Posts by Casey Ross
Align MFG Vietnam Expands Global Footprint with New Strategic Office in Hồ Chí Minh
Align Manufacturing proudly announces the expansion of its global operations with the opening of its new Align MFG Vietnam strategic office at Nguyễn Văn Luông, Phường 12, Quận 6, in former District 6, Hồ Chí Minh City. This three‑story facility, located just three minutes from the Vòng Xoay Phú Lâm–27A Kinh Dương Vương bus stop, is designed to enhance operations, quality control, logistics, inspection, and sourcing, all under one roof. Featuring a meeting room, employee lounge, and balcony space, it reflects Align’s commitment to operational excellence in a thriving regional hub.
Prime Location: District 6, Phú Lâm Intersection and Connectivity
Directly adjacent to the bustling Phú Lâm rotary and within minutes of key arterial roads like Kinh Dương Vương, the new office lies in a strategic logistics corridor of Ho Chi Minh City. The area bridges the city center with major industrial zones, and lies near Saigon Port, Vietnam’s busiest container port and a key gateway for southern exports.
Since the July 1, 2025 merger, Ho Chi Minh City expanded to annex former Bình Dương and Bà Rịa–Vũng Tàu provinces, elevating its role as Vietnam’s top industrial and trade hub. District 6 offers easy access to major highways and inland logistic corridors, providing fast connections westward toward Trung Luong Expressway and southward to the Mekong Delta.
Office Design & Facilities: Collaboration, QC, Logistics Hub
The three‑level layout enhances both efficiency and employee experience. On the ground floor, the logistics and inspection teams operate with direct receipt and outgoing shipments flow. The middle floor houses quality control, inspection bays, and sourcing coordination, facilitating data-driven decision-making. The top floor includes a meeting room for clients and partners, a balcony overlooking the neighborhood, and a lounge area that fosters employee engagement.
By centralizing operations, Align MFG ensures faster feedback loops, tighter quality control, and streamlined processes, ideal for high-margin industries where responsiveness and precision matter.
Why Vietnam: Manufacturing Growth, Trade Diversification, Strategic Hub
Vietnam’s manufacturing sector contributes over 20% of GDP, and in 2022 alone industrial output grew nearly 9% year-over-year despite pandemic challenges. As of mid‑2025, manufacturing and construction employed 17.4 million workers, accounting for 33.4% of total national employment.
Vietnam raised its 2025 GDP growth goal from 6.5% to between 7% and 8%, fueled by stronger manufacturing output and foreign direct investment, especially in processing-related industries.
Foreign investment continues to pour in: by Q3 2024, manufacturing and processing accounted for ~63% of total FDI (≈ US $17.5B). And in the first half of this year FDI reached $21.5B a 36.2% rise year on year.
Align MFG’s Manufacturing Excellence: Smart Processes and High Standards
Align MFG is positioning itself at the forefront of Vietnam’s manufacturing shift into Industry 4.0. The national strategy accelerates adoption of AI, IoT, data analytics, and automation to modernize production lines. The domestic smart manufacturing market, valued at US $116.8 billion in 2024, is projected to grow at 10.7% CAGR through 2033, reaching nearly US $304 billion.
Within Vietnam, smart factories integrate lean manufacturing driven by AI-enabled SOPs and real-time monitoring, delivering measurable gains in productivity and defect reduction.
Vietnam’s major industrial hubs are transforming into smart industrial parks. Notably:
- Saigon Hi‑Tech Park (HCMC) is a dedicated high‑technology cluster just 15 km from downtown, hosting global leaders like Intel and Nidec, integrating digital connectivity and streamlined customs support for chip assembly and advanced electronics work.
- VSIP III (Bình Dương) stands out with its 50-hectare solar farm, closed‑loop wastewater systems, smart logistics networks, and carbon‑neutral target factories with LEGO’s global first located here.
- Amata Long Thanh (Đồng Nai) is built from the ground up on eco-IP principles, combining Industry 4.0-ready infrastructure with resource-efficient planning, renewable power, and ESG-aligned facilities.
- WHA Industrial Zone (Nghe An) offers smart utilities, real-time environmental monitoring, blockchain energy solutions, and biotech-enabled water treatment, all designed to meet global eco-industrial standards.
Vietnam’s government supports digital transformation through wide deployment of 5G networks in industrial parks, enabling autonomous inspection robots, edge computing, and real-time monitoring systems which are crucial for precision operations in sectors like semiconductors and electronics.
Smart industrial parks also lead in circular economy approaches. Pilot zones implemented with UNIDO support have collectively saved significant energy and water, reused resources, and cut CO₂ emissions, all while enabling businesses to scale sustainably.
Target Industries: Electronics, Semiconductors, Textiles & EV Components
Vietnam’s electronics sector has emerged as a powerhouse, generating $134.5 billion in exports in 2024, and reaching $60.8 billion by May 2025, representing a 39% year‑on‑year growth. It ranks as the world’s fifth-largest exporter of electronics and computer components, second in mobile phone and parts exports.
The country currently hosts over 174 FDI projects in semiconductors and packaging, positioning Vietnam as a rising global chip ATP hub. Major investors like Amkor Technology and Hana Micron are investing billions, aiming to push Vietnam’s global chip packaging share from 1% in 2022 to 8–9% by 2032.
Additional industrial sectors such as textiles, garments, and emerging EV components are also expanding steadily, supported by growing FDI and domestic capabilities. Align MFG’s QC-inspection-sourcing model aligns well with the precision requirements of these high-value sectors.
Supply Chain & Logistics Advantage: Proximity to Markets & Infrastructure
The new Ho Chi Minh City office is strategically placed near Saigon Port and arterial roads like Kinh Dương Vương, bridging city manufacturing hubs to inland waterways and industrial zones. Vietnam operates 44 seaports, handling up to 500 million tonnes annually, and 22 airports (12 international) to support global exports.
Regionally, the Mekong Delta logistics market alone is forecast to reach US $7.8 billion in 2025, growing to $12.5 billion by 2030 at ~8.2% CAGR. The government is expanding expressways, targeting multi-hundred kilometers connecting Delta routes, and modernizing inland waterway transport to boost export efficiency.
Total Vietnamese logistics costs remain high, estimated at 18–20% of GDP, compared to a global average of ~10.6%. Yet, Align MFG’s close-in urban location allows it to mitigate transport inefficiencies, reduce lead times, and maintain tighter control across operations.
Strategic Positioning: Vietnam as China-Plus-One Supply Chain Hub
With increasing trade tensions and supply chain realignment, global manufacturers are shifting operations from China to more stable and cost-effective locations. Vietnam has benefited disproportionately, surpassing India in capturing these relocations. It now serves as a preferred alternative, backed by central planning, streamlined regulation, and a proven track record with companies like Samsung, Intel, and Apple.
Vietnam’s electronics output, $134.5 billion in 2024, is more than triple the size of India’s comparable sector despite population differences, underscoring the country’s manufacturing efficiency and export orientation.
However, geopolitical uncertainty remains: agreed U.S. tariffs of 20% on Vietnamese exports and 40% on goods shipped through Vietnam, highlight inherent trade risk. Despite that, Vietnam’s low labor costs, improving infrastructure, and manufacturing momentum continue to attract major investments.
Align MFG’s Vision and Vietnam’s Smart Manufacturing Trajectory
Vietnam’s transition to smart manufacturing is gathering pace. Digital technologies, IoT, robotics, AI-enabled SOPs, are being integrated into inspection, analytics, and sourcing workflows. The smart manufacturing market, already valued at $116.8 billion in 2024, is projected to grow at 10.7% CAGR through 2033.
Align MFG Vietnam’s office is designed to support this evolution by connecting clients to reliable and affordable manufacturing solutions for projects of all sizes.
Looking ahead, Align is positioned to deepen partnerships with key players in electronics, EV components, and precision industries flowing through Ho Chi Minh City’s manufacturing corridors. The office also places Align at the junction of expanding transport projects, like the Trung Lương‑Mỹ Thuận and Mỹ Thuận–Cần Thơ expressways, enhancing access to the Mekong Delta corridor and export nodes.
By leveraging proximity to cutting-edge smart industrial parks, efficient logistics infrastructure, and rapidly expanding high-tech sectors, Align MFG is positioned to drive superior value for partners and clients alike. This strategic presence in Ho Chi Minh City affirms Align’s commitment to innovation, collaboration, and excellence, reinforcing its role as a pivotal player in Vietnam’s journey toward becoming a global manufacturing powerhouse.
Grades of Stainless Steel: Types, Properties, and Applications
Stainless steel is a versatile and corrosion-resistant alloy composed primarily of iron, chromium, and other elements such as nickel, molybdenum, and carbon. Its unique properties make it indispensable across various industries, including construction, automotive, medical, and kitchenware. The specific grades of stainless steel determine their mechanical properties, corrosion resistance, and suitability for particular applications.
Stainless steel, a family of iron-based alloys, is distinguished by its resistance to corrosion. This resistance stems from the formation of a stable passive layer, which shields the underlying metal from the effects of air and moisture, unlike other ferrous alloys.. This rust resistance makes it a preferred material for many applications, including outdoor structures, aqueous environments, food service, and high-temperature uses.
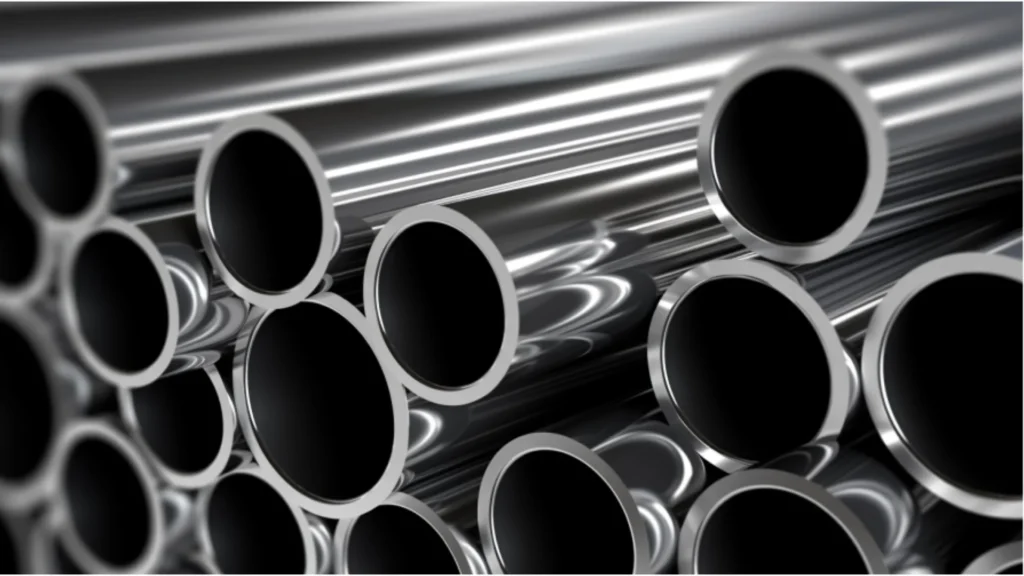
How Is Stainless Steel Made?
Stainless steel can be cast or wrought, with the key difference being how it is formed into the final product.
- Cast stainless steel is produced by pouring liquid metal into a mold to create a specific shape.
- Wrought stainless steel starts at a steel mill, where it is processed into ingots, blooms, billets, or slabs before being shaped further through rolling or hammering.
Wrought stainless steel products are far more common than cast stainless steel products because of their superior strength, versatility, and wide range of applications.
Production Steps of Stainless Steel
- Raw Material Selection
- Stainless steel is made from iron, carbon, and chromium (minimum 10.5%) along with other alloying elements like nickel, molybdenum, and manganese.
- Melting and Alloying
- The raw materials are melted in an electric arc furnace (EAF) at high temperatures (over 1600°C).
- Elements like nickel and molybdenum are added for enhanced corrosion resistance and strength.
- Casting into Forms
- The molten stainless steel is cast into semi-finished forms:
- Ingots (for forging and machining)
- Billets (for long products like bars and rods)
- Slabs (for flat products like sheets and plates)
- The molten stainless steel is cast into semi-finished forms:
- Hot Rolling and Cold Rolling
- The cast stainless steel is then shaped through hot rolling (above recrystallization temperature) or cold rolling (for smoother finishes and greater strength).
- Heat Treatment (Annealing)
- Annealing improves ductility and corrosion resistance by softening the material and removing internal stresses.
- Descaling & Pickling
- After rolling, stainless steel undergoes pickling, where an acid bath removes oxide scales that form during heat treatment.
- Finishing & Fabrication
- Final processes include polishing, grinding, or coating to enhance corrosion resistance and aesthetics.
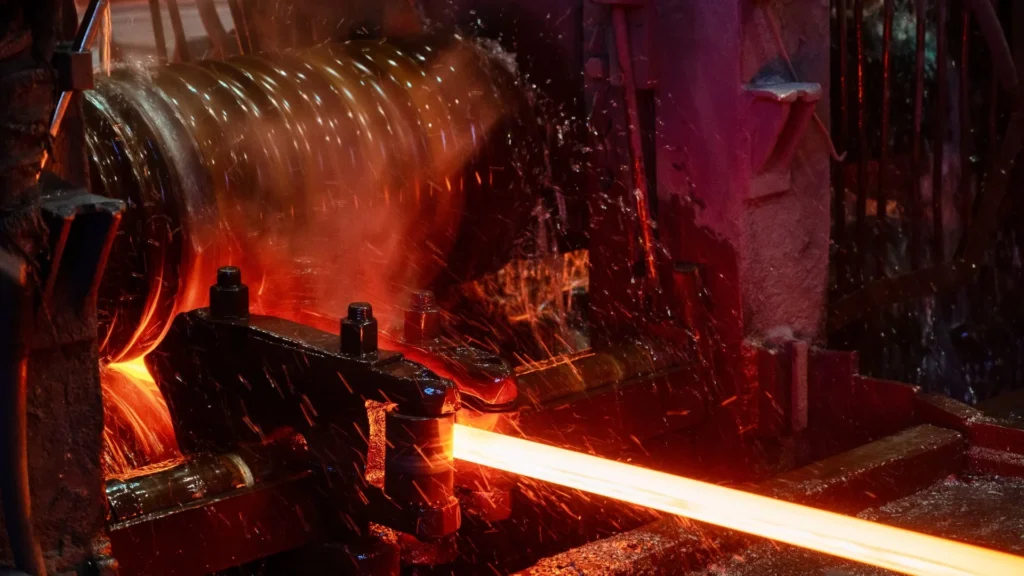
2. What Is Stainless Steel Made Of?
Like all steel, stainless steel starts with iron and carbon. However, its key differentiator is the addition of chromium (Cr), which provides its corrosion resistance.
When stainless steel is exposed to oxygen, the chromium reacts to form a thin passivation layer of chromium (III) oxide (Cr₂O₃). This layer:
- Prevents oxidation (rust)
- Self-heals when scratched, unlike plated metals (e.g., zinc-plated steel, which loses its protection if scratched)
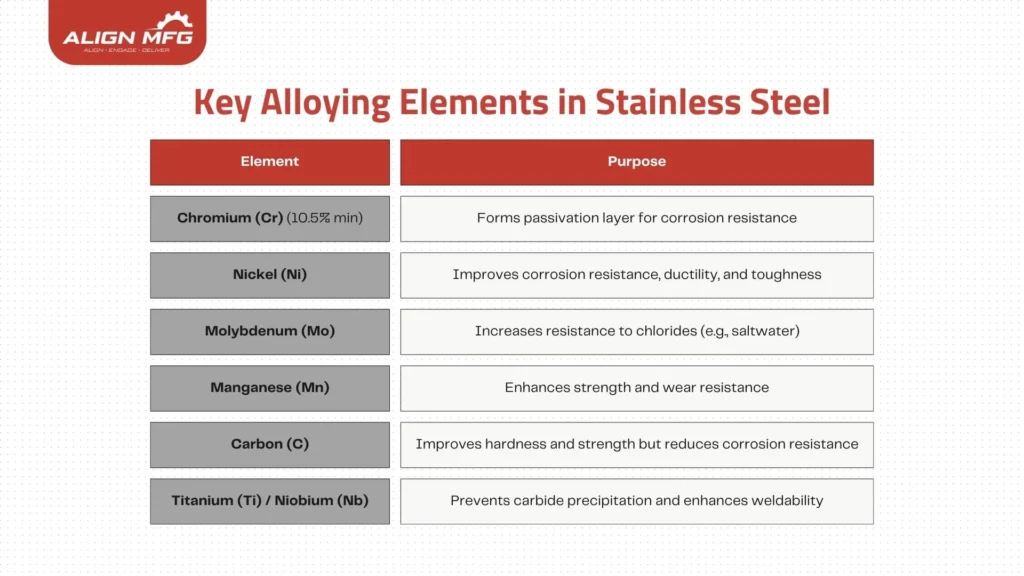
Download our guide to understand the different grades of stainless steel.
Understanding the Microstructures and Technical Aspects of Stainless Steel
When stainless steel solidifies from its molten state, it forms distinct microstructures that dictate its mechanical properties. The interplay of temperature, elemental composition, and cooling rate influences the crystalline lattice within the steel, leading to variations in strength, ductility, and magnetism.
Microstructural Evolution in Stainless Steel
The foundation of stainless steel’s structure lies in the way iron atoms arrange themselves at different temperatures. Three primary phases characterize its transformation:
- Ferrite (α-iron): A body-centered cubic (BCC) structure dominant below 912°C, known for its magnetism and lower ductility.
- Austenite (γ-iron): A face-centered cubic (FCC) structure forming between 912°C and 1394°C, which enhances ductility and corrosion resistance.
- Delta Ferrite (δ-iron): A high-temperature BCC phase appearing above 1395°C before iron fully melts at 1538°C.
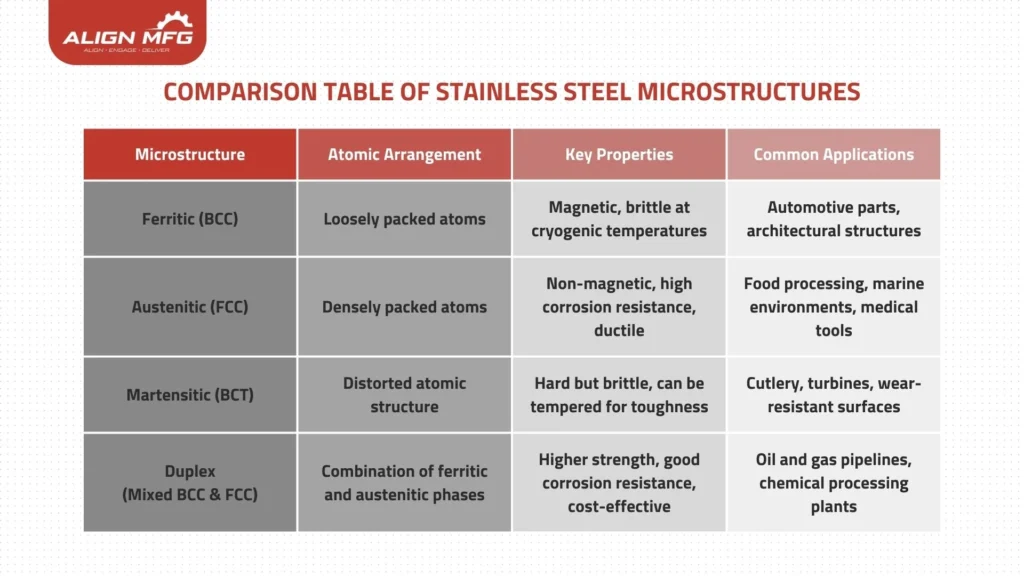
Influence of Alloying Elements
The addition of elements such as carbon, nickel, and manganese plays a crucial role in stabilizing these phases. Carbon increases hardness by promoting carbide formation, while nickel enhances the retention of the FCC structure at room temperature. This ability to maintain austenite at ambient conditions is critical for producing austenitic stainless steels, which are highly resistant to corrosion and non-magnetic.
The Role of Cooling and Heat Treatment
Steel’s final properties depend on how it cools post-processing:
- Slow Cooling (Annealing): Allows atoms to arrange into stable configurations, promoting ductility and toughness.
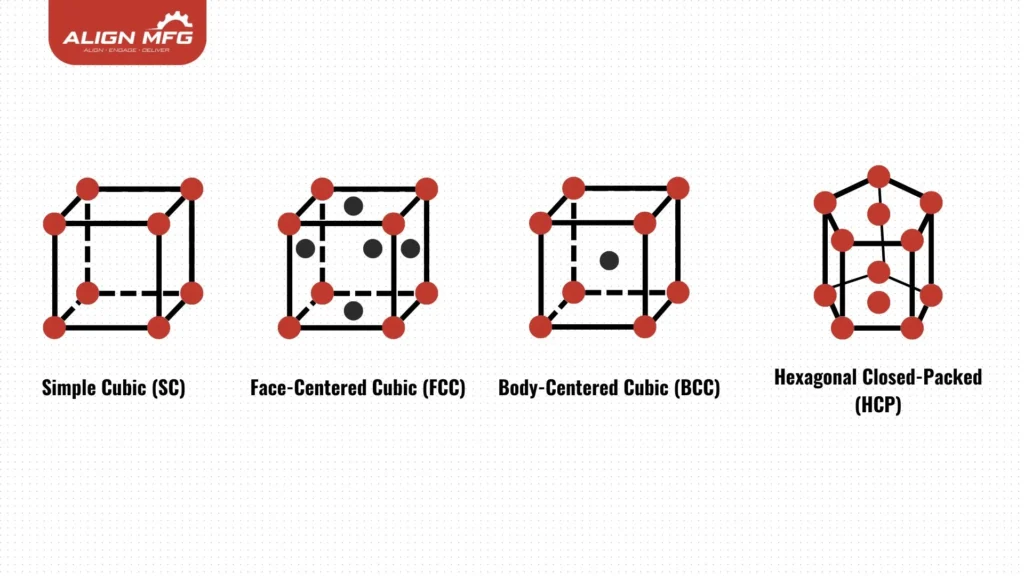
- Rapid Quenching: Traps the lattice in a strained configuration, leading to hard but brittle martensitic structures.
- Tempering: A controlled reheating process that refines martensitic steel, reducing brittleness while maintaining hardness.
Real-World Applications of Stainless Steel Microstructures
- Cryogenic Storage (Austenitic Steel – FCC): Retains strength and ductility even at extremely low temperatures, making it ideal for LNG storage tanks.
- High-Speed Machinery (Martensitic Steel – BCT): Hard, wear-resistant surfaces enable turbine blades and surgical tools to maintain sharpness.
- Bridges and Marine Environments (Duplex Steel – Mixed FCC & BCC): Provides a balance of corrosion resistance and structural strength.
- Magnetic Applications (Ferritic Steel – BCC): Used in motor components and electrical transformers where magnetism is required.
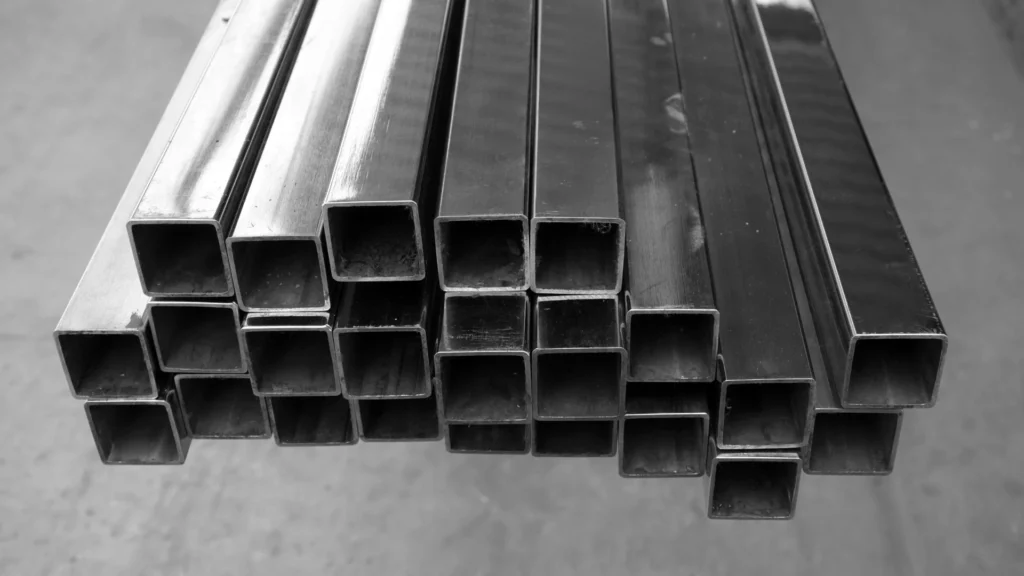
Other Key Factors in Selecting Stainless Steel Grades
When choosing the right stainless steel grade, consider:
- Corrosion Resistance – For marine or chemical environments, 316 or duplex stainless steel is recommended.
- Strength & Hardness – Applications requiring high strength should use martensitic or PH grades.
- Temperature Resistance – 321 and 430 are suitable for high-temperature environments.
- Cost Considerations – 201 or 430 are budget-friendly alternatives for non-critical applications.
- Magnetism – Austenitic stainless steels (300 series) are generally non-magnetic, whereas ferritic and martensitic steels (400 series) are magnetic.
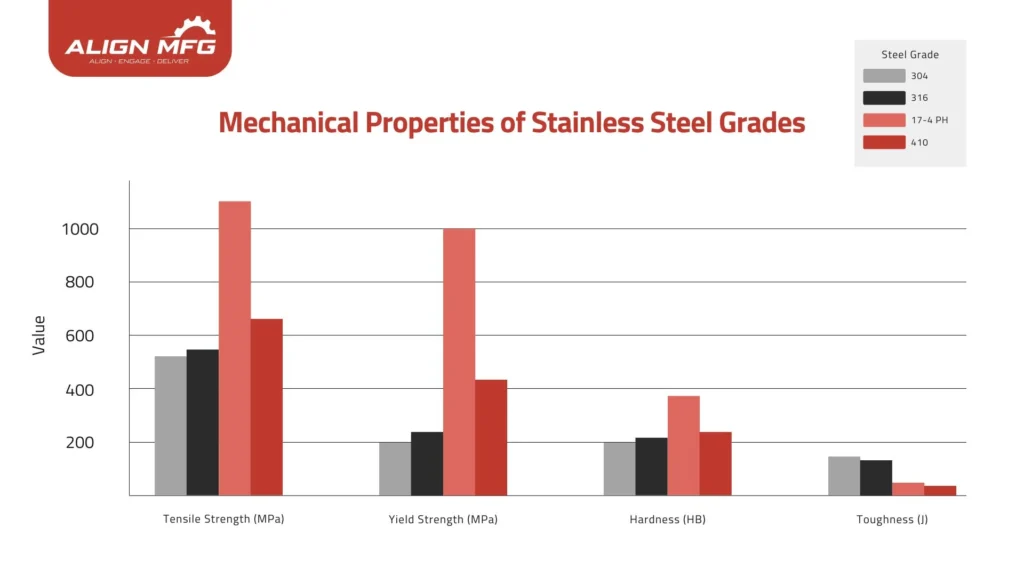
Stainless steel grades vary significantly based on composition, mechanical properties, and applications. 304 and 316 are the most commonly used grades due to their excellent corrosion resistance, while martensitic and duplex grades are preferred for strength and durability.
Understanding the characteristics of each stainless steel grade is crucial for selecting the right material for a specific application. Whether you need stainless steel for kitchenware, medical devices, industrial machinery, or marine environments, choosing the right grade ensures optimal performance and longevity.
For more on stainless steel, request a custom quote or project with Align Manufacturing. We have served the metal manufacturing industry for over a decade and offer a comprehensive range of stainless steel products and services such as sand casting,
Extend the Life of Your Stainless Steel: A Maintenance Guide
How to Successfully Order Custom Castings: A Step-by-Step Guide
Metal casting has shaped human civilization since 4000 BC , evolving from ancient bronze statues to today's precision-engineered components. In the modern world, this transformative process—where molten metal is poured into carefully designed molds—drives a global industry worth over Us$179.08 billion.
Custom castings represent the cutting edge of this field, where advanced engineering meets ancient craft to create components that precisely match specific requirements.
The impact of custom castings touches virtually every aspect of modern life. From the engine blocks powering your car to the massive turbine housings generating electricity, from delicate medical devices to robust mining equipment, custom castings provide the backbone for countless industries. Their applications span an impressive range:
- Automotive components requiring exceptional durability
- Precision aerospace parts where failure isn't an option
- Heavy machinery for construction and farming
- Intricate architectural elements in landmark buildings
- Critical components in renewable energy systems
- Custom parts for shipbuilding and rail transportation
- Specialized equipment for oil and gas extraction
- Robust processing equipment for forestry and mining
While the possibilities are nearly limitless, achieving success in custom casting requires meticulous attention to detail and comprehensive planning. From initial design concepts to final production, each step demands careful consideration to ensure the finished product meets exact specifications while remaining cost-effective. This guide by Align Manufacturing will walk you through every crucial aspect of ordering custom castings, helping you navigate the complexities of this sophisticated manufacturing process.
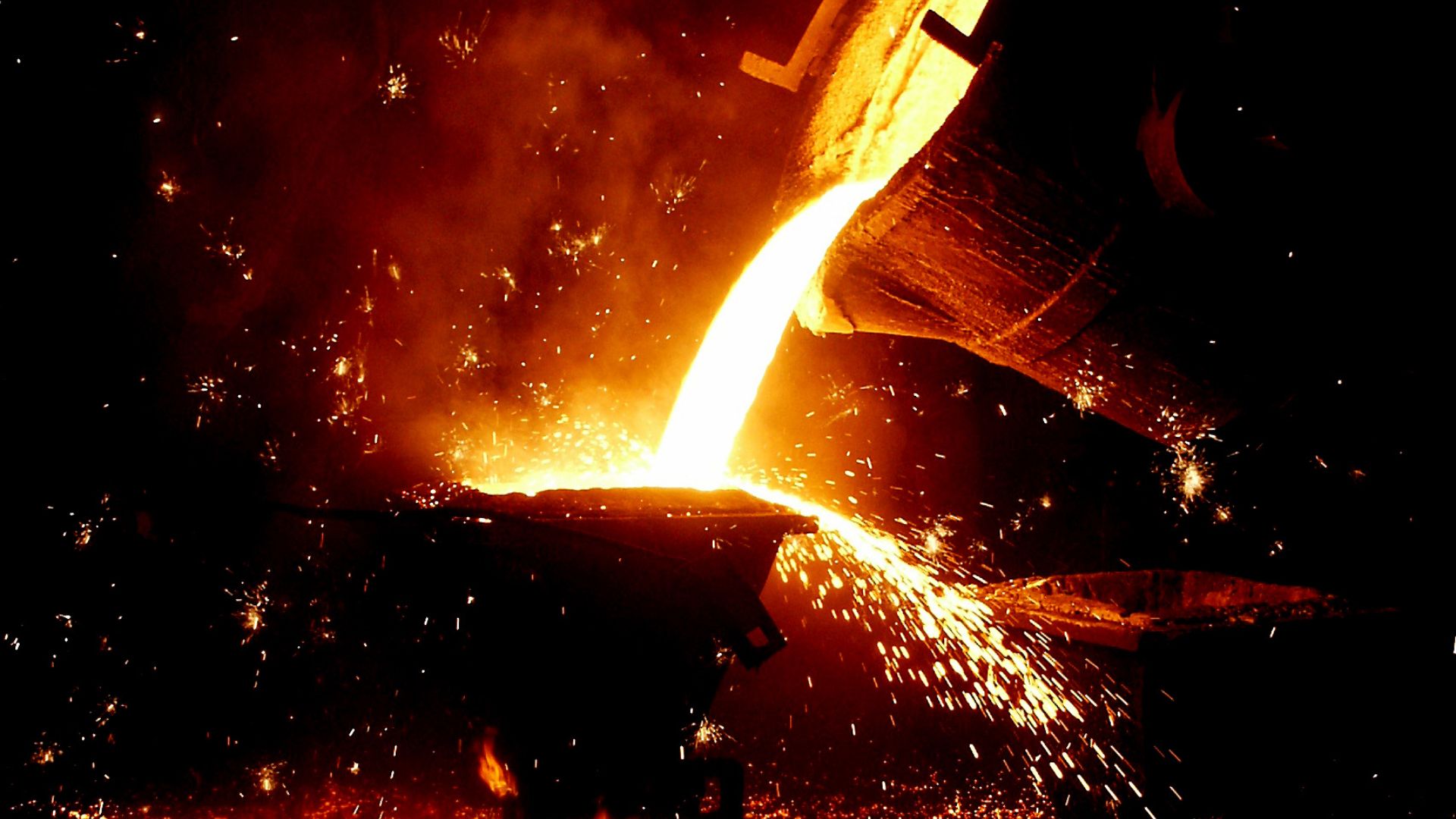
1.Design Specifications
The first step in ordering custom castings is defining the design requirements. This includes:
Component Requirements
- The component's function
- Shape and dimensions
- Required mechanical properties
- Quantity needed
Critical Design Elements
- Minimum Section Thickness: Typically no thinner than 0.25 in (6 mm) for conventional processes
- Draft Requirements: Generally 3/16 in of draft per ft (approximately 1.5 degrees)
- Parting Line Considerations: Straight parting lines reduce costs and simplify production
- Core Design: Consider accessibility for core removal and minimum diameter requirements.
Mold Preparation: Crafting the Cavity
Core Design Considerations
The minimum diameter of a core depends on:
- The thickness of surrounding metal
- Core length
- Special foundry procedures
- Reinforcement needs for larger cores
- Accessibility for core removal
Collaborating with a casting manufacturer early ensures the design aligns with both functional requirements and manufacturability. Utilizing 3D modeling and simulations helps visualize the final product and identify potential design challenges.
2. Material Selection
Selecting the right material is crucial as it impacts performance, durability, and cost. Common casting materials include:
- Steel: High strength and wear resistance
- Aluminum: Lightweight with good corrosion resistance
- Brass/Bronze: Excellent for corrosion-resistant applications
- Specialized Alloys: Used for extreme environments
Material Selection Factors
- Required strength and hardness
- Corrosion and heat resistance
- Machinability and finishing needs
- Industry-specific regulations (e.g., ASTM, ISO)
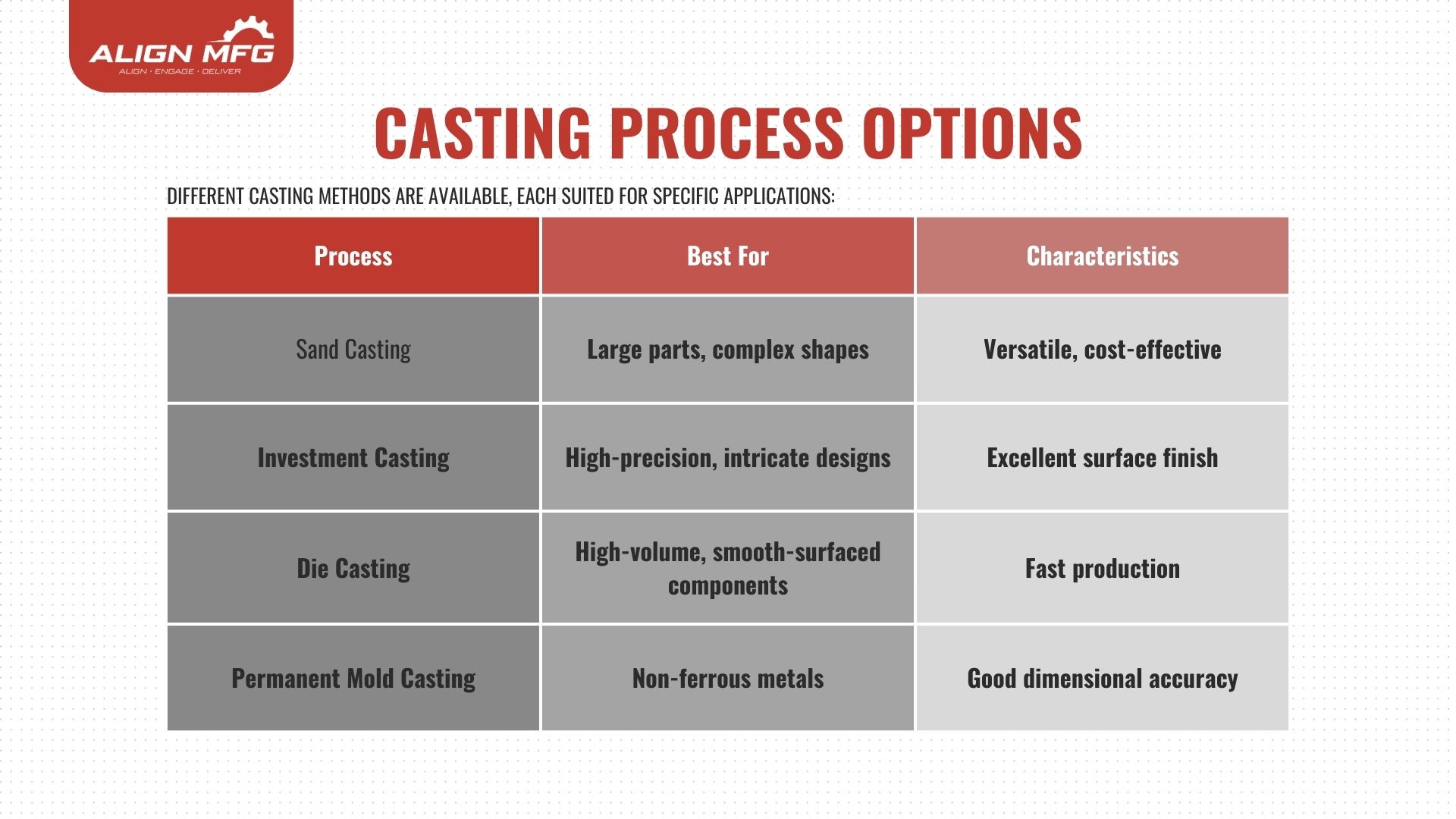
4. Soundness & Quality Considerations
Understanding that perfect castings are impossible is crucial. Quality considerations include:
Defect Types
- Sand inclusions
- Slag inclusions
- Macroporosity
- Shrinkage
The Importance of Quality Control in Custom Casting Production
Establishing rigorous quality control (QC) measures is crucial to ensuring that custom castings meet performance requirements, comply with industry standards, and minimize costly defects. A well-defined QC process helps align manufacturing with customer expectations, ensuring consistent production and preventing disputes over acceptance criteria.
Key Quality Control Measures for Custom Castings
To maintain high standards, foundries and customers must establish clear acceptance and rejection criteria before production begins. Essential QC factors include:
✔ Acceptance & Rejection Criteria
- Clearly define the allowable defect levels and ensure both parties agree on what constitutes acceptable variations.
- Use recognized international standards (such as ASTM, ISO, or SAE) to benchmark quality expectations.
✔ Dimensional Tolerances & Surface Finish Requirements
- Specify critical tolerances to ensure precision and fit for the intended application.
- Define surface finish expectations based on the casting process used (e.g., investment casting vs. sand casting).
- Consider post-processing treatments (such as grinding, polishing, or machining) to achieve the required finish.
✔ Defining the Exact Alloy Specification
- Specify the exact metal alloy to be used, referencing an internationally recognized standard (ASTM, ISO, EN, or JIS).
- Different alloys offer varying levels of strength, corrosion resistance, and machinability.
- Ferrous Metals (Iron-Based): Cast steel (most common), stainless steel, ductile iron, malleable iron.
- Non-Ferrous Metals (Non-Iron-Based): Aluminum, copper, and specialty alloys.
✔ Soundness & Defect Control in Castings
- No casting is 100% free of defects, but strict control over metal purity, shrinkage, and porosity helps minimize imperfections.
- Implement Non-Destructive Testing (NDT) such as:
- Ultrasonic Testing (UT): Detects internal flaws.
- Radiographic Testing (X-ray): Examines internal structures for porosity and inclusions.
- Dye Penetrant Testing (DPT): Identifies cracks and surface defects.
- Foundries must follow ASTM acceptance criteria for evaluating defects and determining whether a casting meets specifications.
✔ Heat Treatment & Mechanical Properties
- Mechanical properties (strength, hardness, ductility, etc.) depend on solidification conditions, cooling rates, and heat treatment processes.
- Some alloys require post-casting heat treatment to achieve specific mechanical properties.
- Heat treatment options include:
- Normalizing & Annealing: Enhances ductility and removes internal stresses.
- Flame Hardening & Case Hardening: Improves surface hardness for wear resistance.
- Tempering & Quenching: Adjusts strength and toughness to required specifications.
Align Manufacturing ensures precise temperature control and monitoring using advanced heat treatment equipment to maintain consistent quality across production batches.
5. Prototyping
Before full-scale production, creating prototypes allows for functional testing through:
- 3D Printing
- Small-Batch Casting
- CNC Machining
6. Weight Considerations
Weight impacts both cost and production methods:
Weight Factors
- Net Weight: Final casting weight
- Gross Weight: Total metal poured, including gates and risers
- Casting Yield: Efficiency ratio between net and gross weight
- Material Cost Impact: Higher weight increases material costs
Let me streamline this into the most practical calculation that foundries commonly use.
Weight and Yield Calculations in Casting
The most critical calculation in casting is determining the total material needed and its cost, as this directly impacts project feasibility and pricing.
Key Weight Components
- Net Weight (Wn): Final casting weight
- Gross Weight (Wg): Total metal poured (including feeding system)
- Casting Yield: Efficiency ratio (typically 60-75% for sand casting)
Essential Casting Calculation Example
Let's say you need to produce a steel casting weighing 100 kg (net weight):
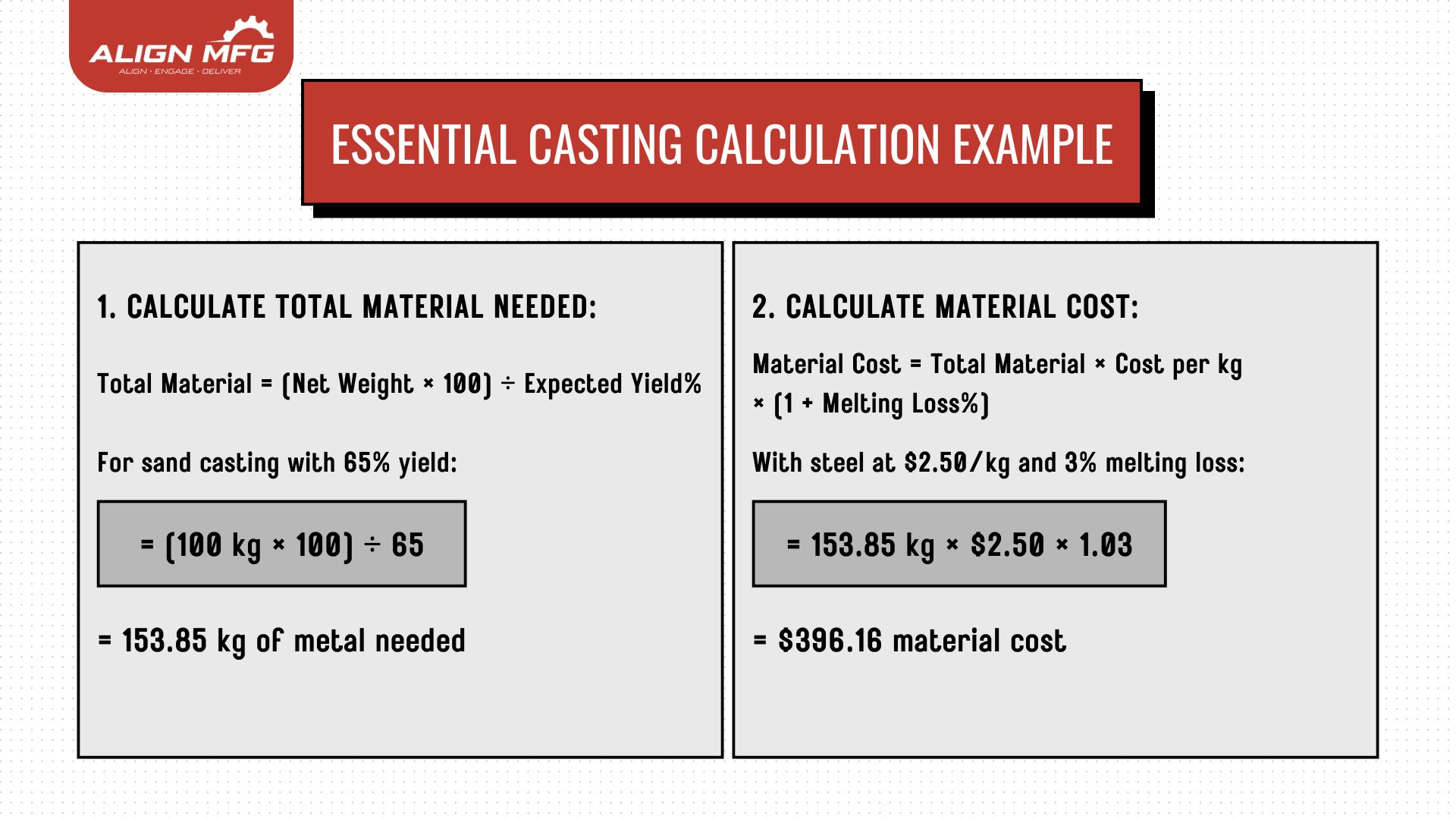
This basic calculation helps:
- Determine material requirements
- Estimate project costs
- Set appropriate pricing
- Plan production efficiency
Typical Yield Ranges (for reference):
- Sand Casting: 60-75%
- Die Casting: 85-95%
- Investment Casting: 55-65%
7. Pattern Equipment & Tooling
Pattern quality directly affects casting quality and costs:
Types of Patterns
Each pattern type offers distinct advantages and trade-offs:
- Wood Patterns
- Pros: Lower initial cost, easier to modify
- Cons: Shorter lifespan, can warp over time
- Best For: Low-volume production, prototyping, and sand casting
- Metal Patterns
- Pros: High durability, maintains precision over many cycles
- Cons: Higher upfront cost, heavier, harder to modify
- Best For: High-volume production, die casting, investment casting
- Mounted vs. Loose Patterns
- Mounted: Affixed to a plate for consistent alignment, improving repeatability
- Loose: Freely placed in the mold, more flexible but can lead to variations
- Split Patterns
- Used to simplify mold separation and improve accuracy in complex geometries
- Can involve full split core boxes or half core boxes, depending on foundry requirements
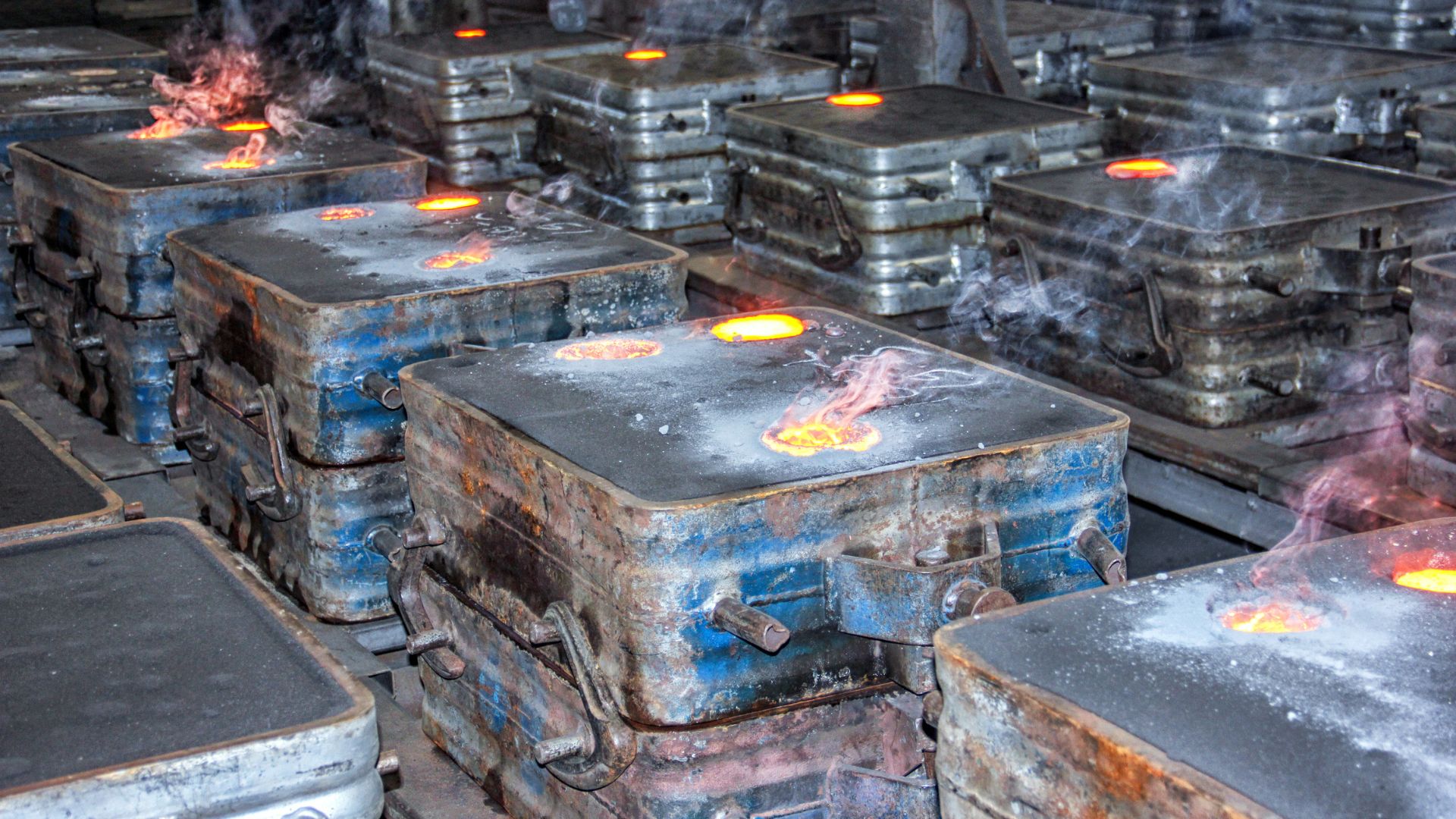
Pattern Considerations & Cost Implications
The decision on pattern design must take into account long-term costs, foundry compatibility, and quality control. Some key considerations include:
- Compatibility with Foundry Equipment
- Even if an existing pattern is available, a foundry may require new tooling to match its specific machinery.
- This can involve:
- Full split core boxes instead of half core boxes
- Metal pattern replacement for wooden patterns
- Switching to mounted patterns for better consistency
- Balancing Upfront Costs vs. Long-Term Savings
- More sophisticated pattern equipment leads to higher pattern costs initially.
- However, this investment reduces per-unit casting costs over time by:
- Increasing efficiency
- Improving dimensional accuracy
- Reducing scrap and rework
- Example: A metal pattern may cost 2-3x more than a wooden one, but for large-scale production, it can lower overall casting costs due to reduced wear and fewer defects.
- Storage & Maintenance
- Patterns require proper storage and maintenance to prolong their usability.
- Foundries may charge for pattern storage or request maintenance fees, especially for high-volume production.
- Investing in high-quality pattern materials reduces maintenance frequency and improves overall casting consistency.
The Design Phase: Pattern Creation
8. Testing & Inspection
Comprehensive testing ensures quality through:
Destructive Testing
- Requires separate test castings
- Provides internal soundness verification
- Used to validate production methods
Non-Destructive Testing (NDT)
- Visual Inspection
- Liquid Dye Penetrant Inspection (LPI)
- Magnetic Particle Inspection (MPI)
- Ultrasonic Testing (UT)
- Radiographic Inspection (X-Ray)
9. Machining Requirements
Machining considerations affect both design and cost:
Machining Factors
- Stock allowance for machined surfaces
- Fixture and clamping requirements
- Material specification impacts
- Production quantity considerations
Verification Process
- Complete layout for complex machining
- Target point marking
- First article inspection
- Machining allowance verification
10. Supplier Selection
Choose a reliable foundry based on:
- Experience & Expertise
- Certifications
- Production Capabilities
- Quality Control Measures
- Specialization (short-run vs. high-volume)
11. Requesting a Quote
Provide detailed information including:
- Technical Drawings
- Material Specifications
- Production Quantity
- Finishing Requirements
- Testing Requirements
- Delivery Timeline
12. Production & Delivery Timelines
Understanding typical timelines is crucial:
Timeline Components (up to 24 weeks)
- Commercial Administration
- Pattern/Tooling Construction
- Sampling
- Inspections
- Pattern Modifications
- Production Setup
- Manufacturing
- Post-Production Processing
Production Planning
- Early communication of delivery requirements
- Regular progress updates
- Buffer time for unexpected issues
- Quality control checkpoints
Final Thoughts
Success in custom casting projects requires:
- Thorough planning and design
- Clear communication with suppliers
- Understanding of manufacturing constraints
- Comprehensive quality control
- Realistic timeline expectations
By considering all these factors during the planning and ordering process, you can achieve cost-effective and high-performance custom castings suited to your needs.
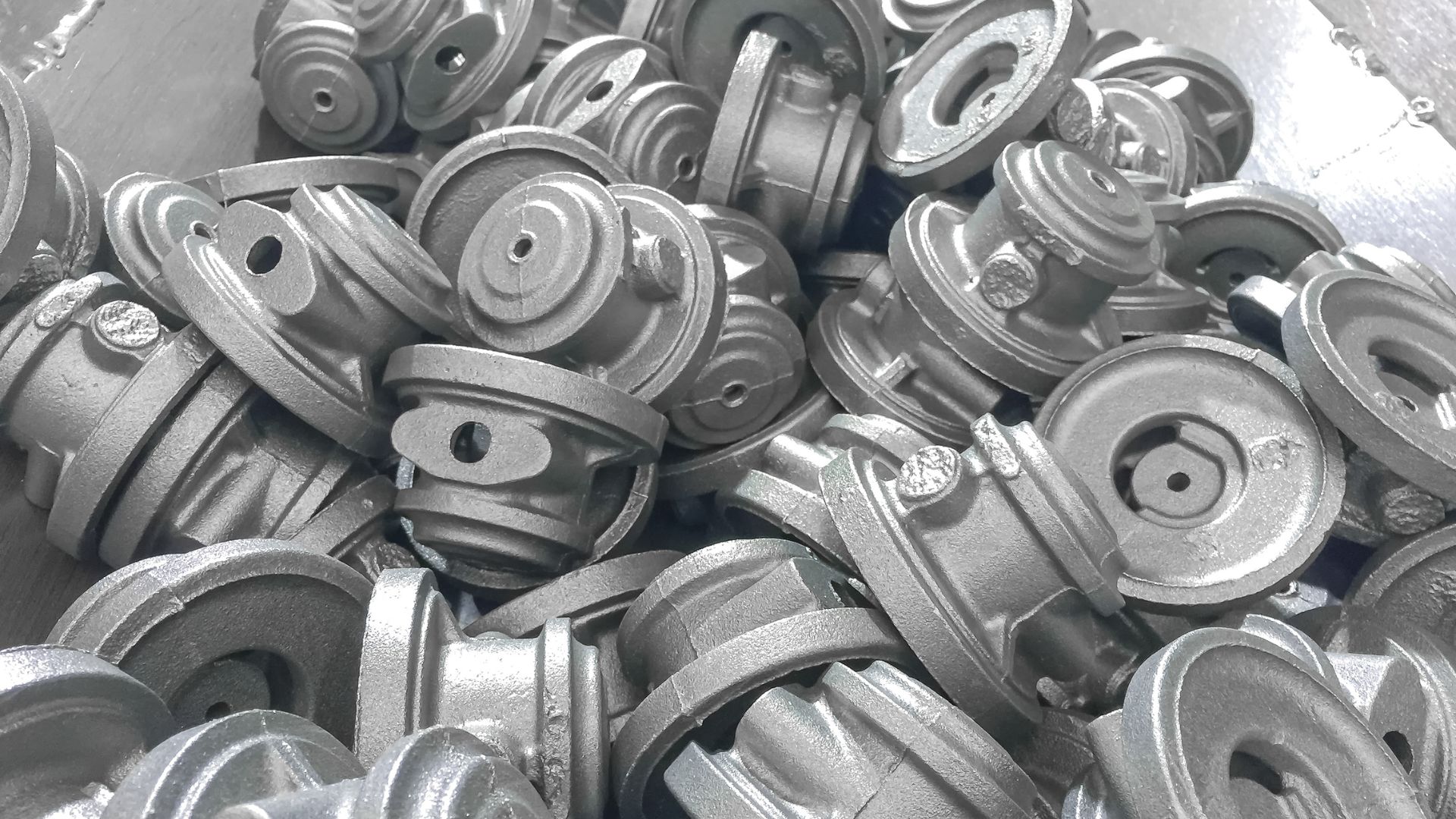
Frequently Asked Questions (FAQs)
Lead times vary based on the casting method and project complexity. For instance:
- Sand Casting: Approximately 3-5 weeks.
- Investment Casting: Tooling design and manufacturing take about 4-6 weeks, with sample castings requiring an additional 2-4 weeks.
- Production Runs: New parts can take up to 24 weeks for full production and delivery.
To synchronize your needs with the foundry's capabilities:
- Early Engagement: Initiate discussions and request quotes well in advance of your required delivery date.
- Clear Communication: Provide detailed information about batch sizes, frequency, and specific requirements.
- Partner Selection: Choose foundries with a proven track record in handling both immediate and long-term production needs.
Align Manufacturing provides:
- Diverse Manufacturing Processes: Expertise in sand casting, investment casting, stamping, precision machining, forging, fabrication, high-pressure die casting, and gravity casting.
alignmfg.co - Strategic Production Planning: Ability to scale short-run productions for urgent needs and offer long-term solutions with stable pricing.
- Global Presence: Facilities in SE&South East Asia, ensuring optimal outcomes across various markets.
Align Manufacturing emphasizes:
- Early Involvement & Planning: Assembling materials, and manufacturing feasibility before production begins.
- Transparent Communication: Providing detailed feedback and recommendations to refine designs for cost-effectiveness.
- Custom Solutions: Tailoring processes to meet the unique needs of industries such as automotive, aerospace, and heavy machinery.
- Reliable Scheduling: Proper forecasting and scheduling to prevent last-minute disruptions.
Several elements influence lead times, including:
- Complexity of Design: Intricate designs may require more time for tooling and production.
- Material Selection: Some materials may have longer procurement times.
- Order Volume: Larger orders might extend production schedules.
- Quality Assurance Processes: Rigorous testing and inspections can add to the timeline but ensure superior quality.
To accelerate your order:
- Provide Detailed Specifications: Clear and comprehensive details reduce the likelihood of revisions.
- Maintain Open Communication: Regular updates and prompt responses facilitate smoother processes.
- Collaborate Closely with the Foundry: Early and continuous collaboration can identify potential challenges and address them proactively.
For more information or to discuss your specific project needs, contact us today.
How to Weld Cast Iron Without Cracking: Best Methods, Tips, and Techniques
Welding cast iron is a specialized process that requires careful attention due to its unique properties. This elevated carbon level makes cast iron prone to cracking and other challenges during welding. In this article, we will explore the definition of cast iron, the challenges associated with welding it, effective techniques, and best practices to ensure successful outcomes.
What Is Cast Iron?
Cast iron is an iron-carbon alloy characterized by its high carbon content, typically between 2% and 4%. This composition gives cast iron its distinctive hardness and brittleness. Common types of cast iron include gray cast iron, white cast iron, ductile (nodular) cast iron, and malleable cast iron, each with varying properties and applications.
- Gray Cast Iron: Gray cast iron is the most common type of cast iron, characterized by graphite flakes that form within a pearlite or ferrite microstructure. While it is more ductile and weldable than white cast iron, these graphite flakes can enter the weld pool, leading to embrittlement and weakened welds. To achieve a successful weld, preheating and careful filler metal selection are crucial to minimizing cracking and maintaining structural integrity. Due to these challenges, welding gray cast iron requires expertise and a controlled approach to ensure durable and machinable results.
- White Cast Iron: White cast iron is known for its extreme hardness and brittleness, as it retains carbon in the form of iron carbide (cementite) rather than graphite. This cementite microstructure makes the material highly wear-resistant but also incredibly difficult to machine or weld. Unlike gray cast iron, which allows some degree of weldability, white cast iron is unweldable due to its tendency to crack under thermal stress.
- Attempts to weld white cast iron often result in rapid cooling and the formation of even harder, brittle microstructures, making post-weld machining nearly impossible. In cases where repair is necessary, alternatives such as brazing or buttering with a machinable weld overlay are sometimes used. Another approach is to anneal white cast iron before welding, converting some of the iron carbide into graphite to improve ductility—though this is rarely practical in most industrial applications. Given these challenges, white cast iron is typically repaired using mechanical fastening methods or part replacement rather than welding.
- Ductile (Nodular) Cast Iron: More flexible and weldable than gray cast iron, but still requires special techniques.
- Malleable Cast Iron: Similar to ductile cast iron, it has some flexibility but is more challenging to weld without preheating.
Identifying the cast iron type helps determine the right welding approach and filler material.
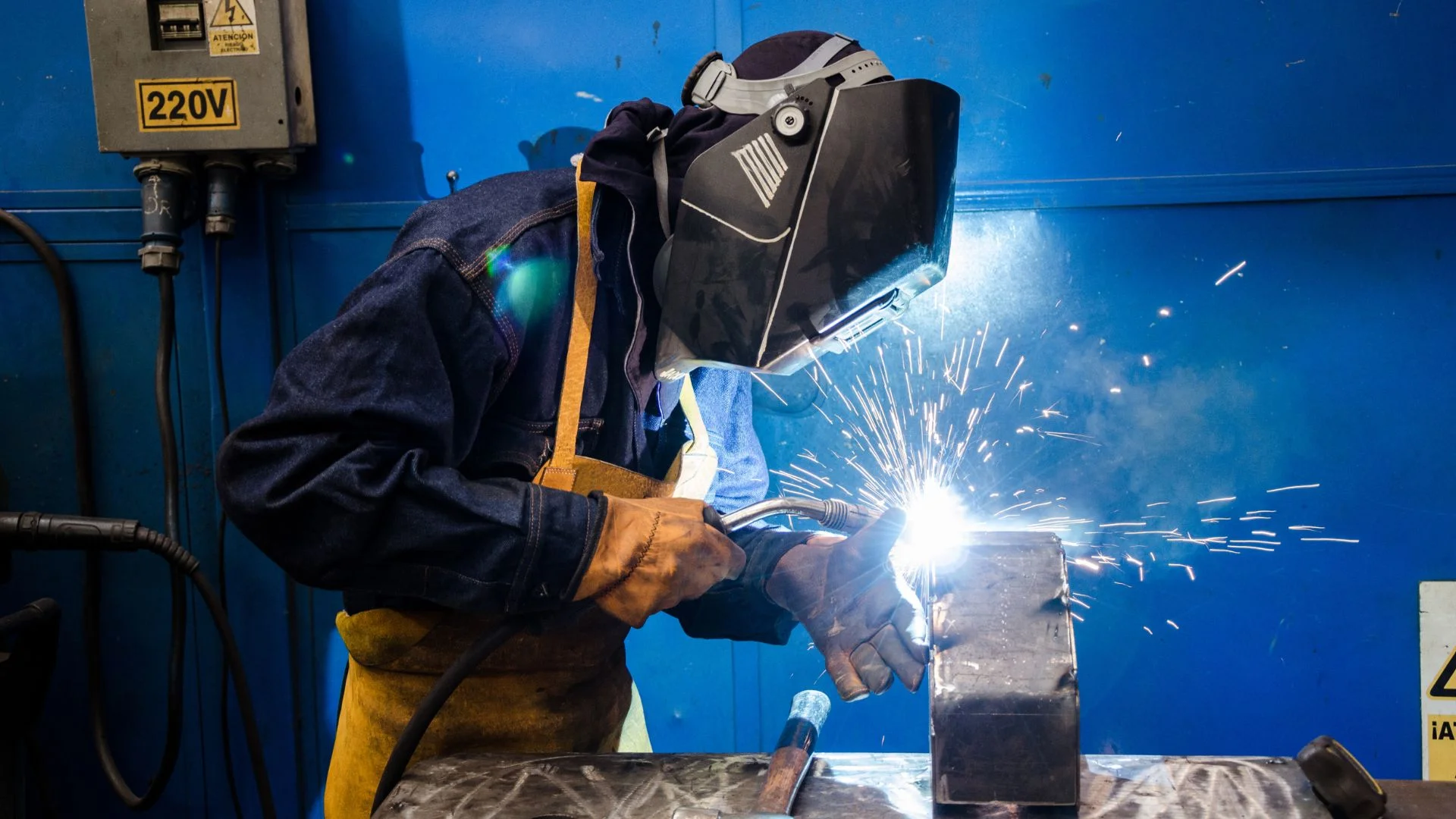
Challenges in Welding Cast Iron
Welding cast iron presents several challenges, primarily due to its high carbon content and brittle nature. Key issues include:
- Cracking: Rapid cooling can lead to the formation of hard, brittle microstructures, increasing the risk of cracks.
- Porosity: Entrapped gases during welding can cause porosity, weakening the weld.
- Contamination: Surface impurities like oil, grease, and rust can lead to defects in the weld.
- Hardening: The heat-affected zone (HAZ) can become excessively hard, making machining difficult.
Techniques for Welding Cast Iron
Several welding methods are suitable for cast iron, each with its advantages and considerations:
1. Shielded Metal Arc Welding (SMAW)
Also known as stick welding, Shielded Metal Arc Welding (SMAW) is one of the most commonly used techniques for welding cast iron. The process utilizes a consumable electrode coated with flux, which creates a protective gas shield when burned, preventing contamination and ensuring a clean weld.
Different types of electrodes can be used depending on the application, required color match, and post-weld machinability. The three primary filler materials for cast iron stick welding include:
- Cast iron covered electrodes – Designed for cast iron applications, though they may be brittle.
- Copper alloy electrodes – Provide a strong bond but are less common for structural welding.
- Nickel alloy electrodes – The most popular choice due to their compatibility with cast iron’s properties.
Nickel-based electrodes are especially preferred because they create a softer, more ductile weld that is less prone to cracking. According to New Hampshire Materials Laboratory Inc., nickel-iron welds are stronger and have a lower coefficient of thermal expansion, reducing welding stresses and improving crack resistance.
Key Considerations for SMAW on Cast Iron:
- Electrode Handling: An electric arc between the electrode and the welding area melts the metals and enables fusion. The arc should be directed at the weld pool, not the base metal, to minimize dilution and reduce hardening.
- Current Setting: It is recommended to use the lowest current setting approved by the manufacturer to avoid excessive heat input, which can increase the likelihood of cracking.
- Preheating: Heating the workpiece to a moderate temperature (typically between 500°F and 1200°F) helps to reduce thermal stress and minimize the formation of brittle zones.
- Post-Weld Cooling: Gradual cooling is essential to prevent cracking. Wrapping the part in an insulating blanket or burying it in dry sand helps slow the cooling rate and prevents the formation of hard, brittle microstructures.
2. Oxy-Acetylene Welding
This method uses a flame produced by burning acetylene with oxygen to weld cast iron. It allows for slow heating and cooling, which can reduce the risk of cracking. A cast iron filler rod is typically used, and the process is suitable for repairing thin sections or intricate parts. However, it requires skilled handling to avoid overheating and potential distortion.
3. Braze Welding
Braze welding involves using a filler metal with a lower melting point than the base metal, such as a bronze or brass alloy. This filler metal melts and flows into the joint through capillary action.This technique is beneficial for joining dissimilar metals and minimizing heat-induced stresses, as it does not melt the base cast iron. Proper surface preparation and flux application are essential to ensure a strong, defect-free joint.
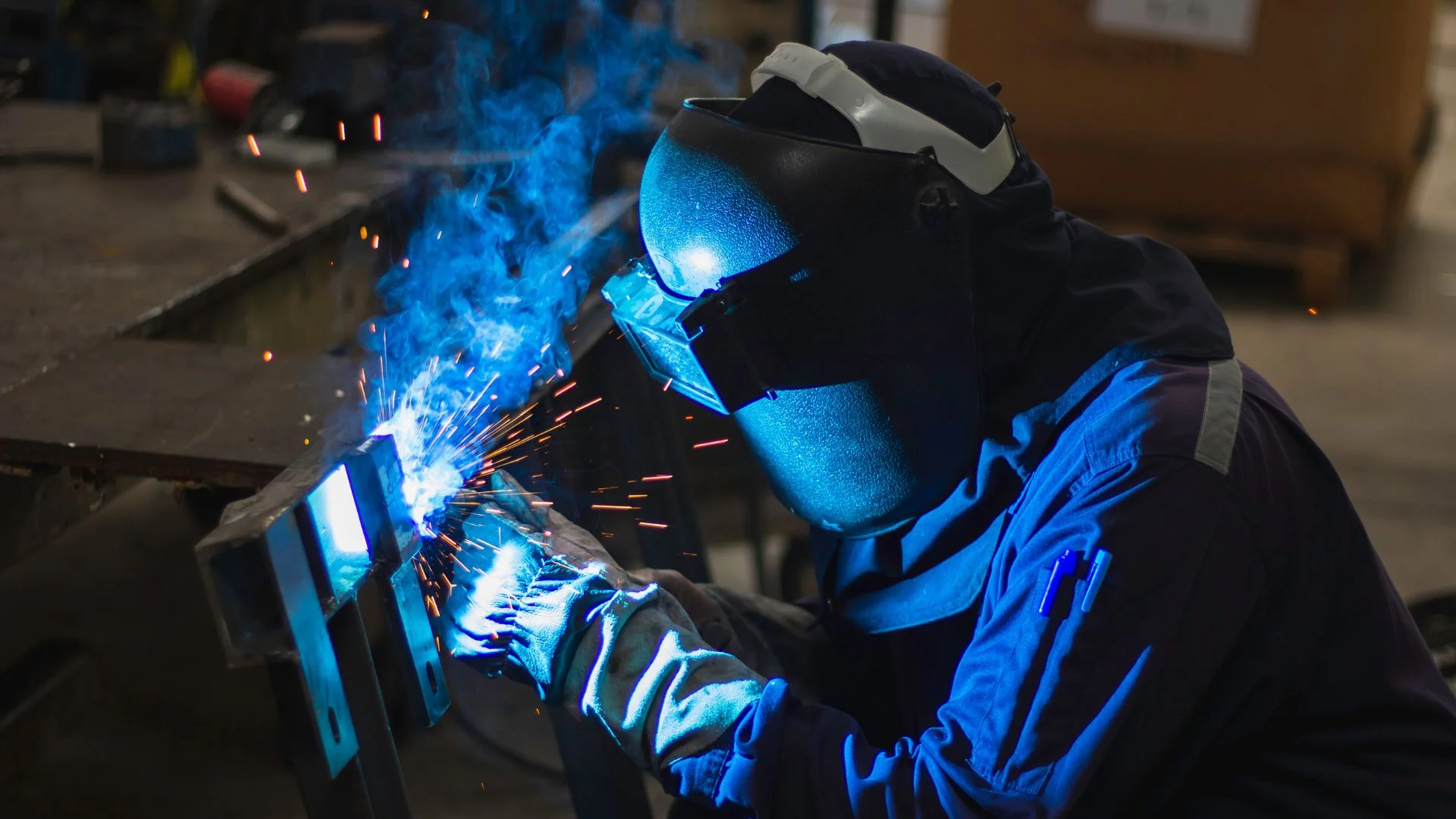
Best Practices for Welding Cast Iron
To achieve optimal results when welding cast iron, consider the following best practices:
Best Practices for Welding Cast Iron
1. Surface Preparation
Proper surface preparation ensures a clean and strong weld.
- Thorough Cleaning: Remove paint, rust, oil, and grease before welding to prevent impurities in the weld pool.
- Avoid Abrasive Grinding: Using abrasive tools can smear graphite over the surface, leading to porosity. Instead, use a carbide burr or gouging electrode for preparation.
2. Preheating the Cast Iron
Preheating Cast Iron: Why It Matters and How to Do It Right
Preheating cast iron is a critical step in preventing thermal stress, cracking, and weld failure. Since cast iron is brittle and has poor ductility, it does not stretch to relieve stress like steel or other ductile metals. Instead, any localized heating can result in restricted expansion, leading to stress buildup and ultimately cracking during the cooling phase.
Why Preheating is Important
The primary reason for preheating is to control thermal expansion and contraction during welding. If only the weld zone heats up, while the surrounding metal remains cool, the heat-affected zone (HAZ) expands unevenly, creating internal tensile stresses that can cause cracks—either immediately or after cooling.
Preheating reduces the thermal gradient between the weld area and the rest of the casting, allowing for a more uniform expansion and contraction. This minimizes stress buildup and lowers the risk of cracking both during and after welding.
How to Properly Preheat Cast Iron
1. Determining the Right Preheat Temperature
The required preheat temperature depends on:
- Type of Cast Iron:
- Gray cast iron: 500°F - 1200°F (260°C - 650°C)
- Ductile cast iron: 500°F - 900°F (260°C - 480°C)
- White cast iron: Typically unweldable; extreme caution required
- Size and Thickness of the Casting:
- Thicker and larger castings require higher preheating temperatures to ensure even heat distribution.
- Welding Method Used:
- Higher-temperature welding methods (e.g., stick welding) require higher preheating temperatures.
- Lower-temperature methods (e.g., brazing) may require little or no preheating.
2. Even Heating: Preventing Uneven Expansion
- Heat the entire casting evenly to avoid creating temperature differentials that can induce stress.
- Use large ovens, torches, or induction heating to distribute heat uniformly.
- Avoid spot heating, as this can cause localized expansion, leading to cracks.
- Slow heating is crucial—do not rush the preheating process.
3. Maintaining a Consistent Temperature
- Once the desired temperature is reached, maintain it throughout the welding process.
- If the workpiece cools below the necessary preheat temperature during welding, reheat it before proceeding.
- Use temperature indicating sticks, thermocouples, or infrared thermometers to monitor temperature.
What to Do When Preheating Isn’t Possible
In some cases, preheating may not be practical due to part size, accessibility, or equipment limitations.
Use a low-heat welding process (such as TIG or brazing).
- Select low-melting-point welding rods or wires to reduce heat input.
- Increase interpass cooling time—welding in small passes with extended cooling time between them.
- Apply peening between weld passes to relieve stress.
3. Welding Techniques
Different welding techniques can be used for cast iron, each with advantages and considerations.
Shielded Metal Arc Welding (SMAW) - Stick Welding
- Uses nickel-based or cast iron-specific electrodes.
- Requires preheating for best results.
- Produces a strong, machinable weld.
Oxy-Acetylene Welding
- Allows for slow heating and cooling.
- Suitable for thin sections and small repairs.
- Requires a cast iron filler rod.
Braze Welding
- Uses a filler metal with a lower melting point.
- Ideal for joining dissimilar metals.
- Reduces heat-induced stress.
In-House Welding Feasibility
While welding cast iron in-house is possible, for critical repairs or structural components, professional expertise is recommended to ensure weld integrity.
4. Welding Execution Techniques
Certain techniques can improve the chances of a successful weld.
- Short Weld Passes: Limit weld beads to 1 inch (25 mm) or less to control heat input and minimize cracking (WeldingHandbook.com).
- Peening: Gently hammering the weld bead while still hot relieves internal stress and prevents cracking (WeldingHandbook.com).
5. Filler Material Selection
Choosing the right filler material is crucial to a strong and durable weld.
- Nickel-Based Electrodes:
- 99% Nickel rods are preferred for their machinability and compatibility with cast iron.
- Ferro-nickel rods (47% nickel, 53% steel) are more affordable and suitable for welding cast iron to steel.
6. Cooling Methods
Controlled cooling is essential to avoid cracks and maintain weld integrity.
- Slow Cooling: Rapid cooling can lead to hardening and cracking. Wrap the welded part in an insulating blanket or bury it in dry sand to cool gradually (MakeItFromMetal.com).
- Slow cooling methods include:
- Wrapping the welded part in heat-resistant blankets
- Burying the casting in dry sand, ashes, or lime
- Placing it in an insulated oven for controlled cooling
- Never quench or expose the welded part to sudden temperature drops, as this will create excessive stress and lead to cracking.
By understanding the inherent challenges of welding cast iron and implementing these techniques and best practices, welders can achieve strong, durable repairs and fabrications.
7. Alternative Methods for Repairing Cast Iron
In some cases, welding may not be the best option. Alternative techniques include:
- Brazing: Uses a filler metal that melts at a lower temperature than the base metal, reducing thermal stress.
- Suitable for non-structural repairs or when welding risks damaging the part.
(Eng-Tips.com).
- Suitable for non-structural repairs or when welding risks damaging the part.
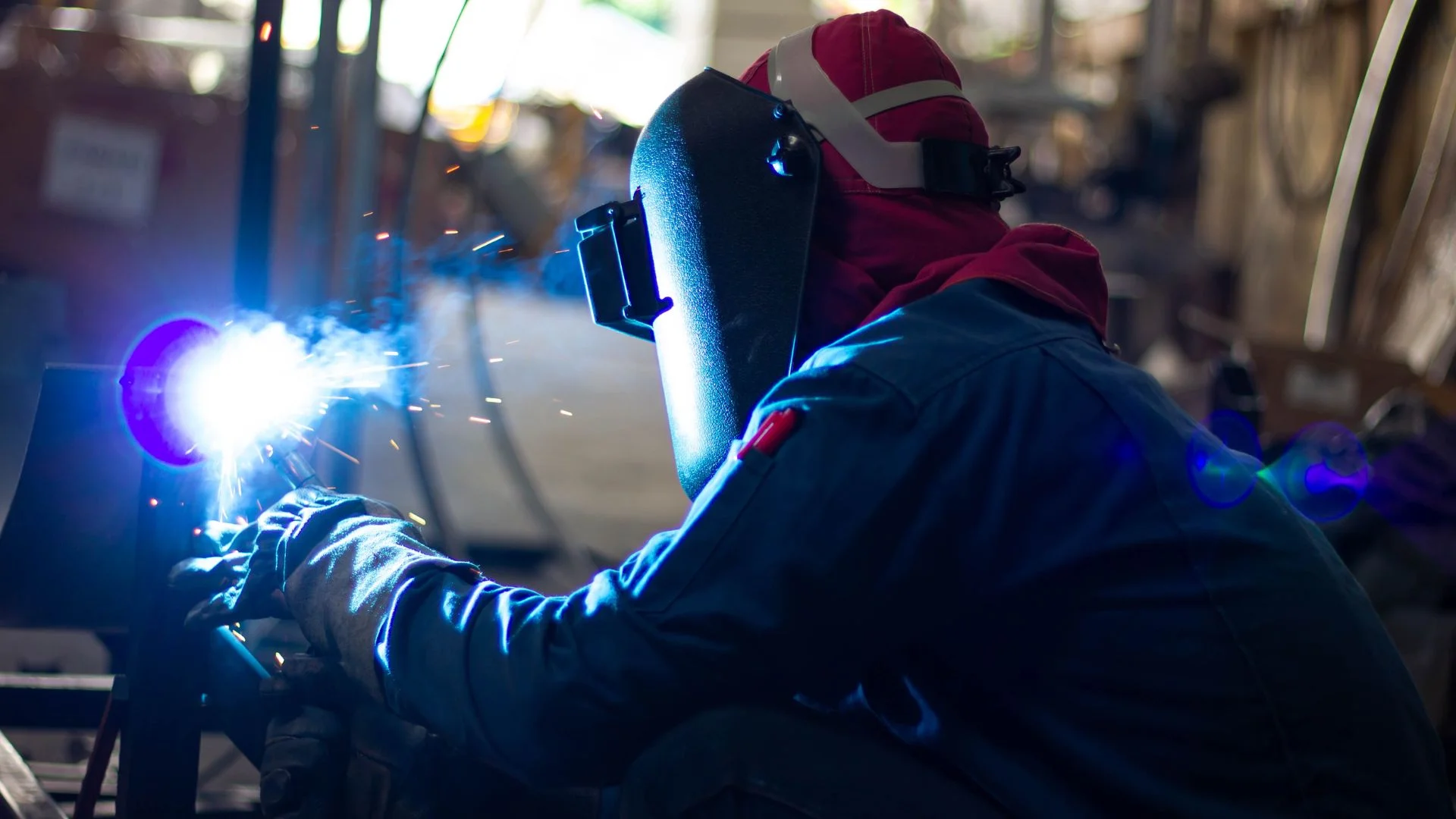
Welding plays a crucial role in the broader manufacturing ecosystem, often complementing our key processes such as casting, forging, and machining. By understanding how welding fits into fabrication and assembly workflows, manufacturers can make more informed decisions about when to incorporate welding into their production strategies.
Whether you need high-strength cast components, machined parts with tight tolerances, or fabricated assemblies, Align helps you achieve cost-effective and durable manufacturing solutions tailored to your industry needs.
Frequently Asked Questions (FAQs)
While it is possible using cold welding techniques, preheating significantly reduces the risk of cracking and improves weld quality.
99% Nickel electrodes offer the best machinability, while ferro-nickel electrodes are more cost-effective for structural applications.
MIG welding is generally not recommended due to its high heat input, which can increase cracking risks.
For high-strength repairs, stick welding with nickel electrodes is best. However, brazing can be an effective alternative for non-structural repairs.’
- Preheat the workpiece properly.
- Use short weld passes.
- Peen the weld bead to relieve stress.
- Cool the part slowly using insulating materials.
Cast Aluminum: Benefits, Applications, and Manufacturing Process
Cast aluminum is more than just a material; it’s a versatile cornerstone in the manufacturing world, enabling the creation of products that shape our everyday life. From the car you drive to the pots and pans in your kitchen, cast aluminum plays a pivotal role. This blog post will guide you through the essence of cast aluminum, its unique properties, the advantages and challenges it presents, and how it stacks up against other metals like cast steel and grey iron.
What is Cast Aluminum?
Cast aluminum refers to a process where aluminum is melted and poured into a mold to create complex shapes and components. Unlike wrought aluminum, which is shaped through methods like rolling, hammering, or extruding, casting allows for intricate designs and detailed textures that would be difficult or impossible to achieve with other techniques. This versatility makes cast aluminum an attractive option for manufacturers seeking to produce high-quality parts with precision.
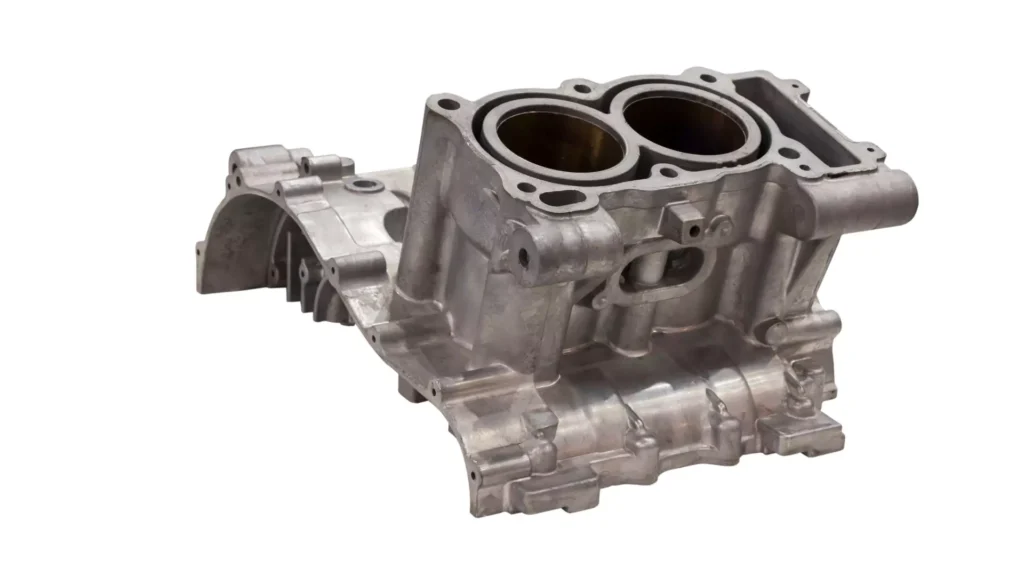
The Aluminum Casting Process
The journey of creating a cast aluminum part involves several steps. It begins with melting aluminum ingots or scraps and then injecting the molten metal into a steel or aluminum mold under high pressure. Once the aluminum cools and solidifies, the mold opens to reveal a lightweight yet sturdy component. Techniques like die casting, permanent mold casting, and sand casting are commonly employed, each suitable for different complexity levels and production volumes.
Process | Description | Key Features | Applications |
Die Casting | High-pressure injection of molten aluminum into a metal mold. | Fast, precise, excellent surface finish, high dimensional accuracy, and good thermal conductivity. | Automotive, electronics, consumer goods. |
Sand Casting | Molten aluminum is poured into a mold made from a sand mixture. | Low tooling cost, suitable for large and complex parts, flexible in size and shape, but rougher surface finish. | Heavy machinery, industrial equipment. |
Permanent Mold Casting | Molten aluminum is poured into reusable metal molds using gravity or low pressure. | Consistent quality, smoother finish than sand casting, good dimensional stability, and improved mechanical properties. | Automotive, aerospace components. |
The Properties of Cast Aluminum
Aluminum casting alloys typically contain over 90% aluminum, with other elements like silicon, copper, magnesium, or zinc added to enhance specific characteristics. Here are some key properties that make cast aluminum a popular choice:
- Lightweight: Aluminum’s low density makes it an ideal choice for applications where weight reduction is crucial without sacrificing strength. This property is particularly valuable in industries like automotive and aerospace, where every ounce counts.
- Strength and Durability: While not as strong as steel, certain cast aluminum alloys offer impressive strength and durability, often exceeding that of plastic or wood. This makes it suitable for a range of demanding applications.
- Corrosion Resistance: Aluminum naturally forms a protective oxide coating when exposed to air, rendering it resistant to corrosion. This characteristic can be further enhanced through treatments like anodizing or painting, making it ideal for outdoor applications.
- Conductivity: Aluminum is an excellent conductor of heat and electricity, which makes it suitable for applications like heat sinks in electronics and electrical components.
- Recyclability: Aluminum is 100% recyclable without any loss of quality, contributing to its popularity in sustainable manufacturing practices. This aspect aligns with the growing emphasis on eco-friendly production methods.
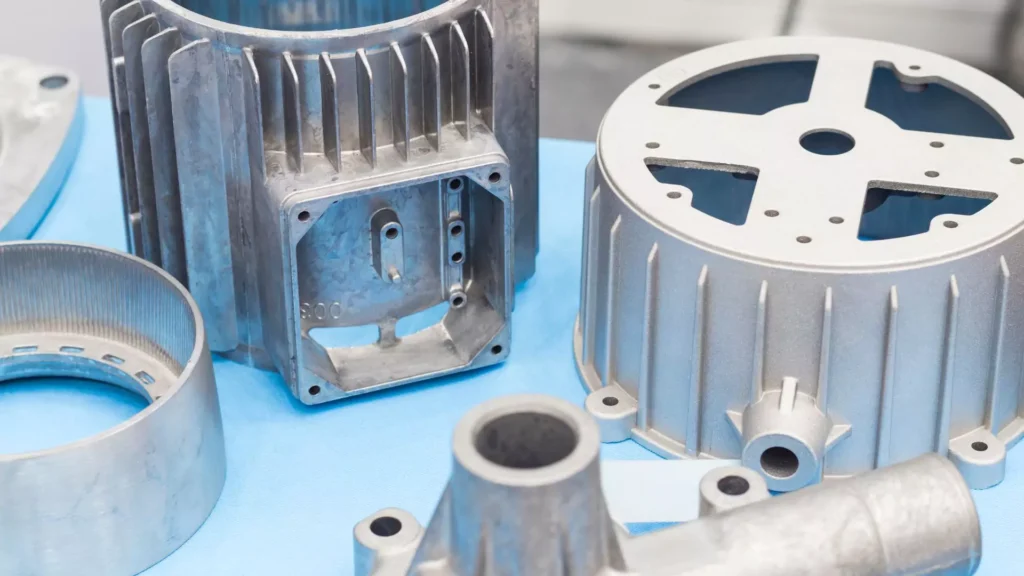
Benefits of Using Cast Aluminum
The advantages of using cast aluminum in manufacturing are vast:
- Design Flexibility: The casting process allows for the creation of complex shapes and intricate details, providing designers with a high degree of creative freedom. This flexibility enables the production of parts that are both functional and aesthetically pleasing.
- Cost-Effective Production: Aluminum casting can be more cost-effective than other metalworking processes, especially for large production runs. The ability to produce multiple parts in a single cycle reduces overall costs.
- Reduced Assembly Needs: Components can often be designed to consolidate multiple parts into a single cast, minimizing the need for assembly and lowering production costs.
- Superior Aesthetics: Cast aluminum can achieve a high-quality surface finish that is both functional and visually appealing, making it suitable for consumer products where appearance matters.
Applications of Cast Aluminum
The versatility of cast aluminum makes it a staple in numerous industries:
- Automotive: Engine components, wheels, and transmission housings are often made from cast aluminum for their strength and lightweight properties.
- Aerospace: The process is used to create structural parts for aircraft that require precision and strength without adding unnecessary weight.
- Consumer Goods: Everything from electronics to cookware benefits from aluminum’s thermal properties and ease of casting.
- Construction: Aluminum casting is used in building materials for its durability and resistance to corrosion.
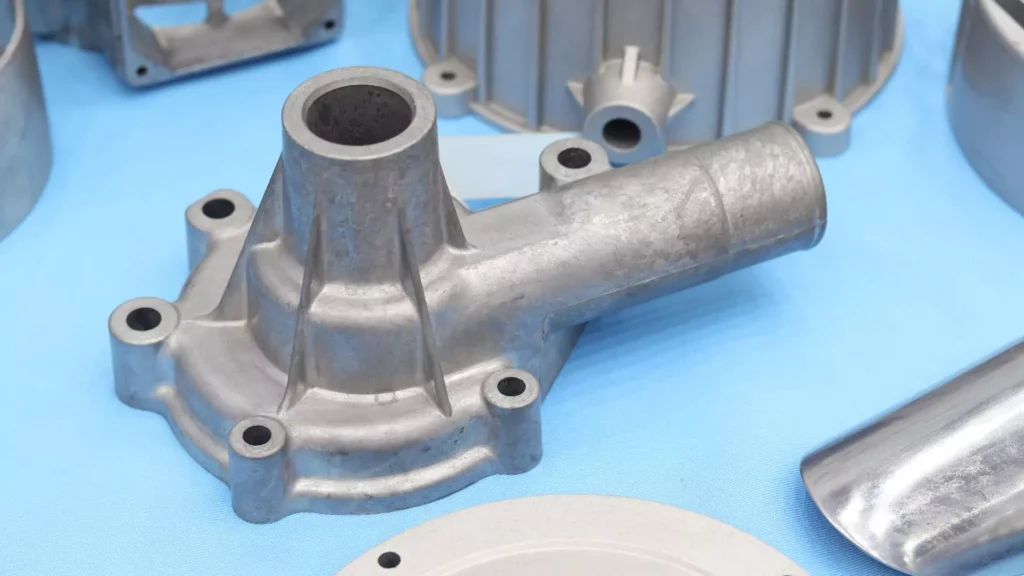
Disadvantages of Cast Aluminum
While cast aluminum offers numerous benefits, there are some limitations to consider:
- Lower Strength Compared to Steel: Although strong, cast aluminum does not match the tensile strength of steel, which can limit its use in high-stress applications.
- Brittleness: Certain aluminum alloys can be more brittle than other metals, especially under extreme conditions, leading to potential cracking.
- Higher Initial Costs: The costs associated with casting aluminum can be higher than some other materials, particularly if complex molds are required.
Cast Aluminum vs. Cast Steel
When comparing cast aluminum to cast steel, several factors come into play:
Strength and Weight
Cast steel generally offers higher strength, but cast aluminum’s strength-to-weight ratio is advantageous for many applications.
Cost Implications
Cast steel can be more expensive due to its material properties and the energy required to produce it.
Application Suitability
- Cast Steel: Preferred for heavy-duty structural components due to its high strength.
- Cast Aluminum: Chosen for applications where weight savings are critical, such as in transportation and mobile equipment.
Cast Aluminum vs. Grey Iron
Grey iron and cast aluminum are used in different scenarios based on their material characteristics:
Material Characteristics
Grey iron is known for its compressive strength and excellent vibration damping, whereas cast aluminum offers better corrosion resistance and weight savings.
Machinability and Usage
Grey iron is easily machinable but cast aluminum is preferred for complex shapes and thin-walled components.
Industry Preferences
- Grey Iron: Favored in the construction and industrial sectors.
- Cast Aluminum: Popular in the automotive, aerospace, and consumer electronics industries due to its lightness and durability.
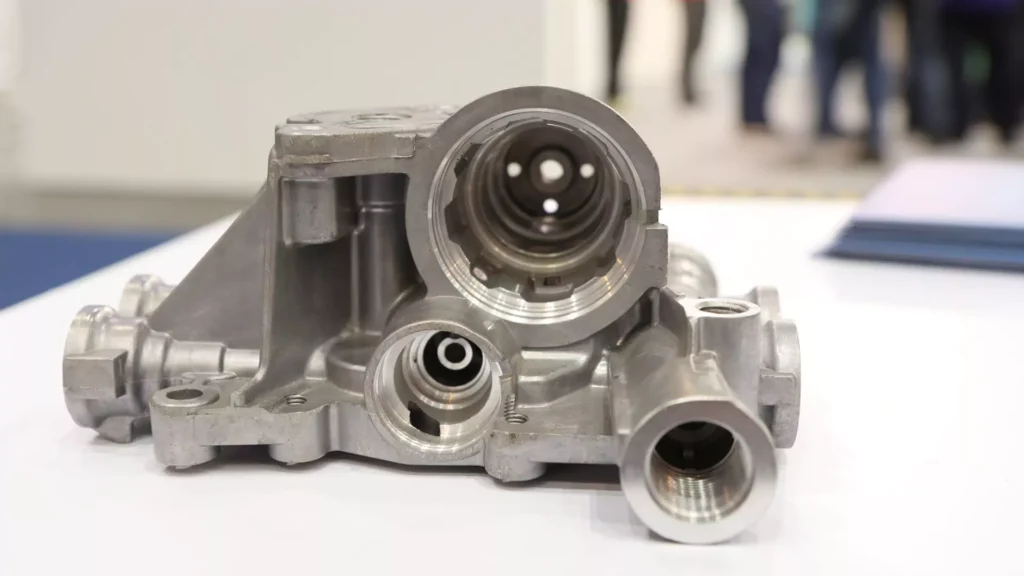
Comparison of Cast Aluminum, Cast Steel, and Grey Iron
Property/Aspect | Cast Aluminum | Cast Steel | Grey Iron |
Density | ~2.7 g/cm³, lightweight. | ~7.7–7.85 g/cm³, heavier. | ~7.1–7.3 g/cm³, relatively heavy. |
Tensile Strength | 100–400 MPa; 7068 alloy can reach 710 MPa. | 340–1800 MPa, depending on alloy and heat treatment. | 150–400 MPa; ASTM A48 Class 40 has 276 MPa. |
Compressive Strength | Good, lower than cast iron; depends on alloy. | High, suitable for heavy loads. | Excellent, often >1000 MPa. |
Melting Point | 570–655°C. | 1450–1520°C. | 1150–1250°C. |
Thermal Conductivity | 120–180 W/m·K, excellent for heat dissipation. | Moderate. | ~46 W/m·K, moderate. |
Electrical Conductivity | Good, ideal for electrical components. | Poor, not suited for electrical applications. | Poor, unsuitable for electrical applications. |
Machinability | Easy to machine, allows for complex shapes. | Moderate, requires specialized tools. | Good machinability; brittleness requires care. |
Corrosion Resistance | Excellent; protective oxide layer enhances durability. | Moderate; rusts without surface treatment. | Poor; prone to corrosion, especially in moisture. |
Vibration Damping | Moderate; less effective than grey iron. | Good; better than aluminum but less effective than grey iron. | Excellent; graphite flakes provide superior damping. |
Common Applications | Automotive parts, aerospace components, consumer electronics. | Heavy machinery, structural components, applications needing high strength and toughness. | Engine blocks, machine bases, pipes, and vibration-damping applications. |
Cost | Lower for mass production due to efficiency and material availability. | Higher, due to material and processing costs. | Moderate; brittleness may lead to higher maintenance or replacement costs in specific applications. |
Conclusion
Cast aluminum stands as a testament to the ingenuity of modern manufacturing. With its blend of durability, versatility, and sustainability, this material continues to push the boundaries of what’s possible across various sectors. Whether it’s in the engine of your car, the body of your smartphone, or the frame of your bicycle, cast aluminum is a material that not only meets the demands of today’s manufacturers but also holds promise for the innovations of tomorrow.
For businesses looking to maximize the benefits of cast aluminum in their products, Align Manufacturing offers expert engineering solutions and support to help navigate the complexities of aluminum casting. Their commitment to quality and efficiency ensures that your projects meet the highest standards and expectations.
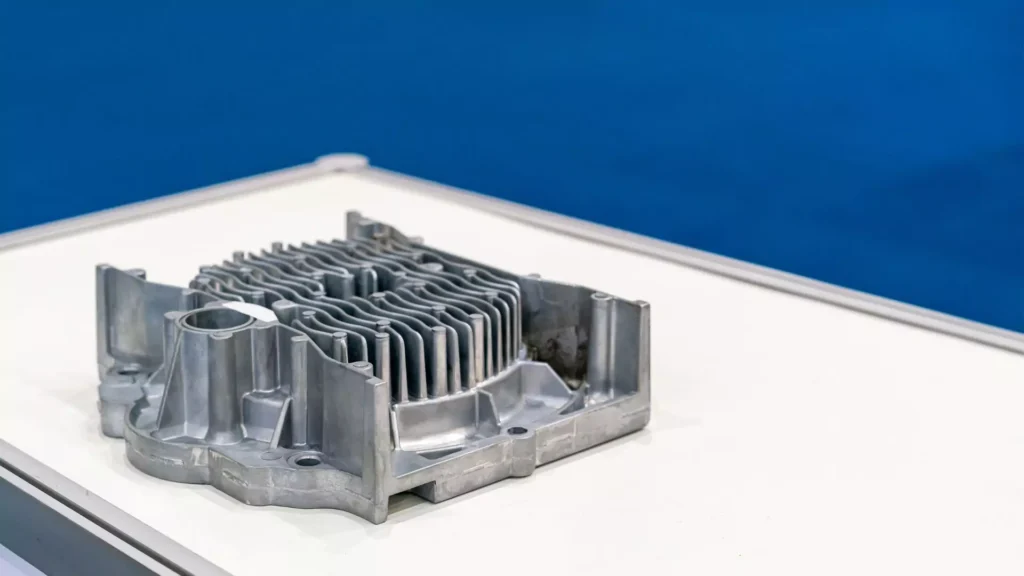
FAQs
Lightweight with High Strength-to-Weight Ratio
Cast aluminum is significantly lighter than materials like cast steel or grey iron, reducing overall product weight without compromising strength. This is particularly advantageous in industries like aerospace, automotive, and electronics, where weight reduction directly impacts performance and efficiency.
Lower Melting Point for Energy Efficiency
With a melting point of 570–655°C, aluminum requires less energy to cast compared to steel or iron, lowering energy costs in the production process. This makes it particularly suited for methods like permanent mold casting, where efficiency is critical.
Versatile Casting Options
Aluminum’s lower melting point and excellent fluidity enable the use of various casting techniques (e.g., die casting, sand casting, permanent mold casting) to create complex shapes and intricate designs. This versatility reduces tooling costs and expands design possibilities.
Corrosion Resistance for Durability
Aluminum naturally forms a protective oxide layer, which enhances its resistance to rust and corrosion. This eliminates or reduces the need for additional surface treatments, saving on production and maintenance costs while ensuring longevity.
Thermal and Electrical Conductivity
Its excellent thermal and electrical conductivity makes cast aluminum ideal for applications requiring efficient heat dissipation or electrical performance, such as electronic enclosures and heat exchangers.
Machinability for Lower Production Time
Cast aluminum is easier to machine compared to steel or iron, allowing for faster production cycles and reduced labor costs. This also facilitates the production of custom or precision parts with minimal tool wear.
Cost-Effectiveness in High-Volume Production
Aluminum casting is particularly economical for mass production due to its combination of low material costs, reduced energy requirements, and quick production times. This provides manufacturers with a
- Cast Aluminum: Produced through casting, where molten aluminum is poured into molds to create complex shapes with high density and strength.
- Aluminum: Typically created through extrusion, forging, or rolling, forming simpler shapes like plates, rods, or profiles with variable strength and hardness.
How do their applications differ?
- Cast Aluminum: Commonly used in automotive parts, machinery, and equipment requiring intricate designs and durability.
- Aluminum: Preferred for aerospace, construction, and electronics due to its versatility, lightweight nature, and ability to handle higher strength and hardness needs.
Which material is more cost-effective for manufacturing?
- Cast Aluminum: Has lower manufacturing costs due to the efficiency of the casting process.
- Aluminum: Raw material is generally less expensive, but processing costs (e.g., extrusion or forging) are higher.
How do they compare in terms of processability and surface treatments?
Both materials offer excellent processability and surface treatment properties, including the ability to be anodized or sprayed, making them suitable for various functional and aesthetic applications.
What are the density and strength differences?
- Cast Aluminum: Features higher density and strength, making it ideal for parts requiring structural integrity and durability.
- Aluminum: Typically lighter and has variable strength depending on the alloy and manufacturing process, suiting applications where weight reduction is critical.
By understanding these differences, manufacturers can select the material that best aligns with their project’s requirements, whether for cost efficiency, strength, or design complexity.
- What are the main raw materials in cast aluminum?
Cast aluminum is made from various aluminum alloys, which include alloying elements like silicon, copper, zinc, magnesium, and manganese to enhance specific properties such as strength, corrosion resistance, and machinability. - What are common types of aluminum alloys used in casting?
- Aluminum-Silicon Alloy (Al-Si): Improves fluidity and reduces thermal shrinkage, used in engine parts and hydraulic components. Examples: A390, A380, A356.
- Aluminum-Copper Alloy (Al-Cu): Offers high strength and wear resistance, ideal for aircraft parts and turbine blades. Examples: A201, A202.
- Aluminum-Magnesium Alloy (Al-Mg): Features low density and excellent corrosion resistance, used in aerospace and automotive wheels. Examples: A5182, A5052.
- Aluminum-Zinc Alloy (Al-Zn): Provides high strength and corrosion resistance, commonly used for automotive and mechanical parts. Examples: A7075, A7049.
- Aluminum-Manganese Alloy (Al-Mn): Known for corrosion resistance, suitable for special environments like seawater applications. Examples: A3004, A3003.
For more information on alloys check out our guide : https://alignmfg.co/materials/metal/alloys-customizable-and-high-performance/
Yes, aluminum can be welded, but it requires specialized techniques and equipment compared to steel. Different aluminum alloys also have varying weldability.
Aluminum Die Casting: Definition & Process
Key Takeaways: Aluminum Die Casting
Aspect | Key Details |
What It Is | A manufacturing process that produces smooth, textured, and precise metal parts. |
How It Works | Involves forcing molten aluminum into a steel mold (die) using high-pressure systems. |
Key Properties | - Corrosion resistance- High thermal and electrical conductivity- Good stiffness and strength-to-weight ratio. |
Advantages | - Lightweight and high dimensional stability- Suitable for complex geometries and thin walls- Cost-effective compared to other casting processes. |
Production Efficiency | - Rapid production allows high volumes to be produced quickly.- Ideal for mass manufacturing. |
Durability | Retains strength and dimensional stability even at very high temperatures. |
Cold Chamber Process | Uses cold chamber machines to handle molten aluminum, which is ladled into the die due to high operating temperatures. |
Applications | Widely used in automotive, aerospace, electronics, and consumer goods for durable, lightweight parts. |
Aluminum die casting has become a transformative force in the manufacturing industry, offering unparalleled efficiency, precision, and durability for a wide range of products. This process is a staple in sectors such as automotive, aerospace, electronics, and consumer goods due to its ability to produce complex shapes with high accuracy. In this comprehensive guide, we will explore the intricacies of aluminum die casting, including its various applications, types, advantages, disadvantages, and the overall process involved.
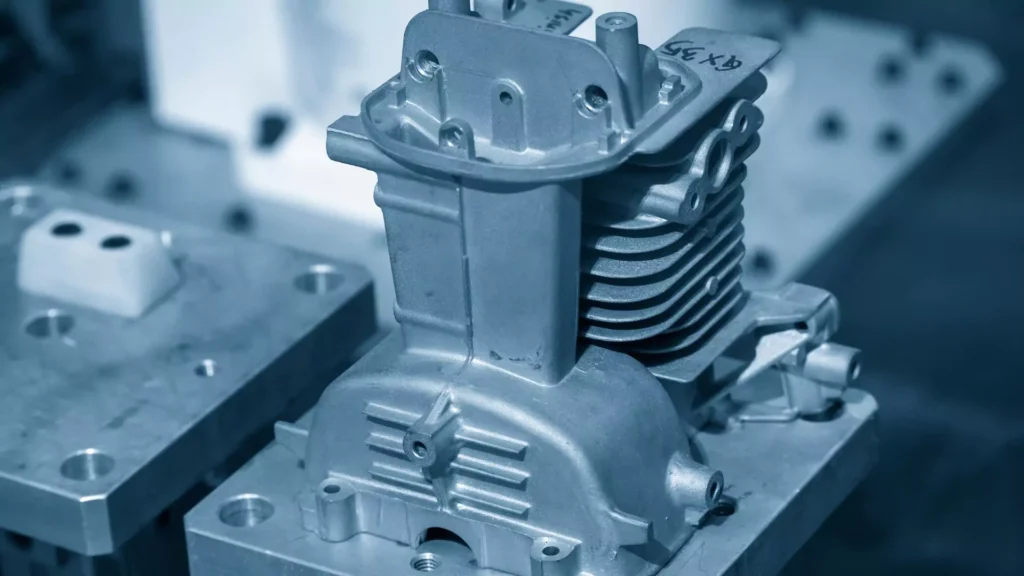
What is Aluminum Die Casting?
Aluminum die casting is a metal fabrication process that involves forcing molten aluminum under high pressure into a steel mold, known as a die. Once the aluminum solidifies, the die is opened to reveal a lightweight yet sturdy component. This method allows for the creation of intricate designs and tight tolerances, making it ideal for mass production of detailed parts.
The Aluminum Die Casting Process
The aluminum die casting process typically follows these key steps:
The Aluminum Die Casting Process
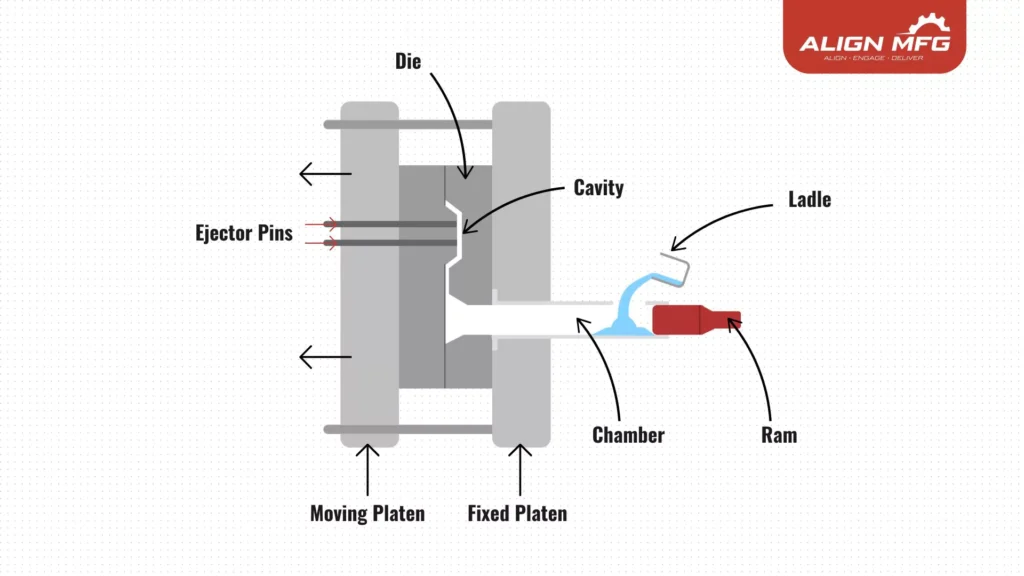
The aluminum die casting process follows these key steps, each involving precise engineering to ensure high-quality results:
- Mold Design and Creation:
- The process begins with designing and manufacturing a durable steel mold capable of producing tens of thousands of castings.
- Each mold consists of at least two sections, allowing for the removal of cast parts. Depending on the complexity of the design, molds may include movable slides, cores, or other specialized sections.
- Clamping and Preparation:
- The two mold halves are mounted securely in the die casting machine. One half remains stationary, while the other is movable.
- Before injection, the mold halves are clamped tightly together using hydraulic cylinders or direct hydraulic pressure, ensuring no gaps exist for molten aluminum to escape.
- Melting and Injection:
- Aluminum is melted in a furnace to the necessary temperature and prepared for injection.
- The molten aluminum is then injected into the die cavity under high pressure, which ensures the material fills every detail of the mold.
- Depending on the machine type (cold chamber or hot chamber), the method of injecting molten aluminum may vary, but the fundamental principles remain the same.
- Hot chamber machines feature a built-in furnace that melts the metal directly within the casting machine, making it ideal for low-melting-point metals like zinc and magnesium alloys. This process is faster, with shorter cycle times.
- Cold chamber machines, on the other hand, use an external furnace to melt higher-melting-point metals, such as aluminum and brass. The molten metal is then transferred to the casting machine using a ladle, resulting in longer cycle times due to the additional transfer step.
- Cooling and Solidification:
- The molten aluminum rapidly cools within the mold cavity, taking on its precise shape as it solidifies.
- The rapid cooling process enhances the part’s dimensional accuracy and structural integrity.
- Ejection:
- Once the part has solidified, the movable die half separates from the stationary half.
- The casting is ejected using ejector pins or other mechanisms, ensuring smooth removal without damaging the mold or the part.
- Trimming and Flash Removal:
- Excess material, known as flash, is trimmed away to refine the part's edges and ensure it meets design specifications.
- Additional trimming may be needed for complex designs with slides or cores.
- Finishing:
Types of Finishing for Aluminum Die-Cast Parts
Bead Blasting
- Creates a uniform, matte finish by using fine beads to smooth and clean the surface.
- Ideal for aesthetic purposes and removing minor surface imperfections.
Anodizing
- Enhances corrosion resistance, improves wear resistance, and provides a decorative finish.
- Available in various colors and commonly used in consumer goods and automotive applications.
Plating
- Adds a protective or decorative metal layer (e.g., chrome, nickel) to improve durability and aesthetics.
- Often used in electrical, automotive, and decorative parts.
Powder Coating
- Provides a durable, corrosion-resistant, and attractive finish using an electrostatically applied powder that is baked to cure.
- Available in a wide range of colors and textures, commonly used in industrial and outdoor applications.
Painting
- Used for aesthetic purposes or additional corrosion resistance.
- Includes wet painting or spray painting with various finishes (glossy, matte, etc.).
Polishing
- Achieves a smooth, reflective surface by mechanically buffing the part.
- Often applied to components requiring a sleek, high-end look.
Chromate Conversion Coating
- A chemical treatment to improve corrosion resistance and paint adhesion.
- Commonly used in aerospace and automotive parts.
Brushing
- Produces a directional, textured finish with fine lines, enhancing visual appeal while reducing visible imperfections.
Deburring
- Removes sharp edges or burrs left from the die-casting process to improve safety and functionality.
E-Coating (Electrocoating)
- Involves immersing the part in a liquid paint solution and applying an electric charge to coat the surface uniformly.
- Offers excellent corrosion resistance and is used in automotive and industrial applications.
These finishing options enhance the appearance, durability, and performance of aluminum die-cast parts, making them suitable for diverse applications across industries.
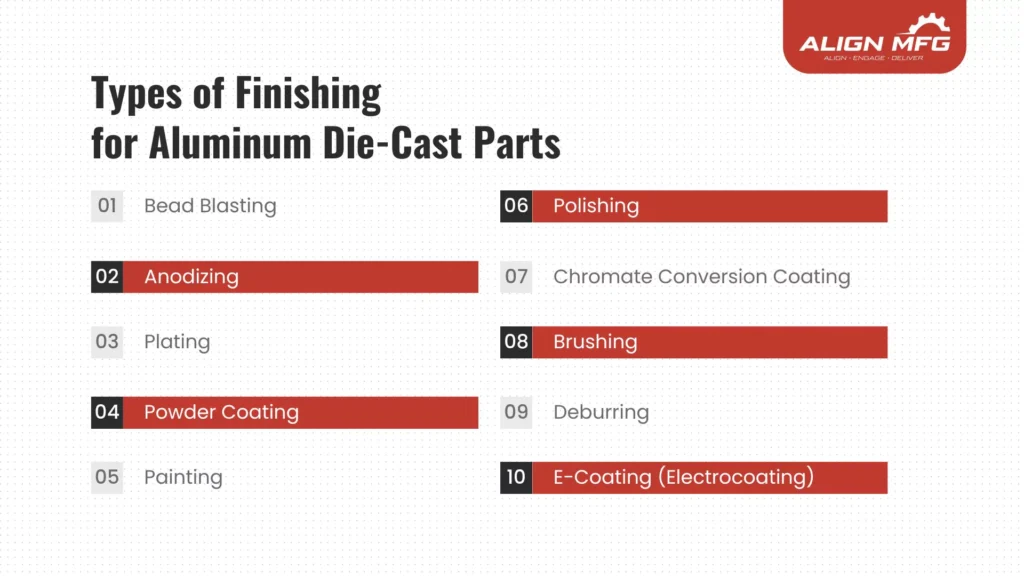
Different Types of Aluminum Casting
Aluminum casting can be categorized into several types, each suited for specific applications:
- Die Casting: As discussed, this involves forcing molten aluminum into a mold under high pressure. It's ideal for high-volume production of complex parts.
- Sand Casting: This method uses sand molds to create parts by pouring molten aluminum into the mold. It's more flexible for low-volume production and complex shapes but may not provide the same precision as die casting.
- Investment Casting: Also known as lost-wax casting, this technique involves creating a wax model, coating it in ceramic, and then melting away the wax to leave a mold for aluminum. It’s excellent for intricate designs but is generally more expensive.
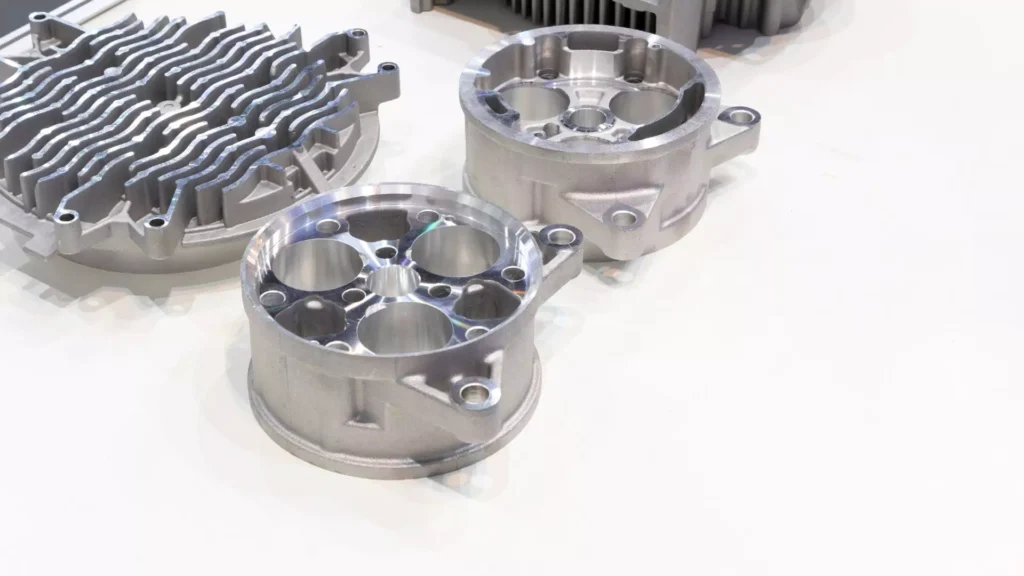
Advantages of Aluminum Die Casting
The benefits of using aluminum die casting in manufacturing are numerous:
- High-Speed Production: Die casting enables rapid production of parts, significantly reducing lead times and allowing for high-volume manufacturing without sacrificing quality.
- Dimensional Accuracy and Stability: The die casting process produces parts with exceptional precision and consistency, ensuring that each piece meets strict specifications.
- Strength and Lightweight: Aluminum’s natural strength-to-weight ratio makes it perfect for creating robust parts that are lighter than those made from other metals, contributing to fuel efficiency in automotive and aerospace applications.
- Multiple Finishing Techniques: Aluminum die cast parts can be easily finished with various techniques, including sandblasting, painting, or plating, providing aesthetic versatility and additional corrosion resistance.
- Recyclability: Aluminum is highly recyclable, which reduces waste and promotes sustainability in manufacturing.
Disadvantages of Aluminum Die Casting
While aluminum die casting has many advantages, there are also some limitations to consider:
- High Startup Costs: High Startup Costs: The initial tooling costs for die casting can be significant, as custom molds need to be designed and manufactured, which can be time-consuming and expensive. Additionally, CNC machines are often required for precision machining and finishing of the die-cast parts, further increasing the upfront investment.
For more on how to reduce costs when buying aluminum die cast parts,check out our guide.
- Limited to High-Volume Production: Due to the high costs associated with tooling, die casting is most economical for medium to high-volume production runs. Smaller production runs can lead to increased per-unit costs.
- Complex Geometries Can Be Costly: Parts with intricate designs may require additional machining or sliding cores, increasing the overall production cost.
- Low Initial Production Speed: The tooling process can take time before any final production parts are made, which can delay the start of manufacturing.
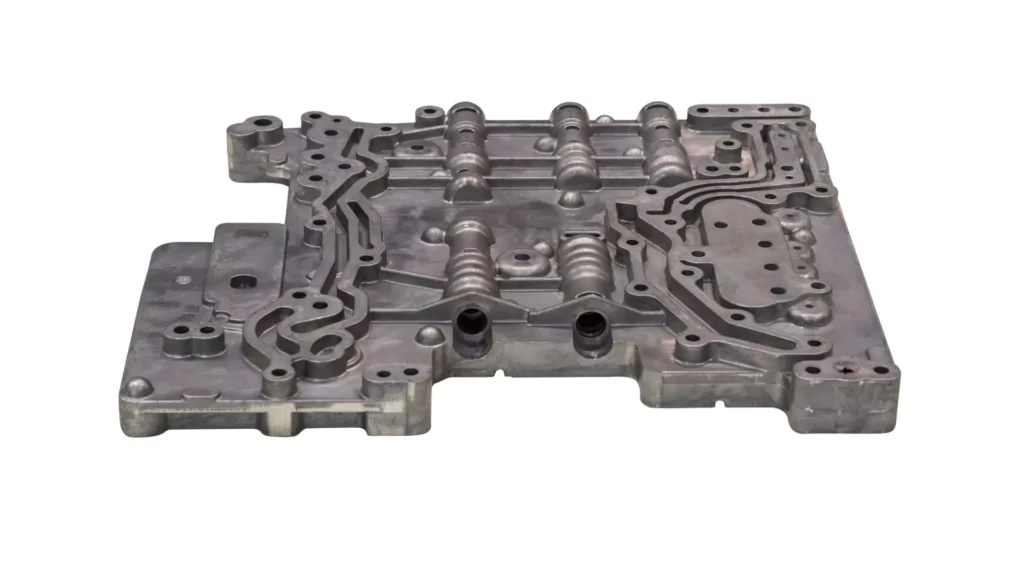
Grades of Aluminum Die Casting
Aluminum die casting utilizes various grades of aluminum alloys, each offering different properties:
- A380: This is the most commonly used grade due to its excellent casting characteristics, mechanical strength, and thermal properties. It offers good castability and is cost-effective.
- A383 / ADC12: This grade is great for intricate parts with thin walls and has better corrosion resistance than A380, although it has lower tensile strength.
- A413: Known for its excellent pressure tightness, this grade is ideal for high-pressure applications and offers superior corrosion resistance.
Applications of Aluminum Die Casting
The versatility of aluminum die casting leads to its use in various industries:
- Automotive: Parts such as engine components, transmission cases, and structural components benefit from aluminum's lightweight and strength properties.
- Aerospace: The process is used to create structural parts for aircraft that require precision and strength without adding unnecessary weight.
- Consumer Electronics: Aluminum die castings are found in laptops, smartphones, and other devices, where their thermal properties and sleek finishes are highly valued.
- Industrial Machinery: Manufacturers rely on die-cast aluminum parts for their reliability and resistance to harsh conditions.
Cost of Aluminum Die Casting
The cost of aluminum die casting can vary significantly based on several factors, including the complexity of the part, the volume of production, and the specific aluminum alloy used. Initial tooling costs can range from a few thousand dollars to much higher amounts for complex designs. However, once the tooling is established, the per-unit cost can be very low, making aluminum die casting an economical choice for high-volume production.
Conclusion
Aluminum die casting stands as a cornerstone of modern manufacturing, delivering an exceptional balance of efficiency, precision, and performance. As industries evolve and demand for lightweight, durable components increases, the significance of aluminum die casting will only grow. For those seeking a reliable partner in aluminum die casting, look no further than Align Manufacturing. Their expertise in this innovative process ensures high-quality results tailored to your specific needs.
Align Manufacturing recognizes the growing importance of aluminum die casting in today's evolving industries, where lightweight and durable components are increasingly crucial. As a trusted partner, Align Manufacturing leverages its expertise to deliver high-quality, custom-tailored aluminum die-castings that meet the unique demands of your specific applications.
FAQs
Aluminum die casting has several environmental advantages compared to other casting methods like sand casting and investment casting. One of the primary benefits is the recyclability of aluminum. Aluminum can be recycled indefinitely without losing its properties, which significantly reduces waste and energy consumption associated with raw material extraction and processing.
Furthermore, die casting typically produces less scrap material compared to sand casting, where excess sand can lead to greater waste. Additionally, advancements in die casting technology are leading to more energy-efficient processes, further minimizing the environmental footprint.
Aluminum die casting, developed in the early 20th century, has become a cornerstone in manufacturing due to its efficiency and the superior properties of aluminum alloys. The process involves injecting molten aluminum into steel molds under high pressure, enabling the rapid production of complex, high-precision parts. Aluminum's inherent corrosion resistance, high thermal and electrical conductivity, and excellent strength-to-weight ratio make it a preferred material across various industries.
Industries Utilizing Aluminum Die Casting:
- Automotive: Engine components, transmission housings, and structural parts.
- Aerospace: Aircraft fittings and components requiring precision and reliability.
- Electronics: Housings and heat sinks benefiting from aluminum's conductivity.
- Consumer Goods: Appliance parts and handheld device enclosures.
According to statistics, the global aluminum die casting market is set to significantly expand. In 2024, it was valued at $31.37 billion. Projections indicate a substantial growth trajectory, reaching an estimated $66.28 billion by 2032. This translates to a compound annual growth rate (CAGR) of 9.80% throughout the forecast period from 2025 to 2032.
This growth is driven by increasing demand in the automotive sector for lightweight, fuel-efficient vehicles, as well as expanding applications in industrial and consumer products.
Aluminum die casting's combination of efficiency, precision, and material advantages continues to make it a popular choice for manufacturers aiming to produce high-quality components across diverse sectors.
Several innovations are shaping the future of aluminum die casting, including advancements in automation and robotics, which enhance production efficiency and precision. New materials, such as advanced aluminum alloys and metal matrix composites, are being developed to improve the mechanical properties of die-cast parts. Additionally, there is a growing emphasis on improving recycling techniques to facilitate the reuse of aluminum scrap generated during the die casting process. These innovations not only streamline manufacturing but also contribute to sustainability goals by reducing waste and energy consumption.
The choice of aluminum alloy significantly impacts the die casting process and the properties of the final product. Different alloys have varying melting points, fluidity, and mechanical properties, which can influence the casting process's efficiency and the quality of the parts produced. For example, alloys like A380 are commonly used due to their excellent castability and mechanical strength, making them suitable for a wide range of applications. On the other hand, alloys like A413 offer superior pressure tightness and corrosion resistance, making them ideal for specific high-pressure applications. When selecting an alloy, factors such as the desired mechanical properties, application requirements, and cost considerations must be taken into account.
Yes, aluminum die casting can be used to create parts with very tight tolerances, but there are limitations. The inherent nature of the die casting process allows for high precision, typically within ±0.005 inches for most applications. However, achieving extremely tight tolerances may require additional machining or specific techniques, such as using sliding cores or advanced mold designs. It's essential to work closely with experienced manufacturers who can implement best practices in design and production to meet stringent tolerance requirements while ensuring the efficiency and cost-effectiveness of the process.
Extend the Life of Your Stainless Steel: A Maintenance Guide
Stainless steel is a versatile and durable material that has become a staple in both industrial and consumer applications. Whether used in kitchen appliances, architectural elements, or medical equipment, the aesthetic appeal and functionality of stainless steel make it a popular choice. However, to preserve its shine and integrity, proper maintenance is essential. .
This guide will explore the best practices for maintaining stainless steel, emphasizing the importance of regular care and the expertise offered by Align Manufacturing, a leading provider of stainless steel products and maintenance solutions.
Stainless steel is an iron alloy with a minimum of 10.5% chromium content by mass. This chromium forms a passive layer of chromium oxide on the surface, which prevents further surface corrosion and blocks corrosion from spreading into the metal’s internal structure. While stainless steel is known for its resistance to rust, it can still accumulate dirt, grime, and even undergo corrosion if not properly maintained.
Type | Composition | Key Properties | Common Applications |
304 | 18% Cr, 8% Ni | Excellent corrosion resistance; good formability and weldability; non-magnetic | Kitchen equipment, chemical processing, architectural applications |
316 | 16% Cr, 10% Ni, 2% Mo | Superior corrosion resistance, especially against chlorides and marine environments; non-magnetic | Marine equipment, medical devices, chemical processing |
409 | 11% Cr | Good corrosion resistance; high-temperature tolerance; magnetic | Automotive exhaust systems, heat exchangers |
430 | 17% Cr | Good corrosion resistance; formability; magnetic | Appliance trims, kitchen utensils, decorative applications |
440C | 17% Cr, 1.1% C | High hardness and wear resistance; moderate corrosion resistance; magnetic | Cutting tools, bearings, surgical instruments |
Cr = Chromium, Ni = Nickel, Mo = Molybdenum, C = Carbon
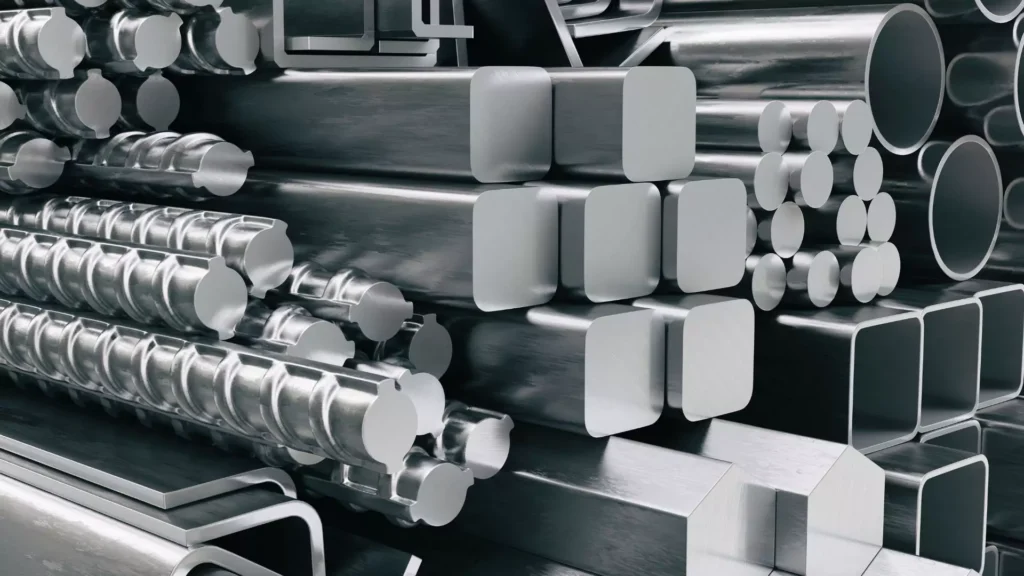
Types of Corrosion
Galvanic Corrosion:
- Galvanic corrosion occurs when two dissimilar metals are in electrical contact in the presence of an electrolyte (like saltwater or even just moisture).
- The more active metal (the anode) corrodes while the less active metal (the cathode) is protected.
Key Tip
Common Combinations to Avoid:
- Stainless Steel and Copper: Copper is more noble than many stainless steels, leading to accelerated corrosion of the stainless steel.
- Stainless Steel and Brass: Brass, containing copper, can also induce galvanic corrosion in stainless steel.
- Stainless Steel and Lead: Lead is more anodic than many stainless steels, increasing the risk of corrosion.
- Stainless Steel and Zinc: While zinc is often used for sacrificial protection, direct contact with certain stainless steels can lead to localized corrosion.
Minimizing Galvanic Corrosion:
- Isolate Dissimilar Metals: Whenever possible, physically separate dissimilar metals using insulating materials like plastic washers, gaskets, or coatings.
- Select Compatible Metals: Choose metals that are close together in the galvanic series to minimize the potential for significant galvanic corrosion.
- Consider Sacrificial Anodes: In some applications, using a more active metal (like zinc) as a sacrificial anode can protect the stainless steel from corrosion.
Design for Drainage: Ensure proper drainage to minimize the accumulation of moisture and electrolytes.
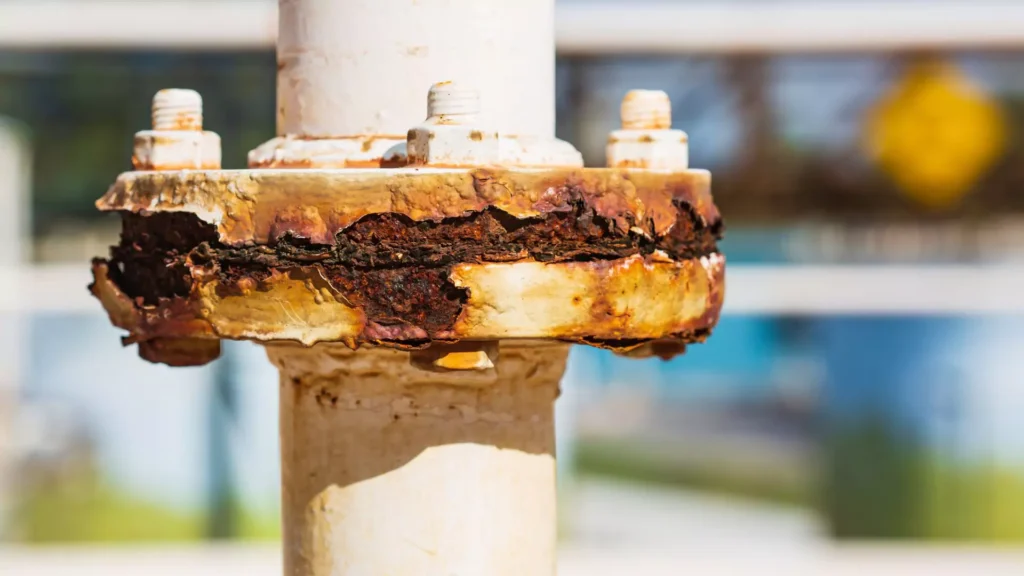
Crevice Corrosion:
- Crevice corrosion happens in confined spaces where moisture can become trapped.
- The trapped moisture becomes stagnant and oxygen-depleted, creating an environment where corrosion can thrive.
- Common locations:
- Under gaskets, washers, and fasteners
- Inside joints and seams
- Beneath stacked materials
- Prevention:
- Ensure proper drainage to prevent water accumulation.
- Regularly clean and inspect crevices.
- Use non-absorbent materials for gaskets and seals.
Pitting Corrosion:
- Pitting corrosion is characterized by the formation of small, localized pits or holes in the metal surface.
- It often occurs in the presence of chlorides (like saltwater) and acidic environments.
- Identification:
- Look for small, often inconspicuous, pits or holes in the surface.
- Prevention:
- Regularly clean and rinse the surface to remove chlorides and other contaminants.
- Use corrosion inhibitors in environments with high chloride concentrations.
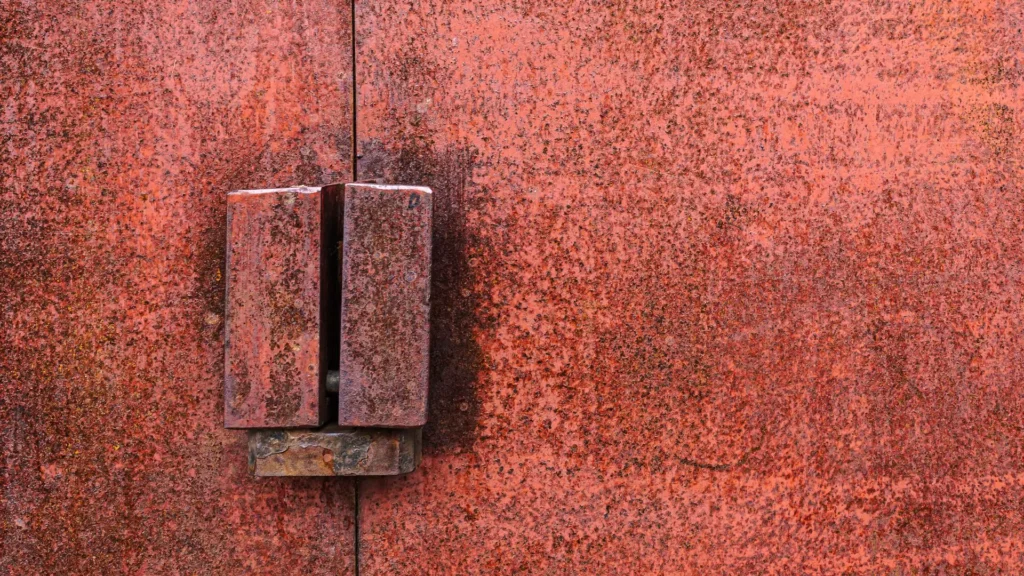
Environmental Factors
- Humidity: High humidity increases the rate of corrosion by providing a constant source of moisture.
- Pollution: Industrial pollutants and airborne contaminants, such as sulfur dioxide and nitrogen oxides, can accelerate corrosion.
- Temperature Fluctuations: Rapid temperature changes can cause thermal stresses in the metal, leading to the formation of microcracks that can accelerate corrosion.
Chlorides, such as salt from de-icing chemicals or seawater, can break down stainless steel’s passive layer, accelerating corrosion. Acids and harsh chemicals also pose risks by stripping away the protective film. To maintain stainless steel’s integrity, avoid cleaners with chlorides, rinse surfaces regularly, and neutralize chemical residues promptly.
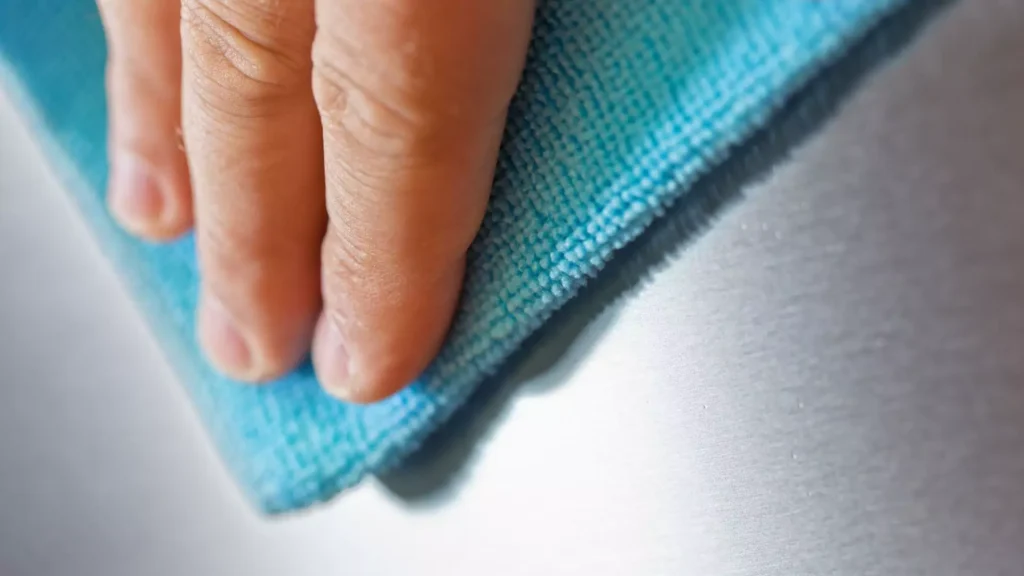
Effective Cleaners for Stainless Steel in Manufacturing
- E-NOX CLEAN
- A specialized cleaner for removing corrosion, stains, and surface contaminants from stainless steel. It is particularly effective for light corrosion caused by environmental factors.
- WD-40 Specialist Cleaner
- A multi-purpose cleaner that provides lubrication and corrosion protection. Commonly used to clean and protect stainless steel surfaces while adding a protective layer.
- Bar Keepers Friend
- A non-abrasive cleaner that effectively removes tough stains, grease, and mild corrosion from stainless steel.
- Sheila Shine
- A stainless steel polish and cleaner that restores shine while protecting against corrosion and fingerprints.
- 3M Stainless Steel Cleaner and Polish
- Designed to clean, polish, and protect stainless steel in one step. It prevents dirt and corrosion buildup.
- Simple Green Pro HD
- A heavy-duty degreaser and cleaner, effective on stainless steel machinery and equipment without causing damage to the surface.
- ZEP Stainless Steel Cleaner
- Formulated for industrial use to remove grease, grime, and stains, while protecting against corrosion.
- Blue Magic Metal Polish Cream
- Effective for restoring and maintaining stainless steel surfaces, particularly those exposed to harsh conditions.
- Flitz Stainless Steel Cleaner
- A biodegradable cleaner that removes oxidation and protects stainless steel surfaces from further corrosion.
- Stellar Solutions CitriSurf 77
- A citric acid-based passivation cleaner that enhances the formation of the chromium oxide layer, preventing corrosion on stainless steel surfaces.
Avoiding Installation Damage
Improper installation can compromise stainless steel’s protective layer.
Stainless steel is an alloy of carbon, iron, and chromium, designed for durability and rust resistance. During manufacturing, processes like polishing and passivation help form a thin chromium oxide layer. This “passive film” acts as a protective barrier, shielding the metal from rust. Remarkably, if this layer is scratched, it self-heals by regenerating when exposed to air, ensuring long-lasting protection
For example, using steel tools on stainless steel can deposit ferrous particles that interfere with the formation of the chromium oxide layer. Even minor scratches from screwdrivers or abrasions from iron equipment can dilute chromium at the surface, leading to rust. Post-installation cleaning is crucial to remove any contaminants and restore balance to the surface chemistry.
Polishing Stainless Steel
For that extra shine, you can polish stainless steel with products designed specifically for this purpose. Remember to polish in the direction of the grain and use a clean, soft cloth for application.
Outdoor Stainless Steel Maintenance
Outdoor stainless steel items are exposed to harsher conditions:
- Frequent Cleaning: Clean outdoor stainless steel more frequently to combat exposure to the elements.
- Protective Coatings: Consider applying a protective coating to outdoor stainless steel to guard against environmental damage.
- Inspection and Repair: Regularly inspect outdoor items for signs of rust or corrosion and address them promptly.
Outdoor stainless steel faces harsher conditions, such as salt, pollutants, and weather fluctuations, which can accelerate corrosion. Regular maintenance includes rinsing surfaces after rain or snow, inspecting for rust or staining, and applying protective coatings to enhance resistance. Adjust your cleaning schedule based on environmental stress—e.g., quarterly for high-salt areas or during seasons with heavy use of de-icing chemicals.
Key Tip: Conduct regular inspections, at least monthly, to identify any signs of corrosion, such as:
- Discoloration
- Rust spots
- Pits
- Cracks
- Staining
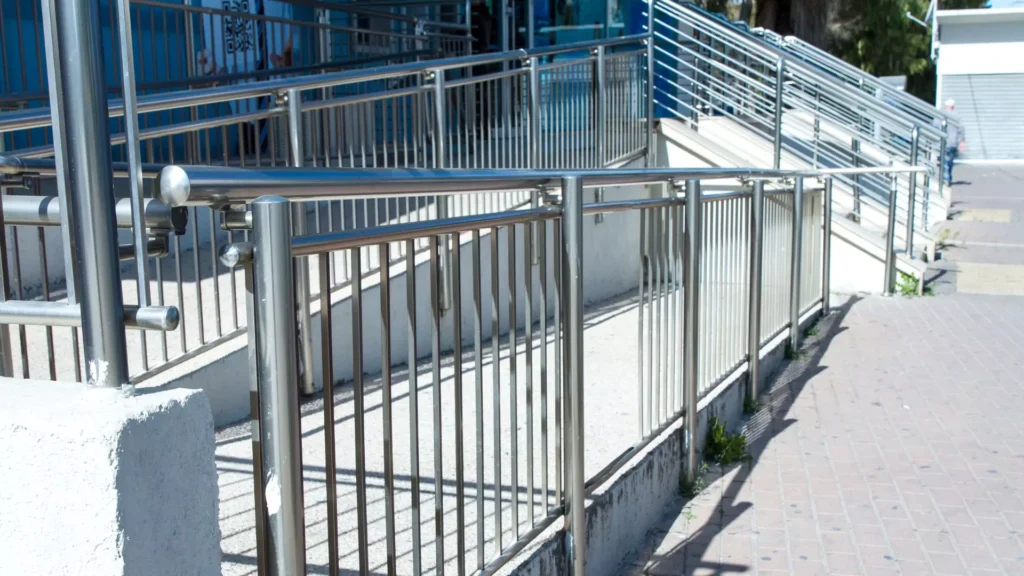
Conclusion
For more information on stainless steel maintenance, contact Align Manufacturing .Whether it’s addressing minor corrosion or maintaining large-scale installations, Align Manufacturing offers the tools and knowledge needed to preserve stainless steel’s shine and strength.
Here’s a concise table summarizing various types of stainless steel, highlighting their key properties and common applications:
For more on how to extend the lifespan of your stainless steel check out our guide here.
Plastic Injection Molding: Understanding the Process and Its Applications
Plastic is an indispensable part of our daily lives, shaping everything from simple household items to complex medical devices. In this blog post, we'll delve into the basics of plastic injection molding, how it works, and why it's such a crucial technique in modern manufacturing.
What is Plastic Injection Molding?
Plastic injection molding is a manufacturing process used to produce large volumes of identical plastic parts. It involves melting plastic pellets and injecting the molten plastic into a mold under high pressure. Once the plastic cools and solidifies, the mold is opened to release the finished part. This process can be repeated multiple times with an incredibly high level of accuracy and speed, making it ideal for mass production.
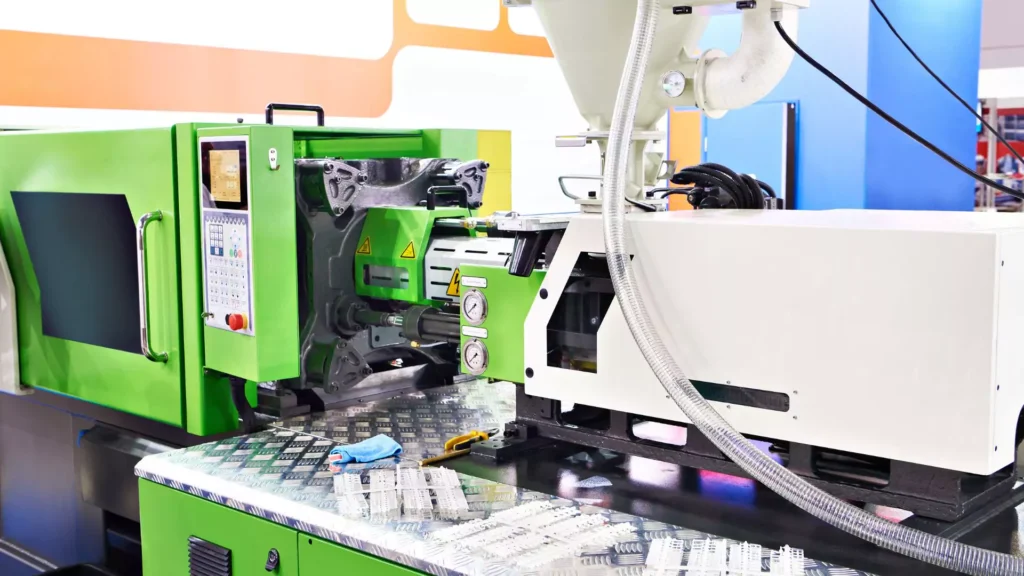
Key Components of Plastic Injection Molding
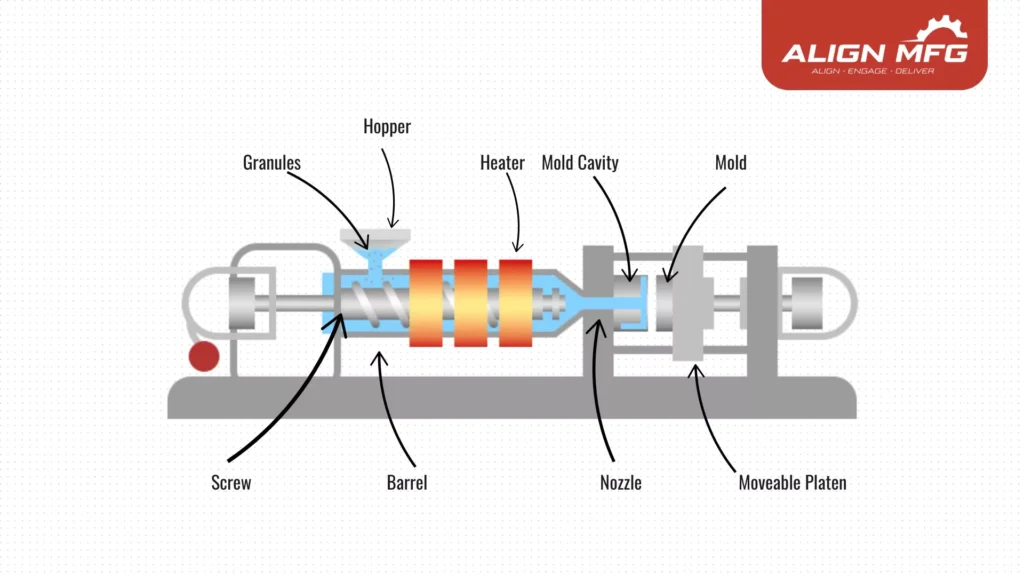
The plastic injection molding process revolves around several key components:
The Injection Molding Machine
At the heart of the injection molding process is the injection molding machine, which consists of two primary components:
- The Injection Unit: This section is responsible for melting the plastic pellets and injecting the molten material into the mold. It features a hopper for feeding the pellets, a barrel for heating, and a screw mechanism that pushes the molten plastic into the mold.
- The Clamping Unit: This part secures the mold during the injection and cooling phases. It ensures that the mold remains tightly closed to prevent any leakage of the molten plastic, which is critical for maintaining the integrity of the final product.
The Mold
Molds are typically crafted from steel or aluminum and are custom-built for each specific project. They can be designed with multiple cavities, allowing for the simultaneous production of several parts in one cycle. The design of the mold is crucial, as it determines the shape, surface finish, and overall quality of the finished product.
Part Name | Function | Details/Insights |
Hopper | Holds and feeds plastic pellets into the barrel. | Often equipped with a dryer to remove moisture, ensuring the quality of the molten plastic. |
Barrel | Heats and melts the plastic pellets into a molten state. | Contains heating bands and uses shear heat from the screw rotation for efficient melting. |
Screw (Reciprocating) | Mixes, melts, and pushes the molten plastic forward into the mold. | Designed to control material flow and ensure uniform melting. |
Nozzle | Directs molten plastic from the barrel into the mold cavity. | May include heaters to maintain consistent flow and avoid cooling before injection. |
Clamp Unit | Holds the mold halves together under high pressure during injection and cooling. | Hydraulic or mechanical clamping systems ensure the mold remains sealed tightly. |
Mold (Fixed and Movable Halves) | Shapes the molten plastic into the desired part. | Consists of a stationary half (attached to the platen) and a movable half (attached to the clamping unit). |
Ejector Pins | Push the cooled, solidified plastic part out of the mold. | Automatically reset for the next injection cycle, ensuring seamless operation. |
Hydraulic System | Powers the clamping and ejection functions. | Operates using hydraulic pressure to move large components like the mold halves efficiently. |
Controller | Manages and monitors machine operations, including temperature, pressure, and cycle timing. | Advanced systems may include touchscreen interfaces and data logging for process optimization. |
Cooling System | Maintains the mold temperature to ensure proper solidification of the plastic. | Uses water or oil circulating through channels within the mold. |
Tie Bars | Provide structural stability to the machine and hold the mold in place during operation. | Commonly found in 4-tie bar configurations for even pressure distribution. |
Injection Unit | Includes the screw, barrel, and nozzle; responsible for injecting molten plastic into the mold cavity. | Controls shot size, injection speed, and pressure. |
Platen (Fixed and Movable) | Supports the mold halves and provides the framework for clamping and ejecting parts. | Movable platen allows for the opening and closing of the mold during cycles. |
Injection Cylinder | Applies high pressure to push the molten plastic into the mold. | Ensures the material completely fills the cavity, even in complex or intricate designs. |
Heater Bands | Surround the barrel to melt the plastic pellets. | Can be individually controlled for precise temperature settings. |
Sprue Bushing | Guides molten plastic from the nozzle into the mold sprue. | Prevents leakage and ensures smooth material flow. |
The Plastic Material
A diverse array of thermoplastics is available to manufacturers, each selected based on the unique properties required for the end product. Commonly used materials include:
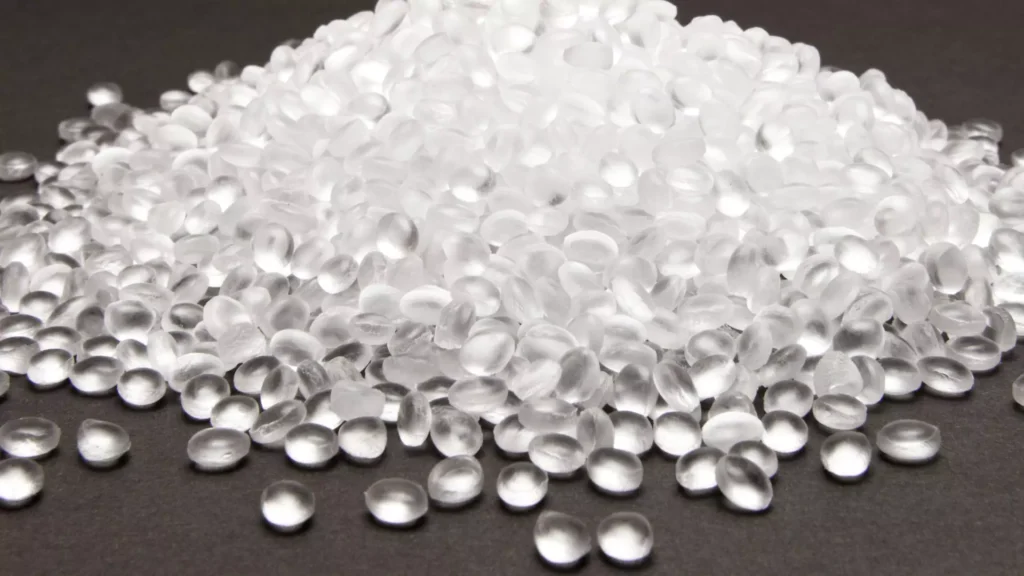
- Acrylonitrile Butadiene Styrene (ABS) : Known for its strength and impact resistance, making it ideal for automotive and consumer products.
- Polycarbonate: Valued for its clarity and heat resistance, often used in applications requiring transparency, such as eyewear lenses.
- Nylon: Recognized for its durability and flexibility, commonly used in automotive and industrial applications.
- Polypropylene (PP) : Lightweight and resistant to chemicals, making it suitable for packaging and consumer goods.
The Injection Molding Process
Plastic injection molding follows a series of steps:
- Step 1: Material Preparation
Plastic pellets are loaded into the hopper, which feeds them into the barrel. Inside the barrel, the reciprocating screw melts the pellets using heat and friction while ensuring uniform mixing. - Step 2: Injection
The molten plastic is pushed forward by the screw under high pressure and forced through the nozzle into the mold cavity. The clamping unit ensures the mold halves are tightly sealed to prevent leaks. - Step 3: Filling and Venting
The molten plastic flows through the sprue, runners, and gates, filling every part of the mold cavity. Trapped air escapes through mold vents, ensuring a flawless part. - Step 4: Cooling and Holding
The mold is kept at a constant temperature to cool the plastic evenly. Holding pressure is applied to prevent backflow and control material shrinkage as the part solidifies. - Step 5: Ejection
Once the plastic has cooled and hardened, ejector pins push the part out of the mold. The platen opens to release the finished part. - Step 6: Repeat
More pellets are automatically fed into the hopper to start the next cycle. The process repeats in a continuous loop, enabling high-speed, efficient production.
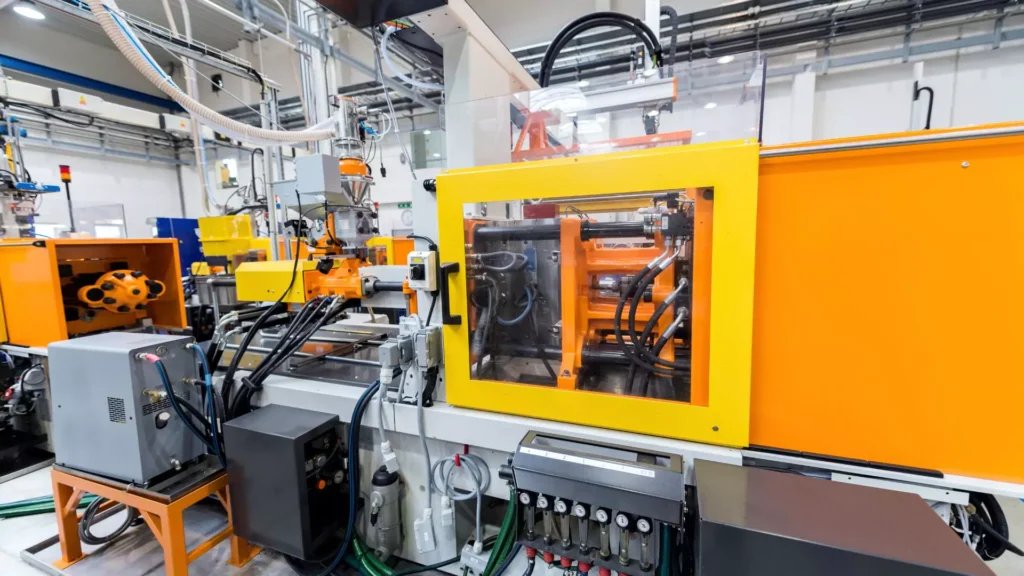
Advantages of Plastic Injection Molding
The popularity of plastic injection molding is due to several compelling advantages:
- Mass Production: One of the strongest benefits is the ability to produce large quantities of parts with consistent quality and tight tolerances.
- Material and Color Flexibility: Manufacturers can choose from a vast array of materials and can easily mix in colors for custom part design.
- Reduced Waste: Excess plastic from the process can often be recycled and reused, minimizing waste.
- Cost-Effectiveness: After the initial cost of designing and creating the mold, the cost per unit during manufacturing is extremely low, especially for high-volume orders.
Disadvantages of Plastic Injection Molding
While plastic injection molding offers many advantages, there are some drawbacks to consider:
- High Initial Costs: The cost of designing and creating molds can be significant, making it less economical for low-volume production runs.
- Limited Design Changes: Once a mold is created, making changes to the design can be costly and time-consuming.
- Material Limitations: Not all plastics are suitable for injection molding, and some materials may require specific conditions or processes.
Applications of Plastic Injection Molding
Plastic injection molding is ubiquitous, finding applications across industries:
1. Automotive Components
Plastic injection molding is widely used in the automotive industry to create components such as dashboards, bumpers, interior trim, and housings for electronic devices. The lightweight nature of molded plastics helps improve fuel efficiency while maintaining strength and durability.
2. Consumer Electronics
Many consumer electronics, including smartphones, tablets, and laptops, incorporate plastic injection-molded parts. This process is used to produce casings, buttons, and internal components that require precision and a high-quality finish.
3. Medical Devices
The medical industry relies on plastic injection molding to manufacture disposable items such as syringes, IV bags, and surgical instruments. The ability to produce sterile, precise, and complex shapes makes this process ideal for medical applications.
4. Household Items
Plastic injection molding is commonly used to create everyday household products, including kitchenware, storage containers, toys, and furniture components. The process allows for mass production of affordable and functional items.
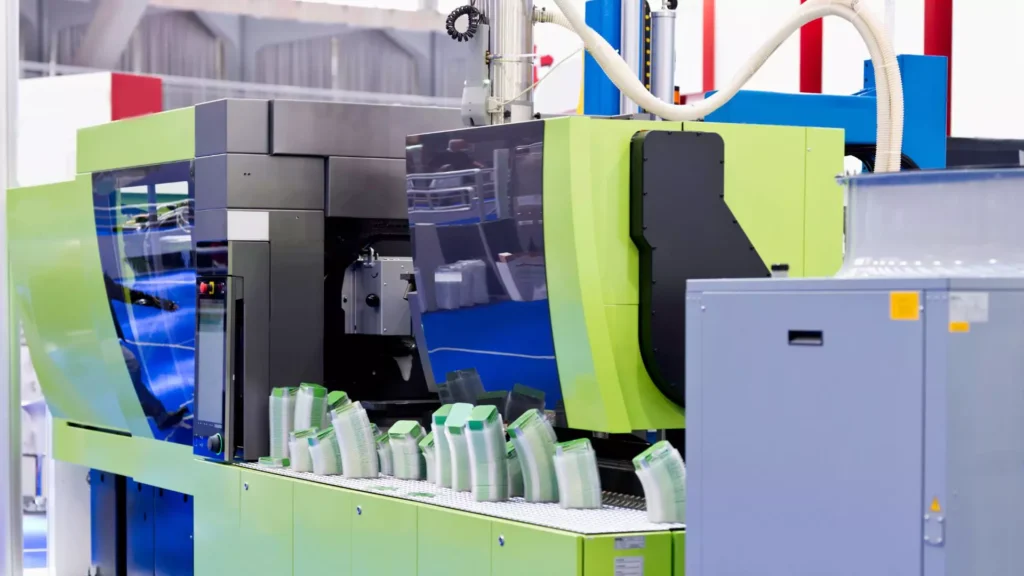
5. Packaging
The packaging industry utilizes plastic injection molding to produce a variety of containers, bottles, and closures. This method allows for the creation of lightweight yet strong packaging solutions that can be tailored to specific product requirements.
6. Industrial Equipment
Many industrial applications use plastic injection-molded components for machinery, tools, and equipment housings. The durability and resistance to chemicals make molded plastics suitable for harsh working environments.
7. Aerospace Parts
In the aerospace sector, plastic injection molding is used to create lightweight, high-strength components that contribute to overall aircraft efficiency. Parts such as interior fittings, housings, and structural elements can be produced using this method.
8. Construction Materials
Plastic injection molding is also employed in the construction industry to manufacture items like window frames, fittings, and fixtures. The versatility of molded plastics allows for innovative designs that meet specific building requirements.
Conclusion
Plastic injection molding is a vital process that continues to evolve with advancements in materials and technology. Its ability to create reliable, uniform parts quickly and cost-effectively makes it a cornerstone of modern manufacturing. As we move towards a future that demands more precision and sustainability, plastic injection molding remains at the forefront, ready to meet the challenges and needs of industries worldwide.
If you’re interested in exploring the potential of plastic injection molding for your projects, consider reaching out to Align Manufacturing.Their team of industry experts can provide valuable insights and solutions tailored to your specific needs. Understanding this manufacturing process opens the door to endless possibilities in product design and production, and Align Manufacturing is well-equipped to help you navigate this landscape
FAQs
Plastic injection molding can utilize a wide variety of thermoplastic materials, including ABS, polycarbonate, nylon, and polypropylene. Each material has unique properties that make it suitable for different applications. For instance, ABS is known for its strength and impact resistance, while polycarbonate is favored for its clarity and heat resistance.
The injection molding process ensures precision through the use of custom-designed molds and high-pressure injection techniques. The molds are engineered to exact specifications, allowing for tight tolerances and consistent part dimensions. This level of accuracy is crucial for industries like automotive and medical, where even minor variations can lead to significant issues.
Learn more about how Align Manufacturing can help you with injection molding here.
- Consider the following factors:
- Part function and requirements: Strength, flexibility, chemical resistance, temperature resistance, etc.
- Aesthetics: Color, finish, transparency.
- Cost: Material cost, processing cost.
- Environmental impact: Recyclability, biodegradability.
- Common mold materials include:
- Steel: Most durable and widely used.
- Aluminum: Lighter and less expensive than steel, but less durable.
- Beryllium copper: Excellent for high-precision parts.
Ductile Iron vs. Cast Iron: Understanding the Differences and Applications
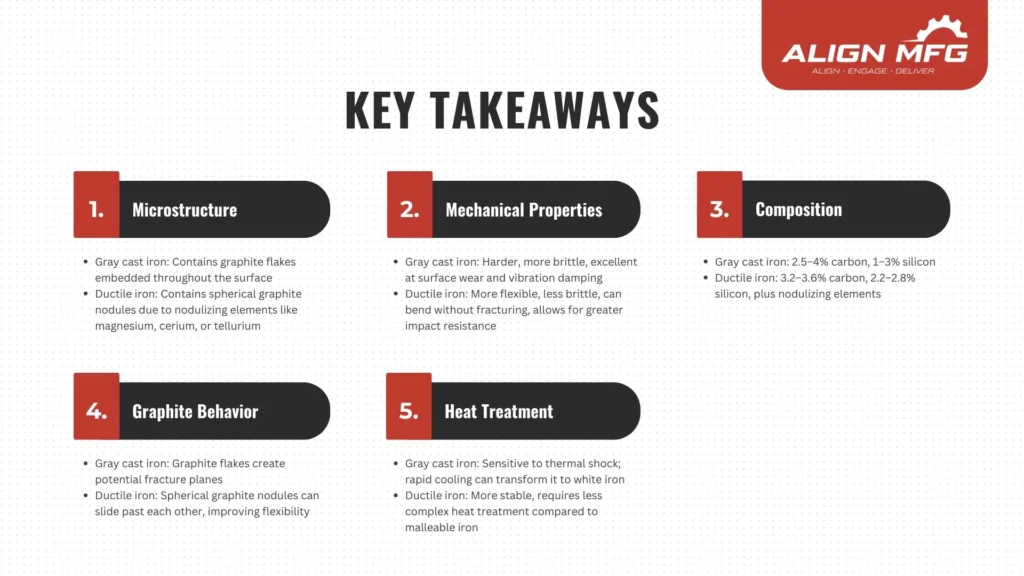
Iron has long been a cornerstone of industrial manufacturing and construction, with various forms serving distinct purposes. Among these, ductile iron and cast iron are two of the most widely utilized materials. While both originate from iron, they exhibit unique properties that make them suitable for different applications. In this comprehensive blog post, we will explore the characteristics, advantages, and disadvantages of ductile iron and cast iron, as well as their respective applications and welding capabilities.
Historical Context
Cast iron has a rich history, dating back to ancient China in the 5th century BC, where it was first used for making tools and weapons. Its use spread to Europe in the 14th century, where it became a popular material for cookware, pipes, and construction due to its durability and ease of casting.
Ductile iron, also known as spheroidal graphite iron, was developed much later, in the 1940s. The invention is attributed to the work of American metallurgist Keith Millis, who discovered that adding small amounts of magnesium to molten iron could change the graphite structure from flakes to nodules. This transformation significantly improved the material's strength and ductility, addressing the brittleness associated with traditional cast iron. Since its introduction, ductile iron has become increasingly popular in various applications, particularly in the automotive and construction industries.
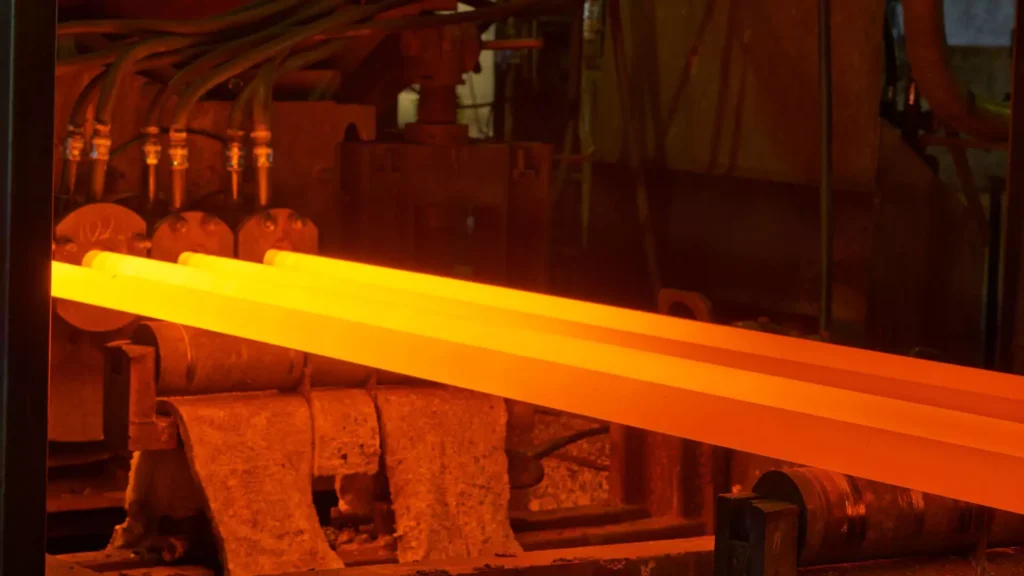
What is Cast Iron?
Cast iron is an alloy primarily composed of iron, carbon (typically 2-4%), and silicon (1-3%). It is produced by melting iron and pouring it into molds to create various shapes. The distinctive microstructure of cast iron, characterized by the presence of graphite flakes, gives it a grey color and contributes to its mechanical properties.
The term "gray cast iron" refers to a specific type of cast iron characterized by its distinctive microstructure and appearance. Here's some context:
When molten iron cools and solidifies, its carbon content determines its microstructure. In gray cast iron, the carbon precipitates out as graphite flakes during cooling. These flakes give the metal a characteristic gray color when fractured or polished, hence the name "gray" cast iron.
The gray color comes from the graphite flakes distributed throughout the iron matrix. These flakes create a distinctive metallic appearance and contribute to the material's unique mechanical properties. Under a microscope, the graphite appears as flat, interconnected structures embedded in the iron.
The formation of these graphite flakes depends on specific cooling conditions and chemical composition, particularly the silicon content. The silicon helps stabilize the graphite formation, preventing the carbon from forming harder, more brittle structures like cementite.
This microstructure gives gray cast iron its notable characteristics:
- Good vibration damping
- High wear resistance
- Low ductility
- Excellent machinability
One of the notable features of cast iron is its remarkable hardness, which makes it resistant to wear and abrasion. However, this hardness comes at a cost; cast iron is also brittle, meaning it can fracture easily under stress. Despite this brittleness, cast iron offers excellent machinability and vibration damping properties, making it a popular choice for applications such as cookware, engine blocks, pipes, and architectural elements.
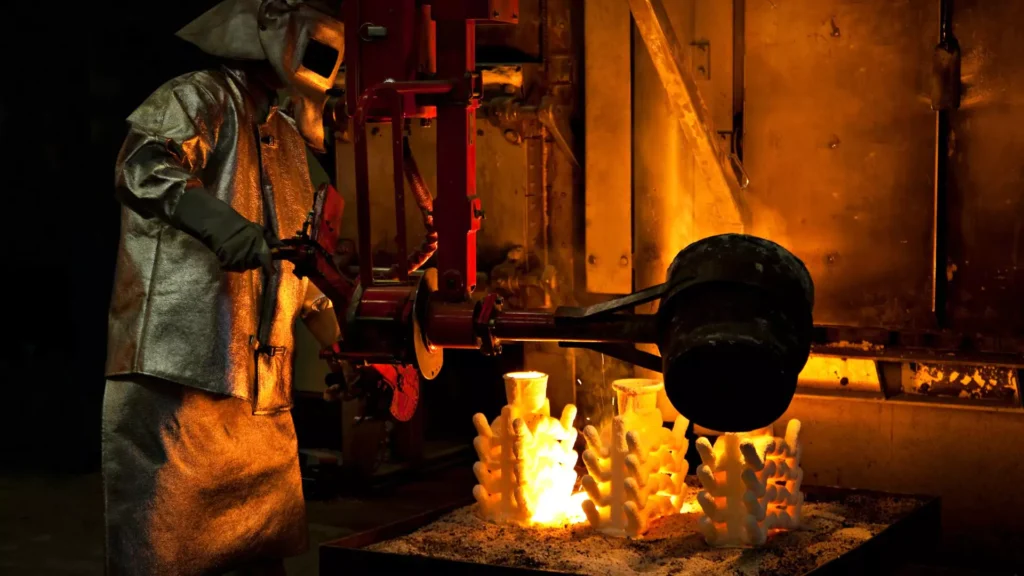
Advantages and Disadvantages of Cast Iron
Advantages:
- Cost-Effective: Generally less expensive to produce than ductile iron, making it a budget-friendly option.
- Wear Resistance: Its hardness provides excellent resistance to wear, suitable for various applications.
- Good Vibration Damping: Ideal for machinery and equipment that require stability and noise reduction.
Disadvantages:
- Brittleness: Prone to cracking and breaking under high stress, limiting its use in certain applications.
- Corrosion: Over time, cast iron can rust and degrade if not properly maintained.
Applications of Cast Iron
Due to its durability and affordability, cast iron is widely used in various industries. Common applications include:
- Cookware: Frying pans, Dutch ovens, and griddles are often made from cast iron for its excellent heat retention.
- Engine Blocks: Cast iron is commonly used in automotive manufacturing for engine components due to its strength.
- Pipes: It is a popular choice for water and sewage pipes due to its corrosion resistance.
- Architectural Elements: Decorative features like railings, columns, and manhole covers often utilize cast iron for its aesthetic appeal and durability.
Exploring Ductile Iron
Ductile iron, also known as nodular cast iron or spheroidal graphite iron, is a more modern alloy developed in the mid-20th century. It is produced by adding small amounts of magnesium to molten iron, which transforms the graphite structure into nodules rather than flakes. This unique microstructure imparts significant toughness and ductility to the material.
Ductile iron is characterized by its ability to bend and deform without breaking, making it far less brittle than cast iron. It exhibits excellent tensile and yield strength, making it suitable for demanding applications. This material also offers good machinability, allowing for precision engineering and manufacturing.

Advantages and Disadvantages of Ductile Iron
Advantages:
- Strength and Toughness: Ductile iron is superior to cast iron, making it ideal for high-stress applications.
- Flexibility: Its ability to bend without breaking allows for better performance under stress.
- Corrosion Resistance: More suitable for outdoor and moist environments, reducing the risk of degradation.
Disadvantages:
- Cost: Generally more expensive to produce due to its complex manufacturing process.
- Weight: Heavier than some alternative materials, which may be a consideration in weight-sensitive applications.
Comparing Properties of Ductile Iron and Cast Iron
To better understand the differences between ductile iron and cast iron, the following table outlines their key properties:
Property | Cast Iron | Ductile Iron |
Composition | Iron, 2-4% Carbon, 1-3% Silicon | Iron, 3-4% Carbon, 0.1-0.5% Magnesium |
Microstructure | Flake Graphite | Nodular Graphite |
Ductility | Low | High |
Strength | Moderate | High |
Corrosion Resistance | Moderate | High |
Machinability | Good | Good |
Cost | Lower | Higher |
Welding Capability | Difficult | Good, with appropriate techniques |
Welding Capabilities
When it comes to welding, ductile iron is generally more favorable than cast iron. The brittleness of cast iron makes it challenging to weld, as it can crack or warp during the welding process. However, if welding cast iron is necessary, techniques such as pre-heating and using nickel-based electrodes can help mitigate some of the issues.
In contrast, ductile iron can be welded using traditional welding methods, including MIG (Metal Inert Gas) and TIG (Tungsten Inert Gas) welding. The presence of nodular graphite allows ductile iron to absorb the stresses associated with welding, making it a more versatile choice for applications that require welding.
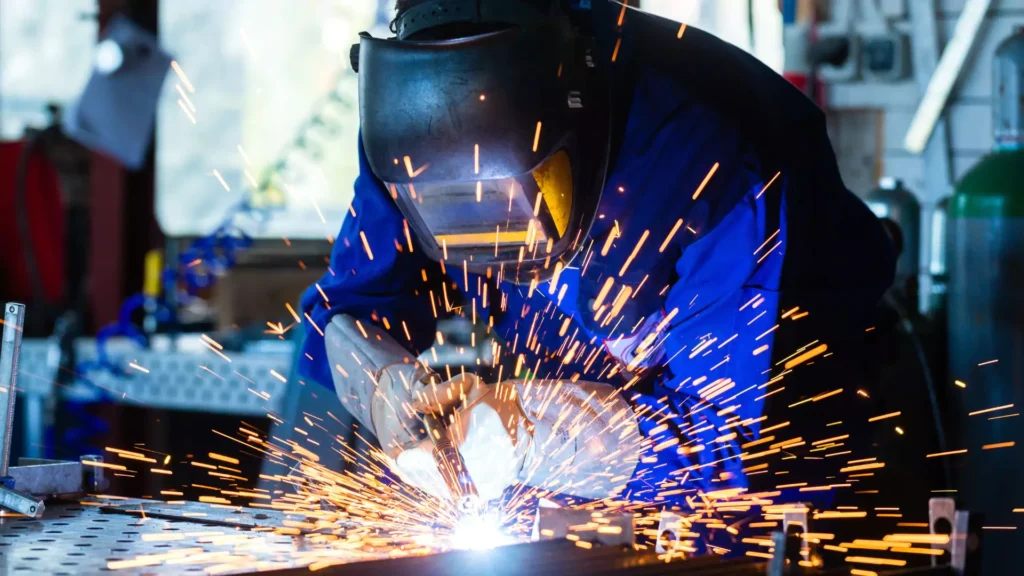
Which Should You Choose?
Both ductile iron and cast iron play vital roles in the industrial sector, and recognizing their differences will enable you to make well-informed decisions for your upcoming projects. With continuous technological advancements, both materials are evolving to meet the demands of modern industry. For further inquiries and assistance, you can contact Align Manufacturing, where our experts are ready to help you choose the right material for your project needs.
Material Selection Criteria for Iron Alloys:
Key Considerations:
- Analyze working stress and component requirements
- Evaluate specific mechanical properties
- Compare cost-effectiveness
Selection Factors:
- Load-bearing capacity
- Stress tolerance
- Dimensional stability
- Environment of use
- Manufacturing constraints
- Budget limitations
Decision Process:
- Ductile iron: More flexible, better impact resistance
- Cast iron: Higher hardness, better vibration damping
Final Choice: Balances technical performance with economic feasibility. Not just about material properties, but matching precise application needs.
FAQS
The primary differences between ductile iron and cast iron lie in their microstructure and mechanical properties. Ductile iron contains nodular graphite, which provides it with greater ductility and toughness, making it less brittle than cast iron, which has flake graphite. As a result, ductile iron can withstand higher stress and is more resistant to cracking.
Yes, ductile iron can be welded using traditional welding methods such as MIG (Metal Inert Gas) and TIG (Tungsten Inert Gas) welding. Its unique microstructure allows it to absorb welding stresses effectively. In contrast, welding cast iron is more challenging due to its brittleness, but it can be done using pre-heating techniques and nickel-based electrodes.
While cast iron can be used outdoors, it is prone to corrosion if not properly coated or maintained. Over time, exposure to moisture can lead to rust and degradation. Ductile iron, however, is generally more resistant to corrosion, making it a better choice for outdoor applications.
Cast iron is typically more cost-effective to produce than ductile iron, making it a budget-friendly option for many applications. However, ductile iron's superior mechanical properties often justify its higher cost in high-stress applications where durability and flexibility are essential. The choice ultimately depends on the specific requirements and constraints of the project.
Ductile Iron Applications:
- Pump casings
- Valve bodies
- Large gas and oil pipes
- Major water and sewage lines
- Bollards designed for impact resistance
- Automotive components
- Cable casings
- Pipes under pressure
Cast Iron Applications:
- Manhole covers
- Tree grating
- Trench grating
- Cookware (like cast iron skillets)
- Engine blocks
- Machine bases
- Brake components
- Smaller pipes
- Guttering pipes
- Stove and grill plates
Trump Tariffs and Their Implications
Tariff Proposals:
Trump aims to impose broad tariffs to address trade imbalances and boost U.S. manufacturing.
Proposes creating a new agency, the “External Revenue Service,” to collect tariffs directly from foreign importers.
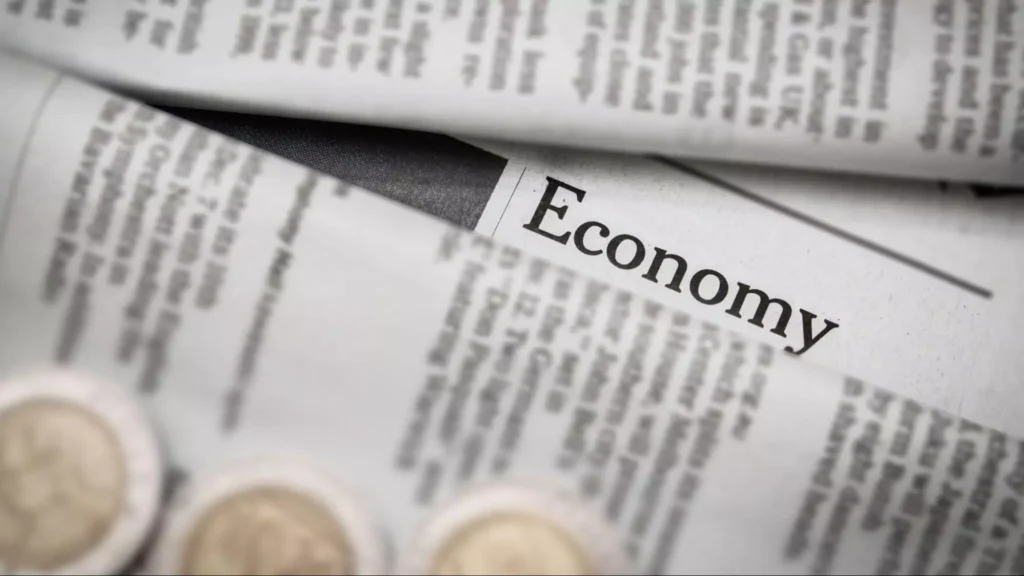
Impact on Trade and Economy:
Short-Term Costs:
Tariffs would increase prices for U.S. consumers, affecting essential goods like apparel, appliances, and toys.
Organizations like the National Retail Federation warn of a reduction in consumer spending power by up to $78 billion.
Long-Term Adjustments:
Tariffs may lead to restructuring of global supply chains, but the U.S. might remain too expensive for onshore manufacturing.
Historical Context:
Under Trump’s previous administration, tariffs on $360 billion worth of Chinese goods triggered a trade war.
Subsequent actions by President Biden retained and expanded tariffs, highlighting bipartisan support for economic protectionism.
Strategic Considerations:
While tariffs aim to boost U.S. jobs and revenue, they risk economic retaliation and higher costs for businesses and consumers.
Critics argue that such measures create a “lose-lose” scenario: exporters face reduced demand, while U.S. consumers and businesses bear higher costs.
Global Trends:
The rise in tariffs reflects a broader trend of linking economic security to national security.
Countries are focusing on industrial policies to ensure self-reliance and mitigate geopolitical risks.
China’s Resilience:
Despite tariffs, China’s cost-efficient manufacturing capabilities continue to dominate global markets.
Tariffs often lead to indirect imports via other countries, circumventing their intended effects.
Interesting Insights
Tariffs might generate short-term government revenue but risk eroding consumer spending and global economic growth.
Biden, despite criticizing tariffs during his campaign, upheld many of Trump’s trade policies, illustrating a global shift toward protectionism.
Manufacturing and services are becoming intertwined as nations prioritize self-reliance in critical industries.
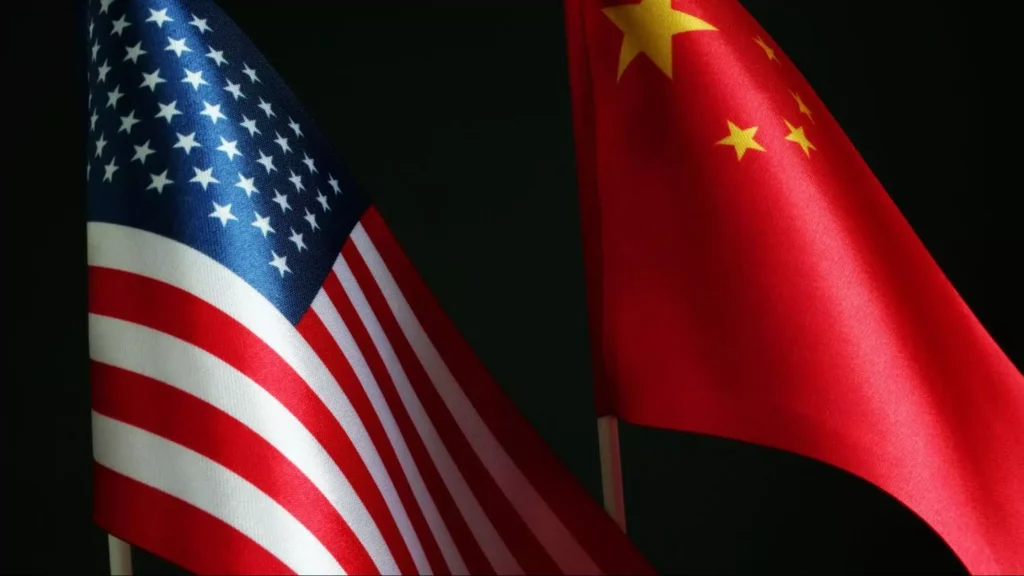
Watch more here
Trump Tariffs and Their Implications
The U.S. President-elect Donald Trump’s proposed tariffs, including a 10% universal import tariff and rates as high as 60% on Chinese goods, present a unique challenge for businesses dependent on international supply chains. These tariffs are aimed at addressing trade imbalances and promoting U.S. manufacturing, but they also significantly increase costs for businesses and consumers alike. For companies navigating these changes, Align Manufacturing offers a solution to ensure supply chain stability, cost efficiency, and resilience in a volatile global trade environment.
1. Mitigating Tariff Impact
- Align Manufacturing provides access to a diversified manufacturing network in Southeast Asia (SEA), including countries like Vietnam, Thailand, and India. By shifting production to these regions, businesses can significantly reduce exposure to high tariffs on Chinese goods.
- SEA’s favorable trade agreements with the U.S. and other markets offer additional cost savings and competitive advantages.
2. Cost-Effective Solutions
- Align Manufacturing’s partners in SEA provide competitive labor and production costs without compromising on quality. This ensures that businesses can maintain profitability even amidst rising tariffs.
- Our expertise in sourcing the right manufacturing processes ensures efficient production tailored to your specific needs.
3. Access to High-Quality Manufacturing
- With decades of experience, Align Manufacturing ensures high standards across all projects, leveraging advanced technologies and robust quality control measures.
- We collaborate with reliable SEA manufacturers who are investing in quality infrastructure and sustainable practices.
4. Supply Chain Resilience
- Diversifying your manufacturing base with Align Manufacturing reduces reliance on a single source, such as China, and minimizes disruptions caused by trade wars or geopolitical instability.
- Our global expertise ensures smooth operations and on-time delivery, even in challenging trade environments.
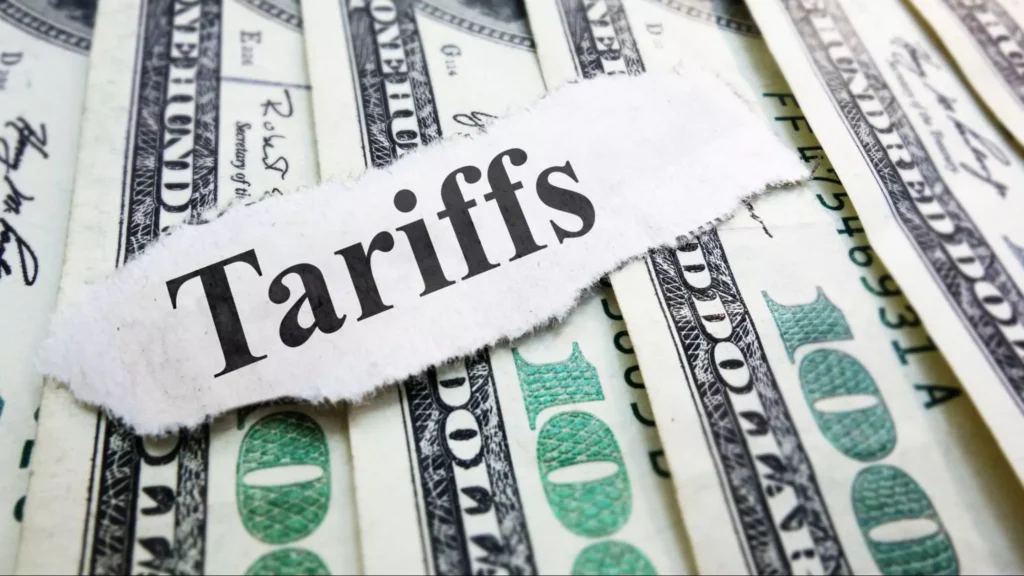
The Strategic Advantage of Align Manufacturing
The proposed tariffs highlight the importance of proactive supply chain management and diversification. Align Manufacturing is uniquely positioned to help businesses transition smoothly, offering:
- Tailored Manufacturing Solutions: We customize our services to fit your product requirements, ensuring cost-effective and high-quality outcomes.
- Comprehensive Support: From initial consultation to final delivery, Align Manufacturing offers end-to-end support, ensuring your operations remain seamless.
- Trusted Expertise: Our deep knowledge of SEA markets and long-standing relationships with manufacturers provide businesses with a competitive edge.
Why Now is the Time to Act
Trump’s tariff proposals underscore the urgency for businesses to reevaluate their global manufacturing strategies. Delaying action could result in higher costs, supply chain disruptions, and lost market share. By partnering with Align Manufacturing, businesses can:
- Avoid the financial strain of tariffs by leveraging cost-effective SEA manufacturing.
- Maintain product quality and delivery timelines with a diversified supply chain.
- Stay competitive in an increasingly protectionist global market.
Conclusion
Align Manufacturing is your strategic partner in navigating the complexities of global trade. With our expertise in Southeast Asia’s manufacturing landscape, we help businesses reduce costs, mitigate risks, and thrive despite tariff challenges.
Contact Align Manufacturing today to learn how we can support your business in adapting to these changing trade dynamics and securing a competitive advantage.
Visit Align Manufacturing and explore our manufacturing services to learn more about how we can help your business succeed in the face of global trade challenges.