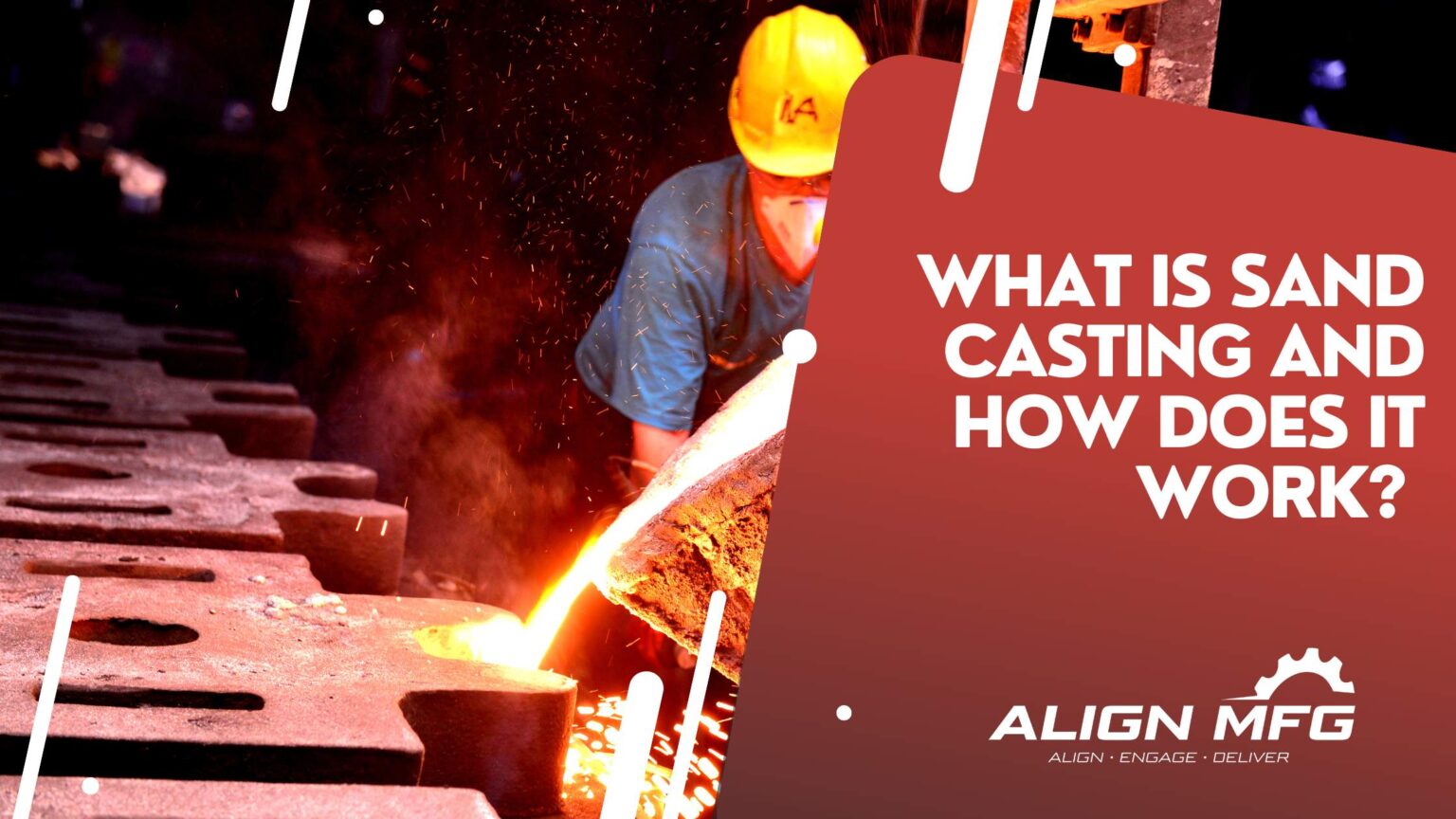
What is Sand Casting and How Does It Work?
Sand casting is one of the oldest and most versatile metal casting methods used in the manufacturing industry, with origins tracing back to ancient Egypt and China. This time-tested technique has been employed for thousands of years, evolving over centuries to become a cornerstone of modern manufacturing. This blog aims to provide a thorough understanding of sand casting, including its process, materials, advantages, and applications across various industries.
What is Sand Casting?
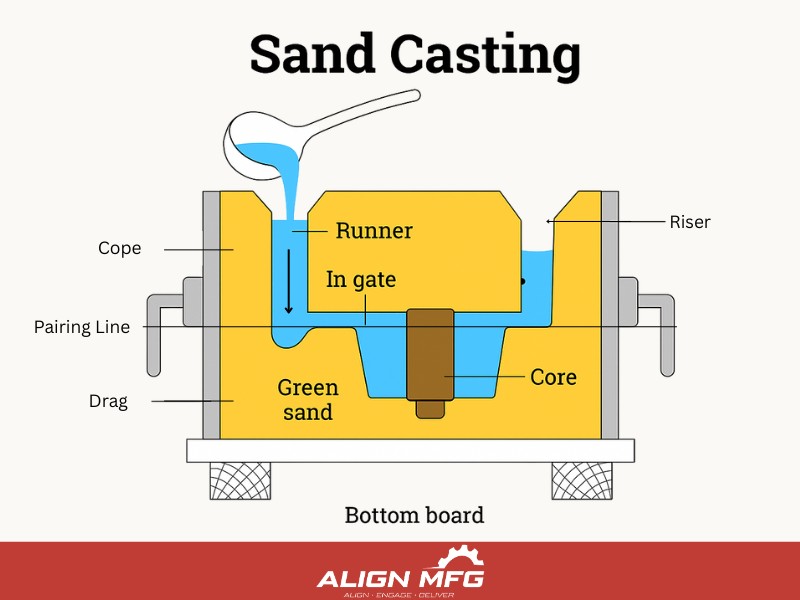
Sand casting is a flexible and economical casting method used in various industries to produce metal objects and components. The process involves creating a mold from sand, into which molten metal is poured to form the desired shape.
Sand casting is particularly valued for its versatility, as it can produce both small-scale custom items and large-scale industrial parts. The method accommodates a wide range of metals, including steel, aluminum, brass, and iron, making it suitable for diverse applications.
Sand Casting vs. Other Types of Casting
When choosing a casting method, understanding the differences between sand casting, die casting, and investment casting is crucial. Each method has its unique advantages and disadvantages. Sand casting offers several advantages, including being cost-effective for low to medium production volumes, the capability to produce large and complex parts, and accommodating a wide range of material options. However, it does have disadvantages, such as a lower surface finish quality compared to die casting and longer production times. Die casting, on the other hand, boasts advantages such as high production speed, excellent surface finish, and dimensional accuracy, making it ideal for high-volume production of smaller parts. Its drawbacks include higher initial tooling costs and limitations to non-ferrous metals. Investment casting provides superior surface finish and intricate detail, making it suitable for complex geometries and a variety of alloys. Nevertheless, it comes with higher costs and longer lead times, rendering it less ideal for producing large parts.
How Does Sand Casting Work?
Pattern Making
Pattern Making is the first step in the sand casting process. A pattern, which is a replica of the final casting, is created using materials such as wood, metal, or plastic. The pattern includes allowances for shrinkage and machining to ensure the final product meets precise dimensions. This step requires skilled craftsmanship to capture all the details and features required in the casting.
- Materials Used: Patterns are made from wood, metal, or plastic.Metal patterns, typically made from aluminum or steel, offer greater durability and precision compared to wood. They are ideal for high-volume production runs and parts requiring fine details and tight tolerances. .
- Shrinkage Allowances: Patterns are slightly larger to account for metal shrinkage during cooling.
- Core Prints: Patterns may include core prints to position sand cores accurately within the mold.
Mold Making
Mold Making involves creating a mold by packing sand around the pattern. The mold is divided into two halves: the cope (top half) and the drag (bottom half). Once the pattern is removed, the cavity left behind forms the mold for the casting.
- Molding Sand: A mixture of sand, clay, and water (green sand) or chemically bonded sand.
- Cope and Drag: The mold is split into two halves to facilitate pattern removal and metal pouring.
- Compaction Methods: Sand is compacted around the pattern using ramming or vibration techniques to ensure a dense, stable mold.
Core Making
Core Making involves inserting cores into the mold to create internal cavities in the final casting. Cores are made from sand and held together with binders. They are positioned within the mold using core prints on the pattern.
- Core Materials: Typically sand with organic or chemical binders.
- Core Placement: Cores are placed within the mold cavity to form internal passages or complex shapes.
- Chaplets: Metal supports, known as chaplets, may be used to hold cores in place during metal pouring.
Pouring
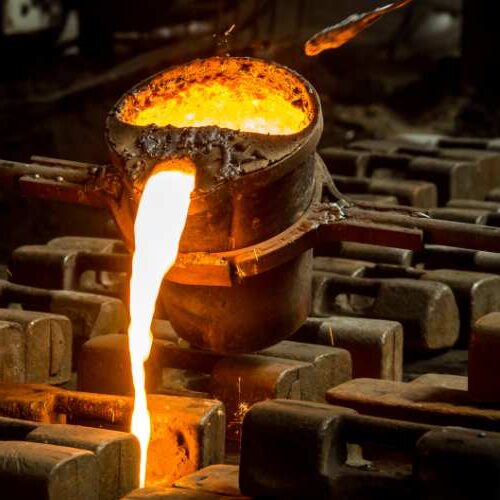
Pouring is the process of melting the metal and pouring it into the mold cavity. The metal is heated in a furnace until it reaches the required temperature, then transferred to a ladle for controlled pouring into the mold.
- Melting Furnace: Different types of furnaces (e.g., induction, electric arc) are used to melt the metal.
- Pouring Techniques: The metal is poured at a controlled rate to avoid defects like misruns or inclusions.
- Temperature Control: Proper pouring temperature is crucial to ensure complete filling of the mold and optimal metal properties.
Cooling
Cooling allows the molten metal to solidify within the mold. The cooling time depends on the size and complexity of the casting. Controlled cooling is essential to achieve the desired mechanical properties and dimensional accuracy.
- Solidification: The metal solidifies and takes the shape of the mold cavity.
- Cooling Rate: Proper cooling rates prevent defects such as internal stresses or shrinkage cavities.
Removing
Removing involves breaking the mold to retrieve the solidified casting. This step, also known as shakeout, separates the casting from the sand mold.
- Shakeout Methods: Mechanical or manual methods are used to break the mold and remove the casting.
- Handling: Careful handling of the hot casting to avoid damage.
Cleaning
Cleaning is the final step where any excess sand and metal remnants are removed from the casting. This process includes various finishing operations to achieve the desired surface finish and dimensions.
- Sand Removal: Remaining sand is removed using pneumatic tools, brushes, or water jets.
- Finishing Operations: Grinding, blasting, and machining are performed to smooth surfaces and meet dimensional specifications.
- Quality Inspection: Final inspection ensures the casting meets all quality and dimensional requirements.
Materials Used in Sand Casting
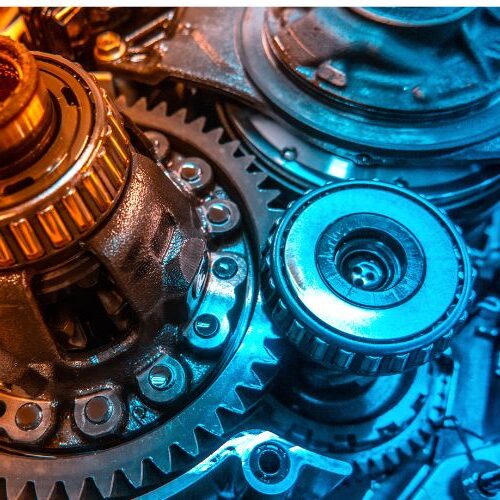
The sand casting process relies on various materials to create high-quality molds and castings. Each material plays a crucial role in ensuring the effectiveness and efficiency of the casting process.
Casting Sand
Casting Sand is the primary material used in the sand casting process. High-quality silica sand is commonly used due to its excellent properties, which include high refractoriness, good permeability, and the ability to withstand the high temperatures required for metal casting.
- Silica Sand: The most widely used type of sand in sand casting. It offers high melting points and low thermal expansion, making it ideal for creating stable molds.
- Chromite Sand: Often used for its high heat resistance and thermal conductivity. It’s beneficial for casting metals with high melting points.
- Zircon Sand: Known for its low thermal expansion and high thermal conductivity, zircon sand helps in producing precise castings with minimal defects.
Binders
Binders are materials that hold the sand grains together, providing the mold with the necessary strength and stability. In green sand casting, clay and water are the primary binders used.
- Clay: Bentonite clay is the most common binder used in green sand casting. It provides the necessary cohesiveness to the sand mixture, allowing it to hold its shape during the molding process.
- Water: Acts as an activating agent for the clay, helping it to bind the sand particles together effectively. The moisture content in the green sand mix is crucial for achieving the right mold properties.
Additives
Additives are used to enhance the properties of the sand mold, improving its performance during the casting process. These materials can improve the mold’s strength, permeability, and surface finish.
- Coal Dust: Commonly added to green sand to improve the surface finish of the casting and reduce defects such as gas porosity.
- Organic Compounds: Such as wood flour or cereal binders, are sometimes added to green sand to improve its collapsibility, making it easier to remove the casting from the mold.
- Chemical Binders: In dry sand casting, chemical binders such as sodium silicate or phenolic resins are used to enhance the sand’s bonding properties and improve mold stability.
Types of Sand Used in Casting
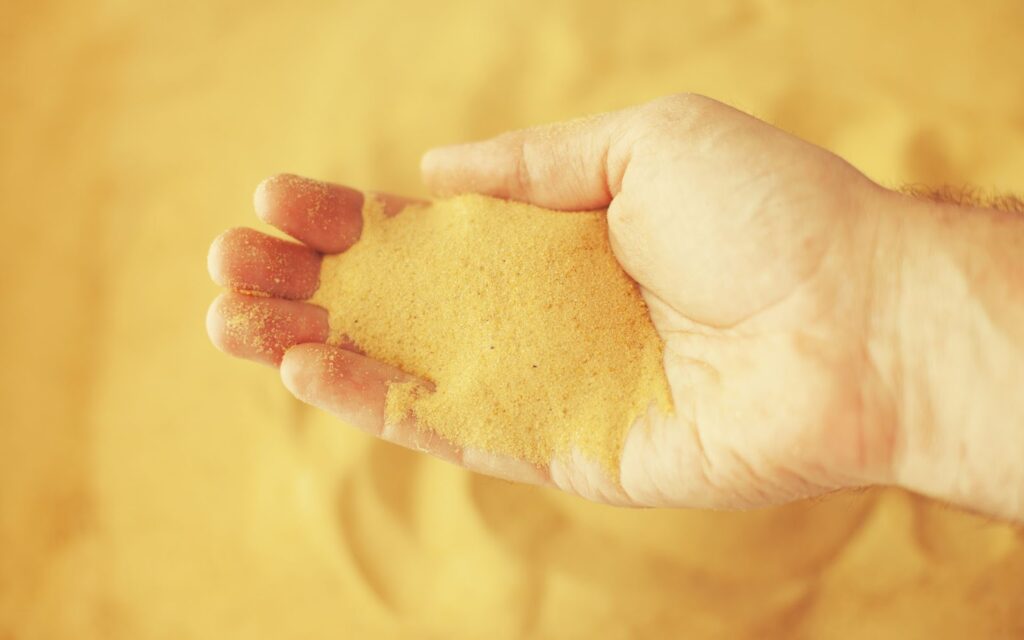
There are two basic types of sand used in the sand casting process: green sand and dry sand. Each type has its own composition, characteristics, and applications, making them suitable for different casting needs.
Green Sand vs. Dry Sand
Composition and Characteristics
Green Sand:
- Composition: Green sand is a mixture of silica sand, clay (usually bentonite), and water. Sometimes, organic compounds like coal dust are added to enhance the mold’s strength and surface finish.
- Characteristics: The name “green” refers to the sand’s moisture content. Green sand remains pliable and can be easily shaped and compacted around the pattern. It is not “green” in color but “green” in the sense that it is used in a wet, uncured state. The clay and water act as binders, providing cohesiveness and allowing the mold to hold its shape during metal pouring.
Dry Sand:
- Composition: Dry sand is similar to green sand but without the water content. It is typically baked or cured using chemical binders to increase its strength and stability.
- Characteristics: Dry sand molds are stronger and more rigid than green sand molds. They can withstand higher temperatures and pressures during the casting process, making them suitable for more complex and precise castings. The baking process also reduces the likelihood of defects caused by moisture.
Applications and Benefits
Green Sand:
- Applications: Green sand is widely used in the automotive, aerospace, and general manufacturing industries. It is ideal for producing large, complex shapes such as engine blocks, cylinder heads, and pump housings.
- Benefits:
- Good for casting both ferrous and non-ferrous metals
- Versatility: Easy to mold and reshape,capable of producing a wide range of sizes and shapes, from small intricate parts to large complex components.
- Cost-Effectiveness: Lower production costs compared to other casting methods, making it ideal for both short and long production runs.
- Quality: High-quality castings with excellent mechanical properties, suitable for demanding applications across multiple industries.
Dry Sand:
- Applications: Dry sand is often used for casting intricate and high-precision parts. It is commonly employed in the production of small to medium-sized components that require fine details and tight tolerances, such as aerospace components, medical devices, and high-performance machinery parts.
- Benefits:
- Higher strength and stability compared to green sand.
- Better surface finish and dimensional accuracy.
- Reduced risk of defects related to moisture and gas entrapment
No-Bake Sand Castings:
Sand casting encompasses various types, each tailored for specific applications and requirements. One such type is No-Bake sand casting, which includes Furan and Alphaset. These methods require no baking, relying solely on ramming and binder to hold the mold shape. Within No-Bake sand casting, Shell molding stands out as a notable technique, particularly favored for casting cylinder heads due to its precision and efficiency compared to Dry Sand casting.
Types of Metals Used in Sand Casting
A critical aspect of sand casting is its versatility with different metals. It accommodates all metals except for exotic ones like gallium or mercury. Particularly, sand casting is well-suited for high-cost/high-temperature materials, such as titanium and nickel. Below is a detailed list of metals commonly used in sand casting:
- Aluminum Alloys : Lightweight and corrosion-resistant, ideal for automotive and aerospace applications.
- Cast Iron : Known for its excellent wear resistance, often used in engine blocks and heavy machinery.
- Bronze: Offers high corrosion resistance and is often used in marine applications.
Applications of Green Sand Casting
Automotive Industry
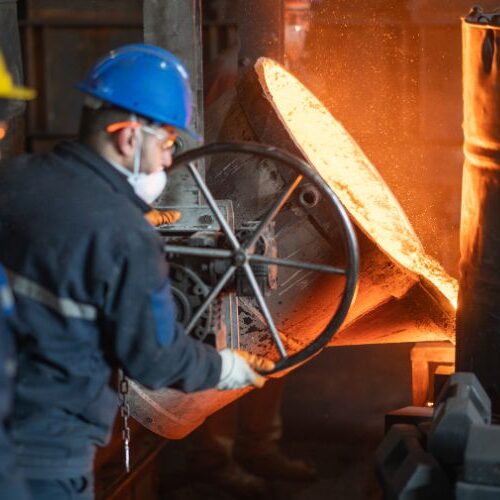
In the automotive sector, green sand casting is essential for manufacturing complex engine components, transmission housings, and various structural parts. Align MFG produces durable and precise castings that meet the stringent requirements of automotive manufacturers.
- Engine Blocks: High-strength engine blocks and cylinder heads are cast using green sand molds to ensure durability and performance under high stress.
- Transmission Housings: The method allows for the creation of complex geometries required for efficient and reliable transmission systems.
Construction Industry
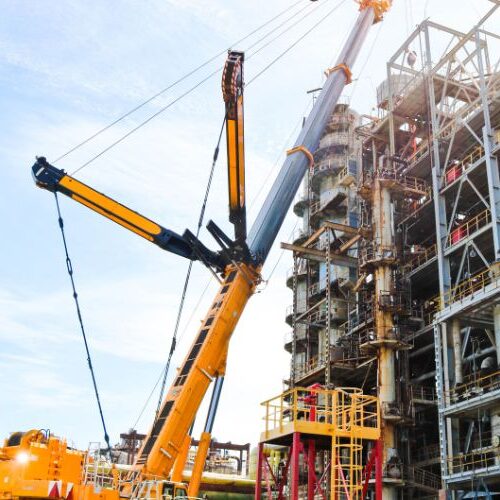
In the construction industry, green sand casting is utilized to produce robust and durable parts for heavy machinery and infrastructure projects. Align MFG’s expertise ensures high-quality castings for these demanding applications.
- Machinery Parts: Large and complex machinery components, such as gear housings and brackets, are cast using green sand molds to ensure strength and longevity.
- Infrastructure Components: Custom castings for bridges, buildings, and other infrastructure elements are made to meet specific design and performance criteria.
Advantages and Disadvantages of Sand Casting
Advantages
- Cost-effective for Small to Medium Production Runs: Sand casting is an economical choice for producing parts in small to medium quantities. The low cost of raw materials and molds makes it a cost-effective solution for various manufacturing needs.
- Capable of Producing Large and Complex Shapes: Sand casting is highly versatile and can be used to produce large and intricate components that might be difficult to create using other methods. This flexibility is particularly beneficial for industries requiring custom and complex shapes. Align MFG are among a handful of manufacturers that can assist with massive scale sand casting projects ranging to over 15 tons, find out more about our large scale sand casting.
- Reusable Sand Molds: The sand used in the casting process can be recycled and reused multiple times, reducing material costs and minimizing waste. This sustainability aspect makes sand casting an environmentally friendly option compared to other casting methods.
- Wide Range of Metal Compatibility: Sand casting can accommodate a variety of metals, including iron, steel, aluminum, brass, and bronze. This versatility allows manufacturers to produce components for different applications using the same casting method.
- Short Lead Times: The simplicity of the sand casting process enables quicker turnaround times for production runs, which is advantageous for meeting tight deadlines and market demands.
Disadvantages
- Lower Dimensional Accuracy Compared to Other Casting Methods: Sand casting generally produces parts with lower dimensional accuracy and a rougher surface finish compared to precision casting methods like investment casting or die casting. Additional machining may be required to achieve the desired specifications.
- Surface Finish May Require Additional Machining: Due to the rough texture of sand molds, the surface finish of sand-cast parts often needs further finishing processes such as grinding, polishing, or machining to meet the required standards.
- Limited Complexity for Fine Details: While sand casting is excellent for large and complex shapes, it may not be suitable for parts that require extremely fine details or tight tolerances. Other casting methods might be more appropriate for such requirements.
- Higher Labor Costs for Complex Parts: The manual aspects of the sand casting process, such as pattern making and mold preparation, can result in higher labor costs, especially for complex parts. Automation and advanced techniques can help mitigate this issue but might increase the initial investment.
Properties Determining the Quality of a Sand Mold
Key Properties
Permeability refers to the ability of the sand mold to allow gases to escape during the casting process. Proper permeability is essential to prevent gas defects, such as porosity, in the final casting.
- Importance: As molten metal is poured into the mold, gases are generated. High permeability ensures that these gases escape through the sand mold rather than becoming trapped within the casting, which could lead to defects and structural weaknesses.
- Measurement: Permeability is typically measured by the rate at which air can pass through a standard sand sample. The sand’s grain size, shape, and distribution all affect its permeability.
Strength
Strength is the ability of the sand mold to retain its shape under pressure and during the metal pouring process. Adequate strength is necessary to maintain the integrity of the mold and prevent it from collapsing or deforming.
- Importance: A strong mold can withstand the mechanical stresses during pattern removal, core setting, and metal pouring without breaking or distorting. This ensures that the casting dimensions remain accurate and consistent.
- Types of Strength:
- Green Strength: The strength of the mold when it is still moist.
- Dry Strength: The strength of the mold after it has dried and hardened.
- Hot Strength: The mold’s strength at elevated temperatures, crucial during the actual pouring of molten metal.
Refractoriness
Refractoriness is the ability of the sand mold to withstand high temperatures without breaking down or melting. This property is critical when casting metals with high melting points.
- Importance: High refractoriness ensures that the sand mold does not degrade or fuse with the molten metal during the casting process, which could result in defects and surface imperfections in the final product.
- Materials Contributing to Refractoriness: Silica sand is commonly used due to its high melting point. Other materials, like zircon and chromite sands, are also used to enhance refractoriness for specific applications.
Precision and Tolerances in Sand Casting
Sand casting can achieve a decent level of precision and tolerances, but it is generally less accurate than other methods like investment casting or die casting. Precision depends on factors such as mold quality and the casting process control.
- Mold Quality: The precision of the mold directly influences the accuracy of the casting. High-quality molds with fine sand grains can produce smoother surfaces and more accurate dimensions.
- Pattern Design: Accurate pattern design with appropriate allowances for shrinkage and machining ensures that the final casting meets the required dimensions. Patterns must also include draft angles to facilitate easy removal from the mold without damaging the sand walls.
- Core Placement: Proper placement and securing of cores within the mold are crucial for achieving the desired internal geometries and maintaining dimensional accuracy.
- Pouring Techniques: Controlled pouring of molten metal at the correct temperature and speed helps prevent defects such as misruns, cold shuts, and inclusions, which can affect the precision of the casting.
- Cooling Rate: Uniform and controlled cooling prevents warping and ensures the casting retains its intended shape and dimensions. Variations in cooling rates can lead to internal stresses and dimensional inaccuracies.
Industry Standards and Tolerances
Industry Standards and Tolerances define acceptable levels of dimensional variations in cast components. These standards ensure that castings meet the functional and performance requirements of their intended applications.
- Dimensional Tolerances: Sand casting generally achieves dimensional tolerances of ±0.020 inches per inch. However, this can vary based on the complexity of the part and the skill of the foundry.
- Surface Finish: The surface finish of sand-cast parts is typically rougher than that of investment or die-cast parts. Secondary machining processes are often required to achieve smoother surfaces and tighter tolerances.
- Geometric Tolerances: Geometric tolerances, including flatness, roundness, and concentricity, are crucial for ensuring the parts fit and function correctly. These tolerances are specified according to industry standards to maintain consistency and quality from Align MFG.
Design Considerations
Shrinkage Allowances:
- Importance: During cooling, molten metal shrinks as it solidifies. Patterns must be designed larger than the final casting to account for this shrinkage, ensuring that the final dimensions are accurate.
- Calculation: The amount of shrinkage allowance depends on the type of metal being cast. Different metals have different shrinkage rates, and these must be factored into the pattern design.
Draft Angles:
- Purpose: Draft angles are slight tapers added to the vertical surfaces of the pattern to facilitate its removal from the mold without damaging the mold walls.
- Specification: The angle of the draft depends on the complexity and depth of the pattern. Common draft angles range from 1° to 3°.
Core Prints:
- Function: Core prints are features added to the pattern to create recesses in the mold where sand cores will be placed. These ensure proper positioning and support of the cores during the casting process.
- Design: Core prints must be accurately designed to match the size and shape of the cores, providing stability and preventing movement during metal pouring.
Machining Allowances:
- Necessity: Additional material is added to the pattern to allow for machining and finishing processes after casting. This ensures that the final part meets the precise specifications and surface finish requirements.
- Allowance Size: The amount of machining allowance depends on the casting’s size, complexity, and the required finish. Typically, allowances range from 1.5 mm to 3 mm for most applications.
Functions of Cores and Chaplets
Cores and chaplets play essential roles in the sand casting process, enabling the creation of complex internal geometries and providing support within the mold. Understanding their functions helps ensure the production of high-quality castings.
Achieving Temper in Sand Casting
Achieving temper in sand casting involves controlling the moisture content and compactability of the sand to ensure optimal mold conditions. Proper tempering of the sand is crucial for creating high-quality molds that produce accurate and defect-free castings.
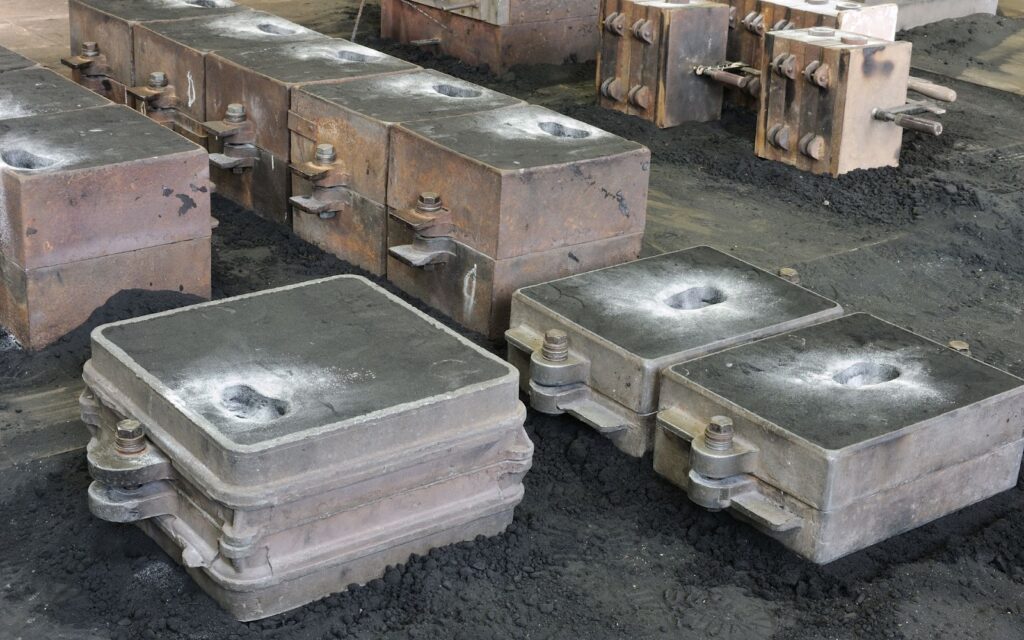
Tempering Process
The tempering process in sand casting is essential for preparing the sand mixture to achieve the right consistency and properties for molding. This process involves adding the correct amount of water and other additives to the sand, followed by thorough mixing to distribute moisture evenly.
Techniques and Best Practices:
- Moisture Control: Maintaining the appropriate moisture content is critical for achieving the desired sand temper. Too much moisture can lead to a weak mold, while too little can result in poor sand cohesion and mold instability/
- Measurement Tools: Use moisture meters to regularly check the moisture content of the sand. Aim for a consistent moisture level, typically between 2-4%, depending on the specific requirements of the casting process.
- Water Addition: Gradually add water to the sand mixture while continuously mixing to ensure even distribution. This helps achieve the desired moisture content without oversaturating the sand.
- Compactability: The compactability of the sand affects the mold’s strength and surface finish. Proper compaction ensures that the sand particles are tightly packed, providing a stable and robust mold.
- Compaction Methods: Utilize ramming, squeezing, or jolting techniques to compact the sand around the pattern. These methods help achieve uniform density and improve the mold’s overall integrity.
- Additives: Incorporate additives such as bentonite clay and coal dust to enhance the sand’s compactability and overall performance. Bentonite increases cohesion, while coal dust improves surface finish by reducing metal penetration and burn-on defect.
- Mixing Equipment: Use appropriate mixing equipment to ensure the sand mixture is homogeneous. Mechanical mixers or mullers are commonly used to achieve consistent sand properties throughout the batch.
- Mixing Duration: Ensure adequate mixing time to distribute moisture and additives evenly. Overmixing can degrade the sand particles, while undermixing can result in uneven tempering.
Advanced Sand Casting Technologies: Disamatic Innovations
Advanced technologies in sand casting have revolutionized the industry, enhancing efficiency and precision in manufacturing. One such technology is the Disamatic molding system, well-known among foundry professionals. Disamatic offers cutting-edge solutions like the DISA FLEX and DISA MATCH, which provide high-quality molding capabilities. The DISA FLEX combines the versatility of a horizontal flask molding machine with the speed and precision of modern automation, making it ideal for various casting applications. Similarly, the DISA MATCH delivers superior accuracy and repeatability, ensuring consistent quality in every cast. These innovations streamline the sand casting process, reducing waste and improving overall productivity. For more details, you can explore DISA FLEX and DISA MATCH.
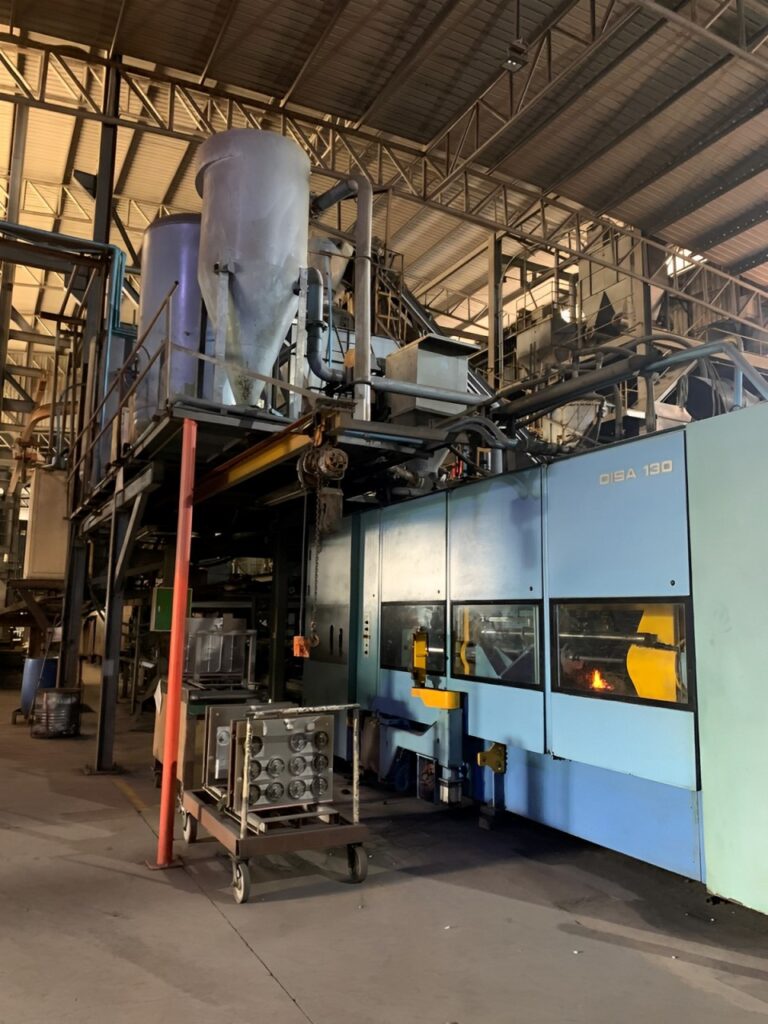

Examples of Sand Casting Products
The versatility and broad applicability of sand casting are exemplified through various products across multiple industries. Here are some standout examples:
– Engine Blocks: Integral to automotive and industrial engines, these components exemplify the method’s strength and durability.
– Pulleys and Gears: Critical machinery parts that showcase the precision achievable through sand casting.
– Medium-Speed Marine Diesel Flywheels: These can weigh several tons, demonstrating the method’s ability to handle significant mass.
– Marine Applications: Through-hull nickel-aluminum bronze fittings in boat and ship hulls, illustrating corrosion resistance and robustness.
– Barbecue Grills and Burner Components: Common household and commercial items that benefit from sand casting’s adaptability.
– ICE Engine Blocks and Vehicle Brake Discs: Essential automotive parts ensuring safety and performance.
– Door Furniture: Stylish and functional elements in residential and commercial settings.
– Heavy Machinery and Oil Field Tools: Durable tools designed to withstand harsh environments.
– Jewelry: Crafted from various precious and common metals, showcasing intricate detailing.
These examples highlight how sand casting can deliver both functional and artistic results through its wide-ranging applications.
Conclusion
Sand casting remains a vital process in the manufacturing industry due to its versatility and cost-effectiveness. By understanding its stages, materials, advantages, and applications, businesses can make informed decisions about utilizing this method for their production needs.
For more information on sand casting or to receive a personalized quote, contact Align Manufacturing today. Our team is ready to assist you in selecting the best casting method for your project needs, ensuring quality and efficiency.