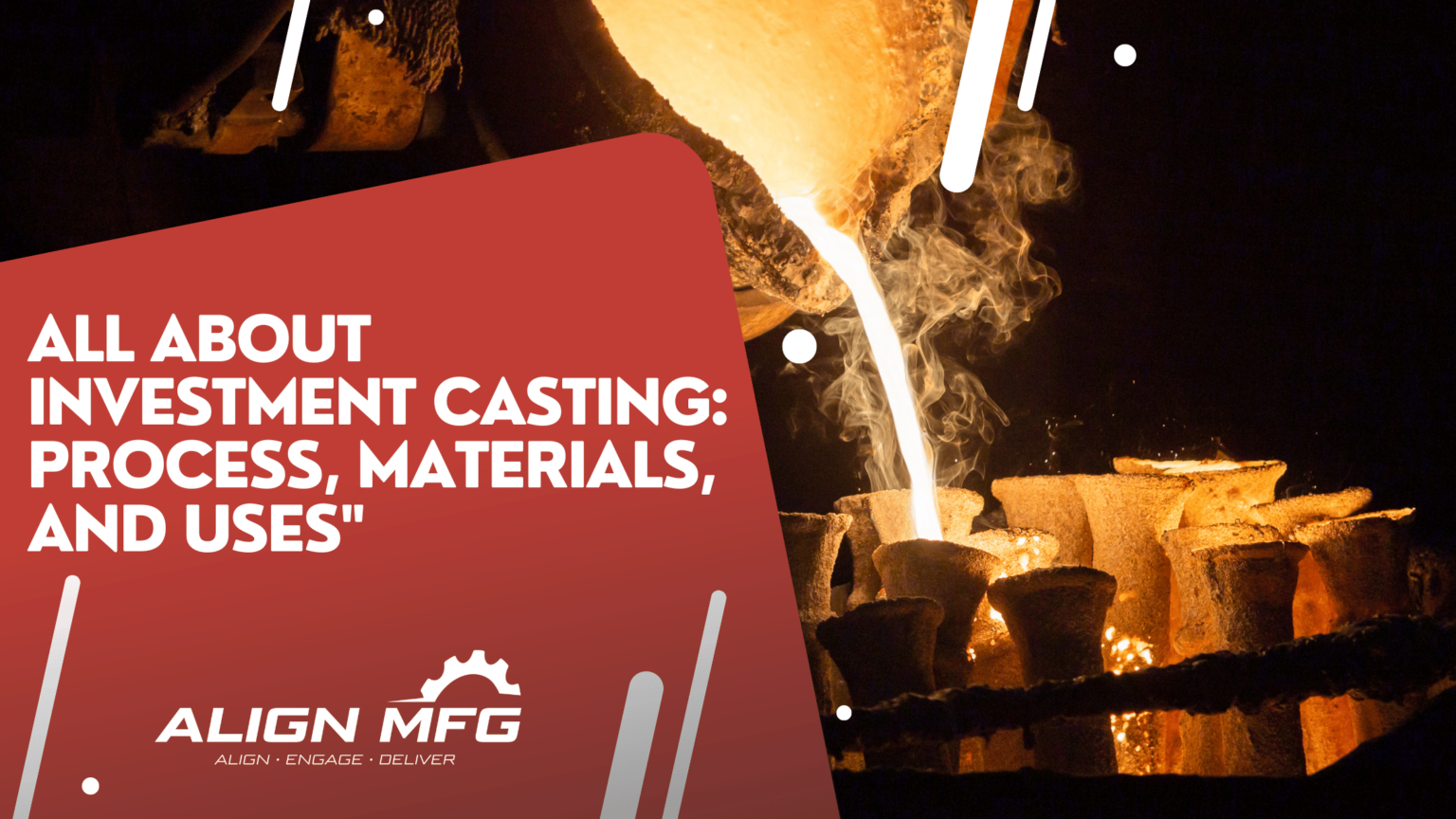
All About Investment Casting: Process, Materials, and Uses
Investment casting, also referred to as lost-wax casting, is a manufacturing process that has been utilized for thousands of years to produce intricately detailed metal parts. This method is highly esteemed for its ability to create precise and complex shapes with excellent surface finishes. From ancient artifacts to modern industrial components, investment casting continues to be a versatile and essential technique in various manufacturing sectors. Notably, the investment casting market is expected to reach USD 17.57 billion by 2031, registering a CAGR of 4.58%.
What is Investment Casting?
Lost wax investment casting involves creating a wax pattern, which is then coated with a ceramic material to form a mold. Once the ceramic mold hardens, the wax is melted away, leaving a hollow mold into which molten metal is poured. This technique allows for the production of detailed and high-quality metal components, making it a preferred method for industries requiring precision and complexity in their parts.
Benefits of Investment Casting
Investment casting offers numerous advantages, including:
High Precision: This method can achieve tight tolerances and detailed geometries that are often challenging or impossible with other casting techniques. The precision of lost wax makes it ideal for components that require high levels of accuracy and detail.
Versatility: It is suitable for a wide range of metals and alloys, including both ferrous and non-ferrous materials. This versatility allows manufacturers to choose the best material for their specific application.
Smooth Surface Finish: The process produces parts with excellent surface quality, reducing the need for extensive machining or finishing work. This results in lower overall production costs and improved aesthetic appeal.
Reduced Machining: Investment casting minimizes the need for secondary machining operations, as the parts come out of the mold very close to the final dimensions. This not only saves time but also reduces material waste.
Design Flexibility: Lost wax casting allows for complex and intricate designs that would be difficult or impossible to achieve with other casting methods. This flexibility enables engineers to create innovative solutions that meet specific performance requirements.
Overview of the Investment Casting Process
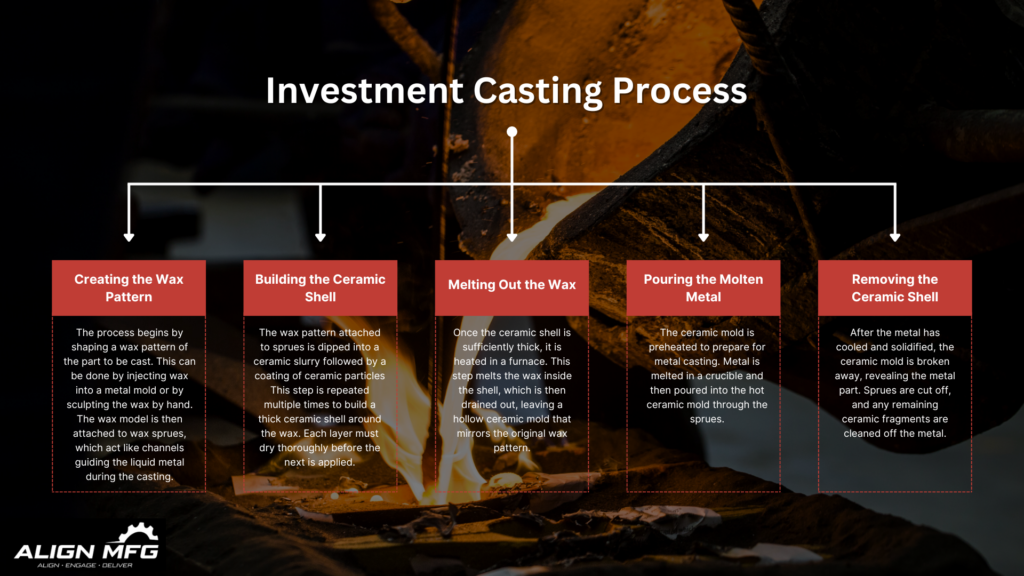
The investment casting process can be broken down into several key stages, each crucial for producing high-quality castings:
- Die Design: The process begins with the design and manufacture of injection molding dies. These dies are used to produce hundreds or thousands of wax models, and their correct design is essential to reduce casting defects and ensure the metal flows correctly into the shell.
- Pattern Creation: Using the injection molding dies, a wax model is created, which is an exact replica of the part to be manufactured.This wax pattern is typically produced using a metal die or by 3D printing, allowing for precise replication of complex geometries.
- Pattern Assembly: Before mold building, the wax patterns are arranged on a wax tree. This assembly facilitates the simultaneous creation of multiple castings and ensures efficient use of materials.
- Mold Building: The wax pattern is repeatedly dipped into a ceramic slurry and coated with fine sand to build a thick, durable ceramic shell around the pattern. This shell will eventually serve as the mold for the molten metal.
- Wax Removal: Once the ceramic mold has dried and hardened, it is heated in a kiln, causing the wax to melt and drain away. This leaves a hollow ceramic mold ready for metal casting.
- Metal Pouring: Molten metal is then poured into the ceramic mold, filling the cavity left by the melted wax pattern. The liquid metal flows into every detail of the mold, capturing the intricate design of the original pattern.
- Cooling and Solidification: The metal is allowed to cool and solidify within the ceramic mold. Proper cooling is essential to ensure that the casting achieves the desired mechanical properties and dimensional accuracy.
- Final Touches: After the metal has solidified, the ceramic mold is broken away to reveal the metal casting. The casting is then subjected to finishing processes such as grinding, polishing, and machining to achieve the final specifications and surface finish.
When to Use Investment Casting
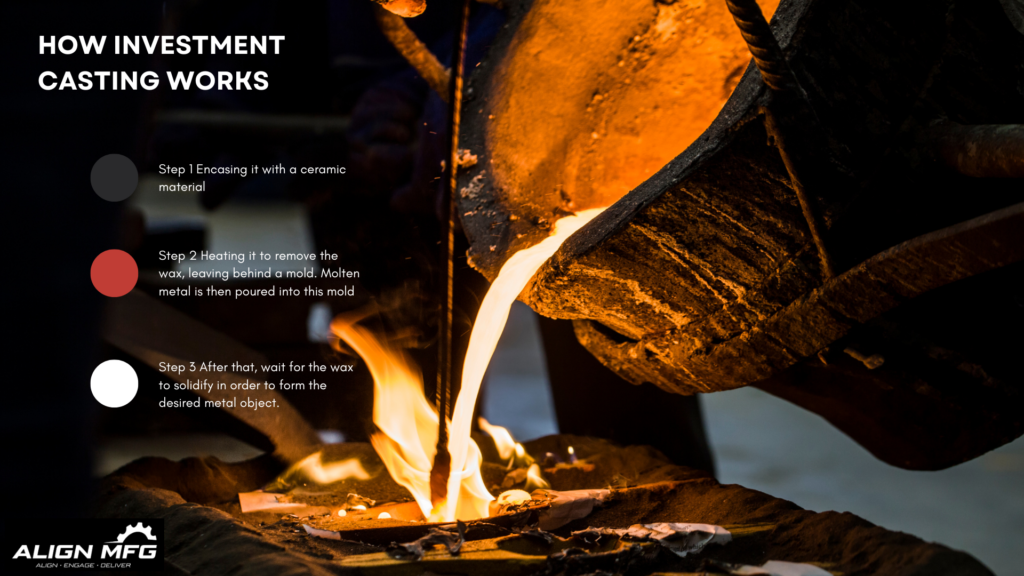
Investment casting is a process known for its complexity and labor intensity, making it relatively costly. However, the advantages it offers often justify the expense. This method is highly versatile and can accommodate nearly any metal. Although typically used for smaller parts, it is also effective for producing components that weigh 75 lbs or more.
The process yields parts with exceptional dimensional accuracy, often achieving net-shape forms that require minimal to no secondary machining. The same die can be reused repeatedly with minimal maintenance. For high-volume orders, the time and labor saved by reducing or eliminating secondary machining can compensate for the cost of new tooling. Conversely, smaller production runs may not justify the initial investment, making investment casting most economical for batches of 25 parts or more.
The entire process from creating a fresh wax pattern to completing a casting typically takes around seven days. The majority of this time is spent building and drying the ceramic shell mold. Some foundries have quick-dry capabilities that can expedite the process. The labor and time-intensive nature of investment casting impacts not only cost but also production timelines. Due to limited equipment and production capacity in foundries, longer lead times are often encountered for investment casting projects.
Common Materials Used
Lost wax casting can utilize a variety of metals and alloys, each chosen for specific properties and applications:
- Stainless Steel: Known for its corrosion resistance, high strength, and excellent durability, stainless steel is commonly used in industries such as aerospace, medical, and food processing.
- Carbon Steel: Valued for its durability, machinability, and cost-effectiveness, carbon steel investment casting is widely used for auto parts, construction, and heavy machinery applications.
- Alloy Steel: Offers enhanced mechanical properties such as increased strength, toughness, and wear resistance, making it suitable for demanding applications in the oil and gas, mining, and defense industries.
- Aluminum: Lightweight and corrosion-resistant, aluminum is ideal for aerospace, automotive, and consumer electronics applications where weight reduction is critical.
- Brass and Bronze: These alloys are excellent for decorative and electrical applications due to their attractive appearance, good conductivity, and resistance to corrosion.
Applications of Investment Casting in Various Industries
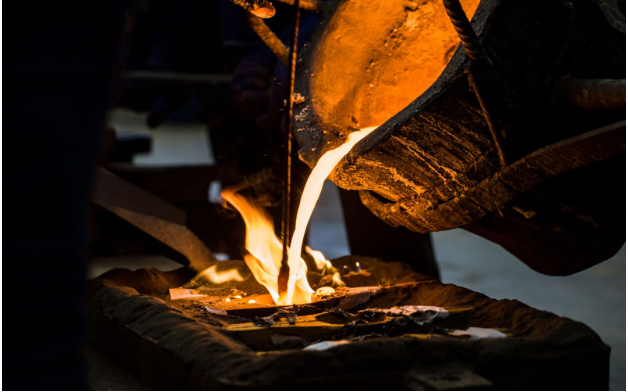
Investment casting is employed across numerous industries due to its versatility, precision, and ability to produce complex shapes with high-quality finishes:
Aerospace: It is used to produce turbine blades, engine components, and other critical parts that require high strength, heat resistance, and precise geometries.
Automotive: Engine parts, suspension components, and various other automotive parts benefit from the precision and durability of lost wax casting, contributing to improved performance and longevity.
Medical: Surgical instruments, prosthetic devices, and orthopedic implants are manufactured using investment casting to achieve the high levels of precision and biocompatibility required for medical applications.
Military: Weapon components, vehicle parts, and other defense-related items rely on lost wax casting for their strength, reliability, and ability to meet stringent specifications.
Industrial: Pumps, valves, impellers, and various other machinery parts are produced using investment casting to ensure durability, reliability, and efficiency in industrial operations.
Success Story: Precision Investment Casting for Hydraulic Hose Manufacturing
A hydraulic hose machinery manufacturer required parts with extremely tight tolerances (+0.0000”, -0.0002”) and high durability for 1,000 RPM. They needed around 200 pieces annually but faced challenges with technical specifications, cost, and volume, as most factories demanded minimum quantities of 1,000 pieces.
Align Manufacturing partnered with an AS9100-certified foundry in Thailand. We determined the necessary CNC machining processes for the required tolerances and proposed consolidating shipments with another order from a different Thai factory, cutting shipping costs by approximately $2,000 per shipment.
Relocating production to Thailand saved the client tens of thousands of dollars annually by avoiding a 25% tariff. The consolidation strategy further reduced shipping costs, enhancing overall cost efficiency.
Automation and Quality Control
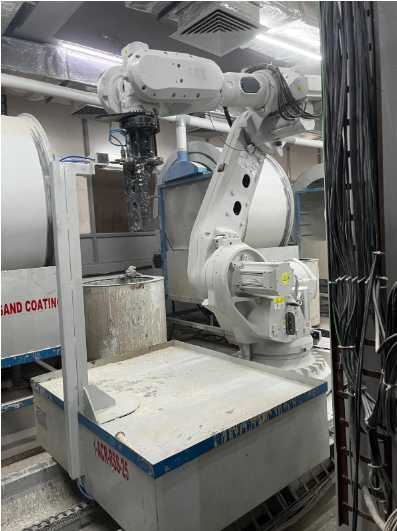
Automation plays a significant role in modern investment casting, enhancing consistency and efficiency throughout the process. Automated systems are used for wax injection, shell building, and even metal pouring, ensuring that each step is performed with precision and minimal human error. Quality control is also crucial, involving rigorous inspections at various stages, such as dimensional checks, non-destructive testing, and metallurgical analysis. These measures ensure that the final castings meet the stringent requirements of industries where precision and reliability are paramount.
Innovation and New Technologies
Innovation and new technologies are continuously transforming the field of investment casting. The integration of advanced computer-aided design (CAD) and simulation software allows engineers to optimize mold designs and predict potential issues before production begins. Additionally, 3D printing technology is revolutionizing the creation of wax patterns, enabling more complex and precise designs. New materials and coating technologies are also being developed to enhance the durability and performance of cast components, ensuring they meet the ever-evolving demands of various industries.
Advanced Insights and Decision-Making
Comparison with Other Casting Methods
Investment Casting vs. Sand Casting:
- Precision: Investment casting offers higher precision and better surface finishes compared to sand casting, making it ideal for components with complex geometries and tight tolerances.
- Complexity: Investment casting is better suited for producing parts with intricate designs and fine details, while sand casting is more appropriate for simpler shapes and larger parts.
- Cost: Investment casting generally has higher upfront costs due to the detailed process and materials involved, but it can lead to overall cost savings through reduced machining and finishing. Sand casting is typically less expensive for larger, simpler parts but may require more extensive post-casting work.
Investment Casting vs. Die Casting:
- Materials: Investment casting allows for a broader range of materials compared to die casting, which is often limited to non-ferrous metals such as aluminum, magnesium, and zinc.
- Precision and Surface Finish: While both methods can produce high-precision parts with smooth surface finishes, investment casting is generally preferred for more complex geometries and tighter tolerances.
- Tooling Costs: Die casting typically involves higher tooling costs but can be more economical for large production runs due to faster cycle times and lower per-part costs. Investment casting, with its ability to produce complex parts in smaller quantities, can be more cost-effective for lower volume production.
Cost Analysis
While investment casting can be more expensive initially compared to other methods like sand casting, it often leads to cost savings in the long run due to reduced need for machining and finishing. Additionally, investment casting allows for more complex designs, which can consolidate multiple parts into a single casting, reducing assembly costs and improving overall product performance. The ability to produce high-quality, detailed parts with minimal waste also contributes to the overall cost-effectiveness of the process.
Conclusion
Investment casting is a versatile and precise manufacturing process suitable for producing complex metal parts across various industries. Its benefits, such as high precision, excellent surface finish, and design flexibility, make it a valuable method for producing high-quality components. By understanding the process, materials, and applications, manufacturers can leverage lost wax casting to enhance their products and achieve superior results. At Align MFG, we exemplify the innovative applications and advancements in investment casting, driving the industry forward. The investment in this casting method can lead to long-term cost savings, improved product performance, and greater design possibilities.
FAQs
What are the advantages of investment casting?
Investment casting offers high precision, versatility in material choice, excellent surface finish, reduced machining, and design flexibility. These advantages make it a preferred method for producing complex and high-quality metal components across various industries.
How precise is investment casting?
It can achieve tight tolerances, often within ±0.005 inches per inch, making it ideal for components that require high levels of accuracy and detail. This precision ensures that parts fit together correctly and function as intended.
What materials can be used in investment casting?
A wide range of materials can be used, including stainless steel, carbon steel, alloy steel, aluminum, brass, and bronze. The choice of material depends on the specific properties required for the investment casting application, such as strength, corrosion resistance, weight, and conductivity.
What are the limitations of investment casting?
While investment casting offers numerous advantages, it also has some limitations. The process can be more expensive and time-consuming compared to other casting methods, especially for larger parts. Additionally, the size and weight of the parts are generally limited by the ceramic shell’s strength.