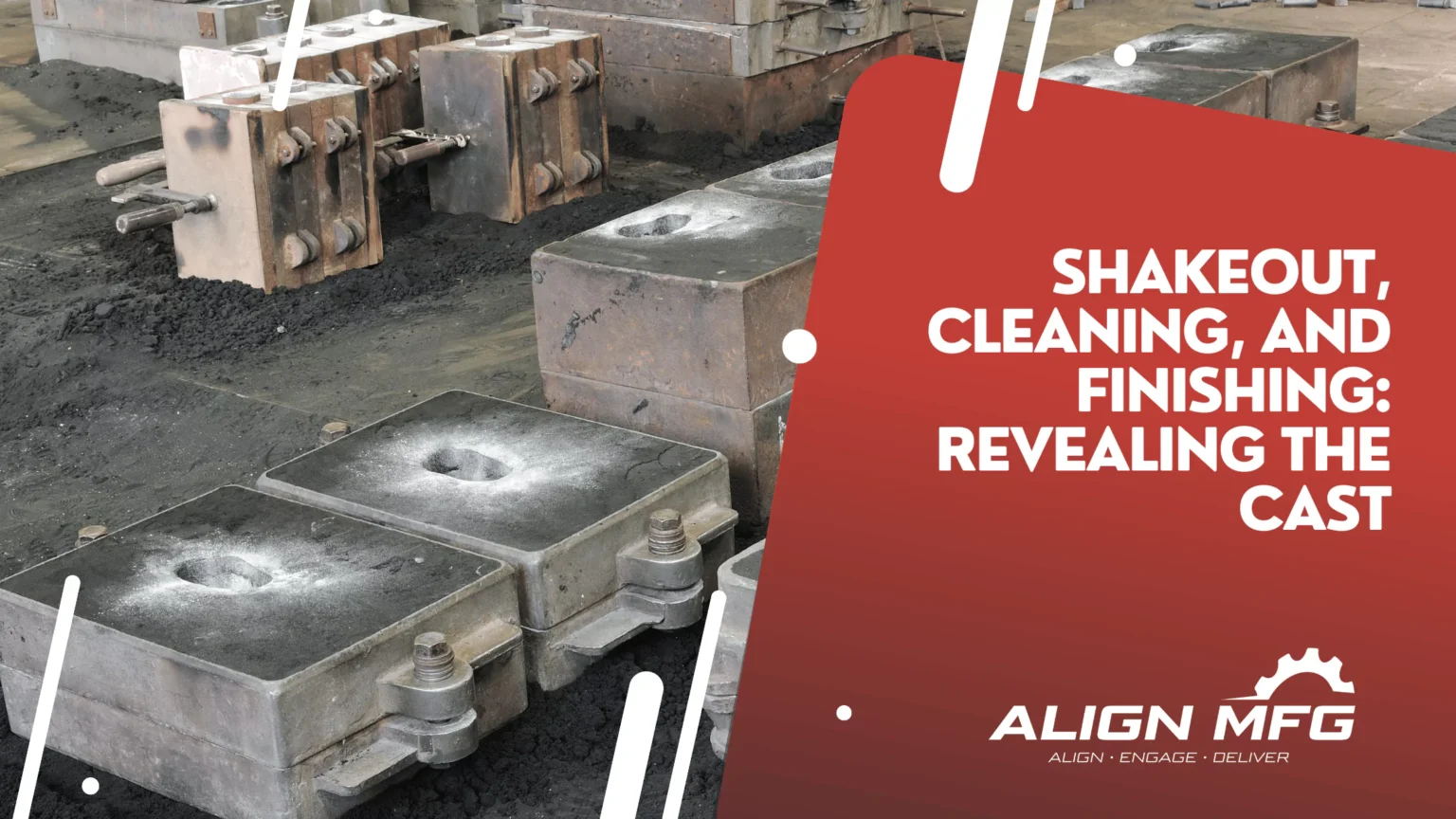
Shakeout, Cleaning, and Finishing: Revealing the Cast
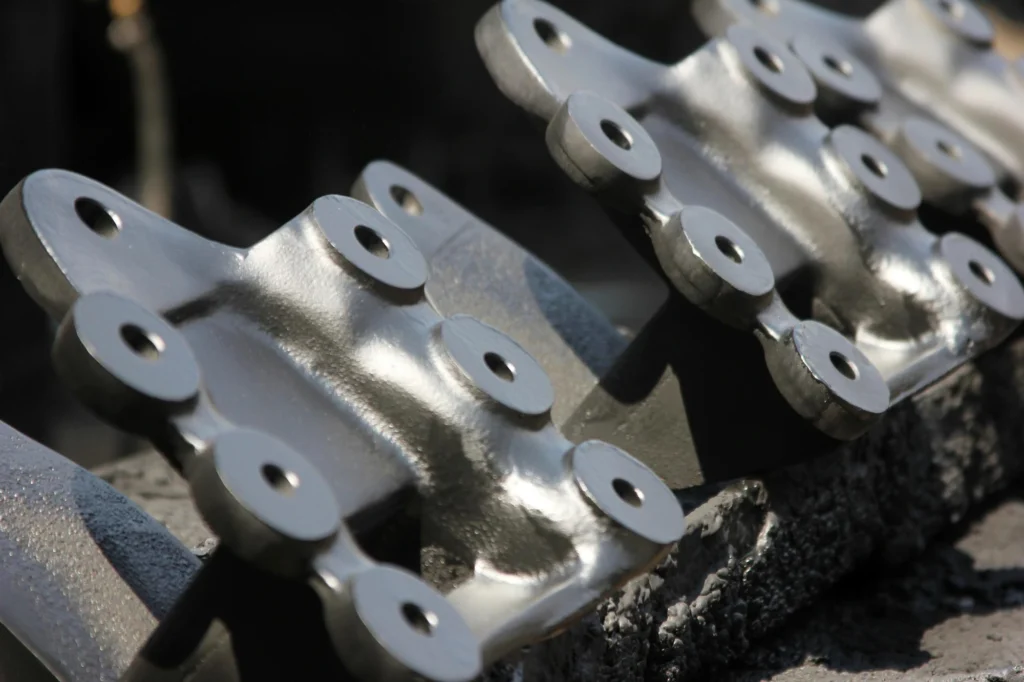
After the metal has cooled and solidified within the mold, the next phase is one of transformation, where the rough cast emerges from its sandy cocoon, ready to undergo the metamorphosis into a finished piece. This phase, comprising the shakeout, cleaning, and finishing processes, is crucial for revealing the cast’s true form and preparing it for its intended function. Let’s explore these steps that take the casting from a raw state to a polished final product.
The Shakeout Process: Separating the Cast Part from the Sand Mold
Shakeout marks the first crucial step in revealing a newly formed metal casting from its sand mold. This process involves carefully breaking apart the mold to uncover the casting, while ensuring the delicate new structure remains intact. The timing of shakeout is critical, as removing a casting too soon can expose it to rapid cooling, leading to undesirable effects such as embrittlement or microstructural changes. For example, in the case of ductile iron, premature exposure to air can alter its balance of pearlite, ferrite, or martensite structures, affecting the final material properties.
Foundries often rely on specific formulas or visual indicators to determine the optimal moment for shakeout. For instance, the greying of ductile iron is a common sign that it has cooled sufficiently to be safely removed.
Once the timing is right, the casting can be separated from the mold through various methods. In smaller foundries, this might involve manual tools such as tongs, where workers carefully lift the casting out of the mold as it crumbles away. In larger operations, automated systems like agitation or vibration tables are typically employed. These tables vigorously shake unflasked molds, causing the sand to detach from the casting and fall through perforated surfaces into collection bins. The reclaimed sand can then be treated and reused for future molds, contributing to sustainable foundry practices.
In some cases, sand molds include internal sand cores, which are used to create hollow sections within the casting. Removing these cores often requires additional methods, such as mechanical agitation, chemical treatment, or heat application, depending on the binder material used in the core construction. This ensures that all residual sand is dislodged and the casting is free from obstructions.
For cores made with chemical binders, additional measures may be necessary. For example, applying solutions of sodium or potassium hydroxide can dissolve certain binders effectively. Similarly, steam, cold water, or other thermal treatments can weaken the core material, facilitating its removal.
Once the core is sufficiently loosened, any remaining sand is typically cleared using a final mechanical step, such as an agitation table or pneumatic hammers. This ensures the casting is thoroughly free of residual material, preserving both the structural integrity and the precision of the design
By the end of the shakeout process, the casting is freed from its sandy cocoon, ready to move on to the next phase of cleaning and finishing. Each step requires a balance of efficiency and care to protect the structural integrity of the freshly unveiled piece.
Cleaning Operations: Fettling, Trimming, and Surface Enhancements
After the casting is removed from its mold, it must undergo a series of cleaning steps to remove residual sand, excess metal, and any imperfections caused during the casting process. This phase is traditionally referred to as fettling and is critical to preparing the casting for subsequent stages such as machining or final finishing.
Key Cleaning Steps in Fettling
- Trimming:
Excess metal, including gates, risers, and flash, is removed during trimming. These protrusions form where molten metal flows through the mold’s channels or leaks at the mold’s seams. Trimming typically involves mechanical cutting tools, such as saws or grinders, to ensure clean edges and a smooth surface. - Shot Blasting and Sandblasting:
To eliminate stubborn sand particles and refine the casting’s surface, abrasive blasting is employed.- Shot Blasting: Small steel balls or iron grit are propelled at high speed to remove scale, flash, and surface impurities. This process not only cleans but also slightly smoothens the surface.
- Sandblasting: Sand or other fine abrasives are directed at the surface under high pressure to dislodge debris and improve texture.
- Surface Treatments:
Additional treatments enhance the casting’s durability and appearance. These may include:- Acid Etching: Applied to clean the surface chemically and prepare it for further finishing.
- Shot Peening: Strengthens the metal by imparting compressive stress, enhancing fatigue resistance.
- Removing Flashing and Burrs:
Thin layers of excess metal, known as flashing, often form along the parting lines of the mold. Burrs, which are small, sharp protrusions, can also appear. These imperfections are carefully ground or filed away to ensure the casting is safe and functional. - Use of Tumblers and Automated Systems:
Castings may be placed in rotating tumblers or conveyors to be cleaned more thoroughly. In these systems, the components are agitated while abrasives like steel shot or air-blasting systems target hard-to-reach areas. - Final Fettling and Inspection:
After primary cleaning, fettling continues with detailed inspection and touch-ups. Pneumatic hammers or grinders may be used for intricate areas. At this stage, the casting is checked for surface flaws and dimensional accuracy.
Importance of Fettling in High-Quality Castings
Fettling transforms the rough, freshly cast metal into a refined and functional component. By removing imperfections and ensuring clean, smooth surfaces, this process plays a crucial role in meeting industry standards and preparing castings for specialized applications, whether in automotive, aerospace, or industrial machinery.
Incorporating Water Blasting in Cleaning Operations
In addition to traditional methods like shot blasting and tumbling, water blasting is another effective cleaning technique for castings. This method utilizes high-pressure water jets to clean the casting’s surface, often referred to as hydroblasting.
How Water Blasting Works
- Pressure Washing:
At its core, water blasting involves directing powerful streams of water at the casting. This pressure effectively removes residual sand, scale, and other surface impurities. - Abrasive-Enhanced Hydroblasting:
In advanced systems, abrasive materials like fine grit or beads are added to the water stream. This combination enhances the cleaning action, making it suitable for removing tougher contaminants and providing a finer surface finish. - Advantages:
- Eco-Friendly: Water blasting reduces the reliance on chemical cleaning agents and abrasives, making it an environmentally friendly option.
- Gentle on Castings: Unlike some abrasive methods, hydroblasting minimizes the risk of damaging delicate features or intricate details on the casting.
- Versatility: Suitable for a wide range of metals and casting types, from aluminum to steel.
- Applications:
Water blasting is often used in industries requiring high-quality finishes, such as aerospace or medical equipment manufacturing, where cleanliness and surface integrity are critical.
Role in the Cleaning Process
Water blasting can either be a primary cleaning step for delicate castings or a supplementary process after traditional methods like shot blasting. Following hydroblasting, castings may undergo inspection or additional surface treatments to achieve the desired finish.
By integrating modern water-blasting techniques, foundries can enhance efficiency, improve the casting’s surface quality, and reduce environmental impact.
Removing Gates and Risers
Gates and risers, essential features for directing molten metal through the mold, often leave behind excess material that must be removed during the cleaning process. Unlike smaller imperfections, these larger sections are too substantial to be dislodged through tumbling or air blasting.
Methods for Removal
- Oxy-Acetylene Torches:
High-temperature torches effectively cut through thick sections of excess metal, providing a precise and efficient removal method. - Chipping and Hammering:
Foundry workers may use tools like chipping hammers or sledges to physically break off gates and risers. This method is often employed for larger or more rugged castings. - Sawing:
Saws equipped with durable blades can trim excess stock, especially when precision is required. This is common for castings that demand detailed finishing. - Machining Integration:
In some cases, gates and risers are left for removal during the machining stage. This allows the removal process to be integrated with fine-tuning the part’s dimensions and surface quality, reducing redundancy in operations.
Recycling Removed Material
The metal trimmed from gates and risers is highly valuable. Unlike raw scrap, this material has already undergone purification during the casting process, as gases and impurities, such as paint or oil, are burned off in the furnace. This ensures the recycled metal is of superior quality, helping foundries maintain consistent material standards while minimizing waste.
Machining for Precision
Sand casting often produces surfaces that are rough and lack tight dimensional tolerances. To meet specific standards, additional machining is required.
Purpose of Machining
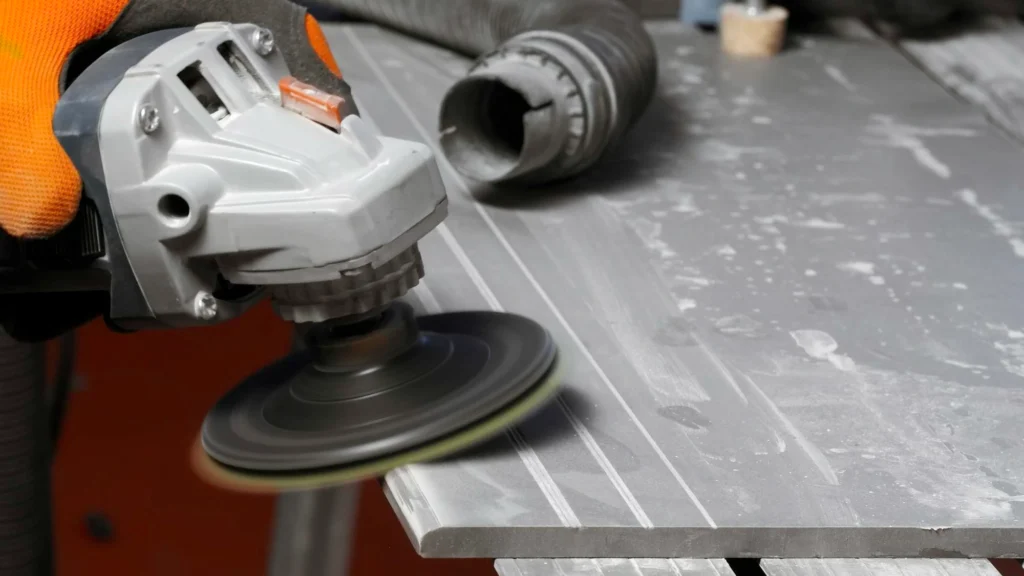
- Surface Finishing:
Machining creates a smoother surface, essential for parts that require aesthetic appeal or functional precision. - Dimensional Accuracy:
Tight tolerances are achieved through techniques like grinding, lathing, or milling. These methods ensure the part fits seamlessly with other components in assemblies. - Cost-Effective Design:
Since machining is costly, foundries aim to cast parts as close to the final shape as possible, minimizing the amount of material that requires machining. This reduces both time and expense while maintaining high-quality results.
By carefully removing gates and risers and employing machining only where necessary, foundries strike a balance between efficiency, cost, and precision, ensuring the castings meet exact specifications.
Finishing Touches: Machining, Painting, or Coating for Aesthetic and Functional Purposes
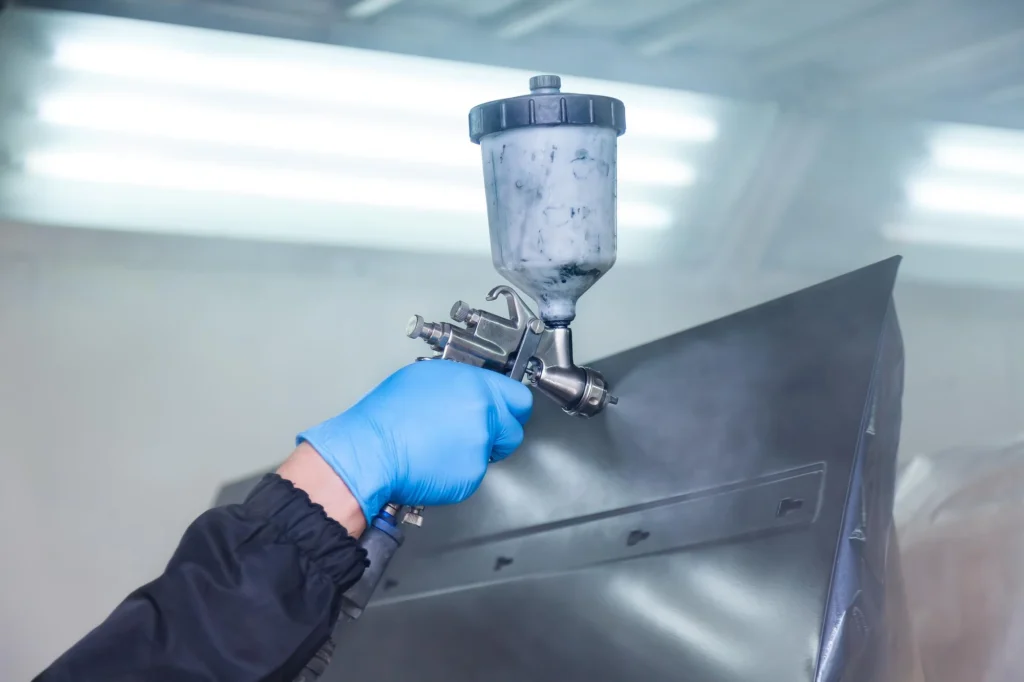
The final step in the casting process is finishing, where the cast part is refined to meet the precise specifications required for its intended use. This can involve a variety of processes, tailored to the demands of the final product:
- Machining: Precision machining is often necessary to achieve the exact dimensions and tolerances needed for the casting to function as designed. Processes like milling, drilling, and turning are used to refine the shape and size of the part.
- Painting or Coating: For aesthetic enhancement or to provide a protective layer against corrosion, castings may be painted or coated with various materials. This can range from simple paint applications to complex chemical coatings designed to withstand extreme environments.
- Quality Inspection: Finally, the casting undergoes a thorough inspection to ensure it meets all quality standards and specifications. This may include visual inspection, dimensional measurement, and non-destructive testing methods.
Real Life Examples
High-quality castings play a pivotal role in industries like automotive, where engine blocks and transmission housings must meet precise specifications. Similarly, in aerospace, turbine blades and structural components require exceptional durability and precision. For example, the aerospace industry often uses investment casting to produce lightweight yet robust components for jet engines.
Finishing technology is undergoing a revolution, with robotics and artificial intelligence transforming processes like machining and cleaning. For example, automated robotic grinders ensure precision in trimming and reduce manual labor. AI-powered systems are used for quality inspection, identifying defects with unmatched accuracy.
Sustainability in Foundries
Foundries today are adopting eco-friendly practices to reduce waste and improve efficiency. Sand reclamation systems, for instance, allow foundries to recycle up to 90% of their sand, reducing the environmental footprint. Additionally, advancements in closed-loop water systems minimize water waste, making foundries more sustainable.
Some foundries are also exploring green technologies like bio-based binders instead of synthetic chemicals for sand cores, lowering emissions and reducing reliance on fossil fuels.
Through the meticulous processes of shakeout, cleaning, and finishing, the casting is transformed from a rough, sand-encrusted object into a precise, polished component, ready to take its place in the world. This journey from mold to masterpiece underscores the blend of brute force and delicate precision that defines sand casting.
During the first production run, castings at this stage often serve as prototypes for clients or designers to assess for aesthetics and functionality. These prototypes provide crucial insight into the product’s viability and whether any design flaws need to be addressed.Align Manufacturing plays a key role ensuring that the final components meet the exact specifications and client expectations, making any necessary adjustments to improve the product before moving forward with full production.