Posts by Casey Ross
Why Now is the Time to Relocate Manufacturing Outside of China
Southeast Asia and South Asia have become increasingly attractive options for OEMs seeking stability and resiliency. This trend, which began in earnest during the pandemic, continues to accelerate as OEMs from a variety of sectors have come to appreciate the simple value proposition that other Asian countries can offer.
Yet, there is more than just value in leaving China for more suitable destinations. There is also a great deal of urgency, even for companies that don’t yet realize time is running out.
Consider, first of all, factory capacity. As more businesses relocate to Southeast Asia and South Asia, capacity at the best factories will fill up. Each passing month yields fewer and fewer vacancies at the most desirable factory locations — with less and less desirable manufacturing partners, as the best ones will already have found their clients.
Just as alarmingly, prices will rise as available factory capacity shrinks. Factory prices follow market rules on scarcity, so the best time to enter into agreements is when there are many open facilities to choose from. Predatory pricing takes over when industrial estates and manufacturing partners know that their customers are getting desperate.
Although many companies might prefer to wait until November 2024 or later, so as to make their strategy decisions with a better view of future business conditions, such a delay will actually cause the quality of their options to deteriorate. Without a head start on contract manufacturing relocation, OEMs are likely to be stuck with pricing that doesn’t benchmark against China. It will instead benchmark against China + any prevailing tariffs, likely up to 60%.
Another consideration is the long onboarding process for many kinds of production. Projects that require tooling will need six months before they start shipping production.
As more businesses act on 'China +1' orders, once new tariffs are implemented, these orders will consume a significant portion of available factory capacity.
Companies will face not only the financial burden of thousands or millions of dollars in tariffs but also the challenge of finding suitable production space as capacity tightens. This places even greater importance on moving quickly to secure space at desirable factories, as delaying could leave less favorable options available for latecomers, impacting their capabilities in areas like parts manufacturing and component manufacturing.
The logic behind these tariffs represents another reason to begin the relocation process as early as possible. The tariffs were enacted to enable the US to pursue its foreign policy interests with minimal impact on American importers. For American businesses, this strategy is primarily about avoiding the financial burden of tariffs. For the US government, it's about decoupling from a foreign adversary with as little disruption as possible to domestic business operations, ensuring that national security interests are maintained without compromising economic stability.
OEMs should therefore understand that it makes not only economic sense, but also reputational sense, to move their investments and production partnerships away from China. For all the reasons stated above, that move will become increasingly challenging the longer those OEMs wait to get started.
About Align Manufacturing:
Align Manufacturing, headquartered in Singapore and with offices in Bangkok, specializes in delivering high-quality industrial production solutions. Our expertise ranges from intricate sand casting and robust forging to efficacious stamping and state-of-the-art precision machining. This diverse capability ensures that we meet the complex needs of our clients with meticulous attention to detail and seamless communication. Partner with Align Manufacturing for efficient and precise manufacturing outcomes tailored to your project's success.
Note:
This article is part of an ongoing series exploring why US-based companies need to move their manufacturing operations outside of China.
To read the next article, click HERE.
To read the previous article, click HERE.
To download the entire series as a report, click the button below.
Looming Threats to China’s Trade and Manufacturing Landscape
The relationship between the US and China has been deteriorating over recent years, as evidenced by ongoing trade wars, trade deficits, military posturing, and ideological conflicts. The imposition of tariffs on Chinese goods by the Trump administration aimed to correct trade imbalances and address concerns over intellectual property theft and unfair trade practices. The continuance of tariffs under the Biden administration indicates a bipartisan consensus on the need to address these issues.
In the absence of any positive breakthrough between the two nations, the potential for future tariff increases remains high. Nor is the US alone; the EU recently raised its tariffs on Chinese-made electric cars, a move which could lead to more such trade barriers on both sides.
The mere possibility of a tariff increase creates an unstable environment for manufacturers reliant on Chinese imports. Notably, tariffs on Chinese goods have resulted in an estimated $195 billion in additional costs for American consumers and businesses since 2018.
Trump has stated that if he is re-elected, he may increase tariffs on Chinese goods to 60% or more, undermining any remaining cost competitiveness for almost every category of goods manufactured in China. Yet regardless of what the next administration may do, relocating to a different country is the only way for OEMs to reliably eliminate the punitive 301 tariffs and maintain efficiency in areas like parts manufacturing.
Increasing age
China’s rapidly aging population will soon lead to increased labor costs alongside a smaller talent pool, making the country significantly less attractive for the production of goods. By 2035, it is projected that nearly one-third of China’s population will be over 60 years old.
Relocating to regions with younger populations and growing workforces can provide OEMs with a more sustainable labor supply, reducing the costs associated with talent shortages and enhancing their capabilities in areas such as component manufacturing.
Increasing authoritarianism
The Chinese government’s consolidation of control over business operations and foreign investments poses significant supply chain risks, particularly in the form of sudden regulatory changes and increased scrutiny. For example, the Chinese government has imposed strict regulations on data security which directly impact projects affiliated with foreign companies. Additionally, firms may need to implement robust compliance and risk management frameworks to navigate China’s complex regulatory landscape.
In this environment, American businesses face difficulty protecting their intellectual property and maintaining their competitive advantage. Proactively moving production to greener pastures can help companies safeguard their interests.
It is also worth noting that China is the only adversary nation with which the US has an extensive trade relationship. Continuing tensions between these two nations suggests that future trade relationships may be difficult to sustain moving forward, to say nothing of potential national security concerns.
As businesses consider their future in a global market, understanding these dynamics is crucial for maintaining competitiveness and securing operational stability.
About Align Manufacturing:
Align Manufacturing, based in Bangkok, specializes in delivering high-quality industrial production solutions. Our expertise ranges from intricate sand casting and robust forging to efficacious stamping and state-of-the-art precision machining. This diverse capability ensures that we meet the complex needs of our clients with meticulous attention to detail and seamless communication. Partner with Align Manufacturing for efficient and precise manufacturing outcomes tailored to your project's success.
Note:
This article is part of an ongoing series exploring why US-based companies need to move their manufacturing operations outside of China.
To read the next article, click HERE.
To download the entire series as a report, click the button below.
All About Investment Casting: Process, Materials, and Uses
Investment casting, also referred to as lost-wax casting, is a manufacturing process that has been utilized for thousands of years to produce intricately detailed metal parts. This method is highly esteemed for its ability to create precise and complex shapes with excellent surface finishes. From ancient artifacts to modern industrial components, investment casting continues to be a versatile and essential technique in various manufacturing sectors. Notably, the investment casting market is expected to reach USD 17.57 billion by 2031, registering a CAGR of 4.58%.
What is Investment Casting?
Lost wax investment casting involves creating a wax pattern, which is then coated with a ceramic material to form a mold. Once the ceramic mold hardens, the wax is melted away, leaving a hollow mold into which molten metal is poured. This technique allows for the production of detailed and high-quality metal components, making it a preferred method for industries requiring precision and complexity in their parts.
Benefits of Investment Casting
Investment casting offers numerous advantages, including:
High Precision: This method can achieve tight tolerances and detailed geometries that are often challenging or impossible with other casting techniques. The precision of lost wax makes it ideal for components that require high levels of accuracy and detail.
Versatility: It is suitable for a wide range of metals and alloys, including both ferrous and non-ferrous materials. This versatility allows manufacturers to choose the best material for their specific application.
Smooth Surface Finish: The process produces parts with excellent surface quality, reducing the need for extensive machining or finishing work. This results in lower overall production costs and improved aesthetic appeal.
Reduced Machining: Investment casting minimizes the need for secondary machining operations, as the parts come out of the mold very close to the final dimensions. This not only saves time but also reduces material waste.
Design Flexibility: Lost wax casting allows for complex and intricate designs that would be difficult or impossible to achieve with other casting methods. This flexibility enables engineers to create innovative solutions that meet specific performance requirements.
Overview of the Investment Casting Process
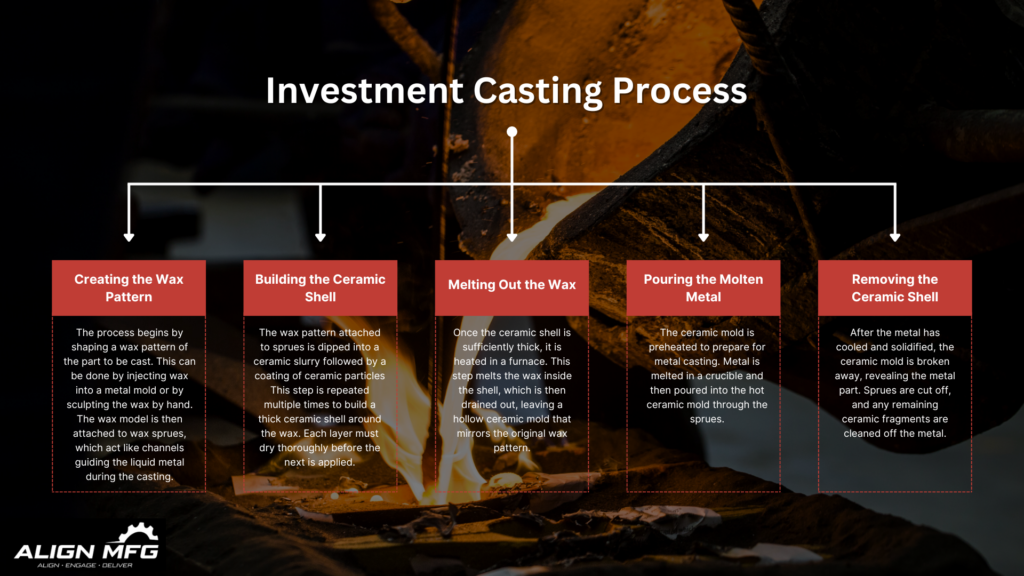
The investment casting process can be broken down into several key stages, each crucial for producing high-quality castings:
- Die Design: The process begins with the design and manufacture of injection molding dies. These dies are used to produce hundreds or thousands of wax models, and their correct design is essential to reduce casting defects and ensure the metal flows correctly into the shell.
- Pattern Creation: Using the injection molding dies, a wax model is created, which is an exact replica of the part to be manufactured.This wax pattern is typically produced using a metal die or by 3D printing, allowing for precise replication of complex geometries.
- Pattern Assembly: Before mold building, the wax patterns are arranged on a wax tree. This assembly facilitates the simultaneous creation of multiple castings and ensures efficient use of materials.
- Mold Building: The wax pattern is repeatedly dipped into a ceramic slurry and coated with fine sand to build a thick, durable ceramic shell around the pattern. This shell will eventually serve as the mold for the molten metal.
- Wax Removal: Once the ceramic mold has dried and hardened, it is heated in a kiln, causing the wax to melt and drain away. This leaves a hollow ceramic mold ready for metal casting.
- Metal Pouring: Molten metal is then poured into the ceramic mold, filling the cavity left by the melted wax pattern. The liquid metal flows into every detail of the mold, capturing the intricate design of the original pattern.
- Cooling and Solidification: The metal is allowed to cool and solidify within the ceramic mold. Proper cooling is essential to ensure that the casting achieves the desired mechanical properties and dimensional accuracy.
- Final Touches: After the metal has solidified, the ceramic mold is broken away to reveal the metal casting. The casting is then subjected to finishing processes such as grinding, polishing, and machining to achieve the final specifications and surface finish.
When to Use Investment Casting
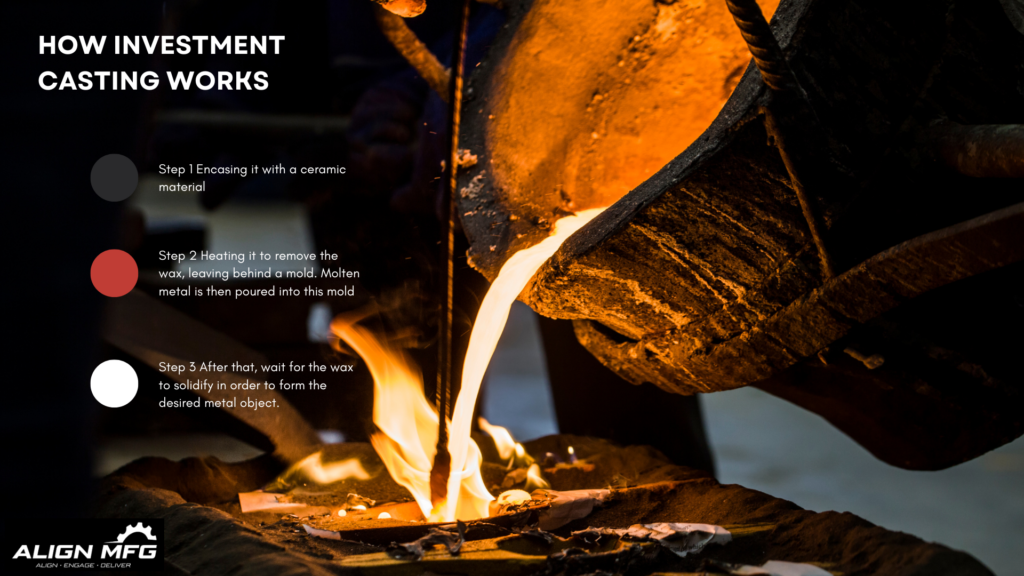
Investment casting is a process known for its complexity and labor intensity, making it relatively costly. However, the advantages it offers often justify the expense. This method is highly versatile and can accommodate nearly any metal. Although typically used for smaller parts, it is also effective for producing components that weigh 75 lbs or more.
The process yields parts with exceptional dimensional accuracy, often achieving net-shape forms that require minimal to no secondary machining. The same die can be reused repeatedly with minimal maintenance. For high-volume orders, the time and labor saved by reducing or eliminating secondary machining can compensate for the cost of new tooling. Conversely, smaller production runs may not justify the initial investment, making investment casting most economical for batches of 25 parts or more.
The entire process from creating a fresh wax pattern to completing a casting typically takes around seven days. The majority of this time is spent building and drying the ceramic shell mold. Some foundries have quick-dry capabilities that can expedite the process. The labor and time-intensive nature of investment casting impacts not only cost but also production timelines. Due to limited equipment and production capacity in foundries, longer lead times are often encountered for investment casting projects.
Common Materials Used
Lost wax casting can utilize a variety of metals and alloys, each chosen for specific properties and applications:
- Stainless Steel: Known for its corrosion resistance, high strength, and excellent durability, stainless steel is commonly used in industries such as aerospace, medical, and food processing.
- Carbon Steel: Valued for its durability, machinability, and cost-effectiveness, carbon steel investment casting is widely used for auto parts, construction, and heavy machinery applications.
- Alloy Steel: Offers enhanced mechanical properties such as increased strength, toughness, and wear resistance, making it suitable for demanding applications in the oil and gas, mining, and defense industries.
- Aluminum: Lightweight and corrosion-resistant, aluminum is ideal for aerospace, automotive, and consumer electronics applications where weight reduction is critical.
- Brass and Bronze: These alloys are excellent for decorative and electrical applications due to their attractive appearance, good conductivity, and resistance to corrosion.
Applications of Investment Casting in Various Industries
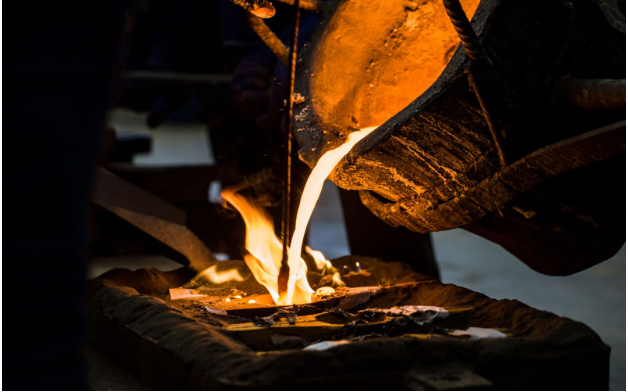
Investment casting is employed across numerous industries due to its versatility, precision, and ability to produce complex shapes with high-quality finishes:
Aerospace: It is used to produce turbine blades, engine components, and other critical parts that require high strength, heat resistance, and precise geometries.
Automotive: Engine parts, suspension components, and various other automotive parts benefit from the precision and durability of lost wax casting, contributing to improved performance and longevity.
Medical: Surgical instruments, prosthetic devices, and orthopedic implants are manufactured using investment casting to achieve the high levels of precision and biocompatibility required for medical applications.
Military: Weapon components, vehicle parts, and other defense-related items rely on lost wax casting for their strength, reliability, and ability to meet stringent specifications.
Industrial: Pumps, valves, impellers, and various other machinery parts are produced using investment casting to ensure durability, reliability, and efficiency in industrial operations.
Success Story: Precision Investment Casting for Hydraulic Hose Manufacturing
A hydraulic hose machinery manufacturer required parts with extremely tight tolerances (+0.0000”, -0.0002”) and high durability for 1,000 RPM. They needed around 200 pieces annually but faced challenges with technical specifications, cost, and volume, as most factories demanded minimum quantities of 1,000 pieces.
Align Manufacturing partnered with an AS9100-certified foundry in Thailand. We determined the necessary CNC machining processes for the required tolerances and proposed consolidating shipments with another order from a different Thai factory, cutting shipping costs by approximately $2,000 per shipment.
Relocating production to Thailand saved the client tens of thousands of dollars annually by avoiding a 25% tariff. The consolidation strategy further reduced shipping costs, enhancing overall cost efficiency.
Automation and Quality Control
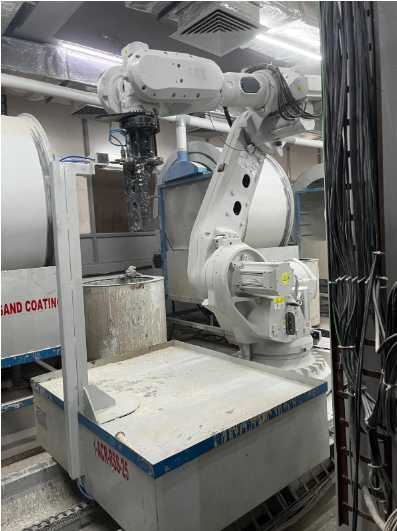
Automation plays a significant role in modern investment casting, enhancing consistency and efficiency throughout the process. Automated systems are used for wax injection, shell building, and even metal pouring, ensuring that each step is performed with precision and minimal human error. Quality control is also crucial, involving rigorous inspections at various stages, such as dimensional checks, non-destructive testing, and metallurgical analysis. These measures ensure that the final castings meet the stringent requirements of industries where precision and reliability are paramount.
Innovation and New Technologies
Innovation and new technologies are continuously transforming the field of investment casting. The integration of advanced computer-aided design (CAD) and simulation software allows engineers to optimize mold designs and predict potential issues before production begins. Additionally, 3D printing technology is revolutionizing the creation of wax patterns, enabling more complex and precise designs. New materials and coating technologies are also being developed to enhance the durability and performance of cast components, ensuring they meet the ever-evolving demands of various industries.
Advanced Insights and Decision-Making
Comparison with Other Casting Methods
Investment Casting vs. Sand Casting:
- Precision: Investment casting offers higher precision and better surface finishes compared to sand casting, making it ideal for components with complex geometries and tight tolerances.
- Complexity: Investment casting is better suited for producing parts with intricate designs and fine details, while sand casting is more appropriate for simpler shapes and larger parts.
- Cost: Investment casting generally has higher upfront costs due to the detailed process and materials involved, but it can lead to overall cost savings through reduced machining and finishing. Sand casting is typically less expensive for larger, simpler parts but may require more extensive post-casting work.
Investment Casting vs. Die Casting:
- Materials: Investment casting allows for a broader range of materials compared to die casting, which is often limited to non-ferrous metals such as aluminum, magnesium, and zinc.
- Precision and Surface Finish: While both methods can produce high-precision parts with smooth surface finishes, investment casting is generally preferred for more complex geometries and tighter tolerances.
- Tooling Costs: Die casting typically involves higher tooling costs but can be more economical for large production runs due to faster cycle times and lower per-part costs. Investment casting, with its ability to produce complex parts in smaller quantities, can be more cost-effective for lower volume production.
Cost Analysis
While investment casting can be more expensive initially compared to other methods like sand casting, it often leads to cost savings in the long run due to reduced need for machining and finishing. Additionally, investment casting allows for more complex designs, which can consolidate multiple parts into a single casting, reducing assembly costs and improving overall product performance. The ability to produce high-quality, detailed parts with minimal waste also contributes to the overall cost-effectiveness of the process.
Conclusion
Investment casting is a versatile and precise manufacturing process suitable for producing complex metal parts across various industries. Its benefits, such as high precision, excellent surface finish, and design flexibility, make it a valuable method for producing high-quality components. By understanding the process, materials, and applications, manufacturers can leverage lost wax casting to enhance their products and achieve superior results. At Align MFG, we exemplify the innovative applications and advancements in investment casting, driving the industry forward. The investment in this casting method can lead to long-term cost savings, improved product performance, and greater design possibilities.
FAQs
What are the advantages of investment casting?
Investment casting offers high precision, versatility in material choice, excellent surface finish, reduced machining, and design flexibility. These advantages make it a preferred method for producing complex and high-quality metal components across various industries.
How precise is investment casting?
It can achieve tight tolerances, often within ±0.005 inches per inch, making it ideal for components that require high levels of accuracy and detail. This precision ensures that parts fit together correctly and function as intended.
What materials can be used in investment casting?
A wide range of materials can be used, including stainless steel, carbon steel, alloy steel, aluminum, brass, and bronze. The choice of material depends on the specific properties required for the investment casting application, such as strength, corrosion resistance, weight, and conductivity.
What are the limitations of investment casting?
While investment casting offers numerous advantages, it also has some limitations. The process can be more expensive and time-consuming compared to other casting methods, especially for larger parts. Additionally, the size and weight of the parts are generally limited by the ceramic shell’s strength.
Comprehensive Guide to Stamping
What is Stamping?
Stamping is a crucial manufacturing technique that transforms flat metal sheets or coils into specified shapes. This process encompasses several methods, including punching, blanking, bending, and piercing, utilizing machinery equipped with dies. It is a versatile method extensively employed across various industries to produce large volumes of uniform parts with exceptional accuracy. The process involves a sequence of operations that shape the metal sheet by deforming it plastically into the desired configuration.
Also, the global metal stamping market was valued at USD 213.8 billion in 2023 and is projected to reach USD 257.1 billion by 2028, growing at a CAGR of 3.7% from 2023 to 2028, indicating strong and sustained demand for stamping solutions across various industries.
Benefits of Stamping
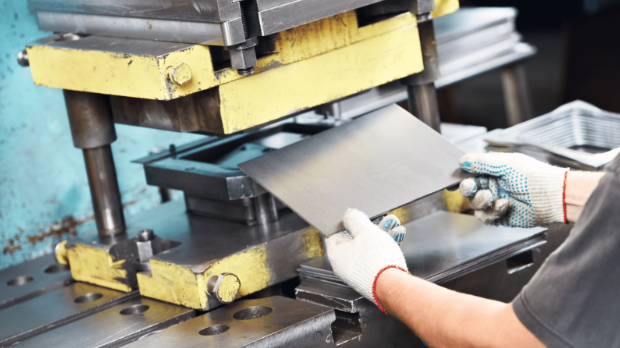
It presents numerous advantages, such as:
- Economic Efficiency: Highly suitable for large-scale production, which lowers the price per unit significantly. The initial investment in tooling and equipment is offset by the reduced per-part cost when manufacturing in high volumes.
- High Precision: Capable of producing intricate parts with precise tolerances. This precision ensures that parts meet exact specifications and function as intended in their applications.
- Rapid Production: Ensures high-speed manufacturing while maintaining consistent quality. The processes can produce thousands of parts per hour, making it ideal for industries that require mass production.
- Versatility: Applicable to a wide range of metals and alloys, making it adaptable for various applications. Different materials can be chosen based on the required properties, such as strength, flexibility, or resistance to corrosion.
- Consistency and Reliability: The use of dies ensures that each part produced is identical, providing high reliability and consistency in large production runs.
Overview of the Stamping Process
The process of metal stamping begins with the design and creation of a die. This die is then installed on a press. Metal sheets are fed into the press, where the die shapes the material into the desired form through a series of operations. The entire process can be automated to improve efficiency and maintain uniformity.
Step-by-Step Explanation of the Process
- Design and Engineering: Crafting detailed designs and specifications for the component and die. This stage involves creating a precise blueprint of the part to ensure it meets all required dimensions and tolerances.
- Die Fabrication: Constructing the die based on the provided design specifications. Dies are typically made from hardened steel and are designed to withstand repeated use.
- Material Selection and Preparation: Choosing and preparing the metal sheets for the process. This includes cutting the sheets to size and ensuring they are free from defects.
- Stamping Execution: Feeding the metal sheets into the press where the die performs the required operations. The press applies force to the die, which shapes the metal sheet into the desired form.
- Post-Stamping Finishing: Applying post-stamping treatments such as cleaning, deburring, and surface finishing to the stamped parts. This step ensures that the parts have the required surface finish and are free from sharp edges or burrs.
The Essence of Die Design
At the heart of stamping lies the design and creation of the die, a specialized tool used to cut, shape, and form metal parts. Accuracy in die design translates directly to the precision of the final stamped product.
Understanding the Role of Dies in the Design Process
Dies serve as the lifeline for the process. They function through a meticulous configuration of the punch, die block, and other components to bring a metal part from concept to reality. Die sets need to be engineered to match exact specifications for the stamping operation to meet stringent manufacturing tolerances.
The Complexity in Die Creation
The intricacies of producing a die encompass the consideration of material properties, intended use of the stamped product, and the specific stamping technique being employed. Advanced computational tools are typically employed to simulate the process before the die is manufactured, ensuring that any potential issues are identified and addressed.
Considerations for Efficient Die Design
Successful die design hinges on several factors. Designers must consider metal flow, the clearance between the punch and die, material thickness, and the necessary force for cutting and shaping. These factors, along with the anticipated volume of production, affect the lifespan and performance of the die, and by extension, the cost-effectiveness of the stamping operation.
Mastery in die design incorporates the use of high-tech software alongside seasoned expertise. Designers balance material properties, anticipated wear and abrasion, and even the type of stamping press that will be used. Such comprehensive planning streamlines the process, minimizes the likelihood of errors, and reduces the need for costly rework.
Diagram 1:Understanding the Role of Dies in the Design Process
Delving into the Diversity of Stamping Operations
The landscape of stamping operations allows fabrication of intricate product designs catering to a multitude of industries. Under the umbrella of this manufacturing process, various specialized stamping operations come to light, each distinct, serving its purpose to shape metal into desired products.
Progressive Stamping
Engaging in a step-by-step approach, progressive stamping transforms metal strips progressively through multiple stations. At each station, a different action - punching, coining, bending - is performed. Finished components are sheared off at the final stage, boasting consistency and high production rates.
Transfer Stamping
It separates individual workpieces from the metal strip and transports them from one station to another using mechanical transport systems. Often utilized for larger components, this method enables different operations to be conducted on a single piece, even from varied angles.
Fine Blanking
Fine blanking stands out for its precision. By exerting immense pressure, it produces edges that are smooth and extremely accurate, unlike conventional methods. Automotive, electronics, and medical industries rely on fine blanking for high-fidelity parts.
Additional Techniques
- Fourslide: A versatile process adapting to intricate parts with multiple bends or twists, incorporating the actions of four sliding tools.
- Deep Draw: Ideal for creating deep, hollow shapes like pots and sinks, using a series of dies to draw the metal into the desired form.
- Short Run: Optimal for small-scale production where the setup and costs of progressive stamping are not justified.
Diverse in approach, each stamping operation molds the metal into final products with varying attributes of precision, efficiency, and design complexity. This tableau of techniques gives manufacturers the flexibility to match any production requirement, fueling innovation across industries.
Types of Materials Used in Stamping
Stamping can be performed on various types of metals, each offering unique properties and benefits:
- Steel: Often used for its strength and durability, making it suitable for automotive and industrial applications. Different grades of steel can be used depending on the required properties, such as tensile strength or hardness.
- Aluminum: Lightweight and corrosion-resistant, aluminum is ideal for aerospace and consumer electronics. Its light weight makes it suitable for applications where reducing overall weight is crucial.
- Copper: Known for its excellent electrical conductivity, copper is commonly used in electrical components and connectors. It is also used for its thermal conductivity in heat exchangers and similar applications.
- Brass: Combines durability and malleability, making it suitable for decorative and functional applications. Brass is often used in applications where both appearance and performance are important.
- Stainless Steel: Resistant to rust and staining, stainless steel is frequently used in kitchenware and medical instruments. Its resistance to corrosion makes it ideal for applications in harsh environments.
Applications of it in Various Industries
Stamping is indispensable in several sectors, including:
Automotive Industry
It is crucial in the production of body panels, engine components, and interior parts. The ability to produce large volumes of high-precision parts makes it essential for the automotive industry, where consistency and quality are paramount.
Electronics Sector
In the electronics sector, stamping is used for manufacturing connectors, enclosures, and heat sinks. The high precision and ability to work with conductive metals like copper make it ideal for producing components that require tight tolerances and reliable performance.
Aerospace Industry
The aerospace industry relies on stamping for the creation of intricate parts for aircraft and spacecraft. Components such as brackets, fasteners, and structural elements benefit from the precision and durability provided by stamping processes.
Consumer Goods Sector
In the consumer goods sector, it is used for the fabrication of kitchen appliances, tools, and various household items. The versatility and efficiency of stamping make it suitable for producing a wide range of consumer products with consistent quality.
Custom Stamping
This involves specialized metal forming processes that utilize unique tooling and techniques to create parts tailored to customer specifications. This method is used across a wide array of industries and applications, ensuring high-volume production needs are met while maintaining precise part specifications.
Automation in Stamping
The integration of automation in stamping has revolutionized the manufacturing process. Automated stamping presses and robotic arms significantly enhance production speed and precision, reducing the need for manual labor. Automation ensures consistent quality, minimizes errors, and allows for real-time monitoring and adjustments, leading to higher efficiency and reduced production costs. Moreover, automated systems can handle complex and repetitive tasks, increasing overall productivity and enabling manufacturers to meet the high demands of modern industries.
Benefits of Automation
- Increased Efficiency: Automated systems can operate continuously, significantly increasing production rates compared to manual operations.
- Improved Quality Control: Automation reduces the likelihood of human error, ensuring that each part meets the required specifications.
- Cost Savings: Although the initial investment in automation technology can be high, the long-term savings in labor costs and increased production efficiency can offset these costs.
- Enhanced Flexibility: Automated systems can be programmed to handle a variety of tasks, making it easier to switch between different production runs.
Ensuring Quality Control
Manufacturers must ensure the precision and durability of metal stamped parts. These characteristics hinge on strict quality control procedures during fabrication. A robust quality control system involves routine inspection at multiple stages of the production cycle and adherence to established manufacturing standards.
Quality Control Throughout the Manufacturing Process
Manufacturers adopt a multi-tiered approach to quality control, applying checks at every stage of the stamping process. From the initial material selection to the final product inspection, each phase undergoes rigorous scrutiny. This ensures that the end product meets exact specifications and performance expectations. Such meticulous oversight can significantly reduce the risk of product failure in the field.
Common Quality Control Measures and Standards
- Dimensional Inspection: Gauges and CMM (Coordinate Measuring Machines) are deployed to verify component dimensions against design specifications.
- Material Verification: To confirm material integrity, tests such as tensile strength and hardness are conducted.
- Surface Inspection: Surface defects are identified through visual checks and technologies like laser scanning.
Advanced Insights and Decision-Making
Comparison with Other Forming Methods
When compared to other forming methods like casting, forging, and precision machining, stamping stands out for its ability to produce large volumes of parts with excellent repeatability and precision. While casting and forging are suitable for producing robust parts, they often require more extensive post-processing. Precision machining, though highly accurate, can be more costly for high-volume production.
Cost Analysis
It generally offers a more cost-effective solution for large-scale production due to its automation capabilities and reduced labor costs. Although the initial tooling costs can be substantial, these are offset by the economies of scale achieved in mass production. The efficiency of stamping in producing large volumes of parts with consistent quality contributes to overall cost savings.
Environmental Considerations
Stamping is an environmentally friendly manufacturing process compared to other methods. The process generates less waste material, and the metal scraps produced can be recycled.These scraps are highly coveted in many industries, particularly the foundry industry, for their value and reusability. Additionally, the energy consumption in stamping is lower than in processes like casting and forging, contributing to a smaller carbon footprint.
Innovation in Stamping
Advancements in technology continue to shape the industry. Computer-aided design (CAD) and computer-aided manufacturing (CAM) software have revolutionized die design, allowing for more complex and precise parts. Additionally, the development of high-strength materials and coatings has extended the life of dies, reducing downtime and maintenance costs.
Future Trends in Stamping
The future of stamping is being shaped by several key trends. The adoption of Industry 4.0 technologies, such as the Internet of Things (IoT) and artificial intelligence (AI), is enhancing the efficiency and capabilities of its operations. These technologies enable predictive maintenance, real-time monitoring, and data-driven decision-making, further optimizing the manufacturing process.
Conclusion
Stamping remains an essential manufacturing technique due to its versatility, efficiency, and precision. This process transforms flat metal sheets into various intricate shapes, making it indispensable across numerous industries such as automotive, electronics, aerospace, and consumer goods. The benefits of it include cost-effectiveness, high-speed production, and the ability to work with a wide range of metals.
At Align MFG, we exemplify the innovative applications and advancements in stamping, driving the industry forward. Overall, it is a highly efficient and reliable method for producing complex parts on a large scale, making it a cornerstone of modern manufacturing. Its integration with automation and continuous innovation ensures that stamping will remain a vital manufacturing process for the foreseeable future.
Innovations Transforming Investment Casting
Investment casting, also known as lost-wax casting, has existed for centuries in manufacturing. This is a process for casting metallic parts with great precision and detail; it is, however, a somewhat old format compared to newer versions. This article takes a look at some of the recent developments in investment casting today, with a special focus on 3D printing and new material technologies.
Lost-wax casting is a manufacturing process that produces a wide variety of products of complex geometries. It generally involves a wax pattern surrounded by a ceramic shell. When the shell hardens, the wax is melted out to leave a mold. Hot metal is poured into the mold and the casting can be completed. It is highly commended for products that have excellent surface finish quality and have close tolerances. It is applied in several industries, from aerospace and automotive to medical, where precision, quality control and automation take the foremost place.
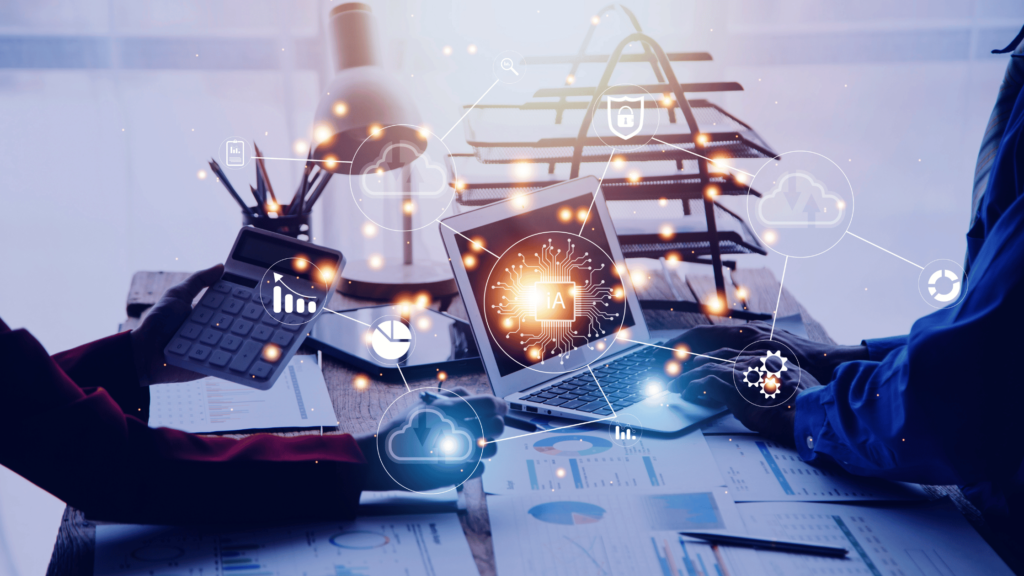
Historical Context and Traditional Methods
Historical origins date back over 5,000 years to ancient civilizations like Mesopotamia and Egypt. Traditional investment casting usually involves several labor-intensive steps:
- Pattern Creation: A wax pattern has to be made that is a replica of the final part.
- Assembly: Several wax patterns can be attached to a tree-like configuration.
- Shell Building: The wax pattern is to be dipped into a ceramic slurry and coated with sand to produce a hard shell.
- Wax Removal: The shell is heated to melt and drain out the wax to leave behind a hollow ceramic mold.
- Casting: Molten metal is poured into the mold.
- Finishing: The ceramic shell is broken away from the cooled metal and the metal part is finished.
While effective, this traditional method is time-consuming and requires significant manual labor. Innovations in technology are addressing these challenges and transforming the process.
3D Printing: A Game Changer in Investment Casting
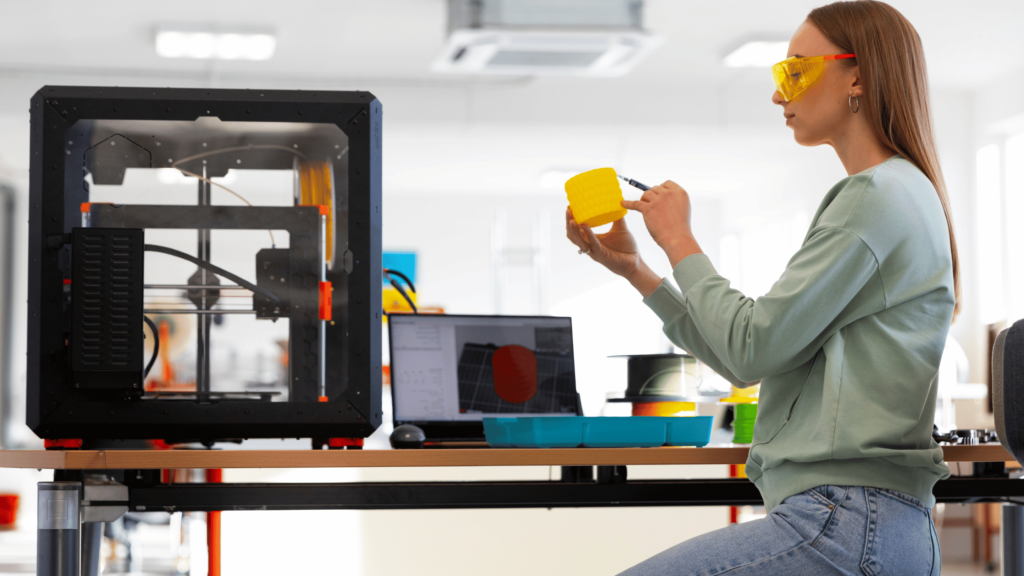
Application of 3D printing or additive manufacturing in the investment casting has significantly revolutionized the process. Earlier, the wax patterns were made by molds and were laborious and, on occasion, costly, especially for something with complex shapes. 3D printing avails a cost-effective and quick alternative.
Advantages of 3D Printing in Investment Casting
- Design Flexibility: It is perfect for creating complex geometries, impossible or very hard to create using traditional methods.
- Reduced Lead Time: The application of 3D printing to make patterns nullifies the need to make the molds, and this way, it reduces the time taken to manufacture patterns significantly.
- Cost Effective: In case of low volume production itself, or prototyping, 3D printing can turn out to be more cost-effective than the traditional lost-wax method in cases of tooling.
- Parts Customization: it has easy parts customization. No additional tooling, neither molds are needed.
3D Printing Technologies in Use
There are several 3-D printing technologies applied to investment casting, each with its unique sets of benefits:
- Stereolithography (SLA): This makes use of a laser to cure liquid resin into solid shapes. It can come up with never seen before detailed and accurate patterns.
- Selective Laser Sintering (SLS): It is a laser kerosene that fuses powdered material, layer by layer, to make powerful and robust patterns.
- Fused Deposition Modeling (FDM): In the FDM process, the melted material gets extruded and laid down to construct the layers. The cost-effective and rapid method to build patterns which are relatively simple.
New Material Technologies
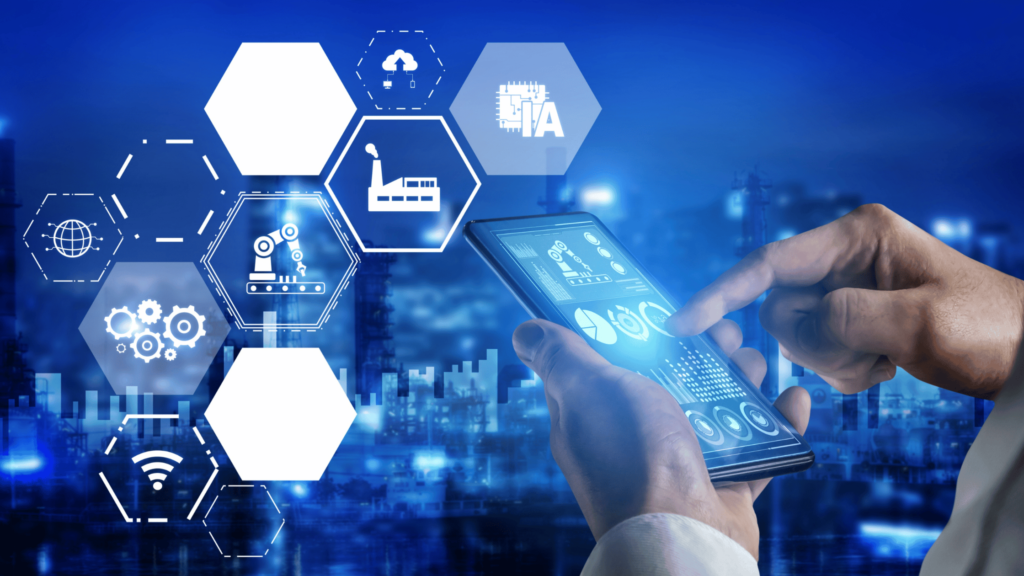
Advancements in material science are also revolutionizing investment casting. New material and new alloys are making the cast parts of better quality, robust, light, and durable.
High-Performance Alloys
New high-performance metals are manufactured to cater to the demanding needs of industries ranging from aerospace, automotive, and medical. These new materials boast improved mechanical properties, corrosion resistance, and temperature tolerance.
Ceramic Shell Improvements
Advanced ceramic shells revolutionize the investment casting process. Improved ceramic formulations enhance the strength and stability, thus reducing the risk of defects and increasing the quality of the cast parts.
Benefits of Advanced Ceramic Shells
- Higher Strength: Improved ceramic materials can withstand higher temperatures and mechanical stresses, allowing for the casting of more robust parts.
- Reduced Defects: Enhanced formulations reduce the occurrence of common casting defects such as cracks and inclusions, leading to higher quality parts.
- Faster Production: Advanced ceramics can shorten the shell-building process, increasing production speed and efficiency.
Integration of Smart Technologies
The integration of smart technologies, such as the Internet of Things (IoT) and Artificial Intelligence (AI), is also making its way into investment casting.
IoT and AI in Investment Casting
- Real-Time Monitoring: The Internet of Things will monitor the casting process in real time by means of different built-in sensors to provide data for maximizing production and minimizing defects.
- Predictive Maintenance: Using AI algorithms to analyze, equipment breakdowns could be predicted, and timeously fixed before they occurred. Reduces downtime and maintenance costs.
- Process Optimization: AI can analyze production data and detect inefficiencies. It can even suggest alternatives, enhancing the general efficiency of the process used in casting.
Future Trends
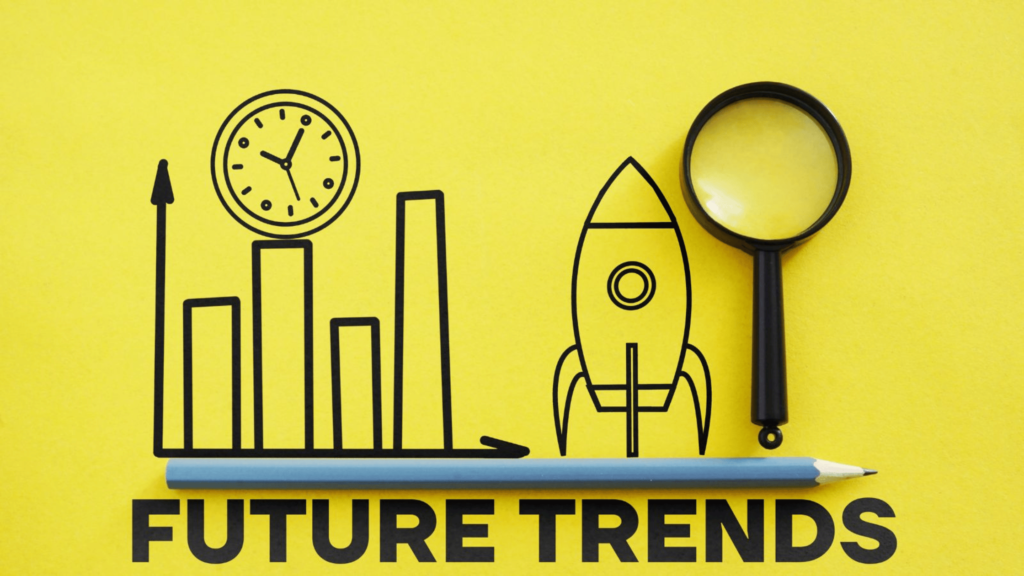
The future of investment casting looks promising, with continued advancements in 3D printing, material technologies, and smart manufacturing. As these technologies evolve, they will further enhance the capabilities and applications of investment casting, opening up new possibilities in various industries.
Emerging Technologies
- Digital Twin Technology: This is the technique for the development of a digital replication or model of physical process operation. This helps to monitor internal operations in real time for optimization. In general, it can help in the prediction and prevention of potential problems that would occur.
- Sustainable Practices: Developments of materials and processes are also done in sustainability. A conductive approach towards eco-friendly materials and the recycling of the materials used in the casting is reducing the impact of investment casting on the environment.
- Hybrid Manufacturing: Traditional techniques used in casting are combined with modern-day techniques, like 3D printing, to design hybrid manufacturing processes. This develops efficient production and better-quality parts.
Conclusion
Investment casting is indeed being transformed through innovative technologies. Other applications of 3D printing and new material technologies besides improving efficiencies and qualities within the manufacturing process continue to expand the applicability of the casting process. These innovations will undeniably be the logos of the manufacturing future that will thus make the investment casting process more flexible and effective than ever before.
Automation and Quality Control in Investment Casting
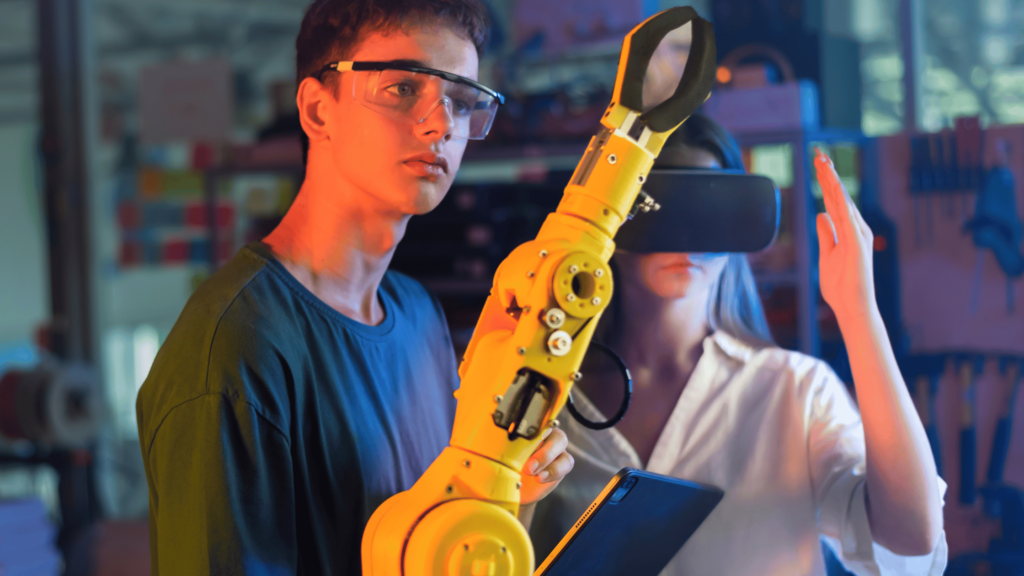
Investment casting, also known as lost-wax or precision casting, is one of the oldest doctrines to intricately craft components. Though the origin of the process can fold many centuries back, it does not necessarily mean that it is antiquated thereby. The improvements and changes made have been brought on by automation and advanced quality control. These have improved the areas of efficiency, precision, and part reliability, all of which contribute to the competitiveness of investment casting in this high-paced manufacturing environment. This blog goes through the aspects of automation: its role in the enhancement of the process and the critical quality control measures that ensure part reliability.
The process of Investment Casting
Investment casting is a manufacturing process for generating complicated and high-precision components. Such a process starts with the creation of a wax pattern, which is an exact replica of the desired part. The pattern is then coated with a ceramic shell to fashion a mold. After this ceramic shell hardens, wax is melted out of it, leaving a cavity that is then filled with molten metal. Later on, after it solidifies, it is to be broken away to reveal the final casting. The process is marked by its ability to generate parts with high surface finish and tight tolerances, which qualifies it to be applied in critical industries such as oil, railway, construction, and industrial sectors.
The Role of Automation
Automation has revolutionized many aspects of the lost-wax casting process. Manufacturers no longer have to rely on the human hand for repetitive and precise tasks. Instead, automated systems have been incorporated, which allow them to achieve higher levels of precision while reducing lead times and improving overall efficiency. Outlined below are some of the ways in which automation is bringing much improvement to precision casting.
Automated Pattern Creation
Historically, the making of wax patterns has been a very labor-intensive process. However, this process has been improved with automation to a great extent. Automated pattern making machines can produce wax patterns with remarkable tolerance and repeatability based on computer-aided design data.
- Faster Delivery and Shorter Production Time: Automation processes the pattern making at a quicker rate, thus reducing the lead time for production.
- Makes Patterns of Complex Geometries: Machines are capable of producing complex geometries for the patterns of designs that would not either be possible or practical to reproduce using manual techniques.
Robotic Shell Building
Another area of the process that has been revolutionized with automation is the shell building process in making the ceramic shell around the wax patterns. The robotic system carries out the wax pattern’s dipping, draining, and stuccoing (coating with ceramic).
- Higher Precision: Automation ensures precise control over the amount and parameters of pouring. Since molten metal is poured into ceramic shells, automation can maintain the right temperature of molten metal thus preventing defects due to poor pour temperature.
- Even Pouring: Delivering molten metal through robots at a steady pace prevents defects like entrapment of air or incomplete fills.
- Safety: Since automation prevents accidents due to molten metal handling, the workers’ safety is ensured.
Quality Control Measures in Investment Casting
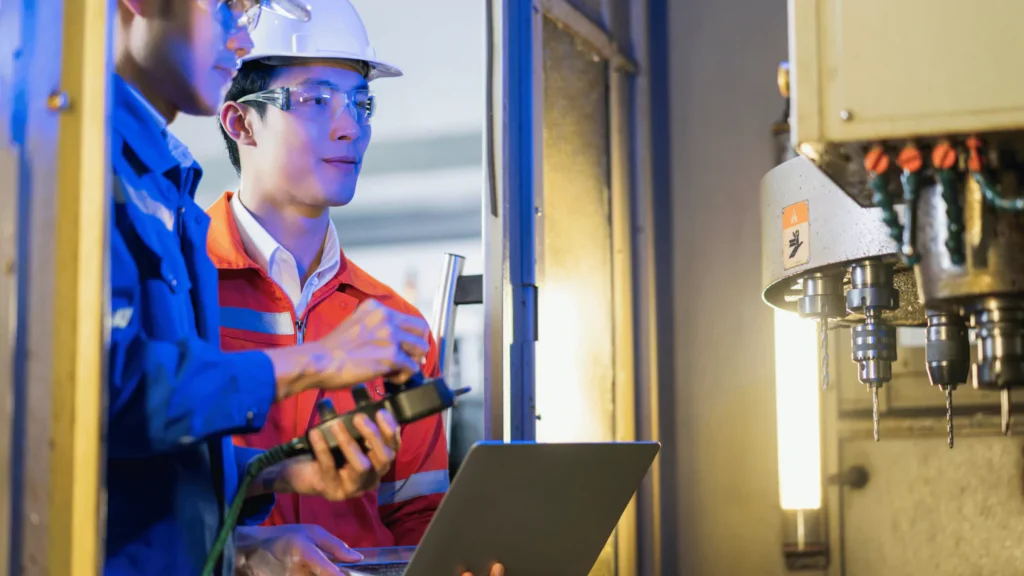
Quality control involves various critical steps, from inspection of patterns in the initial stages to the final evaluation of the products. In a nutshell, the following is major quality control measures in lost-wax casting:
Pattern Inspection
The quality of the final cast part depends on the tolerance of the wax pattern. Inspection of the wax pattern is hence an important step.
- Dimensional Criteria: The patterns are gauged for dimensional features, and modern gauging appliances like CMM are used for inspection.
- Surface Condition: Scrutinizing the surface of the wax pattern for imperfections prevents flaws from appearing in the final casting.
Shell Integrity Testing
This is critical in the case of the ceramic shell used in the casting process. Any defect in the shell may result in defects in the final part.
- Visual Inspection: The shell is visually inspected for cracks, incomplete covering, or some other defects.
- Non-Destructive Testing (NDT): Ultrasonic testing and radiographic inspection help to detect internal defects in the ceramic shell.
Metal Quality Control
The quality of the molten metal is another important factor in casting. Quality metal is free of impurities and has the right composition to produce quality cast parts.
- Spectroscopy: This will be applied in analyzing the chemical composition of the metal to assure that it meets the required specifications.
- Inclusion Analysis: The analysis is carried out using such techniques as optical and scanning electron microscopy to detect non-metallic inclusions present in the metal.
Post-Casting Inspection
After the metal has been poured and the ceramic shell has been removed, these post-cast inspections help ensure the quality of the end product.
- Dimensional Testing: Checking the dimensions of the cast part to verify with the specifications undertaken.
- Surface Testing: Testing the cast part for cracks, porosity, or surface roughness.
- Mechanical tests: Test and confirm that mechanical properties, including, for example, tensile strength and hardness, are as per or meet the specified in the required specification.
Advanced Automation Techniques
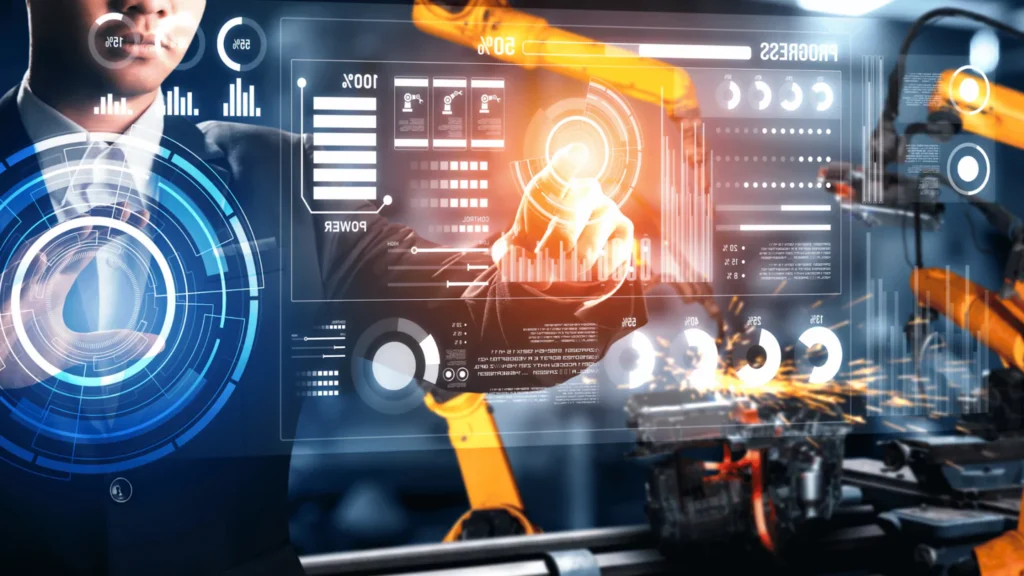
The adoption of advanced automation further elevates the process. Artificial intelligence, machine learning, and the Internet of Things are some commonly used concepts.
Artificial Intelligence and Machine Learning
In the context of casting, artificial intelligence and machine learning can be harnessed to study the huge data that comes out from the casting process to note the patterns and sometimes even predict results. The manufacturers employ it for improvement in process and quality control.
- Predictive Maintenance: Predicts when equipment is likely to fail, allowing maintenance to be planned in advance, thereby reducing unplanned downtime.
- Process optimization: ML algorithms can analyze process parameters and suggest adjustments which enhance yield and reduce defects.
- Defect Prediction: AI can predict the likelihood of defects in cast parts and allow early intervention and corrective measures.
Internet of Things (IoT)
IoT is about implementing a setup to help collect data regarding various parameters around the casting process. IoT sensors monitor the temperature, pressure, and other critical parameters of the casting process in real-time. Data collected by IoT can further be analyzed for trends, detecting anomalies, and optimizing processes. This process can be adjusted and controlled remotely, allowing for interventions from a distant location.
Automation and Innovation in Critical Industries
Automation and quality control in investment casting have brought transformative changes, particularly in critical industries. These industries demand high precision, reliability, and innovation, and it has risen to the challenge.
Digital Twin Technology
Digital twin technology means a fully detailed virtual copy of the foundry process. The model is digital, allowing for process simulation and optimization in real-time.
- Process Simulation: The digital twins can simulate various situations, through which the manufacturers can optimize process parameters.
- Predictive Analytics: Data from the digital twin is subjected to analytics to allow manufacturers to make predictions concerning possible failures and, in that way, take preventive actions.
- Continuous Improvement: The foundry process can be continually monitored and improved through digital twin technology, thereby increasing process efficiency and quality.
Sustainable Manufacturing Practices
The current trend in the manufacturing industry is a move toward more sustainability. Automation and quality control make possible more sustainable lost -wax casting. An automated process ensures optimization in the consumption of energy and, in return, minimizes the environmental impact brought about by the casting process. Quality control measures will also help reduce defects and scrap, thus reducing waste materials and conserving resources. Material science has not been left behind in this quest, and more eco-friendly casting materials have been developed.
Conclusion
Automation together with quality control has created the most significant changes in the industry of investment casting. With the help of advanced technologies, the manufacturer can achieve the highest levels of precision, efficiency, and part reliability. Automation of casting steps, starting from pattern creation up to pouring, and quality control of the results of every step, streamlines the process, ensuring that every part meets strict standards. Financial investment casting will only shine more with the constant development of technologies such as AI, IoT, and digital twins. The innovations will put manufacturers well in the race in a market that is rapidly changing and in regard to top-quality components meeting high requirements, especially in the aerospace, automotive, and medical industries. It is expected that the merging of automation and quality control will bring further improvements in functionality and sustainability.
The Materials Behind Investment Casting
Investment casting is a widely used manufacturing process that allows the production of intricate and complex metal components with high precision. This process involves creating a wax pattern of the desired part, coating it with a ceramic shell mold, and then melting the wax out to create a hollow metal mold. The mold material is then filled with molten metal to produce the final component.
One of the critical aspects of lost-wax casting is the choice of materials, both for the wax pattern and the shell, as they directly influence the quality, integrity, and performance of the finished product. In this article, we will explore various precision casting materials, including plastic pattern materials, shell materials, and the metals commonly used for casting.
We will delve into their properties and characteristics, highlighting their suitability for different applications and discussing their advantages and limitations in the investment casting process.
Advantages of Investment Casting
Precision casting is a highly advantageous manufacturing process, known for its ability to produce precision components with intricate and complex shapes that other methods may struggle to achieve. One of the standout benefits of this technique is its exceptional dimensional accuracy and the ability to maintain tight tolerances, which are essential in industries such as aerospace and medical devices where precision is paramount.
Additionally, investment casting can utilize a vast range of materials, providing flexibility in application across various industries. The process also allows for excellent surface finish, reducing the need for additional machining and finishing steps, which can significantly lower production costs.
Moreover, the versatility in size and weight of the components that can be produced makes it suitable for both small and large parts, enhancing its applicability for different product requirements.
If you want to know more about investment casting, check out our article about The Basics of Investment Casting: An Introduction.
But for now, let’s dive into the different materials that can be used for the different casting methods.
Stainless Steel
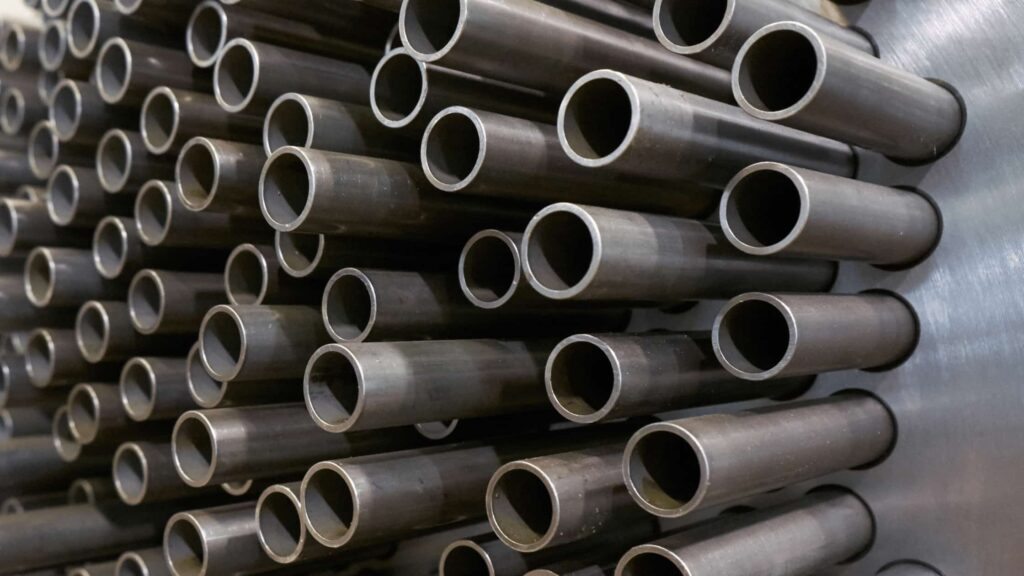
It is a versatile material with numerous applications and advantages. Its primary characteristic is its superior durability, making it ideal for various industries. One significant area where stainless steel is extensively used is investment casting.
In the automotive industry, stainless steel is utilized in gearbox parts and gears. The high strength and corrosion resistance of it ensure that these components can withstand the demanding conditions of a vehicle’s transmission system. Moreover, stainless steel’s resistance to heat and wear makes it an excellent choice for cam components, which are essential for controlling the opening and closing of valves in an engine. Golf club heads also benefit from stainless steel’s durability and resistance to corrosion, ensuring longevity and performance on the golf course.
Compared to other materials, it offers numerous advantages. Its corrosion resistance eliminates the need for maintenance and frequent replacements. Additionally, it can withstand high temperatures, making it suitable for applications where heat resistance is crucial. Furthermore, the aesthetic appeal, with its shiny and clean appearance, adds to its desirability in various industries. Overall, stainless steel’s unmatched durability, corrosion resistance, and versatility make it a highly sought-after material for investment casting process, automotive gearbox parts and gears, cam components, golf club heads, and many other applications.
Low Alloy Steel
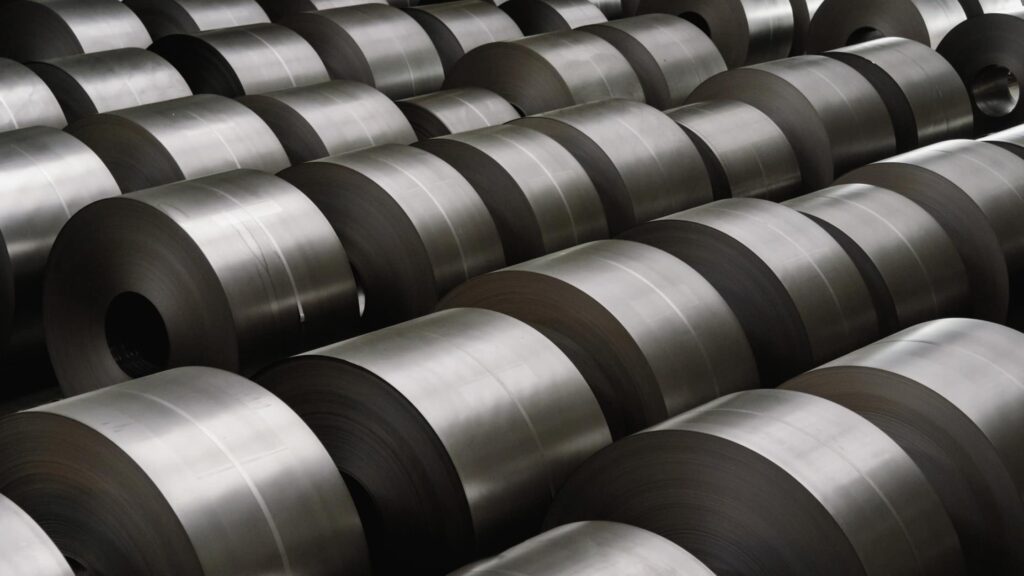
Low alloy steel, as the name suggests, is a type of steel that has a low percentage of alloying elements, usually less than 8%. This makes it more affordable compared to high alloy steels, which contain higher amounts of alloying elements.
It offers numerous benefits due to its beneficial mechanical properties. It has excellent strength and toughness, making it suitable for demanding applications where high strength and impact resistance are required. Additionally, it has good corrosion resistance, making it ideal for use in corrosive environments.
One of the key advantages is its suitability for specialized heat-treating processes. These processes involve altering the microstructure of the steel to enhance its properties. For engineered parts, low alloy steel can undergo specific heat treatments such as quenching and tempering to achieve desired hardness, strength, and wear resistance.
The applications are diverse. It is commonly used in the automotive and aerospace industries for parts that require high strength and durability, such as engine components and aircraft landing gear. Low alloy steel is also widely used in construction, oil and gas, and manufacturing industries for structural applications and machinery components.
Aluminum Alloy
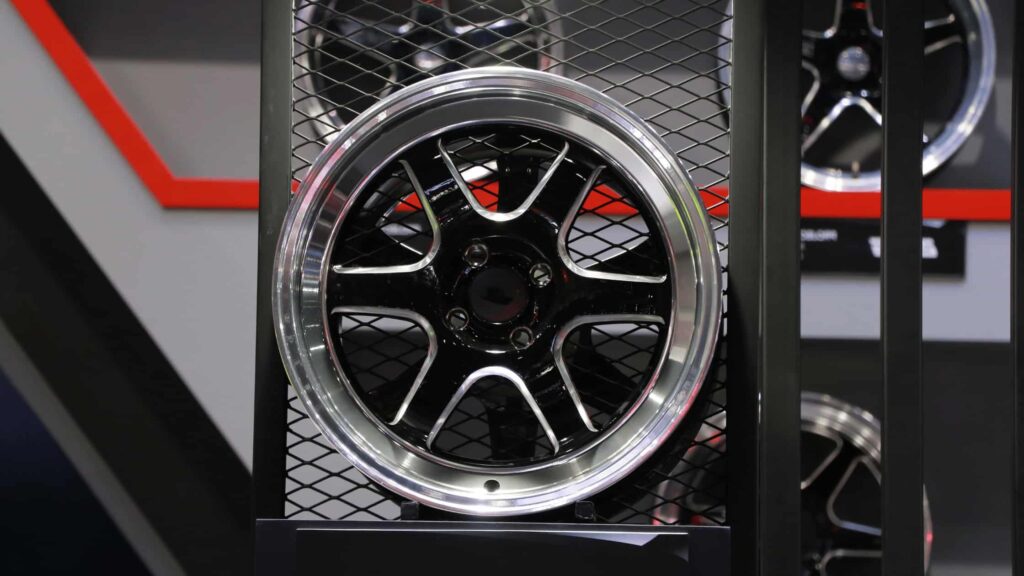
Aluminum alloy is a versatile material widely used for investment castings due to its beneficial properties and wide range of applications. Its key advantages include excellent strength-to-weight ratio, corrosion resistance, and high thermal and electrical conductivity.
Investment castings made of aluminum alloy find applications in various industries, including automotive, electronics, and industrial equipment. In the automotive sector, they are preferred for their lightweight nature, which helps improve fuel efficiency and reduce emissions. They are commonly used for components like engine blocks, cylinder heads, and wheels.
The blend of aluminum, silicon, and magnesium greatly enhances the strength and suitability of aluminum alloy for these applications. The addition of silicon provides improved fluidity during the casting process, making it easier to achieve intricate and complex shapes. Magnesium, on the other hand, increases the alloy’s strength and ductility, allowing it to withstand high-stress applications.
In electronics, aluminum alloy investment castings are used for heat sinks, connectors, and housings, as they possess excellent thermal conductivity, ensuring efficient heat dissipation and component protection. In the industrial equipment sector, these castings are employed in pumps, valves, and machinery components, benefiting from the alloy’s durability and resistance to wear and tear.
Carbon Steel
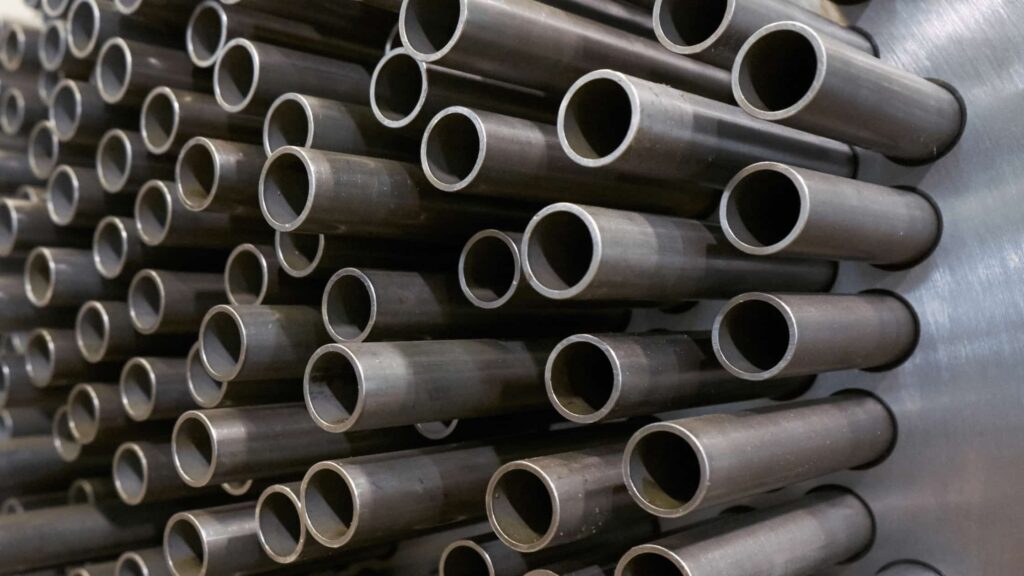
Carbon steel, composed primarily of carbon and iron, is a widely used material known for its low cost compared to other alloys. It comes in various grades based on carbon content, with higher carbon levels resulting in stronger and harder steel.
Carbon steel can be easily shaped and formed into different products, and its performance can be improved through heat treatment, which enhances its hardness, strength, and toughness. One notable property is its ferromagnetic nature, making it useful in motors and electrical appliances. Carbon steel is commonly used in the construction of electric motors, transformers, and generators due to its magnetic properties and cost-effectiveness.
Super Alloy
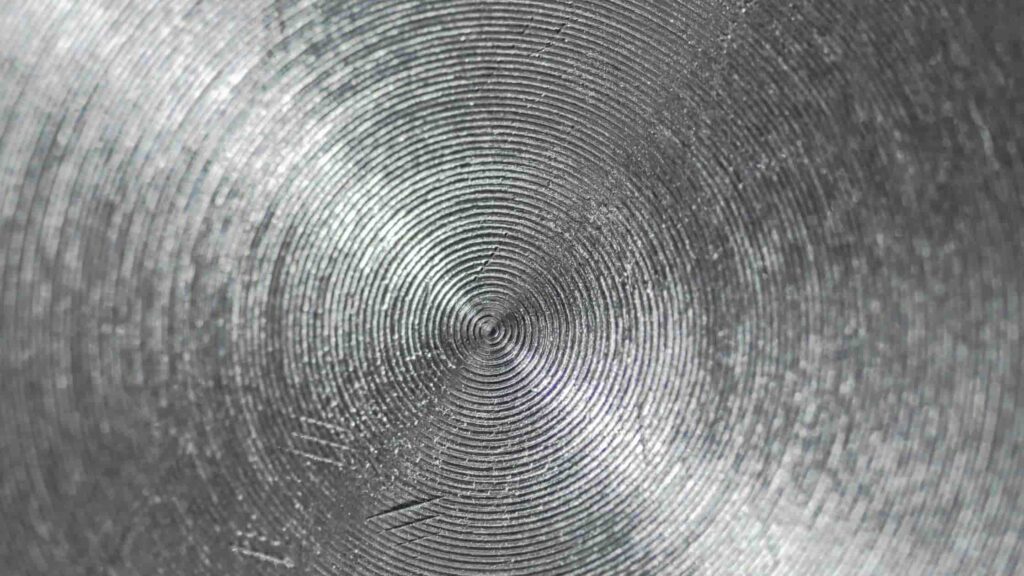
Super alloys, or high-performance alloys, particularly nickel-based and cobalt-based, exhibit exceptional mechanical strength, resistance to extreme temperatures, corrosion, oxidation, and wear. They retain their mechanical properties at temperatures exceeding 1000°C, making them indispensable in gas turbine engines, aerospace components, and nuclear reactors.
Super alloys also offer excellent corrosion resistance in aggressive chemicals, acids, and seawater, benefiting chemical processing plants, marine applications, and oil and gas exploration. Their wear resistance allows them to withstand abrasive materials and heavy mechanical loads, making them ideal for high-stress components like turbine blades and jet engine parts. Despite their higher cost compared to sheet metal, super alloys’ superior properties, reliability, and longevity make them a cost-effective choice for demanding applications.
Copper Alloy
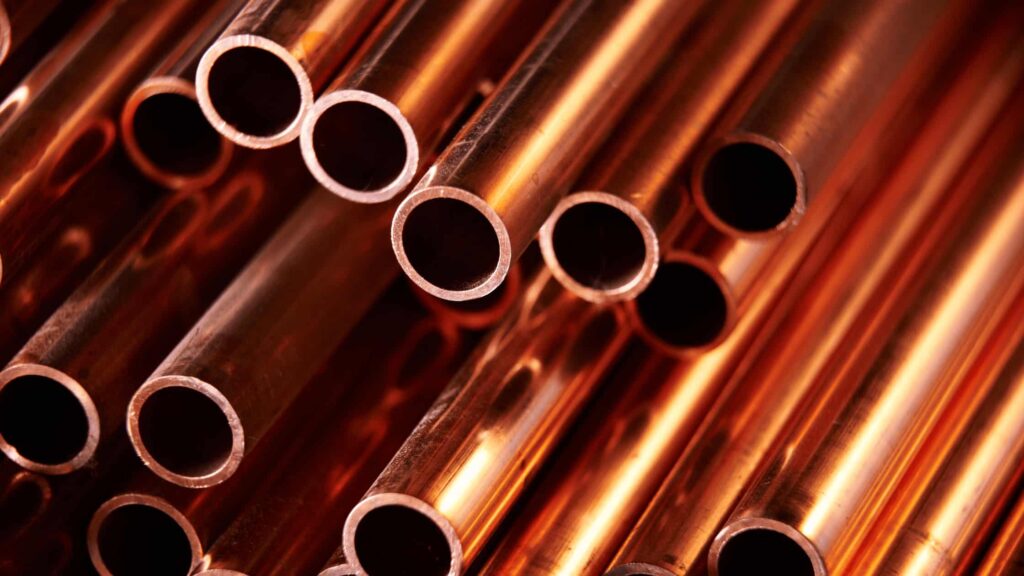
Copper alloys, created by mixing copper with other metals, offer superior strength, corrosion resistance, electrical conductivity, thermal conductivity, and good formability. Bronze and brass are two common types of copper-based alloys used in investment castings. Bronze, an alloy of copper and tin, offers high strength, corrosion resistance, and excellent thermal conductivity, making it suitable for musical instruments, statues, and fittings. Brass, an alloy of copper and zinc, is known for its attractive appearance and easy molding, making it popular for decorative items, plumbing fittings, and electrical connectors. Beryllium-copper, one of the strongest copper-based alloys, possesses exceptional corrosion resistance, high strength, hardness, and electrical conductivity, making it ideal for components in the aerospace and automotive industries subjected to harsh environments and high stress conditions.
Cast Iron
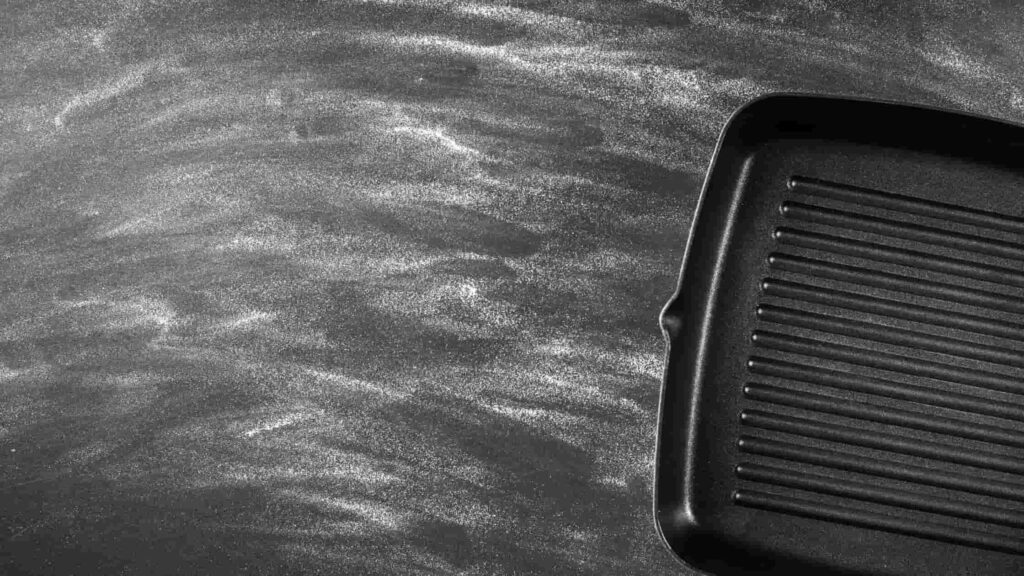
Cast iron is a strong and versatile material that is commonly used in various industries due to its unique characteristics. It is derived from iron and carbon, with a carbon content of at least 2%, making it harder and more brittle than steel. The production process of cast iron involves melting iron and adding carbon and other alloys to achieve the desired properties. This mixture is then poured into molds and allowed to cool and solidify.
One characteristic that makes cast iron desirable is its affordability and high accuracy. Iron castings, especially those made from gray iron and ductile iron, are known for their cost-effectiveness and precise dimensions. This makes them suitable for a wide range of applications, from automotive parts to appliances.
Gray iron, in particular, is easy to cast and has good damping properties, making it ideal for applications that require vibration resistance. On the other hand, ductile iron offers high strength, heat-resistance, and toughness. Its complex production process, which involves adding magnesium to the iron-carbon mixture, results in superior mechanical properties. However, this more intricate process leads to higher production costs compared to cast steel.
Key Takeaways
The selection of metal casting is a critical decision that significantly impacts the final product’s performance and cost-effectiveness. By carefully considering factors like the part’s function, desired mechanical properties, and compatibility with the investment casting process, manufacturers can ensure they choose the optimal ceramic material for their application. This not only guarantees the part meets its performance specifications but also minimizes the need for extensive post-processing, leading to improved production efficiency and tooling cost savings. Therefore, investing time and effort in material selection is a strategic step that unlocks the full potential of precision casting for a broad range of industries.
The Basics of Investment Casting: An Introduction
Investment casting, also referred to as precision casting, is a method for crafting detailed and high-quality metal parts with excellent accuracy and smooth finishes. It’s utilized in sectors such as aerospace, automotive, healthcare, and defense.
This technique offers multiple benefits, including the capability to fabricate complex and intricate designs that might be challenging or unachievable with other manufacturing processes. It also delivers high dimensional accuracy, as the mold faithfully reproduces the details of the die. Additionally, the method allows for fine surface finishes, reducing the need for further machining.
How Investment Casting Works
The investment casting process involves creating a wax pattern, encasing it with a ceramic material, and then heating it to remove the wax, leaving behind a mold. Molten metal is then poured into this mold, which solidifies to form the desired metal object.
Understanding the Step-by-Step Investment Casting Process
Step-by-Step Breakdown:
- Creating the Wax Pattern: The process begins by shaping a wax pattern of the part to be cast. This can be done by injecting wax into a metal mold or by sculpting the wax by hand. The wax model is then attached to wax sprues, which act like channels guiding the liquid metal during the casting.
- Building the Ceramic Shell:The wax pattern attached to sprues is dipped into a ceramic slurry followed by a coating of ceramic particles. This step is repeated multiple times to build a thick ceramic shell around the wax. Each layer must dry thoroughly before the next is applied.
- Melting Out the Wax:Once the ceramic shell is sufficiently thick, it is heated in a furnace. This step melts the wax inside the shell, which is then drained out, leaving a hollow ceramic mold that mirrors the original wax pattern.
- Pouring the Molten Metal:The ceramic mold is preheated to prepare for metal casting. Metal is melted in a crucible and then poured into the hot ceramic mold through the sprues.
- Removing the Ceramic Shell:After the metal has cooled and solidified, the ceramic mold is broken away, revealing the metal part. Sprues are cut off, and any remaining ceramic fragments are cleaned off the metal.
Further Steps to Perfect the Casting:
- Refining Wax Patterns:The accuracy of the wax patterns is crucial as they directly influence the final metal part’s details. Techniques like hand carving, using steel tools, or 3D printing are employed based on the complexity and quantity needed. Each method offers different benefits, from artisanal detail to consistent mass production.
- Setting Up the Wax Assembly:Wax patterns are mounted to a sprue and carefully arranged on a casting board to ensure stability and precise alignment during casting. This setup is crucial for maintaining design integrity and ensuring the molten metal flows correctly into each cavity.
- Forming the Mold Shell:The assembly is repeatedly dipped into a ceramic slurry and coated with sand stucco to form a strong, heat-resistant mold. Achieving the right thickness and strength of the shell is vital for withstanding the molten metal’s temperature.
- Wax Removal Techniques:Removing the wax can be done manually or using automated ejectors in the die, depending on the precision and delicacy required. This step is critical for maintaining the mold’s integrity and ensuring clean metal flow.
- Casting the Metal:Techniques such as gravity pouring, vacuum pouring, or pressure casting are chosen based on the part’s complexity and required precision. Each method has its advantages in achieving a defect-free cast.
- Final Touches on Castings:After breaking the mold, the castings are finalized by removing any excess material and refining the surfaces. This can involve various finishing techniques, depending on the metal and the part’s function.
What Is the Main Goal of Investment Casting?
It has been around for centuries and is used to create complex metal parts with great precision. The process of investment casting starts with a wax pattern, which is coated with ceramic to form a hollow mold after the wax is melted away. The main goal of lost-wax casting is to produce intricate, high-quality metal components that are tough or impossible to make with other methods. This casting process is favored in industries such as automotive, aerospace, defense, and jewelry for its ability to produce detailed and precise components.
If you are looking for a more in-depth explanation about the different materials that can be used in investment casting, check out our article about The Materials Behind Investment Casting.
Advantages of Investment Casting
Investment casting is great for making complex and detailed shapes that would be hard to make with other methods. It’s very accurate because the mold captures all the details of the wax model. It also makes parts with smooth surfaces, which means less work is needed to finish them. Some things made with this method include turbine blades, surgical tools, and jewelry.
Understanding the Disadvantages of Investment Casting Products
Despite its advantages, it’s important to be aware of the potential drawbacks of using this process. Here are some of the main disadvantages:
Size and Weight Limitations:
- Lost-wax casting has inherent limits on the size and weight of the products it can produce. The detailed nature of the process restricts the dimensions and mass that can be achieved effectively.
- This method is not ideal for manufacturing large parts or components that require substantial volumes of common material. For larger parts, alternative manufacturing methods might be necessary.
Extended Production Time:
- The process involves several intricate steps, including creating wax patterns, assembling ceramic shells, and multiple stages of heating and cooling. These steps contribute to a prolonged production cycle.
- This extended timeframe can be a significant disadvantage in industries where rapid time-to-market is crucial.
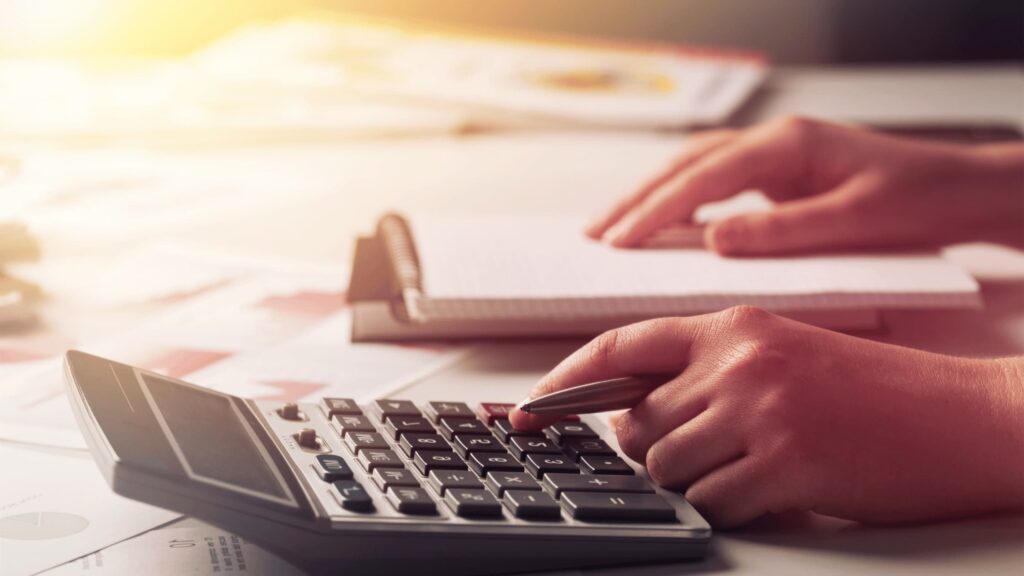
Assessing the Cost of Investment Casting
Although initially perceived as expensive, various aspects of the process contribute to its overall cost-effectiveness.
Initial Tooling Investment:
- It requires significant upfront investment in tooling, including the creation of wax patterns and ceramic molds. This precision work necessitates expertise, which adds to the initial costs.
- Despite these higher initial expenses, the durability of the molds allows them to be reused for multiple production runs, which lead to cost savings per unit over time.
Material Costs:
- The process uses a wide variety of metal alloys, such as stainless steel, aluminum, and titanium. Some of these materials are more expensive than others.
- Investment casting is efficient with materials, often using lightweight alternatives that help lower overall production costs by reducing material usage.
Efficiency and Waste Reduction:
- The method is notable for its efficiency and minimal waste production. Unlike other manufacturing techniques, investment casting produces complex parts without requiring extensive machining or secondary operations, which further cuts down on material and labor costs.
Detailed and Precise Outputs:
- The wax patterns used in investment casting allow for intricate designs and fine details, which are exact replicas in the final metal parts. The ceramic molds maintain the geometry of the wax patterns, ensuring the cast parts retain their complex features.
- This precision is challenging to achieve with other manufacturing processes, making investment casting particularly valuable for applications requiring high detail.
How Does Investment Casting Stand Out from Other Casting Methods?
Investment casting is unique compared to other types of casting like die casting and sand casting. The key difference is how the mold is made. In investment casting, a wax pattern of the final part is created first. This wax model is then covered with a ceramic material that hardens into a solid mold. Die casting, on the other hand, involves forcing molten metal under high pressure into a metal mold material. Sand casting uses a mixture of sand and a binder packed around a pattern to shape the mold cavity.
The precision and detail in investment casting are higher than in die casting and sand casting because the wax model can capture intricate details. This method is especially good for making thin-walled parts without any holes or gaps, achieving high accuracy.
Investment casting combines the benefits of detailed accuracy and reasonable costs, making it ideal for complex shapes and parts that need tight tolerances. It also allows for using various metal alloys, giving manufacturers flexibility in choosing materials.
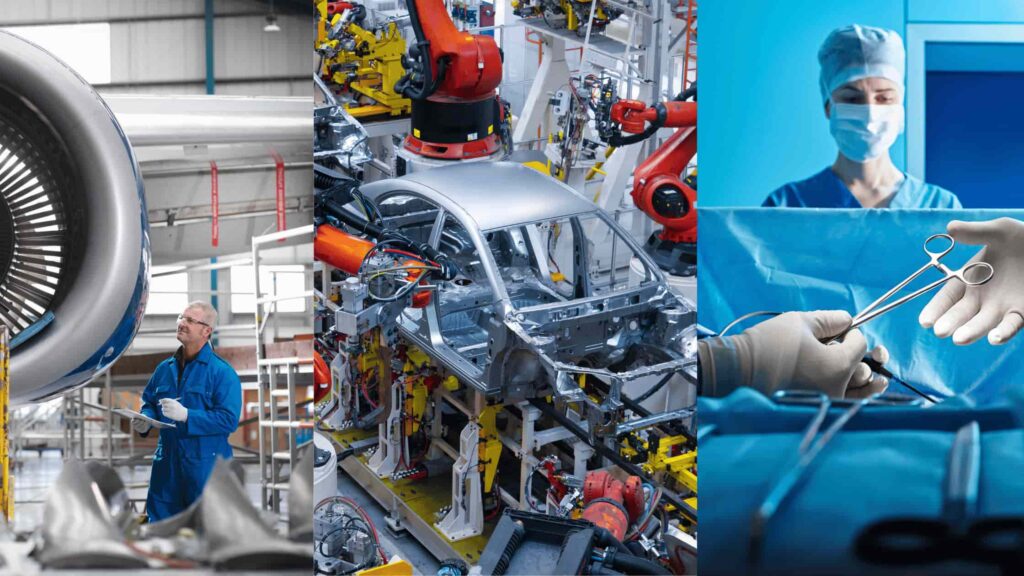
Which Industries Rely on Investment Casting?
Investment casting is popular across various sectors, including aerospace, automotive, and medical industries. In aerospace, it is used to make complex parts like turbine blades and engine components, offering excellent precision and minimal waste. Automotive manufacturers use investment casting for parts like cylinder heads and transmission components, benefiting from its ability to create lightweight and high-performance designs. The medical field also uses this technique for producing detailed implants and surgical tools, ensuring high precision and reliability essential for medical devices.
Exploring the Durability of Investment Casting Products
Precision casting products are renowned for their exceptional durability. This durability can be attributed to several factors including design, operational conditions, and material selection.
- Design Considerations: The durability of the products largely depends on their design. A well-thought-out design incorporates elements such as stress distribution, load-bearing capacity, and structural integrity. For instance, brass bearing surfaces in machinery are specifically designed to handle high loads and provide frictionless operation, which contributes to their longevity.
- Operational Limitations: The operating conditions that a product will face play a crucial role in determining its durability. Products are designed with these conditions in mind, ensuring they can withstand specific forces, vibrations, and environmental exposures. A prime example is automotive suspension knuckle joints, which are engineered to endure constant vibrations and harsh environmental conditions, thus enhancing their durability.
- Material Selection: Selecting appropriate materials is critical for the durability of investment casting products. The chosen materials must possess the necessary mechanical properties and corrosion resistance to ensure the product’s longevity. Stainless steel, for example, is often used in the process for its excellent strength, toughness, and resistance to corrosion.
- Additional Factors Contributing to Durability: It also allows for the creation of complex geometries, which can optimize the functionality and therefore the durability of the products. The process ensures precise dimensional accuracy, which is essential for the correct fit and alignment of components, enhancing both performance and durability. Furthermore, investment casting minimizes material wastage and facilitates the use of high-quality materials, both of which are instrumental in improving the structural integrity of the final product.
- Heat Resistance: The durability is also influenced by their ability to resist heat. This is dependent on the materials used; certain materials such as superalloys are chosen specifically for their exceptional heat resistance properties. These materials ensure that the products can operate effectively in high-temperature environments without degrading.
In summary, investment casting is a versatile process used in industrial applications for creating parts with different metals. It has size and cross-sectional limits, making it suitable for small to medium-sized parts. Correct product choice and strict process and quality control procedures are vital for successful investment casting.
Shakeout, Cleaning, and Finishing: Revealing the Cast
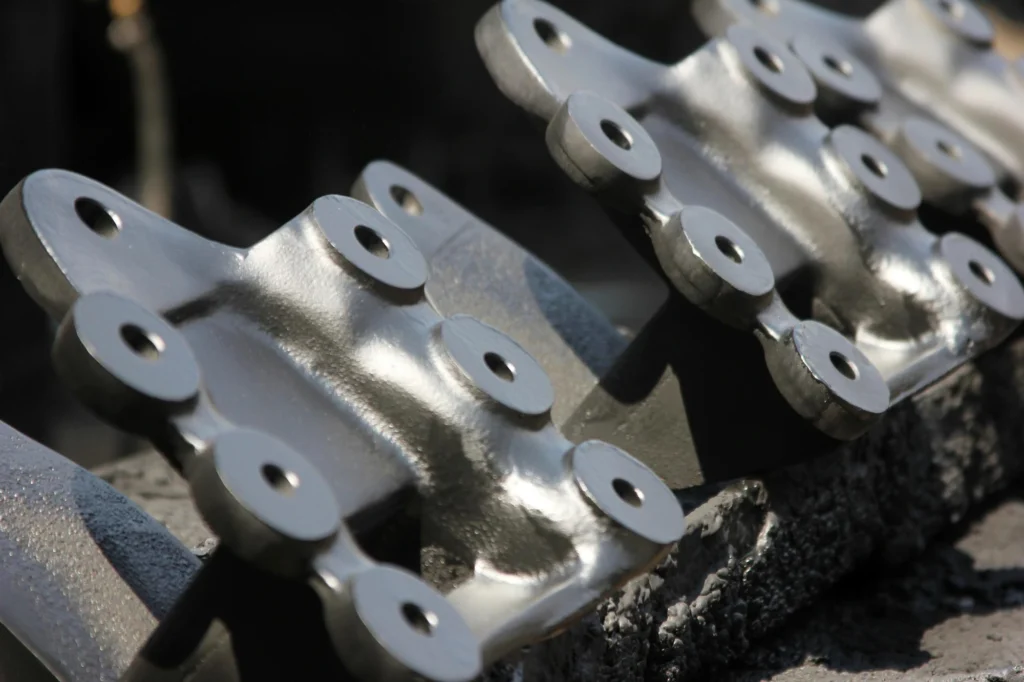
After the metal has cooled and solidified within the mold, the next phase is one of transformation, where the rough cast emerges from its sandy cocoon, ready to undergo the metamorphosis into a finished piece. This phase, comprising the shakeout, cleaning, and finishing processes, is crucial for revealing the cast’s true form and preparing it for its intended function. Let’s explore these steps that take the casting from a raw state to a polished final product.
The Shakeout Process: Separating the Cast Part from the Sand Mold
Shakeout marks the first crucial step in revealing a newly formed metal casting from its sand mold. This process involves carefully breaking apart the mold to uncover the casting, while ensuring the delicate new structure remains intact. The timing of shakeout is critical, as removing a casting too soon can expose it to rapid cooling, leading to undesirable effects such as embrittlement or microstructural changes. For example, in the case of ductile iron, premature exposure to air can alter its balance of pearlite, ferrite, or martensite structures, affecting the final material properties.
Foundries often rely on specific formulas or visual indicators to determine the optimal moment for shakeout. For instance, the greying of ductile iron is a common sign that it has cooled sufficiently to be safely removed.
Once the timing is right, the casting can be separated from the mold through various methods. In smaller foundries, this might involve manual tools such as tongs, where workers carefully lift the casting out of the mold as it crumbles away. In larger operations, automated systems like agitation or vibration tables are typically employed. These tables vigorously shake unflasked molds, causing the sand to detach from the casting and fall through perforated surfaces into collection bins. The reclaimed sand can then be treated and reused for future molds, contributing to sustainable foundry practices.
In some cases, sand molds include internal sand cores, which are used to create hollow sections within the casting. Removing these cores often requires additional methods, such as mechanical agitation, chemical treatment, or heat application, depending on the binder material used in the core construction. This ensures that all residual sand is dislodged and the casting is free from obstructions.
For cores made with chemical binders, additional measures may be necessary. For example, applying solutions of sodium or potassium hydroxide can dissolve certain binders effectively. Similarly, steam, cold water, or other thermal treatments can weaken the core material, facilitating its removal.
Once the core is sufficiently loosened, any remaining sand is typically cleared using a final mechanical step, such as an agitation table or pneumatic hammers. This ensures the casting is thoroughly free of residual material, preserving both the structural integrity and the precision of the design
By the end of the shakeout process, the casting is freed from its sandy cocoon, ready to move on to the next phase of cleaning and finishing. Each step requires a balance of efficiency and care to protect the structural integrity of the freshly unveiled piece.
Cleaning Operations: Fettling, Trimming, and Surface Enhancements
After the casting is removed from its mold, it must undergo a series of cleaning steps to remove residual sand, excess metal, and any imperfections caused during the casting process. This phase is traditionally referred to as fettling and is critical to preparing the casting for subsequent stages such as machining or final finishing.
Key Cleaning Steps in Fettling
- Trimming:
Excess metal, including gates, risers, and flash, is removed during trimming. These protrusions form where molten metal flows through the mold’s channels or leaks at the mold’s seams. Trimming typically involves mechanical cutting tools, such as saws or grinders, to ensure clean edges and a smooth surface. - Shot Blasting and Sandblasting:
To eliminate stubborn sand particles and refine the casting’s surface, abrasive blasting is employed.- Shot Blasting: Small steel balls or iron grit are propelled at high speed to remove scale, flash, and surface impurities. This process not only cleans but also slightly smoothens the surface.
- Sandblasting: Sand or other fine abrasives are directed at the surface under high pressure to dislodge debris and improve texture.
- Surface Treatments:
Additional treatments enhance the casting’s durability and appearance. These may include:- Acid Etching: Applied to clean the surface chemically and prepare it for further finishing.
- Shot Peening: Strengthens the metal by imparting compressive stress, enhancing fatigue resistance.
- Removing Flashing and Burrs:
Thin layers of excess metal, known as flashing, often form along the parting lines of the mold. Burrs, which are small, sharp protrusions, can also appear. These imperfections are carefully ground or filed away to ensure the casting is safe and functional. - Use of Tumblers and Automated Systems:
Castings may be placed in rotating tumblers or conveyors to be cleaned more thoroughly. In these systems, the components are agitated while abrasives like steel shot or air-blasting systems target hard-to-reach areas. - Final Fettling and Inspection:
After primary cleaning, fettling continues with detailed inspection and touch-ups. Pneumatic hammers or grinders may be used for intricate areas. At this stage, the casting is checked for surface flaws and dimensional accuracy.
Importance of Fettling in High-Quality Castings
Fettling transforms the rough, freshly cast metal into a refined and functional component. By removing imperfections and ensuring clean, smooth surfaces, this process plays a crucial role in meeting industry standards and preparing castings for specialized applications, whether in automotive, aerospace, or industrial machinery.
Incorporating Water Blasting in Cleaning Operations
In addition to traditional methods like shot blasting and tumbling, water blasting is another effective cleaning technique for castings. This method utilizes high-pressure water jets to clean the casting’s surface, often referred to as hydroblasting.
How Water Blasting Works
- Pressure Washing:
At its core, water blasting involves directing powerful streams of water at the casting. This pressure effectively removes residual sand, scale, and other surface impurities. - Abrasive-Enhanced Hydroblasting:
In advanced systems, abrasive materials like fine grit or beads are added to the water stream. This combination enhances the cleaning action, making it suitable for removing tougher contaminants and providing a finer surface finish. - Advantages:
- Eco-Friendly: Water blasting reduces the reliance on chemical cleaning agents and abrasives, making it an environmentally friendly option.
- Gentle on Castings: Unlike some abrasive methods, hydroblasting minimizes the risk of damaging delicate features or intricate details on the casting.
- Versatility: Suitable for a wide range of metals and casting types, from aluminum to steel.
- Applications:
Water blasting is often used in industries requiring high-quality finishes, such as aerospace or medical equipment manufacturing, where cleanliness and surface integrity are critical.
Role in the Cleaning Process
Water blasting can either be a primary cleaning step for delicate castings or a supplementary process after traditional methods like shot blasting. Following hydroblasting, castings may undergo inspection or additional surface treatments to achieve the desired finish.
By integrating modern water-blasting techniques, foundries can enhance efficiency, improve the casting’s surface quality, and reduce environmental impact.
Removing Gates and Risers
Gates and risers, essential features for directing molten metal through the mold, often leave behind excess material that must be removed during the cleaning process. Unlike smaller imperfections, these larger sections are too substantial to be dislodged through tumbling or air blasting.
Methods for Removal
- Oxy-Acetylene Torches:
High-temperature torches effectively cut through thick sections of excess metal, providing a precise and efficient removal method. - Chipping and Hammering:
Foundry workers may use tools like chipping hammers or sledges to physically break off gates and risers. This method is often employed for larger or more rugged castings. - Sawing:
Saws equipped with durable blades can trim excess stock, especially when precision is required. This is common for castings that demand detailed finishing. - Machining Integration:
In some cases, gates and risers are left for removal during the machining stage. This allows the removal process to be integrated with fine-tuning the part’s dimensions and surface quality, reducing redundancy in operations.
Recycling Removed Material
The metal trimmed from gates and risers is highly valuable. Unlike raw scrap, this material has already undergone purification during the casting process, as gases and impurities, such as paint or oil, are burned off in the furnace. This ensures the recycled metal is of superior quality, helping foundries maintain consistent material standards while minimizing waste.
Machining for Precision
Sand casting often produces surfaces that are rough and lack tight dimensional tolerances. To meet specific standards, additional machining is required.
Purpose of Machining
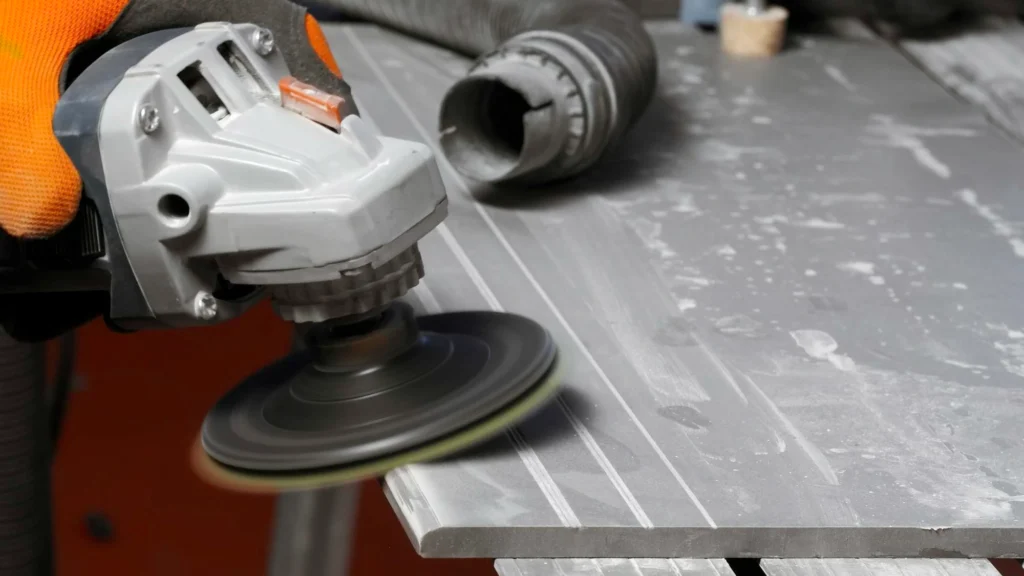
- Surface Finishing:
Machining creates a smoother surface, essential for parts that require aesthetic appeal or functional precision. - Dimensional Accuracy:
Tight tolerances are achieved through techniques like grinding, lathing, or milling. These methods ensure the part fits seamlessly with other components in assemblies. - Cost-Effective Design:
Since machining is costly, foundries aim to cast parts as close to the final shape as possible, minimizing the amount of material that requires machining. This reduces both time and expense while maintaining high-quality results.
By carefully removing gates and risers and employing machining only where necessary, foundries strike a balance between efficiency, cost, and precision, ensuring the castings meet exact specifications.
Finishing Touches: Machining, Painting, or Coating for Aesthetic and Functional Purposes
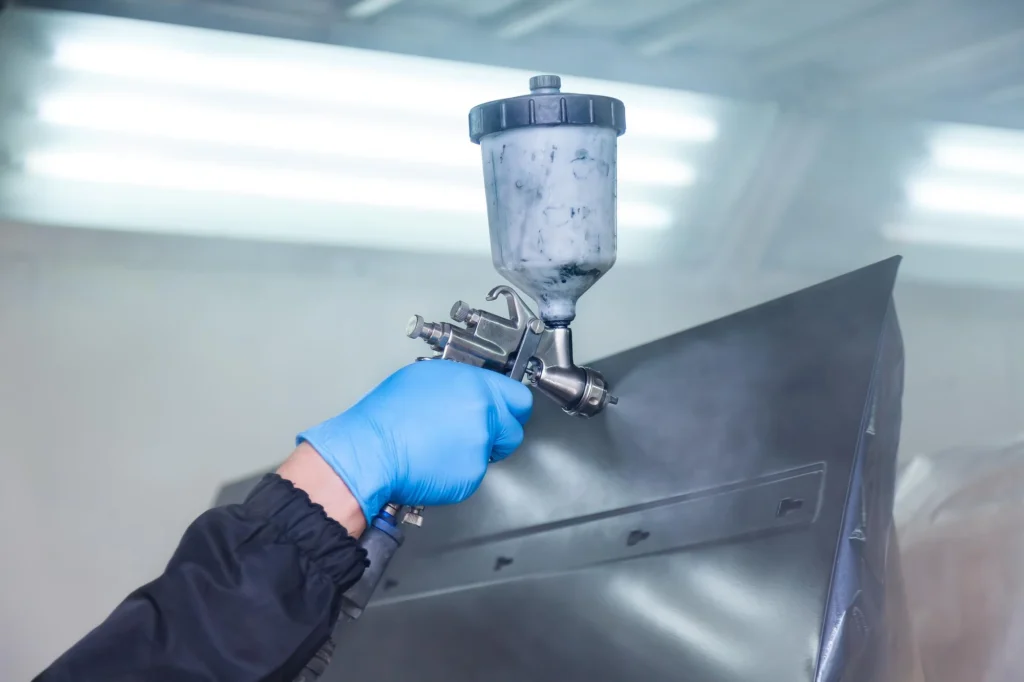
The final step in the casting process is finishing, where the cast part is refined to meet the precise specifications required for its intended use. This can involve a variety of processes, tailored to the demands of the final product:
- Machining: Precision machining is often necessary to achieve the exact dimensions and tolerances needed for the casting to function as designed. Processes like milling, drilling, and turning are used to refine the shape and size of the part.
- Painting or Coating: For aesthetic enhancement or to provide a protective layer against corrosion, castings may be painted or coated with various materials. This can range from simple paint applications to complex chemical coatings designed to withstand extreme environments.
- Quality Inspection: Finally, the casting undergoes a thorough inspection to ensure it meets all quality standards and specifications. This may include visual inspection, dimensional measurement, and non-destructive testing methods.
Real Life Examples
High-quality castings play a pivotal role in industries like automotive, where engine blocks and transmission housings must meet precise specifications. Similarly, in aerospace, turbine blades and structural components require exceptional durability and precision. For example, the aerospace industry often uses investment casting to produce lightweight yet robust components for jet engines.
Finishing technology is undergoing a revolution, with robotics and artificial intelligence transforming processes like machining and cleaning. For example, automated robotic grinders ensure precision in trimming and reduce manual labor. AI-powered systems are used for quality inspection, identifying defects with unmatched accuracy.
Sustainability in Foundries
Foundries today are adopting eco-friendly practices to reduce waste and improve efficiency. Sand reclamation systems, for instance, allow foundries to recycle up to 90% of their sand, reducing the environmental footprint. Additionally, advancements in closed-loop water systems minimize water waste, making foundries more sustainable.
Some foundries are also exploring green technologies like bio-based binders instead of synthetic chemicals for sand cores, lowering emissions and reducing reliance on fossil fuels.
Through the meticulous processes of shakeout, cleaning, and finishing, the casting is transformed from a rough, sand-encrusted object into a precise, polished component, ready to take its place in the world. This journey from mold to masterpiece underscores the blend of brute force and delicate precision that defines sand casting.
During the first production run, castings at this stage often serve as prototypes for clients or designers to assess for aesthetics and functionality. These prototypes provide crucial insight into the product’s viability and whether any design flaws need to be addressed.Align Manufacturing plays a key role ensuring that the final components meet the exact specifications and client expectations, making any necessary adjustments to improve the product before moving forward with full production.
Cooling and Solidification: A Delicate Transition
After the exhilarating moment of pouring molten metal into the mold, the sand casting process enters a phase of quiet transformation: cooling and solidification. This stage is pivotal, as the characteristics of the final casting are largely determined by the events that occur as the metal transitions from liquid to solid. Understanding the science of cooling curves and solidification patterns, alongside managing the factors that influence cooling rates, is essential in producing high-quality castings.
Explanation of Cooling Curves and Solidification Patterns
Cooling curves are graphical representations that show how the temperature of the metal changes over time as it cools and solidifies in the mold. Each metal or alloy has a unique cooling curve, influenced by its chemical composition, which dictates the rate at which it must be cooled to achieve desired properties. Solidification patterns, on the other hand, describe the manner in which the metal transforms from liquid to solid. These patterns can reveal insights into the potential for defects, the formation of different microstructures, and the overall quality of the cast.
Factors Affecting Cooling Rates and Their Impact on Casting Quality
Several factors influence how quickly and uniformly a casting cools, each affecting the casting's final characteristics:
- Mold Material: The thermal conductivity of the mold material plays a significant role. Sand molds, with relatively low thermal conductivity, cool the metal slower than metal molds, affecting the microstructure and mechanical properties of the casting.
- Casting Thickness: Thicker sections of a casting cool more slowly than thinner sections, leading to variations in microstructure and potential for defects such as shrinkage cavities.
- Temperature of the Molten Metal: The initial temperature of the molten metal when poured can influence the cooling rate; higher temperatures result in longer cooling times.
- Environmental Conditions: Ambient temperature and airflow around the mold can also affect cooling rates.
These factors can lead to a range of casting defects if not properly managed, including porosity, inclusions, and uneven mechanical properties.
Strategies to Control Cooling and Avoid Defects
To mitigate the risk of defects and ensure a high-quality casting, several strategies can be employed to control cooling rates:
- Chills: These are materials with high thermal conductivity that are placed in the mold to accelerate cooling in specific areas of the casting. Chills can be used to create more uniform cooling rates across the casting, preventing areas of localized shrinkage.
- Insulation: Conversely, insulating materials may be used to slow the cooling rate in certain sections of the casting to avoid thermal stresses and cracking. This is often necessary for castings with varying cross-sectional thicknesses.
- Controlled Pouring Temperature: Adjusting the temperature of the molten metal to the optimal pouring temperature for the specific alloy and casting size can help manage the cooling rate.
- Mold Design Adjustments: Modifying the design of the mold, including the thickness and placement of the sand, can help achieve more uniform cooling.
Cooling and solidification are not merely passive stages in the sand casting process; they are phases ripe with potential for influencing the final outcome. Through a deep understanding of the underlying principles and a strategic approach to managing cooling rates, foundry workers and artisans can significantly enhance the quality and integrity of their castings. This delicate transition, when navigated with skill and knowledge, marks the birth of a new metal form, ready to be revealed to the world.
FAQ:Everything You Need to Know
The cooling process directly impacts a casting's strength, structure, and durability. Faster cooling creates a finer grain structure, enhancing the metal's mechanical properties. Foundries adjust cooling rates by adding chills, using conductive sand types, or modifying mold designs to manage heat dissipation effectively.
A high-performing foundry goes beyond metal pouring by ensuring cleanliness throughout the process. It uses degassing techniques to remove hydrogen from aluminum melts, reducing porosity and improving strength. Applying flux treatment further purifies the molten metal, ensuring defect-free castings with reliable performance.
Foundries manipulate solidification by selecting appropriate mold materials and positioning cooling aids like chills. For example, zircon sand accelerates cooling due to its superior thermal conductivity. Feeder placement and mold design adjustments ensure an even cooling process, reducing internal stresses and shrinkage defects.
Maintaining the correct metal temperature prevents quality issues. Overheating may cause essential alloying elements to vaporize, weakening the final product. If the metal is too cool, incomplete fills or cold shuts can occur, leaving gaps in the casting. Temperature consistency ensures predictable and defect-free results.
Effective casting design minimizes common defects like gas bubbles, shrinkage cavities, and inclusions. A well-designed mold includes low-turbulence runner systems and rounded internal features to ensure smooth metal flow. These adjustments help produce structurally sound castings with fewer production failures.
Turbulence in the pouring process can lead to gas entrapment, inclusions, and reduced casting strength. To counteract this, foundries use controlled pouring methods with low-turbulence systems that reduce air pockets and ensure a smooth metal flow. This approach improves density and eliminates hidden flaws often detectable only through advanced inspections.