Posts by Align Manufacturing
Plug Valves: What are they and What are they Used for?
In the world of fluid control, plug valves stand out for their simplicity and reliability. Known for their straightforward design and effectiveness, they play a crucial role in numerous industrial applications where tight shut-off is essential. A deeper understanding of their functionality and versatile usage can demystify these pivotal components of fluid dynamics.
The hallmark of plug valves is their conically tapered plug, which aligns ports to regulate flow efficiently. From lubricated to non-lubricated, multi-port to eccentric, and jacketed types, the varied designs offer an array of solutions tailored to specific needs, from quick shut-off requirements to specialized use cases in diverse industries.
Definition of a Plug Valve
A plug valve is a type of quarter-turn valve used for controlling the flow of fluids through a pipe system. Its primary feature is a cylindrical or conical plug that can be rotated inside the valve body to open or close the passageway, allowing or stopping the flow of fluids. The design ensures a tight shut-off, making them suitable for a wide range of applications, including those requiring minimal leakage.
Basic Design and Operation
Plug valves are integral components in managing the flow of fluids in pipelines. Their simple yet robust design offers a reliable, efficient solution for fluid control, suitable for numerous applications from chemical processing to oil and gas distribution. The valve’s body, crafted from durable materials like stainless steel or carbon steel, supports longevity and performance under diverse operating conditions. Operators favor plug valves for their minimal leakage potential and overall resilience, making them a top choice for ensuring tight shut-offs and consistent system operation.
Conically Tapered Plug
Its conically tapered plug, plays a crucial role in controlling the flow of fluids. This taper is designed to fit snugly within the valve body, ensuring minimal leakage and a reliable seal when closed. The conical shape not only aids in achieving a tight shut-off but also facilitates easy rotation, allowing for swift actuation and precise fluid control. Its design provides low resistance to flow, minimizing energy consumption and pressure drop, which are critical considerations in maintaining an efficient network. The conical plug design is versatile, allowing it to adapt to various fluid types and flow rates, further solidifying its status as an essential component in numerous industrial applications.
Ports Alignment for Flow Control
Ports alignment in plug valves is vital for accurate and efficient fluid flow management. The alignment involves positioning the plug’s openings to match the valve’s ports, ensuring optimal fluid passage. Proper alignment allows for precise control over the flow of fluids between connected pathways, a feature crucial in systems where fluid direction must be regularly adjusted. The ability to direct flow efficiently helps in maintaining desired flow rates and preventing potential bottlenecks in the system. This control mechanism optimizes the operational efficiency by reducing issues such as pressure loss and product contamination, making plug valves an indispensable asset in processes that demand high accuracy and dependability in fluid handling.
Types of Plug Valves
The main valve types include lubricated, non-lubricated, multi-port, eccentric, and jacketed plug valves. Each type is designed with specific features tailored to enhance performance and efficiency, thereby reducing energy consumption and ensuring optimal fluid flow.
Lubricated Plug Valves
Lubricated plug valves incorporate a lubricant film between the plug and valve body, facilitating smoother operation and minimizing friction. This type of plug valve is favorable in handling gases and fluids at varying flow rates, due to its capacity to withstand higher pressure drops with less wear and tear. Lubricated plug valves are commonly used in industries that require durable and reliable sealing for high-temperature applications, making them a popular choice across a wide range of sectors.
Non-Lubricated Plug Valves
Non-lubricated plug valves utilize a different mechanism where the smooth surfaces of the plug and body are polished to achieve a tight seal without the need for lubrication. This type is generally more compact and requires less maintenance, as there is no need to replace or monitor lubricants. The absence of lubrication reduces the risk of contamination, making them ideal in industries like food and pharmaceuticals. Their design, commonly utilizing materials like stainless steel, helps in efficiently managing fluid flow where product purity is critical. Additionally, non-lubricated plug valves are known for their low friction operation and long service life.
Multi-Port Plug Valves
Multiport valves are designed to handle the flow of fluids through multiple pathways with a single valve body. These valves can streamline piping systems by allowing for flow direction changes without the need for multiple valves, effectively reducing energy consumption and pressure drop. They are particularly beneficial in chemical and processing industries, where altering fluid paths quickly and efficiently is crucial. This type of plug valve promotes operational flexibility and minimizes downtime during maintenance.
Eccentric Plug Valves
Eccentric plug valves, such as the DeZURIK Eccentric Plug Valves, are distinct due to their unique plug design that moves off-center, allowing for an unobstructed flow path and reduced resistance. These valves provide excellent tight shut-off capabilities and are known for handling solid or fibrous materials without clogging. Suitable for applications involving abrasive slurries, sewage, and wastewater, these valves are vital in industries where robust performance is required under challenging conditions.
Jacketed Plug Valves
Jacketed plug valves are designed to maintain process fluid temperatures by providing additional insulation around the valve body. This design is crucial for applications dealing with viscous or temperature-sensitive fluids that need consistent thermal control to prevent solidification or degradation. By circulating a heating medium through the jacket, these valves ensure the fluid flow remains unobstructed and efficient. Their construction, often in stainless or carbon steel, supports durability and effective thermal management.
Plug Valve Application
Plug valves are versatile components used widely to control the flow of fluids in various systems. These valves provide excellent performance in a wide range of applications and are available in materials such as carbon steel and stainless steel, enabling them to cater to diverse operational needs. Their ability to offer tight shut-off and control flow between ports makes them suitable for numerous industrial settings.
Quick Shut-Off Requirements
In settings where quick shut-off is critical, plug valves are the valves of choice. They are designed to provide an almost instantaneous stop to fluid flow, minimizing any potential loss or contamination. This feature is vital in preventing pressure drop and reducing energy consumption. This capability makes them an excellent choice for applications requiring frequent and rapid operation settings, ensuring operational efficiency and safety.
Industrial Use Cases
Plug valves are integral to industrial operations, offering robust performance in a range of applications. With sizes varying from 3 – 24 inches, they are adaptable to different systems and specifications. In industries where tight shut-off and precise flow rates are necessary, such as chemical processing, plug valves maintain the integrity of fluid flow while reducing the risk of product contamination. Their durability is enhanced by using materials like carbon steel and stainless steel, ensuring longevity in aggressive environments. Industrial applications also benefit from non-lubricated plug valves, which reduce maintenance requirements and offer enhanced reliability.
Factors to Consider When Choosing a Plug Valve
Plug valves are essential components in various industries, providing reliable flow control for numerous applications. When selecting a plug valve, understanding the specific needs and operational context is vital. Several factors, including the type of plug valve, construction materials, and desired flow rates, play a crucial role in determining the most suitable choice. Considering these aspects ensures optimal performance, minimizes pressure drop, and decreases energy consumption. By evaluating these critical factors, you can secure the right plug valve for your requirements and enhance system efficiency and longevity.
Specific Application Needs
Identifying the specific needs of your application is the first step in choosing the right plug valve. Different plug designs cater to varied requirements, including tight shut-off, high flow rates, or flow-directing possibilities. Typical applications range from chemical processing to oil and gas transportation, each with unique demands. Multi-port plug valves are ideal for systems needing more than one flow path without additional piping. Understanding these distinct needs allows for the selection of a plug valve that efficiently directs the flow of fluids and supports overall system functionality.
Construction Materials
The construction material of a plug valve is a decisive factor impacting its durability and suitability for particular operations. Common materials used in valve bodies include stainless steel and carbon steel. Stainless steel is preferred in environments with harsh chemicals and extreme temperatures. In contrast, carbon steel suits applications where cost-effective, reliable performance is paramount. Choosing the appropriate material ensures the plug valve withstands operational strains and reduces the risk of product contamination and valve damage.
Operating Pressure and Temperature
Operating pressure and temperature significantly influence the type of plug valve needed. Various plug valves are rated for different pressure ranges and temperature conditions, affecting their performance and safety. Ensuring your chosen valve can handle your system’s maximum and minimum pressure and temperature levels is crucial. Eccentric plug valves, such as the DeZURIK models, are well-suited for high-pressure environments, offering reliable performance even under demanding conditions.
Sealing Systems
Sealing systems within plug valves play a pivotal role in ensuring leak-tight performance and preventing fluid loss. Non-lubricated plug valves often utilize elastomeric or PTFE-lined seals to minimize leakage and extend the valve’s operational life. These seals provide effective sealing without the need for continuous lubrication, reducing maintenance efforts. Depending on the application type, choose sealing systems that offer the best balance of tight shut-off capabilities and operational efficiency. Proper sealing ensures minimal pressure drop and protects against undesired fluid flow between ports.
Advantages and Disadvantages of Plug Valves:
Beyond ensuring a tight shut-off, gas plug valves offer numerous benefits:
– Minimal Maintenance: Simple design results in fewer problems and reduced maintenance costs. Without lubrication needs, they are ideal for contamination-sensitive areas like food processing. Made from stainless or carbon steel, they’re durable.
– Wear Risks: Plug valves are efficient but susceptible to wear, especially with abrasive or corrosive fluids, damaging the plug and seating. Regular maintenance is crucial to extend their lifespan and efficiency.
– Versatility – You can use plug valves with large flow rates as well.
However, there are disadvantages of plug valves:
– Inefficiency in Throttling: They are unsuitable for throttling tasks, limiting their versatility in specific applications.
– High Actuation Force: They require more force to operate due to their high-friction, full-contact design, necessitating stronger actuators or increased manual effort, which can be inconvenient in some scenarios.
– Potential Galling: There is a susceptibility to galling, which can impair function over time.
– Reduced Port Size: The tapered plug design often results in a smaller port, which may not be ideal for all flow requirements.
Metal Injection Molding vs. Powder Metallurgy: A Comprehensive Comparison
In the realm of metal part manufacturing, Metal Injection Molding (MIM) and Powder Metallurgy (PM) stand out as two prominent techniques. Both processes utilize metal powders to fabricate components, yet they differ significantly in methodology, capabilities, and applications. Understanding these differences is crucial for engineers and manufacturers aiming to select the most suitable process for their specific needs.
Manufacturing Processes
Metal Injection Molding (MIM)
MIM is a hybrid manufacturing process that combines the versatility of plastic injection molding with the strength and integrity of powdered metallurgy. The process involves several key steps:
- Feedstock Preparation: Fine metal powders, typically less than 20 microns in size, are mixed with thermoplastic and wax binders to create a homogeneous feedstock.
- Injection Molding: The feedstock is heated and injected into molds to form “green parts,” which are near-net-shape components.
- Debinding: The binder materials are removed through thermal or solvent processes, resulting in “brown parts” that are porous and fragile.
- Sintering: The brown parts are heated to temperatures just below the melting point of the metal, causing the particles to fuse and densify, achieving final mechanical properties.
MIM is particularly advantageous for producing small, intricate parts in high volumes, offering excellent surface finish and dimensional accuracy.
Powder Metallurgy (PM)
PM is a traditional process that involves the following steps:
- Powder Production: Metal powders are produced through various methods, including atomization, reduction, and electrolysis.
- Blending: Different metal powders and additives are mixed to achieve desired properties.
- Compaction: The powder blend is compressed in a die under high pressure to form a “green compact.”
- Sintering: The green compact is heated in a controlled atmosphere to bond the particles metallurgically, enhancing strength and integrity.
PM is well-suited for producing simple, high-volume parts with consistent properties, often used in automotive and industrial applications.
Material Characteristics
Density and Porosity
- MIM: Achieves high-density parts, typically ranging from 95% to 99% of theoretical density, resulting in superior mechanical properties.
- PM: Generally results in parts with 80% to 90% density, which may be beneficial for applications requiring porosity, such as self-lubricating bearings.
Mechanical Properties
- MIM: Offers excellent mechanical strength, comparable to wrought materials, making it suitable for demanding applications.
- PM: While adequate for many applications, PM parts may exhibit lower strength due to inherent porosity.
Material Utilization
- MIM: Utilizes fine powders and achieves near-net-shape parts, minimizing material waste.
- PM: Also efficient in material usage, especially for simple geometries, but may require additional machining for complex features.
Cost Analysis
When evaluating manufacturing processes, cost considerations play a pivotal role. Both Metal Injection Molding (MIM) and Powder Metallurgy (PM) have distinct cost structures influenced by factors such as material expenses, tooling, production volume, and post-processing requirements.
Material Costs
- MIM: Utilizes fine metal powders combined with polymer binders, resulting in greater material costs. MIM feedstock can cost approximately $10–$12 per pound or higher.
- PM: Employs coarser metal powders without binders, making it more economical. PM materials typically cost around $1–$2 per pound.
Tooling and Equipment
- MIM: Requires specialized injection molding machines, debinding ovens, and sintering furnaces. The complexity of molds for intricate parts leads to higher tooling costs.
- PM: Involves simpler compaction dies and sintering equipment, resulting in lower initial tooling investments.
Production Volume and Economies of Scale
- MIM: Becomes cost-effective at high production volumes due to the amortization of tooling costs over large quantities.
- PM: Suitable for medium to high-volume production, especially for parts with simpler geometries.
Post-Processing Requirements
- MIM: Produces near-net-shape parts with excellent surface finish and dimensional accuracy, often eliminating the need for secondary operations.
- PM: May require additional machining or finishing processes to achieve desired tolerances and surface quality.
Applications and Industry Usage
The choice between MIM and PM often depends on the specific requirements of the application, including part complexity, mechanical properties, and production volume.
Metal Injection Molding (MIM)
Industries and Applications:
- Medical and Dental: Production of surgical instruments, orthodontic brackets, and implant components requiring high precision and biocompatibility.
- Aerospace: Manufacture of complex components like fittings, latches, and spray nozzles that demand high strength-to-weight ratios.
- Automotive: Creation of intricate parts such as fuel injector components, actuators, and locking mechanisms.
- Consumer Electronics: Fabrication of small, complex parts like connectors and housings with tight tolerances.
Powder Metallurgy (PM)
Industries and Applications:
- Automotive: Production of gears, bushings, and structural components where cost-effectiveness and material efficiency are paramount.
- Industrial Machinery: Manufacture of components like bearings and filters that benefit from the inherent porosity of PM parts.
- Aerospace: Creation of structural parts where simplicity and reliability are essential.
- Appliances and Tools: Fabrication of various components where high-volume production and cost savings are critical.
Advantages and Limitations
Understanding the strengths and weaknesses of both Metal Injection Molding (MIM) and Powder Metallurgy (PM) is crucial for selecting the appropriate manufacturing process for specific applications.
Metal Injection Molding (MIM)
Advantages:
- Complex Geometries: MIM excels at producing intricate and complex shapes that would be challenging or impossible with other manufacturing methods. This capability is due to the flexibility of the injection molding process, allowing for detailed features and thin walls.
- High Density and Strength: MIM parts typically achieve densities of 95–99% of theoretical density, resulting in mechanical properties comparable to wrought materials. This high density contributes to superior strength and durability.
- Excellent Surface Finish: The process yields parts with smooth surface finishes, often eliminating the need for secondary machining or finishing operations.
- Material Utilization: MIM generates minimal waste, utilizing nearly all the material in the final product, which is both cost-effective and environmentally friendly.
Limitations:
- High Initial Tooling Costs: The molds required for MIM are often expensive, especially for intricate designs, making the process more suitable for high-volume production to amortize the tooling investment.
- Size Constraints: MIM is generally limited to small to medium-sized parts, typically less than 100 grams, due to equipment limitations and the nature of the process.
- Material Limitations: Not all metals are suitable for MIM. Some materials may not sinter well or may have issues with binder removal, limiting the range of applicable materials.
Powder Metallurgy (PM)
Advantages:
- Cost-Effective for Simple Parts: PM is highly economical for producing simple, high-volume parts, especially when complex geometries are not required.
- Material Efficiency: The process utilizes over 97% of the starting material, minimizing waste and making it an environmentally friendly manufacturing option.
- Controlled Porosity: PM allows for the production of parts with controlled porosity, which is beneficial for applications like self-lubricating bearings and filters.
- Energy Efficiency: PM typically requires lower processing temperatures than other metal forming methods, leading to energy savings during production.
Limitations:
- Design Limitations: PM is generally limited to simpler shapes due to the constraints of the compaction process. Complex geometries may require additional machining or alternative manufacturing methods.
- Lower Density and Strength: PM parts often have lower densities at about 80–90% of theoretical density compared to MIM, which can result in reduced mechanical strength and a possibility that it may not be suitable for high-stress applications.
- Size Limitations: There are practical limits to the size of parts that can be produced using PM, often constrained by the capacity of the pressing equipment.\
Conclusion
Both metal injection molding and powder metallurgy offer unique advantages and are suited to different applications. MIM is ideal for producing small, complex parts with high strength and excellent surface finishes, making it suitable for industries like medical, aerospace, and electronics. However, it comes with higher initial costs and size limitations. Conversely, PM is cost-effective for manufacturing simple, high-volume parts with controlled porosity, commonly used in automotive and industrial applications. The choice between MIM and PM should be based on factors such as part complexity, required mechanical properties, production volume, and cost considerations. By understanding the strengths and limitations of each process, manufacturers can make informed decisions that align with their production goals and operational needs. Check out Align Manufacturing if you are looking for a place that provides high-precision metal injection molding solutions.
Understanding Manifolds: Applications in Oil and Gas Operations
In the oil and gas sector, manifolds are critical assemblies that consist of interconnected valves, pipes, and fittings. Their primary function is to control, distribute, and monitor the flow of fluids, such as oil, gas, and water, during various phases of operations, including exploration, drilling, production, and processing. By efficiently managing fluid flow, manifolds ensure operational safety, flexibility, and efficiency.
Core Functions of Manifolds
Manifolds serve several essential purposes in oil and gas operations:
- Flow Control: Regulating the direction and rate of fluid flow from multiple wells or equipment.
- Distribution: Routing fluids to appropriate processing facilities or storage units.
- Isolation: Allowing sections of the system to be shut off for maintenance or emergency response.
- Monitoring: Facilitating the measurement of pressure, temperature, and flow rates to ensure optimal operation.
Types of Manifolds and Their Applications
Understanding the different types of manifolds is crucial for selecting the appropriate system for specific operational needs:
1. Production Manifolds
Production manifolds collect fluids from multiple wells and direct them to processing facilities. They are designed to handle high-pressure flows and are essential for efficient production management.
2. Choke Manifolds
Choke manifolds regulate wellhead pressure using adjustable or fixed chokes. They are vital for controlling the flow rate from wells, especially during drilling and testing phases, ensuring safety and preventing blowouts.
3. Kill Manifolds
Kill manifolds are used to inject kill fluids into wells to control pressure during emergencies. They play a critical role in well control operations, allowing for the safe shutdown of wells when necessary.
4. Test Manifolds
Test manifolds isolate individual wells for performance testing. They enable operators to assess well productivity and reservoir characteristics without affecting the overall production system.
5. Injection Manifolds
Injection manifolds distribute fluids like water or gas into wells for enhanced oil recovery. They help maintain reservoir pressure and improve hydrocarbon extraction efficiency.
6. Block and Bleed Manifolds
Block and bleed manifolds are designed to isolate sections of piping for maintenance by blocking flow and bleeding off pressure. They ensure safety during equipment servicing and prevent contamination.
Design Considerations and Material Selection
Key Design Considerations for Manifolds
Designing manifolds for oil and gas operations requires meticulous attention to various factors to ensure safety, efficiency, and longevity. The following are critical considerations:
- Pressure Ratings: Manifolds must be designed to withstand the maximum operating pressures they will encounter, including transient pressure surges. Industry benchmarks such as Maximum Allowable Working Pressures (MAWP) reach up to 6000 psig, with operational temperatures ranging from -65°F to 1200°F.
- Material Selection: Choosing appropriate materials is vital to resist corrosion, erosion, and other environmental factors. Materials should be compatible with the fluids handled and the operational environment.
- Temperature Tolerance: Manifolds should be capable of operating effectively within the temperature ranges expected in the system, accounting for both ambient and process temperatures.
- Flow Capacity: The design must accommodate the required flow rates without causing excessive pressure drops or turbulence, ensuring efficient fluid distribution.
- Safety Features: Incorporating safety mechanisms such as pressure relief valves, isolation valves, and emergency shutdown systems is essential to protect personnel and equipment.
- Ease of Maintenance: Designs should allow for straightforward access to components for inspection, maintenance, and replacement, minimizing downtime and operational disruptions.
- Detailed Valve Configurations: Specific valve configurations, like the two, three, and five-valve setups, are crucial for controlling flow parameters and offering system flexibility. These arrangements impact pressure monitoring, calibration, isolation, and bleed functions, enhancing the manifold’s operational precision.
Standards and Certifications
- API 6A / API 16C: Wellhead, choke, and kill manifolds.
- API 600: Bolted bonnet steel gate valves
- API 6D: Pipeline valves
- ANSI/ASME B16.34: Valve design.
- ISO 14313: Ensures product quality and testing protocols.
- NACE MR0175 / ISO 15156: Covers materials for sour environments (when Hydrogen Sulfide, H₂S, is present).
Material Selection for Manifold Construction
Selecting the right materials for manifold construction is crucial for durability and performance:
- Carbon Steel: Commonly used due to its strength and cost-effectiveness, suitable for non-corrosive environments.
- Stainless Steel: Offers excellent corrosion resistance and is suitable for handling corrosive fluids. Grades like 316L are commonly used in harsh environments.
- Duplex Stainless Steel: Combines high strength with superior corrosion resistance, suitable for high-pressure and corrosive applications.
- Aluminum: Lightweight and corrosion-resistant, aluminum is suitable for low-pressure applications and where weight reduction is a priority.
- Ductile Iron: Known for its good machinability and corrosion resistance, making it a viable option for certain applications
- Plastics and Polymers: Suitable for extremely corrosive fluids but limited in high-temperature or high-pressure use.
Skid-Mounted Manifolds
Skid-mounted manifolds are pre-assembled units mounted on a frame or skid, offering several advantages:
- Ease of Installation: Pre-fabricated units can be quickly installed on-site, reducing downtime.
- Mobility: Skid-mounted systems can be relocated as needed, providing flexibility in operations.
- Compact Design: Efficient use of space, especially beneficial in offshore or space-constrained environments.
Below is an image of a skid-mounted production manifold:
Operational Benefits and Strategic Importance of Manifolds
Enhancing Operational Efficiency
Manifolds play a pivotal role in streamlining oil and gas operations by centralizing control over fluid distribution. This centralization reduces the complexity of piping systems, minimizes potential leak points, and facilitates easier monitoring and maintenance. By directing the flow of oil, gas, and water through a unified system, operators can achieve smoother transitions between different operational phases, such as drilling, testing, and production.
Improving Safety Measures
Safety is paramount in oil and gas operations, and manifolds contribute significantly to this aspect. By allowing for the isolation of specific sections of the pipeline, manifolds enable maintenance and emergency interventions without halting the entire system. This capability not only ensures the safety of personnel but also protects the integrity of the equipment and the environment.
Cost-Effectiveness and Resource Optimization
Implementing manifold systems leads to cost savings by reducing the need for extensive piping networks and associated components. The modular nature of manifolds allows for scalable operations, meaning facilities can adjust their systems based on current production needs without significant overhauls. This adaptability ensures optimal use of resources and capital.
Facilitating Advanced Monitoring and Automation
Modern manifolds are often equipped with sensors and automation technologies that provide real-time data on pressure, flow rates, and temperature. This information is crucial for predictive maintenance, allowing operators to address potential issues before they escalate into major problems. Additionally, automated systems can adjust operations dynamically, enhancing efficiency and reducing manual intervention.
Supporting Environmental Compliance
With increasing environmental regulations, manifolds assist in ensuring compliance by providing precise control over fluid handling. Their ability to prevent leaks and spills aligns with environmental protection standards, and their integration with monitoring systems allows for accurate reporting and rapid response to any anomalies.
Conclusion
In conclusion, manifolds are integral to the efficiency, safety, and functionality of oil and gas operations. Understanding their core functions, types, design considerations, and material selection is essential for optimizing their performance in various applications. By leveraging advanced technologies and adhering to safety and environmental standards, the oil and gas industry can enhance operational efficiency while ensuring the safety of personnel and the environment. Check out Align Manufacturing to find out more about manifold components in the oil and gas industry.
Gate Valve 101: Understanding Gate Valves and Their Applications
Gate valves are essential components in fluid control systems, designed primarily to start or stop the flow of liquids through pipelines. These valves operate by lifting a gate out of the fluid’s path, providing a straight-through passage when fully open, which results in minimal pressure drop. This characteristic makes gate valves ideal for applications requiring a free flow of fluid. Commonly used in industries such as oil and gas, water treatment, and manufacturing, gate valves are favored for their durability and ability to provide tight sealing. Their bi-directional flow design allows them to be used in systems where they remain either fully open or fully closed, rather than for flow regulation.
Gate Valve Components: Anatomy of a Gate Valve
Understanding the main components of a gate valve helps in proper selection, maintenance, and troubleshooting.
- Body: The main pressure-retaining structure that houses the internal parts and connects to the piping system.
- Bonnet: Attached to the body, it encloses the valve’s stem and forms a seal. Common types include bolted, union, and pressure seal bonnets.
- Gate or Disc: The actual flow-blocking component that moves vertically to open or close the valve. Can be solid, flexible, or split.
- Stem: Connects the actuator or handwheel to the gate, transmitting motion to open or close the valve.
- Seat Rings: Provide the sealing interface between the gate and the body. Can be integral or replaceable.
- Packing and Gland: Prevent leakage around the stem and are adjustable to maintain a tight seal.
- Handwheel or Actuator: Allows manual or automated operation of the valve.
Each part plays a critical role in ensuring the functionality, efficiency, and longevity of the gate valve.
Material Compatibility: Selecting the Right Gate Valve Material
Choosing the appropriate material for a gate valve is crucial, as it determines the valve’s suitability for specific fluids, temperatures, and pressures. Different materials offer varying levels of corrosion resistance, strength, and temperature tolerance. Here’s an overview of common gate valve materials and their applications:
Stainless Steel
Stainless steel gate valves are renowned for their excellent corrosion resistance and strength. They are suitable for a wide range of temperatures and are often used in chemical processing, food and beverage, and pharmaceutical industries. Their resistance to corrosion makes them ideal for applications involving corrosive fluids.
Carbon Steel
Carbon steel gate valves are robust and cost-effective, making them suitable for high-pressure applications. However, they are less resistant to corrosion compared to stainless steel. These valves are commonly used in the oil and gas, petrochemical, and power generation industries.
Cast Iron
Cast iron gate valves are economical and provide good resistance to wear. They are typically used in water distribution systems, HVAC, and fire protection systems. However, they are not suitable for high-pressure or high-temperature applications due to their brittleness.
Bronze and Brass
Bronze and brass gate valves offer good corrosion resistance and are often used in marine environments and potable water systems. They are suitable for low to moderate pressure applications and provide reliable performance in systems where dezincification resistance is important.
Steel Alloys
Gate valves made from steel alloys are designed for high-temperature and high-pressure applications. They are commonly used in power plants, refineries, and chemical processing facilities. Their enhanced mechanical properties make them suitable for severe service conditions.
Selecting the right material involves considering factors such as the nature of the fluid, operating temperature and pressure, and potential for corrosion. Proper material selection ensures the longevity and reliability of the gate valve in its intended application.
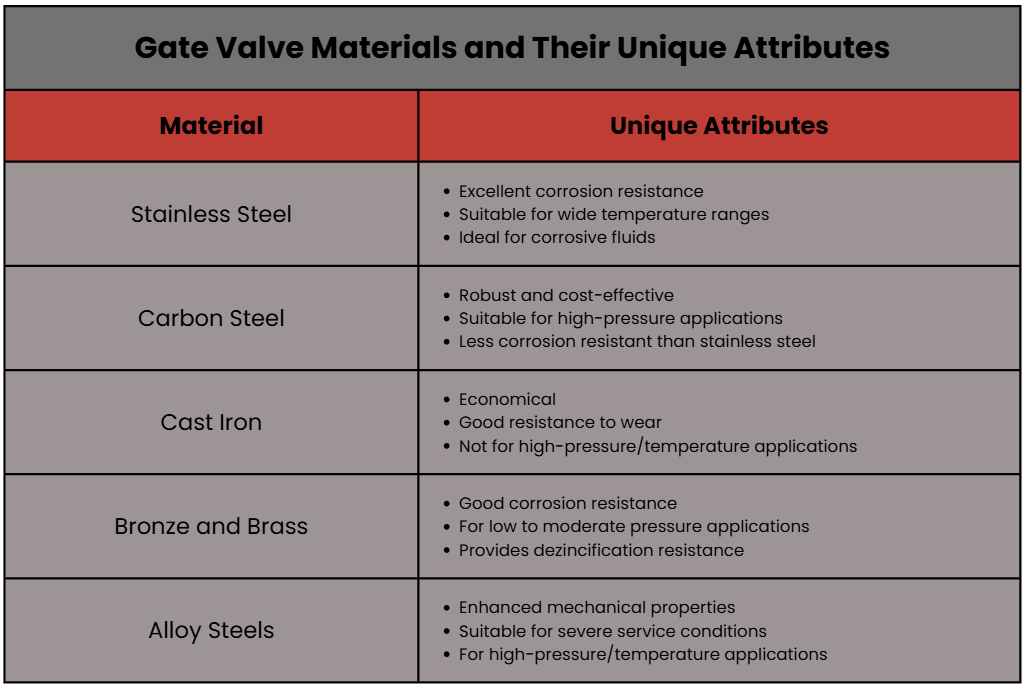
Valve Size & Pressure Ratings: Matching Valve to System Requirements
Choosing the appropriate valve size and pressure rating is crucial for ensuring optimal performance and safety within a piping system.
Valve Sizes
Gate valves are available in a wide range of sizes, commonly ranging from DN15 (1/2 inch) to DN600 (24 inches). The choice of size depends on the flow requirements of the system. For instance:
- Smaller sizes like DN15 or DN25 are suitable for residential plumbing.
- Larger sizes like DN300 or DN600 are used in industrial pipelines and municipal water systems.
Pressure Ratings
Pressure ratings indicate the maximum pressure a valve can handle at a specific temperature. The American National Standards Institute (ANSI) classifies pressure ratings into different classes, such as Class 150, Class 300, Class 600, etc. As the class number increases, the maximum pressure in pounds per square inch (psi) that can be handled at a reference temperature (usually 100°F) also increases. Smaller valve sizes are used in homes, while larger ones are used in industrial pipelines.
- Class 150: Typically handles pressures up to 285 psi at 100°F (38°C)
- Class 300: Handles pressures up to 740 psi at 100°F (38°C)..
It’s essential to select a valve with a pressure rating that exceeds the maximum operating pressure of the system to ensure safety and longevity.
Stem Design: Rising vs. Non-Rising Stems
The stem design of a gate valve affects its installation, maintenance, and operation. There are two primary stem designs: rising stem and non-rising stem.
Rising Stem
In rising stem gate valves, the stem moves up and down as the valve is operated. This movement provides a visual indication of the valve’s position. Do note that when the stem is visible, the valve is open, and when it is not, the valve is closed.
Advantages:
- Position Indication: Easy to determine the valve’s status.
- Ease of Maintenance: Exposed stem threads are accessible for lubrication.
Considerations:
- Space Requirements: Requires more vertical space for operation.
Non-Rising Stem
In non-rising stem gate valves, the stem remains stationary, and the gate moves along the stem’s threads. This design is compact, making it suitable for installations with limited space.
Advantages:
- Space Efficiency: Ideal for underground or confined installations.
- Protection: Stem threads are enclosed, reducing exposure to external elements.
Considerations:
- Position Indication: Does not provide a visual cue of the valve’s status; external indicators may be necessary
Understanding the differences between rising and non-rising stem designs helps in selecting the appropriate valve for specific applications, considering factors like space constraints, maintenance requirements, and operational preferences.
Bonnet Types: Sealing and Maintenance Considerations
The bonnet of a gate valve is a critical component that houses the stem and provides a leak-proof closure for the valve body. Different bonnet designs offer varied advantages in terms of sealing capabilities, maintenance ease, and suitability for specific applications.
Bolted Bonnet
Bolted bonnets are the most common design, where the bonnet is bolted to the valve body using studs and nuts, with a gasket in between to ensure a tight seal.
Advantages:
- Ease of Maintenance: The bolted design allows for straightforward disassembly, making inspection and maintenance more convenient.
- Versatility: Suitable for a wide range of pressures and temperatures, making it applicable in various industries.
Considerations:
- Potential for Leakage: The seal relies on the integrity of the gasket and the torque applied to the bolts. Over time, thermal cycling and pressure fluctuations can compromise the seal, leading to potential leaks.
Union Bonnet
Union bonnets are designed with a threaded union nut that holds the bonnet to the valve body, providing a pressure-tight seal.
Advantages:
- Compact Design: Ideal for small-sized valves and applications where space is limited.
- Ease of Disassembly: The union nut allows for quick removal of the bonnet for inspection and maintenance.
Considerations:
- Pressure Limitations: Generally suitable for low to medium pressure applications.
Pressure Seal Bonnet
Pressure seal bonnets are specifically designed for high-pressure applications. The unique feature of this design is that the internal pressure enhances the seal between the bonnet and the valve body
Advantages:
- Enhanced Sealing: As internal pressure increases, the seal becomes tighter, reducing the risk of leakage.
- Suitable for High-Pressure Applications: Commonly used in power generation, oil and gas, and petrochemical industries.
Considerations:
- Maintenance Complexity: Disassembly can be more complex compared to other bonnet types, requiring careful handling to avoid damage to the sealing surfaces.
End Connection Types: Integrating Valves into Piping Systems
The end connection of a gate valve determines how it integrates into a piping system. The choice of connection affects installation, maintenance, and the overall integrity of the system.
Flanged Connections
Flanged ends are among the most commonly used valve connections, featuring protruding rims, also known as flanges, that are bolted together with a gasket in between to ensure a leak-proof seal.
Advantages:
- Ease of Installation and Removal: Flanged connections allow for easy disassembly, facilitating maintenance and inspection.
- Versatility: Suitable for a wide range of pressures and temperatures, and compatible with various pipe sizes.
Considerations:
- Space Requirements: Flanged connections require more space due to the size of the flanges and the need for bolt tightening.
Threaded Connections
Threaded ends involve male and female threads on the valve and pipe, screwed together to form a seal.
Advantages:
- Simplicity: Easy to install without the need for specialized tools or equipment.
- Cost-Effective: Generally less expensive than flanged or welded connections.
Considerations:
- Pressure Limitations: Typically used for low-pressure applications.
- Maintenance Challenges: Disassembly can be more challenging, and repeated assembly or disassembly can wear out the threads, leading to potential leaks.
Welded Connections
Welded ends involve permanently joining the valve to the pipe through welding, creating a strong, leak-proof connection.
Advantages:
- High Integrity Seal: Ideal for high-pressure and high-temperature applications where leakage is not acceptable.
- Compact Design: Eliminates the need for flanges, saving space.
Considerations:
- Maintenance Complexity: Disassembly requires cutting the valve out of the pipeline, making maintenance more time-consuming and costly.
- Installation Requirements: Requires skilled labor and proper welding equipment.
Understanding the various bonnet and end connection types is essential for selecting the appropriate gate valve for specific applications, ensuring optimal performance, safety, and ease of maintenance.
Conclusion
Gate valves play a vital role in fluid control systems across various industries. Understanding their design features, material compatibility, size and pressure ratings, stem designs, bonnet types, and end connection options is crucial for selecting the right gate valve for your application. Check out Align Manufacturing for more information on gate valves that will help you ensure optimal performance, safety, and longevity in your fluid control systems.
Metal Injection Molding (MIM) Guide
What it is, how it works, when to use it, and how it compares to alternative manufacturing methods
Why MIM Matters in Modern Manufacturing
As consumer products become more compact, functional, and refined, the components inside them must meet higher standards—mechanically and visually. That’s where Metal Injection Molding (MIM) stands out.
MIM is a modern manufacturing method that blends the precision of machining with the scalability of injection molding. It’s designed for small, complex metal parts that need to be produced in high volumes, with the performance characteristics of solid metal.
For brands working on everything from wearables to medical devices or even firearm components, MIM offers a reliable path from prototype to scale. Let’s explore how this innovative process works and why it might be the manufacturing solution your next product needs.
What Is Metal Injection Molding?
Metal Injection Molding (MIM) is best described as plastic injection molding for metal.
Instead of molten metal, the process uses metal powder mixed with a plastic binder to form a moldable pellet (feedstock). These pellets are injected into a mold—just like plastic parts—and then go through a heat-driven process to burn off the plastic and fuse the metal, creating a fully dense component.
Think of it as a three-phase process:
- Mold the shape using a plastic-metal hybrid
- Remove the plastic binder
- Sinter the part into solid metal
This gives you the freedom to design intricate geometries, internal features, and tight tolerances that would be expensive (or impossible) to CNC.
Understanding these fundamentals helps explain why MIM offers unique advantages for certain applications. Now, let’s look at exactly how the process unfolds…
How the MIM Process Works: Step-by-Step
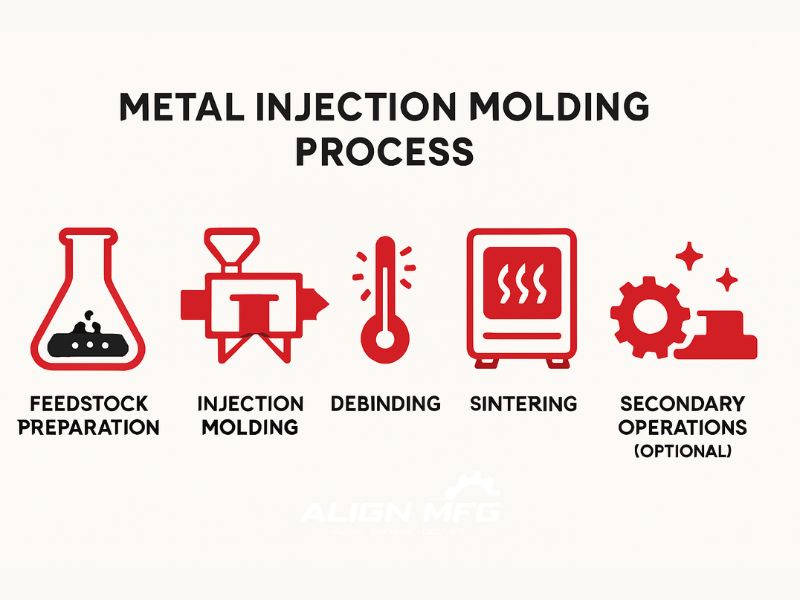
1. Feedstock Preparation
Fine metal powders (typically 1-20 μm particle size) are precisely blended with thermoplastic binders (usually a combination of polymers, waxes, and surfactants) in a ratio of approximately 60% metal by volume (90% by weight). This mixture is compounded into homogeneous pellets that can be fed into standard injection molding equipment.
2. Injection Molding
These feedstock pellets are heated to 150-180°C and injected into precision molds at pressures ranging from 50-200 MPa. The result is a “green part”—the shape is formed, but it’s not yet solid metal. At this stage, the part is approximately 15-20% larger than the final desired dimensions to account for later shrinkage.
3. Debinding
The green part undergoes a carefully controlled debinding process to remove the binder material:
- Primary Debinding: Often uses solvent extraction (water, ethanol, or specialized solvents) to remove 30-40% of the binder
- Secondary Debinding: Thermal debinding at 200-600°C removes the remaining binder, leaving behind a fragile “brown part” that is approximately 60% porous
4. Sintering
This brown part is placed in a precisely controlled atmosphere furnace and heated to near the melting point of the metal (typically 1,200–1,400°C). During this process:
- The metal particles fuse together through solid-state diffusion
- The part shrinks uniformly by 15-20% in all dimensions
- Density increases to 96-99% of theoretical full metal density
- The microstructure develops to provide the desired mechanical properties
5. Secondary Operations (Optional)
Depending on application requirements, MIM parts may undergo additional processing:
- Heat Treatment: Annealing, hardening, or tempering to optimize mechanical properties
- Precision Machining: For critical features requiring tighter tolerances than as-sintered
- Surface Treatments: Including plating, coating, polishing, or PVD for enhanced performance
- Quality Inspection: Dimensional verification, material testing, and non-destructive evaluation
Process Quality Control
Throughout the MIM process, manufacturers implement rigorous quality control measures:
- Feedstock testing for consistent rheological properties
- In-process monitoring of molding parameters
- Statistical process control for dimensional stability
- Microstructural analysis and mechanical testing of finished parts
This careful, multi-step process results in parts with specific characteristics that make MIM particularly valuable in certain industries and applications.
Where MIM Shines: Ideal Applications
MIM is particularly suited for:
- High-volume production of small metal parts
- Intricate designs that would be costly to machine
- Applications where mechanical strength, complexity, and cost need to balance
Common industries using MIM include:
- Firearms: Triggers, safeties, linkages
- Automotive: Small actuators, gears, sensor housings
- Medical: Surgical instruments, dental brackets, implants
- Consumer Electronics: Hinges, structural frames, wearable components
To determine if your component is suitable for MIM, it helps to understand the specific parameters and design considerations that optimize the process.
Part Characteristics and Design Guidelines
- ✅ Size Range: Most MIM parts range from 2 grams to 100 grams, with optimal performance for small, complex components
- ✅ Tolerances: MIM can hold tolerances of ±0.3% (minimum of ±0.075mm/0.003″), which is excellent for precise applications
- ✅ Geometries: Undercuts, thin walls (down to 0.5mm), logos, internal features, and complex shapes that would be difficult or impossible to machine
- ✅ Material Density: MIM produces parts with 96-99% density, significantly higher than many other metal forming processes
- ✅ Surface Finish: As-sintered parts typically achieve 1-2 μm Ra without additional finishing
Compatible Materials for MIM
MIM works with a wide range of metal powders, categorized into four main groups:
- Stainless Steels
- 316L (excellent corrosion resistance, medical applications)
- 17-4PH (high strength, good corrosion resistance)
- 420 (high hardness, moderate corrosion resistance)
- 440C (excellent wear resistance)
- Low Alloy and Carbon Steels
- 4140 (high fatigue strength)
- 8620 (excellent carburizing properties)
- 1070 (high carbon for wear applications)
- 4605 (high strength, good toughness)
- Specialty Alloys
- Titanium (Ti-6Al-4V, medical and aerospace)
- Inconel (high temperature applications)
- Kovar (controlled expansion for electronics)
- Tungsten alloys (high density applications)
- Soft Magnetic Alloys
- Fe-Ni alloys (high magnetic permeability)
- Fe-Si (low core loss)
- Soft ferrites (high frequency applications)
Design Tips for MIM Success:
- Maintain consistent wall thickness (ideally between 0.5-6mm)
- Design with uniform cross-sections where possible
- Account for 15-20% shrinkage during sintering
- Include draft angles of 0.5° or greater
- Avoid sharp corners (use radii of at least 0.25mm)
- Consider gating locations in the design phase
With these characteristics in mind, how does MIM compare to other common manufacturing methods? This comparison highlights where MIM truly offers an advantage.
MIM vs. CNC vs. Die Casting
Feature | MIM | CNC Machining | Die Casting |
Volume Suitability | High (10k+ parts) | Low to medium | Medium to high |
Design Complexity | Very high | High | Moderate |
Material Density | ~98% solid metal | 100% | Typically lower |
Surface Finish | Smooth, uniform | Variable | Good |
Setup Cost | Moderate (tooling required) | Low | High |
Per-Part Cost | Low (at scale) | High | Moderate |
Use MIM when your part is:
- Small and complex
- Needed in volume
- Doesn’t justify expensive machining
- Requires good mechanical properties
While the advantages are compelling, being aware of MIM’s limitations helps ensure you’re making the right manufacturing choice.
Advantages and Limitations of MIM
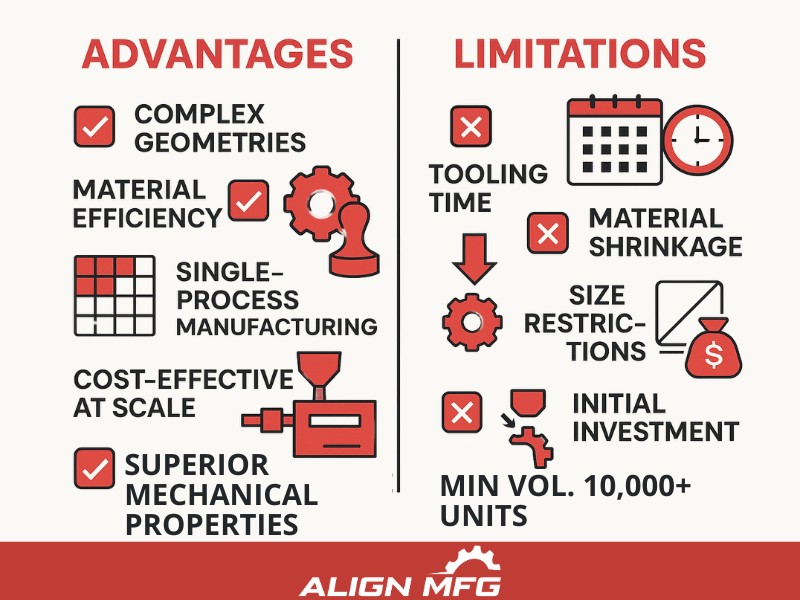
Key Advantages
- Complex Geometries: MIM can produce intricate shapes that would be difficult or impossible with other methods
- Material Efficiency: Up to 98% of material can be converted to usable parts, reducing waste compared to machining
- Single-Process Manufacturing: Complex parts can be produced in one go, eliminating the need for assembly of multiple components
- Cost-Effective at Scale: For high volumes, MIM can be more economical than investment casting, machining, and sometimes even stamping
- Superior Mechanical Properties: Parts feature excellent strength, hardness, and density comparable to wrought metals
- Excellent Surface Finish: As-sintered parts typically have smooth surfaces requiring minimal post-processing
Limitations to Consider
- Tooling Time: Expect 6–10 weeks for tool creation
- Material Shrinkage: Parts shrink ~15–20% during sintering—Design for Manufacturability (DFM) is essential
- Minimum Volume: MIM makes most sense at 10,000+ units annually
- Size Restrictions: Generally limited to small parts under 100 grams
- Initial Investment: Tooling costs can be significant, though they’re amortized over large production runs
- Limited Material Selection: While diverse, not all metal alloys are compatible with the MIM process
MIM vs. Alternative Metal Manufacturing Processes
When considering Metal Injection Molding, it’s helpful to understand how it compares to other metal manufacturing processes:
Process | Advantages over MIM | Disadvantages compared to MIM |
Die Casting | Faster cycle times, larger parts possible | Lower material properties, more porosity, fewer material options |
Investment Casting | Larger parts, wider material range | Higher cost per part, lower detail resolution |
Metal 3D Printing (DMLS) | No tooling costs, design freedom | Much higher per-part cost, slower production, surface finish limitations |
Metal Binder Jetting | Larger build volumes | Lower density, requires infiltration for full density |
CNC Machining | No tooling needed, 100% density | Expensive for complex geometries, material waste, limited internal features |
Metal Stamping | Very high production rates | Limited to thin, flat parts with simple geometries |
Brands often work with manufacturing partners like Align to get early design input, manage tooling, and prevent production issues. This partnership approach helps mitigate risks while maximizing the benefits MIM can offer.
Industry Applications and Case Studies
Automotive Industry
MIM components are widely used in automotive applications, including:
- Powertrain Components: Turbocharger vanes, fuel injector parts, valve components
- Safety Systems: Airbag initiators, seatbelt components, sensor housings
- Interior Hardware: Gear selectors, switch components, decorative trim parts
Case Study: A major automotive manufacturer replaced a machined stainless steel transmission component with a MIM alternative, reducing part cost by 43% while improving wear resistance through better material uniformity.
Medical and Dental Sector
The biocompatibility and excellent surface finish of MIM make it ideal for:
- Surgical Instruments: Forceps, hemostats, endoscopic tools
- Implantable Devices: Orthopedic implant components, dental brackets
- Diagnostic Equipment: Precision components for medical devices
Case Study: A medical device company utilized MIM to produce titanium components for surgical tools, achieving complex geometries with thin walls that would have been prohibitively expensive to machine.
Firearms Industry
MIM has revolutionized firearms manufacturing for components like:
- Triggers and Fire Control Groups: Complex geometries with precise tolerances
- Hammers and Sears: High-wear components requiring excellent mechanical properties
- Safety Mechanisms: Intricate components with precise operational requirements
Case Study: A leading firearms manufacturer converted 14 different machined components to MIM, reducing production costs by over 60% while maintaining all performance specifications.
Consumer Electronics
As devices become smaller and more feature-rich, MIM is increasingly used for:
- Hinge Mechanisms: In smartphones, laptops, and wearables
- Structural Frames: For strength in compact devices
- Heat Sink Components: Thermal management in small form factors
Case Study: A smartwatch manufacturer implemented MIM for their watch case components, achieving complex aesthetics with integrated structural functionality that couldn’t be produced using alternative methods.
Final Thoughts: Is MIM Right for Your Product?
If your product includes small, high-detail metal components and you’re planning to scale, MIM could dramatically cut costs while improving part quality and consistency.
It’s particularly compelling for:
- Consumer brands scaling hardware production
- Product teams converting from CNC to something more scalable
- Engineers needing structural performance in a small form factor
- Designers seeking to consolidate multiple parts into single components
Decision Framework for MIM Implementation
When deciding whether MIM is right for your product, consider these key factors:
- Production Volume
- Under 50,000 units/year: Consider machining or metal 3D printing
- 50,000-1
- 0,000 units/year: MIM begins to be competitive, especially for complex parts
- Over 100,000 units/year: MIM typically offers significant cost advantages
- Part Complexity
- Simple geometries: May be better suited for traditional manufacturing
- Moderate complexity: Compare MIM with machining based on volume
- High complexity: MIM likely offers substantial advantages, especially with internal features
- Material Requirements
- Standard alloys: Readily available in MIM
- Specialized properties: Verify compatibility with your MIM supplier
- Certification requirements: Discuss material certification capabilities early
- Timeline Considerations
- Prototype phase: 2-4 weeks for initial samples
- Tooling development: 6-10 weeks for production tooling
- Production ramp-up: 2-4 weeks after tooling approval
- Cost Structure Analysis
- Initial investment: $15,000-$50,000 for tooling (depending on complexity)
- Per-part cost: Typically 30-60% lower than machining at volume
- Total cost of ownership: Consider assembly elimination and secondary operation reduction
The best approach is to consult with manufacturing experts early in your design process. They can help evaluate your specific requirements and determine if MIM offers the optimal balance of cost, quality, and manufacturability for your application.
🔗 Explore Align’s MIM Capabilities
Looking for help with MIM design, sourcing, or production? Align can manage your entire Metal Injection Molding process—from design validation to delivery.