different plug designs cater to varied requirements, including tight shut-off, high flow rates, or flow-directing possibilities. Typical applications range from chemical processing to oil and gas transportation, each with unique demands. Multi-port plug valves are ideal for systems needing more than one flow path without additional piping. Understanding these distinct needs allows for the selection of a plug valve that efficiently directs the flow of fluids and supports overall system functionality.
Construction Materials
The construction material of a plug valve is a decisive factor impacting its durability and suitability for particular operations. Common materials used in valve bodies include stainless steel and carbon steel. Stainless steel is preferred in environments with harsh chemicals and extreme temperatures. In contrast, carbon steel suits applications where cost-effective, reliable performance is paramount. Choosing the appropriate material ensures the plug valve withstands operational strains and reduces the risk of product contamination and valve damage.
Operating Pressure and Temperature
Operating pressure and temperature significantly influence the type of plug valve needed. Various plug valves are rated for different pressure ranges and temperature conditions, affecting their performance and safety. Ensuring your chosen valve can handle your system’s maximum and minimum pressure and temperature levels is crucial. Eccentric plug valves, such as the DeZURIK models, are well-suited for high-pressure environments, offering reliable performance even under demanding conditions.
Sealing Systems
Sealing systems within plug valves play a pivotal role in ensuring leak-tight performance and preventing fluid loss. Non-lubricated plug valves often utilize elastomeric or PTFE-lined seals to minimize leakage and extend the valve’s operational life. These seals provide effective sealing without the need for continuous lubrication, reducing maintenance efforts. Depending on the application type, choose sealing systems that offer the best balance of tight shut-off capabilities and operational efficiency. Proper sealing ensures minimal pressure drop and protects against undesired fluid flow between ports.
Advantages and Disadvantages of Plug Valves:
Beyond ensuring a tight shut-off, gas plug valves offer numerous benefits:
– Minimal Maintenance: Simple design results in fewer problems and reduced maintenance costs. Without lubrication needs, they are ideal for contamination-sensitive areas like food processing. Made from stainless or carbon steel, they’re durable.
– Wear Risks: Plug valves are efficient but susceptible to wear, especially with abrasive or corrosive fluids, damaging the plug and seating. Regular maintenance is crucial to extend their lifespan and efficiency.
– Versatility – You can use plug valves with large flow rates as well.
However, there are disadvantages of plug valves:
– Inefficiency in Throttling: They are unsuitable for throttling tasks, limiting their versatility in specific applications.
– High Actuation Force: They require more force to operate due to their high-friction, full-contact design, necessitating stronger actuators or increased manual effort, which can be inconvenient in some scenarios.
– Potential Galling: There is a susceptibility to galling, which can impair function over time.
– Reduced Port Size: The tapered plug design often results in a smaller port, which may not be ideal for all flow requirements.