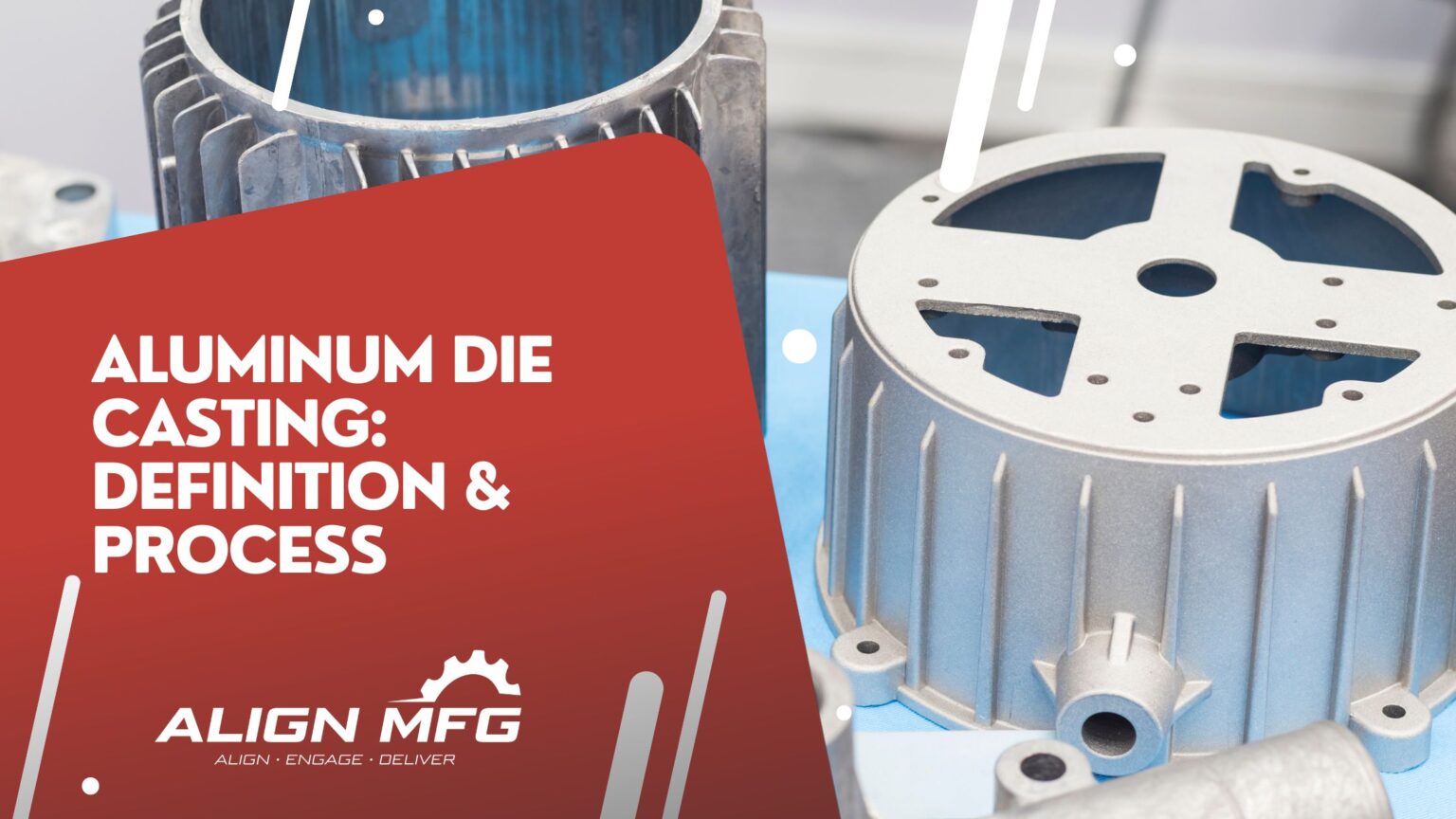
Aluminum Die Casting: Definition & Process
Key Takeaways: Aluminum Die Casting
Aspect | Key Details |
What It Is | A manufacturing process that produces smooth, textured, and precise metal parts. |
How It Works | Involves forcing molten aluminum into a steel mold (die) using high-pressure systems. |
Key Properties | - Corrosion resistance- High thermal and electrical conductivity- Good stiffness and strength-to-weight ratio. |
Advantages | - Lightweight and high dimensional stability- Suitable for complex geometries and thin walls- Cost-effective compared to other casting processes. |
Production Efficiency | - Rapid production allows high volumes to be produced quickly.- Ideal for mass manufacturing. |
Durability | Retains strength and dimensional stability even at very high temperatures. |
Cold Chamber Process | Uses cold chamber machines to handle molten aluminum, which is ladled into the die due to high operating temperatures. |
Applications | Widely used in automotive, aerospace, electronics, and consumer goods for durable, lightweight parts. |
Aluminum die casting has become a transformative force in the manufacturing industry, offering unparalleled efficiency, precision, and durability for a wide range of products. This process is a staple in sectors such as automotive, aerospace, electronics, and consumer goods due to its ability to produce complex shapes with high accuracy. In this comprehensive guide, we will explore the intricacies of aluminum die casting, including its various applications, types, advantages, disadvantages, and the overall process involved.
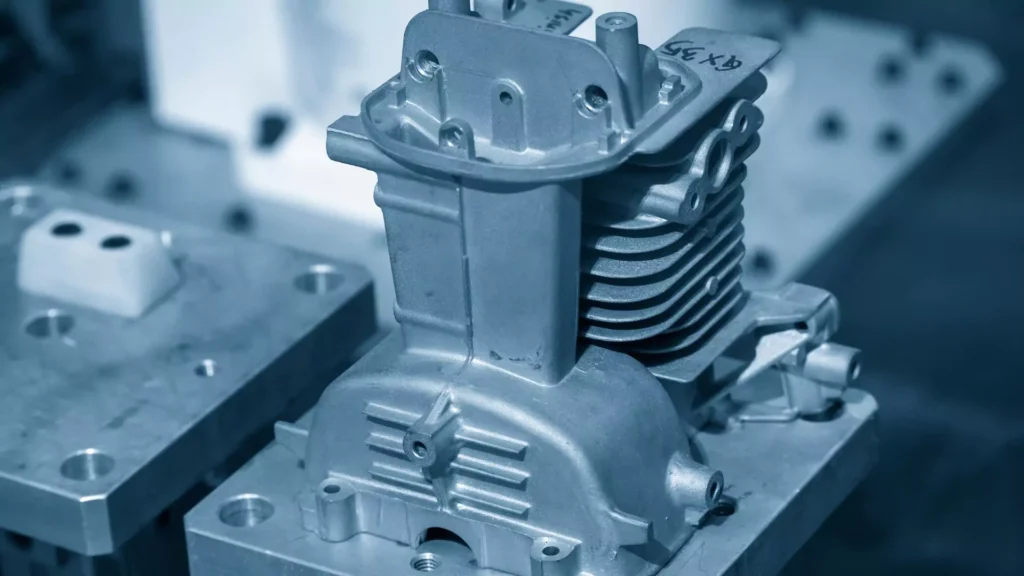
What is Aluminum Die Casting?
Aluminum die casting is a metal fabrication process that involves forcing molten aluminum under high pressure into a steel mold, known as a die. Once the aluminum solidifies, the die is opened to reveal a lightweight yet sturdy component. This method allows for the creation of intricate designs and tight tolerances, making it ideal for mass production of detailed parts.
The Aluminum Die Casting Process
The aluminum die casting process typically follows these key steps:
The Aluminum Die Casting Process
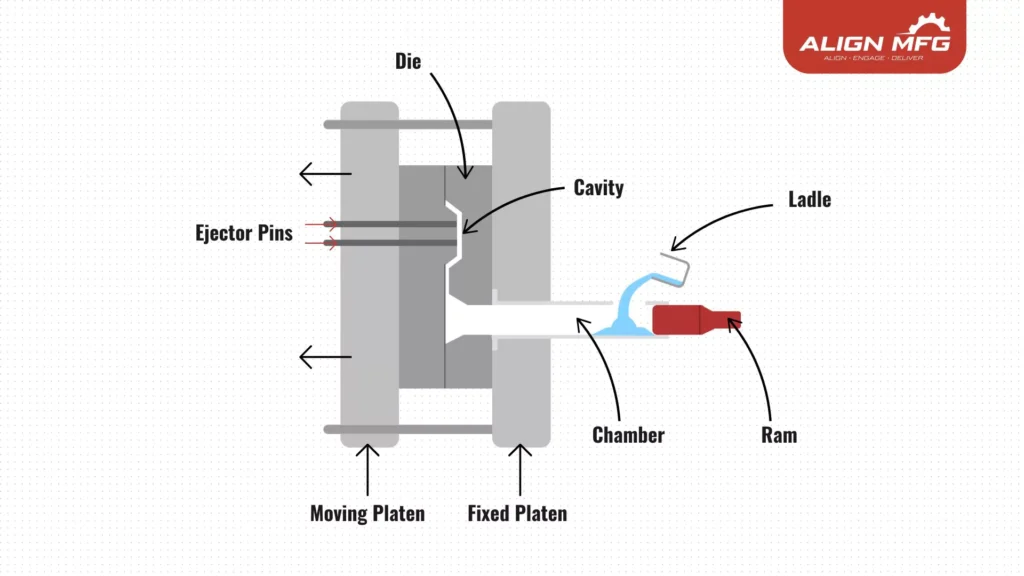
The aluminum die casting process follows these key steps, each involving precise engineering to ensure high-quality results:
- Mold Design and Creation:
- The process begins with designing and manufacturing a durable steel mold capable of producing tens of thousands of castings.
- Each mold consists of at least two sections, allowing for the removal of cast parts. Depending on the complexity of the design, molds may include movable slides, cores, or other specialized sections.
- Clamping and Preparation:
- The two mold halves are mounted securely in the die casting machine. One half remains stationary, while the other is movable.
- Before injection, the mold halves are clamped tightly together using hydraulic cylinders or direct hydraulic pressure, ensuring no gaps exist for molten aluminum to escape.
- Melting and Injection:
- Aluminum is melted in a furnace to the necessary temperature and prepared for injection.
- The molten aluminum is then injected into the die cavity under high pressure, which ensures the material fills every detail of the mold.
- Depending on the machine type (cold chamber or hot chamber), the method of injecting molten aluminum may vary, but the fundamental principles remain the same.
- Hot chamber machines feature a built-in furnace that melts the metal directly within the casting machine, making it ideal for low-melting-point metals like zinc and magnesium alloys. This process is faster, with shorter cycle times.
- Cold chamber machines, on the other hand, use an external furnace to melt higher-melting-point metals, such as aluminum and brass. The molten metal is then transferred to the casting machine using a ladle, resulting in longer cycle times due to the additional transfer step.
- Cooling and Solidification:
- The molten aluminum rapidly cools within the mold cavity, taking on its precise shape as it solidifies.
- The rapid cooling process enhances the part’s dimensional accuracy and structural integrity.
- Ejection:
- Once the part has solidified, the movable die half separates from the stationary half.
- The casting is ejected using ejector pins or other mechanisms, ensuring smooth removal without damaging the mold or the part.
- Trimming and Flash Removal:
- Excess material, known as flash, is trimmed away to refine the part's edges and ensure it meets design specifications.
- Additional trimming may be needed for complex designs with slides or cores.
- Finishing:
Types of Finishing for Aluminum Die-Cast Parts
Bead Blasting
- Creates a uniform, matte finish by using fine beads to smooth and clean the surface.
- Ideal for aesthetic purposes and removing minor surface imperfections.
Anodizing
- Enhances corrosion resistance, improves wear resistance, and provides a decorative finish.
- Available in various colors and commonly used in consumer goods and automotive applications.
Plating
- Adds a protective or decorative metal layer (e.g., chrome, nickel) to improve durability and aesthetics.
- Often used in electrical, automotive, and decorative parts.
Powder Coating
- Provides a durable, corrosion-resistant, and attractive finish using an electrostatically applied powder that is baked to cure.
- Available in a wide range of colors and textures, commonly used in industrial and outdoor applications.
Painting
- Used for aesthetic purposes or additional corrosion resistance.
- Includes wet painting or spray painting with various finishes (glossy, matte, etc.).
Polishing
- Achieves a smooth, reflective surface by mechanically buffing the part.
- Often applied to components requiring a sleek, high-end look.
Chromate Conversion Coating
- A chemical treatment to improve corrosion resistance and paint adhesion.
- Commonly used in aerospace and automotive parts.
Brushing
- Produces a directional, textured finish with fine lines, enhancing visual appeal while reducing visible imperfections.
Deburring
- Removes sharp edges or burrs left from the die-casting process to improve safety and functionality.
E-Coating (Electrocoating)
- Involves immersing the part in a liquid paint solution and applying an electric charge to coat the surface uniformly.
- Offers excellent corrosion resistance and is used in automotive and industrial applications.
These finishing options enhance the appearance, durability, and performance of aluminum die-cast parts, making them suitable for diverse applications across industries.
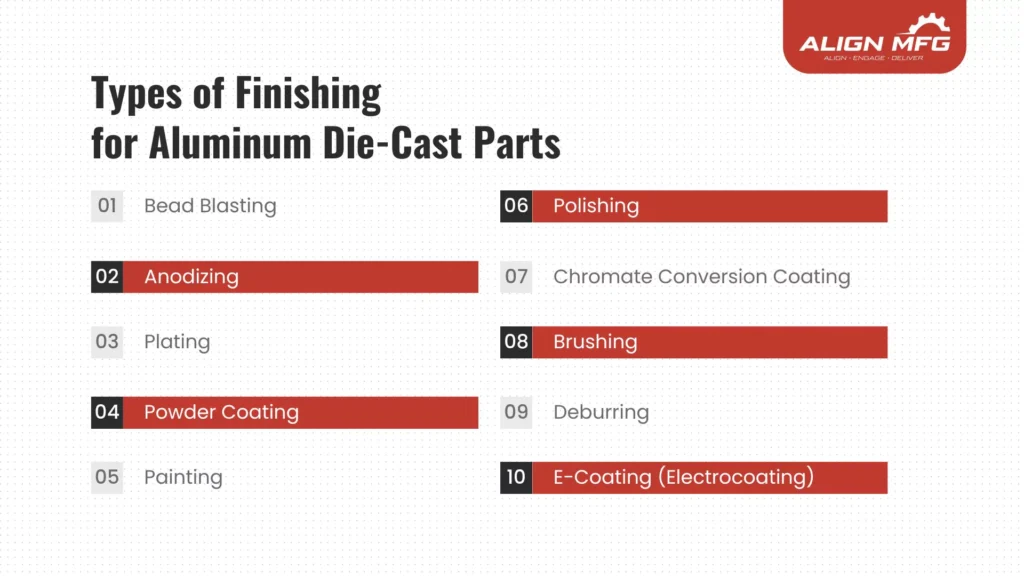
Different Types of Aluminum Casting
Aluminum casting can be categorized into several types, each suited for specific applications:
- Die Casting: As discussed, this involves forcing molten aluminum into a mold under high pressure. It's ideal for high-volume production of complex parts.
- Sand Casting: This method uses sand molds to create parts by pouring molten aluminum into the mold. It's more flexible for low-volume production and complex shapes but may not provide the same precision as die casting.
- Investment Casting: Also known as lost-wax casting, this technique involves creating a wax model, coating it in ceramic, and then melting away the wax to leave a mold for aluminum. It’s excellent for intricate designs but is generally more expensive.
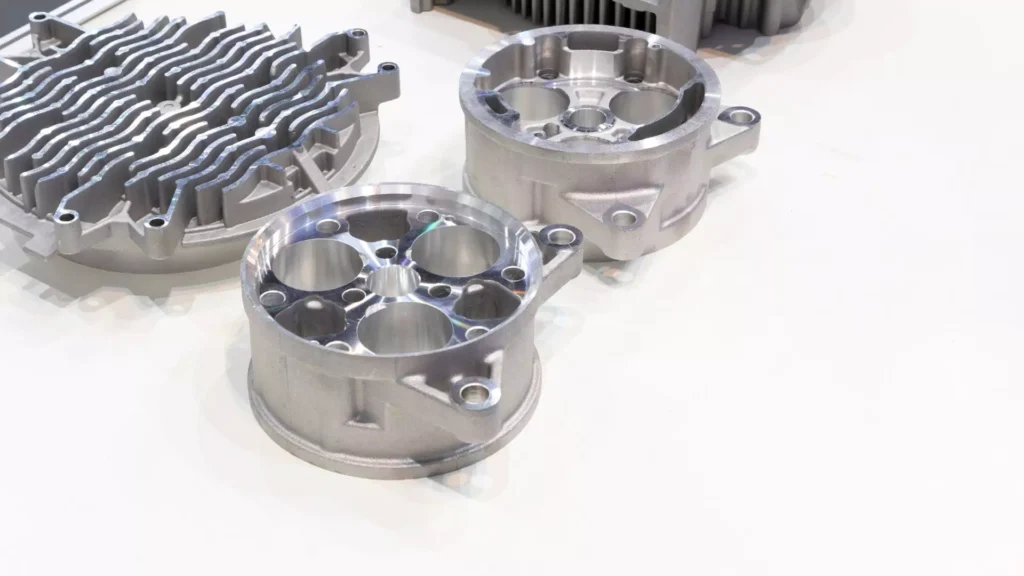
Advantages of Aluminum Die Casting
The benefits of using aluminum die casting in manufacturing are numerous:
- High-Speed Production: Die casting enables rapid production of parts, significantly reducing lead times and allowing for high-volume manufacturing without sacrificing quality.
- Dimensional Accuracy and Stability: The die casting process produces parts with exceptional precision and consistency, ensuring that each piece meets strict specifications.
- Strength and Lightweight: Aluminum’s natural strength-to-weight ratio makes it perfect for creating robust parts that are lighter than those made from other metals, contributing to fuel efficiency in automotive and aerospace applications.
- Multiple Finishing Techniques: Aluminum die cast parts can be easily finished with various techniques, including sandblasting, painting, or plating, providing aesthetic versatility and additional corrosion resistance.
- Recyclability: Aluminum is highly recyclable, which reduces waste and promotes sustainability in manufacturing.
Disadvantages of Aluminum Die Casting
While aluminum die casting has many advantages, there are also some limitations to consider:
- High Startup Costs: High Startup Costs: The initial tooling costs for die casting can be significant, as custom molds need to be designed and manufactured, which can be time-consuming and expensive. Additionally, CNC machines are often required for precision machining and finishing of the die-cast parts, further increasing the upfront investment.
For more on how to reduce costs when buying aluminum die cast parts,check out our guide.
- Limited to High-Volume Production: Due to the high costs associated with tooling, die casting is most economical for medium to high-volume production runs. Smaller production runs can lead to increased per-unit costs.
- Complex Geometries Can Be Costly: Parts with intricate designs may require additional machining or sliding cores, increasing the overall production cost.
- Low Initial Production Speed: The tooling process can take time before any final production parts are made, which can delay the start of manufacturing.
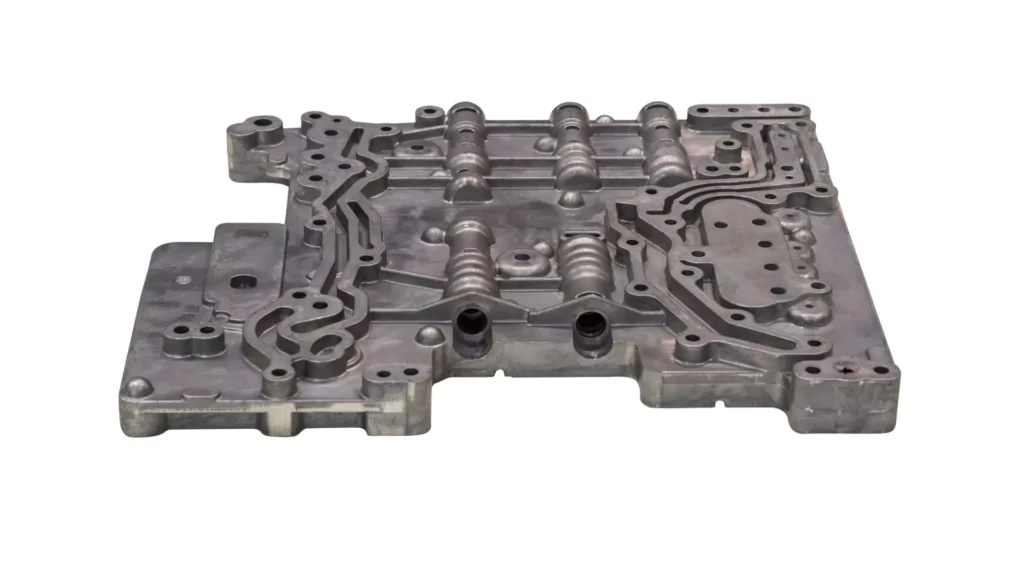
Grades of Aluminum Die Casting
Aluminum die casting utilizes various grades of aluminum alloys, each offering different properties:
- A380: This is the most commonly used grade due to its excellent casting characteristics, mechanical strength, and thermal properties. It offers good castability and is cost-effective.
- A383 / ADC12: This grade is great for intricate parts with thin walls and has better corrosion resistance than A380, although it has lower tensile strength.
- A413: Known for its excellent pressure tightness, this grade is ideal for high-pressure applications and offers superior corrosion resistance.
Applications of Aluminum Die Casting
The versatility of aluminum die casting leads to its use in various industries:
- Automotive: Parts such as engine components, transmission cases, and structural components benefit from aluminum's lightweight and strength properties.
- Aerospace: The process is used to create structural parts for aircraft that require precision and strength without adding unnecessary weight.
- Consumer Electronics: Aluminum die castings are found in laptops, smartphones, and other devices, where their thermal properties and sleek finishes are highly valued.
- Industrial Machinery: Manufacturers rely on die-cast aluminum parts for their reliability and resistance to harsh conditions.
Cost of Aluminum Die Casting
The cost of aluminum die casting can vary significantly based on several factors, including the complexity of the part, the volume of production, and the specific aluminum alloy used. Initial tooling costs can range from a few thousand dollars to much higher amounts for complex designs. However, once the tooling is established, the per-unit cost can be very low, making aluminum die casting an economical choice for high-volume production.
Conclusion
Aluminum die casting stands as a cornerstone of modern manufacturing, delivering an exceptional balance of efficiency, precision, and performance. As industries evolve and demand for lightweight, durable components increases, the significance of aluminum die casting will only grow. For those seeking a reliable partner in aluminum die casting, look no further than Align Manufacturing. Their expertise in this innovative process ensures high-quality results tailored to your specific needs.
Align Manufacturing recognizes the growing importance of aluminum die casting in today's evolving industries, where lightweight and durable components are increasingly crucial. As a trusted partner, Align Manufacturing leverages its expertise to deliver high-quality, custom-tailored aluminum die-castings that meet the unique demands of your specific applications.
FAQs
Aluminum die casting has several environmental advantages compared to other casting methods like sand casting and investment casting. One of the primary benefits is the recyclability of aluminum. Aluminum can be recycled indefinitely without losing its properties, which significantly reduces waste and energy consumption associated with raw material extraction and processing.
Furthermore, die casting typically produces less scrap material compared to sand casting, where excess sand can lead to greater waste. Additionally, advancements in die casting technology are leading to more energy-efficient processes, further minimizing the environmental footprint.
Aluminum die casting, developed in the early 20th century, has become a cornerstone in manufacturing due to its efficiency and the superior properties of aluminum alloys. The process involves injecting molten aluminum into steel molds under high pressure, enabling the rapid production of complex, high-precision parts. Aluminum's inherent corrosion resistance, high thermal and electrical conductivity, and excellent strength-to-weight ratio make it a preferred material across various industries.
Industries Utilizing Aluminum Die Casting:
- Automotive: Engine components, transmission housings, and structural parts.
- Aerospace: Aircraft fittings and components requiring precision and reliability.
- Electronics: Housings and heat sinks benefiting from aluminum's conductivity.
- Consumer Goods: Appliance parts and handheld device enclosures.
According to statistics, the global aluminum die casting market is set to significantly expand. In 2024, it was valued at $31.37 billion. Projections indicate a substantial growth trajectory, reaching an estimated $66.28 billion by 2032. This translates to a compound annual growth rate (CAGR) of 9.80% throughout the forecast period from 2025 to 2032.
This growth is driven by increasing demand in the automotive sector for lightweight, fuel-efficient vehicles, as well as expanding applications in industrial and consumer products.
Aluminum die casting's combination of efficiency, precision, and material advantages continues to make it a popular choice for manufacturers aiming to produce high-quality components across diverse sectors.
Several innovations are shaping the future of aluminum die casting, including advancements in automation and robotics, which enhance production efficiency and precision. New materials, such as advanced aluminum alloys and metal matrix composites, are being developed to improve the mechanical properties of die-cast parts. Additionally, there is a growing emphasis on improving recycling techniques to facilitate the reuse of aluminum scrap generated during the die casting process. These innovations not only streamline manufacturing but also contribute to sustainability goals by reducing waste and energy consumption.
The choice of aluminum alloy significantly impacts the die casting process and the properties of the final product. Different alloys have varying melting points, fluidity, and mechanical properties, which can influence the casting process's efficiency and the quality of the parts produced. For example, alloys like A380 are commonly used due to their excellent castability and mechanical strength, making them suitable for a wide range of applications. On the other hand, alloys like A413 offer superior pressure tightness and corrosion resistance, making them ideal for specific high-pressure applications. When selecting an alloy, factors such as the desired mechanical properties, application requirements, and cost considerations must be taken into account.
Yes, aluminum die casting can be used to create parts with very tight tolerances, but there are limitations. The inherent nature of the die casting process allows for high precision, typically within ±0.005 inches for most applications. However, achieving extremely tight tolerances may require additional machining or specific techniques, such as using sliding cores or advanced mold designs. It's essential to work closely with experienced manufacturers who can implement best practices in design and production to meet stringent tolerance requirements while ensuring the efficiency and cost-effectiveness of the process.