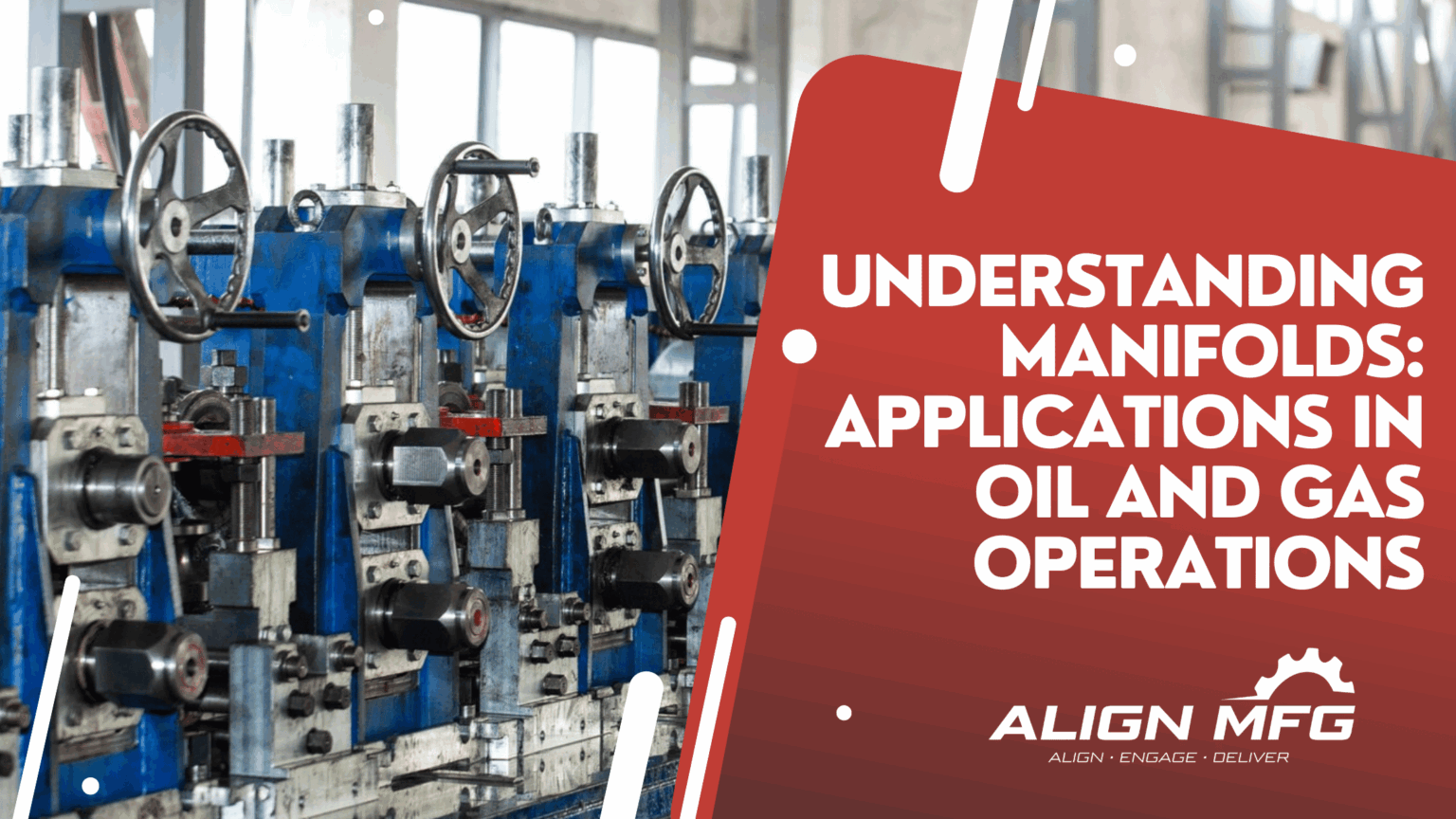
Understanding Manifolds: Applications in Oil and Gas Operations
In the oil and gas sector, manifolds are critical assemblies that consist of interconnected valves, pipes, and fittings. Their primary function is to control, distribute, and monitor the flow of fluids, such as oil, gas, and water, during various phases of operations, including exploration, drilling, production, and processing. By efficiently managing fluid flow, manifolds ensure operational safety, flexibility, and efficiency.
Core Functions of Manifolds
Manifolds serve several essential purposes in oil and gas operations:
- Flow Control: Regulating the direction and rate of fluid flow from multiple wells or equipment.
- Distribution: Routing fluids to appropriate processing facilities or storage units.
- Isolation: Allowing sections of the system to be shut off for maintenance or emergency response.
- Monitoring: Facilitating the measurement of pressure, temperature, and flow rates to ensure optimal operation.
Types of Manifolds and Their Applications
Understanding the different types of manifolds is crucial for selecting the appropriate system for specific operational needs:
1. Production Manifolds
Production manifolds collect fluids from multiple wells and direct them to processing facilities. They are designed to handle high-pressure flows and are essential for efficient production management.
2. Choke Manifolds
Choke manifolds regulate wellhead pressure using adjustable or fixed chokes. They are vital for controlling the flow rate from wells, especially during drilling and testing phases, ensuring safety and preventing blowouts.
3. Kill Manifolds
Kill manifolds are used to inject kill fluids into wells to control pressure during emergencies. They play a critical role in well control operations, allowing for the safe shutdown of wells when necessary.
4. Test Manifolds
Test manifolds isolate individual wells for performance testing. They enable operators to assess well productivity and reservoir characteristics without affecting the overall production system.
5. Injection Manifolds
Injection manifolds distribute fluids like water or gas into wells for enhanced oil recovery. They help maintain reservoir pressure and improve hydrocarbon extraction efficiency.
6. Block and Bleed Manifolds
Block and bleed manifolds are designed to isolate sections of piping for maintenance by blocking flow and bleeding off pressure. They ensure safety during equipment servicing and prevent contamination.
Design Considerations and Material Selection
Key Design Considerations for Manifolds
Designing manifolds for oil and gas operations requires meticulous attention to various factors to ensure safety, efficiency, and longevity. The following are critical considerations:
- Pressure Ratings: Manifolds must be designed to withstand the maximum operating pressures they will encounter, including transient pressure surges. Industry benchmarks such as Maximum Allowable Working Pressures (MAWP) reach up to 6000 psig, with operational temperatures ranging from -65°F to 1200°F.
- Material Selection: Choosing appropriate materials is vital to resist corrosion, erosion, and other environmental factors. Materials should be compatible with the fluids handled and the operational environment.
- Temperature Tolerance: Manifolds should be capable of operating effectively within the temperature ranges expected in the system, accounting for both ambient and process temperatures.
- Flow Capacity: The design must accommodate the required flow rates without causing excessive pressure drops or turbulence, ensuring efficient fluid distribution.
- Safety Features: Incorporating safety mechanisms such as pressure relief valves, isolation valves, and emergency shutdown systems is essential to protect personnel and equipment.
- Ease of Maintenance: Designs should allow for straightforward access to components for inspection, maintenance, and replacement, minimizing downtime and operational disruptions.
- Detailed Valve Configurations: Specific valve configurations, like the two, three, and five-valve setups, are crucial for controlling flow parameters and offering system flexibility. These arrangements impact pressure monitoring, calibration, isolation, and bleed functions, enhancing the manifold’s operational precision.
Standards and Certifications
- API 6A / API 16C: Wellhead, choke, and kill manifolds.
- API 600: Bolted bonnet steel gate valves
- API 6D: Pipeline valves
- ANSI/ASME B16.34: Valve design.
- ISO 14313: Ensures product quality and testing protocols.
- NACE MR0175 / ISO 15156: Covers materials for sour environments (when Hydrogen Sulfide, H₂S, is present).
Material Selection for Manifold Construction
Selecting the right materials for manifold construction is crucial for durability and performance:
- Carbon Steel: Commonly used due to its strength and cost-effectiveness, suitable for non-corrosive environments.
- Stainless Steel: Offers excellent corrosion resistance and is suitable for handling corrosive fluids. Grades like 316L are commonly used in harsh environments.
- Duplex Stainless Steel: Combines high strength with superior corrosion resistance, suitable for high-pressure and corrosive applications.
- Aluminum: Lightweight and corrosion-resistant, aluminum is suitable for low-pressure applications and where weight reduction is a priority.
- Ductile Iron: Known for its good machinability and corrosion resistance, making it a viable option for certain applications
- Plastics and Polymers: Suitable for extremely corrosive fluids but limited in high-temperature or high-pressure use.
Skid-Mounted Manifolds
Skid-mounted manifolds are pre-assembled units mounted on a frame or skid, offering several advantages:
- Ease of Installation: Pre-fabricated units can be quickly installed on-site, reducing downtime.
- Mobility: Skid-mounted systems can be relocated as needed, providing flexibility in operations.
- Compact Design: Efficient use of space, especially beneficial in offshore or space-constrained environments.
Below is an image of a skid-mounted production manifold:
Operational Benefits and Strategic Importance of Manifolds
Enhancing Operational Efficiency
Manifolds play a pivotal role in streamlining oil and gas operations by centralizing control over fluid distribution. This centralization reduces the complexity of piping systems, minimizes potential leak points, and facilitates easier monitoring and maintenance. By directing the flow of oil, gas, and water through a unified system, operators can achieve smoother transitions between different operational phases, such as drilling, testing, and production.
Improving Safety Measures
Safety is paramount in oil and gas operations, and manifolds contribute significantly to this aspect. By allowing for the isolation of specific sections of the pipeline, manifolds enable maintenance and emergency interventions without halting the entire system. This capability not only ensures the safety of personnel but also protects the integrity of the equipment and the environment.
Cost-Effectiveness and Resource Optimization
Implementing manifold systems leads to cost savings by reducing the need for extensive piping networks and associated components. The modular nature of manifolds allows for scalable operations, meaning facilities can adjust their systems based on current production needs without significant overhauls. This adaptability ensures optimal use of resources and capital.
Facilitating Advanced Monitoring and Automation
Modern manifolds are often equipped with sensors and automation technologies that provide real-time data on pressure, flow rates, and temperature. This information is crucial for predictive maintenance, allowing operators to address potential issues before they escalate into major problems. Additionally, automated systems can adjust operations dynamically, enhancing efficiency and reducing manual intervention.
Supporting Environmental Compliance
With increasing environmental regulations, manifolds assist in ensuring compliance by providing precise control over fluid handling. Their ability to prevent leaks and spills aligns with environmental protection standards, and their integration with monitoring systems allows for accurate reporting and rapid response to any anomalies.
Conclusion
In conclusion, manifolds are integral to the efficiency, safety, and functionality of oil and gas operations. Understanding their core functions, types, design considerations, and material selection is essential for optimizing their performance in various applications. By leveraging advanced technologies and adhering to safety and environmental standards, the oil and gas industry can enhance operational efficiency while ensuring the safety of personnel and the environment. Check out Align Manufacturing to find out more about manifold components in the oil and gas industry.