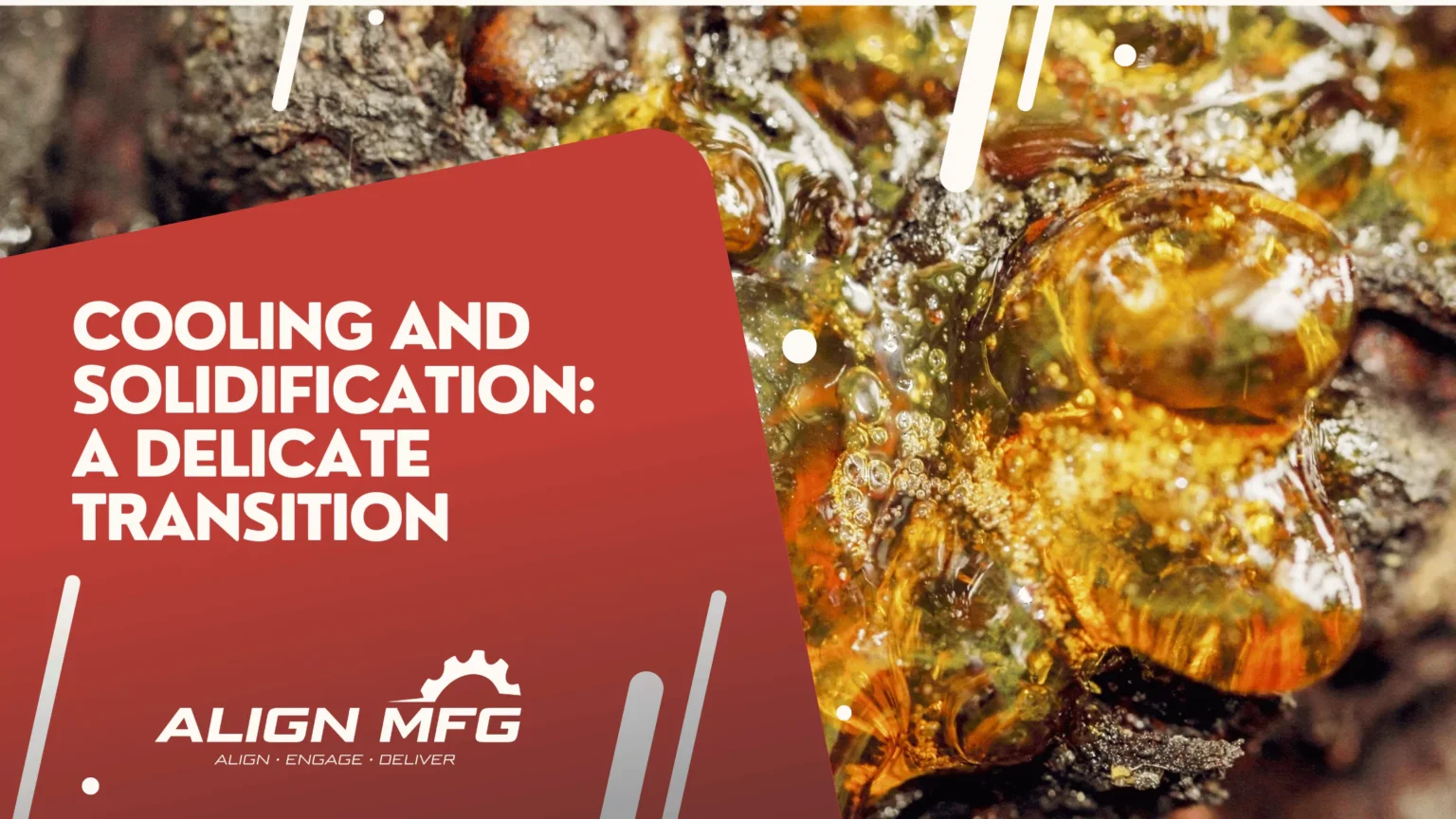
Cooling and Solidification: A Delicate Transition
After the exhilarating moment of pouring molten metal into the mold, the sand casting process enters a phase of quiet transformation: cooling and solidification. This stage is pivotal, as the characteristics of the final casting are largely determined by the events that occur as the metal transitions from liquid to solid. Understanding the science of cooling curves and solidification patterns, alongside managing the factors that influence cooling rates, is essential in producing high-quality castings.
Explanation of Cooling Curves and Solidification Patterns
Cooling curves are graphical representations that show how the temperature of the metal changes over time as it cools and solidifies in the mold. Each metal or alloy has a unique cooling curve, influenced by its chemical composition, which dictates the rate at which it must be cooled to achieve desired properties. Solidification patterns, on the other hand, describe the manner in which the metal transforms from liquid to solid. These patterns can reveal insights into the potential for defects, the formation of different microstructures, and the overall quality of the cast.
Factors Affecting Cooling Rates and Their Impact on Casting Quality
Several factors influence how quickly and uniformly a casting cools, each affecting the casting's final characteristics:
- Mold Material: The thermal conductivity of the mold material plays a significant role. Sand molds, with relatively low thermal conductivity, cool the metal slower than metal molds, affecting the microstructure and mechanical properties of the casting.
- Casting Thickness: Thicker sections of a casting cool more slowly than thinner sections, leading to variations in microstructure and potential for defects such as shrinkage cavities.
- Temperature of the Molten Metal: The initial temperature of the molten metal when poured can influence the cooling rate; higher temperatures result in longer cooling times.
- Environmental Conditions: Ambient temperature and airflow around the mold can also affect cooling rates.
These factors can lead to a range of casting defects if not properly managed, including porosity, inclusions, and uneven mechanical properties.
Strategies to Control Cooling and Avoid Defects
To mitigate the risk of defects and ensure a high-quality casting, several strategies can be employed to control cooling rates:
- Chills: These are materials with high thermal conductivity that are placed in the mold to accelerate cooling in specific areas of the casting. Chills can be used to create more uniform cooling rates across the casting, preventing areas of localized shrinkage.
- Insulation: Conversely, insulating materials may be used to slow the cooling rate in certain sections of the casting to avoid thermal stresses and cracking. This is often necessary for castings with varying cross-sectional thicknesses.
- Controlled Pouring Temperature: Adjusting the temperature of the molten metal to the optimal pouring temperature for the specific alloy and casting size can help manage the cooling rate.
- Mold Design Adjustments: Modifying the design of the mold, including the thickness and placement of the sand, can help achieve more uniform cooling.
Cooling and solidification are not merely passive stages in the sand casting process; they are phases ripe with potential for influencing the final outcome. Through a deep understanding of the underlying principles and a strategic approach to managing cooling rates, foundry workers and artisans can significantly enhance the quality and integrity of their castings. This delicate transition, when navigated with skill and knowledge, marks the birth of a new metal form, ready to be revealed to the world.
FAQ:Everything You Need to Know
The cooling process directly impacts a casting's strength, structure, and durability. Faster cooling creates a finer grain structure, enhancing the metal's mechanical properties. Foundries adjust cooling rates by adding chills, using conductive sand types, or modifying mold designs to manage heat dissipation effectively.
A high-performing foundry goes beyond metal pouring by ensuring cleanliness throughout the process. It uses degassing techniques to remove hydrogen from aluminum melts, reducing porosity and improving strength. Applying flux treatment further purifies the molten metal, ensuring defect-free castings with reliable performance.
Foundries manipulate solidification by selecting appropriate mold materials and positioning cooling aids like chills. For example, zircon sand accelerates cooling due to its superior thermal conductivity. Feeder placement and mold design adjustments ensure an even cooling process, reducing internal stresses and shrinkage defects.
Maintaining the correct metal temperature prevents quality issues. Overheating may cause essential alloying elements to vaporize, weakening the final product. If the metal is too cool, incomplete fills or cold shuts can occur, leaving gaps in the casting. Temperature consistency ensures predictable and defect-free results.
Effective casting design minimizes common defects like gas bubbles, shrinkage cavities, and inclusions. A well-designed mold includes low-turbulence runner systems and rounded internal features to ensure smooth metal flow. These adjustments help produce structurally sound castings with fewer production failures.
Turbulence in the pouring process can lead to gas entrapment, inclusions, and reduced casting strength. To counteract this, foundries use controlled pouring methods with low-turbulence systems that reduce air pockets and ensure a smooth metal flow. This approach improves density and eliminates hidden flaws often detectable only through advanced inspections.