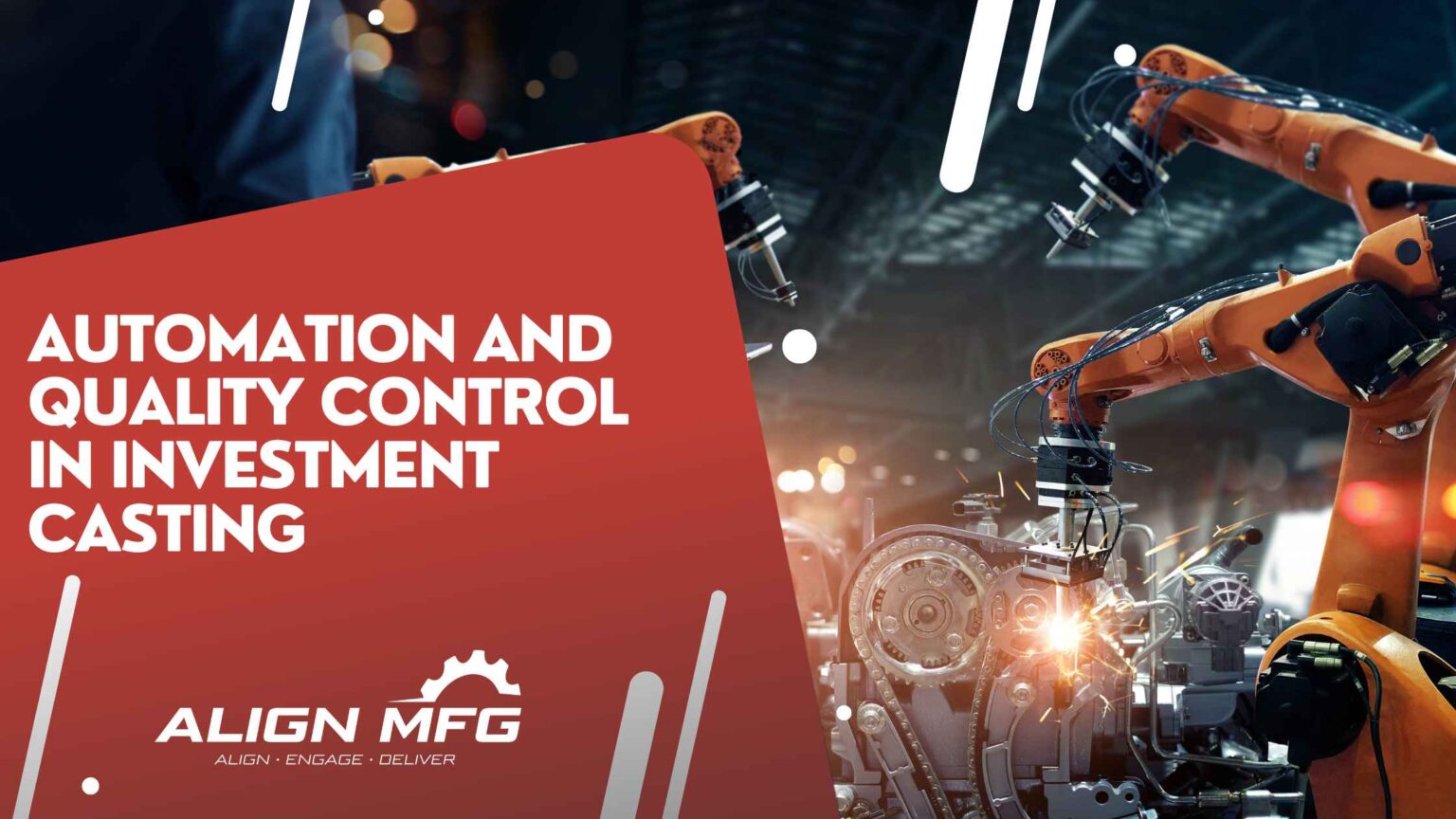
Automation and Quality Control in Investment Casting
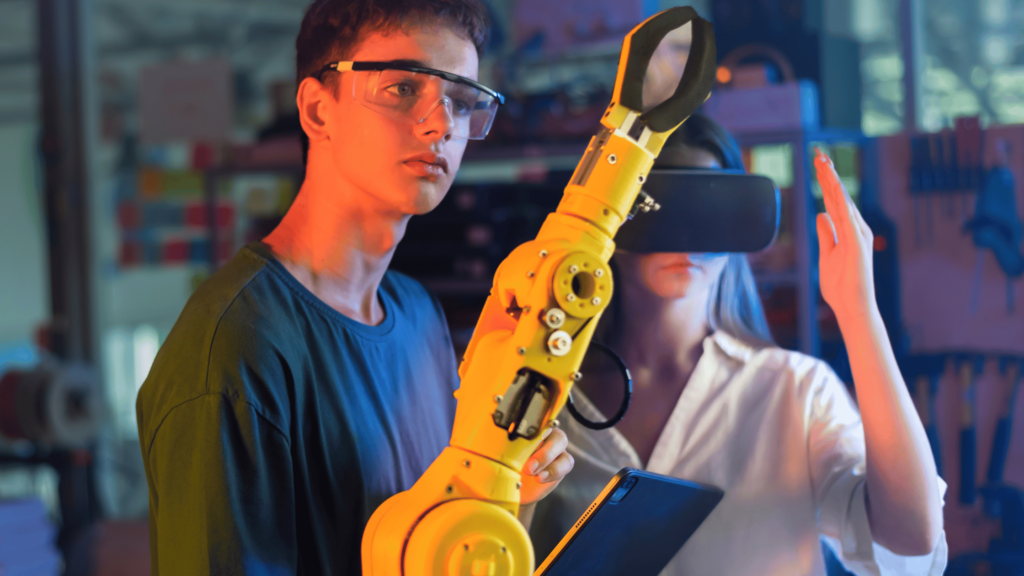
Investment casting, also known as lost-wax or precision casting, is one of the oldest doctrines to intricately craft components. Though the origin of the process can fold many centuries back, it does not necessarily mean that it is antiquated thereby. The improvements and changes made have been brought on by automation and advanced quality control. These have improved the areas of efficiency, precision, and part reliability, all of which contribute to the competitiveness of investment casting in this high-paced manufacturing environment. This blog goes through the aspects of automation: its role in the enhancement of the process and the critical quality control measures that ensure part reliability.
The process of Investment Casting
Investment casting is a manufacturing process for generating complicated and high-precision components. Such a process starts with the creation of a wax pattern, which is an exact replica of the desired part. The pattern is then coated with a ceramic shell to fashion a mold. After this ceramic shell hardens, wax is melted out of it, leaving a cavity that is then filled with molten metal. Later on, after it solidifies, it is to be broken away to reveal the final casting. The process is marked by its ability to generate parts with high surface finish and tight tolerances, which qualifies it to be applied in critical industries such as oil, railway, construction, and industrial sectors.
The Role of Automation
Automation has revolutionized many aspects of the lost-wax casting process. Manufacturers no longer have to rely on the human hand for repetitive and precise tasks. Instead, automated systems have been incorporated, which allow them to achieve higher levels of precision while reducing lead times and improving overall efficiency. Outlined below are some of the ways in which automation is bringing much improvement to precision casting.
Automated Pattern Creation
Historically, the making of wax patterns has been a very labor-intensive process. However, this process has been improved with automation to a great extent. Automated pattern making machines can produce wax patterns with remarkable tolerance and repeatability based on computer-aided design data.
- Faster Delivery and Shorter Production Time: Automation processes the pattern making at a quicker rate, thus reducing the lead time for production.
- Makes Patterns of Complex Geometries: Machines are capable of producing complex geometries for the patterns of designs that would not either be possible or practical to reproduce using manual techniques.
Robotic Shell Building
Another area of the process that has been revolutionized with automation is the shell building process in making the ceramic shell around the wax patterns. The robotic system carries out the wax pattern’s dipping, draining, and stuccoing (coating with ceramic).
- Higher Precision: Automation ensures precise control over the amount and parameters of pouring. Since molten metal is poured into ceramic shells, automation can maintain the right temperature of molten metal thus preventing defects due to poor pour temperature.
- Even Pouring: Delivering molten metal through robots at a steady pace prevents defects like entrapment of air or incomplete fills.
- Safety: Since automation prevents accidents due to molten metal handling, the workers’ safety is ensured.
Quality Control Measures in Investment Casting
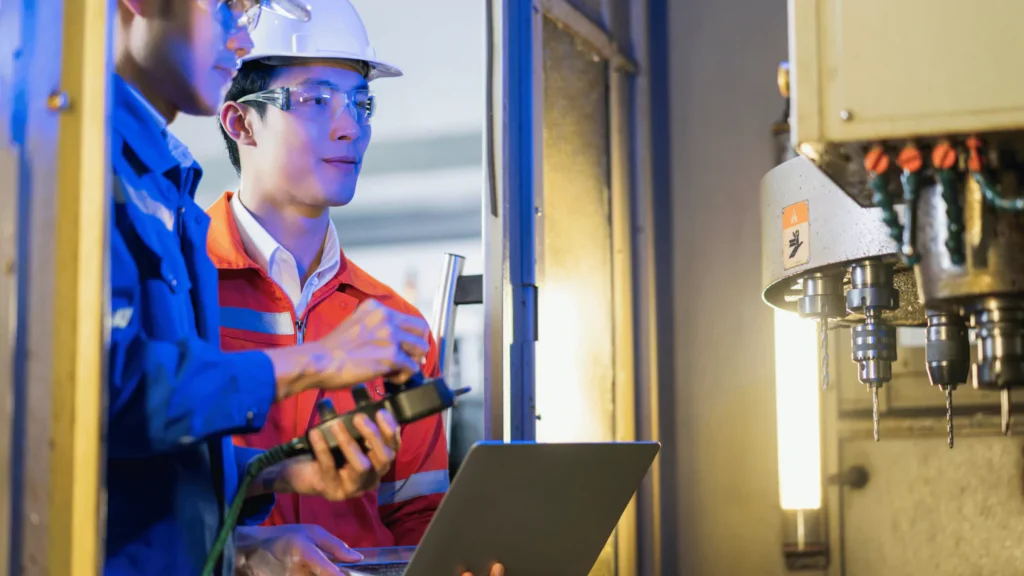
Quality control involves various critical steps, from inspection of patterns in the initial stages to the final evaluation of the products. In a nutshell, the following is major quality control measures in lost-wax casting:
Pattern Inspection
The quality of the final cast part depends on the tolerance of the wax pattern. Inspection of the wax pattern is hence an important step.
- Dimensional Criteria: The patterns are gauged for dimensional features, and modern gauging appliances like CMM are used for inspection.
- Surface Condition: Scrutinizing the surface of the wax pattern for imperfections prevents flaws from appearing in the final casting.
Shell Integrity Testing
This is critical in the case of the ceramic shell used in the casting process. Any defect in the shell may result in defects in the final part.
- Visual Inspection: The shell is visually inspected for cracks, incomplete covering, or some other defects.
- Non-Destructive Testing (NDT): Ultrasonic testing and radiographic inspection help to detect internal defects in the ceramic shell.
Metal Quality Control
The quality of the molten metal is another important factor in casting. Quality metal is free of impurities and has the right composition to produce quality cast parts.
- Spectroscopy: This will be applied in analyzing the chemical composition of the metal to assure that it meets the required specifications.
- Inclusion Analysis: The analysis is carried out using such techniques as optical and scanning electron microscopy to detect non-metallic inclusions present in the metal.
Post-Casting Inspection
After the metal has been poured and the ceramic shell has been removed, these post-cast inspections help ensure the quality of the end product.
- Dimensional Testing: Checking the dimensions of the cast part to verify with the specifications undertaken.
- Surface Testing: Testing the cast part for cracks, porosity, or surface roughness.
- Mechanical tests: Test and confirm that mechanical properties, including, for example, tensile strength and hardness, are as per or meet the specified in the required specification.
Advanced Automation Techniques
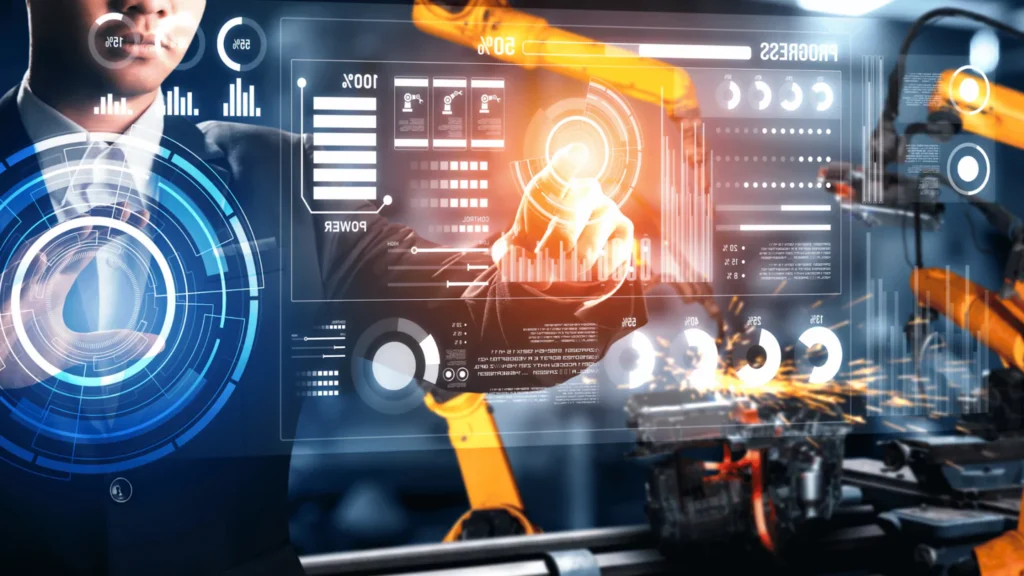
The adoption of advanced automation further elevates the process. Artificial intelligence, machine learning, and the Internet of Things are some commonly used concepts.
Artificial Intelligence and Machine Learning
In the context of casting, artificial intelligence and machine learning can be harnessed to study the huge data that comes out from the casting process to note the patterns and sometimes even predict results. The manufacturers employ it for improvement in process and quality control.
- Predictive Maintenance: Predicts when equipment is likely to fail, allowing maintenance to be planned in advance, thereby reducing unplanned downtime.
- Process optimization: ML algorithms can analyze process parameters and suggest adjustments which enhance yield and reduce defects.
- Defect Prediction: AI can predict the likelihood of defects in cast parts and allow early intervention and corrective measures.
Internet of Things (IoT)
IoT is about implementing a setup to help collect data regarding various parameters around the casting process. IoT sensors monitor the temperature, pressure, and other critical parameters of the casting process in real-time. Data collected by IoT can further be analyzed for trends, detecting anomalies, and optimizing processes. This process can be adjusted and controlled remotely, allowing for interventions from a distant location.
Automation and Innovation in Critical Industries
Automation and quality control in investment casting have brought transformative changes, particularly in critical industries. These industries demand high precision, reliability, and innovation, and it has risen to the challenge.
Digital Twin Technology
Digital twin technology means a fully detailed virtual copy of the foundry process. The model is digital, allowing for process simulation and optimization in real-time.
- Process Simulation: The digital twins can simulate various situations, through which the manufacturers can optimize process parameters.
- Predictive Analytics: Data from the digital twin is subjected to analytics to allow manufacturers to make predictions concerning possible failures and, in that way, take preventive actions.
- Continuous Improvement: The foundry process can be continually monitored and improved through digital twin technology, thereby increasing process efficiency and quality.
Sustainable Manufacturing Practices
The current trend in the manufacturing industry is a move toward more sustainability. Automation and quality control make possible more sustainable lost -wax casting. An automated process ensures optimization in the consumption of energy and, in return, minimizes the environmental impact brought about by the casting process. Quality control measures will also help reduce defects and scrap, thus reducing waste materials and conserving resources. Material science has not been left behind in this quest, and more eco-friendly casting materials have been developed.
Conclusion
Automation together with quality control has created the most significant changes in the industry of investment casting. With the help of advanced technologies, the manufacturer can achieve the highest levels of precision, efficiency, and part reliability. Automation of casting steps, starting from pattern creation up to pouring, and quality control of the results of every step, streamlines the process, ensuring that every part meets strict standards. Financial investment casting will only shine more with the constant development of technologies such as AI, IoT, and digital twins. The innovations will put manufacturers well in the race in a market that is rapidly changing and in regard to top-quality components meeting high requirements, especially in the aerospace, automotive, and medical industries. It is expected that the merging of automation and quality control will bring further improvements in functionality and sustainability.