Posts by Casey Ross
What is Gravity Die Casting?
Gravity die casting is a metal casting technique that uses gravity rather than external pressure to fill a mold. In this process, molten aluminum is poured into a steel or iron mold, known as a "die," where it flows down into the mold cavity under the force of gravity. This method differs from other types of casting, such as high-pressure die casting, as it relies solely on the natural pull of gravity, resulting in less turbulent flow and fewer air pockets. The result is a dense, high-quality metal part with excellent dimensional accuracy and strength, making it especially suitable for components requiring durability and precision.
The process achieves tolerances of ±0.3mm to ±0.5mm, with wall thickness capabilities ranging from 3mm to 20mm. Parts can range from small components weighing 0.1 kg to larger pieces up to 100 kg, offering remarkable versatility in production capabilities.
Compared to sand casting, gravity die casting is more efficient in terms of both material use and production time. The reusable steel or iron molds used in gravity casting allow for rapid production cycles and consistent quality across batches, making it a cost-effective solution for medium-to-high volume production runs.Its ability to produce parts in quantities ranging from 250 to 50,000 units per annum makes it a popular choice.This adaptability is achieved through its efficient use of resources and streamlined production cycles.
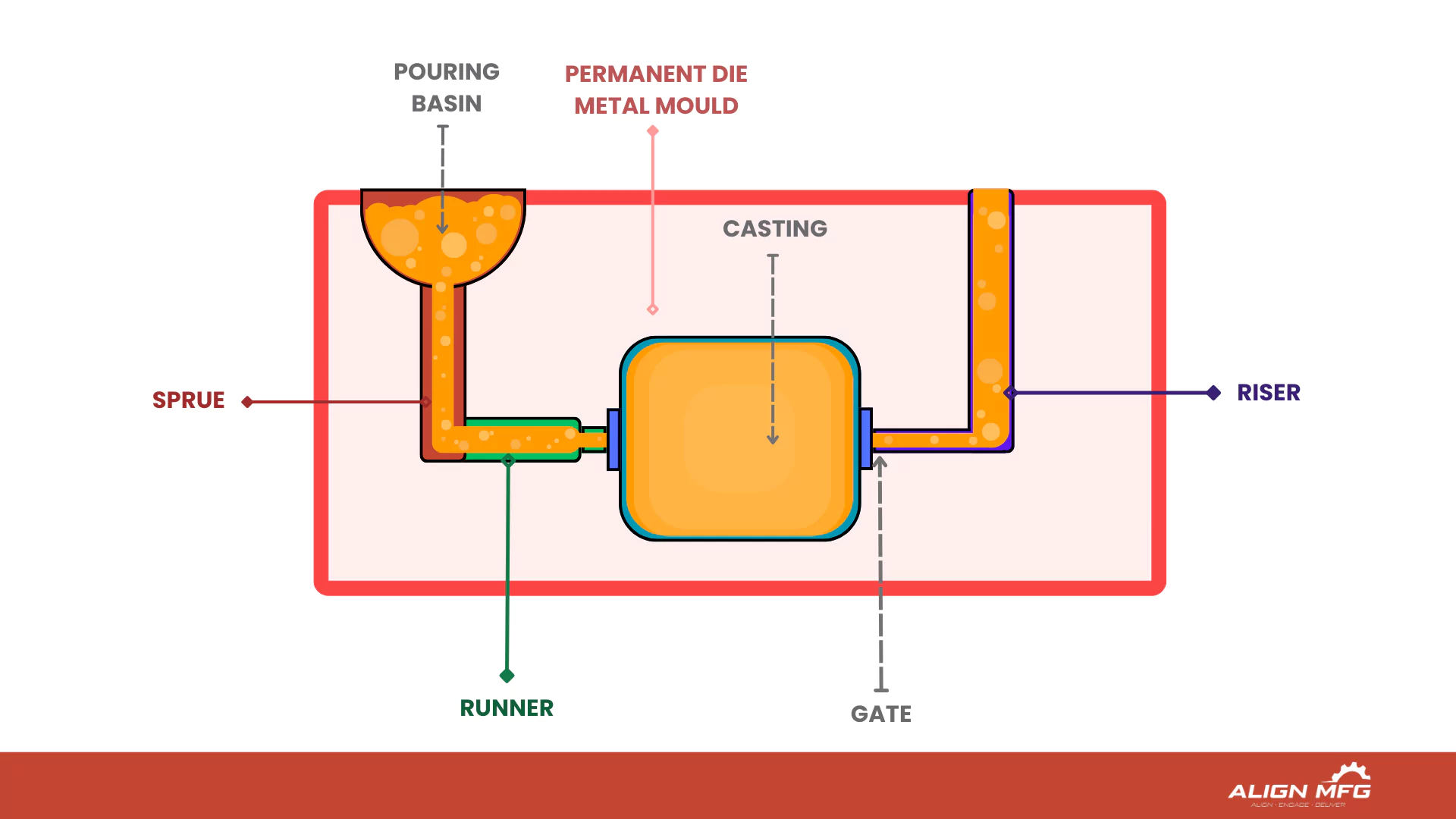
Process of Aluminum Gravity Die Casting
The aluminum gravity die casting process is straightforward yet precise, requiring careful handling and skilled workmanship to ensure optimal results. Here’s a step-by-step breakdown of how the process works:
1.Preparing the Mold
The process begins with preheating the die to temperatures between 200-300°C to prevent thermal shock and ensure smooth flow of molten aluminum, which is typically heated to 650-750°C. Lubricants are applied to the mold to help with release after solidification. The mold design incorporates specific features like draft angles of 2-3° for external surfaces and strategically placed parting lines to ensure optimal results."
2.Pouring the Molten Aluminum
Once the mold is ready, molten aluminum is poured into the mold cavity. As gravity pulls the molten metal into every corner of the mold, it begins to fill the cavity, shaping the metal according to the mold’s design. This step requires precise control to ensure an even flow and avoid air pockets.
3.Solidification and Cooling
After pouring, the aluminum is left to solidify within the mold. The cooling phase is crucial, as controlled cooling can impact the material's final properties, such as its strength and structural integrity. Faster cooling generally produces finer grain structures, which can enhance the material's durability.
4.Removing the Casting
Once the metal has solidified and cooled to a manageable temperature, the mold is opened, and the casting is removed. Any residual material, such as sprues or runners, is trimmed off in preparation for the finishing process.
5.Finishing and Inspection
The final casting may go through secondary operations like machining, polishing, or surface treatments to achieve the desired finish and precision. Each part undergoes inspection to ensure it meets quality standards and specifications before moving on to the next phase.
Advantages of Aluminum Gravity Die Casting
Aluminum gravity die casting offers several distinct advantages that make it an attractive choice for various industries. Here are some of the key benefits:
- High Dimensional Accuracy
Gravity die casting produces components with precise dimensions and excellent surface finishes, reducing the need for additional machining. This accuracy is ideal for parts that must meet tight tolerances and specifications.Compared to alumnium sand casting - Superior Strength and Density
Quality control is paramount in gravity die casting. The process includes comprehensive testing methods such as X-ray inspection, pressure testing, and dimensional verification to prevent common defects like porosity and shrinkage. Surface finishing options range from as-cast finish to various post-processing treatments including machining, coating, and painting, depending on the application requirements. - Cost-Effective for Medium-to-High Production Volumes
The reusable nature of steel or iron molds makes gravity die casting cost-effective for medium-to-high production runs. The upfront investment in the mold is offset by the long-term savings from its reusability and the consistency it provides. - Enhanced Mechanical Properties
Components produced by gravity die casting generally exhibit better mechanical properties compared to sand-cast parts, thanks to the controlled cooling and reduced air entrapment. These properties make gravity die-cast parts suitable for applications where durability and longevity are critical. - Eco-Friendly and Less Material Waste
Gravity die casting tends to produce less material waste than sand casting, as the molds can be reused multiple times. The efficiency of the process also reduces the need for excess metal, making it more environmentally friendly. - Improved Production Speed
The rapid cooling time of metal molds in gravity die casting allows for faster production cycles, making it a practical choice for projects needing quick turnarounds without sacrificing quality.
Aluminum Gravity Die Casting Applications
Aluminum gravity die casting is widely used across various industries, especially in sectors where precision, strength, and reliability are paramount. Some of the common applications include:
- Automotive Industry
Gravity die casting is often used to create engine components, transmission cases, and suspension parts. Aluminum alloy A357 is particularly favored for its higher strength properties, while A356 is chosen for parts requiring excellent fluidity and corrosion resistance. The process's ability to maintain uniform wall thickness and proper corner radii makes it ideal for complex automotive components. - Aerospace Industry
Aerospace manufacturers use gravity die casting for parts that require excellent mechanical properties and corrosion resistance. Components like housings, brackets, and supports benefit from the dimensional accuracy and structural integrity of gravity-cast aluminum. - Industrial Machinery
Many machinery parts, including hydraulic components, pump housings, and gearboxes, are produced using gravity die casting. Using alloys like A356 for its excellent fluidity and corrosion resistance, these components can be manufactured with wall thicknesses ranging from 3mm to 20mm. The process ensures uniform material properties through controlled cooling and proper mold design, incorporating features like strategic parting lines and adequate draft angles (2-3°) for easy part removal. - Consumer Electronics and Appliances
Aluminum gravity die casting is also common in consumer electronics and home appliances, where it’s used to create durable, lightweight casings and structural parts. The method’s accuracy and finish quality are ideal for products with aesthetic and functional requirements. - Medical Equipment
Medical devices and equipment that require reliable, corrosion-resistant parts often incorporate gravity die-cast aluminum components. From casings to support structures, gravity die casting ensures that medical equipment meets high standards for both safety and durability. - Marine Industry
Due to aluminum’s natural corrosion resistance and strength, gravity die-cast aluminum parts are widely used in marine applications such as motor housings, brackets, and propeller blades. These components benefit from the durability and resistance to seawater corrosion that gravity casting provides.
Types of components
Gravity Die Casting (GDC), which is typically used for producing medium to high-precision parts with moderate complexity, here are the relevant components that Align Manufacturing could produce using GDC:
1. Oil & Gas Industry Components
- Flanges: High-strength parts used to connect pipes and equipment, benefiting from the precision and consistency of GDC.
- Valve Bodies: Ideal for controlling fluid flow, requiring dimensional accuracy and durability.
- Impellers: Used in pumps for fluid movement, made with fine surface finishes and low porosity offered by GDC.
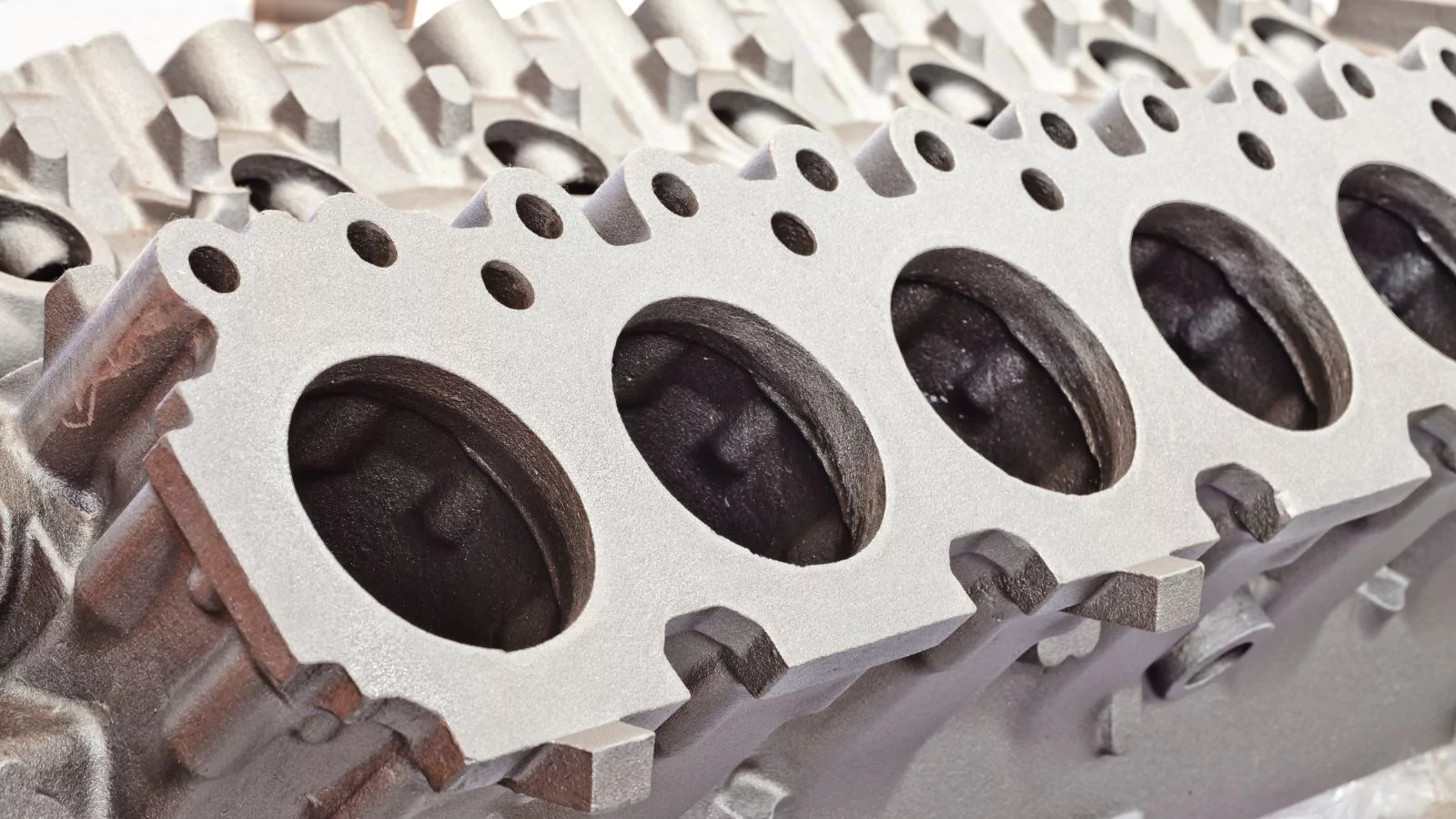
2. Truck & Trailer Industry Components
- Suspension Parts: Durable components benefiting from GDC's ability to produce parts with high structural integrity.
- Engine Brackets: Precision-engineered to securely mount engines while reducing vibrations.
- Brake Rotors: Made with precise dimensions and excellent surface finishes for consistent braking performance.
- Hubs: Cast with high accuracy to support smooth wheel rotation.
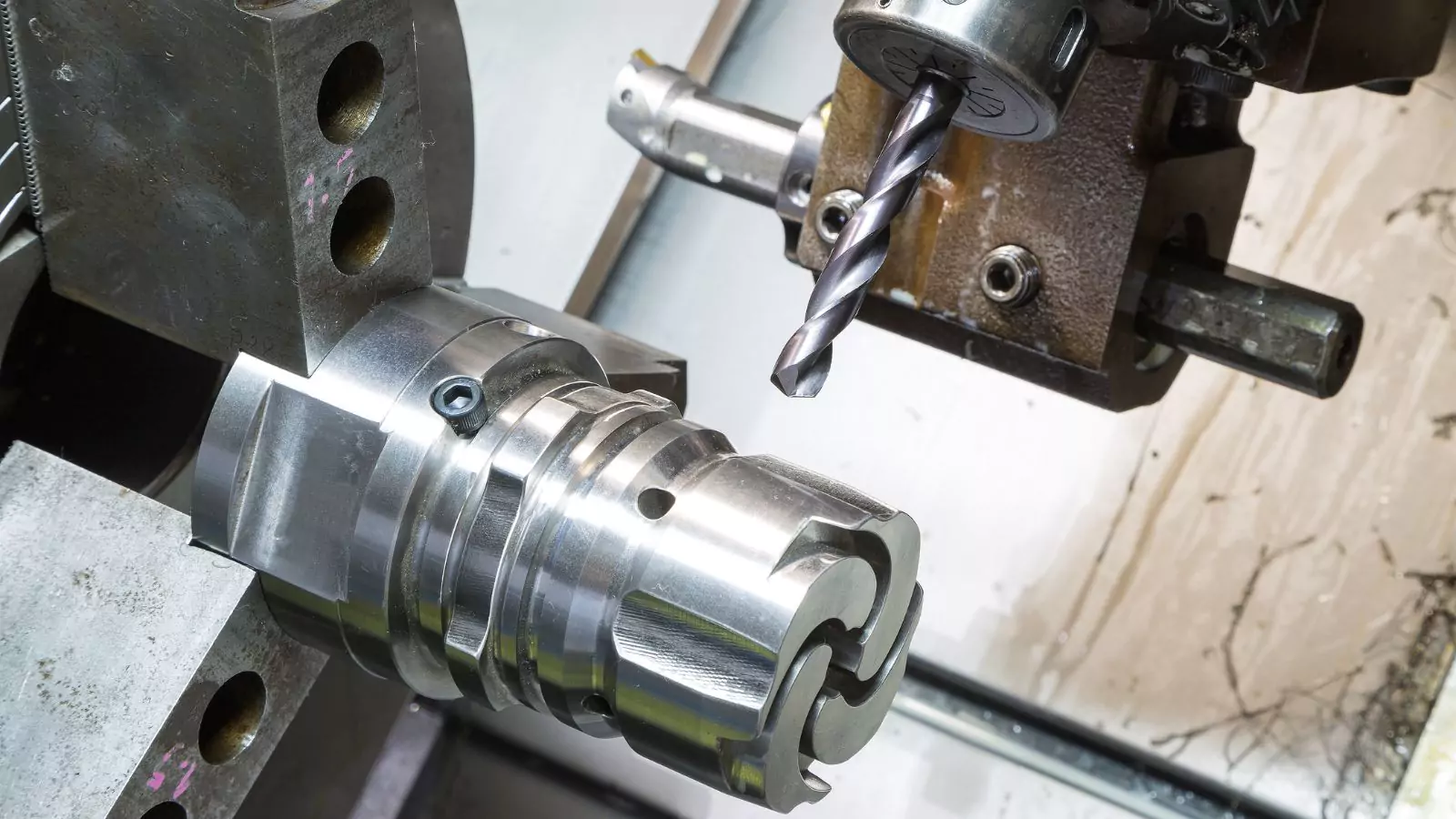
- Industrial Components
- Manhole Covers: High-strength covers that can be precisely cast for consistent performance.
- Vent Release Valves: Suitable for precise control of gases or liquids, taking advantage of GDC’s low porosity properties.
Best Practices and Quality Control
- Mold Design Optimization:
- Proper gating system design for smooth metal flow
- Strategic placement of cooling channels
- Adequate venting to prevent gas entrapment
- Draft angles of 2-3° minimum for external surfaces
- Temperature Management:
- Die preheating to 200-300°C
- Maintaining consistent pouring temperature (650-750°C)
- Controlled cooling rates for optimal material properties
- Quality Assurance:
- X-ray inspection for internal defects
- Pressure testing for leakage
- Dimensional verification using precision measurement tools
- Surface finish inspection and testing
- Surface Finishing Options:
- As-cast finish for non-critical surfaces
- Machining for precise dimensional requirements
- Various coating options for enhanced durability
- Paint preparation and application when required
Conclusion
Aluminum gravity die casting remains a vital process for producing high-quality, precise components across various industries. Its unique combination of strength, lightweight properties, and cost-effectiveness make it ideal for applications ranging from automotive to medical equipment. By using gravity to guide molten metal into molds, this casting method achieves impressive dimensional accuracy and surface finish, meeting the needs of industries that demand reliability and durability.
If you’re interested in learning more about other casting methods and how they compare, explore the wide range of casting processes available on Align Manufacturing’s website. Each method offers unique benefits tailored to specific applications, helping you find the perfect solution for your manufacturing needs.
FAQs on Gravity Die Casting
Gravity die casting primarily uses non-ferrous metals, with aluminum alloys being the most common. Specific alloys include:
- A356: Excellent for general-purpose applications, offering good fluidity and corrosion resistance
- A357: Higher strength applications requiring superior mechanical properties
- Other materials include zinc alloys, magnesium alloys, and some copper-based alloys Each material requires specific die temperatures and pouring temperatures for optimal results."
Gravity die casting offers distinct advantages in terms of precision (±0.3mm to ±0.5mm tolerances) compared to sand casting, though it may be slower than high-pressure die casting. The initial tooling cost is higher than sand casting but lower than high-pressure die casting. Part size capabilities (up to 100 kg) and production volumes (250-50,000 units annually) position it perfectly for medium-to-high volume production runs."
Manual Process Time: While manual gravity die casting offers superior precision (±0.3mm tolerance), it requires longer production cycles compared to high-pressure die casting.
Design Restrictions: Complex geometries with deep recesses or intricate internal features can be challenging to produce, as the process relies on natural metal flow. Wall thickness must be carefully controlled between 3-20mm for optimal results.
Initial Investment: Tooling costs are significant due to the need for high-quality steel molds designed with proper gating systems, cooling channels, and venting.
Temperature Management: Precise control of both die temperature (200-300°C) and molten metal temperature (650-750°C) is crucial for quality, adding complexity to the process.
Industries that require lightweight, high-strength components benefit greatly from aluminum gravity die casting. These include the automotive, aerospace, industrial machinery, consumer electronics, medical equipment, and marine industries. Each of these sectors relies on the process to produce parts that are durable, corrosion-resistant, and capable of meeting stringent performance standards.
Gravity die casting is relatively sustainable compared to other casting methods. The reusable molds minimize waste, and the aluminum used is recyclable, reducing the environmental impact. Additionally, the process’s efficiency in terms of material usage and energy consumption contributes to its eco-friendliness. Many manufacturers prioritize recycling aluminum and repurposing materials to make the process even more sustainable.
Friend-shoring, Near-shoring, Reshoring, and Other Buzzwords
Supply chain landscape is evolving rapidly, fueled by shifting geopolitics, emerging technologies, and changing consumer demands. Terms like friend-shoring, near-shoring, and re-shoring are gaining traction as businesses seek to adapt. But what do these buzzwords mean, and how do they impact global supply chain strategies?
In this article, we'll explore these key concepts, compare their benefits, challenges, and applications, and provide actionable insights for supply chain professionals. By the end, you'll understand why companies like Align Manufacturing are leading the way in navigating these trends.
What is Friend-shoring?
Friend-shoring is the strategic relocation of supply chains to countries that share aligned political, economic, or ideological interests. This emerging approach addresses growing concerns over geopolitical risks, fostering economic collaboration among nations that are considered reliable allies.
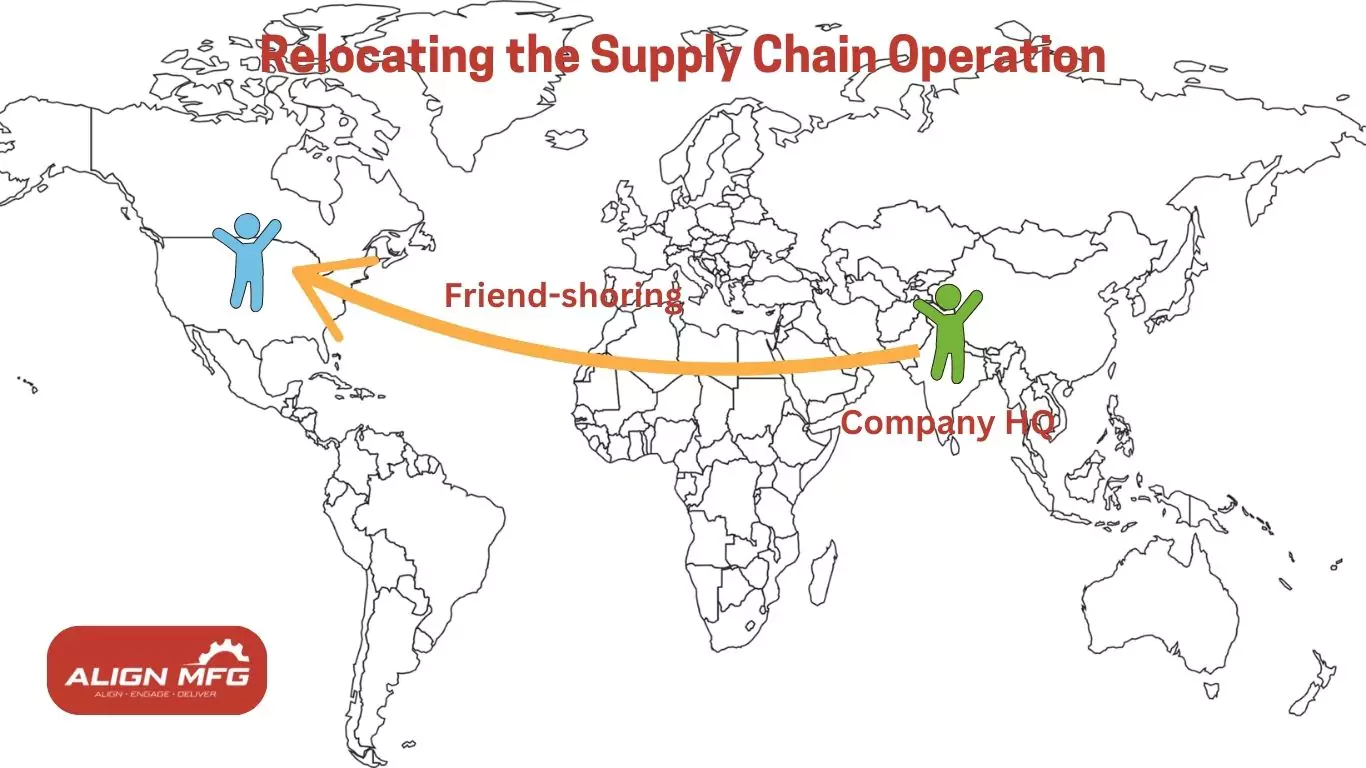
Key Objectives of Friend-shoring:
- Mitigating Risks: By focusing on countries with stable governance and aligned values, businesses minimize the risk of trade disruptions caused by geopolitical tensions.
- Strengthening Alliances: Encourages mutual economic growth and reinforces trust among allied nations.
- Reducing Overdependence: Diversifies supply chains, reducing reliance on politically unstable or adversarial countries.
Benefits of Friend-shoring:
- Reduced Geopolitical Risks: Relocating supply chains to trusted countries ensures continuity even during global tensions.
- Improved Economic Collaboration: Aligning trade policies and practices fosters smoother operations and better partnerships.
- Examples in Action: Semiconductor manufacturers are a notable example, shifting production to countries within alliances like NATO to reduce dependency on regions with volatile relations, such as China.
Challenges of Friend-shoring:
- Finding Reliable Partners: Evaluating a nation’s infrastructure, workforce skills, and regulatory environment is critical.
- Regulatory Variations: Even allied countries may have differing legal frameworks, complicating compliance.
- Cost Implications: While offering political stability, these shifts may incur higher costs compared to traditional offshoring.
Friend-shoring is gaining momentum as nations and businesses aim to build resilient supply chains in the face of geopolitical instability. Its focus on allied nations offers a pragmatic solution for long-term sustainability.
Exploring Near-shoring
Near-shoring refers to the relocation of supply chain operations closer to a company’s home market. This strategy improves operational efficiency by reducing transportation costs and delivery times, offering an agile response to market demands.
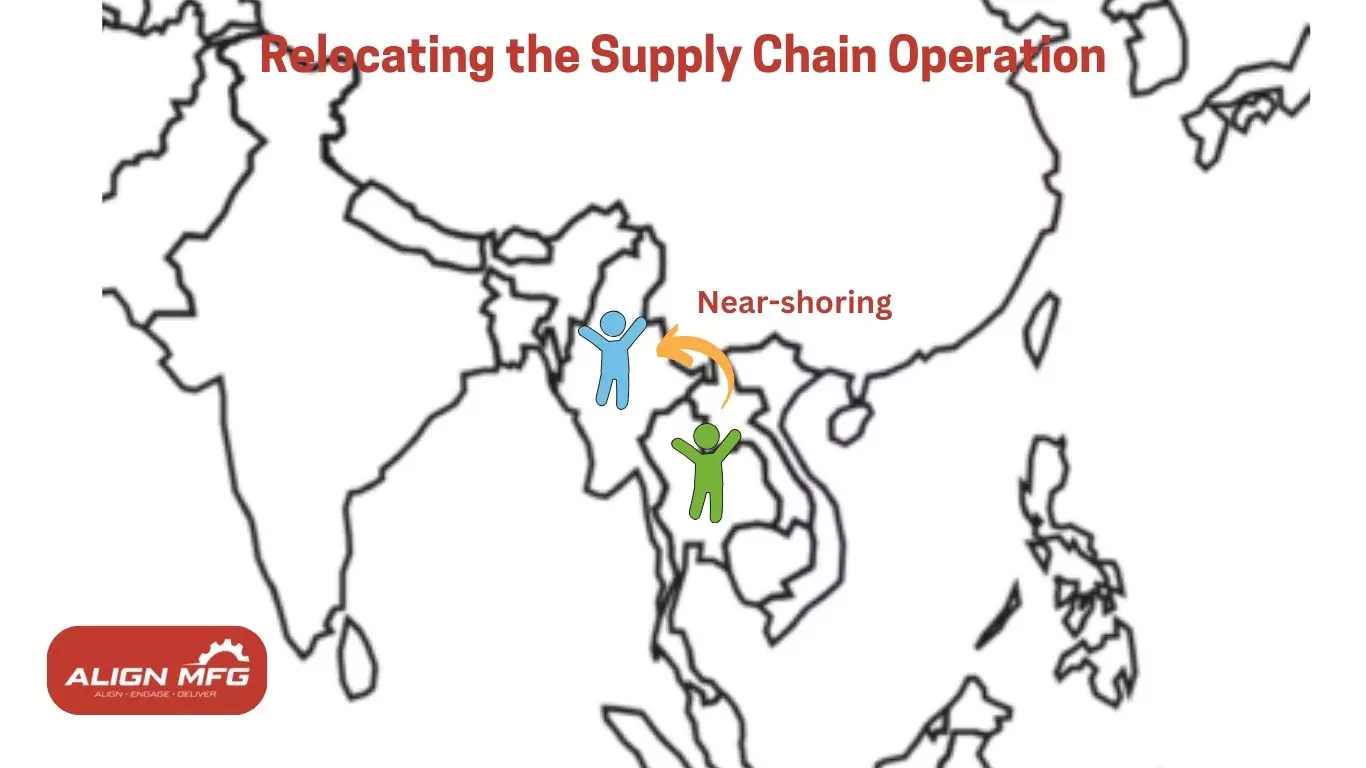
Core Principles of Near-shoring:
- Proximity: Operating closer to key markets reduces time-to-market.
- Cost Efficiency: While not as low-cost as offshoring, reduced logistics expenses offset higher labor costs.
- Supply Chain Agility: Faster access to resources and production facilities enhances adaptability.
Benefits of Near-shoring:
- Faster Delivery Times: Shortened supply chains mean quicker access to products for consumers.
- Reduced Transportation Costs: Geographic proximity lowers shipping and storage expenses.
- Enhanced Collaboration: Being closer geographically often fosters better communication and understanding with suppliers.
Real-World Applications:
- Example: Many U.S. companies are opting to shift operations to Mexico rather than Asia to save on costs and reduce transit delays.
- Case Study: A North American electronics manufacturer reported a 40% decrease in delivery times after relocating operations to Mexico, allowing them to better compete with local rivals.
Challenges of Near-shoring:
- Labor Costs: Though lower than home markets, labor costs are often higher than traditional offshoring destinations.
- Infrastructure Readiness: Some near-shore countries may lack adequate infrastructure, leading to bottlenecks.
- Supplier Availability: Limited availability of specialized suppliers in certain regions can hinder progress.
Near-shoring is a middle-ground strategy, balancing operational proximity with cost efficiency, making it an attractive option for many industries.
Re-shoring: Bringing It Home
Re-shoring, also called onshoring, involves moving manufacturing or production processes back to the company’s home country. This strategy emphasizes boosting domestic economic activity, enhancing brand reputation, and reducing external dependencies.
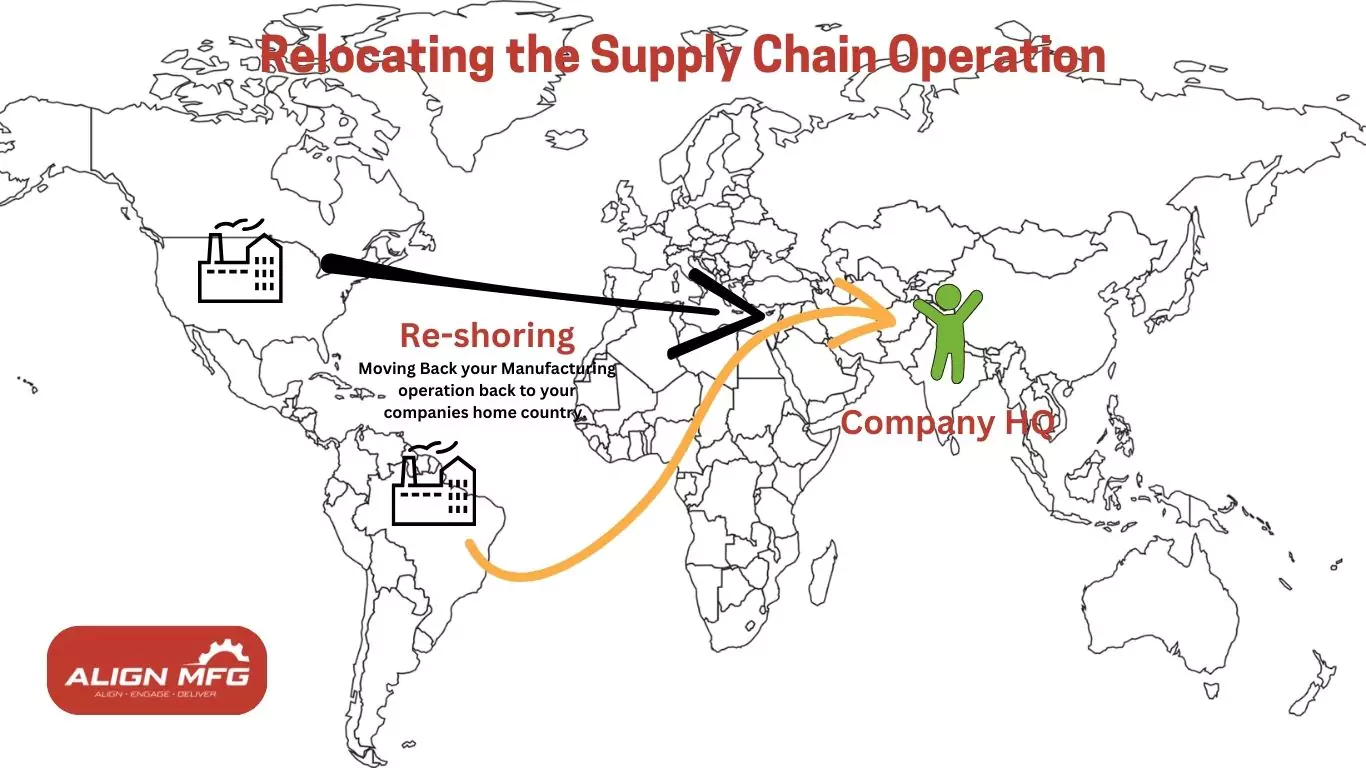
Why Companies are Re-shoring:
- Government Incentives: Many governments provide tax breaks, grants, or subsidies to encourage businesses to bring operations back home.
- Consumer Demand: “Made in the USA” or similar homegrown labels resonate strongly with consumers, fostering trust and brand loyalty.
- Supply Chain Stability: By operating domestically, businesses avoid global shipping uncertainties and reduce overreliance on external suppliers.
Benefits of Re-shoring:
- Job Creation: Brings employment opportunities back to domestic markets.
- Improved Quality Control: Having production closer allows for stringent oversight and quality assurance.
- Enhanced Resilience: Reduces the risk of disruptions caused by international supply chain interruptions.
Examples in Practice:
- Apple: While much of its manufacturing remains overseas, Apple has partially re-shored some production of key components to the U.S., ensuring compliance with local quality standards.
- Boeing: Relocated significant operations back to U.S. soil to address concerns over outsourcing quality and supply chain resilience.
Challenges of Re-shoring:
- Higher Costs: Domestic labor is generally more expensive compared to traditional offshore or near-shore options.
- Logistical Complexity: Transitioning existing supply chains to domestic locations involves significant planning and investment.
- Scaling Issues: Home markets may lack the resources or infrastructure to support large-scale operations in certain industries.
Re-shoring is often seen as a long-term investment, prioritizing quality, reliability, and local economic growth over immediate cost savings.
Offshoring: The Precursor
Offshoring refers to outsourcing production or services to countries with lower labor and operational costs. This practice, dominant in the late 20th century, was a cornerstone of globalization and remains a key strategy for cost reduction.
Why Offshoring Became Popular:
- Cost Savings: Access to cheaper labor markets and lower production costs made offshoring highly lucrative.
- Scalability: The ability to rapidly scale operations in manufacturing hubs like China or India.
- Global Markets: Many companies capitalized on both low production costs and new consumer markets in these regions.
Benefits of Offshoring:
- Significant Cost Reductions: Labor and operational expenses are substantially lower in many developing nations.
- Increased Capacity: Access to a larger, cost-effective workforce allows companies to expand rapidly.
- Global Reach: Establishing a presence in foreign markets often aligns with the growth of a global consumer base.
Current Challenges with Offshoring:
- Supply Chain Disruptions: Events like COVID-19 exposed vulnerabilities in relying on global supply chains.
- Reputation Concerns: Companies face criticism over ethical concerns, such as poor labor conditions in certain regions.
- Geopolitical Risks: Trade wars, sanctions, and international conflicts can severely impact operations.
While offshoring remains a vital strategy for many businesses, its drawbacks are causing companies to reconsider alternative approaches, such as near-shoring and friend-shoring, to mitigate risks and improve resilience.
Benefits of These Strategies
Strategy | Cost | Risk Mitigation | Delivery Speed |
Friend-shoring | Moderate | High | Moderate |
Near-shoring | High | High | High |
Re-shoring | Highest | Very High | Highest |
Current Trends in Supply Chain Strategies
Modern strategies emphasize regionalization, automation, and sustainability. For example:
- Digital twins for monitoring supply chains.
- Blockchain for transparency.
- Geopolitical events like Brexit are increasing regionalization efforts.
Future Predictions
The future of supply chain management will likely see:
- Increased investment in technology like AI for forecasting.
- Expansion of regional trade networks.
Role of Align Manufacturing in Supporting Strategies
Align Manufacturing offers expertise in simplifying these transitions by:
- Streamlining logistics through technology.
- Providing end-to-end supply chain solutions tailored to business needs.
Why Align Manufacturing is Your Partner
With its expertise in supply chain optimization, Align Manufacturing helps businesses stay ahead in a volatile global market. Their custom solutions, supported by cutting-edge technology, ensure smooth implementation of these strategies.
Conclusion
Adapting your supply chain strategy isn’t just a competitive advantage—it’s a survival necessity. Approaches like friend-shoring, near-shoring, and re-shoring enable businesses to enhance resilience, optimize costs, and strengthen their market positioning. However, each strategy comes with unique benefits and challenges, requiring careful evaluation to align with your business goals.
Companies like Align Manufacturing make navigating these transitions seamless, leveraging their expertise in supply chain optimization and cutting-edge technology to craft tailored solutions. Whether you’re mitigating risks, reducing delivery times, or enhancing supply chain agility, Align Manufacturing is your trusted partner for turning strategy into success.
FAQ
- Friend-shoring: Relocates operations to allied countries with shared political and economic values to minimize geopolitical risks.
- Near-shoring: Moves operations closer to the home market to reduce transportation costs and improve delivery times.
- Re-shoring: Brings manufacturing or production back to the company’s home country for improved quality control and local job creation.
Companies are prioritizing resilience and risk mitigation over cost savings. Friend-shoring and near-shoring reduce dependence on volatile regions, improve supply chain agility, and address concerns over geopolitical instability and supply chain disruptions exposed during events like COVID-19 and trade wars.
Re-shoring benefits include:
- For businesses: Improved quality control, reduced shipping uncertainties, and enhanced brand reputation with "Made in Home Country" labeling.
- For the economy: Boosts domestic employment, supports local industries, and promotes economic growth.
The decision depends on several factors:
- Cost considerations: Offshoring is often the cheapest but comes with higher risks.
- Proximity needs: Near-shoring suits businesses requiring quicker delivery times.
- Geopolitical concerns: Friend-shoring reduces risks by focusing on stable and allied regions.
- Brand reputation: Re-shoring appeals to consumers seeking local products.
A detailed cost-benefit analysis and risk assessment are critical before making a decision.
Industries that rely heavily on timely delivery, quality control, or geopolitical stability benefit the most, such as:
- Healthcare: Ensures quick delivery of medical supplies.
- Automotive: Reduces risks of disruptions in complex, multi-tier supply chains.
- Technology: Protects intellectual property by operating in trusted locations.
- Retail and E-commerce: Improves delivery speed to consumers by relocating closer to home markets.
Secure Your Manufacturing Future Beyond China
The complex interplay of economic, demographic, and geopolitical factors necessitates a strategic approach for manufacturers currently reliant on China. The economic stability, favorable demographic trends, and business-friendly environments of Southeast Asia and South Asia, particularly in Thailand, Vietnam, and India, offer compelling alternatives.
These locations provide significant advantages, including robust growth potential, competitive labor costs, and supportive government policies. Each country has its own unique strengths, making it essential to consult with experts before deciding on a new location.
Immediate Action Required
OEMs need to act now—waiting until the November election is too late. As we have stated above, several factors will make future project placements increasingly challenging:
-
- Factory Capacity: The best factories will fill up quickly. Delaying could result in having to work with less desirable manufacturing partners.
- Predatory Pricing: Factories price to market, and without a head start, you may face prices that benchmark against China + 60%, not just China.
- Potential EU Tariffs: These could further decrease available capacity.
- China +1 Orders: The surge of China +1 orders following the tariffs will consume a significant portion of available capacity.
- Tariff Costs: Importers have already paid substantial tariffs since the trade war began. Acting now can prevent further financial strain.
- Lead Time: The process of making tooling, obtaining T1 part approval, and the combined production and shipping time can take up to 6-8 months before full production orders begin to be delivered.
Proactively diversifying supply chains and relocating can mitigate the risks associated with over-reliance on China and leverage the opportunities in dynamic and growing markets. This strategic shift not only enhances supply chain resilience but also positions OEMs for long-term success in the evolving global landscape, particularly in areas like metal component manufacturing and machining components.
Align Manufacturing: Your Boots on the Ground in South & Southeast Asia
We encourage OEMs to take immediate action to diversify their supply chains into South and Southeast Asia. By partnering with Align Manufacturing, companies will receive comprehensive support services and local expertise throughout the transition process.
For more information and to start your transition with Align Manufacturing, please visit our website or contact us directly. Let us help you relocate your contract manufacturing operations for sustained success in new and exciting markets.
About Align Manufacturing:
Align Manufacturing, headquartered in Singapore and with offices in Bangkok, specializes in delivering high-quality industrial production solutions. Our expertise ranges from intricate sand casting and robust forging to efficacious stamping and state-of-the-art precision machining. This diverse capability ensures that we meet the complex needs of our clients with meticulous attention to detail and seamless communication. Partner with Align Manufacturing for efficient and precise manufacturing outcomes tailored to your project's success.
Note:
This article is part of an ongoing series exploring why US-based companies need to move their manufacturing operations outside of China.
To read the previous article, click HERE.
To download the entire series as a report, click the button below.
Success Stories of Clients Who Have Transitioned with Align MFG
Align Manufacturing has successfully helped many clients transition their manufacturing out of China. These case studies highlight the challenges faced, the solutions provided, and the successful outcomes achieved.
Client 1: Success Story in Thailand
Investment Casting parts for use in the braided hose manufacturing industry
Overview of the Project and Its Challenges: This client, a manufacturer of machines used to produce hydraulic hoses, faced significant challenges due to the extremely tight tolerances required for these parts (+0.0000”, -0.0002”). The parts are produced using Lost Wax Investment Casting and are critical wear components that must withstand hundreds of revolutions per minute.
The project faced three main challenges: technical parameters, cost, and volume. The technical parameters included requirements for surface roughness testing, concentricity, and perpendicularity. Additionally, these machines are not mass-produced, with an estimated annual usage of around 200 pieces each, and had an aggressive target price. Many factories were unwilling to take on such a small order, as the typical minimum order quantity for parts of this size is around 1,000 pieces.
How Align Manufacturing Facilitated the Transition: The client had been manufacturing these parts in China for over 20 years but struggled to find a vendor outside of China who could meet the technical specifications and cost requirements. Align Manufacturing leveraged its relationships to place the parts with an AS9100 (Aerospace) certified foundry in Thailand. We worked closely with the client to discuss the correct CNC machining processes needed to achieve the required tolerances. Additionally, we proposed consolidating shipments with another order from a different factory in Northern Thailand, reducing shipping costs by thousands of dollars per shipment. This strategy involved combining shipments between our parts and a client's existing supplier in Thailand, offering further logistics savings.
Results and Benefits: By moving production out of China, the client saved tens of thousands of dollars annually on just these two lower volume parts, avoiding the 25% tariff. The consolidation strategy also significantly lowered shipping costs, enhancing overall cost efficiency.
Client 2: Success Story in Vietnam
High Pressure Die Casting Vent Release Valve
Overview of the Project and Its Challenges: This client, one of the largest gas station supply companies in the US, needed a Vent Release Valve, a critical component that prevents gasoline overflow and requires rigorous testing and government approval. Previously manufactured as a Sand Cast part in China, the quantities were high enough to consider High Pressure Die Casting (HPDC), which offers lower unit costs despite higher tooling expenses.
How Align Manufacturing Facilitated the Transition: Align Manufacturing proposed switching to HPDC to reduce long-term costs. Although initially hesitant about the high tooling costs, the client saw the value of the proposed approach after we demonstrated the long-term savings. The first sample testing was approved and the client subsequently requested design revisions. We modified the tooling and delivered an updated sample that also passed testing.
Results and Benefits: The transition from Sand Casting to HPDC halved the unit cost and eliminated the 301 tariff, saving the client hundreds of thousands of dollars annually. Additionally, the part now has a much better finish, enhancing its aesthetic appeal.
Client 3: Success Story in India
Ductile Iron Spill Containment System
Overview of the Project and Its Challenges: This client, a company in the petroleum industry, was looking for a new supplier for a Ductile Iron Spill Containment System, one of their highest volume products. This system consisted of two castings engineered with tight tolerances to fit within each other and required compatibility with vent fittings and various engineered gaskets, seals, and O-rings. The client wanted to match their China pricing, integrate design revisions to lower part weight and improve aesthetics, and meet a 1,000-hour Salt-Spray Test (SST) requirement.
Finding a coating subcontractor in Western India who could commit to 1,000-hour SST resistance on cast iron was challenging. Cast iron is prone to rust, and the desired hammertone finish added extra areas for moisture to pool. We leveraged our relationship with a partner's office to prescribe a coating protocol that met our requirements, including a zinc phosphate pre-treatment, e-coat primer, and hammertone powder coat, and identified a coating subcontractor who could meet these needs.
How Align Manufacturing Facilitated the Transition: We worked with the client through two rounds of mold revisions and performed three rounds of salt spray testing to ensure compliance with specifications. Our efforts ensured that the parts met all technical and aesthetic requirements.
Results and Benefits: By relocating production to India, the client achieved significant cost savings by eliminating the 301 tariffs. Additionally, establishing a basis for regular container exports increased opportunities for consolidation with additional cast iron products and other castings and forgings supplied from Western India.
Proven Success in Strategic Manufacturing Relocation
These case studies illustrate how Align Manufacturing has successfully guided various clients through the complex process of relocating their manufacturing operations from China to more favorable environments in Thailand, Vietnam, and India. By addressing specific challenges and leveraging local expertise, Align Manufacturing not only ensures a seamless transition but also achieves substantial cost savings and operational efficiencies for our clients in areas like component manufacturing and metal parts manufacturing.
About Align Manufacturing:
Align Manufacturing, headquartered in Singapore and with offices in Bangkok, specializes in delivering high-quality industrial production solutions. Our expertise ranges from intricate sand casting and robust forging to efficacious stamping and state-of-the-art precision machining. This diverse capability ensures that we meet the complex needs of our clients with meticulous attention to detail and seamless communication. Partner with Align Manufacturing for efficient and precise manufacturing outcomes tailored to your project's success.
Note:
This article is part of an ongoing series exploring why US-based companies need to move their manufacturing operations outside of China.
To read the next article, click HERE.
To read the previous article, click HERE.
To download the entire series as a report, click the button below.
Align Manufacturing: Your Partner in Transition Outside of China
As companies increasingly seek alternatives to China for their manufacturing operations due to escalating costs and geopolitical uncertainties, the importance of partnering with a knowledgeable and reliable manufacturing facilitator becomes paramount. Such partnerships are essential for navigating the complex landscape of global production shifts, ensuring not only a smooth transition but also the long-term success and adaptability of manufacturing strategies.
Align Manufacturing is an American-owned and operated company with local operations in Thailand, Vietnam, and India. This unique positioning allows us to offer the best of both worlds: American business practices, combined with local expertise. This deep understanding of regional markets and regulatory requirements ensures that OEMs receive tailored solutions to meet their specific needs in areas such as component manufacturing and parts manufacturing, enhancing operational efficiencies and product quality.
Our team has been living and working in these regions for decades, which sets us apart from many competitors whose personnel might visit occasionally but are primarily based in the US. Our enduring presence ensures a deep understanding of regional markets and regulatory requirements, enabling us to develop much closer relationships with our factories and provide tailored solutions that meet the specific needs of OEMs. We truly serve as 'Your Boots on the Ground,' offering regular, face-to-face interaction with our partners to ensure the highest standards of quality and service.
Comprehensive Capabilities
Align Manufacturing offers a full range of services to support OEMs in their transition from China to Southeast Asia and South Asia. Our capabilities include:
- Site Selection and Feasibility: Helping OEMs identify the most suitable locations for contract manufacturing based on factors such as cost, capability, and logistics concerns.
- Regulatory Compliance: Navigating local regulations to remove friction from setup and operations.
- Supply Chain Management: Providing end-to-end supply chain solutions, including procurement , logistics, and inventory management.
- Project Management: Overseeing every aspect of the production process, from planning and execution to monitoring and optimization.
- Quality Control and Assurance: Implementing rigorous quality control measures to ensure that products meet the highest standards.
We provide OEMs with unparalleled support to ensure a smooth transition and high-quality outcomes. We have successfully assisted many clients making this same transition from China to Southeast Asia or to South Asia. For all clients, we ensure minimal disruption and maximum efficiency in their new production location.
Our project managers oversee every aspect of the transition, from planning and logistics to execution and follow-up, so that all projects are completed on time and within budget.
Effective communication and logistical support are key strengths of Align Manufacturing. We remain in constant contact with our clients, providing regular updates and addressing any concerns promptly. Moreover, our logistical support services include supply chain management, enabling transportation and consolidation from multiple factories in the same container.
About Align Manufacturing:
Align Manufacturing, headquartered in Singapore and with offices in Bangkok, specializes in delivering high-quality industrial production solutions. Our expertise ranges from intricate sand casting and robust forging to efficacious stamping and state-of-the-art precision machining. This diverse capability ensures that we meet the complex needs of our clients with meticulous attention to detail and seamless communication. Partner with Align Manufacturing for efficient and precise manufacturing outcomes tailored to your project's success.
Note:
This article is part of an ongoing series exploring why US-based companies need to move their manufacturing operations outside of China.
To read the next article, click HERE.
To read the previous article, click HERE.
To download the entire series as a report, click the button below.
Key Strategies for Efficient Manufacturing Relocation Outside of China
In light of the escalating trade tensions and economic uncertainties between the US and China, adapting manufacturing locations to more stable regions like Southeast and South Asia has become essential for maintaining competitive advantage. This article explores essential strategies that businesses can employ to ensure an efficient transition away from traditional bases like China to more dynamic regions such as Southeast and South Asia for their metal parts manufacturing and metal components manufacturing. By detailing proactive steps for preparation and our bespoke approach, we outline how businesses can minimize disruptions and optimize operational efficiencies during this critical move.
Preparation by Importers:
- Ensure all drawings and 3D models are up-to-date, including the latest revisions.
- Set a realistic target price based on current market conditions.
- Provide records of any quality issues encountered in previous productions to anticipate and mitigate repeat problems.
- Supply samples for reference to maintain consistency in production quality.
- Detail any proprietary inspection techniques, inspection levels, packing standards, specifications, and acceptance/rejection criteria to align expectations and processes.
Our Approach:
- Align Manufacturing reviews the list of parts clients intend to move, considering the process, material, and quantities to develop a tailored procurement strategy.
- We strive to keep parts geographically consolidated to maximize shipping efficiencies and minimize costs, aiming to fully utilize container capacities up to 44,000 lbs.
- We select vendors based on specific manufacturing processes and material costs, leveraging the strengths of each country:
- For open die forging, vendors in India are preferred due to superior capabilities.
- For precise CNC machined parts, our Vietnamese vendors are optimal.
- For materials like Nickel Bronze, which are expensive in Thailand and Vietnam, we opt for Indian production.
- For high volume orders, location is flexible; for low volume orders, Thailand is more accommodating due to its willingness to accept smaller quantities.
- We advise starting with no-tooling parts where possible to save on both time and expenses, thus streamlining the initial phases of production setup.
Starting with the 'Head' vs. 'Dipping Toes':
Rather than 'dipping their toes' with low volume or less critical components, importers should 'start with the head' by prioritizing high-volume or crucial parts. This strategy leads to:
- Easier placement of initial high-volume projects, setting a solid foundation for subsequent smaller productions.
- Improved pricing leverage, reducing the risks of staying dependent on Chinese manufacturing.
- Simplified logistics through high-volume shipments (FCL), which reduce costs and increase the frequency of just-in-time (JIT) inventory deliveries.
This comprehensive approach not only ensures a smoother transition but also maximizes efficiency and cost-effectiveness during the relocation process.
About Align Manufacturing:
Align Manufacturing, headquartered in Singapore and with offices in Bangkok, specializes in delivering high-quality industrial production solutions. Our expertise ranges from intricate sand casting and robust forging to efficacious stamping and state-of-the-art precision machining. This diverse capability ensures that we meet the complex needs of our clients with meticulous attention to detail and seamless communication. Partner with Align Manufacturing for efficient and precise manufacturing outcomes tailored to your project's success.
Note:
This article is part of an ongoing series exploring why US-based companies need to move their manufacturing operations outside of China.
To read the next article, click HERE.
To read the previous article, click HERE.
To download the entire series as a report, click the button below.
Why Manufacturers Need to Get Out of China Now: Strategic Insights from Align Manufacturing
In this video, Casey Ross and Benjamin Unruh from Align Manufacturing and Alex Chiu from Maesot Heavy Industries discuss why manufacturers must urgently consider moving their operations out of China. They explore the impact of geopolitical tensions, rising tariffs, and the key strategies for ensuring a smooth transition to Southeast and South Asia.
Casey: Hi everyone, I'm Casey Ross, Partner at Align Manufacturing. I'm here today with Benjamin Unruh, Partner at Align Manufacturing, and Alex Chiu, Deputy General Manager at Maesot Heavy Industries, to discuss the critical shifts in global manufacturing landscapes and the strategic importance of relocating production from China to more favorable markets in Southeast and South Asia. Ben, Alex, thank you for joining us here on this podcast. Alex, why don't you introduce yourself? You have a very interesting background. So please, tell us about your background and also a little bit about your business.
Alex: Hi. Thank you, Casey and Ben for having me in this podcast. My name is Alex. I'm from Maesot Heavy Industries. Um, we are actually a family owned business. We predominantly do foundry and sand casting, furan resin, green sand and shell molding. I actually graduated from the US with a bachelors in mechanical engineering. We have been in Thailand for a bit more than I would say 8 to 9 years. Yeah. And, we work with many different companies, including foreign like North American companies, Japanese companies, and of course the local Thai industries. Right.
Casey: And I think you actually, you have a really interesting background because being Taiwanese and living in Thailand, owning a factory here gives you a very interesting perspective on what we were going to discuss in this podcast. So yeah, thank you for joining us. So, let's let's dive into it. What is driving the necessity for OEMs to get out of China, or at least have a China plus one?
Ben: Yeah, I mean, the the big one on everyone's mind in our industry is, of course, the tariffs, the duty, the 301 tariffs, which were started under the Trump administration and continued under Biden. It's kind of been a progressive tax on imports from China that started off small and a little bit negligible and have scaled up. And so, you know, every business, every importer is and should be concerned with their bottom line. And, you know, these punitive tariffs that were put in place by the Customs and Border Protection, they wanted to, they're enacted to encourage American businesses to divest from China and seek alternatives. So, you know, that's probably the main driver. But there are some other points as well.
Casey: Sure. And Alex, how have you seen the tariffs impact your business?
Alex: For me as a manufacturer, I would say it's a positive impact for me. We have many customers originally ordering from China due to the tariffs, the cost constraints and they are slowly starting to order from us, a non-Chinese source. So, like for business wise, it's actually a good thing for me. Yeah.
Ben: And yeah, I mean, I would just say, you know, the cost is one thing and that's, you know, first and foremost on everyone's mind. But there's other factors as well. And large companies, like Apple and Sony and multinationals all over the world that, you know, saw this and in kind of earnest and started divesting from China to alternative markets like here in Thailand or Vietnam, you know, more than a decade ago. But now it's kind of small and medium enterprises are making the switch and experiencing, you know, some growing pains associated with that. But, you know, ultimately, it's important for importers to be able to have free access to their goods, and things like increasing authoritarianism in China, clamp down on Western businesses, and just general saber rattling on the geopolitical stage all present pretty large risks to importers who are solely reliant on Chinese manufacturers for their imports.
Casey: I think you bring up a really good point because, you know, like you said, like 10, 15 years ago, these large companies like Panasonic and Samsung, I mean, they started moving their manufacturing a long time ago even before the tariffs, because, you know, I think they saw something coming. And it's true, like a lot of these SME companies, they're now making the jump and they're experiencing a lot of pains, you know, moving their supply chains. So I mean, with your business, is your factory capacity filling up quite quickly?
Alex: Yeah, we actually especially before Covid but especially after Covid, I think people seeing the situation in China. We constantly get more orders each year from like from compared to last year. We also our sales volume increased mostly from the redirected orders.
Casey: So, you know, I would like to talk about maybe the differences between the three countries that we actually work in. So we work in India, Thailand, and Vietnam. And I think, you know, every country has its competitive advantages and its noncompetitive advantages. So, maybe let's talk about the differences between these countries. Let's start off, Ben, like what do you see out of India?
Ben: Yeah, India, you know, it's a huge manufacturing market. It's probably the number two for heavy industrial outside of China. So, India is relatively new as an import source for American companies, but they've been exporting to countries in Asia, particularly in the Middle East as well as Africa, for a long time as the primary supplier. You know, India has a lot of foundries, a lot of forges, there's multiple regions that are kind of manufacturing hubs. At a really high level, you can get great stuff out of India, and it's probably the most cost competitive option of the three. Where you really have to tread carefully is choosing the correct partner. And, there's a lot of incorrect partners out there where, you know, they may promise you that everything is going to be great and you might get your sample, and it just doesn't always work out that way. And so, you know, a lot of what we do behind the scenes when we're not in a studio like this is we're in country. I've been to India four times this year. And we're driving around and we're visiting foundries. We're checking up on our existing projects and always looking for, you know, the next great supplier. And so, to try to just choose someone off of Google, it's a risky proposition. I would say you don't always have the best bet.
Casey: I would say in India, everyone says, yes, it can be done. And then after you sort of start digging down, you find out very quickly that they just say yes to everyone. Yeah. I think that's one of the biggest pitfalls that we see in India and also the infrastructure. You have to be very careful about picking a partner, not just for them, but also their location. You know, I'll give you just a quick example. We were auditing. We were going to an investment cast factory. And when we were going up the road, I noticed that it was dirt and also a lot of potholes. And India has a very strong monsoon season. So we were talking, we were like, well, how is a container going to get up this hill when it's the monsoon season? Because it's going to be muddy. So even like simple things like that, it's very important to know the factory, the layout and also the surroundings of the factory. So yeah.
Ben: Yeah. I think, you know, it's certainly helpful to have an advocate who has boots on the ground and does the hard part of weeding out the duds for you so that you can have confidence in placing your project in India and take advantage of all the, you know, advantages they have for low cost and high quality that certainly does exist.
Casey: What about Thailand?
Ben: Yeah. I mean, I think I'll pass this one over to Alex in a second because of course he has a factory here. Our experience in Thailand is that generally the communication is quite good. The level of English is certainly good, and the quality tends to be right at expectation. So, you know, it's more of a market where people do what they say and say what they do.
Casey: Good infrastructure.
Ben: Good infrastructure too. You know, some of the challenges are just benchmarking against those kind of target costs can be a bit of a challenge with, you know, a relatively higher GDP than surrounding markets. But, you know, it's a good place. I mean, Alex? Right.
Alex: For me, yeah, it's...our factory in Thailand, we rarely see power outages. So the infrastructure is pretty decent. And around the surrounding area, the roads, logistics is very convenient. You can have third party logistics and DHL like or just some like large FCO transporters like everything is in place, but there are some issues, for example, in some RFQ, right? Some parts might not just be casting like for casting, we can just use our like molding machines, and everything is in-house, but sometimes they are like forging parts or like a rubber parts. And then I have to go find suppliers in Thailand, right? And sometimes they kind of reply quite slowly, sometimes. Yeah. Or they don't really have to follow up from phone calls and maybe take some time. Eventually they will quote yes. But it takes some time in the requesting for the RFQ stage. Yeah. And the pricing sometimes is, sometimes our price, our casting parts, machining parts is in targets. It's right for right under the target price. Right. But the accessories, like the parts, stamping parts and a lot of different smaller parts that in the assembly with the casting. It's too high. Right. Yeah.
Casey: We've actually seen, it's kind of funny, like in India everyone says yes, but in Thailand it's very hard to get people to a lot of times to take a project because when they decide to quote and take a project, they do a very good job. But a lot of the times getting them to quote, they're very hesitant, a lot of Thai factories. Once they do it, they'll do it very well. But getting them to do it is sometimes tricky. Yeah. And I guess the third country. What about Vietnam? What do you see? Yeah.
Ben: Vietnam is definitely emerging. A lot of, you know, multinational companies are setting up factories there for both finished goods and industrial parts. In general, it kind of, I would characterize it as kind of being in the middle of the two countries we just described in terms of, you know, generally being a little cheaper than Thailand and generally being a little bit more transparent and communicative than India. Like we touched on earlier, you know, there's a little bit different offerings in terms of the manufacturing processes there. There's fewer heavy industry options like forging or casting. It's more injection molding or machining generally. There are some some larger old forges in the north that, you know, the other challenge with Vietnam is it is kind of still, you know, it's geographically it's a little bit of a challenge, because in Thailand you use kind of one central port no matter where anything is being manufactured. But in Vietnam, there's a main port in the north and a main port in the south, and so that can make things like consolidation tricky. It can also make things like subcontracting, you know, if your coating supplier is in the south, but your foundry's in the north, it's a lot of roadways to cover. And the infrastructure is not amazing for facilitating that yet. There's some changes in the works. High speed rail from the north to south of Vietnam, we're looking forward to. But yeah, it's a geographical challenge.
Casey: I think, we've talked to a lot of customers in the US and when they fail in Vietnam, it's a lot of the times, because they don't have a team there, because the English level in Vietnam is not so good. So it's really critical to have a good team in place there and a local team, a local Vietnamese team there to manage the factories. So yeah, we're we're lucky to have a good team in Vietnam to help us with that. Alex is actually one of our manufacturing partners, and we've worked with Alex on a few different projects. Ben, why don't you tell them about one of the projects we did and how we helped consolidate and save our customers some money? Yeah.
Ben: I mean, I think, it's the most recent project we did where we were producing parts that are ultimately used in machinery, and that machinery is specific for the braided hose industry. So we're supplying parts to a manufacturer in the United States who assembles those parts and turns them into a product that's then used all over the world. It's quite a precise product with a lot of challenging tolerances and engineering requirements. We worked with Alex and his company, Maesot Heavy to produce the parts and, you know, that's super helpful. Being that we're all locally based here, it's very easy for us to go on site to communicate in our own time zone, and to, you know, go up and inspect the goods, make sure that everything is according to the print and drawing requirements, and ultimately, we were able to help this particular client by consolidating with another foundry that they work with, with a different style investment casting foundry. And we were able to consolidate and save a lot of shipping costs. Shipping costs are are always kind of fluctuating, rising and falling. But, if you are able to consolidate it, you can create more frequent shipments that are more efficient. They just have take up. You can use the cubic meter allotment a lot better. So we were able to do that. And, that was extremely helpful for our customer because of the nature of their business, they produce a large mix of products at quite low volumes. And so it's important for them to support their just-in-time inventory to work with MOQs that make sense, and we were able to offer savings on logistics by consolidating with another process of casting.
Casey: What immediate actions should companies consider to avoid potential pitfalls in their relocation efforts?
Ben: Yeah, I would say, you know, choosing the right partner is critical. We have countless examples from our clients, horror stories where they've chosen the wrong partner, and, you know, depending on where you're going, it could be anything from like, you know, most of them are pretty good to it's a total crapshoot. And 99% of them are pretty bad. I think there's, Casey you and I have stories of being in India, to meet a prospective vendor that we felt really good about, and had been chatting with online for weeks. And, you know, we pull up to the shop and we know from the second we arrived that it's just not going to be a fit. And we, you know, we just tell our driver to put it in reverse and head on to the next meeting because, you know, it's tough to know who the right partner is. That's why we feel it's important to have the local presence. Go ahead.
Casey: Well, yeah, I was going to say, I think the reason Alex is a really good partner and we've seen this especially in Thailand. Some of these factories, they've been around for decades and some of the children are running the factories now. You know, their dad's given the reins and the children are not really hungry for business. So, Alex is great because, you know, you're very hands on. You know, you're at site, and, you know, when you're partnering with someone, it's really important to to partner with a factory owner that, you know, is hands on and and knows everything about, you know, their operation. Yeah.
Ben: That that ties straight into like, you know, we always talk about in the office about the three Ps. And, you know, the Ps are, they're 'Process', which is, you know, all of your manufacturing infrastructure, your documentation, your quality programing, which is super hyper critical. Then there's 'Price', which is important to every importer, and then but the last one is the 'People', and you need to have people who are flexible, who are willing to solve problems, to dig deep and investigate. Maybe it's not something they've done before, but, willing to study it and, you know, run a feasibility study, see if it's going to be possible, try to find potential solutions to be able to turn these concepts into cast goods or forgings or anything like that. And I think, the three Ps, the 'People' is really important. All three of those are very important. But the people is one you definitely can't miss. Yeah.
Casey: And like going into like, you know people it's hyper critical like especially you know, communication is of the utmost, you know, importance and you know, just being able to, you know, just work always on WhatsApp with, you know, all of our partners, you know, seeing what's going on, you know, send us a picture or we have to go, you know. So yeah, having a good personnel at the factory is very important. Like Alex, when you're working with companies like ours. What do you see as important to partner with a company such as ours? Right.
Alex: For us, the number one quality that we hope that we can get from our customer or partner would be like be very clear on the specification from the start. Because, like from day one, it would be the RFQ. Right. Very first step, RFQ.
Casey: And what needs to go into the RFQ to make it clear? Right.
Alex: So in the RFQ we need the drawing, the material, the manufacturing process. What kind of QC standards are we talking at. Because that will all affect the price. And some customers, they are either unsure or they don't have the right person on this as the coordinator. So it's kind of frustrating for us. Like, okay, so what kind of quality are we talking about? What kind of process are we talking about? Because we have to write the code with our company name on it at the end of the day. So it's really great working with Align Manufacturing too, like from the emails and the information and the communication is very clear that we know from there what we are working with. If Align Manufacturing, if you guys did not get the information from the customer, we immediately get the feedback. Usually Align will contact the customer and get us that feedback and have been really, really helpful.
Casey: Yeah, I think like, what we found is like, you know, working with, you know, factories and guys like you is like it evolves into more of a like we're on the same team. You know, we all have the same goal. So it's important having that clarity. Yeah, so I mean you know we always try to stress to the OEMs or customers in America, don't wait until November for the election. Like, let's like you should start now. You know, like, let's get going. Why is that these OEMs need to move quickly?
Ben: Yeah. I mean, I can understand why people would want to wait and see. This election it involves importers more drastically than probably any other election in history that I can think of. And so there's a tendency to want to wait, but I think that's a counterintuitive tendency. And that's for a few reasons. I think the biggest reason is that there's only a fixed number of factories. And when you look at that cross-section of factories and talk about which ones are actually good, it's a very, very small percentage and capacity at those factories is filling up. And they're filling up from all the first movers and everybody who already moved. And so, you know, importers who are making the switch now, they're frankly, a little bit late to the game. It's not too late, but the longer you wait, kind of the worse your options will be. And you don't want to be stuck with the wrong manufacturing partner. And, you know, on the flip side, the same point of that is, you know, pricing follows, pricing is the same anywhere, it follows scarcity. And so as capacity decreases, price increases. And you better believe if you're bidding, you know, if Trump wins and a 60% tariff is enacted, your factories are going to know that. And when they're pricing out your quotes, they're not going to be pricing out according to benchmarking your 2017 China price. They're gonna go ahead and tack on an extra 60% to that knowing that they're still competitive. Ad so, you know, moving now is very advantageous for importers to get the correct manufacturer and the correct price. And for those who, you know, want to wait and see, that's a game that any, any business is allowed to play. But it's kind of a 50-50 at this point. And, it's like going to Vegas and betting on red. It might be fun for a weekend, but it's probably not something you should do with the future of your business, especially if it's a product focused business.
Casey: And I think, especially like you're looking at timelines, you know, I mean, how long does tooling take usually at your shop, right.
Alex: Um, for the complicated one, it depends on what you do. We we are foundry. Right. So we have the pattern and then the if it's a complex with a cavity and or a different like undercut geometry, we have to have the core box. Right. So if it's just one model maybe, maybe right now we're kind of busy. So maybe around two months for the medium to simple one. Right. But if it's really complex with like multiple multiple core box, many cavities then maybe it's maybe, like, maybe three months. Yeah.
Casey: And that's the thing. I mean, that's that's just the tooling. And then we have to make the sample and then the customer has to approve the sample. And, you know, sometimes the T-Bone sampling doesn't always get approved. So you're just moving the timeline. And so it's yeah, it's really important.
Ben: And there's third party testing and a million variables that can push that timeline out. And so, you know, even if you were to start today, you're looking at, you know, first production shipping out around the election anyway. So um, it's a, you know, it's just kind of, uh, urgency and expediency is is advantageous in this situation.
Casey: We talked about the 301 tariffs, but like what are some other reasons why manufacturers need or should be moving out of China?
Ben: Yeah. I mean, we kind of touched on this. But you know, when we talk about these other factors besides the tariffs, these are what we're driving the large corporations out of China in the first place, before the trade war and before the pandemic. And there's a lot of them. There's a lot of macro trends that are leaning away. There's increasing cost of labor in China as the economy develops there. The cost of labor is is increasing. And of course, that affects the bottom line in these very labor heavy industries. There's an aging workforce associated with the demographic changes in China. And so that's going to reduce the availability of factory workers who are interested to work in the manufacturing industry. And then there's, you know, kind of the red hot one that nobody really wants to talk about. But it's, you know, in the event that kind of what this kind of cold tit for tat trade war that's going on, if that escalates into something hotter, you know, where there's a real conflict, whether it be, something with the US or something with Taiwan, something in Hong Kong or all of the disputed South China Sea territories. You know, all of these are kind of red hot button issues. And if a conflict goes from cold to hot, you can pretty much kiss your supply chain goodbye. And it doesn't matter if you're willing to pay the tariffs at 30% or 60% or 100%, you just won't be able to get it. It'll be like the beginning of the pandemic, but it lasts forever.
Casey: I think it's important for us to say as well, like we're, these are all like facts. We're not against China at all. I mean, I used to live in China for a few years. I really like the Chinese people. But I think the point of this conversation is to really highlight the need to get out, at the very least.
Ben: Yeah. And I think it's, you know, something that's often overlooked or just not always talked about is that the US has placed China as a designated US foreign adversary, and that's a very short list. There's only seven countries on that list. It's North Korea, it's Iran, it's Cuba, it's Venezuela. And China is on that list. And when you look at the trade between the United States and these other countries that have been designated as an adversary, it's virtually nothing. We have strict embargoes against all of these countries. We're not allowed to import anything. It's not a matter of duty. It's just you can't get it. And the fact that the US government has placed China on this list, and most recently was said that it's actually the most potentially dangerous foreign adversary on the list.
Casey: But yet it's our biggest trade partner.
Ben: Our largest trading partner kind of knocked some reasoning behind this policy, which not everyone kind of understands the why or the how, but, you know, that's kind of the why. And the US government is interested in making sure that they can pursue their foreign policy interests without affecting US businesses. And, you know, US businesses would benefit from falling in line with that. The US government is going to keep these in place as long as China is on that list. And yeah, the government wants you to divest.
Casey: The last sort of question I would have for you guys is, you know, how do you see, like the landscape of global manufacturing evolving, you know, as this relationship between China and the US is decoupling?
Ben: Yeah. I mean, I would say, a lot of the growing pains that importers are having now come from working with less developed, less established factories that are not as familiar with the documentation requirements or the expectations and standards of the importers. You've got to remember that when China first started out, people didn't have very nice things to say about Chinese quality or Chinese suppliers. And that changed. And I expect the same thing to happen in our markets. As you know, these factories become more accustomed to working with Western importers. And, I think that some of those growing pains will change. I think we'll see new types of factories emerge as well, where right now we have mostly process-based factories that, you know, it might be a foundry, it might be a forge, it might be a machine shop. But those generally create parts and not products. And when you're talking about a packaged consumer good or even a complex assembly of an industrial good, that's a different kind of factory. That's an assembly factory. And we are seeing those emerge especially for joint ventures that are, you know, getting set up across the region. But I think you'll also see that as an independent job shops for contract manufacturing.
Casey: Yeah, that is a good point. I think, you know, a lot of the times you go to, you know, you go to a Costco or a Target and you, you see, you know, just as you think it might be so simple, but assembly is just it's extremely complex. And setting up an assembly in a factory, it takes time for it to evolve and be mature. So, yeah. Well, do you guys have anything else that you'd like to add into the conversation?
Ben: I, yeah. I mean, just on your last point, you know, other changes, I think you could see, some more friendly trade policies. You know, India has really been the shining star of this, to really recognize this opportunity and seize it with really manufacturing forward policies. The Made in India policy, which grants, you know, interest free loans as well as all kinds of tax incentives for manufacturers. I think we'll see that deployed across the region and in India. We'll see them continue. Right. Ease of doing business. I see it improving where there may be, you know, importation of child parts to be assembled or the allowance of purchasing a child part domestically. But having it be VAT exempt because it's ultimately being exported. So I think we'll see some change in the regulatory environment in these countries, which are catching on to the opportunity that's there. And it's just it really is a massive opportunity.
Casey: Yeah. I really appreciate you guys joining me. It's been a really nice conversation. Alex came all the way down from north Thailand to join us on this podcast. So Alex, thank you very much for joining us. Thank you for joining us today. If you found this discussion insightful and are considering how best to navigate the complex manufacturing shifts, I encourage you to read our recently published report Guiding US-Based Manufacturers Out of China. It's packed with in-depth analysis, real-world case studies, and practical strategies to help you make your informed decisions. To discuss your specific needs, don't hesitate to get in touch with us at Align Manufacturing. Together, we can ensure that your transition is smooth and successful. Thank you again for watching and we look forward to helping you secure your manufacturing future beyond China.
For a more in-depth exploration of these themes, download this Align Manufacturing report:
What is CNC Machining?
CNC (Computer Numerical Control) machines use command codes to control the movement of tools and machinery, enabling precise and automated operations. This process begins by creating a digital design using CAD software, which is then converted into a set of instructions that control the operation of the CNC machine. As a US-based manufacturing firm sourcing outside China, CNC machining is essential for ensuring high-quality, consistent parts. Whether through CNC milling in China, or China CNC machining parts, the global availability of CNC services ensures efficient manufacturing.
The key benefits of CNC machines include automation, which allows them to operate without manual intervention; precision, ensuring they can create complex parts with tight tolerances; and consistency, guaranteeing each part is identical, crucial for mass production. Whether producing components for cars, airplanes, or intricate molds, CNC machines form the backbone of modern American manufacturing by delivering reliable and repeatable results that improve both efficiency and quality.
How Do CNC Machines Work?
CNC machines operate by following coded instructions, known as G-code, that tell the machine how to move its tools to perform specific tasks like cutting, drilling, or shaping materials. The process typically unfolds in five phases:
- Design Phase: A part is designed using CAD (Computer-Aided Design) software, creating a digital blueprint.
- Programming Phase: The design is converted into G-code using CAM (Computer-Aided Manufacturing) software, which provides the machine with instructions.
- Setup Phase: An operator secures the material (workpiece) and installs the necessary cutting tools.
- Machining Phase: The CNC machine automatically shapes the material as per the programmed instructions, performing tasks like cutting or drilling.
- Finishing Phase: After machining, additional processes like polishing or heat treatment are applied to meet the final specifications.
This process eliminates the need for manual operation, ensuring consistent, high-quality results with minimal human error, making CNC machining ideal for manufacturers in the U.S. who aim to compete globally, including sourcing CNC milling service China for specific projects.
The Versatility of CNC Machining
CNC machining offers unparalleled precision, versatility, and efficiency, making it ideal for a broad range of industries across the U.S. and worldwide. Here’s why CNC machining, including China CNC milling service, excels:
- Precision Manufacturing: CNC machining ensures tight tolerances and high accuracy, crucial for industries like aerospace, automotive, and medical devices where precise measurements are vital.
- Complex Part Production: CNC machines can easily handle intricate designs and complex geometries that would be difficult or impossible to achieve manually, ideal for CNC machining milling operations.
- High-Volume Production: Perfect for mass production, CNC machining ensures identical parts with minimal variation, essential for maintaining quality.
- Prototyping: CNC machining is widely used for rapid prototyping, allowing engineers and designers to quickly create and test physical models.
- Material Versatility: CNC machines can work with a wide range of materials like metals, plastics, wood, and composites, making them adaptable to multiple industries, including China CNC machining parts.
- Reduced Human Error: Automation in CNC reduces the likelihood of errors, ensuring higher quality and consistency across production.
- Time and Cost Efficiency: CNC machining accelerates production processes and reduces labor costs, essential for keeping manufacturing competitive in the U.S., where companies might also consider outsourcing CNC milling service China for cost-effective solutions.
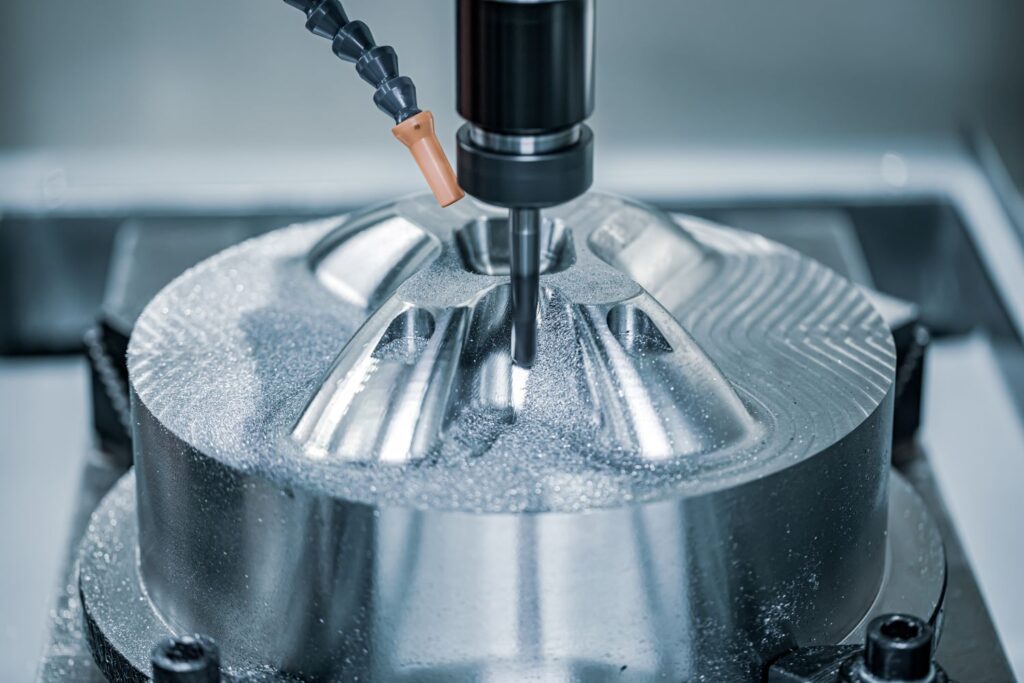
What are the 5 common types of CNC machines?
CNC machines come in various types, each tailored for specific tasks, making them versatile tools in both U.S. and global manufacturing. The most common types include:
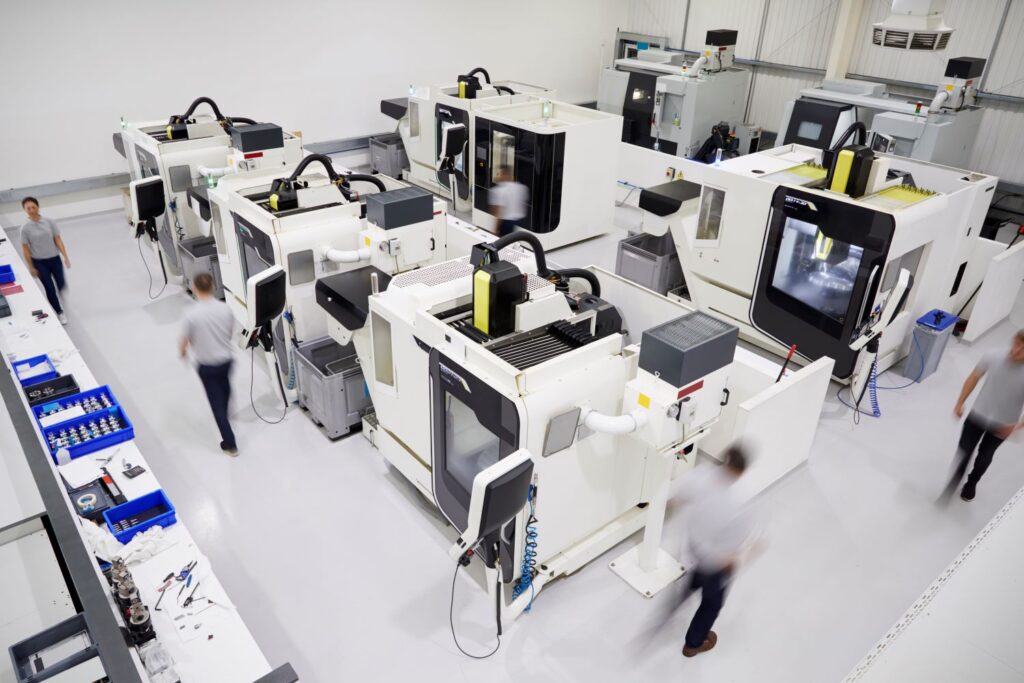
CNC milling machines use rotating tools to cut and shape materials, ideal for creating complex parts with features like holes, slots, and pockets.
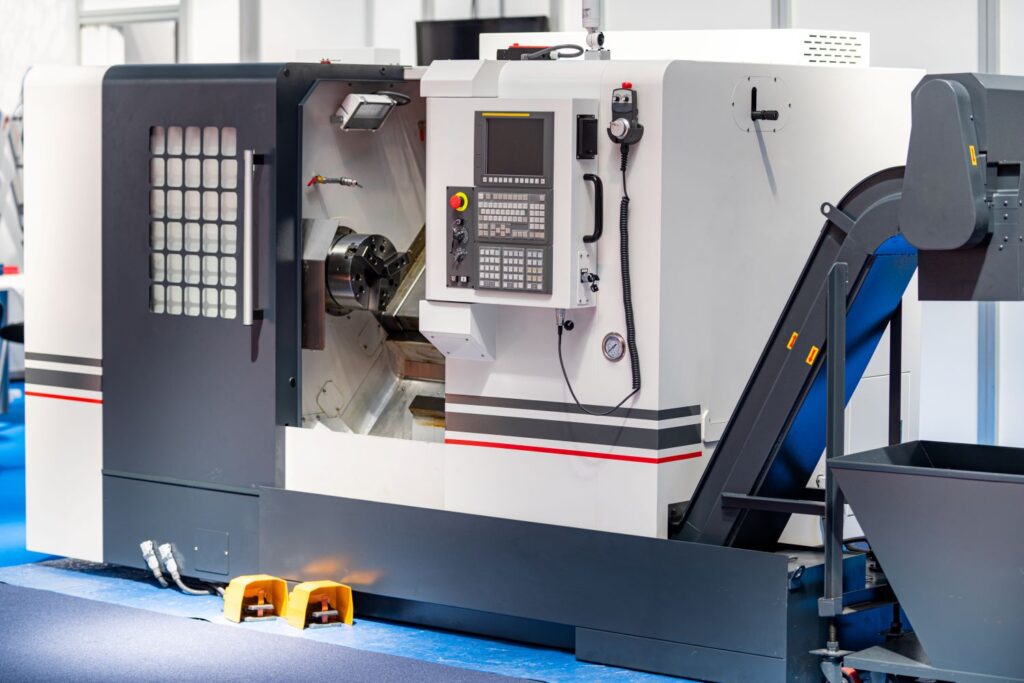
CNC lathes spin the workpiece while a stationary cutting tool shapes it, making them perfect for producing cylindrical parts such as shafts, rings, and threaded components.
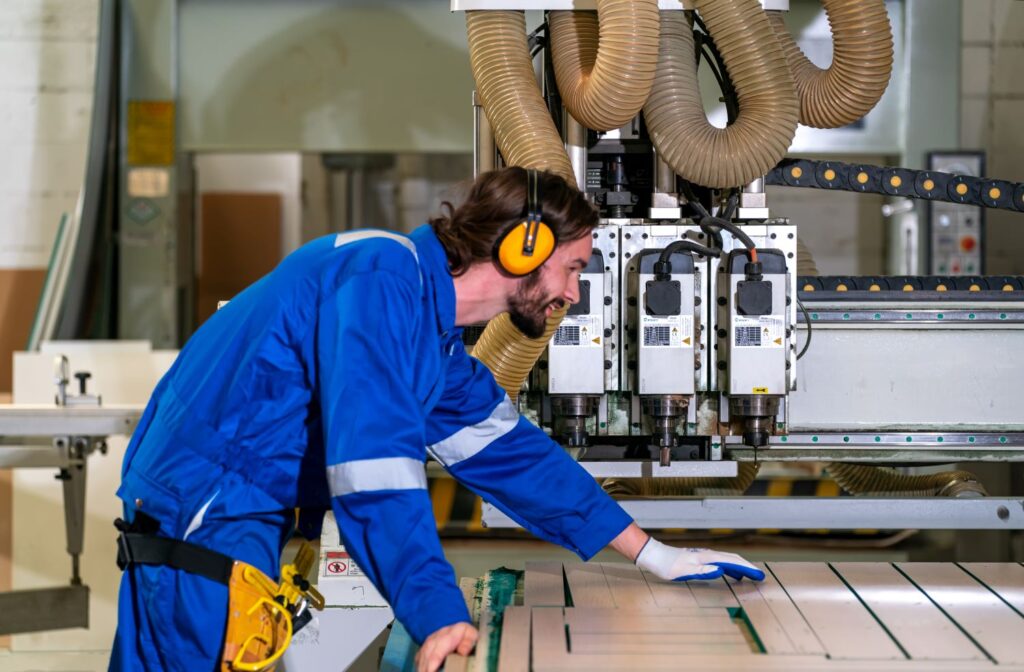
CNC routers function similarly to milling machines but are designed for softer materials like wood and plastic, widely used in woodworking, sign-making, and foam modelling.
CNC plasma cutters use a high-powered plasma torch to cut through conductive metals, commonly used in metal fabrication shops for steel, aluminium, and other metals.
CNC laser cutters employ a focused laser beam to cut or engrave with high precision, suitable for detailed work on metals, plastics, wood, and glass.
The growth of CNC machine usage in the industry over the past five years has been significant, driven by advancements in technology, increased automation, and the demand for precision in manufacturing. Here’s an overview of the trends that contributed to this growth:
- 2019: CNC machine usage started gaining momentum with an approximate growth of 8%, as industries began adopting more automated solutions for efficiency and precision.
- 2020: The demand for CNC machines increased, partly fueled by the pandemic’s impact on labor shortages and the need for automation, resulting in 10% growth. CNC technology became more relevant as manufacturers looked for ways to maintain production while reducing human intervention.
- 2021: As supply chains adapted to the post-pandemic world, CNC machine usage saw further adoption across industries such as automotive, aerospace, and medical devices. The growth rate hit 12%, with companies investing more in digital transformation and advanced manufacturing capabilities.
- 2022: The trend continued as industries embraced CNC machines for their ability to produce complex parts with precision. The growth accelerated to 15%, reflecting increased reliance on CNC technology for both mass production and custom parts.
- 2023: CNC machine usage reached its highest growth at 18%, thanks to innovations like multi-axis machining, AI integration, and smart manufacturing solutions. The expansion of CNC applications in new sectors such as renewable energy and electric vehicles also contributed to the increased demand.
Overall, the last five years have seen CNC machines becoming a critical component of modern manufacturing, with their usage growing steadily due to the need for automation, precision, and cost-efficiency in industries worldwide.
Conclusion
Align Manufacturing, headquartered in Singapore with offices in Bangkok, is dedicated to providing high-quality industrial production solutions on a global scale. Our expertise extends beyond China, offering intricate sand casting, robust forging, efficacious stamping, and state-of-the-art precision machining. This diverse range of metallurgical services ensures we meet the complex needs of our clients worldwide with meticulous attention to detail and seamless communication. Partner with Align Manufacturing for efficient and precise manufacturing outcomes tailored to your project’s success, wherever you may be located
FAQs
Which components move during CNC Machining?
In CNC milling machines, components move along the X, Y, and Z axes. Each axis is divided into two directions: the positive (+) and negative (-) directions. CNC machining involves precise movements of key components, such as the cutting tool, workpiece, and machine table, all controlled by the CNC system. The cutting tool moves along multiple axes to shape or cut the material, while multi-axis machines add rotary movements for complex angles. In some machines, the workpiece rotates, and gantry-style machines move the entire tool-holding gantry, ensuring efficient and accurate production of detailed parts.
What are the basics of CNC?
Automated machinery that operates with a computer system to produce material parts to the desired size and shape through turning. It is suitable for turning work that requires precision or has a high level of complexity.
CAD/CAM Software
- CAD (Computer-Aided Design) software is used to design parts and components in a digital format, creating a 2D or 3D model.
- CAM (Computer-Aided Manufacturing) software converts the CAD design into G-code, which CNC machines can understand. G-code contains instructions for the machine on how to move and manipulate the cutting tools.
G-Code
- G-code is the programming language that tells the CNC machine how to move. It includes commands that dictate the direction, speed, depth of cut, and the specific movements required to shape the material.
CNC Machine Components
CNC machines consist of key components that work together to achieve precision manufacturing:
- Controller: The “brain” of the machine, the controller interprets the G-code and sends the commands to the machine’s moving parts.
- Spindle: Holds and rotates the cutting tool or workpiece, playing a crucial role in the cutting, drilling, or milling processes.
- Axes: CNC machines typically move along the X, Y, and Z axes, while more advanced machines may include rotary axes (A, B, C) for more complex movements.
- Tool Changer: Automatically switches between different cutting tools for various machining tasks.
Automated Movements
- CNC machines are capable of highly precise and repeatable movements. Based on the programmed G-code, CNC machines perform tasks such as cutting, drilling, and milling without human input.
- Machines can move along multiple axes simultaneously, allowing for the creation of intricate and complex parts.
Material Versatility
- CNC machines can work with a wide range of materials, including metals, plastics, wood, and composites. The choice of material depends on the specific industry and application.
Consistency and Precision
- CNC technology ensures that every part produced is identical to the original design, maintaining tight tolerances and high levels of precision. This is critical for industries such as aerospace, automotive, and medical devices.
Applications of CNC
CNC is widely used in industries such as automotive, aerospace, electronics, medical devices, and consumer goods manufacturing. The versatility of CNC technology allows it to produce complex components in large quantities while maintaining quality and precision.
What are the 7 basic types of machine tools?
The seven basic types of machine tools are essential in shaping and forming materials in manufacturing processes. These tools provide precision, efficiency, and consistency in creating parts and components across various industries. Here are the seven basic types of machine tools:
Lathe
A lathe rotates the workpiece while a stationary cutting tool shapes it. It’s ideal for creating cylindrical parts such as shafts, bolts, and rings.
Milling Machine
This machine uses rotating cutting tools to remove material from a stationary workpiece. It is commonly used to create complex shapes with slots, holes, and pockets.
Drill Press
A drill press uses a rotating drill bit to create precise holes in a workpiece. It is often used for boring holes in metals, wood, and other materials.
Grinder
Grinders use abrasive wheels to remove material from the surface of a workpiece, usually for finishing or shaping. They are used for smoothing surfaces or precision finishing.
Shaper
A shaper moves a single-point cutting tool back and forth across a stationary workpiece, removing material in a linear motion. It is typically used for creating flat surfaces, grooves, and keyways.
Planer
Similar to a shaper but larger, a planer moves the workpiece back and forth while the cutting tool remains stationary. It is used for shaping large, flat surfaces.
Broaching Machine
Broaching machines use a toothed tool (broach) to remove material in a single pass, typically creating precision holes, slots, or keyways with specific shapes.
Future Trends of CNC Technology
CNC technology continues to evolve, pushing the boundaries of global manufacturing, including in the U.S. and China CNC milling service. As demand for precision, speed, and customization grows, CNC technology is adapting to meet new challenges. Key trends include:
- Increased Automation and Smart Manufacturing: The integration of Industry 4.0 is set to make CNC machines more interconnected, leveraging data analytics, cloud computing, and the Internet of Things (IoT) to improve production efficiency.
- Additive Manufacturing Integration: Hybrid CNC machines that combine subtractive and additive manufacturing (3D printing) will allow manufacturers to build complex parts layer by layer and then refine them using traditional CNC methods, minimizing waste and enhancing customization.
- Multi-Axis and Multi-Tasking Machines: As industries demand more complex parts, multi-axis CNC machines will allow manufacturers to perform multiple operations in one setup, increasing efficiency.
- Artificial Intelligence (AI) and Machine Learning: AI-driven CNC systems will optimize tool paths, predict tool wear, and automate quality control, leading to enhanced productivity.
- Advanced CNC Materials: CNC machining will increasingly focus on advanced materials like composites, high-strength alloys, and carbon fiber, particularly for industries like aerospace and medical devices.
- Green and Sustainable Manufacturing: CNC machines will play a critical role in green manufacturing, focusing on reducing waste, optimizing energy use, and supporting sustainable practices.
- Customization and Personalization: As consumer demand shifts toward customized products, CNC technology will enable manufacturers to efficiently produce small, personalized batches without compromising quality.
- Cloud-Based CNC and Remote Operation: Cloud-based CNC systems will allow operators to monitor and control machines remotely, increasing flexibility and efficiency across multiple locations.
Take a look at this video to learn everything about CNC machines:
Forging Fundamentals: Understanding the Process
What is Forging?
Forging is a process that involves shaping or forming materials, usually metal, through the application of heat and pressure. This process alters the material’s shape and structure, making it stronger and more durable. Forging is commonly used in manufacturing industries to create tools, machine parts, and various metal products.
How does the forging process enhance the mechanical properties of metal?
Forging strengthens metal by refining its internal grain structure and eliminating defects. During the forging process, the grains within the metal are deformed and realigned in the direction of the applied force, which helps improve its strength and toughness as the grain structure conforms to the new shape. The compression involved in forging also densifies the material, reducing voids and air pockets that can weaken the metal. Additionally, the repeated hammering or pressing causes work hardening, where the internal structure becomes more compact and resistant to deformation. This process also helps remove impurities or defects within the metal, creating a more uniform and robust material, ideal for demanding applications like automotive and aerospace industries.
Metals suitable for forging
The best metal for forging depends on the specific application and desired properties, but some of the most commonly used metals for forging include:
1. Steel: Steel is the most popular metal for forging because it’s strong, easy to work with, and widely available. Different types of steel, like carbon steel and stainless steel, are used based on whether strength or rust resistance is more important.
2.Aluminum: Aluminum is lightweight and easy to forge, making it a good choice for industries like aerospace and car manufacturing. It’s also resistant to rust and corrosion.
3. Titanium: Titanium is very strong and lightweight, making it great for high-performance applications like aircraft and medical tools. However, it’s more expensive and harder to work with than steel.
4. Copper and its alloys (like bronze and brass): Copper and its alloys are softer and easy to shape. They are often used in electrical parts, plumbing, and decorative items because of their good conductivity and resistance to rust.
5. Nickel-based alloys: These metals are used in extreme environments, like jet engines or chemical plants, because they stay strong at high temperatures and resist corrosion.
Forging Equipment
Forge or furnace: This is used to heat the metal to the appropriate temperature for forging, making it soft enough to shape. Traditional forges burn coal, gas, or oil, while modern furnaces may use electric induction for precise temperature control.
Anvil: The anvil provides a hard surface on which the metal is placed while it is being hammered or shaped. It has a flat top and various edges and horns to help form different shapes.
Hammer: Hammers are used to strike the metal and shape it. These can be hand hammers for small-scale work, or power hammers for larger, more industrial processes. Power hammers deliver repeated heavy blows quickly, saving time and effort.
Tongs: Tongs are essential for holding and manipulating the hot metal while it’s being worked on. They come in various sizes and shapes to grip different types of material securely.
Die: Dies are molds used in closed-die forging. The heated metal is placed between two dies, which are then pressed together to form the metal into a specific shape. They are often used for producing consistent parts like gears or tools.
Quenching tank: After forging, the metal is often cooled quickly in a quenching tank filled with water, oil, or another cooling medium. This helps harden the metal and set its final shape.
Protective gear: Since forging involves high heat and heavy tools, safety equipment like heat-resistant gloves, aprons, face shields, and ear protection are necessary to protect the smith from burns, sparks, and loud noise.
Different types of forging
Open-Die Forging
Open-die forging is like traditional blacksmithing. A large piece of heated metal is placed on an anvil or between two flat dies, and it is hammered or pressed into shape. The dies don’t completely enclose the metal, so it can spread out freely, making this process flexible for creating large or irregularly shaped parts. The metal is hammered multiple times to gradually form the desired shape. Open-die forging is often used for big parts like shafts, rollers, and rings that need to be very strong.
Closed-Die Forging (Impression-Die Forging)
Closed-die forging, also known as impression-die forging, involves pressing heated metal between two molds (dies) shaped like the final product. The metal is forced to fill the die cavities, taking on the exact shape of the mold. This method is highly precise and can produce parts with detailed, intricate designs. It’s ideal for making smaller, high-volume parts like automotive gears, bolts, or connecting rods.
Roll Forging
Roll forging is a process where a heated metal bar or rod is passed through two rotating rolls. These rolls have grooved shapes that gradually reduce the thickness of the metal and lengthen it. Roll forging is used to create long, uniform parts like axles, tapered shafts, and leaf springs. This process is very fast and efficient for mass production.
Cold Forging
Cold forging takes place at or near room temperature. The metal is placed into a die and shaped using high pressure. Cold forging doesn’t require heating, which means it uses less energy and produces parts with a very smooth surface and high dimensional accuracy. Since the metal is not heated, it hardens during the forging process, increasing its strength. Cold forging is mainly used for small parts like screws, bolts, rivets, and other fasteners, often made from softer metals like aluminum or copper.
Hot Forging
Hot forging involves heating metal to a very high temperature (above its recrystallization point) before shaping it. When metal is heated, it becomes softer and more malleable, making it easier to form into complex shapes. This process is used to create both small and large parts, including bolts, engine components, and structural parts in the construction industry. Hot forging also helps improve the metal’s internal structure by refining the grain size, making the final product stronger and more durable.
Align MFG offers a range of forging services designed to meet diverse industry needs, ensuring high-quality components that prioritize strength and durability. Their expertise in forging is complemented by metallurgical services available outside of China, providing valuable insights and support to clients globally. This combination allows customers to benefit from not only precision manufacturing but also tailored metallurgical analysis, enhancing the overall quality and performance of their products. Contact us to learn more about how our forging and metallurgical services can support your specific needs.
FAQ
What is forging?
Forging is the process of shaping hot metal by hitting or pressing it. It’s similar to molding clay but with metal. This makes the metal stronger and gives it the desired shape for tools or machine parts.First, we heat the metal until it’s very hot. Then we hit or press the hot metal to change its shape. We use special tools or big machines to do this. This makes the metal very strong. People use forged metal to make things like car parts and construction gear.
What are the three types of forging?
The three main types of forging are
- Open-die forging: The metal is placed between two flat or simply shaped dies. It’s then hammered or pressed, allowing the metal to flow freely except where it contacts the dies.
- Closed-die forging: The metal is placed in a die resembling a mold of the desired final shape. It’s then compressed between two dies that contain the metal, forcing it to take the shape of the cavity.
- Roll forging: The heated metal is passed between two rotating rolls with semi-circular grooves. As the metal passes through, it’s shaped into a round or cylindrical form.
Why is forging used?
Forging is used because it strengthens metal by aligning its grain structure, making it more durable and resistant to wear. It also allows for precise shaping, which is essential for creating tools, machine parts, and other components that need to withstand heavy use.
Emerging Manufacturing Hubs: Why Southeast and South Asia are Winning Over Businesses
Southeast Asia and South Asia offer simple regulatory frameworks and higher growth potential, making them attractive alternatives to China for contract manufacturing operations. Key players in these regions include Thailand, Vietnam, and India, each presenting unique advantages.
Thailand
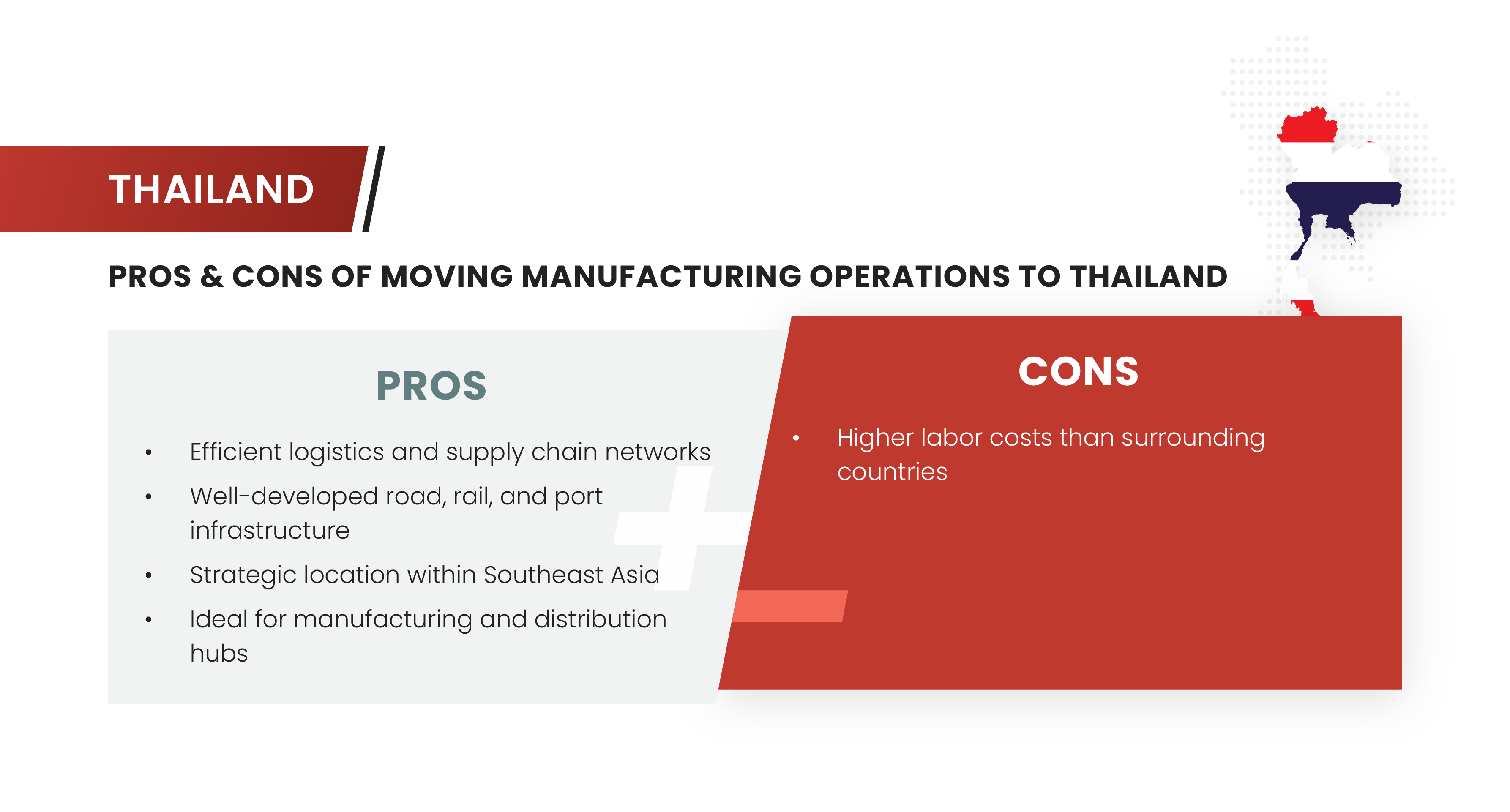
Thailand is expected to see steady economic growth moving forward, with a projected GDP increase of 3.9% in 2024. This growth is driven by strong domestic consumption, a robust industrial base, and strategic initiatives like the Eastern Economic Corridor (EEC), which is aimed at transforming the region into a hub for advanced industries such as robotics, aviation, and biofuels.
Thailand is already a massive automotive hub, and has some of the longest established foundries and steel mills in the region. On the strength of this well-established manufacturing base, Thailand's industrial sector comprises approximately 35% of the national GDP.
Thailand also offers a favorable regulatory framework and numerous incentives for foreign investors. Its Board of Investment incentives let overseas companies enjoy tax exemptions, infrastructure support, and streamlined business registration processes, particularly in high-tech and advanced manufacturing sectors. These factors helped Thailand rank an impressive 21st out of 190 economies in the most recent Ease of Doing Business Index, highlighting its supportive business climate.
Concerns within Thailand’s industrial and technology community tend to revolve around the country’s education system, which is not especially well adapted to a culture of digital innovation. Still, Thailand’s current centers of advanced industrial production, powered largely by foreign investment, are helping a generation of talent gain experience and expertise in areas such as modern metal parts manufacturing methods.
Vietnam
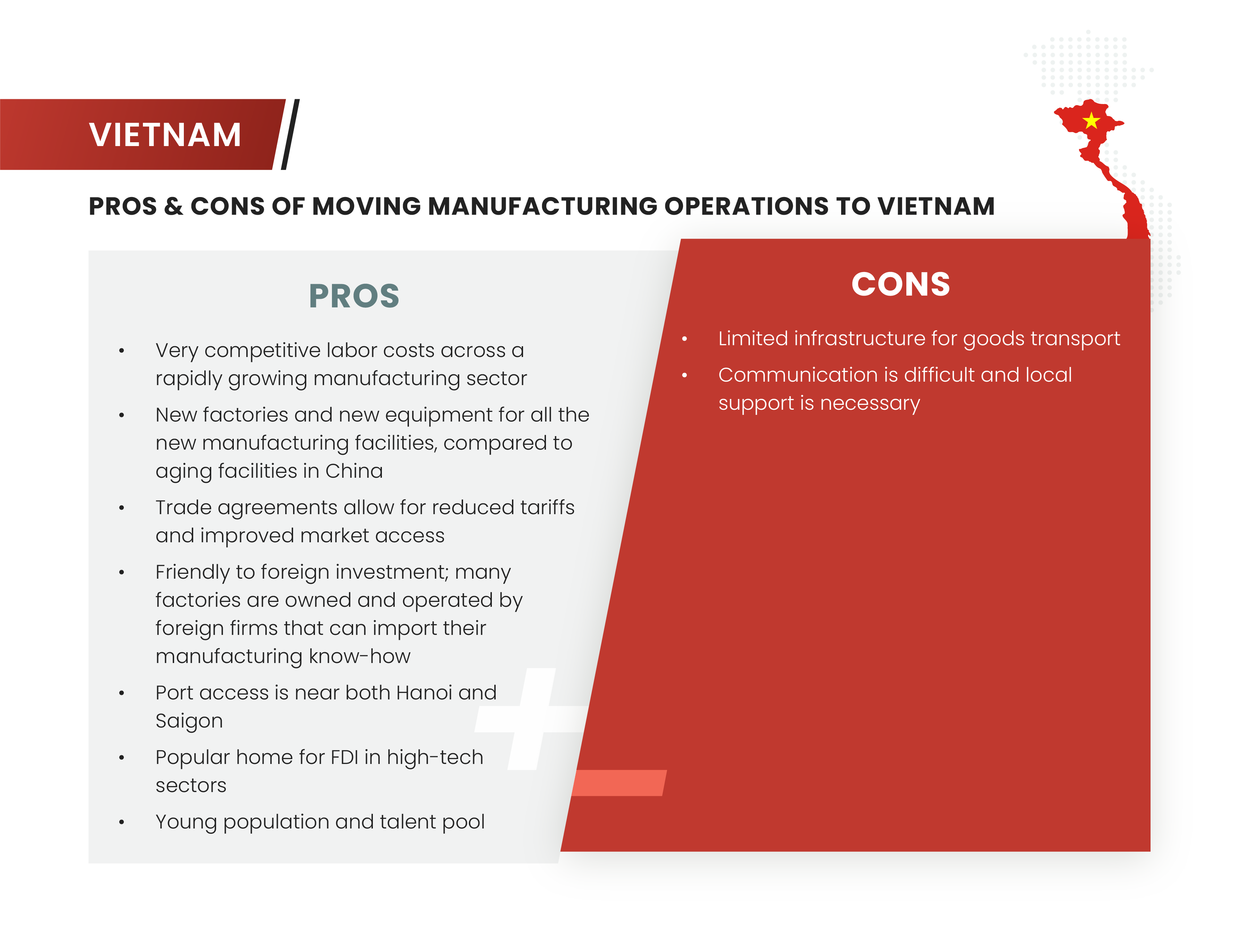
The growing partnership between Vietnam and the US is now stronger than ever. Vietnam continues to attract substantial foreign direct investment, particularly in high-tech industries. With a projected GDP growth of 6% in 2024, the economy benefits from its competitive labor costs and strong manufacturing sector.
In 2023, Vietnam's FDI inflows reached $28.85 billion, marking a significant increase from previous years. Major tech companies, including Apple, are increasingly shifting production to Vietnam, enhancing its role as a manufacturing hub.
Vietnam boasts a young and expanding labor force, crucial for sustaining its manufacturing growth. Approximately 50% of Vietnam's population is under the age of 30, providing a robust workforce for technical industries and vocational trades. The country’s focus on improving educational standards and technical training ensures a competitive talent pool for the foreseeable future, with vocational training schools helping prepare the younger generation for careers in a variety of industries.
Vietnam has streamlined its business regulations and offers attractive incentives for foreign companies, including government-sponsored industrial estates and grants. The country’s trade agreements with major economies, such as the EU-Vietnam Free Trade Agreement (EVFTA) and the Comprehensive and Progressive Agreement for Trans-Pacific Partnership (CPTPP), enhance its business environment, making it easier for foreign companies to contract out their manufacturing bases.
Though current infrastructure is less than ideal for major shipments, Vietnam's commitment to improving such shortcomings and reducing regulatory burdens further boosts its attractiveness for investors.
India
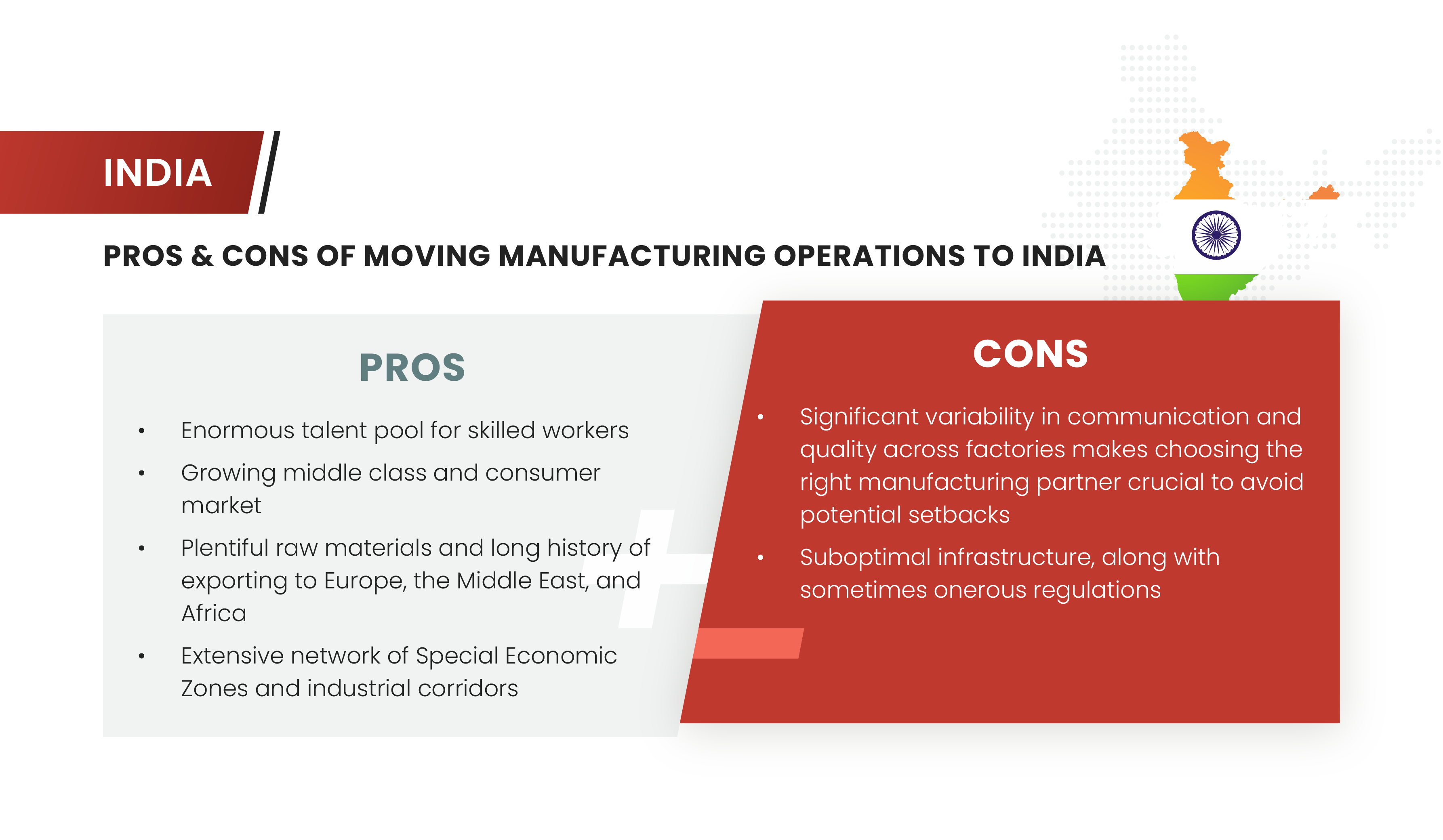
India stands out with its large, skilled workforce and significant market potential. Its GDP is expected to grow at a rate of 6.9% in 2024, supported by economic reforms and initiatives such as "Make in India", which aim to boost manufacturing capabilities and attract foreign investment. This strategic focus is particularly advantageous for businesses looking to establish or expand their component manufacturing operations.
India's industrial sector contributes about 31% to its GDP, with manufacturing alone accounting for over 18%. The country’s significant consumer base, including a growing middle class, further enhances its attractiveness for global businesses.
Although India and China have the two largest populations, the average age in China is 39 whereas in India it is just over 28. With more than 65% of its people under the age of 35, India boasts a vast and cost-effective labor pool. This demographic edge supports long-term economic growth and makes India an attractive destination for labor-intensive manufacturing operations. Additionally, India’s higher education sector is the third largest in the world, with over 43 million students enrolled in various universities and colleges, ensuring a continuous supply of skilled professionals.
In some circumstances, foreign companies aiming to buy land or operate factories themselves may find themselves facing bureaucratic delays. Contract manufacturing sidesteps most of these hurdles, letting domestic businesses benefit from simpler forms of oversight. Moreover, India has implemented significant reforms to improve its business climate, including easing regulations and reducing corporate tax rates. India ranks 63rd in the Ease of Doing Business Index, reflecting significant improvements in its regulatory environment.
Pioneering the Future of Manufacturing in Southeast and South Asia
As businesses globally reassess their manufacturing strategies, Southeast and South Asia emerge as pivotal regions. With their advantageous economic environments, strategic locations, and dynamic workforce, Thailand, Vietnam, and India not only offer compelling alternatives to China but are setting new standards in the manufacturing sector. These nations are proving to be not just viable, but superior choices for companies aiming to enhance their operational resilience and tap into burgeoning markets.
About Align Manufacturing:
Align Manufacturing, headquartered in Singapore and with offices in Bangkok, specializes in delivering high-quality industrial production solutions. Our expertise ranges from intricate sand casting and robust forging to efficacious stamping and state-of-the-art precision machining. This diverse capability ensures that we meet the complex needs of our clients with meticulous attention to detail and seamless communication. Partner with Align Manufacturing for efficient and precise manufacturing outcomes tailored to your project's success.
Note:
This article is part of an ongoing series exploring why US-based companies need to move their manufacturing operations outside of China.
To read the next article, click HERE.
To read the previous article, click HERE.
To download the entire series as a report, click the button below.