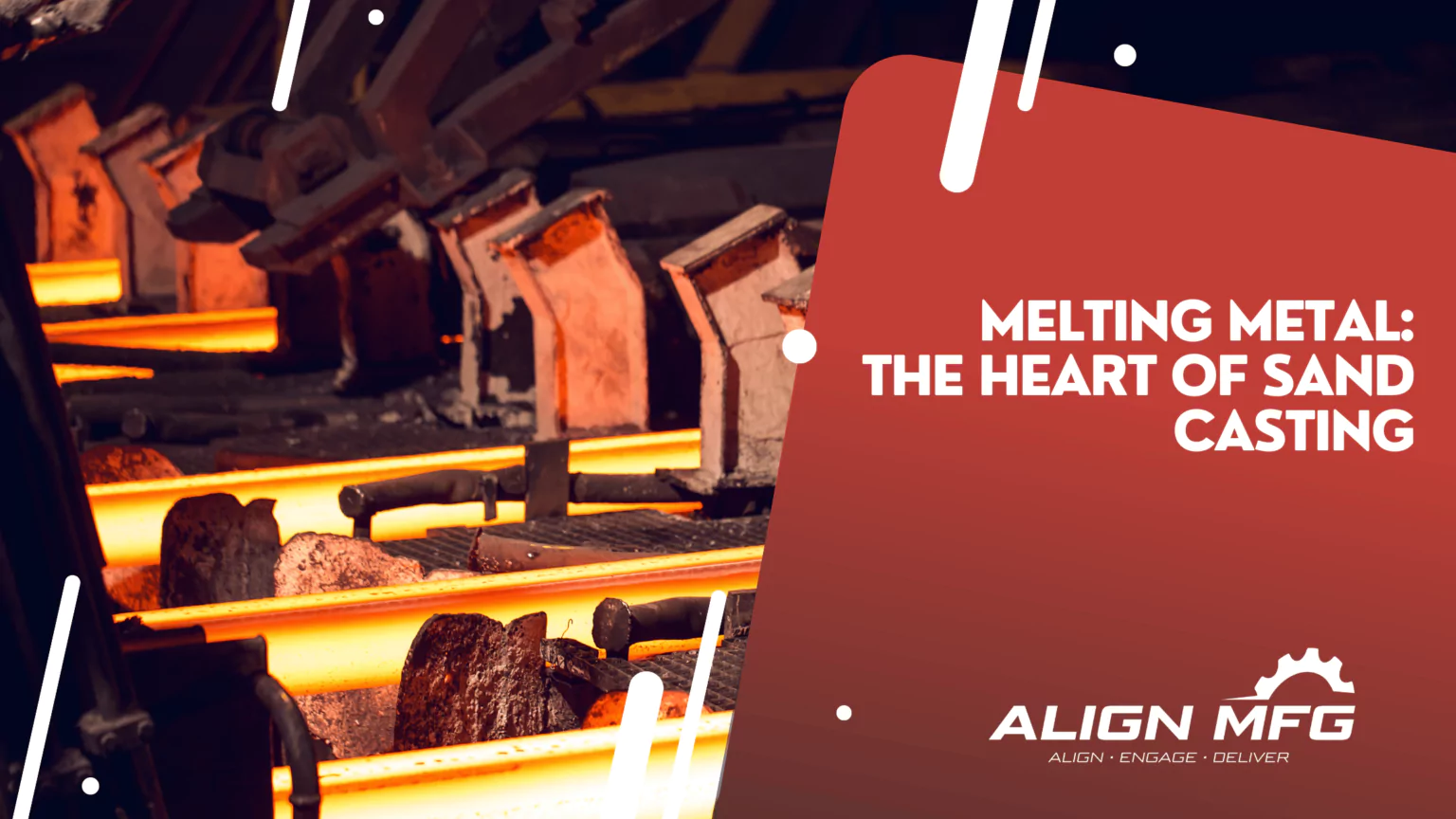
Melting the Metal: The Foundation of Sand Casting
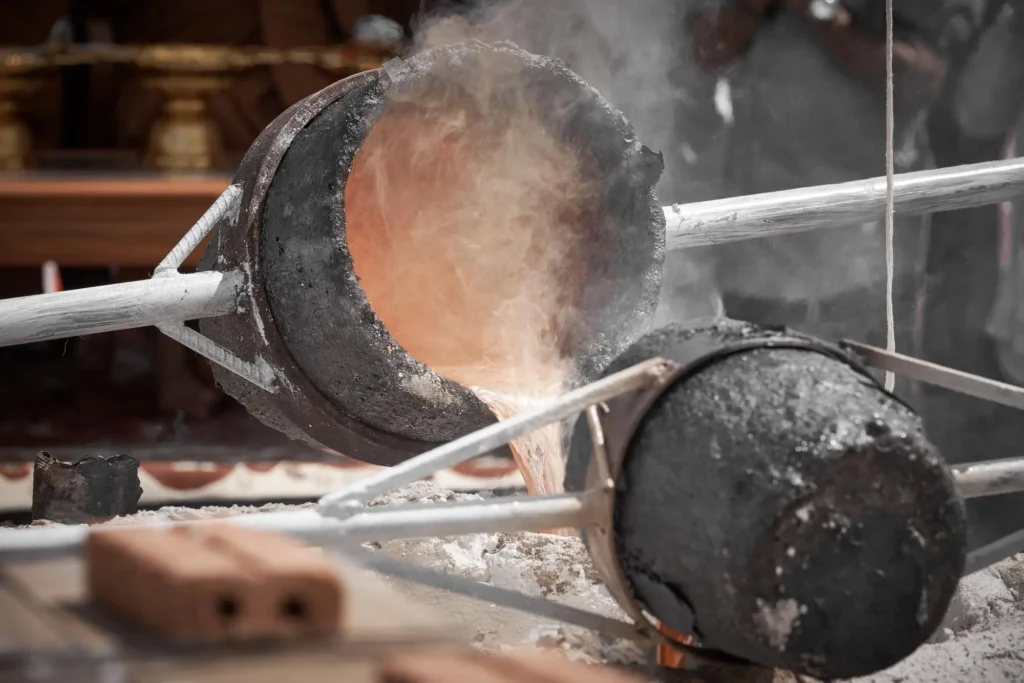
Metalworking has its roots in smelting, the process of extracting metals from ores. Unlike melting, which reshapes pure metals or alloys, smelting involves chemically separating a metal from its natural mineral form. This process laid the foundation for modern metal casting techniques.
The Bloomery Process: The Birthplace of Metal Extraction
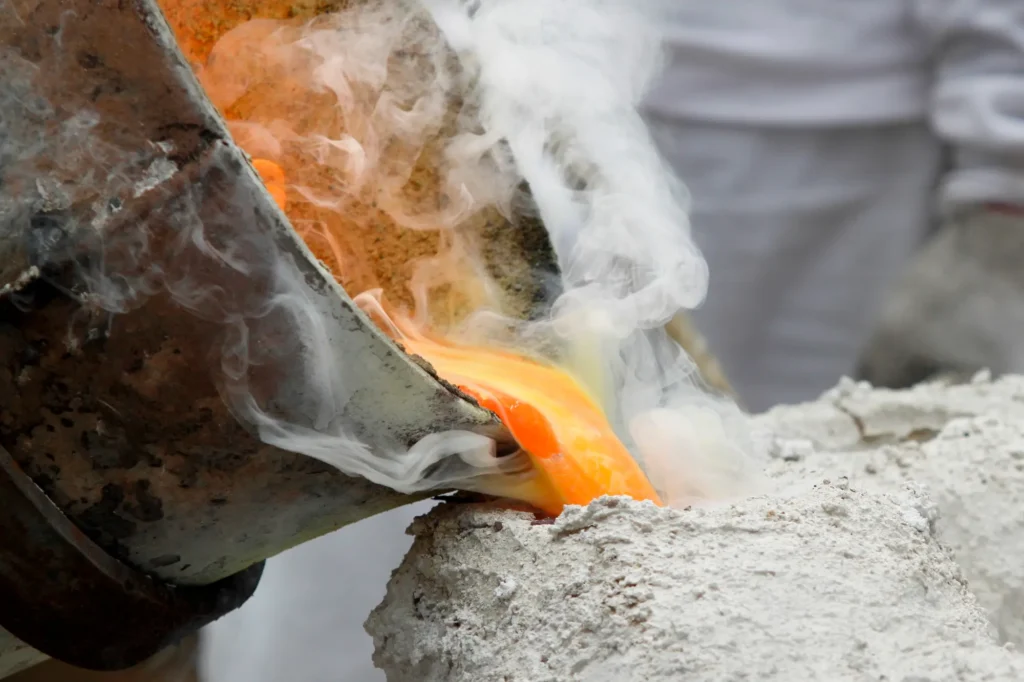
- The bloomery was the first furnace designed to smelt iron ore.
- How It Worked: Charcoal-fueled fires and forced air from bellows produced the intense heat needed to reduce iron ore into a spongy mass called a bloom.
- Key Result: The bloom was hammered to remove slag, yielding workable wrought iron. This primitive process shaped human history by enabling the creation of tools, weapons, and structures.
The Rise of Pig Iron through Advanced Smelting
- Smelting evolved with the invention of the blast furnace, which could sustain higher temperatures and produce pig iron—a crude form of iron with high carbon content.
- Why Pig Iron?: The name comes from the traditional casting setup, where molten iron was poured into molds resembling piglets suckling from a sow.
- Limitations: Pig iron was brittle due to its high carbon content but could be refined into steel, marking a major advancement in metallurgy.
Throughout history, advancements in metallurgy have driven technological progress. The Bronze and Iron Ages marked early breakthroughs, while the Industrial Revolution ushered in the Steel Age. A pivotal innovation was the Bessemer process, which introduced oxygen into molten steel, raising temperatures and accelerating production. This method revolutionized steel manufacturing, enabling the creation of modern infrastructure such as railways, engines, and large-scale construction projects.
Why Alloying Matters
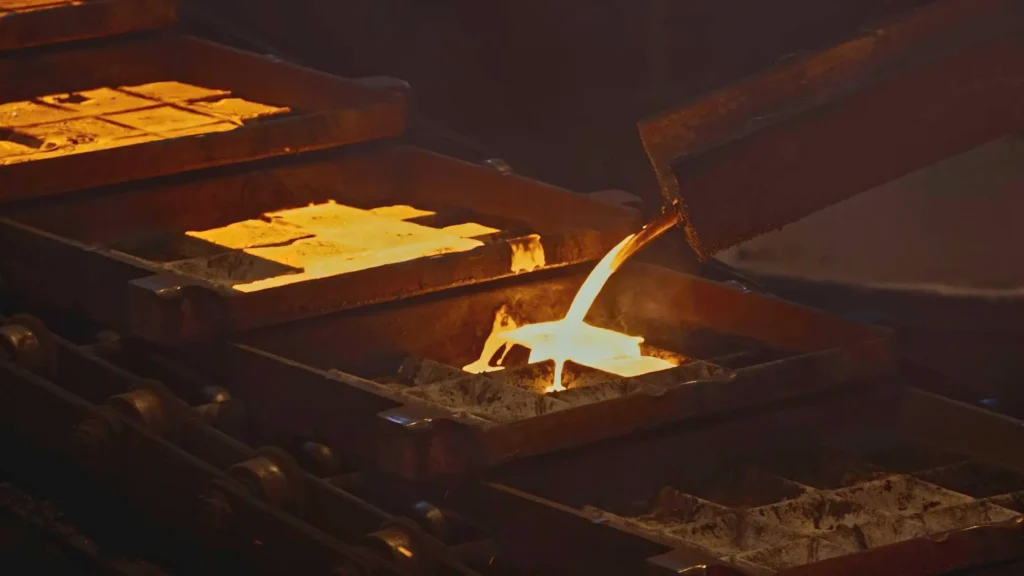
The practice of mixing metals revolutionized metal casting by enhancing the properties of metals, making them stronger, more resistant to corrosion, and easier to work with. This transformative process remains essential in modern metallurgy.
Historical Alloying: The Bronze Age Breakthrough
- The first significant alloy was bronze, a mixture of copper and tin, marking the start of the Bronze Age.
- Impact: Stronger and more versatile than pure copper, bronze was used for weapons, tools, and sculptures, enabling societal and technological advances.
At the heart of sand casting lies the transformative process of melting metal, turning solid ingots or scraps into a fiery liquid form ready to take on a new identity. This stage is where raw materials are prepped to become intricate parts of machinery, beautiful sculptures, or essential everyday tools. Let’s explore the critical aspects of melting metal, from selecting the right type of metal to understanding the intricacies of the melting process and the final adjustments before the pour.
Overview of Metal Selection
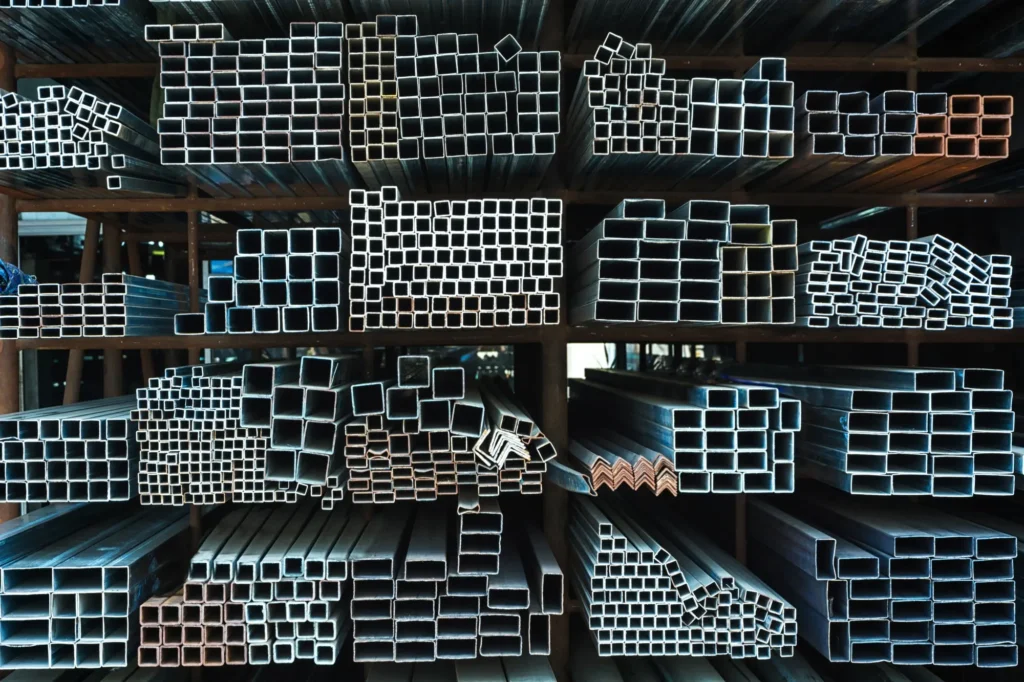
The choice of metal is pivotal and depends on the desired properties of the final cast product. Each metal or alloy offers a unique combination of strength, ductility, corrosion resistance, and thermal conductivity. The most commonly used metals in sand casting include:
- Iron: Renowned for its strength and durability, iron is often used in automotive and machinery components.
- Aluminum: Known for its lightweight and corrosion resistance, aluminum is favored in aerospace and automotive industries.
- Bronze: Valued for its excellent corrosion resistance and aesthetic appeal, bronze is commonly used in sculptures and marine hardware.
The selection process involves considering the application’s requirements and balancing them with cost and material properties to choose the most suitable metal.
The Melting Process
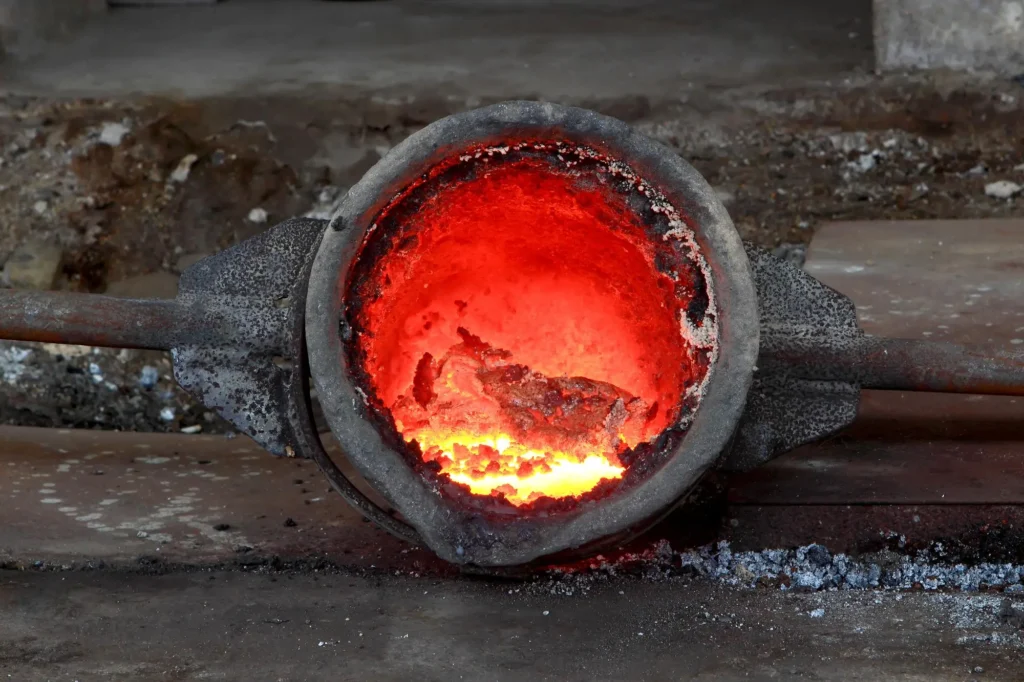
Melting metal is a complex operation that demands precision and safety. The process varies depending on the metal, but the fundamentals remain the same. Here’s a breakdown:
- Furnaces Used: Different types of furnaces are employed based on the metal’s melting point and the volume of metal needed. Common furnaces include cupola furnaces for iron, electric arc furnaces for steel, and induction furnaces for a variety of metals. Each offers advantages in efficiency, temperature control, and environmental impact.
- Safety Measures: Melting metal involves extremely high temperatures, necessitating strict safety protocols to protect workers. Personal protective equipment (PPE), such as heat-resistant gloves, face shields, and aprons, are essential. Proper ventilation and training in handling molten metal are also critical to prevent accidents.
- Automated ladle systems to minimize manual handling.
- Use of advanced PPE (heat-resistant suits, insulated face shields).
Metal Melting Defects and Their Prevention
Metal melting is a precise process, but defects can arise if certain precautions are not taken. These defects can compromise the quality, strength, and appearance of the final casting.
Common Melting Defects:
- Gas Porosity: Caused by dissolved gases like hydrogen being trapped during solidification.
- Slag Inclusion: Non-metallic impurities mixed into the molten metal.
- Oxidation: Formation of oxide layers when molten metal reacts with oxygen.
- Cold Shuts: Premature solidification of metal due to improper pouring.
Prevention Methods:
- Degassing: Use inert gases like argon or nitrogen to remove dissolved gases.
- Fluxing: Add flux materials to absorb impurities and bring them to the surface for skimming.
- Controlled Pouring: Maintain proper pouring temperature and reduce turbulence.
- Clean Charge Materials: Pre-cleaning ingots and scrap reduces impurities.
Types of Melting Furnaces and Their Applications
- Cupola Furnace:
- Description: A traditional furnace used mainly for melting cast iron.
- How It Works: Coke is used as fuel to reach high temperatures. Metal is charged at the top, while slag is removed from the bottom.
- Advantages: Economical, ideal for large volumes of iron casting.
- Induction Furnace:
- Description: Uses electromagnetic induction to melt metals.
- Applications: Melting ferrous and non-ferrous metals for precision casting.
- Advantages: Energy-efficient, precise temperature control, and low environmental impact.
- Electric Arc Furnace (EAF):
- Description: Used for steel production. Electrodes generate heat to melt scrap metal.
- Advantages: Suitable for recycling scrap metal and producing high-quality alloys.
- Crucible Furnace:
- Description: Small-scale furnace where metal is melted in a crucible.
- Applications: Ideal for smaller volumes, prototyping, or precious metals like bronze.
Preheating and Maintaining Furnace Lining
Furnace lining plays a vital role in maintaining temperature consistency and extending furnace life.
- Preheating: Linings must be preheated gradually to avoid thermal shock, which can cause cracks or uneven heat distribution.
- Maintenance: Regular checks for erosion, wear, or slag buildup are essential.
- Replacement: Use high-quality refractory materials to withstand molten metal temperatures and avoid contamination.
- Temperature Control: Precise temperature control is crucial for achieving the desired metal properties. Each metal and alloy has an optimal pouring temperature to ensure it fills the mold cavity correctly without premature solidification or creating defects.
Factors Influencing the Quality of Molten Metal
- Cleanliness of Charge Materials:
- Impurities in ingots or scrap can affect the quality of the final casting. Pre-cleaning the charge material is essential.
- Proper Alloying Ratios:
- Ensuring the correct ratio of base metal and alloying elements to achieve desired strength, corrosion resistance, and machinability.
- Degassing Methods:
- Techniques like inert gas injection (e.g., argon or nitrogen) to eliminate gas porosity.
- Fluxing Agents:
- Chemicals added to molten metal to remove non-metallic inclusions or slag, improving surface finish and reducing defects.
Measuring and Monitoring Melt Quality
Quality assurance during melting ensures the final casting meets required specifications.
- Chemical Analysis: Use spectrometers to measure alloy composition in real time.
- Temperature Sensors: Infrared thermometers and thermocouples monitor precise melting and pouring temperatures.
- Density Testing: Check for gas porosity using density measurements.
These measures reduce defects and ensure molten metal meets performance standards.
Alloying and Treatment
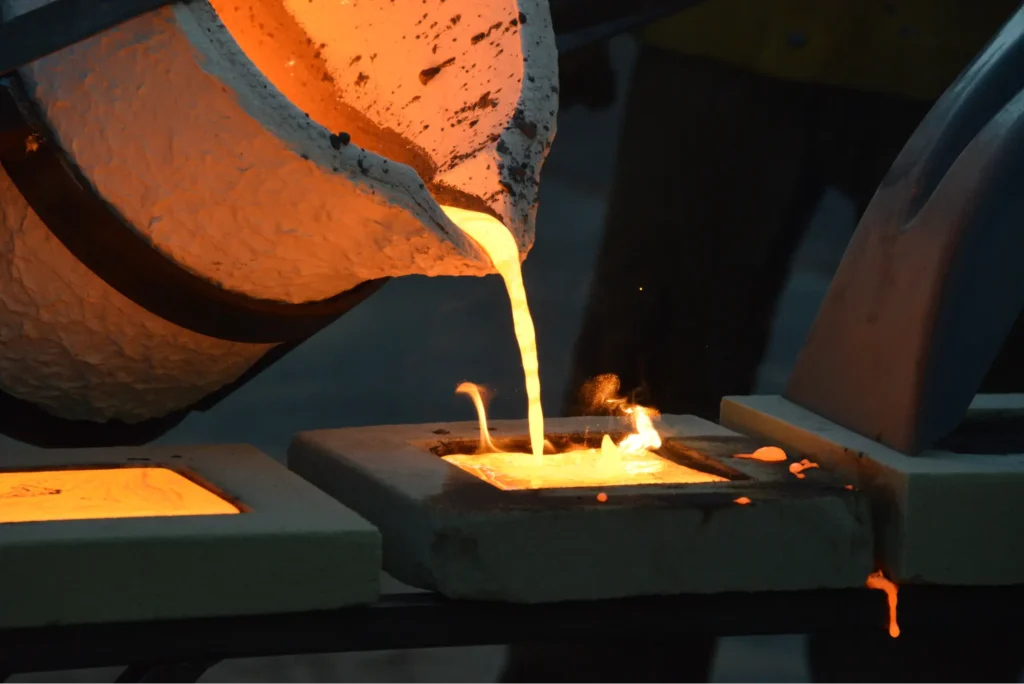
The composition of the metal significantly influences the properties of the final casting. Adjustments can be made during the melting process to achieve the desired characteristics:
- Alloying: Adding specific elements to the base metal can enhance its strength, ductility, or corrosion resistance. For instance, adding chromium and nickel to steel improves its stainless properties, while adding silicon to aluminum can increase its casting ability.
- Treatment: Metal treatments, such as degassing or fluxing, are often performed to improve the quality of the melt. Degassing removes dissolved gases that could cause porosity in the casting, and fluxing cleans the metal by removing impurities to the surface, where they can be skimmed off.
Modern Alloying Techniques
- Micro-Alloying: Adding trace elements such as vanadium or niobium enhances hardness and corrosion resistance.
- Steel Production: Combining iron with carbon produces steel, known for its strength and flexibility. Stainless steel, with added chromium and nickel, resists corrosion and oxidation.
- Aluminum Alloys: Adding magnesium, silicon, or zinc creates lightweight, strong alloys used in aerospace and automotive industries.
The Alloying Process: How It’s Done
- Melting and Blending: Metals are heated in a furnace until molten, allowing for even mixing.
- Chemical Adjustments: Elements are added in precise amounts based on desired mechanical and chemical properties.
- Solidification and Casting: Once mixed, the alloy is poured into molds to form ingots or complex components
Heat Treatments Post-Casting:
After pouring and cooling, alloys can be heat-treated to refine grain structures:
- Annealing: Reduces internal stress and improves ductility.
- Tempering: Enhances toughness by reducing brittleness.
- Quenching: Rapid cooling to increase hardness.
Mold Coatings for Improved Casting Quality
Mold coatings enhance surface finish and reduce casting defects:
- Types of Coatings:
- Graphite-based coatings: For smoother surfaces.
- Zircon-based coatings: High thermal resistance for larger or complex molds.
- Applications: Applied as a wash or spray before pouring to create a non-reactive layer between molten metal and sand.
This reduces surface roughness and minimizes metal-sand reactions.
Environmental and Sustainability Considerations
- Recycling Scrap Metal:
- Importance of using recycled materials to reduce production costs and environmental impact.
- Energy Efficiency:
- Comparing energy consumption of different furnaces (induction vs. cupola).
- Emission Control:
- Technologies like fume extraction systems and slag recycling.
Comparison of Sand Casting Melting with Other Processes
Melting and pouring techniques vary across different casting processes. Here’s how sand casting compares:
Feature | Sand Casting | Investment Casting | Die Casting |
Precision | Moderate | High | Very High |
Cost | Low to moderate | Moderate to high | High |
Volume | Low to high (flexible) | Low to medium | High (mass production) |
Material Variety | Wide range of metals | Mostly non-ferrous metals | Limited (mainly aluminum/zinc) |
Sand casting is versatile and cost-effective, making it ideal for both small and large-scale production runs.
By carefully selecting the metal, mastering the melting process, and fine-tuning the composition, casters ensure the molten metal is perfectly primed for its transformation into a solid, new form within the sand mold. This pivotal phase not only shapes the metal’s destiny but also reflects the profound skill and understanding behind the ancient craft of sand casting.