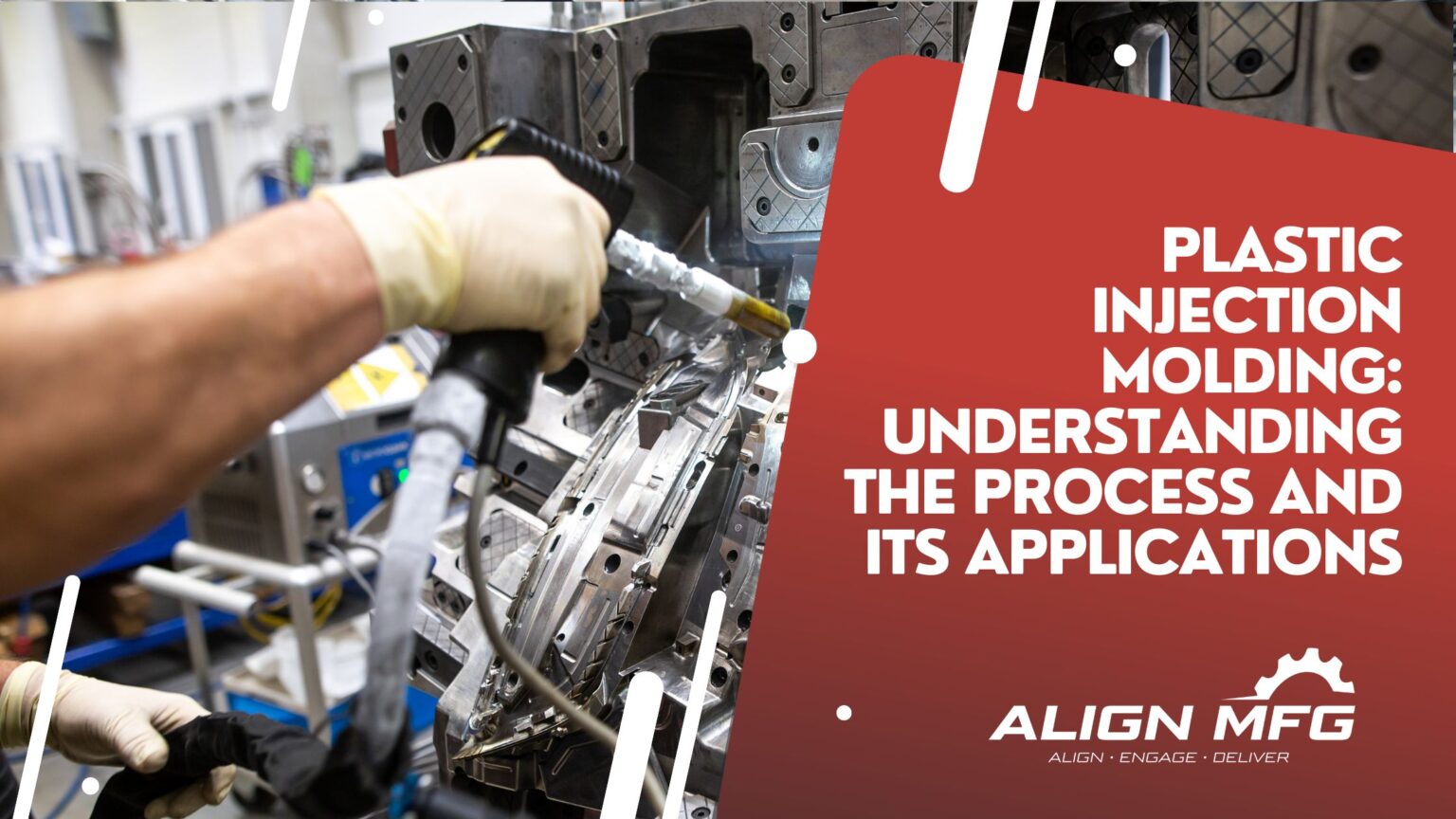
Plastic Injection Molding: Understanding the Process and Its Applications
Plastic is an indispensable part of our daily lives, shaping everything from simple household items to complex medical devices. In this blog post, we'll delve into the basics of plastic injection molding, how it works, and why it's such a crucial technique in modern manufacturing.
What is Plastic Injection Molding?
Plastic injection molding is a manufacturing process used to produce large volumes of identical plastic parts. It involves melting plastic pellets and injecting the molten plastic into a mold under high pressure. Once the plastic cools and solidifies, the mold is opened to release the finished part. This process can be repeated multiple times with an incredibly high level of accuracy and speed, making it ideal for mass production.
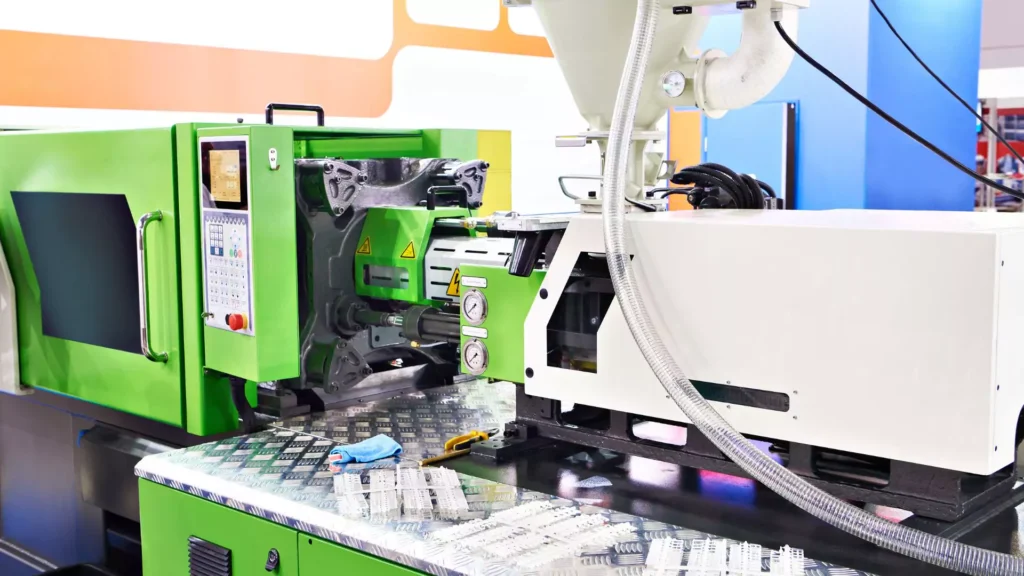
Key Components of Plastic Injection Molding
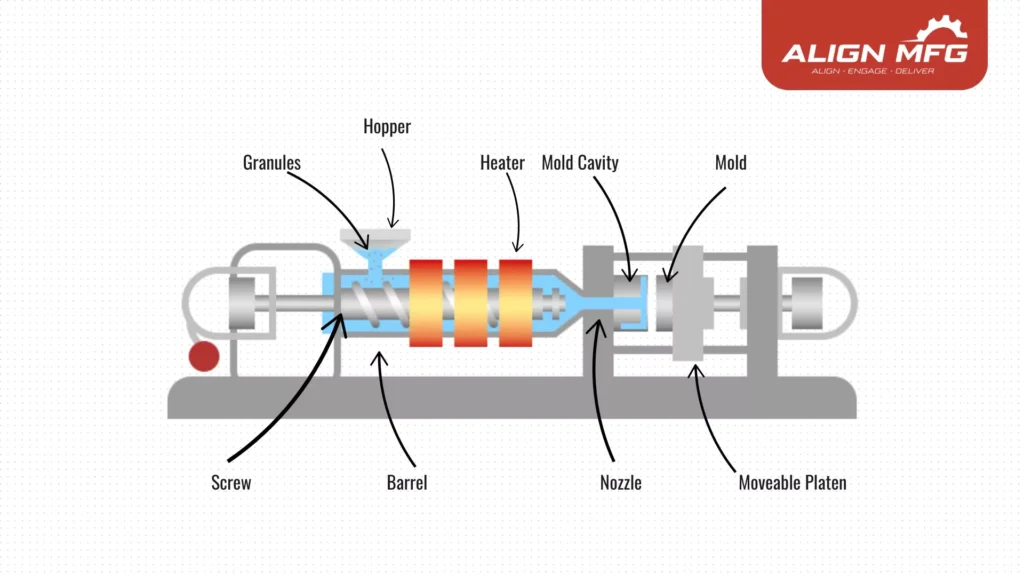
The plastic injection molding process revolves around several key components:
The Injection Molding Machine
At the heart of the injection molding process is the injection molding machine, which consists of two primary components:
- The Injection Unit: This section is responsible for melting the plastic pellets and injecting the molten material into the mold. It features a hopper for feeding the pellets, a barrel for heating, and a screw mechanism that pushes the molten plastic into the mold.
- The Clamping Unit: This part secures the mold during the injection and cooling phases. It ensures that the mold remains tightly closed to prevent any leakage of the molten plastic, which is critical for maintaining the integrity of the final product.
The Mold
Molds are typically crafted from steel or aluminum and are custom-built for each specific project. They can be designed with multiple cavities, allowing for the simultaneous production of several parts in one cycle. The design of the mold is crucial, as it determines the shape, surface finish, and overall quality of the finished product.
Part Name | Function | Details/Insights |
Hopper | Holds and feeds plastic pellets into the barrel. | Often equipped with a dryer to remove moisture, ensuring the quality of the molten plastic. |
Barrel | Heats and melts the plastic pellets into a molten state. | Contains heating bands and uses shear heat from the screw rotation for efficient melting. |
Screw (Reciprocating) | Mixes, melts, and pushes the molten plastic forward into the mold. | Designed to control material flow and ensure uniform melting. |
Nozzle | Directs molten plastic from the barrel into the mold cavity. | May include heaters to maintain consistent flow and avoid cooling before injection. |
Clamp Unit | Holds the mold halves together under high pressure during injection and cooling. | Hydraulic or mechanical clamping systems ensure the mold remains sealed tightly. |
Mold (Fixed and Movable Halves) | Shapes the molten plastic into the desired part. | Consists of a stationary half (attached to the platen) and a movable half (attached to the clamping unit). |
Ejector Pins | Push the cooled, solidified plastic part out of the mold. | Automatically reset for the next injection cycle, ensuring seamless operation. |
Hydraulic System | Powers the clamping and ejection functions. | Operates using hydraulic pressure to move large components like the mold halves efficiently. |
Controller | Manages and monitors machine operations, including temperature, pressure, and cycle timing. | Advanced systems may include touchscreen interfaces and data logging for process optimization. |
Cooling System | Maintains the mold temperature to ensure proper solidification of the plastic. | Uses water or oil circulating through channels within the mold. |
Tie Bars | Provide structural stability to the machine and hold the mold in place during operation. | Commonly found in 4-tie bar configurations for even pressure distribution. |
Injection Unit | Includes the screw, barrel, and nozzle; responsible for injecting molten plastic into the mold cavity. | Controls shot size, injection speed, and pressure. |
Platen (Fixed and Movable) | Supports the mold halves and provides the framework for clamping and ejecting parts. | Movable platen allows for the opening and closing of the mold during cycles. |
Injection Cylinder | Applies high pressure to push the molten plastic into the mold. | Ensures the material completely fills the cavity, even in complex or intricate designs. |
Heater Bands | Surround the barrel to melt the plastic pellets. | Can be individually controlled for precise temperature settings. |
Sprue Bushing | Guides molten plastic from the nozzle into the mold sprue. | Prevents leakage and ensures smooth material flow. |
The Plastic Material
A diverse array of thermoplastics is available to manufacturers, each selected based on the unique properties required for the end product. Commonly used materials include:
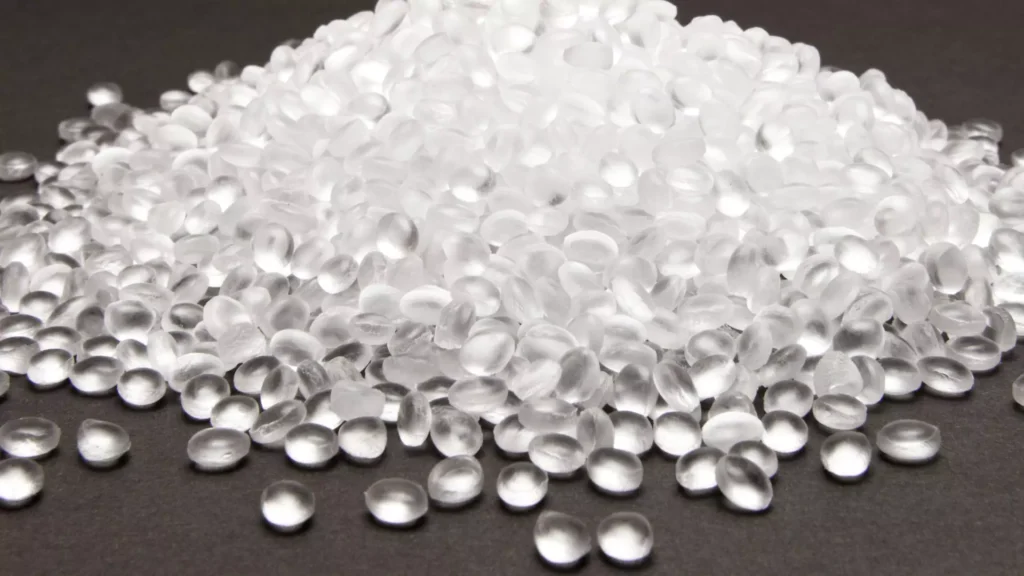
- Acrylonitrile Butadiene Styrene (ABS) : Known for its strength and impact resistance, making it ideal for automotive and consumer products.
- Polycarbonate: Valued for its clarity and heat resistance, often used in applications requiring transparency, such as eyewear lenses.
- Nylon: Recognized for its durability and flexibility, commonly used in automotive and industrial applications.
- Polypropylene (PP) : Lightweight and resistant to chemicals, making it suitable for packaging and consumer goods.
The Injection Molding Process
Plastic injection molding follows a series of steps:
- Step 1: Material Preparation
Plastic pellets are loaded into the hopper, which feeds them into the barrel. Inside the barrel, the reciprocating screw melts the pellets using heat and friction while ensuring uniform mixing. - Step 2: Injection
The molten plastic is pushed forward by the screw under high pressure and forced through the nozzle into the mold cavity. The clamping unit ensures the mold halves are tightly sealed to prevent leaks. - Step 3: Filling and Venting
The molten plastic flows through the sprue, runners, and gates, filling every part of the mold cavity. Trapped air escapes through mold vents, ensuring a flawless part. - Step 4: Cooling and Holding
The mold is kept at a constant temperature to cool the plastic evenly. Holding pressure is applied to prevent backflow and control material shrinkage as the part solidifies. - Step 5: Ejection
Once the plastic has cooled and hardened, ejector pins push the part out of the mold. The platen opens to release the finished part. - Step 6: Repeat
More pellets are automatically fed into the hopper to start the next cycle. The process repeats in a continuous loop, enabling high-speed, efficient production.
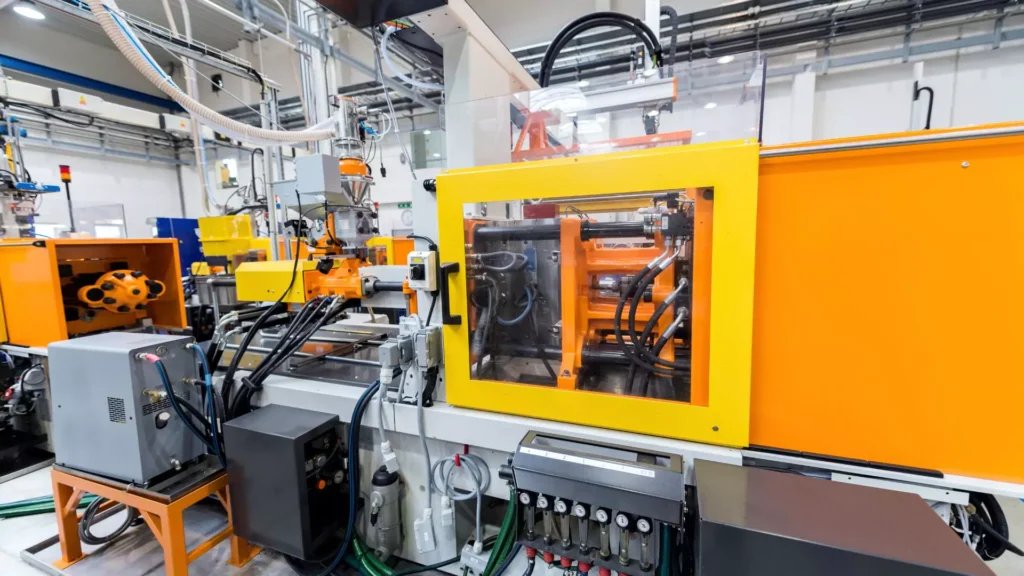
Advantages of Plastic Injection Molding
The popularity of plastic injection molding is due to several compelling advantages:
- Mass Production: One of the strongest benefits is the ability to produce large quantities of parts with consistent quality and tight tolerances.
- Material and Color Flexibility: Manufacturers can choose from a vast array of materials and can easily mix in colors for custom part design.
- Reduced Waste: Excess plastic from the process can often be recycled and reused, minimizing waste.
- Cost-Effectiveness: After the initial cost of designing and creating the mold, the cost per unit during manufacturing is extremely low, especially for high-volume orders.
Disadvantages of Plastic Injection Molding
While plastic injection molding offers many advantages, there are some drawbacks to consider:
- High Initial Costs: The cost of designing and creating molds can be significant, making it less economical for low-volume production runs.
- Limited Design Changes: Once a mold is created, making changes to the design can be costly and time-consuming.
- Material Limitations: Not all plastics are suitable for injection molding, and some materials may require specific conditions or processes.
Applications of Plastic Injection Molding
Plastic injection molding is ubiquitous, finding applications across industries:
1. Automotive Components
Plastic injection molding is widely used in the automotive industry to create components such as dashboards, bumpers, interior trim, and housings for electronic devices. The lightweight nature of molded plastics helps improve fuel efficiency while maintaining strength and durability.
2. Consumer Electronics
Many consumer electronics, including smartphones, tablets, and laptops, incorporate plastic injection-molded parts. This process is used to produce casings, buttons, and internal components that require precision and a high-quality finish.
3. Medical Devices
The medical industry relies on plastic injection molding to manufacture disposable items such as syringes, IV bags, and surgical instruments. The ability to produce sterile, precise, and complex shapes makes this process ideal for medical applications.
4. Household Items
Plastic injection molding is commonly used to create everyday household products, including kitchenware, storage containers, toys, and furniture components. The process allows for mass production of affordable and functional items.
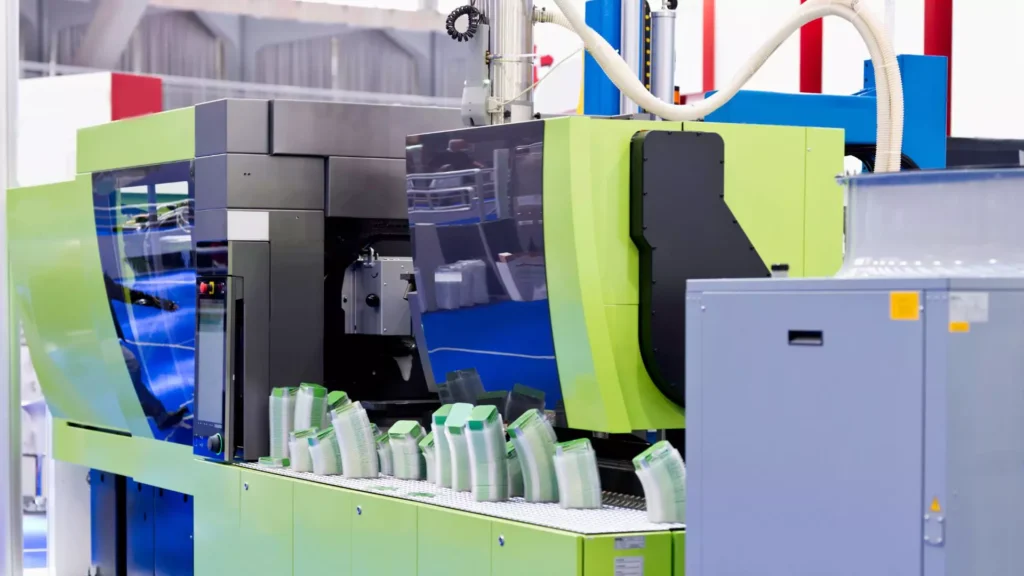
5. Packaging
The packaging industry utilizes plastic injection molding to produce a variety of containers, bottles, and closures. This method allows for the creation of lightweight yet strong packaging solutions that can be tailored to specific product requirements.
6. Industrial Equipment
Many industrial applications use plastic injection-molded components for machinery, tools, and equipment housings. The durability and resistance to chemicals make molded plastics suitable for harsh working environments.
7. Aerospace Parts
In the aerospace sector, plastic injection molding is used to create lightweight, high-strength components that contribute to overall aircraft efficiency. Parts such as interior fittings, housings, and structural elements can be produced using this method.
8. Construction Materials
Plastic injection molding is also employed in the construction industry to manufacture items like window frames, fittings, and fixtures. The versatility of molded plastics allows for innovative designs that meet specific building requirements.
Conclusion
Plastic injection molding is a vital process that continues to evolve with advancements in materials and technology. Its ability to create reliable, uniform parts quickly and cost-effectively makes it a cornerstone of modern manufacturing. As we move towards a future that demands more precision and sustainability, plastic injection molding remains at the forefront, ready to meet the challenges and needs of industries worldwide.
If you’re interested in exploring the potential of plastic injection molding for your projects, consider reaching out to Align Manufacturing.Their team of industry experts can provide valuable insights and solutions tailored to your specific needs. Understanding this manufacturing process opens the door to endless possibilities in product design and production, and Align Manufacturing is well-equipped to help you navigate this landscape
FAQs
Plastic injection molding can utilize a wide variety of thermoplastic materials, including ABS, polycarbonate, nylon, and polypropylene. Each material has unique properties that make it suitable for different applications. For instance, ABS is known for its strength and impact resistance, while polycarbonate is favored for its clarity and heat resistance.
The injection molding process ensures precision through the use of custom-designed molds and high-pressure injection techniques. The molds are engineered to exact specifications, allowing for tight tolerances and consistent part dimensions. This level of accuracy is crucial for industries like automotive and medical, where even minor variations can lead to significant issues.
Learn more about how Align Manufacturing can help you with injection molding here.
- Consider the following factors:
- Part function and requirements: Strength, flexibility, chemical resistance, temperature resistance, etc.
- Aesthetics: Color, finish, transparency.
- Cost: Material cost, processing cost.
- Environmental impact: Recyclability, biodegradability.
- Common mold materials include:
- Steel: Most durable and widely used.
- Aluminum: Lighter and less expensive than steel, but less durable.
- Beryllium copper: Excellent for high-precision parts.