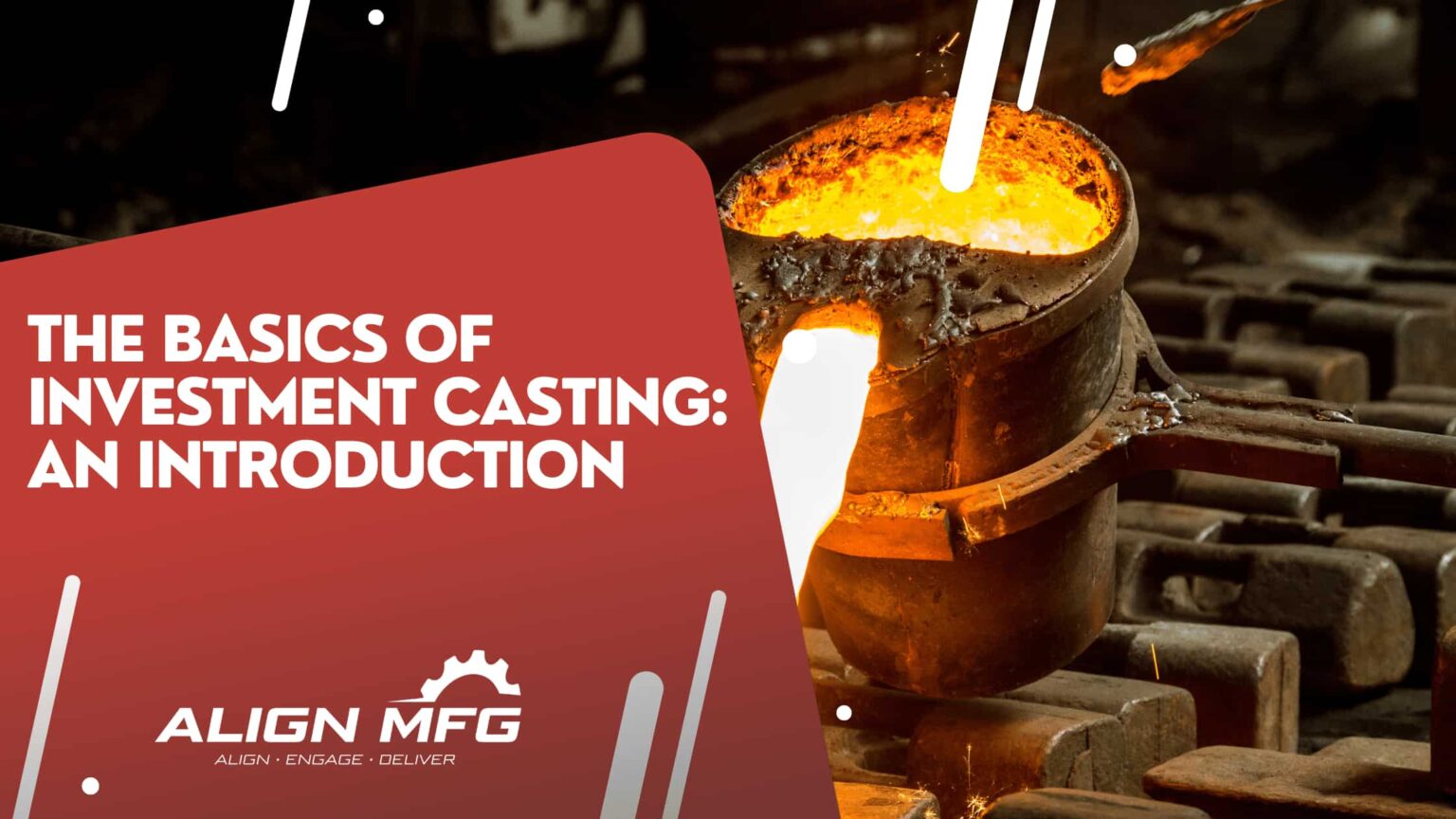
The Basics of Investment Casting: An Introduction
Investment casting, also referred to as precision casting, is a method for crafting detailed and high-quality metal parts with excellent accuracy and smooth finishes. It’s utilized in sectors such as aerospace, automotive, healthcare, and defense.
This technique offers multiple benefits, including the capability to fabricate complex and intricate designs that might be challenging or unachievable with other manufacturing processes. It also delivers high dimensional accuracy, as the mold faithfully reproduces the details of the die. Additionally, the method allows for fine surface finishes, reducing the need for further machining.
How Investment Casting Works
The investment casting process involves creating a wax pattern, encasing it with a ceramic material, and then heating it to remove the wax, leaving behind a mold. Molten metal is then poured into this mold, which solidifies to form the desired metal object.
Understanding the Step-by-Step Investment Casting Process
Step-by-Step Breakdown:
- Creating the Wax Pattern: The process begins by shaping a wax pattern of the part to be cast. This can be done by injecting wax into a metal mold or by sculpting the wax by hand. The wax model is then attached to wax sprues, which act like channels guiding the liquid metal during the casting.
- Building the Ceramic Shell:The wax pattern attached to sprues is dipped into a ceramic slurry followed by a coating of ceramic particles. This step is repeated multiple times to build a thick ceramic shell around the wax. Each layer must dry thoroughly before the next is applied.
- Melting Out the Wax:Once the ceramic shell is sufficiently thick, it is heated in a furnace. This step melts the wax inside the shell, which is then drained out, leaving a hollow ceramic mold that mirrors the original wax pattern.
- Pouring the Molten Metal:The ceramic mold is preheated to prepare for metal casting. Metal is melted in a crucible and then poured into the hot ceramic mold through the sprues.
- Removing the Ceramic Shell:After the metal has cooled and solidified, the ceramic mold is broken away, revealing the metal part. Sprues are cut off, and any remaining ceramic fragments are cleaned off the metal.
Further Steps to Perfect the Casting:
- Refining Wax Patterns:The accuracy of the wax patterns is crucial as they directly influence the final metal part’s details. Techniques like hand carving, using steel tools, or 3D printing are employed based on the complexity and quantity needed. Each method offers different benefits, from artisanal detail to consistent mass production.
- Setting Up the Wax Assembly:Wax patterns are mounted to a sprue and carefully arranged on a casting board to ensure stability and precise alignment during casting. This setup is crucial for maintaining design integrity and ensuring the molten metal flows correctly into each cavity.
- Forming the Mold Shell:The assembly is repeatedly dipped into a ceramic slurry and coated with sand stucco to form a strong, heat-resistant mold. Achieving the right thickness and strength of the shell is vital for withstanding the molten metal’s temperature.
- Wax Removal Techniques:Removing the wax can be done manually or using automated ejectors in the die, depending on the precision and delicacy required. This step is critical for maintaining the mold’s integrity and ensuring clean metal flow.
- Casting the Metal:Techniques such as gravity pouring, vacuum pouring, or pressure casting are chosen based on the part’s complexity and required precision. Each method has its advantages in achieving a defect-free cast.
- Final Touches on Castings:After breaking the mold, the castings are finalized by removing any excess material and refining the surfaces. This can involve various finishing techniques, depending on the metal and the part’s function.
What Is the Main Goal of Investment Casting?
It has been around for centuries and is used to create complex metal parts with great precision. The process of investment casting starts with a wax pattern, which is coated with ceramic to form a hollow mold after the wax is melted away. The main goal of lost-wax casting is to produce intricate, high-quality metal components that are tough or impossible to make with other methods. This casting process is favored in industries such as automotive, aerospace, defense, and jewelry for its ability to produce detailed and precise components.
If you are looking for a more in-depth explanation about the different materials that can be used in investment casting, check out our article about The Materials Behind Investment Casting.
Advantages of Investment Casting
Investment casting is great for making complex and detailed shapes that would be hard to make with other methods. It’s very accurate because the mold captures all the details of the wax model. It also makes parts with smooth surfaces, which means less work is needed to finish them. Some things made with this method include turbine blades, surgical tools, and jewelry.
Understanding the Disadvantages of Investment Casting Products
Despite its advantages, it’s important to be aware of the potential drawbacks of using this process. Here are some of the main disadvantages:
Size and Weight Limitations:
- Lost-wax casting has inherent limits on the size and weight of the products it can produce. The detailed nature of the process restricts the dimensions and mass that can be achieved effectively.
- This method is not ideal for manufacturing large parts or components that require substantial volumes of common material. For larger parts, alternative manufacturing methods might be necessary.
Extended Production Time:
- The process involves several intricate steps, including creating wax patterns, assembling ceramic shells, and multiple stages of heating and cooling. These steps contribute to a prolonged production cycle.
- This extended timeframe can be a significant disadvantage in industries where rapid time-to-market is crucial.
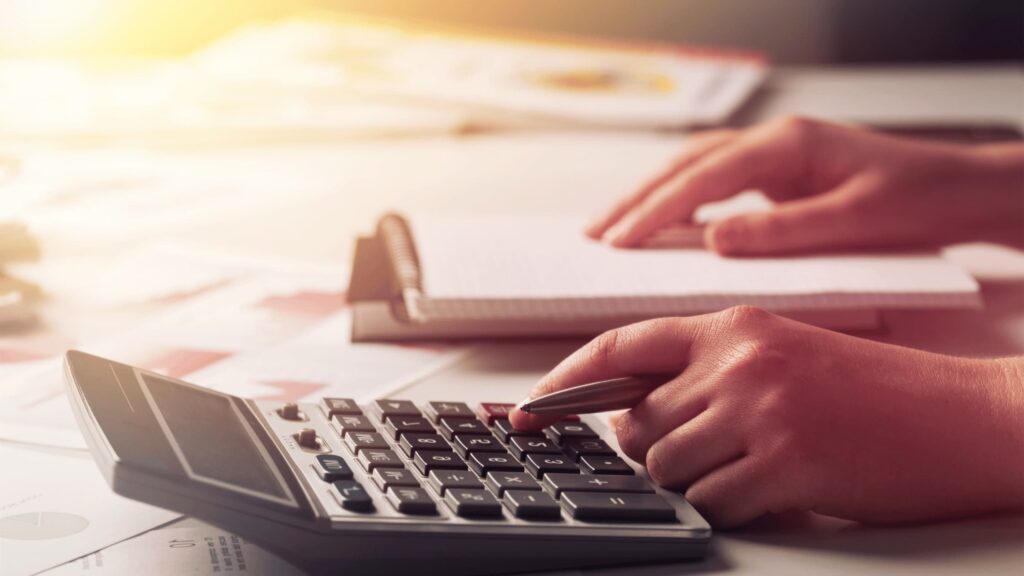
Assessing the Cost of Investment Casting
Although initially perceived as expensive, various aspects of the process contribute to its overall cost-effectiveness.
Initial Tooling Investment:
- It requires significant upfront investment in tooling, including the creation of wax patterns and ceramic molds. This precision work necessitates expertise, which adds to the initial costs.
- Despite these higher initial expenses, the durability of the molds allows them to be reused for multiple production runs, which lead to cost savings per unit over time.
Material Costs:
- The process uses a wide variety of metal alloys, such as stainless steel, aluminum, and titanium. Some of these materials are more expensive than others.
- Investment casting is efficient with materials, often using lightweight alternatives that help lower overall production costs by reducing material usage.
Efficiency and Waste Reduction:
- The method is notable for its efficiency and minimal waste production. Unlike other manufacturing techniques, investment casting produces complex parts without requiring extensive machining or secondary operations, which further cuts down on material and labor costs.
Detailed and Precise Outputs:
- The wax patterns used in investment casting allow for intricate designs and fine details, which are exact replicas in the final metal parts. The ceramic molds maintain the geometry of the wax patterns, ensuring the cast parts retain their complex features.
- This precision is challenging to achieve with other manufacturing processes, making investment casting particularly valuable for applications requiring high detail.
How Does Investment Casting Stand Out from Other Casting Methods?
Investment casting is unique compared to other types of casting like die casting and sand casting. The key difference is how the mold is made. In investment casting, a wax pattern of the final part is created first. This wax model is then covered with a ceramic material that hardens into a solid mold. Die casting, on the other hand, involves forcing molten metal under high pressure into a metal mold material. Sand casting uses a mixture of sand and a binder packed around a pattern to shape the mold cavity.
The precision and detail in investment casting are higher than in die casting and sand casting because the wax model can capture intricate details. This method is especially good for making thin-walled parts without any holes or gaps, achieving high accuracy.
Investment casting combines the benefits of detailed accuracy and reasonable costs, making it ideal for complex shapes and parts that need tight tolerances. It also allows for using various metal alloys, giving manufacturers flexibility in choosing materials.
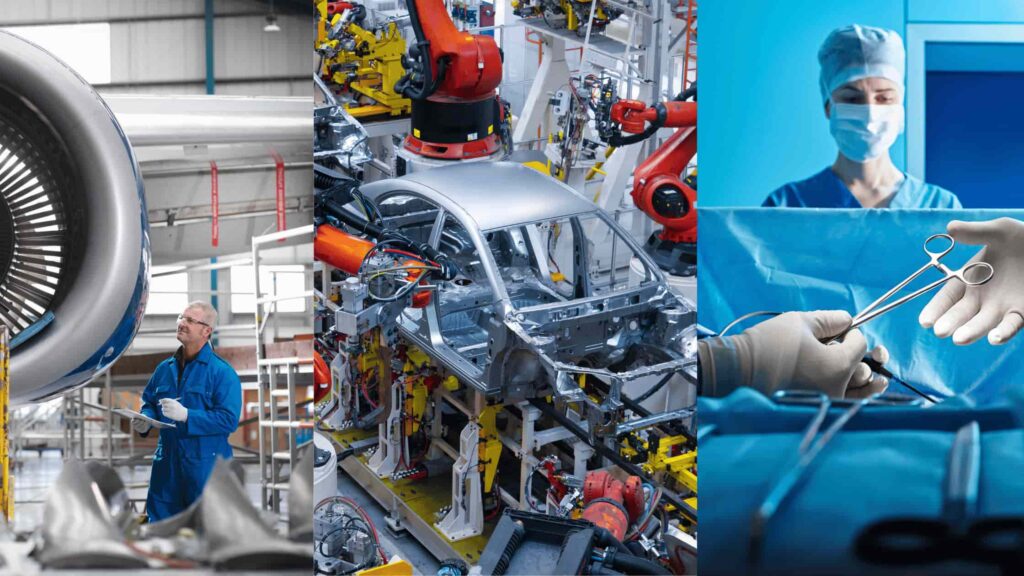
Which Industries Rely on Investment Casting?
Investment casting is popular across various sectors, including aerospace, automotive, and medical industries. In aerospace, it is used to make complex parts like turbine blades and engine components, offering excellent precision and minimal waste. Automotive manufacturers use investment casting for parts like cylinder heads and transmission components, benefiting from its ability to create lightweight and high-performance designs. The medical field also uses this technique for producing detailed implants and surgical tools, ensuring high precision and reliability essential for medical devices.
Exploring the Durability of Investment Casting Products
Precision casting products are renowned for their exceptional durability. This durability can be attributed to several factors including design, operational conditions, and material selection.
- Design Considerations: The durability of the products largely depends on their design. A well-thought-out design incorporates elements such as stress distribution, load-bearing capacity, and structural integrity. For instance, brass bearing surfaces in machinery are specifically designed to handle high loads and provide frictionless operation, which contributes to their longevity.
- Operational Limitations: The operating conditions that a product will face play a crucial role in determining its durability. Products are designed with these conditions in mind, ensuring they can withstand specific forces, vibrations, and environmental exposures. A prime example is automotive suspension knuckle joints, which are engineered to endure constant vibrations and harsh environmental conditions, thus enhancing their durability.
- Material Selection: Selecting appropriate materials is critical for the durability of investment casting products. The chosen materials must possess the necessary mechanical properties and corrosion resistance to ensure the product’s longevity. Stainless steel, for example, is often used in the process for its excellent strength, toughness, and resistance to corrosion.
- Additional Factors Contributing to Durability: It also allows for the creation of complex geometries, which can optimize the functionality and therefore the durability of the products. The process ensures precise dimensional accuracy, which is essential for the correct fit and alignment of components, enhancing both performance and durability. Furthermore, investment casting minimizes material wastage and facilitates the use of high-quality materials, both of which are instrumental in improving the structural integrity of the final product.
- Heat Resistance: The durability is also influenced by their ability to resist heat. This is dependent on the materials used; certain materials such as superalloys are chosen specifically for their exceptional heat resistance properties. These materials ensure that the products can operate effectively in high-temperature environments without degrading.
In summary, investment casting is a versatile process used in industrial applications for creating parts with different metals. It has size and cross-sectional limits, making it suitable for small to medium-sized parts. Correct product choice and strict process and quality control procedures are vital for successful investment casting.