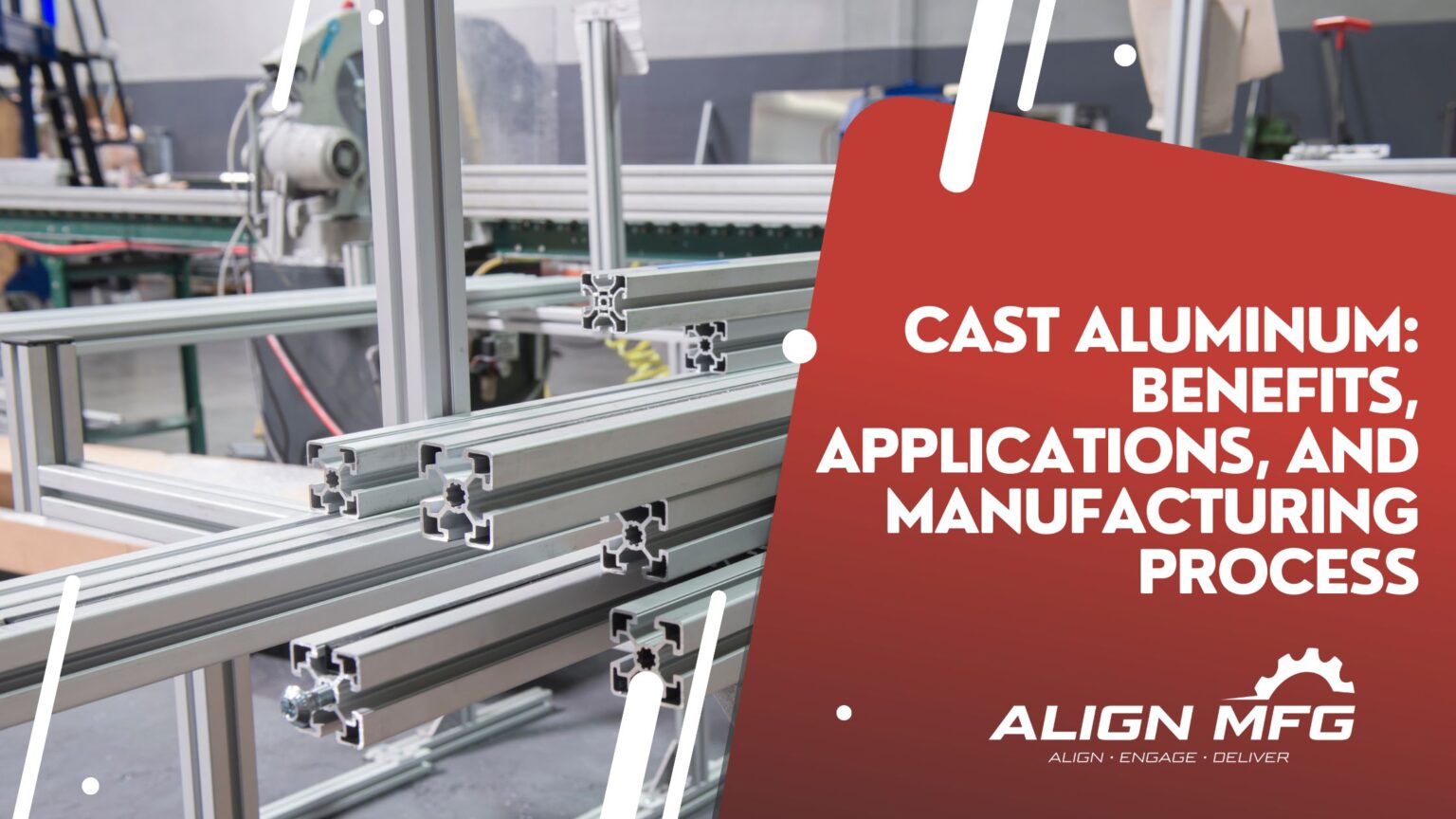
Cast Aluminum: Benefits, Applications, and Manufacturing Process
Cast aluminum is more than just a material; it’s a versatile cornerstone in the manufacturing world, enabling the creation of products that shape our everyday life. From the car you drive to the pots and pans in your kitchen, cast aluminum plays a pivotal role. This blog post will guide you through the essence of cast aluminum, its unique properties, the advantages and challenges it presents, and how it stacks up against other metals like cast steel and grey iron.
What is Cast Aluminum?
Cast aluminum refers to a process where aluminum is melted and poured into a mold to create complex shapes and components. Unlike wrought aluminum, which is shaped through methods like rolling, hammering, or extruding, casting allows for intricate designs and detailed textures that would be difficult or impossible to achieve with other techniques. This versatility makes cast aluminum an attractive option for manufacturers seeking to produce high-quality parts with precision.
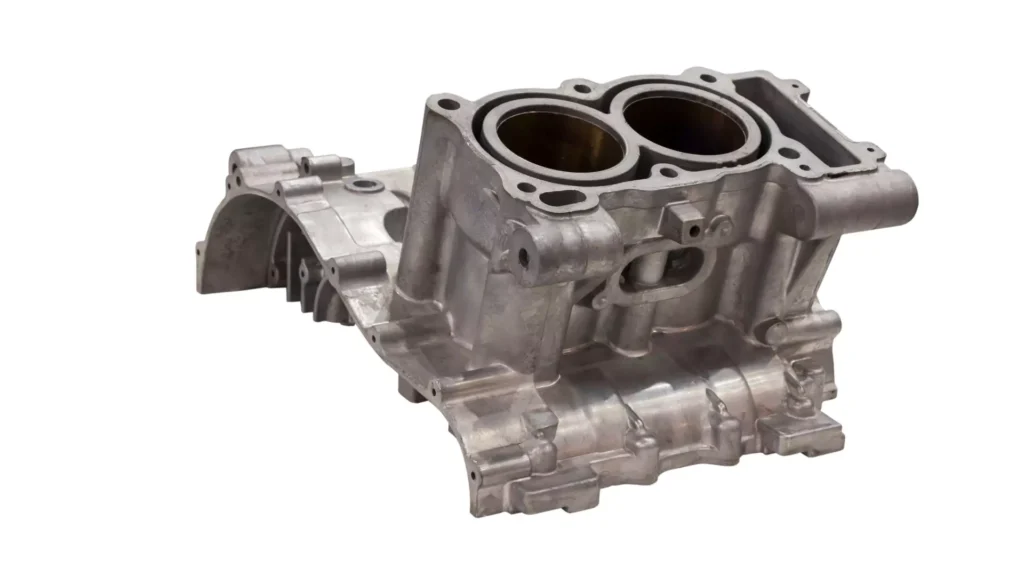
The Aluminum Casting Process
The journey of creating a cast aluminum part involves several steps. It begins with melting aluminum ingots or scraps and then injecting the molten metal into a steel or aluminum mold under high pressure. Once the aluminum cools and solidifies, the mold opens to reveal a lightweight yet sturdy component. Techniques like die casting, permanent mold casting, and sand casting are commonly employed, each suitable for different complexity levels and production volumes.
Process | Description | Key Features | Applications |
Die Casting | High-pressure injection of molten aluminum into a metal mold. | Fast, precise, excellent surface finish, high dimensional accuracy, and good thermal conductivity. | Automotive, electronics, consumer goods. |
Sand Casting | Molten aluminum is poured into a mold made from a sand mixture. | Low tooling cost, suitable for large and complex parts, flexible in size and shape, but rougher surface finish. | Heavy machinery, industrial equipment. |
Permanent Mold Casting | Molten aluminum is poured into reusable metal molds using gravity or low pressure. | Consistent quality, smoother finish than sand casting, good dimensional stability, and improved mechanical properties. | Automotive, aerospace components. |
The Properties of Cast Aluminum
Aluminum casting alloys typically contain over 90% aluminum, with other elements like silicon, copper, magnesium, or zinc added to enhance specific characteristics. Here are some key properties that make cast aluminum a popular choice:
- Lightweight: Aluminum’s low density makes it an ideal choice for applications where weight reduction is crucial without sacrificing strength. This property is particularly valuable in industries like automotive and aerospace, where every ounce counts.
- Strength and Durability: While not as strong as steel, certain cast aluminum alloys offer impressive strength and durability, often exceeding that of plastic or wood. This makes it suitable for a range of demanding applications.
- Corrosion Resistance: Aluminum naturally forms a protective oxide coating when exposed to air, rendering it resistant to corrosion. This characteristic can be further enhanced through treatments like anodizing or painting, making it ideal for outdoor applications.
- Conductivity: Aluminum is an excellent conductor of heat and electricity, which makes it suitable for applications like heat sinks in electronics and electrical components.
- Recyclability: Aluminum is 100% recyclable without any loss of quality, contributing to its popularity in sustainable manufacturing practices. This aspect aligns with the growing emphasis on eco-friendly production methods.
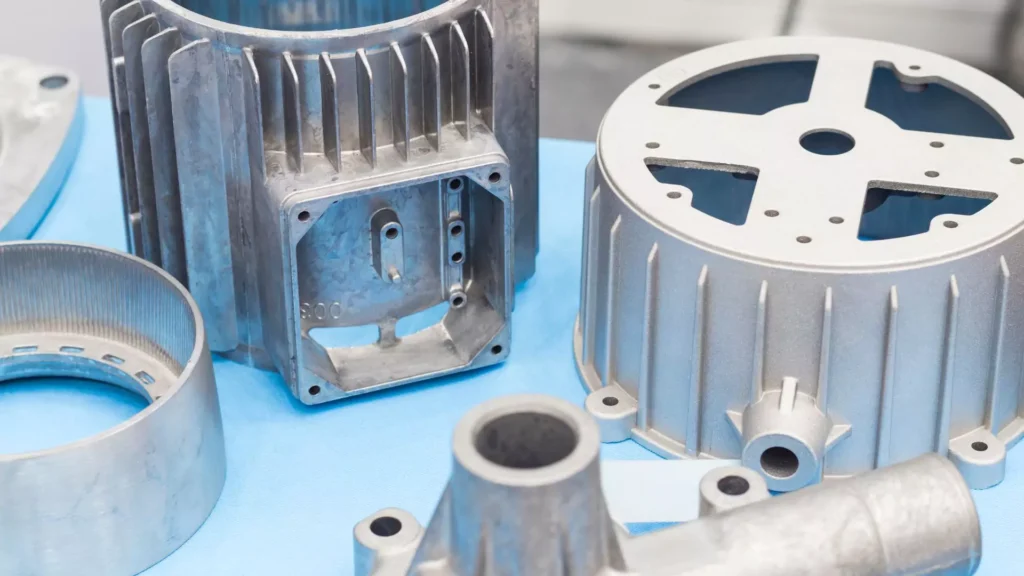
Benefits of Using Cast Aluminum
The advantages of using cast aluminum in manufacturing are vast:
- Design Flexibility: The casting process allows for the creation of complex shapes and intricate details, providing designers with a high degree of creative freedom. This flexibility enables the production of parts that are both functional and aesthetically pleasing.
- Cost-Effective Production: Aluminum casting can be more cost-effective than other metalworking processes, especially for large production runs. The ability to produce multiple parts in a single cycle reduces overall costs.
- Reduced Assembly Needs: Components can often be designed to consolidate multiple parts into a single cast, minimizing the need for assembly and lowering production costs.
- Superior Aesthetics: Cast aluminum can achieve a high-quality surface finish that is both functional and visually appealing, making it suitable for consumer products where appearance matters.
Applications of Cast Aluminum
The versatility of cast aluminum makes it a staple in numerous industries:
- Automotive: Engine components, wheels, and transmission housings are often made from cast aluminum for their strength and lightweight properties.
- Aerospace: The process is used to create structural parts for aircraft that require precision and strength without adding unnecessary weight.
- Consumer Goods: Everything from electronics to cookware benefits from aluminum’s thermal properties and ease of casting.
- Construction: Aluminum casting is used in building materials for its durability and resistance to corrosion.
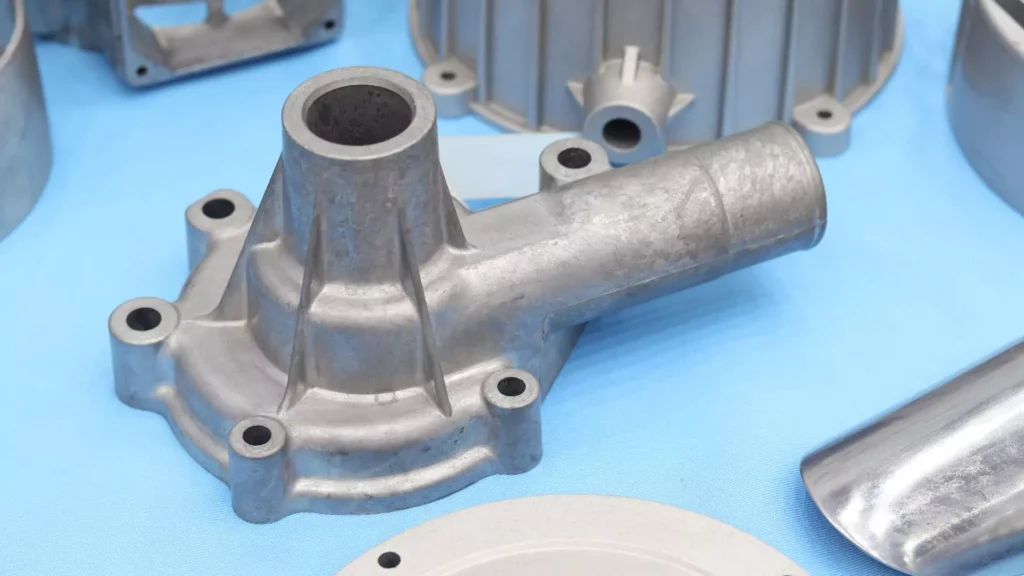
Disadvantages of Cast Aluminum
While cast aluminum offers numerous benefits, there are some limitations to consider:
- Lower Strength Compared to Steel: Although strong, cast aluminum does not match the tensile strength of steel, which can limit its use in high-stress applications.
- Brittleness: Certain aluminum alloys can be more brittle than other metals, especially under extreme conditions, leading to potential cracking.
- Higher Initial Costs: The costs associated with casting aluminum can be higher than some other materials, particularly if complex molds are required.
Cast Aluminum vs. Cast Steel
When comparing cast aluminum to cast steel, several factors come into play:
Strength and Weight
Cast steel generally offers higher strength, but cast aluminum’s strength-to-weight ratio is advantageous for many applications.
Cost Implications
Cast steel can be more expensive due to its material properties and the energy required to produce it.
Application Suitability
- Cast Steel: Preferred for heavy-duty structural components due to its high strength.
- Cast Aluminum: Chosen for applications where weight savings are critical, such as in transportation and mobile equipment.
Cast Aluminum vs. Grey Iron
Grey iron and cast aluminum are used in different scenarios based on their material characteristics:
Material Characteristics
Grey iron is known for its compressive strength and excellent vibration damping, whereas cast aluminum offers better corrosion resistance and weight savings.
Machinability and Usage
Grey iron is easily machinable but cast aluminum is preferred for complex shapes and thin-walled components.
Industry Preferences
- Grey Iron: Favored in the construction and industrial sectors.
- Cast Aluminum: Popular in the automotive, aerospace, and consumer electronics industries due to its lightness and durability.
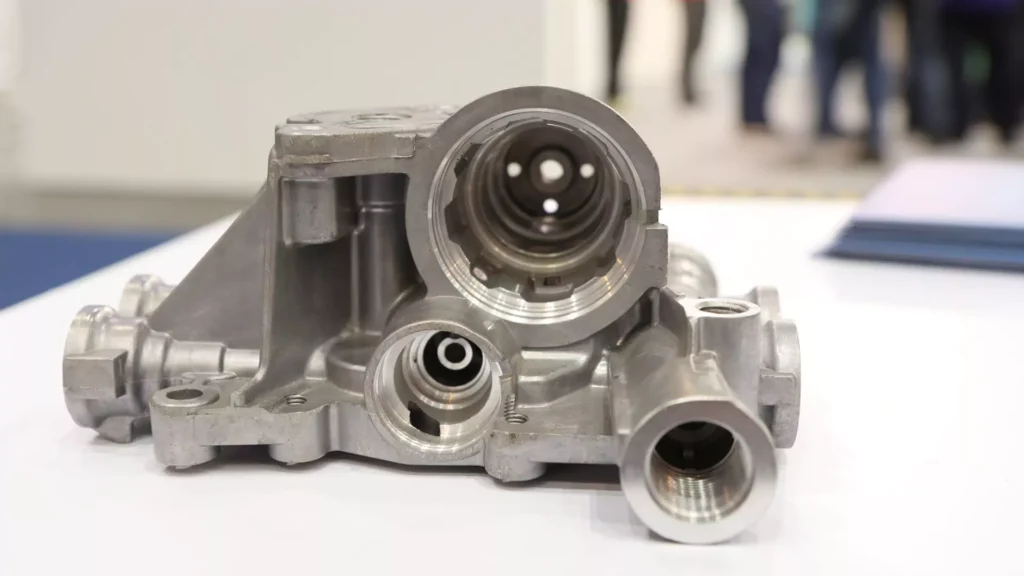
Comparison of Cast Aluminum, Cast Steel, and Grey Iron
Property/Aspect | Cast Aluminum | Cast Steel | Grey Iron |
Density | ~2.7 g/cm³, lightweight. | ~7.7–7.85 g/cm³, heavier. | ~7.1–7.3 g/cm³, relatively heavy. |
Tensile Strength | 100–400 MPa; 7068 alloy can reach 710 MPa. | 340–1800 MPa, depending on alloy and heat treatment. | 150–400 MPa; ASTM A48 Class 40 has 276 MPa. |
Compressive Strength | Good, lower than cast iron; depends on alloy. | High, suitable for heavy loads. | Excellent, often >1000 MPa. |
Melting Point | 570–655°C. | 1450–1520°C. | 1150–1250°C. |
Thermal Conductivity | 120–180 W/m·K, excellent for heat dissipation. | Moderate. | ~46 W/m·K, moderate. |
Electrical Conductivity | Good, ideal for electrical components. | Poor, not suited for electrical applications. | Poor, unsuitable for electrical applications. |
Machinability | Easy to machine, allows for complex shapes. | Moderate, requires specialized tools. | Good machinability; brittleness requires care. |
Corrosion Resistance | Excellent; protective oxide layer enhances durability. | Moderate; rusts without surface treatment. | Poor; prone to corrosion, especially in moisture. |
Vibration Damping | Moderate; less effective than grey iron. | Good; better than aluminum but less effective than grey iron. | Excellent; graphite flakes provide superior damping. |
Common Applications | Automotive parts, aerospace components, consumer electronics. | Heavy machinery, structural components, applications needing high strength and toughness. | Engine blocks, machine bases, pipes, and vibration-damping applications. |
Cost | Lower for mass production due to efficiency and material availability. | Higher, due to material and processing costs. | Moderate; brittleness may lead to higher maintenance or replacement costs in specific applications. |
Conclusion
Cast aluminum stands as a testament to the ingenuity of modern manufacturing. With its blend of durability, versatility, and sustainability, this material continues to push the boundaries of what’s possible across various sectors. Whether it’s in the engine of your car, the body of your smartphone, or the frame of your bicycle, cast aluminum is a material that not only meets the demands of today’s manufacturers but also holds promise for the innovations of tomorrow.
For businesses looking to maximize the benefits of cast aluminum in their products, Align Manufacturing offers expert engineering solutions and support to help navigate the complexities of aluminum casting. Their commitment to quality and efficiency ensures that your projects meet the highest standards and expectations.
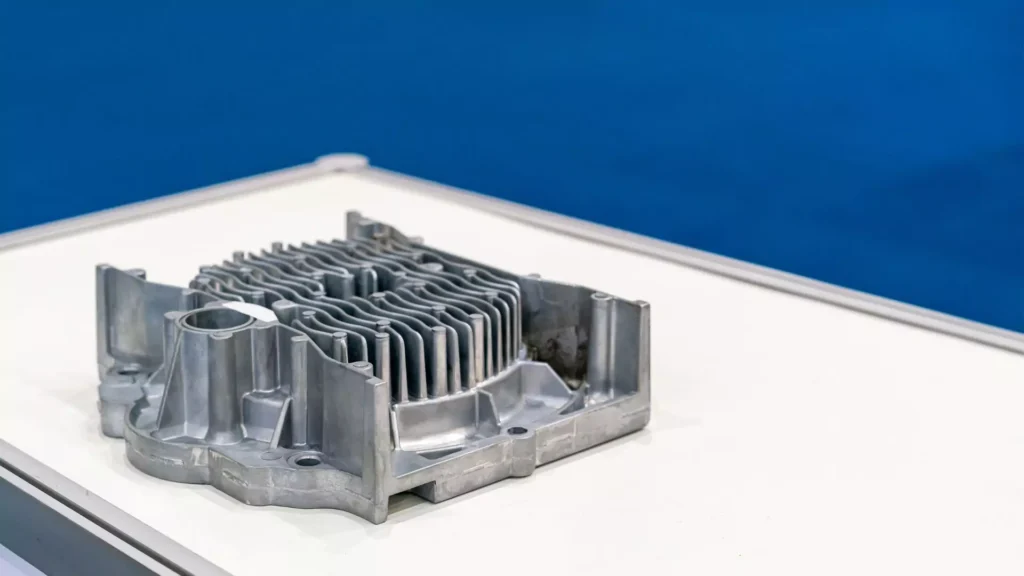
FAQs
Lightweight with High Strength-to-Weight Ratio
Cast aluminum is significantly lighter than materials like cast steel or grey iron, reducing overall product weight without compromising strength. This is particularly advantageous in industries like aerospace, automotive, and electronics, where weight reduction directly impacts performance and efficiency.
Lower Melting Point for Energy Efficiency
With a melting point of 570–655°C, aluminum requires less energy to cast compared to steel or iron, lowering energy costs in the production process. This makes it particularly suited for methods like permanent mold casting, where efficiency is critical.
Versatile Casting Options
Aluminum’s lower melting point and excellent fluidity enable the use of various casting techniques (e.g., die casting, sand casting, permanent mold casting) to create complex shapes and intricate designs. This versatility reduces tooling costs and expands design possibilities.
Corrosion Resistance for Durability
Aluminum naturally forms a protective oxide layer, which enhances its resistance to rust and corrosion. This eliminates or reduces the need for additional surface treatments, saving on production and maintenance costs while ensuring longevity.
Thermal and Electrical Conductivity
Its excellent thermal and electrical conductivity makes cast aluminum ideal for applications requiring efficient heat dissipation or electrical performance, such as electronic enclosures and heat exchangers.
Machinability for Lower Production Time
Cast aluminum is easier to machine compared to steel or iron, allowing for faster production cycles and reduced labor costs. This also facilitates the production of custom or precision parts with minimal tool wear.
Cost-Effectiveness in High-Volume Production
Aluminum casting is particularly economical for mass production due to its combination of low material costs, reduced energy requirements, and quick production times. This provides manufacturers with a
- Cast Aluminum: Produced through casting, where molten aluminum is poured into molds to create complex shapes with high density and strength.
- Aluminum: Typically created through extrusion, forging, or rolling, forming simpler shapes like plates, rods, or profiles with variable strength and hardness.
How do their applications differ?
- Cast Aluminum: Commonly used in automotive parts, machinery, and equipment requiring intricate designs and durability.
- Aluminum: Preferred for aerospace, construction, and electronics due to its versatility, lightweight nature, and ability to handle higher strength and hardness needs.
Which material is more cost-effective for manufacturing?
- Cast Aluminum: Has lower manufacturing costs due to the efficiency of the casting process.
- Aluminum: Raw material is generally less expensive, but processing costs (e.g., extrusion or forging) are higher.
How do they compare in terms of processability and surface treatments?
Both materials offer excellent processability and surface treatment properties, including the ability to be anodized or sprayed, making them suitable for various functional and aesthetic applications.
What are the density and strength differences?
- Cast Aluminum: Features higher density and strength, making it ideal for parts requiring structural integrity and durability.
- Aluminum: Typically lighter and has variable strength depending on the alloy and manufacturing process, suiting applications where weight reduction is critical.
By understanding these differences, manufacturers can select the material that best aligns with their project’s requirements, whether for cost efficiency, strength, or design complexity.
- What are the main raw materials in cast aluminum?
Cast aluminum is made from various aluminum alloys, which include alloying elements like silicon, copper, zinc, magnesium, and manganese to enhance specific properties such as strength, corrosion resistance, and machinability. - What are common types of aluminum alloys used in casting?
- Aluminum-Silicon Alloy (Al-Si): Improves fluidity and reduces thermal shrinkage, used in engine parts and hydraulic components. Examples: A390, A380, A356.
- Aluminum-Copper Alloy (Al-Cu): Offers high strength and wear resistance, ideal for aircraft parts and turbine blades. Examples: A201, A202.
- Aluminum-Magnesium Alloy (Al-Mg): Features low density and excellent corrosion resistance, used in aerospace and automotive wheels. Examples: A5182, A5052.
- Aluminum-Zinc Alloy (Al-Zn): Provides high strength and corrosion resistance, commonly used for automotive and mechanical parts. Examples: A7075, A7049.
- Aluminum-Manganese Alloy (Al-Mn): Known for corrosion resistance, suitable for special environments like seawater applications. Examples: A3004, A3003.
For more information on alloys check out our guide : https://alignmfg.co/materials/metal/alloys-customizable-and-high-performance/
Yes, aluminum can be welded, but it requires specialized techniques and equipment compared to steel. Different aluminum alloys also have varying weldability.