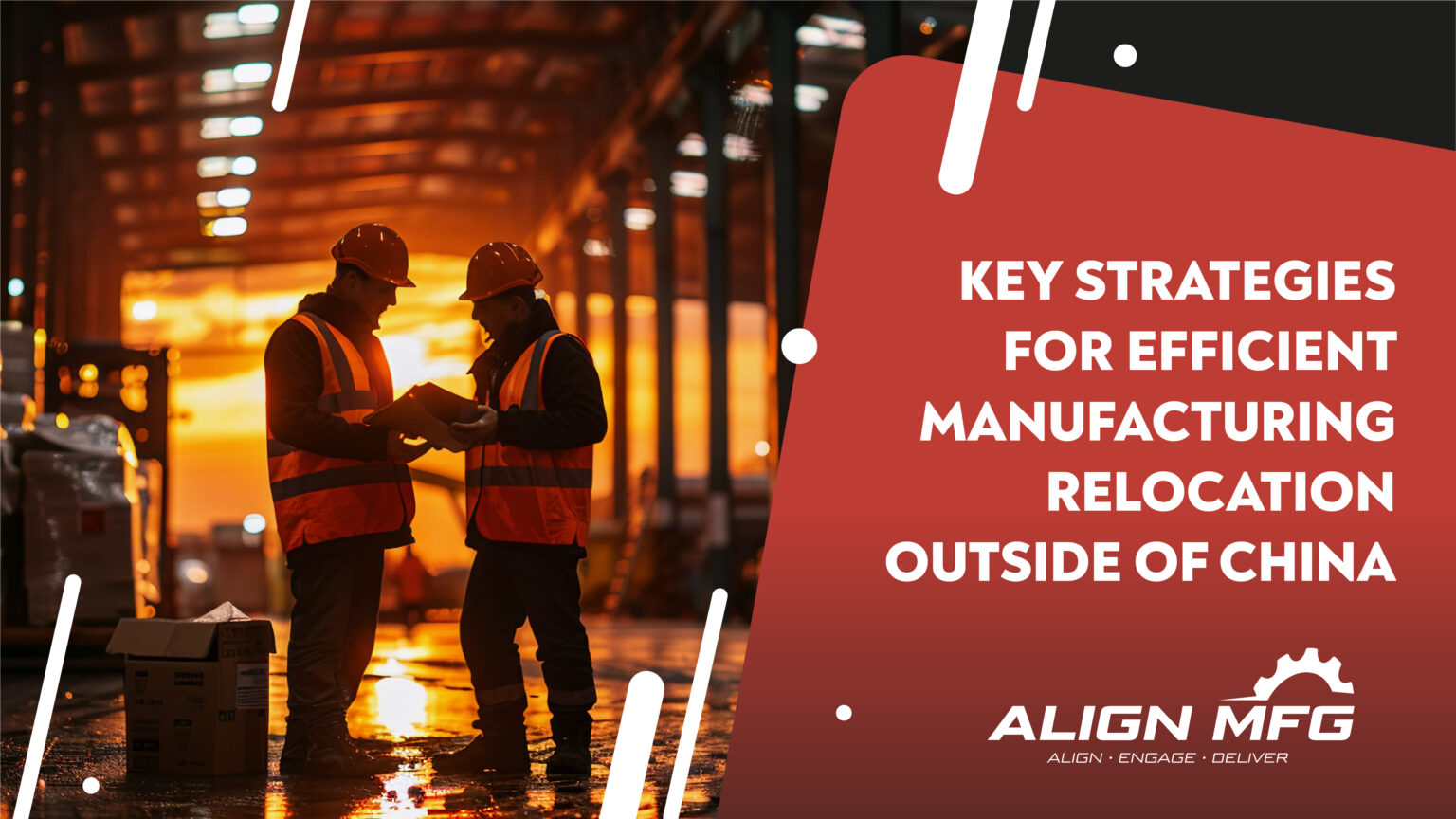
Key Strategies for Efficient Manufacturing Relocation Outside of China
In light of the escalating trade tensions and economic uncertainties between the US and China, adapting manufacturing locations to more stable regions like Southeast and South Asia has become essential for maintaining competitive advantage. This article explores essential strategies that businesses can employ to ensure an efficient transition away from traditional bases like China to more dynamic regions such as Southeast and South Asia for their metal parts manufacturing and metal components manufacturing. By detailing proactive steps for preparation and our bespoke approach, we outline how businesses can minimize disruptions and optimize operational efficiencies during this critical move.
Preparation by Importers:
- Ensure all drawings and 3D models are up-to-date, including the latest revisions.
- Set a realistic target price based on current market conditions.
- Provide records of any quality issues encountered in previous productions to anticipate and mitigate repeat problems.
- Supply samples for reference to maintain consistency in production quality.
- Detail any proprietary inspection techniques, inspection levels, packing standards, specifications, and acceptance/rejection criteria to align expectations and processes.
Our Approach:
- Align Manufacturing reviews the list of parts clients intend to move, considering the process, material, and quantities to develop a tailored procurement strategy.
- We strive to keep parts geographically consolidated to maximize shipping efficiencies and minimize costs, aiming to fully utilize container capacities up to 44,000 lbs.
- We select vendors based on specific manufacturing processes and material costs, leveraging the strengths of each country:
- For open die forging, vendors in India are preferred due to superior capabilities.
- For precise CNC machined parts, our Vietnamese vendors are optimal.
- For materials like Nickel Bronze, which are expensive in Thailand and Vietnam, we opt for Indian production.
- For high volume orders, location is flexible; for low volume orders, Thailand is more accommodating due to its willingness to accept smaller quantities.
- We advise starting with no-tooling parts where possible to save on both time and expenses, thus streamlining the initial phases of production setup.
Starting with the 'Head' vs. 'Dipping Toes':
Rather than 'dipping their toes' with low volume or less critical components, importers should 'start with the head' by prioritizing high-volume or crucial parts. This strategy leads to:
- Easier placement of initial high-volume projects, setting a solid foundation for subsequent smaller productions.
- Improved pricing leverage, reducing the risks of staying dependent on Chinese manufacturing.
- Simplified logistics through high-volume shipments (FCL), which reduce costs and increase the frequency of just-in-time (JIT) inventory deliveries.
This comprehensive approach not only ensures a smoother transition but also maximizes efficiency and cost-effectiveness during the relocation process.
About Align Manufacturing:
Align Manufacturing, headquartered in Singapore and with offices in Bangkok, specializes in delivering high-quality industrial production solutions. Our expertise ranges from intricate sand casting and robust forging to efficacious stamping and state-of-the-art precision machining. This diverse capability ensures that we meet the complex needs of our clients with meticulous attention to detail and seamless communication. Partner with Align Manufacturing for efficient and precise manufacturing outcomes tailored to your project's success.
Note:
This article is part of an ongoing series exploring why US-based companies need to move their manufacturing operations outside of China.
To read the next article, click HERE.
To read the previous article, click HERE.
To download the entire series as a report, click the button below.