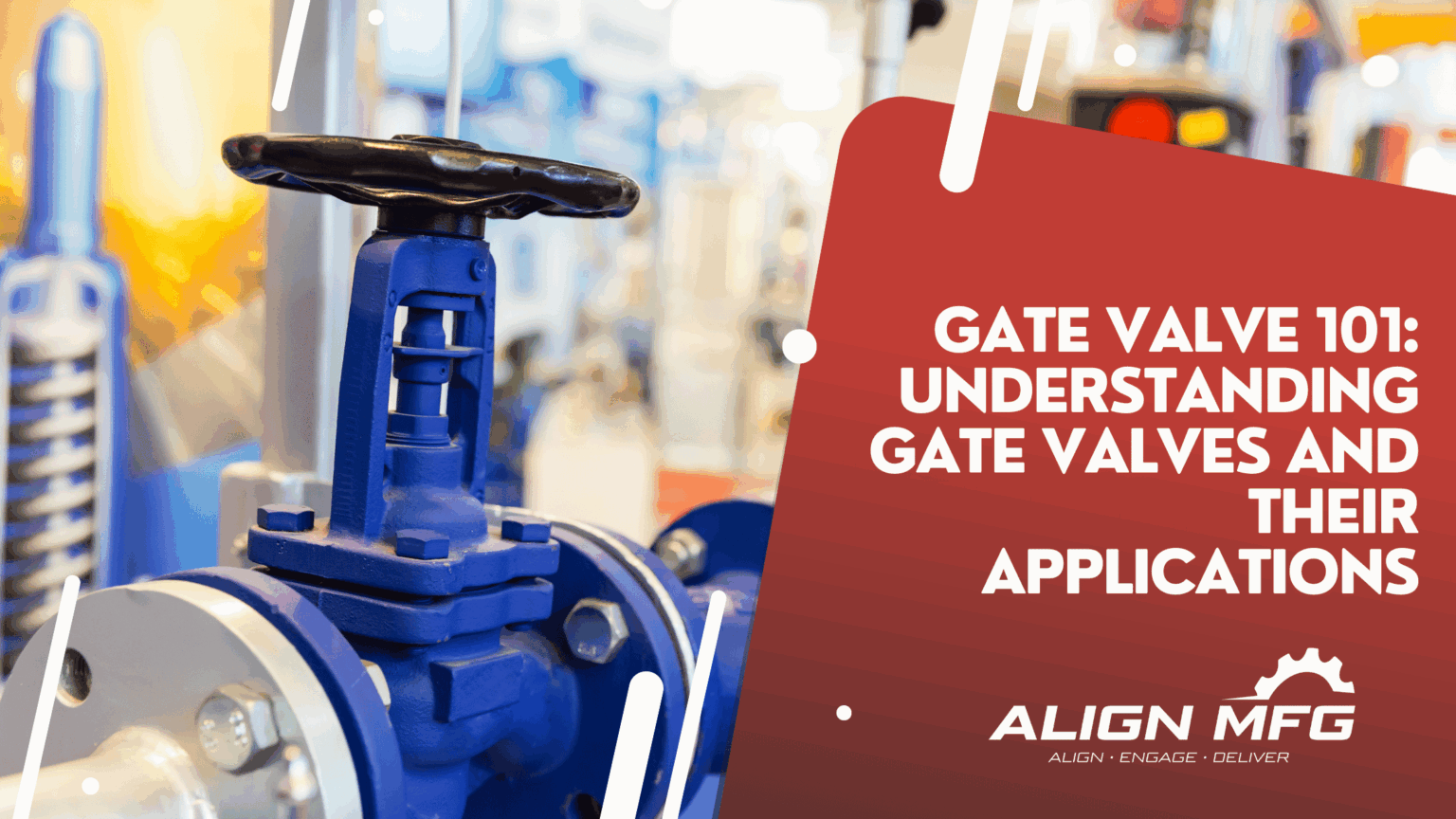
Gate Valve 101: Understanding Gate Valves and Their Applications
Gate valves are essential components in fluid control systems, designed primarily to start or stop the flow of liquids through pipelines. These valves operate by lifting a gate out of the fluid’s path, providing a straight-through passage when fully open, which results in minimal pressure drop. This characteristic makes gate valves ideal for applications requiring a free flow of fluid. Commonly used in industries such as oil and gas, water treatment, and manufacturing, gate valves are favored for their durability and ability to provide tight sealing. Their bi-directional flow design allows them to be used in systems where they remain either fully open or fully closed, rather than for flow regulation.
Gate Valve Components: Anatomy of a Gate Valve
Understanding the main components of a gate valve helps in proper selection, maintenance, and troubleshooting.
- Body: The main pressure-retaining structure that houses the internal parts and connects to the piping system.
- Bonnet: Attached to the body, it encloses the valve’s stem and forms a seal. Common types include bolted, union, and pressure seal bonnets.
- Gate or Disc: The actual flow-blocking component that moves vertically to open or close the valve. Can be solid, flexible, or split.
- Stem: Connects the actuator or handwheel to the gate, transmitting motion to open or close the valve.
- Seat Rings: Provide the sealing interface between the gate and the body. Can be integral or replaceable.
- Packing and Gland: Prevent leakage around the stem and are adjustable to maintain a tight seal.
- Handwheel or Actuator: Allows manual or automated operation of the valve.
Each part plays a critical role in ensuring the functionality, efficiency, and longevity of the gate valve.
Material Compatibility: Selecting the Right Gate Valve Material
Choosing the appropriate material for a gate valve is crucial, as it determines the valve’s suitability for specific fluids, temperatures, and pressures. Different materials offer varying levels of corrosion resistance, strength, and temperature tolerance. Here’s an overview of common gate valve materials and their applications:
Stainless Steel
Stainless steel gate valves are renowned for their excellent corrosion resistance and strength. They are suitable for a wide range of temperatures and are often used in chemical processing, food and beverage, and pharmaceutical industries. Their resistance to corrosion makes them ideal for applications involving corrosive fluids.
Carbon Steel
Carbon steel gate valves are robust and cost-effective, making them suitable for high-pressure applications. However, they are less resistant to corrosion compared to stainless steel. These valves are commonly used in the oil and gas, petrochemical, and power generation industries.
Cast Iron
Cast iron gate valves are economical and provide good resistance to wear. They are typically used in water distribution systems, HVAC, and fire protection systems. However, they are not suitable for high-pressure or high-temperature applications due to their brittleness.
Bronze and Brass
Bronze and brass gate valves offer good corrosion resistance and are often used in marine environments and potable water systems. They are suitable for low to moderate pressure applications and provide reliable performance in systems where dezincification resistance is important.
Steel Alloys
Gate valves made from steel alloys are designed for high-temperature and high-pressure applications. They are commonly used in power plants, refineries, and chemical processing facilities. Their enhanced mechanical properties make them suitable for severe service conditions.
Selecting the right material involves considering factors such as the nature of the fluid, operating temperature and pressure, and potential for corrosion. Proper material selection ensures the longevity and reliability of the gate valve in its intended application.
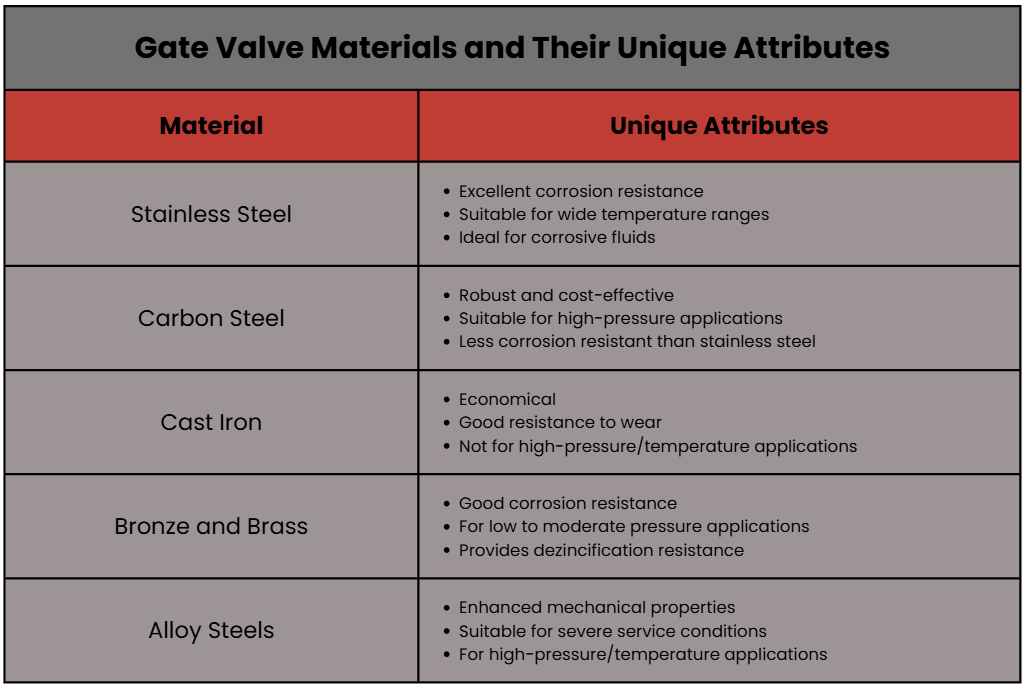
Valve Size & Pressure Ratings: Matching Valve to System Requirements
Choosing the appropriate valve size and pressure rating is crucial for ensuring optimal performance and safety within a piping system.
Valve Sizes
Gate valves are available in a wide range of sizes, commonly ranging from DN15 (1/2 inch) to DN600 (24 inches). The choice of size depends on the flow requirements of the system. For instance:
- Smaller sizes like DN15 or DN25 are suitable for residential plumbing.
- Larger sizes like DN300 or DN600 are used in industrial pipelines and municipal water systems.
Pressure Ratings
Pressure ratings indicate the maximum pressure a valve can handle at a specific temperature. The American National Standards Institute (ANSI) classifies pressure ratings into different classes, such as Class 150, Class 300, Class 600, etc. As the class number increases, the maximum pressure in pounds per square inch (psi) that can be handled at a reference temperature (usually 100°F) also increases. Smaller valve sizes are used in homes, while larger ones are used in industrial pipelines.
- Class 150: Typically handles pressures up to 285 psi at 100°F (38°C)
- Class 300: Handles pressures up to 740 psi at 100°F (38°C)..
It’s essential to select a valve with a pressure rating that exceeds the maximum operating pressure of the system to ensure safety and longevity.
Stem Design: Rising vs. Non-Rising Stems
The stem design of a gate valve affects its installation, maintenance, and operation. There are two primary stem designs: rising stem and non-rising stem.
Rising Stem
In rising stem gate valves, the stem moves up and down as the valve is operated. This movement provides a visual indication of the valve’s position. Do note that when the stem is visible, the valve is open, and when it is not, the valve is closed.
Advantages:
- Position Indication: Easy to determine the valve’s status.
- Ease of Maintenance: Exposed stem threads are accessible for lubrication.
Considerations:
- Space Requirements: Requires more vertical space for operation.
Non-Rising Stem
In non-rising stem gate valves, the stem remains stationary, and the gate moves along the stem’s threads. This design is compact, making it suitable for installations with limited space.
Advantages:
- Space Efficiency: Ideal for underground or confined installations.
- Protection: Stem threads are enclosed, reducing exposure to external elements.
Considerations:
- Position Indication: Does not provide a visual cue of the valve’s status; external indicators may be necessary
Understanding the differences between rising and non-rising stem designs helps in selecting the appropriate valve for specific applications, considering factors like space constraints, maintenance requirements, and operational preferences.
Bonnet Types: Sealing and Maintenance Considerations
The bonnet of a gate valve is a critical component that houses the stem and provides a leak-proof closure for the valve body. Different bonnet designs offer varied advantages in terms of sealing capabilities, maintenance ease, and suitability for specific applications.
Bolted Bonnet
Bolted bonnets are the most common design, where the bonnet is bolted to the valve body using studs and nuts, with a gasket in between to ensure a tight seal.
Advantages:
- Ease of Maintenance: The bolted design allows for straightforward disassembly, making inspection and maintenance more convenient.
- Versatility: Suitable for a wide range of pressures and temperatures, making it applicable in various industries.
Considerations:
- Potential for Leakage: The seal relies on the integrity of the gasket and the torque applied to the bolts. Over time, thermal cycling and pressure fluctuations can compromise the seal, leading to potential leaks.
Union Bonnet
Union bonnets are designed with a threaded union nut that holds the bonnet to the valve body, providing a pressure-tight seal.
Advantages:
- Compact Design: Ideal for small-sized valves and applications where space is limited.
- Ease of Disassembly: The union nut allows for quick removal of the bonnet for inspection and maintenance.
Considerations:
- Pressure Limitations: Generally suitable for low to medium pressure applications.
Pressure Seal Bonnet
Pressure seal bonnets are specifically designed for high-pressure applications. The unique feature of this design is that the internal pressure enhances the seal between the bonnet and the valve body
Advantages:
- Enhanced Sealing: As internal pressure increases, the seal becomes tighter, reducing the risk of leakage.
- Suitable for High-Pressure Applications: Commonly used in power generation, oil and gas, and petrochemical industries.
Considerations:
- Maintenance Complexity: Disassembly can be more complex compared to other bonnet types, requiring careful handling to avoid damage to the sealing surfaces.
End Connection Types: Integrating Valves into Piping Systems
The end connection of a gate valve determines how it integrates into a piping system. The choice of connection affects installation, maintenance, and the overall integrity of the system.
Flanged Connections
Flanged ends are among the most commonly used valve connections, featuring protruding rims, also known as flanges, that are bolted together with a gasket in between to ensure a leak-proof seal.
Advantages:
- Ease of Installation and Removal: Flanged connections allow for easy disassembly, facilitating maintenance and inspection.
- Versatility: Suitable for a wide range of pressures and temperatures, and compatible with various pipe sizes.
Considerations:
- Space Requirements: Flanged connections require more space due to the size of the flanges and the need for bolt tightening.
Threaded Connections
Threaded ends involve male and female threads on the valve and pipe, screwed together to form a seal.
Advantages:
- Simplicity: Easy to install without the need for specialized tools or equipment.
- Cost-Effective: Generally less expensive than flanged or welded connections.
Considerations:
- Pressure Limitations: Typically used for low-pressure applications.
- Maintenance Challenges: Disassembly can be more challenging, and repeated assembly or disassembly can wear out the threads, leading to potential leaks.
Welded Connections
Welded ends involve permanently joining the valve to the pipe through welding, creating a strong, leak-proof connection.
Advantages:
- High Integrity Seal: Ideal for high-pressure and high-temperature applications where leakage is not acceptable.
- Compact Design: Eliminates the need for flanges, saving space.
Considerations:
- Maintenance Complexity: Disassembly requires cutting the valve out of the pipeline, making maintenance more time-consuming and costly.
- Installation Requirements: Requires skilled labor and proper welding equipment.
Understanding the various bonnet and end connection types is essential for selecting the appropriate gate valve for specific applications, ensuring optimal performance, safety, and ease of maintenance.
Conclusion
Gate valves play a vital role in fluid control systems across various industries. Understanding their design features, material compatibility, size and pressure ratings, stem designs, bonnet types, and end connection options is crucial for selecting the right gate valve for your application. Check out Align Manufacturing for more information on gate valves that will help you ensure optimal performance, safety, and longevity in your fluid control systems.