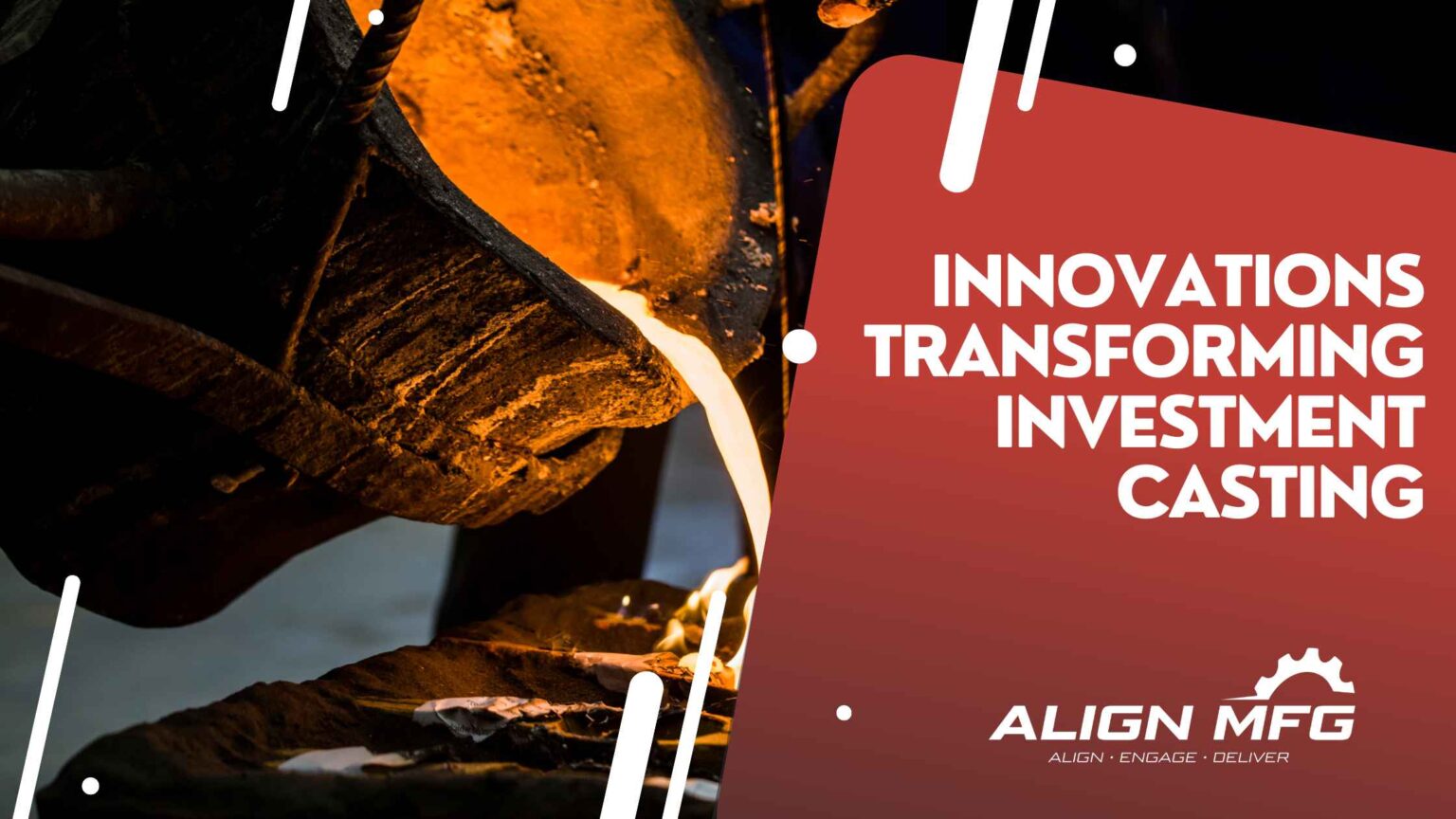
Innovations Transforming Investment Casting
Investment casting, also known as lost-wax casting, has existed for centuries in manufacturing. This is a process for casting metallic parts with great precision and detail; it is, however, a somewhat old format compared to newer versions. This article takes a look at some of the recent developments in investment casting today, with a special focus on 3D printing and new material technologies.
Lost-wax casting is a manufacturing process that produces a wide variety of products of complex geometries. It generally involves a wax pattern surrounded by a ceramic shell. When the shell hardens, the wax is melted out to leave a mold. Hot metal is poured into the mold and the casting can be completed. It is highly commended for products that have excellent surface finish quality and have close tolerances. It is applied in several industries, from aerospace and automotive to medical, where precision, quality control and automation take the foremost place.
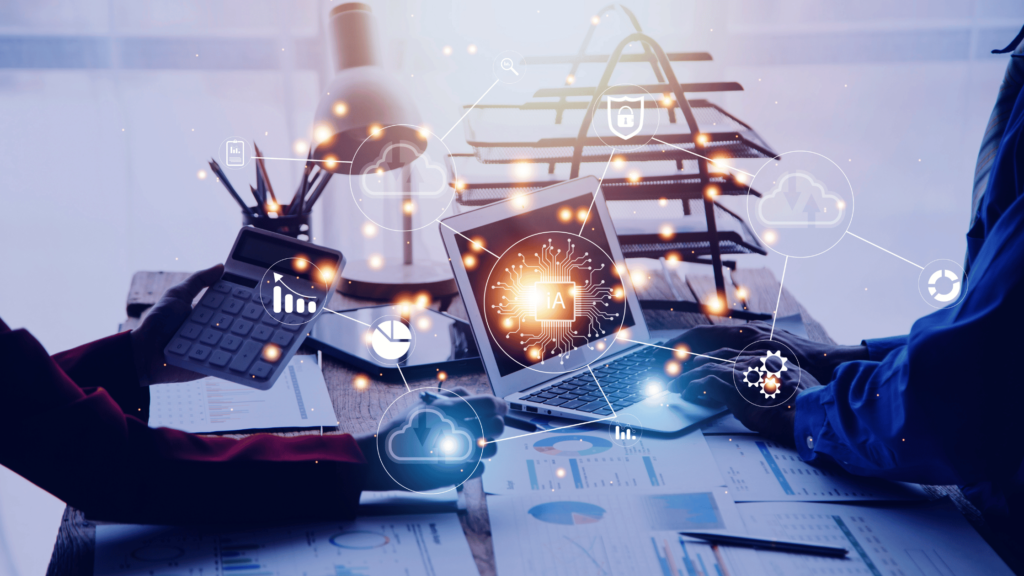
Historical Context and Traditional Methods
Historical origins date back over 5,000 years to ancient civilizations like Mesopotamia and Egypt. Traditional investment casting usually involves several labor-intensive steps:
- Pattern Creation: A wax pattern has to be made that is a replica of the final part.
- Assembly: Several wax patterns can be attached to a tree-like configuration.
- Shell Building: The wax pattern is to be dipped into a ceramic slurry and coated with sand to produce a hard shell.
- Wax Removal: The shell is heated to melt and drain out the wax to leave behind a hollow ceramic mold.
- Casting: Molten metal is poured into the mold.
- Finishing: The ceramic shell is broken away from the cooled metal and the metal part is finished.
While effective, this traditional method is time-consuming and requires significant manual labor. Innovations in technology are addressing these challenges and transforming the process.
3D Printing: A Game Changer in Investment Casting
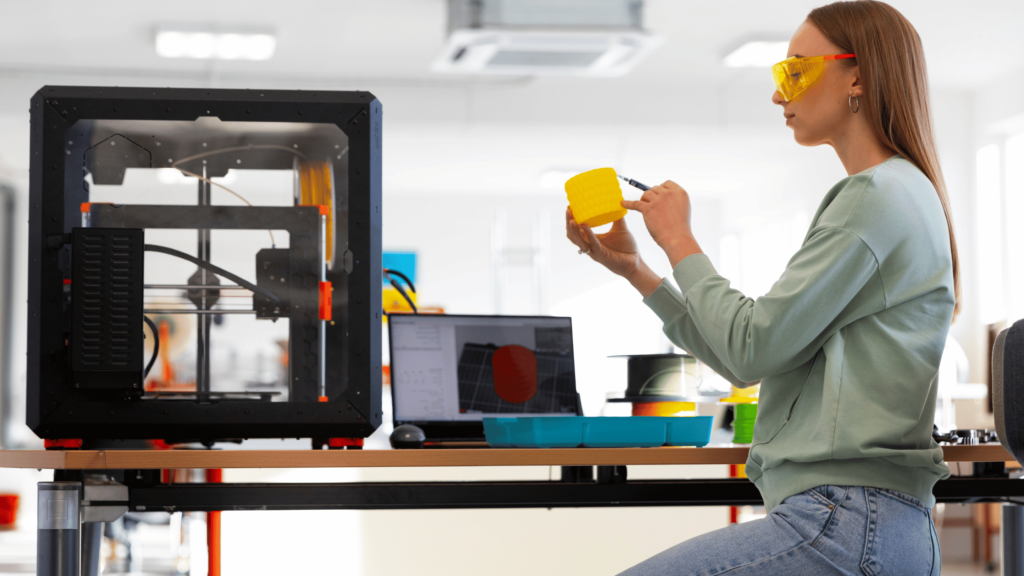
Application of 3D printing or additive manufacturing in the investment casting has significantly revolutionized the process. Earlier, the wax patterns were made by molds and were laborious and, on occasion, costly, especially for something with complex shapes. 3D printing avails a cost-effective and quick alternative.
Advantages of 3D Printing in Investment Casting
- Design Flexibility: It is perfect for creating complex geometries, impossible or very hard to create using traditional methods.
- Reduced Lead Time: The application of 3D printing to make patterns nullifies the need to make the molds, and this way, it reduces the time taken to manufacture patterns significantly.
- Cost Effective: In case of low volume production itself, or prototyping, 3D printing can turn out to be more cost-effective than the traditional lost-wax method in cases of tooling.
- Parts Customization: it has easy parts customization. No additional tooling, neither molds are needed.
3D Printing Technologies in Use
There are several 3-D printing technologies applied to investment casting, each with its unique sets of benefits:
- Stereolithography (SLA): This makes use of a laser to cure liquid resin into solid shapes. It can come up with never seen before detailed and accurate patterns.
- Selective Laser Sintering (SLS): It is a laser kerosene that fuses powdered material, layer by layer, to make powerful and robust patterns.
- Fused Deposition Modeling (FDM): In the FDM process, the melted material gets extruded and laid down to construct the layers. The cost-effective and rapid method to build patterns which are relatively simple.
New Material Technologies
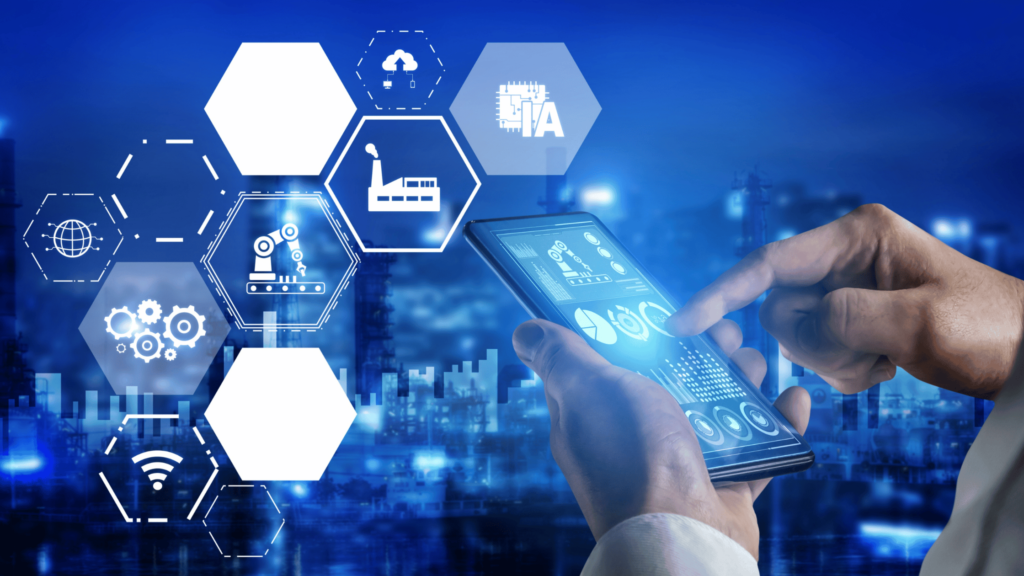
Advancements in material science are also revolutionizing investment casting. New material and new alloys are making the cast parts of better quality, robust, light, and durable.
High-Performance Alloys
New high-performance metals are manufactured to cater to the demanding needs of industries ranging from aerospace, automotive, and medical. These new materials boast improved mechanical properties, corrosion resistance, and temperature tolerance.
Ceramic Shell Improvements
Advanced ceramic shells revolutionize the investment casting process. Improved ceramic formulations enhance the strength and stability, thus reducing the risk of defects and increasing the quality of the cast parts.
Benefits of Advanced Ceramic Shells
- Higher Strength: Improved ceramic materials can withstand higher temperatures and mechanical stresses, allowing for the casting of more robust parts.
- Reduced Defects: Enhanced formulations reduce the occurrence of common casting defects such as cracks and inclusions, leading to higher quality parts.
- Faster Production: Advanced ceramics can shorten the shell-building process, increasing production speed and efficiency.
Integration of Smart Technologies
The integration of smart technologies, such as the Internet of Things (IoT) and Artificial Intelligence (AI), is also making its way into investment casting.
IoT and AI in Investment Casting
- Real-Time Monitoring: The Internet of Things will monitor the casting process in real time by means of different built-in sensors to provide data for maximizing production and minimizing defects.
- Predictive Maintenance: Using AI algorithms to analyze, equipment breakdowns could be predicted, and timeously fixed before they occurred. Reduces downtime and maintenance costs.
- Process Optimization: AI can analyze production data and detect inefficiencies. It can even suggest alternatives, enhancing the general efficiency of the process used in casting.
Future Trends
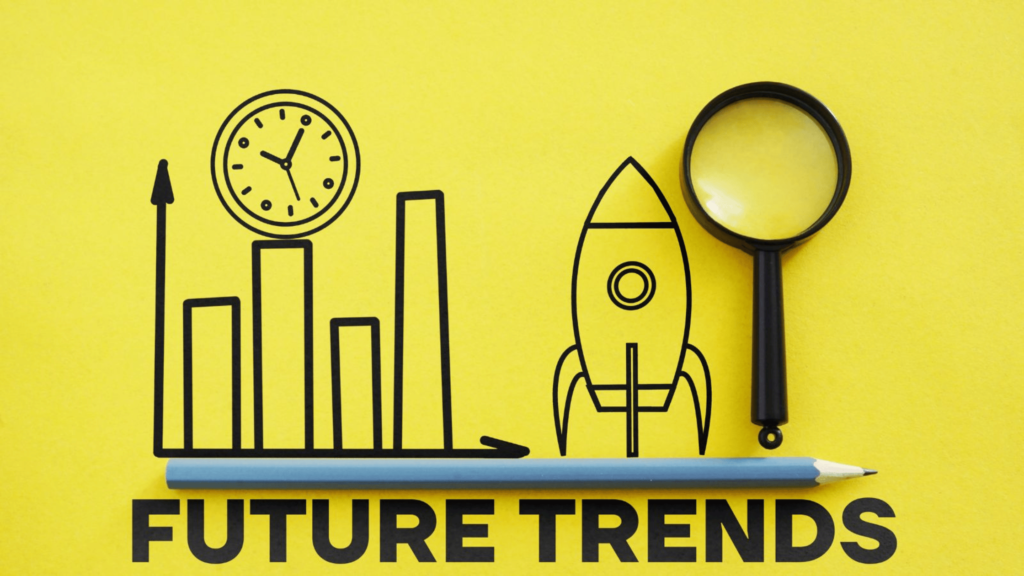
The future of investment casting looks promising, with continued advancements in 3D printing, material technologies, and smart manufacturing. As these technologies evolve, they will further enhance the capabilities and applications of investment casting, opening up new possibilities in various industries.
Emerging Technologies
- Digital Twin Technology: This is the technique for the development of a digital replication or model of physical process operation. This helps to monitor internal operations in real time for optimization. In general, it can help in the prediction and prevention of potential problems that would occur.
- Sustainable Practices: Developments of materials and processes are also done in sustainability. A conductive approach towards eco-friendly materials and the recycling of the materials used in the casting is reducing the impact of investment casting on the environment.
- Hybrid Manufacturing: Traditional techniques used in casting are combined with modern-day techniques, like 3D printing, to design hybrid manufacturing processes. This develops efficient production and better-quality parts.
Conclusion
Investment casting is indeed being transformed through innovative technologies. Other applications of 3D printing and new material technologies besides improving efficiencies and qualities within the manufacturing process continue to expand the applicability of the casting process. These innovations will undeniably be the logos of the manufacturing future that will thus make the investment casting process more flexible and effective than ever before.