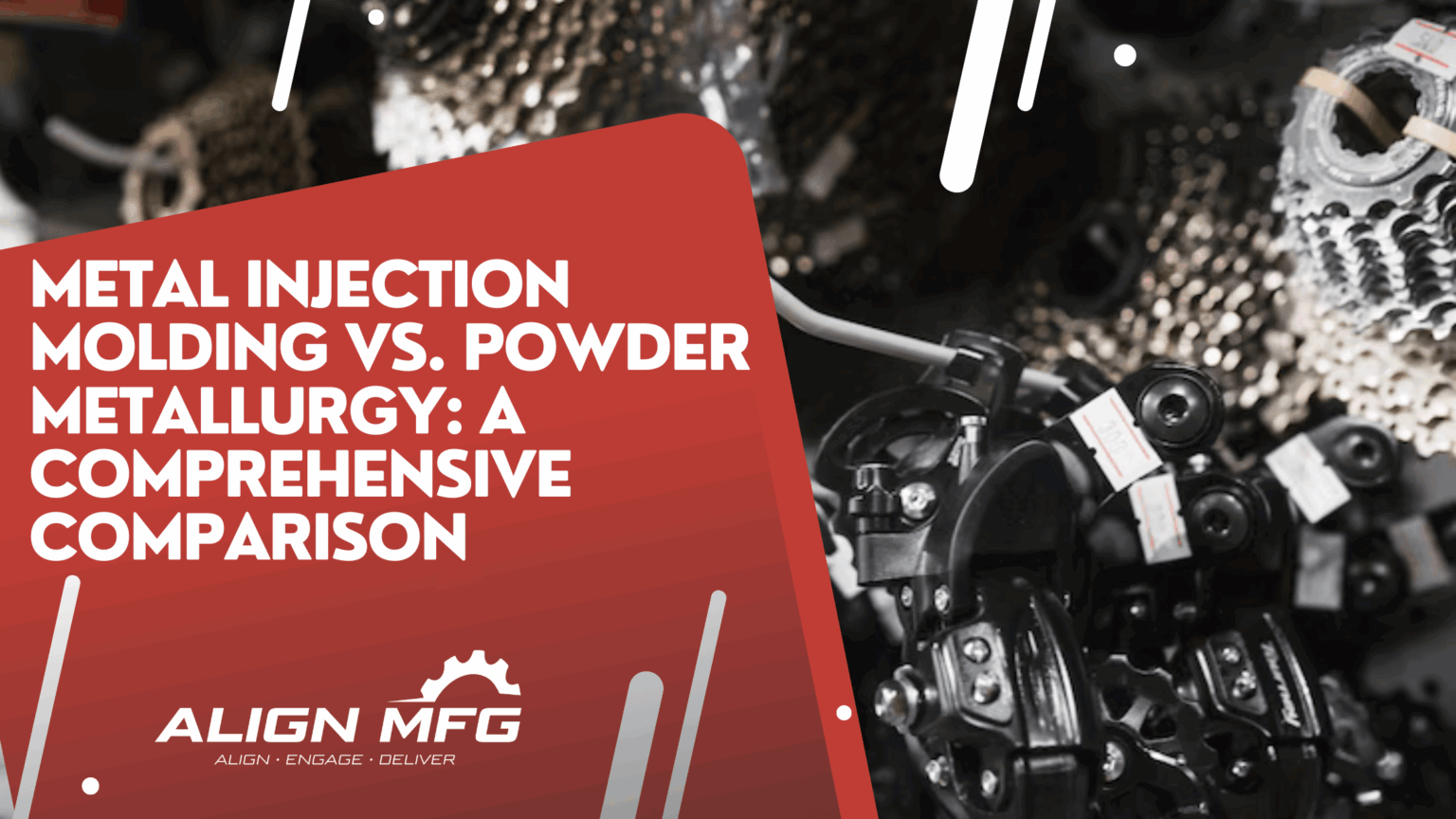
Metal Injection Molding vs. Powder Metallurgy: A Comprehensive Comparison
In the realm of metal part manufacturing, Metal Injection Molding (MIM) and Powder Metallurgy (PM) stand out as two prominent techniques. Both processes utilize metal powders to fabricate components, yet they differ significantly in methodology, capabilities, and applications. Understanding these differences is crucial for engineers and manufacturers aiming to select the most suitable process for their specific needs.
Manufacturing Processes
Metal Injection Molding (MIM)
MIM is a hybrid manufacturing process that combines the versatility of plastic injection molding with the strength and integrity of powdered metallurgy. The process involves several key steps:
- Feedstock Preparation: Fine metal powders, typically less than 20 microns in size, are mixed with thermoplastic and wax binders to create a homogeneous feedstock.
- Injection Molding: The feedstock is heated and injected into molds to form “green parts,” which are near-net-shape components.
- Debinding: The binder materials are removed through thermal or solvent processes, resulting in “brown parts” that are porous and fragile.
- Sintering: The brown parts are heated to temperatures just below the melting point of the metal, causing the particles to fuse and densify, achieving final mechanical properties.
MIM is particularly advantageous for producing small, intricate parts in high volumes, offering excellent surface finish and dimensional accuracy.
Powder Metallurgy (PM)
PM is a traditional process that involves the following steps:
- Powder Production: Metal powders are produced through various methods, including atomization, reduction, and electrolysis.
- Blending: Different metal powders and additives are mixed to achieve desired properties.
- Compaction: The powder blend is compressed in a die under high pressure to form a “green compact.”
- Sintering: The green compact is heated in a controlled atmosphere to bond the particles metallurgically, enhancing strength and integrity.
PM is well-suited for producing simple, high-volume parts with consistent properties, often used in automotive and industrial applications.
Material Characteristics
Density and Porosity
- MIM: Achieves high-density parts, typically ranging from 95% to 99% of theoretical density, resulting in superior mechanical properties.
- PM: Generally results in parts with 80% to 90% density, which may be beneficial for applications requiring porosity, such as self-lubricating bearings.
Mechanical Properties
- MIM: Offers excellent mechanical strength, comparable to wrought materials, making it suitable for demanding applications.
- PM: While adequate for many applications, PM parts may exhibit lower strength due to inherent porosity.
Material Utilization
- MIM: Utilizes fine powders and achieves near-net-shape parts, minimizing material waste.
- PM: Also efficient in material usage, especially for simple geometries, but may require additional machining for complex features.
Cost Analysis
When evaluating manufacturing processes, cost considerations play a pivotal role. Both Metal Injection Molding (MIM) and Powder Metallurgy (PM) have distinct cost structures influenced by factors such as material expenses, tooling, production volume, and post-processing requirements.
Material Costs
- MIM: Utilizes fine metal powders combined with polymer binders, resulting in greater material costs. MIM feedstock can cost approximately $10–$12 per pound or higher.
- PM: Employs coarser metal powders without binders, making it more economical. PM materials typically cost around $1–$2 per pound.
Tooling and Equipment
- MIM: Requires specialized injection molding machines, debinding ovens, and sintering furnaces. The complexity of molds for intricate parts leads to higher tooling costs.
- PM: Involves simpler compaction dies and sintering equipment, resulting in lower initial tooling investments.
Production Volume and Economies of Scale
- MIM: Becomes cost-effective at high production volumes due to the amortization of tooling costs over large quantities.
- PM: Suitable for medium to high-volume production, especially for parts with simpler geometries.
Post-Processing Requirements
- MIM: Produces near-net-shape parts with excellent surface finish and dimensional accuracy, often eliminating the need for secondary operations.
- PM: May require additional machining or finishing processes to achieve desired tolerances and surface quality.
Applications and Industry Usage
The choice between MIM and PM often depends on the specific requirements of the application, including part complexity, mechanical properties, and production volume.
Metal Injection Molding (MIM)
Industries and Applications:
- Medical and Dental: Production of surgical instruments, orthodontic brackets, and implant components requiring high precision and biocompatibility.
- Aerospace: Manufacture of complex components like fittings, latches, and spray nozzles that demand high strength-to-weight ratios.
- Automotive: Creation of intricate parts such as fuel injector components, actuators, and locking mechanisms.
- Consumer Electronics: Fabrication of small, complex parts like connectors and housings with tight tolerances.
Powder Metallurgy (PM)
Industries and Applications:
- Automotive: Production of gears, bushings, and structural components where cost-effectiveness and material efficiency are paramount.
- Industrial Machinery: Manufacture of components like bearings and filters that benefit from the inherent porosity of PM parts.
- Aerospace: Creation of structural parts where simplicity and reliability are essential.
- Appliances and Tools: Fabrication of various components where high-volume production and cost savings are critical.
Advantages and Limitations
Understanding the strengths and weaknesses of both Metal Injection Molding (MIM) and Powder Metallurgy (PM) is crucial for selecting the appropriate manufacturing process for specific applications.
Metal Injection Molding (MIM)
Advantages:
- Complex Geometries: MIM excels at producing intricate and complex shapes that would be challenging or impossible with other manufacturing methods. This capability is due to the flexibility of the injection molding process, allowing for detailed features and thin walls.
- High Density and Strength: MIM parts typically achieve densities of 95–99% of theoretical density, resulting in mechanical properties comparable to wrought materials. This high density contributes to superior strength and durability.
- Excellent Surface Finish: The process yields parts with smooth surface finishes, often eliminating the need for secondary machining or finishing operations.
- Material Utilization: MIM generates minimal waste, utilizing nearly all the material in the final product, which is both cost-effective and environmentally friendly.
Limitations:
- High Initial Tooling Costs: The molds required for MIM are often expensive, especially for intricate designs, making the process more suitable for high-volume production to amortize the tooling investment.
- Size Constraints: MIM is generally limited to small to medium-sized parts, typically less than 100 grams, due to equipment limitations and the nature of the process.
- Material Limitations: Not all metals are suitable for MIM. Some materials may not sinter well or may have issues with binder removal, limiting the range of applicable materials.
Powder Metallurgy (PM)
Advantages:
- Cost-Effective for Simple Parts: PM is highly economical for producing simple, high-volume parts, especially when complex geometries are not required.
- Material Efficiency: The process utilizes over 97% of the starting material, minimizing waste and making it an environmentally friendly manufacturing option.
- Controlled Porosity: PM allows for the production of parts with controlled porosity, which is beneficial for applications like self-lubricating bearings and filters.
- Energy Efficiency: PM typically requires lower processing temperatures than other metal forming methods, leading to energy savings during production.
Limitations:
- Design Limitations: PM is generally limited to simpler shapes due to the constraints of the compaction process. Complex geometries may require additional machining or alternative manufacturing methods.
- Lower Density and Strength: PM parts often have lower densities at about 80–90% of theoretical density compared to MIM, which can result in reduced mechanical strength and a possibility that it may not be suitable for high-stress applications.
- Size Limitations: There are practical limits to the size of parts that can be produced using PM, often constrained by the capacity of the pressing equipment.\
Conclusion
Both metal injection molding and powder metallurgy offer unique advantages and are suited to different applications. MIM is ideal for producing small, complex parts with high strength and excellent surface finishes, making it suitable for industries like medical, aerospace, and electronics. However, it comes with higher initial costs and size limitations. Conversely, PM is cost-effective for manufacturing simple, high-volume parts with controlled porosity, commonly used in automotive and industrial applications. The choice between MIM and PM should be based on factors such as part complexity, required mechanical properties, production volume, and cost considerations. By understanding the strengths and limitations of each process, manufacturers can make informed decisions that align with their production goals and operational needs. Check out Align Manufacturing if you are looking for a place that provides high-precision metal injection molding solutions.