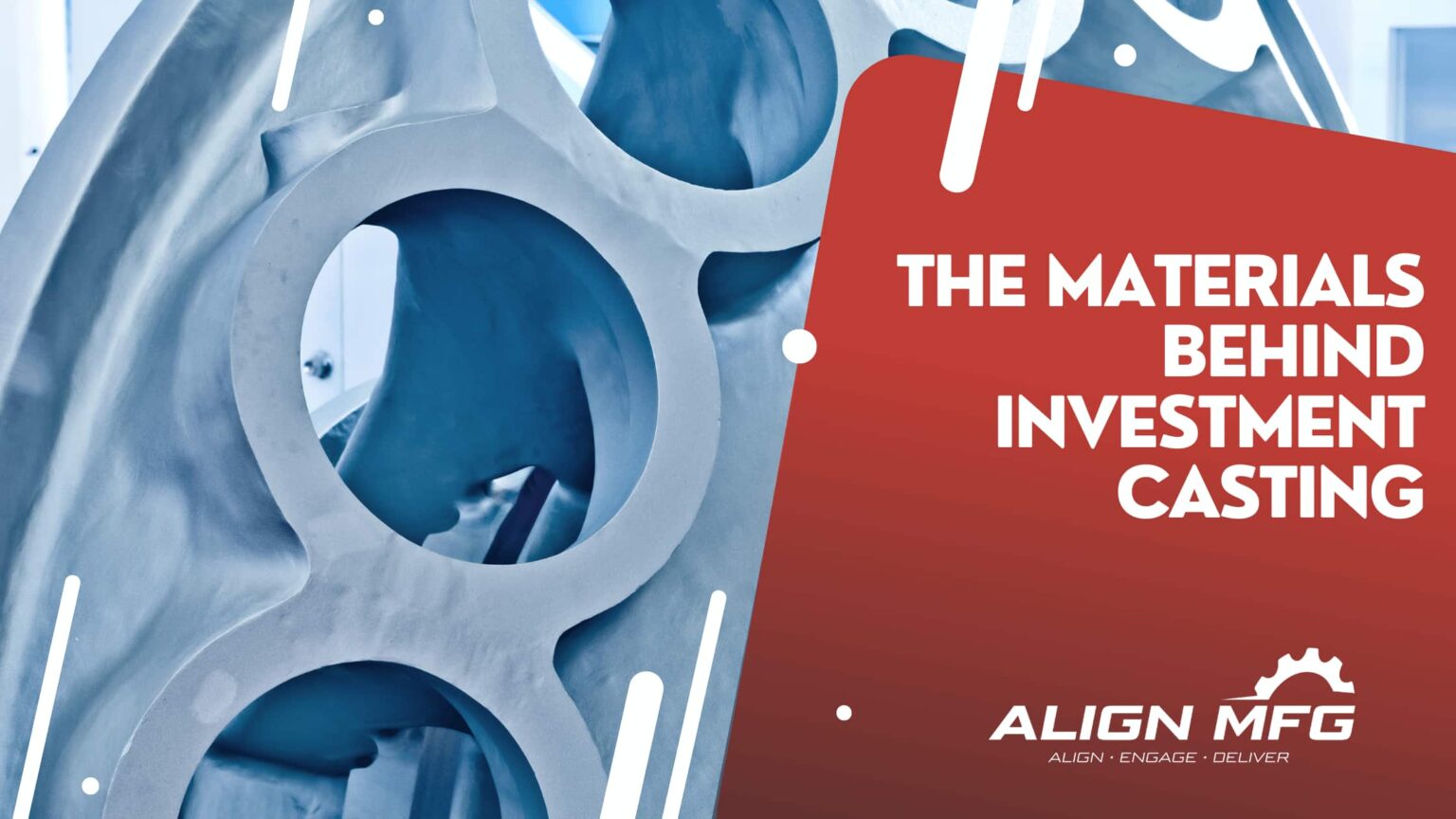
The Materials Behind Investment Casting
Investment casting is a widely used manufacturing process that allows the production of intricate and complex metal components with high precision. This process involves creating a wax pattern of the desired part, coating it with a ceramic shell mold, and then melting the wax out to create a hollow metal mold. The mold material is then filled with molten metal to produce the final component.
One of the critical aspects of lost-wax casting is the choice of materials, both for the wax pattern and the shell, as they directly influence the quality, integrity, and performance of the finished product. In this article, we will explore various precision casting materials, including plastic pattern materials, shell materials, and the metals commonly used for casting.
We will delve into their properties and characteristics, highlighting their suitability for different applications and discussing their advantages and limitations in the investment casting process.
Advantages of Investment Casting
Precision casting is a highly advantageous manufacturing process, known for its ability to produce precision components with intricate and complex shapes that other methods may struggle to achieve. One of the standout benefits of this technique is its exceptional dimensional accuracy and the ability to maintain tight tolerances, which are essential in industries such as aerospace and medical devices where precision is paramount.
Additionally, investment casting can utilize a vast range of materials, providing flexibility in application across various industries. The process also allows for excellent surface finish, reducing the need for additional machining and finishing steps, which can significantly lower production costs.
Moreover, the versatility in size and weight of the components that can be produced makes it suitable for both small and large parts, enhancing its applicability for different product requirements.
If you want to know more about investment casting, check out our article about The Basics of Investment Casting: An Introduction.
But for now, let’s dive into the different materials that can be used for the different casting methods.
Stainless Steel
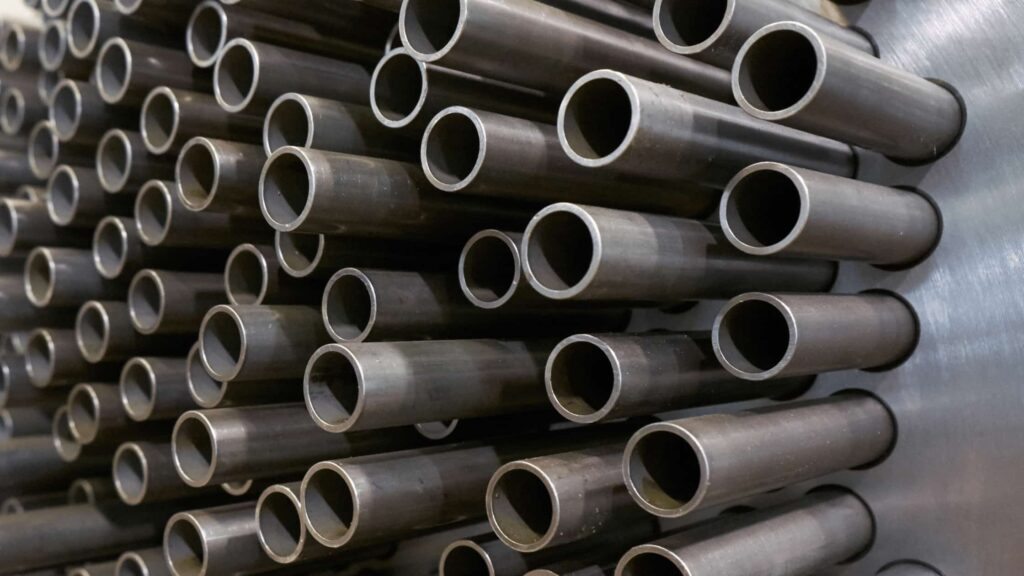
It is a versatile material with numerous applications and advantages. Its primary characteristic is its superior durability, making it ideal for various industries. One significant area where stainless steel is extensively used is investment casting.
In the automotive industry, stainless steel is utilized in gearbox parts and gears. The high strength and corrosion resistance of it ensure that these components can withstand the demanding conditions of a vehicle’s transmission system. Moreover, stainless steel’s resistance to heat and wear makes it an excellent choice for cam components, which are essential for controlling the opening and closing of valves in an engine. Golf club heads also benefit from stainless steel’s durability and resistance to corrosion, ensuring longevity and performance on the golf course.
Compared to other materials, it offers numerous advantages. Its corrosion resistance eliminates the need for maintenance and frequent replacements. Additionally, it can withstand high temperatures, making it suitable for applications where heat resistance is crucial. Furthermore, the aesthetic appeal, with its shiny and clean appearance, adds to its desirability in various industries. Overall, stainless steel’s unmatched durability, corrosion resistance, and versatility make it a highly sought-after material for investment casting process, automotive gearbox parts and gears, cam components, golf club heads, and many other applications.
Low Alloy Steel
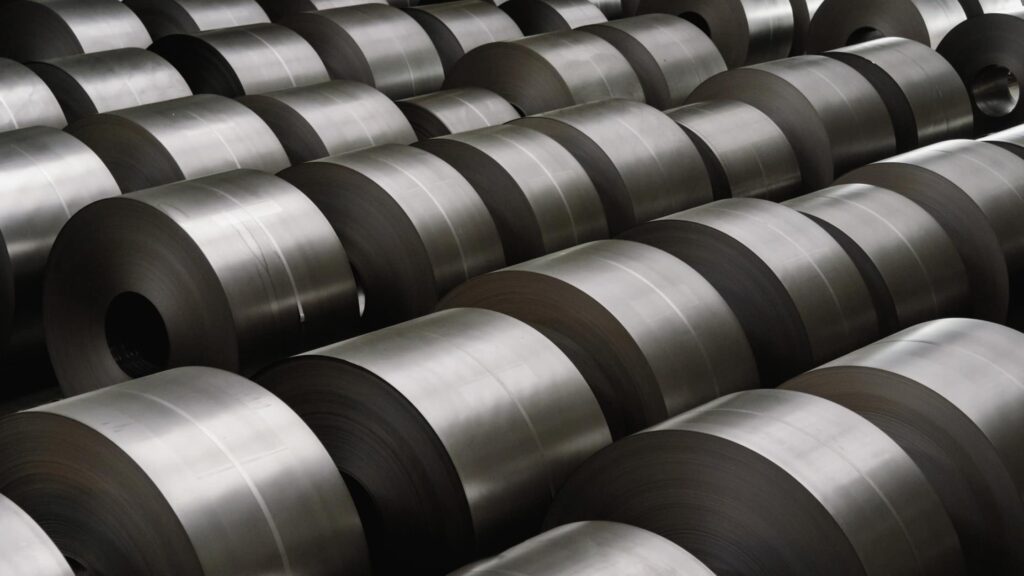
Low alloy steel, as the name suggests, is a type of steel that has a low percentage of alloying elements, usually less than 8%. This makes it more affordable compared to high alloy steels, which contain higher amounts of alloying elements.
It offers numerous benefits due to its beneficial mechanical properties. It has excellent strength and toughness, making it suitable for demanding applications where high strength and impact resistance are required. Additionally, it has good corrosion resistance, making it ideal for use in corrosive environments.
One of the key advantages is its suitability for specialized heat-treating processes. These processes involve altering the microstructure of the steel to enhance its properties. For engineered parts, low alloy steel can undergo specific heat treatments such as quenching and tempering to achieve desired hardness, strength, and wear resistance.
The applications are diverse. It is commonly used in the automotive and aerospace industries for parts that require high strength and durability, such as engine components and aircraft landing gear. Low alloy steel is also widely used in construction, oil and gas, and manufacturing industries for structural applications and machinery components.
Aluminum Alloy
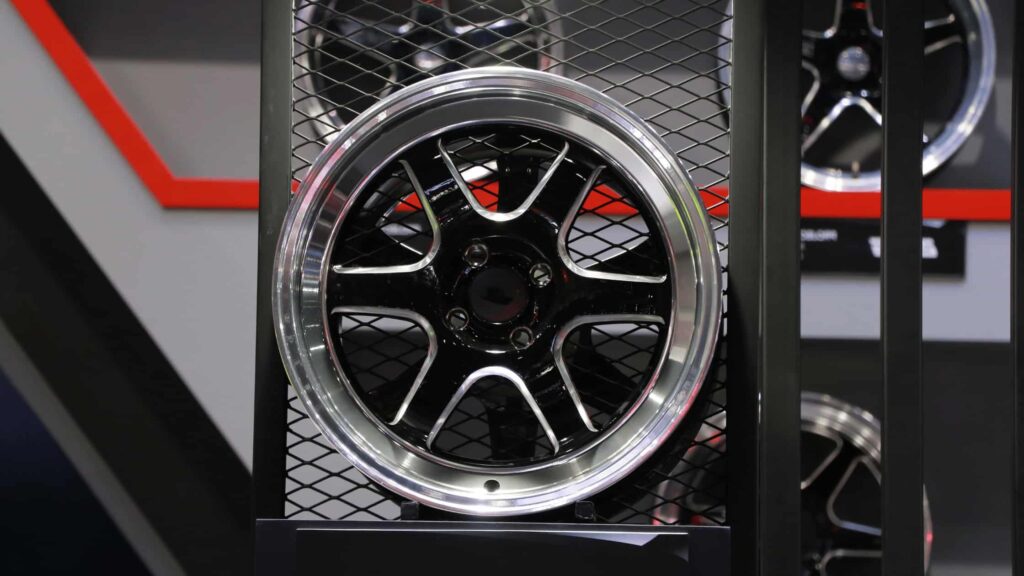
Aluminum alloy is a versatile material widely used for investment castings due to its beneficial properties and wide range of applications. Its key advantages include excellent strength-to-weight ratio, corrosion resistance, and high thermal and electrical conductivity.
Investment castings made of aluminum alloy find applications in various industries, including automotive, electronics, and industrial equipment. In the automotive sector, they are preferred for their lightweight nature, which helps improve fuel efficiency and reduce emissions. They are commonly used for components like engine blocks, cylinder heads, and wheels.
The blend of aluminum, silicon, and magnesium greatly enhances the strength and suitability of aluminum alloy for these applications. The addition of silicon provides improved fluidity during the casting process, making it easier to achieve intricate and complex shapes. Magnesium, on the other hand, increases the alloy’s strength and ductility, allowing it to withstand high-stress applications.
In electronics, aluminum alloy investment castings are used for heat sinks, connectors, and housings, as they possess excellent thermal conductivity, ensuring efficient heat dissipation and component protection. In the industrial equipment sector, these castings are employed in pumps, valves, and machinery components, benefiting from the alloy’s durability and resistance to wear and tear.
Carbon Steel
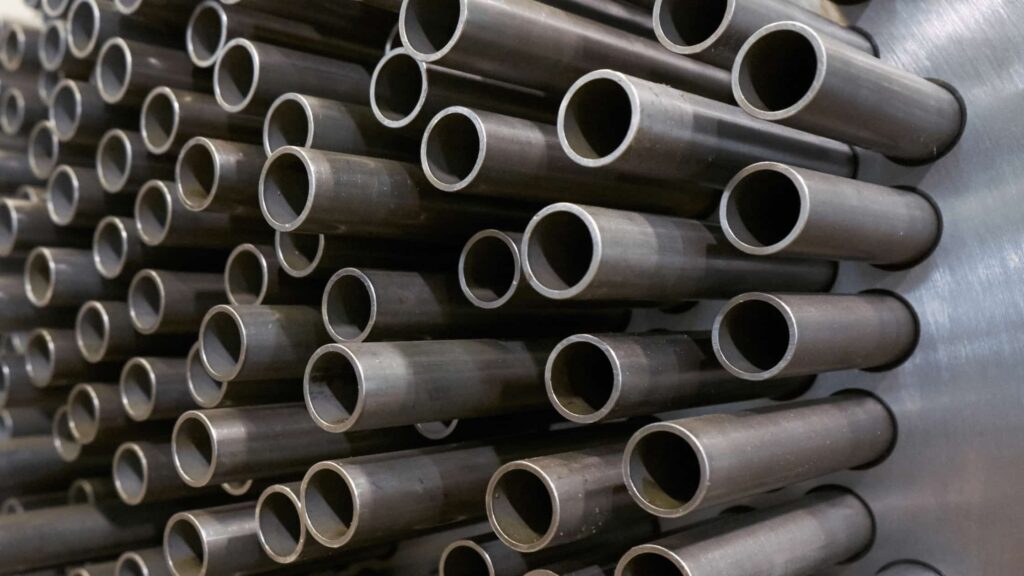
Carbon steel, composed primarily of carbon and iron, is a widely used material known for its low cost compared to other alloys. It comes in various grades based on carbon content, with higher carbon levels resulting in stronger and harder steel.
Carbon steel can be easily shaped and formed into different products, and its performance can be improved through heat treatment, which enhances its hardness, strength, and toughness. One notable property is its ferromagnetic nature, making it useful in motors and electrical appliances. Carbon steel is commonly used in the construction of electric motors, transformers, and generators due to its magnetic properties and cost-effectiveness.
Super Alloy
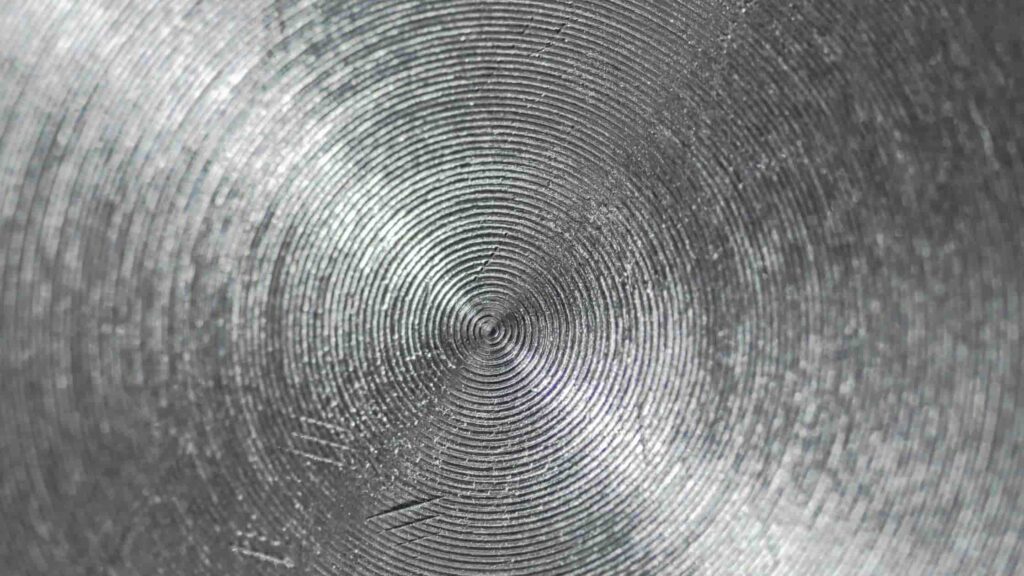
Super alloys, or high-performance alloys, particularly nickel-based and cobalt-based, exhibit exceptional mechanical strength, resistance to extreme temperatures, corrosion, oxidation, and wear. They retain their mechanical properties at temperatures exceeding 1000°C, making them indispensable in gas turbine engines, aerospace components, and nuclear reactors.
Super alloys also offer excellent corrosion resistance in aggressive chemicals, acids, and seawater, benefiting chemical processing plants, marine applications, and oil and gas exploration. Their wear resistance allows them to withstand abrasive materials and heavy mechanical loads, making them ideal for high-stress components like turbine blades and jet engine parts. Despite their higher cost compared to sheet metal, super alloys’ superior properties, reliability, and longevity make them a cost-effective choice for demanding applications.
Copper Alloy
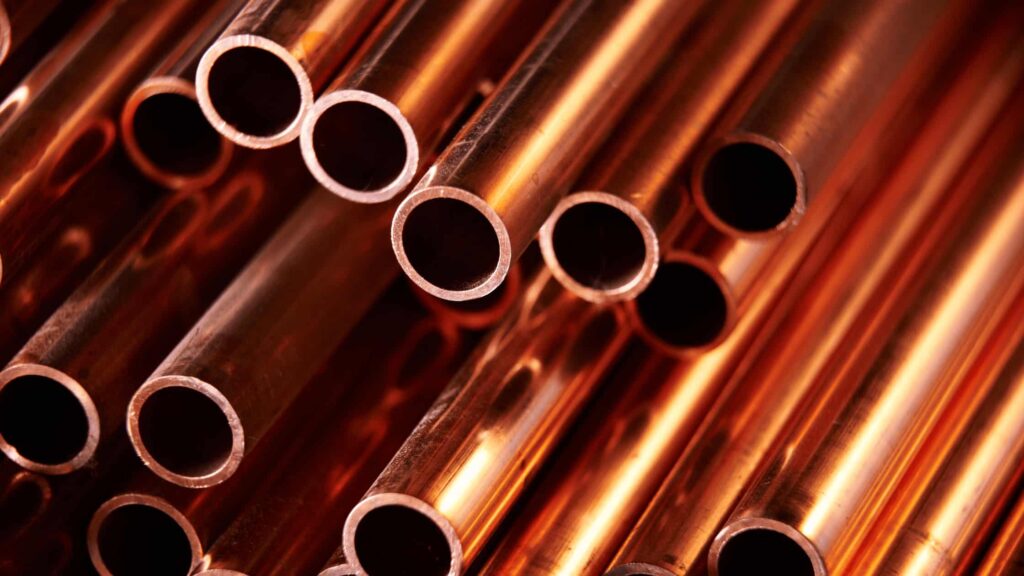
Copper alloys, created by mixing copper with other metals, offer superior strength, corrosion resistance, electrical conductivity, thermal conductivity, and good formability. Bronze and brass are two common types of copper-based alloys used in investment castings. Bronze, an alloy of copper and tin, offers high strength, corrosion resistance, and excellent thermal conductivity, making it suitable for musical instruments, statues, and fittings. Brass, an alloy of copper and zinc, is known for its attractive appearance and easy molding, making it popular for decorative items, plumbing fittings, and electrical connectors. Beryllium-copper, one of the strongest copper-based alloys, possesses exceptional corrosion resistance, high strength, hardness, and electrical conductivity, making it ideal for components in the aerospace and automotive industries subjected to harsh environments and high stress conditions.
Cast Iron
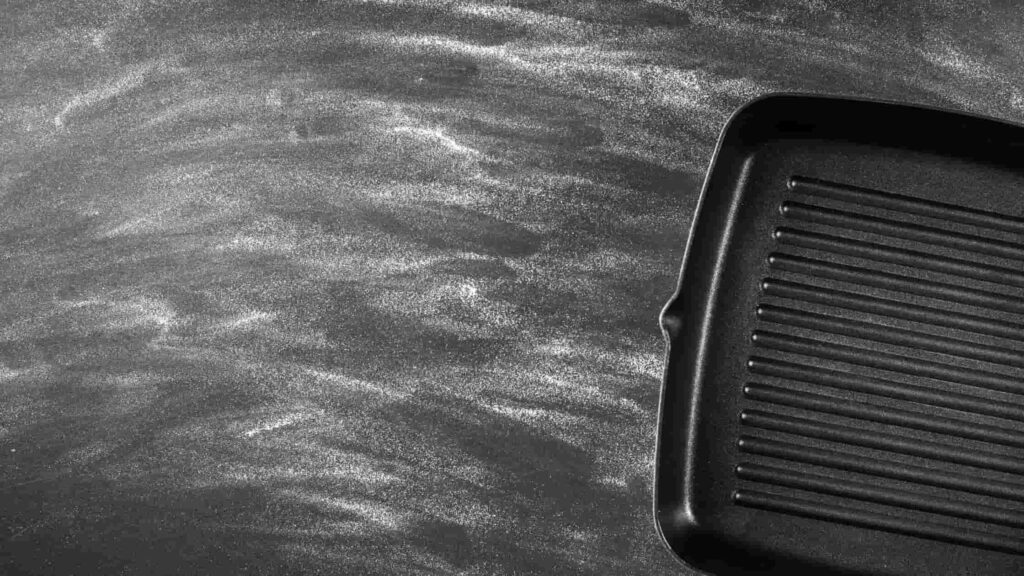
Cast iron is a strong and versatile material that is commonly used in various industries due to its unique characteristics. It is derived from iron and carbon, with a carbon content of at least 2%, making it harder and more brittle than steel. The production process of cast iron involves melting iron and adding carbon and other alloys to achieve the desired properties. This mixture is then poured into molds and allowed to cool and solidify.
One characteristic that makes cast iron desirable is its affordability and high accuracy. Iron castings, especially those made from gray iron and ductile iron, are known for their cost-effectiveness and precise dimensions. This makes them suitable for a wide range of applications, from automotive parts to appliances.
Gray iron, in particular, is easy to cast and has good damping properties, making it ideal for applications that require vibration resistance. On the other hand, ductile iron offers high strength, heat-resistance, and toughness. Its complex production process, which involves adding magnesium to the iron-carbon mixture, results in superior mechanical properties. However, this more intricate process leads to higher production costs compared to cast steel.
Key Takeaways
The selection of metal casting is a critical decision that significantly impacts the final product’s performance and cost-effectiveness. By carefully considering factors like the part’s function, desired mechanical properties, and compatibility with the investment casting process, manufacturers can ensure they choose the optimal ceramic material for their application. This not only guarantees the part meets its performance specifications but also minimizes the need for extensive post-processing, leading to improved production efficiency and tooling cost savings. Therefore, investing time and effort in material selection is a strategic step that unlocks the full potential of precision casting for a broad range of industries.